
3Detali_Mashin_Belan_Kharchenko
.pdf
|
|
106 |
∙ |
106 ∙ 189,1 |
|
|
|
= |
|
|
= |
|
= 12219. |
|
|
|
||||
П |
|
60 ∙ |
60 ∙ 257,8 |
|
||
|
|
|
что меньше срока службы всего редуктора Lh =31536 ч.
Проверяем другой, большего размера подшипник шариковый 313, с динамической грузоподъемностью С=92,3 кН; и статической Со=56,0 кН (см. табл. 3.2).
Определяем отношение: |
|
|
|
|
|
|
|
|||||||||||
|
|
|
|
|
|
|
|
|
1758,6 |
|
|
|
|
|||||
|
|
|
|
|
|
|
|
|
|
= |
|
|
|
= 0,031. |
||||
|
|
|
|
|
|
|
56000 |
|||||||||||
|
|
|
|
|
|
|
|
|
|
|
|
|||||||
|
|
|
|
|
0 |
|
|
|
|
|
|
|
|
|
|
|||
По табл. 8.1 этому отношению соответствует е = 0,23. |
||||||||||||||||||
Отношение: |
|
|
|
|
|
|
|
|
|
|
|
|
|
|
|
|
|
|
|
|
|
|
|
|
|
|
|
|
1758,6 |
|
|
|
|
||||
|
|
|
|
|
|
= |
|
|
|
|
|
|
= 0,215 < . |
|||||
|
|
∙ |
|
|
1 ∙ 8188,8 |
|||||||||||||
|
|
|
|
|
|
|
||||||||||||
|
|
|
|
|
|
|
|
|
|
|
|
|
|
|||||
По этому эквивалентная нагрузка остается прежней, т.е. :Р = |
||||||||||||||||||
11464,3 Н. |
|
|
|
|
|
|
|
|
|
|
|
|
|
|
|
|
|
|
Долговечность в млн. об.: |
|
|
|
|
|
|
||||||||||||
|
|
|
|
3 |
|
|
|
92300 |
3 |
|
||||||||
|
= |
|
|
= |
|
|
|
= 521,87. |
||||||||||
|
|
|
11464,3 |
|||||||||||||||
Долговечность в часах: |
|
|
|
|
|
|
|
|||||||||||
|
= |
106 ∙ |
= |
|
106 ∙ 518,87 |
= 33544 ч, |
||||||||||||
|
|
|
|
|
|
|
|
|
|
|
|
|||||||
П |
|
|
60 ∙ |
|
|
|
|
60 ∙ 257,8 |
|
|||||||||
|
|
|
|
|
|
|
|
что больше срока службы всего редуктора Lh = 31536 часов (см. формулу 2.5). Т.е. подшипник 313 пригоден для ведущего вала.
Ведомый вал
Наиболее нагруженная опора 4.
Внешняя осевая сила: Ra = Fa2 = 1758,6 Н. Радиальная нагрузка. Rr = RΣ4 =8096,5 Н.
1758,60 = 56000 = 0,031, = 0,23;
60
|
|
|
|
|
|
|
|
1758,6 |
|
|
|
||
|
|
|
|
|
= |
|
|
|
= 0,2172 < . |
||||
|
∙ |
|
|
1 ∙ 8096,5 |
|||||||||
|
|
|
|
|
|||||||||
|
|
|
|
|
|
|
|
||||||
Эквивалентная нагрузка :Р = 11464,3 Н. |
|||||||||||||
Долговечность в млн. об.: |
|
|
|
|
|||||||||
|
|
|
|
3 |
|
92300 |
3 |
|
|||||
= |
|
|
|
|
= |
|
= 521,87. |
||||||
|
|
11464,3 |
|||||||||||
Долговечность в часах: |
|
|
|
|
|||||||||
П = |
106 ∙ |
|
= |
106 ∙ 521,87 |
= 151794 ч. |
||||||||
60 ∙ |
60 ∙ 57,3 |
||||||||||||
|
|
|
|
Подшипник пригоден.
9 ПРОВЕРКА ПРОЧНОСТИ ШПОНОЧНЫХ СОЕДИНЕНИЙ
Шпоночное соединение образуют вал, шпонка и ступица насаженной на вал детали (зубчатого колеса, шкива, звѐздочки и т.п.). Предназначено для передачи вращающего момента между валом и ступицей.
