
02 BOPs / Woods D.R 2008 rules-of-thumb-in-Engineering-practice (epdf.tips)
.pdf
4.13 Ion Exchange 121
Weakly acidic cationic exchange resin, WAC, carboxylic; pH i 4; T I 100 hC; hydrogen or sodium form depending on regeneration preference; loading 3.5 eq/L of resin; good selectivity; greatest affinity for alkaline earth metals in the presence of alkalinity.
Strongly acidic cationic exchange resins, SAC, sulfonic; full range of pH, T
I 120 hC; hydrogen or sodium forms; loading 1.9 eq/L resin; high capacity, high activity.IonicsequenceBaiPbiSriCaiNiiMniBeiCd2+iCuiCoiZniMg. Weakly basic anionic resin, WBA: aromatic polyamine: pHI 7; T I 50 hC; chloride(more thermally robust) or OH form; loading 1.6 eq/L resin.
Strongly basic anionic exchange resins: SBA: Type I trimethyl amine: full range of pH; chloride (more thermally stable) or OH forms; loading 0.46 to 1 eq/L resin. Ions being exchanged must have a higher valence than ions in bed from regeneration [F].
For bioseparations: proteins usually have a charge in liquid solution. The magnitude and size of the charge depends on the pH and is zero at the zpc, the pH where the charge is zero. For example, the zpc for invertase is pH = 4.24. To separate a target species, identify the zpc, select a convenient pH different from the zpc and pick the exchange resin of the opposite charge. Operate the column at this pH to load the resin. Then, stop the flow, change the pH to the zpc and elute the target species.
Batch:
Fixed bed: Batch: size on cycle time: load, backwash/rinse, elute, standby. Try to match loading with off-line time. Load: loading feedrate 5–10 BV/h with loading time depends on the ratio of exchange capacity of the resin to the feed concentration of the target species. Usual ratio 10–100 corresponding to a loading time of 1.5–15 h. Backwash with a velocity to fluidize the bed for 1–10 BV (corresponding to about 1.5 h ). Eluent feedrate 1–3 BV/h for typically 8–20. Standby is typically 20 % of the backwash time. When the eluate is valuable, try to match the loading time with the backwash, eluate recovery and standby.
Feed flowrate: superficial velocity 1 to 15 L/m2 s; use 5 L/m2 s. Superficial velocity I 3 L/m2 s gives poor feed distribution. 5 to 10 BV/h; too deep a bed leads to excessive pressure drop; keep below 350 kPa. add 2.5 m to height to allow for bed support and head room for backwashing. Typical bed depths 1 to 5 m; usual industrial bed cross-section 5 m2.
Use fixed bed if I 20 L/s. Pressure, gravity, cocurrent, countercurrent, series, single bed or mixed bed. Gravity is economical where the BV i 80 m3.
Loading times and elution-regeneration times should be approximately equal. For WAC and WBA systems the backwash, regeneration and rinse cycle is 30 to
60 min.
Continuous:
Moving bed: Use if i 20 L/s.
Fluidized bed: Use if slimes or fine particles in feed, elution time i i IX time, eluant is expensive. Use 16 to 20 Mesh resin with superficial velocities of 40 L/m2 s. Try to operate at 50 to 200 % bed expansion. Related topics include adsorption-liquid, Section 4.12.

122 4 Homogeneous Separation
x Good Practice
Use an upstream degasser to remove carbonic acid.
x Trouble Shooting
Usual sources of trouble are change in ions in the feed, the multiport valves improperly seat so that feed or regenerant bypass into the effluent, clogged liquid distributors, clogged underdrains; degradation of the resin and faulty backwash. Organic fouling mainly affects anionic exchangers.
“Throughput capacity I design”: instrument error/increase in feed concentration/ less resin volume than design/regenerant concentration I design/regenerant volume I design, 0.5–3.5 L/s L of resin/regenerant flowrate I design/wrong regeneration ion/contamination of regenerant with high valence ions.
