
10162
.pdfнита и жидкого сплава. Выше tл2 сталь находится полностью в жидком состоянии.
При охлаждении до tл2 сталь находится в жидком состоянии. При tл2
начинается кристаллизация аустенита. От tл2 до tс2 происходит кристалли-
зация аустенита и сталь состоит из аустенита и жидкого сплава. От tл2 до
Ar1 (727°С) сталь состоит из аустенита. При Ar1 происходит превращение аустенита в перлит. Ниже Ar1 сталь имеет структуру перлита (рис. 3.3,б).
Сталь заэвтектоидная с содержанием 1,2% углерода (рис. 3.5).
При нагреве до Ас1 (727°С) превращений нет, и сталь имеет структу-
ру: перлит + цементит вторичный. При Ас1 происходит превращение пер-
лита в аустенит. От Ас1 до Аст (критическая точка, лежащая на линии SE)
происходит растворение вторичного цементита в аустените. При Аст сталь имеет аустенитную структуру. От Аст до температуры солидуса tс3, лежа-
щей на линии АЕ, сталь находится в аустенитном состоянии. При tс3 начи-
нается плавление аустенита. В интервале от tс3 до tл3 сталь состоит из аустенита и жидкого сплава. Выше tл3 сталь полностью находится в жид-
ком состоянии.
При охлаждении до tл3 сталь находится в жидком состоянии. При tл3
(температура ликвидуса) начинается кристаллизация аустенита. От tл3 до tс3 происходит кристаллизация аустенита и сталь состоит из жидкого спла-
ва и аустенита. При tс3 (температура солидуса) сталь полностью затверде-
вает и структура ее представляет аустенит. От tс3 до линии SE (температу-
ра Аст) структура стали не изменяется. При Аст начинается выделение вторичного цементита.
От Аст до Аr1 (727°С) происходит выделение вторичного цементита и структура стали состоит из аустенита и вторичного цементита. При Аr1
(727°С) аустенит превращается в перлит. Ниже Аr1 сталь имеет структуру:
перлит + цементит вторичный (рис. 3.2,в).
Превращения в чугунах. Доэвтектический чугун с содержанием
3,0 % углерода (рис. 3.5). При нагреве до Ас1 превращений нет и чугун
70
имеет структуру: ледебурит + перлит + вторичный цементит. При этом эвтектика состоит из цементита и перлита. При Ac1 происходит превраще-
ние перлита в аустенит. Это превращение претерпевает как свободный перлит, так и перлит, входящий в эвтектику. Выше Ас1 чугун состоит из аустенита, вторичного цементита и ледебурита. При этом эвтектика состо-
ит из цементита и аустенита.
От Ac1 до tэ, (1147°С) происходит растворение вторичного цементита в аустените и аустенит насыщается углеродом до 2,14 %.
При tэ плавится ледебурит. Выше tэ чугун состоит из аустенита и жидкого сплава. От tэ, до tл4 плавится аустенит. Выше tл4 чугун находится полностью в жидком состоянии.
При охлаждении до tл4 чугун находится в жидком состоянии. При tл4
начинается кристаллизация аустенита. От tл4 до tэ (1147°С) происходит кристаллизация аустенита и при tэ чугун состоит из аустенита с содержа-
нием 2,14 % углерода и жидкого сплава эвтектического состава (4,3 %
углерода).
При tэ, происходит эвтектическая кристаллизация и образуется леде-
бурит, состоящий из цементита и аустенита с содержанием углерода 2,14 %. От tэ (1147°С) до Аr1 (727°С) из аустенита, как свободного, так и вхо-
дящего в ледебурит, выделяется вторичный цементит и содержание угле-
рода понижается до 0,8 %. Следовательно, в этом интервале температур чугун состоит из ледебурита, аустенита и вторичного цементита. При Аr1
(727°С) происходит превращение аустенита в перлит. Ниже Аr1 чугун состоит из ледебурита, перлита и вторичного цементита (рис. 3.4,а).
Эвтектический чугун с содержанием 4,3 % углерода (рис. 3.5). При нагреве до Ас1 превращений нет и чугун имеет структуру ледебурит, со-
стоящий из цементита, перлита и вторичного цементита. При Ac1 проис-
ходит превращение перлита в аустенит. Выше Ас1 чугун имеет структуру:
ледебурит, состоящий из цементита, аустенита и вторичного цементита. От
Ас1 до tэ происходит растворение вторичного цементита и аустенит насы-
71
щается углеродом до 2,14 %. При tэ чугун полностью расплавляется. Выше tэ чугун находится полностью в жидком состоянии.