Размеры сечений шпонок и длины шпонок, размеры шпоночных пазов (см. рис 9.1) выбирают по ГОСТ 23360-78 (см. табл. 9.1).
Напряжения смятия и условие прочности определяют по формуле:
см = |
|
2 ∙ ∙ 103 |
≤ см , |
(9.1) |
||
∙ |
− 1 |
∙ − |
||||
|
|
|
где Т - вращающий момент на соответствующем валу, Н*м, d - диаметр вала, мм; h - высота шпонки, мм; 1 - глубина врезания шпонки в паз вала, мм; - длина шпонки, мм; b - ширина шпонки, мм.
При стальной ступице допускаемые напряжения смятия принимают в интервале см =(110... 190) МПа, при чугунной ступице см = (70...
100) МПа. Большие значения следует принимать при спокойной работе, а так же при повышенной прочности материалов ступицы и шпонки (легированные марки сталей).
Напряжение смятия шпоночного соединения «быстроходный вал - ведущий шкив» (ремѐнной передачи):
61
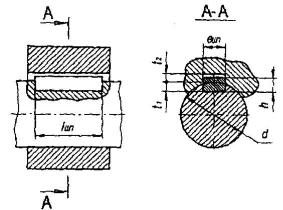
см = |
|
2 ∙ |
|
|
= |
2 ∙ 295,17 ∙ 103 |
= 91,4 МПа |
|
∙ |
− 1 ∙ |
− |
|
45 ∙ 9 − 5,5 |
∙ 55 − 14 |
|||
|
|
|
|
|||||
|
|
< |
см |
= 150 МПа. |
|
|
Условие прочности выполнено.
Рис. 9.1. Шпоночные соединения с призматическими шпонками Таблица 9.1
Шпонки призматические (ГОСТ 23360-78)
Диаметр ва- |
Сечение шпонки |
Глубина паза |
Длина |
|||
|
|
Вала, t1, |
Ступицы, |
шпонки, l, |
||
ла, d, мм |
b, мм |
h, мм |
||||
мм |
t2, мм |
мм |
||||
|
|
|
||||
Св. 12 до 17 |
5 |
5 |
3 |
2,3 |
10-56 |
|
» 17 » 22 |
6 |
6 |
3,5 |
2,8 |
14-70 |
|
» 22 » 30 |
8 |
7 |
4 |
3,3 |
18-90 |
|
» 30 » 38 |
10 |
8 |
5 |
3,3 |
22-110 |
|
» 38 » 44 |
12 |
8 |
5 |
3,3 |
28-140 |
|
» 44 » 50 |
14 |
9 |
5,5 |
3,8 |
36-160 |
|
» 50 » 58 |
16 |
10 |
6 |
4,3 |
45-180 |
|
» 58 » 65 |
18 |
11 |
7 |
4,4 |
50-200 |
|
» 65 » 75 |
20 |
12 |
7,5 |
4,9 |
56-220 |
|
» 75 » 85 |
22 |
14 |
9 |
5,4 |
63-250 |
|
» 85 » 95 |
25 |
14 |
9 |
5,4 |
70-280 |
62

Напряжение смятия шпоночного соединения «тихоходный вал – зубчатое колесо»:
см = |
|
|
2 ∙ 2 |
|
= |
2 ∙ 1288,4 |
= 481,2 МПа |
|
|
∙ |
− |
∙ − |
70 ∙ 12 − 7,5 ∙ 37 − 20 |
||||
|
|
|
||||||
|
2 |
|
1 |
|
|
|
|
|
|
|
|
> |
см = 150 МПа. |
|
Условие прочности не выполнено.
Необходимо установить на валу две шпонки под углом 1800 между ними и увеличить длину шпонки до l=50 мм. Тогда:
2 ∙ 1288,4см = 2 ∙ 70 ∙ 12 − 7,5 ∙ 50 − 20 = 136,3 МПа < см = 150 МПа.
В этом случае условие прочности «тихоходный вал - зубчатая муфта» выполнено.
10 ВЫБОР МУФТ
Муфтами приводов называют устройства, соединяющие валы совместно работающих агрегатов и передающие вращающий момент.