“In the spring, reduced flowrate through the unit demineralizing river water”: high concentration of particulates, clay in spring river water.
“In the summer for a unit demineralizing water, throughput of the cationic exchanger decreases, exchange capacity for calcium and magnesium decreases but the anionic exchanger is unaffected”: suspect ferric or high valency cation present in the feed.
“In the summer for a unit demineralizing river water, throughput of the anionic exchanger decreases, exchange capacity decreases but the cationic exchanger is unaffected”: suspect fertilizer runoff with phosphate, carbonic acid and high sulfate anions as contamination.
“Contamination in exit liquid i design”: instrument error/sampling error/on-line too long/faulty regeneration/[ fouled]*/[poisoned]*/high feed concentration of target ions/feed concentration of high valence co-ions.
“Dp i design”: dirt in feed/water from river in springtime/instrument error/temperature/resin void volume changes/inlet distribution system blocked/[resin degradation]* and backwashes into inlet/backwash rate too high/underbed blocked. [Fouling of the resin]* : iron and high valence ions/oil/mud/polyelectrolyte/calcium sulfate precipitate/silica/barium sulfate/carbonic acid/sulfate or phosphate/ organics/algae and bacterial fouling. More general causes of fouling are given in Section 1.12.
[Poison resin]*: cobalticyanide/polythionate/ferricyanides/complex humic acid/ color bodies in sugar juices.
[Resin degradation]*: ingress of oxidants/free chlorine in feed/temperature increase/[ fouled]*/[poisoned]*/corrosion products/[resin fines]*.
[Resin fines]*: thermal or physical shock/freeze/thaw.
WAC: “Alkalinity leakage during exhaustion cycle”: inadequate regeneration. “Hardness leakage during exhaustion cycle”: regeneration fault with calcium sulfate precipitation (if sulfuric acid is the regenerant).
SAC: “Sodium leakage”: inadequate regeneration: wrong concentration, wrong flowrate, wrong length of time.
“Hardness leakage during exhaustion cycle”: regeneration fault with calcium sulfate precipitation (if sulfuric acid is the regenerant).
WBA: “Mineral acid leakage”: under regenerated/upstream SAC malfunctioning.
“Sodium leakage, high pH and high conductivity”: SAC resins contaminated the bed.

4.15 Membranes and Membrane Configurations 123
“Silica problems”: series regeneration with SBA with pH falling below the isoelectric point of silica in the resin bed.
SBA: “Increase in silica leakage”: [resin degradation]*. “Leakage of target ions”: organic [ fouling]*.
“Low pH and high conductivity”: organic [ fouling]*. “Increase rinse quantities”: organic [ fouling]*.
“Low pH (5.5), increased conductivity, increase silica leakage, increase rinse volumes, loss of throughput capacity:” organic [ fouling]*.
“Product contamination”: leaking valves/crud left in storage tanks/crud left in dead legs in piping/corrosion products/unexpected chemical reactions/sampling fault/ analysis fault/unexpected solubility effects.
4.14
Foam Fractionation
Related topics include gas in liquid, Section 8.1.
x Area of Application
Solute feed concentration usually 1 ppm to 0.1 % with some applications up to 10 %. [10–3 to 10–9 mol]. The bulk/film volume ratio, d+ = 1.
x Guidelines
Surface concentration 1 to 5 mmol/m2 bubble area. Height to diameter 5:1 to 15:1. Usual liquid feed superficial velocity 0.1 to 1 L/s m2. Bubble diameter = 0.8 to 1 mm. Volumetric feedrate ratio of inlet gas to liquid flowrates: 4 to 7.5 dm3 gas/L liquid. Volumetric ratio of gas in foam to overhead liquid in draining foam: 100 to 250:1. Liquid in the foam/liquid in the feed = 6 to 12 % v/v; draining foam density 0.003 Mg/m3. Superficial gas velocity for foam drainage section 3 to 250 dm3/s m2. Scaleup based on constant superficial gas velocity.
x Good Practice
To remove ions, consider adding ionic surfactant.
