
10790
.pdf10
Горе́ние — сложный физико-химический процесс превращения компонентов горючей смеси в продукты сгорания с выделением теплового излучения, света и лучистой энергии. Иногда горение определяют как экзотермическое окисление.
Минимальное процентное соотношение газов или паров с воздухом, при котором наступает условие взрыва, называется нижним пределом взрываемости (НПВ).
Максимальное процентное соотношение газов или паров в смеси с воздухом, при котором существует условие взрыва, называется верхним пределом взрываемости (ВПВ). Газ или пар считается взрывоопасным, если его относительная концентрация находится между нижним и верхним пределами взрываемости.
С точки зрения взрывобезопасности безопасная концентрация газов и паров в воздухе производственных помещений не должна превышать 30 % от НПВ.
Значения пределов взрываемости для наиболее распространенных газов и паров, образующихся на промышленных предприятиях приведены в табл. 2.1
Таблица 2.1
№ |
Наименование вещества |
НПВ, % |
|
ВПВ, % |
п/п |
|
|||
|
|
|
|
|
1. |
Угарный газ СО |
16,1 |
|
73,4 |
|
|
|
|
|
2. |
Этиловый спирт (этанол) С2Н5ОН |
4,0 |
|
13,6 |
|
|
|
|
|
3. |
Аммиак NH3 |
16,5 |
|
26,8 |
|
|
|
|
|
4. |
Ацетон СН3СОСН3 |
3,0 |
|
9,0 |
|
|
|
|
|
5. |
Бензин CnHm |
2,5 |
|
4,8 |
|
|
|
|
|
6. |
Водород Н2 |
4,0 |
|
75,0 |
|
|
|
|
|
7. |
Метан СН4 |
6,0 |
|
13,9 |
|
|
|
|
|
|
Для определения пределов взрываемости Xсм |
паровоздушной смеси |
нескольких компонентов применяют закон Ле Шателье:
|
|
|
|
|
|
|
|
|
|
11 |
Хсм |
= |
|
|
|
100% |
|
|
|
|
|
|
|
|
|
|
|
|
|
|
||
|
Р |
+ |
Р |
+...+ |
Р , |
(2.2) |
||||
|
|
|
1 |
2 |
n |
|
|
|
||
|
Х1 |
Х2 |
Хn |
|
||||||
|
|
|
|
|
|
где P1, P2,…, Pn – относительные (процентные) концентрации компонентов в смеси;
X1, X2,…, Xn – пределы взрываемости компонентов смеси.
Пыль.
Под термином пыль понимают материальную систему, состоящую из мельчайших частичек твердого вещества, рассеянных в газообразной среде. Такие системы называют дисперсными. Дисперсные системы состоят из дисперсной фазы (мельчайшие твердые частицы) и дисперсионной среды (газ, воздух). Когда частицы пыли находятся во взвешенном состоянии в воздухе, их называют аэрозолями. Когда масса газовой составляющей мала (осаждение, скопление пыли), смесь называют аэрогелем.
Источником пыли являются технологические процессы, связанные - с дроблением, шлифовкой, механической очисткой поверхностей
деталей, обработкой древесины и др. При некоторых способах окраски выделяется “красочная пыль” (аэрозоль).
Постоянным выделением пыли сопровождаются производства на следующих предприятиях:
1.текстильной промышленности;
2.деревообрабатывающей промышленности;
3.горнорудной промышленности;
4.зерноперерабатывающей промышленности;
5.металлообрабатывающей промышленности.
По действию на организм человека различают:
- ядовитую пыль (напр. свинцовая, ртутная), которая вызывает отравления с тяжелыми последствиям;
12
- неядовитую (древесная, песчаная, абразивная), которая не вызывает острых отравлений, но при длительном вдыхании может приводит к различным заболеваниям легких.
Пыль от веществ легко сгорающих в воздухе (уголь, мука, сахар, табак и др.) взрывоопасна. Это является следствием очень развитой суммарной поверхности размельченного вещества, что приводит к многократному ускорению процессов обмена молекулами между дисперсной средой и фазой. Из-за возросшей поверхности контакта во много раз увеличивается электроемкость частиц, что в результате, при определенной концентрации пыли в воздухе или ином газе может привести к взрыву.
Запыленность воздуха обычно оценивают в мг/м3.
2.1.Очистка воздуха от пыли
Вцелях защиты атмосферного воздуха от вент выбросов вытяжной воздух от оборудования, выделяющего пыль предварительно очищают. В целях сокращения энергозатрат на подогрев приточного воздуха в системах вентиляции часто используют рециркуляцию внутреннего воздуха. В этом случае также необходима тщательная очистка отработанного воздуха от пыли.