По экономическим и технологическим соображениям машины обычно выполняют из отдельных узлов (агрегатов), которые соединяют муфтами. Однако точная установка валов таких агрегатов невозможна изза ошибок изготовления и монтажа, установки агрегатов на деформируемом (нежестком) основании, расцентровки валов в результате тепловых деформаций корпусов агрегатов при их работе, а также из-за упругих деформаций валов под нагрузкой.
В проектируемых приводах с учѐтом особенностей эксплуатации, как правило, применяют компенсирующие разъѐмные муфты нерасцепляемого класса в стандартном исполнении. Следовательно, из имеющихся нормативных документов необходимо подобрать наиболее подходящий для данных условий тип муфты и еѐ габаритные и присоединительные размеры.
Муфты выбирают по большему диаметру концов cоединяемых валов и номинальному моменту, передаваемому муфтой. После выбора муфты записывают еѐ условное обозначение, основные технические параметры и выполняют эскиз муфты.
Для компенсации перечисленных выше погрешностей на выход-
ном конце ведущего вала редуктора устанавливают муфту упругую втулочно-пальцевую, (ГОСТ 21424-93).
63
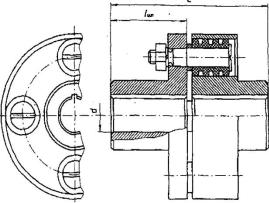
Муфты этого типа применяют в приводе от электродвигателя и в других случаях для валов диаметрами 9... 160 мм, при вращающих моментах 6,3. . . 16000 Нм. Упругие муфты за счет использо- • вания своих упругих силовых элементов способны на только компенсировать радиальные и угловые смещения, но и демпфировать колебания, амортизировать толчки и удары.
На выходном конце ведомого вала устанавливают муфту зуб-
чатую (ГОСТ 5006-83). Зубчатые муфты обладают большой несущей способностью и надежностью из-за значительного числа зубьев, передающих вращающий момент, а также хорошо работают лри высоких частотах, вращения.
Основные параметры муфты упругой втулочно-пальцевой и муфты зубчатой приведены соответственно в тал. 10.1 и табл. 10.2.
L
Рис. 10.1. Муфта упругая втулочно-пальцевая
|
|
|
|
|
|
|
|
Таблица 10.1 |
|
|
Основные параметры и размеры муфт упругих втулочно- |
||||||||
|
|
пальцевых. ГОСТ 21424-93 |
|
|
|
||||
|
|
|
|
|
|
|
|
|
|
|
Частота |
|
Отверстие, мм |
|
Габаритные раз- |
||||
Момент |
вращения, |
|
|
меры, мм |
|||||
|
|
|
|
|
|||||
Т, Н*м |
n, об/мин, |
d |
|
lцил |
|
lкон |
L |
|
D |
|
не более |
|
|
|
|||||
|
|
|
|
|
|
|
|
|
64
Окончание табл.10.1
31,5 |
6360 |
16;18;19 |
28 |
18 |
60 |
90 |
63 |
5700 |
20;22;24 |
36 |
24 |
76 |
100 |
125 |
4620 |
25;28;30 |
42 |
26 |
89 |
120 |
250 |
3780 |
32;36;38 |
58 |
38 |
121 |
140 |
|
|
40;42;45 |
82 |
56 |
169 |
140 |
500 |
3600 |
40;42;45 |
82 |
56 |
169 |
170 |
1000 |
2800 |
50;55;56 |
82 |
56 |
170 |
220 |
|
|
60;63;65 |
105 |
72 |
216 |
220 |
|
|
|
|
|
|
Таблица 10.2 |
|
|
Основные параметры и размеры муфт зубчатых. ГОСТ 5006-83 |
||||||
|
|
|
|
|
|
|
|
Момент |
|
Частота враще- |
Отверстие, мм |
Габаритные размеры, |
|||
|
ния, n, об/мин, |
|
мм |
||||
Т, Н*м |
|
|
|
|
|||
|
не более |
d |
lцил |
L |
|
D |
|
|
|
|
|||||
1000 |
|
5400 |
40 |
82 |
174 |
|
145 |
1600 |
|
4800 |
55 |
82 |
174 |
|
170 |
2500 |
|
4500 |
60 |
105 |
220 |
|
185 |
4000 |
|
3720 |
65 |
105 |
220 |
|
200 |
6300 |
|
3300 |
80 |
130 |
270 |
|
230 |
10000 |
|
2820 |
100 |
165 |
340 |
|
270 |
16000 |
|
2400 |
120 |
165 |
345 |
|
300 |
25000 |
|
2100 |
140 |
200 |
415 |
|
330 |
40000 |
|
1740 |
160 |
200 |
415 |
|
410 |
63000 |
|
1200 |
200 |
240 |
500 |
|
470 |
65
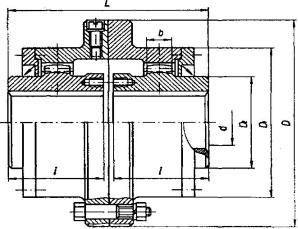
Рис. 10.2. Муфта зубчатая
11 ВЫБОР ПОСАДОК ОСНОВНЫХ СОЕДИНЕНИЙ
Посадка-характер соединения двух деталей, определяемый величиной получающихся в нѐм зазоров или натягов.
