
9534
.pdf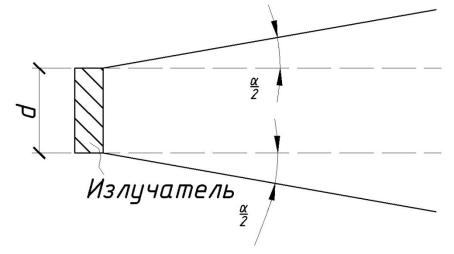
тому же кратчайшему пути к излучателю, который в промежутках между посылками импульсов выполняет роль приемника.
В этом случае на экране электронно-лучевой трубки 4 (рис. 5.1) дефектоскопа будут видны два импульса. Первый из них соответствует моменту посылки зондирующего импульса, а второй – моменту прихода отраженного сигнала, так называемого донного, или эхо-импульса.
Измеряя время, через которое появился данный импульс, и зная скорость с2 , нетрудно определить толщину исследуемого изделия:
S с |
2 |
. |
(5.9) |
|
2 |
|
|
|
|
|
На этом принципе работают ультразвуковые толщиномеры, позволяющие при одностороннем доступе измерить толщину элемента конструкции. Справочные материалы по скорости распространения ультразвуковых волн в различных материалах и сплавах приведены в Приложении 1.
Если на пути ультразвукового сигнала окажется дефект, акустическое сопротивление которого значительно отличается от акустического сопротивления исследуемого материала, например трещины или поры, то происходит отражение волны, и на экране электронно-лучевой трубки появляется дополнительный импульс. Но так как дефект расположен ближе к излучателю-приемнику ультразвука, чем граница раздела II-II, то сигнал от дефекта всегда появляется между зондирующим и донным импульсом. Измеряя время, можно определить глубину залегания дефекта.
С целью направленного поиска дефектов и увеличения амплитуды ультразвуковых колебаний в ультразвуковых дефектоскопах используются узконаправленные лучи (рис. 5.2). Степень фокусировки ультразвукового луча определяется углом расхождения , который определяется по формуле:
|
|
12 |
, |
(5.10) |
|
2 |
d |
||||
|
|
|
где - длина волны, d - диаметр источника колебаний.
Для создания направленного луча используют колебания высоких частот и источники относительно большего диаметра (более 8 10мм).
Рис. 5.2. Фокусировка ультразвукового луча
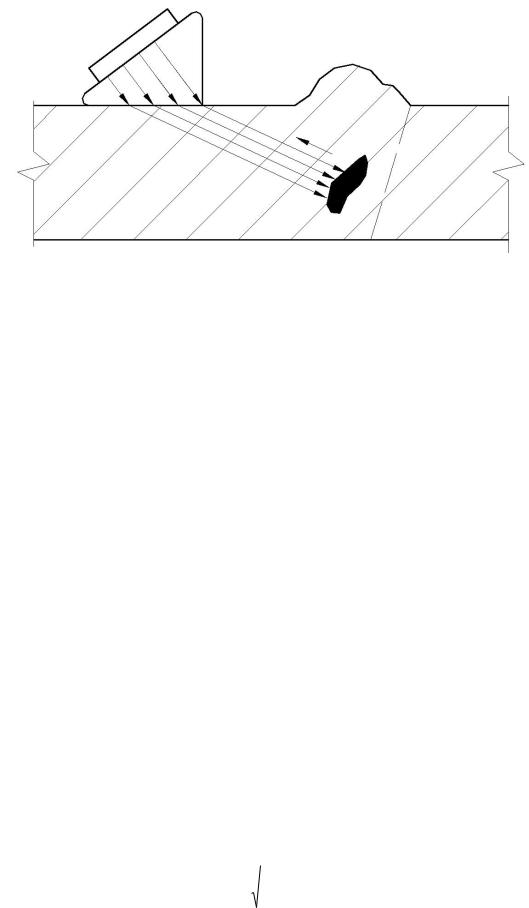
Ввиду того, что при контроле качества сварных швов вследствие неровностей поверхности невозможно вводить колебания, используют призматические излучатели-приемники (рис. 5.3).