Взависимости от принципа действия все пылеулавливающие устройства могут быть разделены на следующие основные группы:
1. Пылеосадочные камеры.
Принцип действия основан на осаждении пыли под действием силы тяжести.
2. Циклоны (инерционные пылеуловители).
Принцип действия основан на использовании сил инерции при изменении направления движения потока запыленного воздуха. Применяют как одиночные, так и “батарейные”.
3. Тканевые, сетчатые, волокнистые фильтры.
Загрязненный воздух в этих устройствах проходит по каналам с изменением направления движения через слой фильтрующего материала
13
(ткань, бумага, металлические сетки, предварительно обработанные маслом и т.п.). Отделение пыли в фильтрах происходит за счет инерционных сил, гравитационных сил диффузионного осаждения.
4. Электрофильтры.
Основным элементом электрофильтров являются электроды с высоким напряжением, сообщающие пылевидным частицам положительный заряд, осадительные электроды, на поверхности которых оседают заряженные частицы и бункеры-пылесборники.
Независимо от принципа действия пылеуловители бывают “сухими” и “мокрыми”. Смачивание фильтрующей поверхности применяют для увеличения эффективности очистки. С этой целью применяются вода (мокрые циклоны) или масло (масляные ячейковые и сетчатые фильтры).
Также для повышения эффективности применяют комбинированную очистку, т.е. устанавливают последовательно различные по принципу действия фильтры.
Большинство фильтров характеризуется следующими основными показателями:
1.степень очистки (к.п.д.), %;
2.производительность (пропускная способность), м3/ч;
3.гидравлическое сопротивление, Па;
4.энергозатраты, кВт-ч/м3;
5.стоимость процесса очистки м3 (или 1000 м3) воздуха.
Для тканевых фильтров дополнительно обычно указывают их предельную пылеемкость – количество осажденной пыли, повышающей сопротивление
проходу воздуху до определенных значений.
Степенью очистки называют отношение массы пыли, улавливаемой очищающим устройством, к первоначальной массе пыли, выраженное в процентах. Степень очистки можно также выразить через разность начальной
С1 , мг/м3, и конечной С2 концентраций пыли |
|
η = (С1 – С2 / С1) 100 % . |
(2.3) |
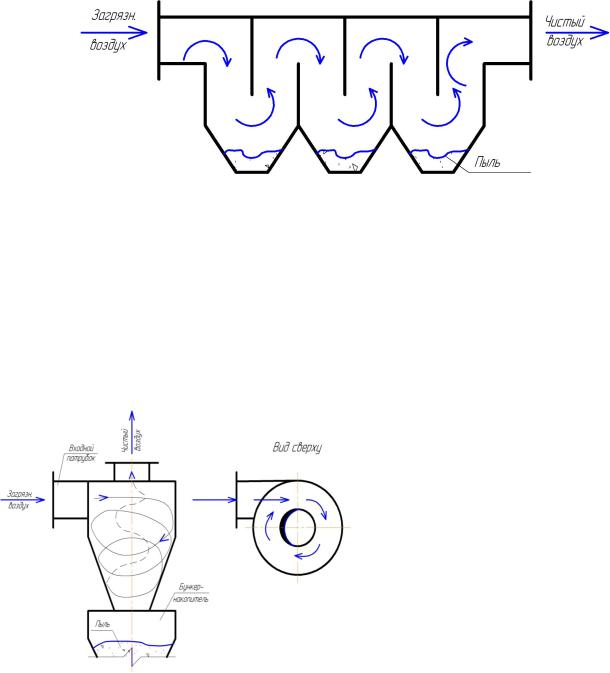
14
Рис. 2.1 Принципиальная схема пылеосадочной камеры
Достоинством пылеосадочных камер является простота эксплуатации, надежность и продолжительный срок эксплуатации. Применяются чаще в комплексе с другими фильтрами как первая ступень (грубой) очистки от крупных фракций пыли.
Циклоны применяются для очистки вытяжного воздуха с высоким начальным пылесодержанием или содержанием взвешенных крупнодисперсных частиц, например, для очистки воздуха, удаляемого от деревообрабатывающих станков.
Рис. 2.2 Принципиальная схема циклона
Достоинством циклонов является простота устройства и эксплуатации, надежность работы, высокая степень очистки.