4.15
Membranes and Membrane Configurations
Consider first the membranes: materials of construction, pore sizes and surface properties. Then consider options for operating membranes and the configurations for membranes: hollow fibers, tubes, flat sheets and spirals.

1244 Homogeneous Separation
4.15.1
Membranes
Membranes can be made of different materials, with different pore sizes and distribution of pore sizes and with different surface characteristics.
Different materials: In general, the materials are polymers, ceramics and sintered metals. Polymers can be divided into elastomeric (or rubbery) and glassy. Usual materials for liquid systems include polyethersulfone, polysulfone, cellulose acetate, and regenerated cellulose.
Membrane pore size and pore size distribution: The pore size can be reported as the average size of the pore (e.g., 5 nm) or according to the molar mass cut-off size, MMCO (and sometimes called the molecular weight cut off, MWCO). The MMCO is measured in daltons. The standard definition for membrane performance is based on 90 % rejection. That is, a 50 kDa membrane will reject up to 90 % of molecules having a molar mass of 50 kDa. For the complete rejection of a species, select a membrane with MMCO rated at 0.2 MM of the target species; i.e. 10 kDa membrane should reject 100 % of a 50 kDa species or select a pore size one order of magnitude smaller than that of the target species.
Based on pore size, membranes are described qualitatively as being nonporous, dense or homogeneous (with pore sizes around 1 nm); microporous (with pore sizes 0.001–20 mm) and macroporous (with pore sizes usually 100–500 mm).
Concerning the distribution of the pore size through the membrane, there are seven classes:
Symmetric: (where the pore size is uniform through the membrane; example, polyolefins, fluoropolymers, nylons with porosity as high as 85 % throughout membrane; sintered metals with porosity 25–30 %).
1.symmetric porous with long tubular pores or isoporous,
2.symmetric microporous,
3.symmetric non-porous or dense (homogeneous).
Asymmetric: (where the pore size differs through the membrane; this gives a small surface area/volume and therefore requires larger filter for a given flowrate. Some examples include ceramics that are most porous with 30–40 % porosity in the thin, membrane layer; and polymers, porosity in thin layer 1–9 %.).
4.asymmetric microporous top layer on porous but all the same polymer.
5.asymmetric nonporous (homogeneous) top layer on porous but all the same polymer.
6.asymmetric composite: non-porous (homogeneous) layer(s) of one material (example polyamide) on top of microporous support (polysulfone).
7.asymmetric composite skinned: thin layers of one material on top and bottom of membrane with porous or microporous support membrane in between.

4.15 Membranes and Membrane Configurations 125
Surface characteristics of the membranes: Two of the key characteristics are the hydrophobicity and the surface charge. Hydrophobic surfaces (or water-hating surfaces) are those where the critical surface tensions of the membrane material I the surface tension of water. Most polymers fall into this category, for example, polysulfones, polyolefins, polyvinylidine fluoride, PVDF, and carbon. By contrast, hydrophilic surfaces are preferentially wet by water and have critical surface tensions i the surface tension of water. Steel, alumina, cellulosic (temperature I 30 hC), polyacrylic, Nylon 66, polyethersulfone, metallic oxides, and ceramic surfaces usually fall into this class. Sometimes we treat the surface of the membrane to make it hydrophilic. Sintered materials are neither hydrophilic nor phobic.
The surface charge is related to whether the pH of the liquid is higher or lower than the zpc of the surface. For a pH i zpc, the surface charge is negatively charged; and vice versa. Some example zpc values are: alumina, 9.2; carbon, 3.8; polysulfone I 4.5; teflon (PTFE), 3; and silica, 1–2.