Рис. 5.3. Призматический излучатель-приемник
Они позволяют вводить ультразвуковые колебания под определенным углом и находят дефекты под неровными поверхностями. Это достигается при определенном угле падения ультразвуковых волн на границу исследуемой поверхности. Практически для дефектоскопии сварных швов обеспечивают угол падения ультразвуковых волн в пределах 300 600. Методика контроля качества изделия (соединения) призматическими излучателями с наклонным углом падения ультразвуковых волн также основана на фиксировании эхо-сигналов от дефектов и донных импульсов.
Следует отметить, что, для обеспечения точности выполнения контроля с учетом способности ультразвуковых волн отражаться от границы раздела сред с разными акустическим свойствами, особые требования предъявляются к качеству контролируемой поверхности, которая должна обеспечивать плотный акустический контакт с датчиком излучателя-приемника (пьезопреобразователя).
5.4. Скорость ультразвука в твердых средах
Скорость распространения ультразвуковых волн в твердых средах зависит от их упругих постоянных. Большинство строительных материалов (металлы, сплавы, пластмассы и др.) являются изотропными. Условно изотропным считается и бетон. Упругие свойства таких материалов характеризуются модулем упругости E и коэффициентом Пуассона . Кроме этих постоянных, используется и модуль сдвига G , который определяется по формуле:
|
|
|
|
|
E |
|
|
||
G |
|
. |
|
|
|
||||
2 1 |
|
|
|||||||
Скорость продольных сl и поперечных сt волн определяется через упругие |
|||||||||
постоянные среды с помощью следующих зависимостей: |
|
||||||||
|
|
|
|
|
|
|
|||
с |
E |
|
1 |
|
; |
(5.11) |
|||
|
1 1 2 |
||||||||
l |
|
|
|
||||||
|
|
|
|
|
|
|
|

с |
|
E |
|
1 |
|
. |
(5.12) |
|
|
||||||
t |
|
2 1 |
|
||||
|
|
|
Скорость распространения продольных и поперечных волн в металлах зависит от их химического состава, кристаллической структуры, технологии обработки и температуры. В приложении 1 приведены значения скоростей распространения продольных волн для широко распространенных в строительстве сталей и сплавов.
Во всех металлах и сплавах скорость ультразвука имеет отрицательную температурную зависимость, то есть уменьшается с ростом температуры. Кроме того, скорость распространения ультразвука в металлоизделиях зависит от вида технологической обработки. При проведении дефектоскопии прессованных изделий из цветных металлов и сплавов, а также в стальном прокате отмечаются отличающие значения скорости ультразвука по длине одного и того же изделия. Причиной этого является различная микроструктура металла или сплава по длине изделия.
6. ДЕФЕКТЫ СВАРНЫХ СОЕДИНЕНИЙ
Качество сварных соединений металлических конструкций зависит от качества подготовки изделия под сварку и качества выполненных сварочных работ.
Дефекты, допущенные при подготовке деталей к сварке, существенно сказываются и на качестве всего сварного соединения. Основными причинами такого рода дефектов могут быть: неисправности оборудования, применяемого для изготовления заготовок и приспособлений для сборки; недоброкачественность исходных материалов; низкая квалификация обслуживающего персонала. Наиболее характерными из них являются:
-неправильный угол скоса кромок в швах;
-слишком большое или малое притупление по длине стыкуемых кромок;
-непостоянство зазора между кромками и несовпадение стыкуемых плоскостей кромок;
-расслоения металла и загрязнения на кромках и т.п.
Правильность сборки контролируют внешним осмотром и геометрическими измерениями с помощью шаблонов и специального инструмента.
Сварочные дефекты могут быть наружными и внутренними.
Форма и размеры сварочных швов задаются соответствующими техническими условиями. При сварке плавлением, как правило, регламентируют ширину и выпуклость шва, число проходов и глубину проплавления.