При охлаждении до tэ (1147°С) чугун находится в жидком состоянии.
При tэ (1147°С) чугун полностью затвердевает и образуется структура
–ледебурит, состоящий из аустенита, содержащего 2,14 % углерода и це-
ментита. От tэ до Аr1 из аустенита выделяется вторичный цементит и со-
держание углерода в аустените понижается до 0,8 %. При Аr1 аустенит превращается в перлит. Ниже Аr1 чугун имеет структуру – ледебурит,
состоящий из цементита, перлита и вторичного цементита (рис. 3.4,б).
Заэвтектический чугун с содержанием 5,0 % углерода (рис. 3.5).
При нагреве до Ас1 превращений нет и чугун имеет структуру – леде-
бурит + первичный цементит. При Ас1 (727°С) перлит, находящийся в эвтектике, превращается в аустенит. Выше Ас1 чугун имеет структуру – ледебурит и первичный цементит, но эвтектика состоит из цементита и аустенита. От Аc1 до tэ (1147°С) происходит насыщение аустенита углеро-
дом вследствие растворения вторичного цементита и при 1147°С в аусте-
ните содержится 2,14 % углерода.
При tэ плавится эвтектика. Выше tэ чугун состоит из жидкого сплава и первичного цементита.
От tэ до tл5 происходит плавление первичного цементита. Выше tл5
чугун полностью находится в жидком состоянии.
При охлаждении до tл5 чугун находится в жидком состоянии. При tл5
начинается кристаллизация первичного цементита. От tл5 до tэ (1147°С)
происходит кристаллизация первичного цементита и чугун состоит из жидкого сплава и первичного цементита. При tэ чугун состоит из первич-
ного цементита и жидкого сплава эвтектического состава, т. е. содержаще-
го 4,3 % углерода, который, кристаллизуясь при этой температуре, образу-
ет ледебурит, состоящий из цементита и аустенита с содержанием 2,14 %
углерода.
72
Ниже tэ превращение претерпевает только ледебурит, а первичный цементит не изменяется. Превращение в ледебурите такое, как описано выше при рассмотрении доэвтектического и эвтектического чугуна, т. е. от tэ до Аr1 внутри ледебурита выделяется вторичный цементит и чугун со-
стоит из ледебурита и первичного цементита.
При Аr1 внутри эвтектики аустенит превращается в перлит. Ниже Ar1
чугун состоит из ледебурита и первичного цементита (рис. 3.3, в).
КОНТРОЛЬНЫЕ ВОПРОСЫ
1. Какие фазы образуются в метастабильной системе железо-углерод?
Дать их характеристику.
2.Напишите эвтектическую и эвтектоидную реакции системы FeFe3C. Какие структурные составляющие при этом образуются?
3.Что такое эвтектоидная сталь, какова ее структура?
4.Какие стали являются заэвтектоидными, какова структура этой ста-
ли?
5. Что такое чугун и как подразделяются чугуны по содержанию угле-
рода?
6.Структура чугунов: 2,5 %С, 3,8 %С, 4,3 %С, 5 %С?
7.Как меняется структурный и фазовый состав сплавов в зависимости от содержания углерода? Как это влияет на свойства?
8.Что такое цементит первичный, вторичный?
9.Какие примеси могут присутствовать в составе стали?
73
4.МЕТАЛЛЫ И СПЛАВЫ В МАШИНОСТРОЕНИИ
4.1.Общие сведения о классификации и получении сталей
Среди конструкционных материалов наиболее распространенным ма-
териалом, обладающим универсальными свойствами, является сталь.
Сталь представляет собой сплав железа с углеродом, количество которого оказывает существенное влияние на прочность стали. Содержание углеро-
да колеблется от 0,03 до 2,14%. К конструкционным относятся стали, со-
держащие до 0,9% углерода. По современной классификации к конструк-
ционным сталям относятся стали, прокатываемые на круг, квадрат, шести-
гранник, полосу и лист, используемые для изготовления деталей машин.
Конструкционные стали по химическому составу согласно современ-
ной классификации подразделяются на углеродистые и легированные.
Конструкционные стали могут быть:
·низкоуглеродистые С<=0,09-0,25%;
·среднеуглеродистые С<=0,25-0,45%;
·высокоуглеродистые С<=0,45-0,75%.
Легированные стали условно подразделяют:
·на низколегированные с содержанием легирующих элементов
2,5-5%;
·среднелегированные – до 10%;
·высоколегированные – более 10%.