4.15.2
Membrane Operation and Configuration
Operation: can be operated deadend or cross flow : “batch” with 100 % recycle of retentate; “continuous” with recycle ratios 15–30/1 and purge and “multistage” where the purge from one stage becomes the feed of the next. Dead end: feed enters the membrane and can only leave through the membrane as permeate. Cross flow: feed flows through the membrane and as it does, some liquid passes through the membrane to create the permeate. Use cross flow especially for compressible cakes (e.g. biosystems). Batch: process: stop feed because the membrane performance has deteriorated or because the target concentrations or volumes of permeate or retentate have been achieved. Deteriorated membrane performance can be (i) because of a buildup of particulates, biological deposits (this can be corrected by backflushing with permeate or cleaning with detergents, acids or bases) or (ii) because the membrane needs to be replaced (the life of a membrane is 1–10 years depending on the operating conditions and the type of membrane). Configuration: Table 4.2 summarizes the characteristics of various configurations used for membranes: fine tubes or hollow fibers, channels and tubes; indicates which configuration can be made out of certain materials. For liquid systems, spiral wound (using cellulose acetate or polyamide membranes) is used extensively and hollow fibers (0.1–2 mm diameter, with polysulfone, polypropylene, nylon 6, or polyvinyl chloride membranes) are used when there are no particles present.
x Good Practice
Fouling is a major consideration. We can try to minimize fouling by supplying high shear at the surface, by selecting hydrophilic or hydrophobic surface properties depending on system; astutely selecting the operating conditions of temperature and pH, by coating the membrane with fouling resistant material and by op-
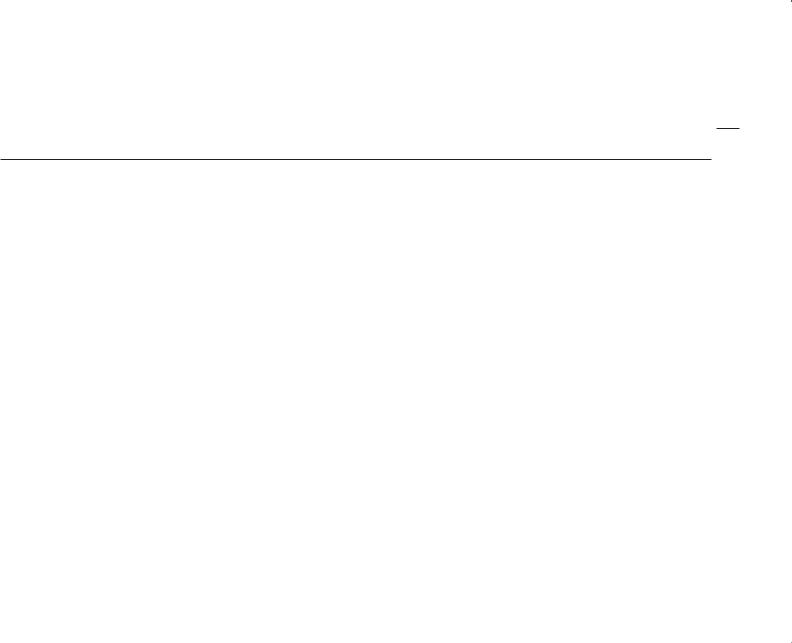
Table 4.2 Characteristics for various membrane configurations.