Швы могут быть неравномерными, что является следствием неустойчивого режима сварки, а также неравномерности зазора и угла скоса кромок. Кроме того, неравномерность шва может появиться в местах расположения прихваток из-за нарушения стабильности сварочного процесса в них.
Неправильная форма швов является следствием неточного направления электрода относительно разделки.
В случае недостаточной скорости подачи электродной проволоки при данной скорости сварки, увеличения угла скоса кромок или зазора между ними, протекания металла в зазор возникает так называемая неполномерность сварных швов.
К внутренним дефектам, нарушающим сплошность сварного соединения, можно отнести поры, шлаковые включения, трещины, несплавления, непровары и др.
Поры в сварном шве – это наиболее часто встречающиеся дефекты, которые образуются при сварке загрязненных кромок металла, т.е. при плохой зачистке от окалины и ржавчины. Поры или шлаковые включения образуются часто вследствие недостаточного сварочного тока и чрезмерно большой скорости сварки. Размеры пор и шлаковых включений колеблются от нескольких микрометров до нескольких миллиметров и по форме близки к сферической. Шлаковые включения могут располагаться на границе сплавления основного металла с наплавленным, а непровары чаще всего – в корне шва.
Трещины являются весьма опасными дефектами, так как создают резкую концентрацию напряжений. Трещины появляются при сварке высокоуглеродистых и легированных сталей в результате слишком быстрого охлаждения. Иногда трещины возникают при охлаждении сваренных заготовок на воздухе. Они могут располагаться вдоль и поперек сварного соединения, в местах пересечения швов, а также в основном металле.
Несплавления кромок основного металла с наплавленным металлом или слоев шва между собой при многослойной сварке называют непроваром, представляющим собой несплошность между основным и наплавленным металлом.
Непровары образуются при небольшом зазоре между кромками и малом угле их скоса, завышенном притуплением и загрязнении кромок, неточном направлении электродной проволоки относительно места сварки, недостаточном сварочном токе или чрезмерно большой скорости сварки.
На поверхности сварных швов образуются подрезы, представляющие собой углубления в основном металле, появляющиеся в процессе сварки вдоль края шва.
При обрыве дуги образуются кратеры в виде углублений, которые уменьшают рабочее сечение шва, снижают его прочность и коррозионную стойкость. Часто кратер служит очагом появления трещин. В результате большого сварочного тока образуются прожоги.
Изготовить сварную конструкцию без дефектов практически невозможно. Поэтому необходимо, чтобы сварная конструкция имела минимум допустимых дефектов и удовлетворяла требованиям, предъявляемым к ней техническими условиями.
Классификация основных дефектов соединений при сварке металлов плавлением по ГОСТ 30242-97 приведена в приложении 2.
7. ПОДГОТОВКА ПОВЕРХНОСТИ К УЛЬТРАЗВУКОВОМУ КОНТРОЛЮ
Сварное соединение подготавливают к ультразвуковому контролю при отсутствии в соединении наружных дефектов. При этом форма и размеры околошовной зоны должны позволять перемещать преобразователь в пределах, обеспечивающих прозвучивание акустической осью преобразователя сварного соединения или его части, подлежащей контролю.
Поверхность соединения, по которой перемещают преобразователь, не должна иметь вмятин и неровностей, с поверхности должны быть удалены брызги металла, отслаивающаяся окалина, краска и загрязнения. Допустимость наличия неотслаивающейся окалины и краски при контроле указывается в технической документации на контроль. При этом обязательным является установление акустического контакта поверхности преобразователя с поверхностью металла околошовной зоны контролируемого участка сварного шва. Для этого на контролируемую поверхность металла наносят контактную смазку. Рекомендуемые виды контактных смазок, в зависимости от температуры, приведены в табл. 7.1.