Различают посадки трѐх типов: с зазором, с натягом и переходные. Поле допуска вала под внутренним кольцом подшипника к6.
Поле допуска вала под резиновыми манжетами (уплотнениями)-
h11.
Поле допуска корпуса редуктора под внешним кольцом подшипника - Н7.
Посадка крышка подшипника - корпус редуктора - H7/h8. Посадка зубчатое колесо - вал - H7/s6.
Посадка стакан - корпус редуктора - H7/h8. Посадка дистанционная втулка - вал - D9/k6. Посадка полумуфта - конец вала - Н7/р6.
Посадка боковая поверхность шпонки - вал - P9/h9.
12КОНТРОЛЬНЫЕ ВОПРОСЫ
1.Какое зубчатое колесо называют шестернѐй?
2.В чѐм различие между редуктором и мультипликатором?
3.Как связаны между собой вращающие моменты на ведущем и ведомом зубчатых колесах?
4.Чем отличается вал от оси?
5.Как образуется эвольвентный профиль зубьев?
66
6.Что называют линией зацепления?
7.Что такое модуль зацепления?
8.Как определяют модуль зацепления?
9.Что такое смещение исходного контура?
10.В чѐм преимущество косозубого цилиндрического зацепления перед прямозубым?
11.В чѐм заключается фланкирование зубьев и для чего его применяют?
12.В каком направлении осуществляют положительное смещение профиля?
13.В чѐм разница между нормальным и окружным модулями?
14.Каковы основные параметры цилиндрических зубчатых передач?
15.Какие три пары сил действуют в косозубом цилиндрическом зубчатом зацеплении?
16.Какая из сил в зацеплении является наибольшей?
17.Каковы основные параметры цилиндрических зубчатых передач?
18.Какие напряжения возникают на поверхности зубьев?
19.Какие напряжения возникают в опасном сечении зуба?
20.Какой параметр определяют проектным расчѐтом цилиндрической зубчатой передачи?
67
БИБЛИОГРАФИЧЕСКИЙ СПИСОК
1.Анурьев В.И. Справочник конструктора-машиностроителя: В3 т. 8-е изд., перераб. И доп. М.: Машиностроение, 2001. 920, 912, и 864с.
2.Детали машин: Атлас конструкций: В 2 ч. 5-е изд. / Под ред. Д.Н.Решетова. М.: Машиностроение, 1992. 352с. и 296с.
3.Детали машин / Под ред. О.А.Ряховского. М.: Изд-во МГТУ им Н.Э.Баумана, 2002. 543с.
4.Дунаев П.Ф., Леликов О.П. Конструирование узлов и деталей машин: Учеб. Пособие для техн. спец. вузов.7-е изд., исправленное.-М.: Высшая школа, 2001. 447с.
5.Дунаев П.Ф., Леликов О.Л. Детали машин. Курсовое проектирование. 3-е изд. М.: Машиностроение, 2002. 536с.
6.Иванов М.Н. Детали машин: Учебник для вузов. 6-е изд. М.: Высшая школа, 2000. 383с.
7.Чернавский С.А., Курсовое проектирование деталей машин / Чернавский С.А., Ицкович Г.М., Боков К.Н. и др. М.: Машиностроение, 1988. 415с.
8.Леликов О.Л. Основы расчета и проектирования деталей и узлов машин. Конспект лекций по курсу «Детали машин». М.: Машино-
строение, 2002. 536с.