|
Tubes: fine hollow fibers to tubules |
|
Channel: |
|
|
|
Tubes |
|
||
|
RO type |
UF/microfilter |
|
Flat |
Flat |
Spiral |
Pleated |
Tubular |
|
|
|
|
|
|
|
sheet: |
sheet: |
wound |
sheet |
mono- |
|
|
|
|
|
|
plate/ |
plate/ |
|
|
lithic |
|
|
|
|
|
|
frame |
frame |
|
|
elements |
|
|
|
|
|
|
|
|
|
|
|
|
Diameter or |
0.01–0.03 |
0.02–0.1 |
0.5 |
1.1 |
0.2–0.4 |
1.2–2.5 |
0.75 or |
|
2.5–6 |
12–25 |
spacing, mm |
|
|
|
|
0.5–1 |
|
1.1 |
|
|
|
Length, cm |
|
I 100 |
|
|
45 |
45 |
|
|
|
1800 |
Reciprocal |
300–7500 |
0.9–6 |
|
|
0.8–30 |
|
|
|
|
0.001– |
volume, 1/cm3 |
|
|
|
|
|
|
|
|
|
0.0001 |
Holdup, L/m2 |
|
0.33 |
0.12 |
0.3 |
|
|
|
|
|
|
Flow conditions, |
|
|
laminar, |
|
|
turbulent |
laminar, |
|
|
turbulent, |
Reynolds no. |
500–3000 |
500–3000 |
500–3000 |
500–3000 |
500–3000 |
|
100–1300 |
|
|
Re i |
|
|
|
|
|
|
|
|
|
|
10000 |
Velocity, m/s |
|
0.01 –2.5 |
0.6–1 |
0.6–1 |
0.06–0.6 |
|
0.1–2 |
|
|
2–6 |
Velocity, m/s for |
|
|
|
1–5 |
|
1–3 |
0.2–0.5 |
|
|
5 |
cross flow |
|
|
|
|
|
|
|
|
|
|
Feed rate/surface |
|
|
|
|
0.25–0.5 |
|
0.25–0.5 |
|
|
1–5 |
area, L/s m2 |
|
|
|
|
|
|
|
|
|
|
Shear stress/ |
|
10–100 |
|
|
80–300 |
|
80–300 |
|
|
500–4000 |
length, 1/cm s |
|
|
|
|
|
|
|
|
|
|
Pressure drop |
|
30–130 |
|
|
70–1000 |
|
100–140 |
|
|
14–20 |
along the |
|
|
|
|
|
|
|
|
|
|
membrane, kPa |
|
|
|
|
|
|
|
|
|
|
|
|
|
|
|
|
|
|
|
|
|
Separation Homogeneous 4 126
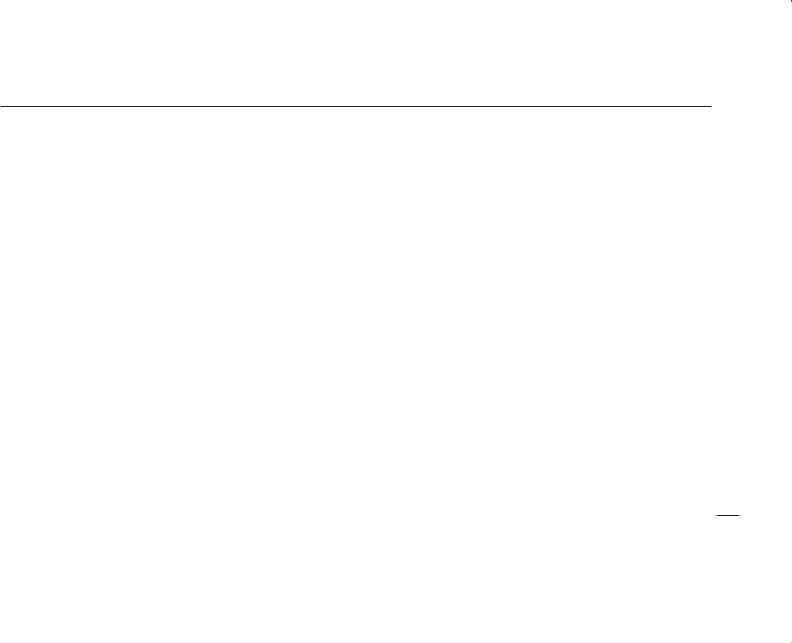
Table 4.2 Continued.