При механической обработке соединения, предусмотренной технологическим процессом на изготовление сварной конструкции, а также при механической подготовке поверхности под ультразвуковой контроль шероховатость должна быть не ниже Rz 40 мкм по ГОСТ 2789-73. Требования к допустимой волнистости и к подготовке поверхности указываются в технической документации на контроль.
При проведении ультразвукового контроля труб и резервуаров, находящихся в эксплуатации, последние должны быть освобождены от жидкости. Допускается контролировать трубы и резервуары с жидкостью по методике, оговариваемой в технической документации на контроль, утвержденной в установленном порядке.
Подготовка поверхности под ультразвуковую толщинометрию выполняется аналогично подготовке для дефектоскопии сварных соединений.
|
|
Т а б л и ц а 7.1 |
|
|
Рекомендуемые контактные смазки |
||
|
|
|
|
Наименование и ГОСТ контактных |
Температура контролируемой |
|
|
|
смазок |
поверхности |
|
|
|
|
|
ЦИАТИМ 201 |
ГОСТ 6267 |
–10о С до +50о С |
|
ЦИАТИМ 202 |
ГОСТ 11110 |
–10о С до +50о С |
|
ЦИАТИМ 221 |
ГОСТ 9433 |
–5о С до +50о С |
|
МС70 ГОСТ 9762 |
–10о С до +50о С |
|
|
Глицерин ГОСТ 6823 |
+10о С до +50о С |
|
|
Масло трансформаторное ГОСТ 982 |
–10о С до +50о С |
|
|
Масло веретенное ГОСТ 1642 |
–10о С до +50о С |
|
|
Масло конденсаторное ГОСТ 5775 |
–10о С до +50о С |
|
Примечание. Допускается в качестве контактной смазки применять моторное масло при соответствующей вязкости в зимний период времени (отрицательных температурах).
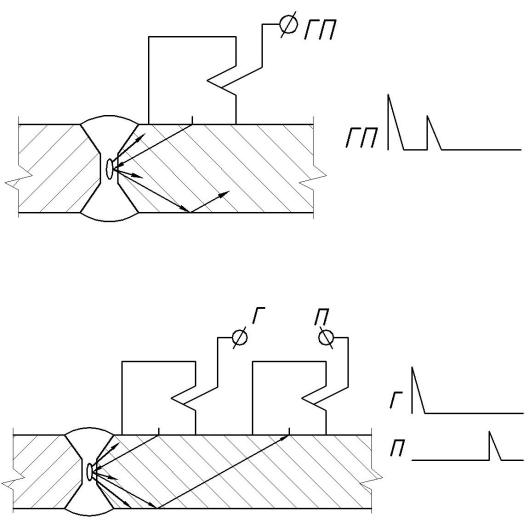
8. УЛЬТРАЗВУКОВОЙ КОНТРОЛЬ КАЧЕСТВА СВАРНЫХ СОЕДИНЕНИЙ
8.1. Методы ультразвукового контроля сварных соединений
При контроле сварных соединений ультразвуковые волны вводятся в шов через основной металл с помощью наклонных акустических преобразователей. Различают способы прозвучивания прямым лучом, однократно отраженным и многократно отраженными лучами.
При контроле сварных соединений применяют эхо-импульсный, теневой (зеркально-теневой) или эхо-теневой методы.
При эхо-импульсном методе применяют совмещенную (рис. 8.1.1), раздельную (рис. 8.1.2 и 8.1.3) и раздельно-совмещенную (рис. 8.1.4 и 8.1.5) схемы включения преобразователей. На рис. 8.1.1-8.1.7 приняты следующие условные обозначения: Г - вывод к генератору ультразвуковых колебаний; П - вывод к приемнику.