В состав углеродистых сталей помимо углерода, определяющего ме-
ханические свойства, входят также остаточные количества раскисляющих элементов марганца (до 1%) и кремния (до 0,8%), а также попутные эле-
менты – сера и фосфор, являющиеся в большинстве случаев вредными примесями (кроме автоматных и особых легированных сталей). Сера вы-
зывает в сталях красноломкость, фосфор – хладноломкость, ухудшая тех-
нологические и эксплуатационные свойства металла. Поэтому одной из
74
основных задач сталеплавильных процессов является максимально воз-
можное удаление серы и фосфора.
В углеродистых и легированных сталях всегда находятся растворяю-
щиеся в жидком металле газы – кислород, азот и водород, которые также ухудшают качество металла, особенно легированного. При выплавке стали наряду с удалением серы и фосфора принимаются технологические меры также по уменьшению растворения газов, а в отдельных случаях проводит-
ся специальная обработка жидкого металла (вакуумирование, продувка инертными газами, обработка синтетическими шлаками). В сталях всегда присутствуют переходящие из сырья остаточные элементы (медь, хром,
никель и др.), содержание которых в углеродистых и многих легированных сталях регламентируется.
В зависимости от содержания углерода и других элементов и пре-
дельного содержания вредных примесей и остаточных элементов углеро-
дистые стали подразделяются на стали обыкновенного качества и качест-
венные конструкционные.
Всостав легированных сталей помимо углерода и других остаточных
ипопутных элементов целенаправленно вводится один или несколько легирующих элементов (хром, никель, молибден, марганец, кремний и др.)
для придания металлу прочностных, пластических и других технологиче-
ских и эксплуатационных свойств. В зависимости от количества введен-
ных легирующих элементов легированные конструкционные стали под-
разделяются на низколегированные (до 2,5% от веса), среднелегированные
(от 2,5 до 10%) и высоколегированные (от 10 до 50%).
Легированные стали подразделяются на группы, наименование кото-
рых отражает входящие в ее состав основные легирующие элементы. Ле-
гирующие элементы обозначаются буквами и цифрами, характеризующи-
ми их примерный химический состав. При этом если содержание элемента в стали не превышает 1%, то в обозначении марки стали этот элемент
75
обозначается соответствующей ему буквой, обозначающей этот элемент,
ставится цифра примерного среднего его содержания.
В зависимости от процесса выплавки сталь подразделяют на марте-
новскую, бессемеровскую, конвертерную и электропечную. Углеродистая сталь обыкновенного качества выплавляется в мартеновских печах, бессе-
меровских конверторах (в настоящее время этот процесс уже не применя-
ется) и кислородных конверторах, а углеродистая качественная, низколе-
гированная и среднелегированная – в мартеновских и электросталепла-
вильных печах, а в последние годы – и в кислородных конверторах. Высо-
колегированные стали выплавляются только в электросталеплавильных печах и при специальных переплавах. Конструкционные стали особо вы-
сокого качества выплавляются в последние годы в индукционных вакуум-
ных печах, а также методами вакуумно-дугового, электрошлакового, элек-
тронно-лучевого и плазменного переплавов.
По степени раскисленности (степени связанности кислорода в жидкой стали) углеродистые стали обыкновенного качества и качественные конст-
рукционные подразделяются на спокойные, кипящие и полуспокойные.
Развитие сортамента конструкционных сталей во многом определяет эксплуатационные характеристики многих машин, оборудования и метал-
локонструкций, создает предпосылки для разработки новых, более эффек-
тивных образцов техники, обеспечивает более экономное и рациональное использование металла в народном хозяйстве, является важным фактором снижения материалоемкости изделия и конструкций из металла, повыше-
ния эффективности общественного производства. В связи с этим работы по созданию новых марок конструкционных сталей в нашей стране и за рубе-
жом ведутся постоянно. Развиваются способы улучшения качественных характеристик выплавляемых сталей, применяются многообразные леги-
рующие элементы, новые, более эффективные их сочетания и способы ввода в жидкий металл.
76
Основным направлением является постоянное расширение марочного сортамента конструкционных сталей, создание технологических и экс-
плуатационных свойств, наиболее полно отвечающих конкретным услови-
ям применения и службы металла. Развитие марочного сортамента конст-
рукционных, а также сталей других типов неразрывно связано с развитием стандартизации в нашей стране.