|
Tubes: fine hollow fibers to tubules |
|
Channel: |
|
|
|
|
Tubes |
|
||
|
RO type |
UF/microfilter |
|
Flat |
Flat |
Spiral |
Pleated |
Tubular |
|
|
|
|
|
|
|
|
sheet: |
sheet: |
wound |
sheet |
mono- |
|
|
|
|
|
|
|
plate/ |
plate/ |
|
|
lithic |
|
|
|
|
|
|
|
frame |
frame |
|
|
elements |
|
|
|
|
|
|
|
|
|
|
|
|
|
|
Area per unit |
6000 |
600–1200 |
500–1100 |
320–505 |
400–1000 |
|
650–1000 |
|
|
|
25–70 |
volume, m2/m3 |
|
|
|
|
|
|
|
|
|
|
|
Max size/unit, m2 |
|
1 |
0.05–5 |
|
0.02–0.07 |
|
8–22 |
|
|
|
0.4 |
Cellulosics |
yes |
yes |
yes |
yes |
yes |
yes |
yes |
yes |
no |
no |
no |
Polysulfone |
|
yes |
|
|
yes |
|
yes |
no |
no |
yes |
yes |
Acrylics |
|
yes |
|
no |
no |
|
no |
no |
no |
no |
no |
Fluoropolymers |
|
|
|
|
yes |
yes |
yes |
no |
no |
yes |
yes |
Ceramics |
|
yes |
yes |
yes |
depends |
|
|
|
yes |
yes |
yes |
Sintered metal |
|
|
|
|
|
|
|
|
no |
yes |
yes |
|
|
|
|
|
|
|
|
|
|
|
|
Configurations Membrane and Membranes 15.4
127

128 4 Homogeneous Separation
erating at subcritical fluxes. The critical flux is that flux (for a given set of feed concentrations, cross-flow rates, pH, temperature and ionic strength) below which fouling is negligible.
4.16 Membranes: Gas
x Area of Application
In general there are two applications: remove volatile organics (VOC) from air and separate permanent gases (such as nitrogen, hydrogen, carbon dioxide). Related VOC removal see Section 6.16 biofilters.
To remove organics from air, VOC: feed concentration is i 0.1 % v/v and the air flowrate is I 480 dm3/s. For lower concentrations use adsorption, Section 4.11; for higher flowrates use adsorption and condensation.
To separate permanent gases: feed concentration is 10 to 85 % and the flowrates range from 0.05 to 65 Nm3/s.
a = 1.4 to 4; gas feed concentration 5 to 75 % w/w; 75 to 90 % gas purity possible. Diameter of the target species: 0.1 to 1 nm.
x Guidelines
Membrane type: asymmetric: homogeneous or microporous; composite of a homogeneous polymer film on microporous substructure or symmetrical homogeneous or porous polymer film.
Driving force for the rate of separation: hydrostatic pressure concentration, partial pressure.
Membrane: nonporous membrane elastomer (example, rubbers and silicone rubbers) or glassy (example, polycarbonate, polyether imide, polyethersulfone, polyimide, polysulfone, polystyrene, polyvinyl chloride, polyvinyl fluoride and teflon.)
Pressure: i 0.7 MPa for separation of permanent gases. Temperature 0 to 60 hC.
For VOC removal from air, use elastomeric membranes (rubbery membranes). The membrane has a 0.1 to 1 mm skin layer on a 100 to 300 mm substrate. These membranes tend to have lower selectivities, higher permeabilities and are relatively impermeable to nitrogen. VOCs preferentially partition into the membrane phase. The permeability of organics tends to be 4 to 100 times higher than that of inert gases. For these membranes the selectivity increases with increasing boiling temperature of the species. The permeability increases 10 % per hC increase in temperature. Typical permeabilities for the organics are i 200 Ndm3 mm/s m2 MPa.
For the separation of permanent gases, use glassy membranes with higher selectivity and lower permeability.

4.18 Membranes: Electrodialysis 129
Typical permeance are:
–for hydrogen methane separation: 0.22 to 3.75 Ndm3/s m2 MPa.
–for carbon dioxide–methane separation: 0.075 to 1.5 Ndm3/s m2 MPa.