Рис. 8.1.1. Совмещенная схема включения преобразователей при эхо-импульсном методе контроля сварных соединений
Рис. 8.1.2. Раздельная схема включения преобразователей при эхо-импульсном методе контроля сварных соединений при определении глубины расположения дефекта и его высоты
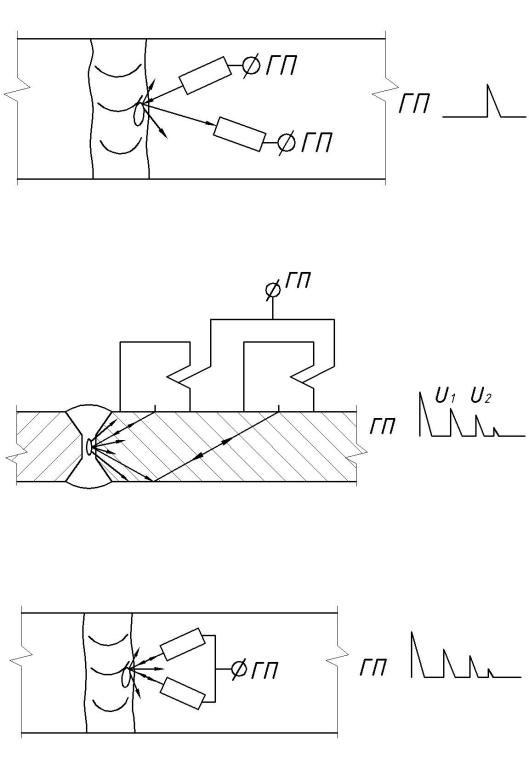
Рис. 8.1.3. Раздельная схема включения преобразователей при эхо-импульсном методе контроля сварных соединений при определении длины дефекта
Рис. 8.1.4. Раздельно-совмещенная схема включения преобразователей при эхо-импульсном методе контроля сварных соединений при определении глубины расположения дефекта и его высоты
Рис. 8.1.5. Раздельно-совмещенная схема включения преобразователей при эхоимпульсном методе контроля сварных соединений при определении длины дефекта
При теневом методе применяют раздельную (рис. 8.1.6) схему включения преобразователей.
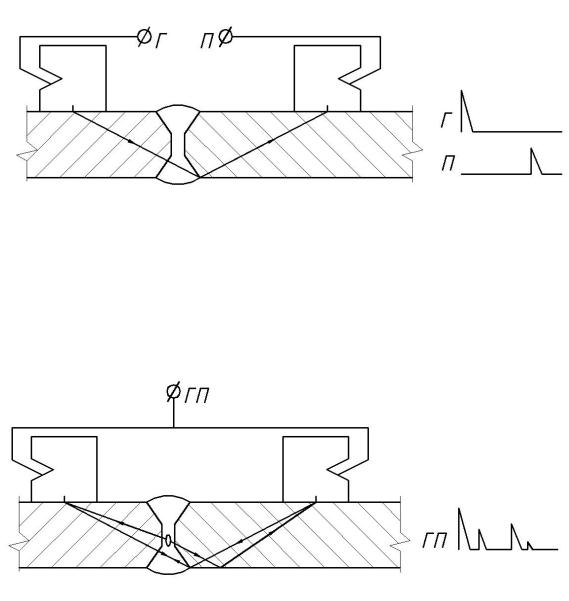
Рис. 8.1.6. Раздельная схема включения преобразователей при теневом методе контроля сварных соединений
При эхо-теневом методе применяют раздельно-совмещенную (рис. 8.1.7) схему включения преобразователей.
Рис. 8.1.7. Раздельно-совмещенная схема включения преобразователей при эхо-теневом методе контроля сварных соединений
Стыковые сварные соединения прозвучиваются по схемам, приведенным на рис. 8.1.8 – 8.1.11, тавровые соединения - по схемам, приведенным на рис. 8.1.12 – 8.1.14, и нахлесточные соединения - по схемам, приведенным на рис. 8.1.15 и
8.1.16.
Допускается применять другие схемы, приведенные в технической документации на контроль, утвержденной в установленном порядке.
Прозвучивание сварного соединения выполняют по способу продольного и (или) поперечного перемещения преобразователя при постоянном или изменяющемся угле ввода луча. Способ сканирования должен быть установлен в технической документации на контроль, утвержденной в установленном порядке.