Опыт эксплуатации и испытаний различных типов циклонов показал, что для обеспечения эффективной очистки воздуха от взвешенных частиц пыли его скорость перед входным патрубком должна быть в пределах vвх = 10…25 м/с. Минимальное значение обусловлено удержанием частиц пыли во взвешенном
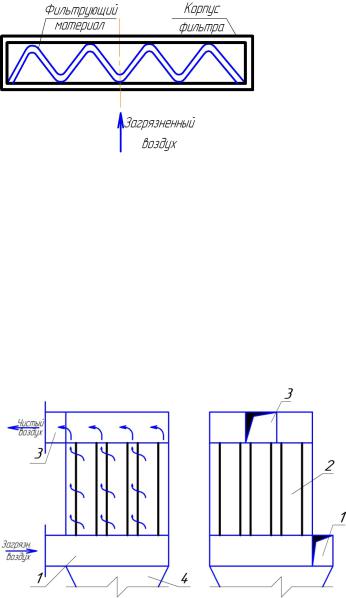
15
состоянии. Максимальное – из-за резкого возрастания гидравлического сопротивления проходу воздуха (пропорционально квадрату скорости) при незначительном повышении степени очистки.
В тканевых фильтрах основным способом является инерционное осаждение частиц пыли в волокнах ткани. Фильтрующий материал сшивают в виде мешков, рукавов или натягивается на каркас.
Для увеличения площади контакта фильтрующую поверхность выполняют зигзагообразно.
Одними из наиболее распространенных являются рукавные тканевые фильтры с устройством автоматического встряхивания для периодической очистки фильтрующего материала.
1 – входной патрубок;
2 – фильтрующий материал (рукав);
3 – выходной патрубок;
4 – бункернакопитель.
Рис. 2.4 Схема рукавного фильтра Достоинством тканевых фильтров является высокая (до 99 %) степень
очистки.
Недостатком – не все виды фильтрующего материала позволяют очищать воздух с повышенной влажностью или с температурой, при которой возможна конденсация водяных паров. Это приводит к заполнению пор фильтра и резкому снижению фильтрующей способности.
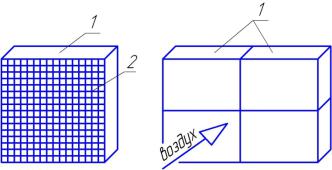
16
1 – ячейка фильтра;
2 – фильтрующий элемент.
Рис. 2.5 Схема масляного фильтра
В качестве фильтрующего заполнителя в масляных фильтрах применяют металлические сетки, стеклянное волокно или тонкостенные металлические кольца покрытые тонким слоем масла. Применяются масляные фильтры для тонкой очистки воздуха (степень очистки до 99 %). Как правило, фильтр набирается из отдельных ячеек, комплектующихся в зависимости от производительности и размеров в общий каркас в горизонтальной или вертикальной плоскости.
2.2. Очистка воздуха от вредных газов и паров
Состав промышленных вентиляционных выбросов отличается большим многообразием видов газообразных веществ и их свойств. Это связано с широкой номенклатурой используемого технологического оборудования, сырья и физико-химических процессов, проводимых при изготовлении продукции.
Вытяжной воздух термических цехов, оборудованных нагревательными печами на жидком и газообразном топливе, содержит пары аммиака, цианистого водорода HCN и других вредных веществ. Гальванические цеха и цехи механической обработки металлов используют при травлении поверхности металла растворы кислот - серной H2S04, соляной НС1, азотной
HNO3 и плавиковой HF.
Вентвыбросы производств неметаллических изделий из стеклопластика, пластмасс, полимеров и лакокрасочных цехов также значительно загрязняют
17
окружающую среду. В атмосферу с выбрасываемым воздухом поступают пары растворителей, красок, SO2, СО, пары бензина, толуола, ксилола, изопропилового спирта и др.
Сырьем для предприятий химической промышленности служат нефть, природный газ, попутные газы, которые образуются, например, при коксовании углей на металлургических предприятиях, разнообразные химические вещества и соединения. К основным выбросам относятся С02, окислы азота NOx, сернистый ангидрид SO2, аммиак NH3 , сероводород H2S и сероуглерод CS2, хлористые, фтористые соединения и др.
Выбросы нефтеперерабатывающей и нефтехимической промышленности содержат большое количество углеводородов и сероводорода. Заводы синтетического каучука выбрасывают в атмосферу стирол C8H8, толуол С6Н5СН3, ацетон (СH3)2СО и др. очень высокотоксичные вещества.