На конструкционные стали и металлопродукцию существуют два вида нормативной документации: базовые государственные стандарты (ГОСТ),
порядковые номера которых начиная с 1941 г. не меняются при периоди-
ческом их пересмотре, а также государственные стандарты на группу спе-
циальных сталей, применяющихся для конкретных целей; технические условия стали, которые применяются в ограниченных количествах, в од-
ной отрасли для узкой цели или производятся в опытно-промышленном порядке. Марочный состав сталей, а также их химический состав с разви-
тием техники и технологии металлургического производства и постоянно растущих требований металлопотребляющих отраслей постоянно пере-
сматриваются, корректируются в сторону повышения качества и расшире-
ния марочного сортамента.
4.2. Влияние углерода и постоянных примесей на свойства сталей
Углерод оказывает определяющее влияние на свойства стали. В рав-
новесном состоянии сталь представляет смесь феррита и цементита, в
которой количество последнего увеличивается пропорционально содержа-
нию углерода.
Феррит малопрочен и пластичен. Цементит твѐрд и хрупок. В связи с этим по мере повышения концентрации углерода повышается прочность и твердость, снижаются пластичность и вязкость стали (рис. 4.1).
На механические свойства заэвтектоидных сталей сильное влияние оказывает вторичный цементит, образующий хрупкий каркас вокруг зерен
77
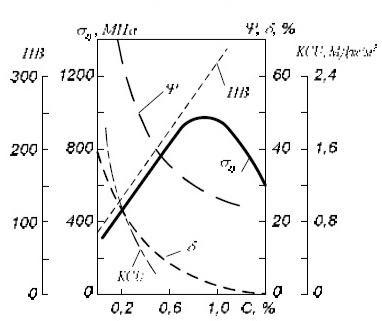
перлита. Под нагрузкой этот каркас преждевременно разрушается, вызывая снижение прочности, пластичности и вязкости. Из-за этих недостатков заэвтектоидные стали применяют после специального отжига со структу-
рой зернистого перлита.
Влияние углерода еще более значительно при неравновесной структу-
ре. После закалки прочность и твердость резко возрастают с увеличением содержания углерода. При низком отпуске эти свойства полностью опре-
деляются концентрацией углерода в твердом растворе.
Рис. 4.1. Влияние углерода на механические свойства отожженных сталей
С увеличением содержания углерода снижается технологическая пла-
стичность – способность деформироваться в горячем и особенно в холод-
ном состояниях. Для сложной холодной штамповки содержание углерода ограничивают 0,1 мас.%.
Постоянные примеси в стали: марганец, кремний, сера, фосфор, а
также газы: кислород, азот, водород.
Содержание Mn и Si обусловлено процессом выплавки стали. Для то-
го чтобы освободиться от FeO (закиси железа), образующегося при плавке
78
и ухудшающего свойства стали, вводят Mn и Si. Этот процесс называют раскислением стали. При этом содержание Mn не должно превышать 0,8
мас.%, a Si – 0,4 мас.%. Содержание Mn и Si в таком количестве практиче-
ски не оказывает влияния на механические свойства углеродистых сталей
(оказывается незначительное упрочняющее действие). Более высокое со-
держание этих элементов существенно изменяет свойства стали.
Сера и фосфор являются вредными примесями. Содержание более чем
0,05 мас.% каждой из этих примесей резко ухудшает качество стали.
Вредное действие S связано с явлением красноломкости стали, т. е. с
повышенной хрупкостью (образованием трещин) в горячем состоянии при ковке и прокатке. Красноломкость стали является следствием того, что S,
соединяясь с Fe, образует эвтектику, температура плавления которой
988°С (значительно ниже температуры плавления стали). При кристалли-
зации эвтектика располагается по границам зерен, а при нагревании стали для ковки или прокатки эвтектика плавится, связь между зернами наруша-
ется, сталь становится хрупкой. Красноломкость ослабляется введением
Mn, образующего с S сульфид марганца, температура плавления которого
1620°С.
Вредное действие Р заключается в резком увеличении хрупкости ста-
ли при обычной температуре. Это явление, называемое хладноломкостью,
возникает в результате того, что Р, растворяясь в феррите, существенно увеличивает его хрупкость при обычных температурах. Вредное влия-
ние Р оказывается более значительным при повышении содержания С.
Однако, например, для облегчения обрабатываемости автоматных сталей
(с содержанием до 0,3 мас.% С) допускается повышенное содержание Р (до
0,15 мас.%) и S (до 0,2 мас.%).
Газы Н, О, N содержатся в стали в небольших количествах в зависи-
мости от способа производства. Они ухудшают свойства стали снижая прочность и пластичность. При вакуумной плавке уменьшается содержа-
ние Н, N и О, а также неметаллических примесей.
79