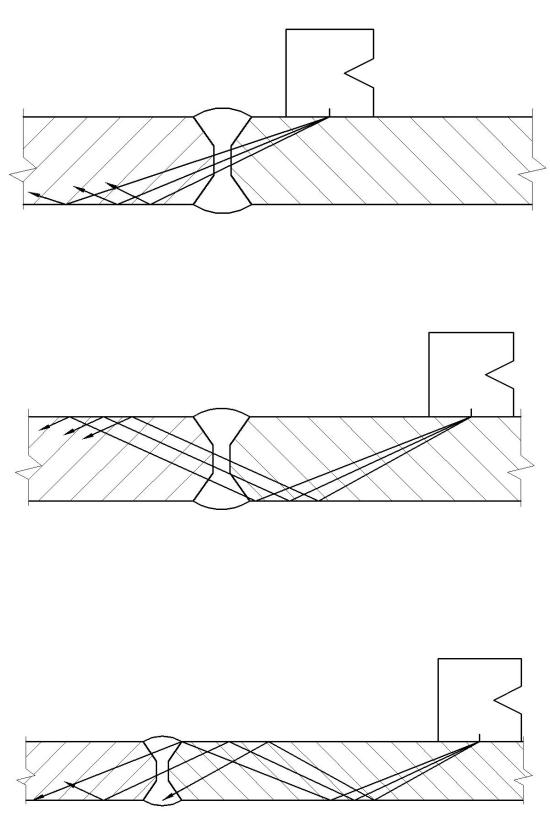
Рис. 8.1.8. Схема прозвучивания стыкового сварного соединения по способу поперечного перемещения преобразователя
Рис. 8.1.9. Схема прозвучивания стыкового сварного соединения по способу поперечного перемещения преобразователя (однократное отражение луча)
Рис. 8.1.10. Схема прозвучивания стыкового сварного соединения по способу поперечного перемещения преобразователя (двукратное отражение луча)
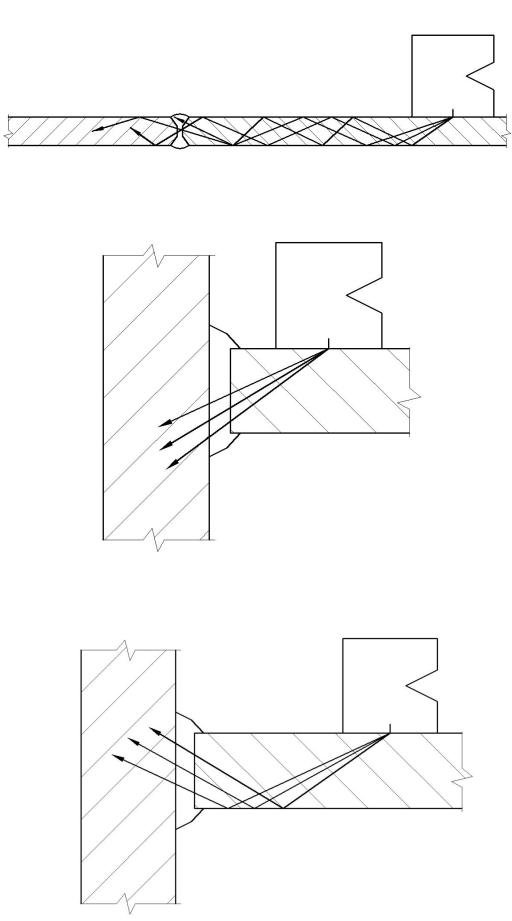
Рис. 8.1.11. Схема прозвучивания стыкового сварного соединения по способу поперечного перемещения преобразователя (многократное отражение луча)
Рис. 8.1.12. Схема прозвучивания таврового сварного соединения прямым лучом
Рис. 8.1.13. Схема прозвучивания таврового сварного соединения однократно отраженным лучом по способу поперечного перемещения преобразователей