Выбросы могут быть нагреты до высоких температур, в них могут присутствовать аэрозольные частицы - пыль, сажа. Поступая в атмосферный воздух, газообразные вещества взаимодействуют друг с другом и могут превращаться в другие соединения, иногда даже более вредные для организма, чем исходные. Интенсивность выбросов по времени не всегда постоянна, изменяется концентрация в них различных вредных веществ и т. д. Зачастую загрязнения многокомпонентны и их необходимо подвергать различным методам обезвреживания.
Поэтому задача проектирования очистки воздуха от газовых загрязнений требует специальных знаний различных дисциплин, в первую очередь, химической технологии. Необходимо знать свойства реагирующих веществ и основные методы улавливания газовых загрязнений, учитывать особенности режимов работы существующего очистного оборудования и техникоэкономические показатели разных вариантов очистки.
Абсорбция газовых примесей
Некоторые жидкости при контакте с многокомпонентной газовой средой способны избирательно извлекать из нее отдельные ингредиенты и поглощать
18
их - сорбировать. Это свойство жидкостей используется при абсорбции* газовых примесей из вентвыбросов.
Вентиляционный воздух и примеси, которые находятся в газовой фазе и при абсорбции не переходят в жидкую фазу, называют газом-носителем.
Жидкость, в которой происходит растворение абсорбируемых компонентов, называют абсорбентом (поглотителем или растворителем), а газ, переходящий в абсорбент, т.е. поглощаемый компонент - абсорбтивом.
Физическая сущность процесса абсорбции объясняется так называемой
пленочной теорией, согласно которой при соприкосновении жидких и газообразных веществ на границе раздела фаз «газ-жидкость» образуется жидкостная и газовая пленки. Растворимый в жидкости компонент газовоздушной смеси проникает путем диффузии сначала через газовую пленку, а затем, сквозь жидкостную пленку, и поступает во внутренние слои абсорбента.
Для диффузии необходимо, чтобы концентрация растворяемого компонента в газовоздушной смеси превосходила его концентрацию в жидкости. Чем менее насыщена жидкость (раствор), тем больше она поглощает газа.
Процесс, завершающийся растворением абсорбтива в поглотителе, называют физической абсорбцией. При физической абсорбции происходит физическое растворение абсорбируемого компонента в растворителе, при этом молекулы абсорбента и молекулы абсорбтива не вступают между собой в химическое взаимодействие.
Иногда растворяющийся газ вступает в химическую реакцию
непосредственно с самим растворителем, образуя новые химические соединения в жидкой фазе. Процесс, сопровождающийся химической реакцией между поглощаемым компонентом и абсорбентом, называют химической абсорбцией (хемосорбцией).
Интенсивность перехода загрязнителя из газовой фазы в жидкую (растворимость газа) зависит от температуры и давления компонентов, а также
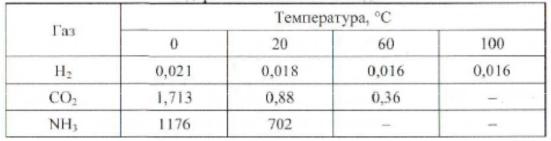
19
от способа организации контакта фаз. Влияние давления достаточно хорошо выражается законом Генри: при постоянной температуре растворимость газа в растворителе прямо пропорциональна давлению этого газа над раствором.
Как правило, растворение газов в жидкости происходит с выделением тепла и с уменьшением объема, поэтому в соответствии с принципом ЛеШателье, при повышении температуры их растворимость снижается. Эту зависимость иллюстрирует табл. 2.2, где приведены данные по содержанию (в нормальных литрах) некоторых газов в 1 л воды при стандартном давлении 101 300 Па:
Таблица 2.2
Содержание газов в 1 л воды
Внекоторых случаях, когда растворение сопровождается не выделением,
апоглощением тепла, возрастание температуры приводит к увеличению растворимости газа.
Вкачестве абсорбента может использоваться любая жидкость, которая растворяет извлекаемый компонент. Это может быть вода, растворы аммиака, едких и карбонатных щелочей, солей марганца, этаноламины, суспензии гидрооксида кальция, оксидов марганца и магния, сульфат магния и другие вещества. Главное, чтобы растворитель отвечал ряду требований, среди которых: необходимая поглотительная способность (абсорбционная ёмкость), высокая селективность (избирательность) по отношению к поглощаемому компоненту, невысокая летучесть во избежание загрязнения очищаемого газа парами абсорбента, небольшая вязкость, способность к регенерации. Поглотитель должен быть термо- и химически устойчивым, не проявлять коррозионную активность, быть доступным и недорогим.