–for air separation: 0.003 to 1.9 Ndm3/s m2 MPa.
The temperature of the feed should be i 20 to 40 hC above the feed dew point. Configuration, see Section 4.15. Usually use flat or hollow fiber.
4.17
Membranes: Dialysis
x Area of Application
a= c21 D2/c11 D1 = 6 to 25 %; liquid feed concentration 2 to 25 % w/w; 99 % purity possible. c2 = concentration of solute in the feed. Diameter of the target species:
0.5 to 5 nm. D = diffusivity, c = concentration.
x Guidelines
Driving force for the rate of separation: concentration of target species. Membrane: symmetric microporous with 0.1 to 10 nm pore diameter. Hydrau-
lic permeability: 10–3 to 8 g/s m2 MPa. Membrane-solute permeability 0.05 to 9 m/s depending on the solute and the membrane. Dialysis transfer coefficient: 1 to 10 mm/s. Hollow fiber.
x Good Practice
Proteins denature at temperatures i 80 hC. Glass temperature for many polymers = 60 hC. Very high flowrates should be avoided since they can generate transmembrane pressure.
4.18
Membranes: Electrodialysis
x Area of Application
Diameter of the target species: 0.2–0.8 nm. Feed concentration I 20 % ionic. Feed range 0.005 to 5 %.
x Guidelines
Driving force for the rate of separation: electropotential.
Membrane: ion exchange, homogeneous or microporous polymer with positively or negatively charged fixed ions.
Hydraulic permeability: 10–3–8 g/s m2 MPa.
Pretreat feed until ferric I 0.3 mg/L, Mn I 0.1 mg/L, H2S I 0.3 mg/L. Temperature: i 10 and I 43 hC.
Optimum feed concentration 1000 to 5000 mg/L. Energy about 5.5 to 9 MJ/m3 product.

130 4 Homogeneous Separation
Pressure drop: horizontal stack 0.2 to 0.4 MPa; vertical stack 0.02 to 0.07 MPa. Configuration: flat, see Section 4.15.
4.19
Membranes: Pervaporation
x Area of Application
a = (ci,3/cj,3)/(ci,1/cj,1) where i is the target permeate species, j is the reject; 3 = permeate and 1 = feed, separates dissolved organics = 1.3–41. Particle diameter,
0.2 nm. Target concentration 5–20 % w/w but 0.1–10 % w/w for economical. Temperature I 120 hC.
x Guidelines
Driving force for the rate of separation: concentration gradient in the vapor pressure.
Membrane: asymmetric: homogeneous or microporous (polyacrylonitrile, cellulose acetate, polyamide, polysulfone,); composite of a homogeneous polymer film on microporous substructure (cellulose acetate, polyamide, polysulfone, polyimide, polyvinyl alcohol). Usual pore 0.1–0.2 mm.
0.1 mm PVA: water i i methanol i ethanol i other organics
Silicone rubber: methanol i ethanoli aldehydesi ketonesi i water; paraffins i olefins
Cellulose esters: aromatics i paraffins; olefins i paraffins; dienes i olefins; n-paraffins i branch; low molar mass paraffins i high molar mass paraffins.
Capacity/unit: feed I 1.5 kg/s. Feed pressure: atmospheric.
Feed temperature = close to the normal boiling temperature; usually 50–100 hC. Permeate conditions: pressure 0.5–2 kPa absolute with condenser tempera-
tures: –20 to +30 hC.
For dehydration, use a difference in partial vapor pressure at least 1 order of magnitude; the permeate flux doubles for an increase in temperature of 10 hC.
Permeate flux: depends on membrane but in the range 0.008–5 g/s m2. Configuration: see Section 4.15.
Spiral wound, transverse hollow fiber.
Use cross flow with recycle ratio 15–30/1. Criterion: 10 % of feed volume is permeate or purity of the permeate or retentate.
Membrane life, 2–4 years.
Cycle time: usually limited by life of membrane.