9.Машиностроение. Энциклопедия. Детали машин. Конструкционная прочность. Трение, износ, смазка. Т IV-1 / Под общ. ред Д.Н.Решетова. М.: Машиностроение, 1995. 864с.
10.Орлов П.И. Основы конструирования. Справочно - методическое пособие. В 2 т. 3-е изд. М.: Машиностроение, 1998. 559 и 542с.
11.Ряховский О.А., Иванов ОС. Справочник по муфтам. Л.: поли-
техника, 1991. 384с.
12.Феодосьев В.И. Сопротивление материалов. 10-е изд. М.: Издво МГТУ им. Н.Э.Баумана, 1999. 589с.
13.Чернавский С.А., Снесарев Г.А., Козинцов Б.С. и др. Проектирование механических передач: Учебно-справочное пособие, М. Машиностроение, 1984. 558с.
14.Шейнблит А.Е. Курсовое проектирование деталей машин. М.: Высшая школа, 1991. 432с.
15.Канаев Я.И., Мезин И.Ю. Дипломный проект. Структура, содержание, общие правила выполнения и оформления: Стандарт предприятия СК МГТУ СК 05.02-2004. Магнитогорск, МГТУ, 2004. 36 с.
68
Другие рекомендуемые информационные источники
16.Харченко, М.В. Теоретическое исследование влияния режимов подачи смазочного материала на изменение энергозатрат при горячей прокатке на стане 2000 ОАО «Магнитогорский металлургический комбинат» [Текст] / Р.Р. Дема, М.В. Харченко, А.А. Горбунова // Производство проката. - 2013. - № 2. - С. 11-13.
17.Дема, Р.Р. Математическое моделирование процесса изнашивания рабочих валков клети кварто при подаче смазочного материала. [Текст] / Р.Р. Дема, Р.Н. Амиров, С.И. Платов, И.В Казаков // Черные металлы. 2012.–Т. 6.–С. 54.
18.Харченко, М.В. Оценка эффективности процесса горячей чистовой прокатки с использованием системы подачи технологической смазки. [Текст] / М.В. Харченко, И.С. Пелымская. // Черная металлургия. 2013.– № 11. – С. 46-50.
19.Амиров, Р.Н. Исследование и оценка загруженности главных приводов непрерывной группы клетей стана 2000 горячей прокатки в зависимости от сортамента выпускаемой продукции. [Текст] / Р.Н. Амиров, Р.Р. Дема, С.И. Платов, У.Д. Мартынова, К.К. Ахметова // Производство проката. 2014.–№ 2.–С. 13-16.
20.Харченко, М.В. Разработка технологии подачи смазки при горячей прокатке на опорные валки для производства высокопрочных марок сталей [Текст] / М.В. Харченко, Р.Р. Дема, А.В. Ярославцев // Актуальные проблемы современной науки, техники и образования: сб. науч. тр./ Магнит. гос. техн. ун-т. им. Г.И. Носова.– Магнитогорск, 2010.– Т. 1.– № 1.–С. 307-310.
21.Харченко, М.В. Расчет усилий при горячей прокатке на стане 2000 ОАО «Магнитогорский металлургический комбинат» с применением системы подачи технологической смазки на основе учета напряженнодеформированного состояния в очаге деформации [Текст] / М.В. Харченко, Р.Р. Дѐма, А.А. Горбунова // Производство проката. 2013.–№ 3.–С. 14-
22.Дема, Р.Р. Исследование теплового состояния прокатных валков черновой группы клетей стана 2000 г.п. ОАО «ММК». [Текст] / Р.Р. Дема, М.В. Зубарева // Процессы и оборудование металлургического производства: межрегион. сб. научн. тр. под ред. С.И. Платова / Магнит. гос. техн. ун-т. им. Г.И. Носова.– Магнитогорск, 2009.–С. 282-283.
23.Дема, Р.Р. Использование методов нейронной сети для прогнозирования энергосиловых параметров процессов горячей прокатки при подаче смазочного материала. [Текст] / Р.Р. Дема, Р.Н. Амиров, У.Д. Мартынова // Моделирование и развитие процессов ОМД: сб. научн. тр. / Магнит. гос. техн. ун-т. им. Г.И. Носова.– Магнитогорск, 2012. № 18. С.
101-103.
69