
scherbo-sp1
.pdf
мациям ε, т. е. соблюдается закон Гука, который справедлив до предела пропорциональности σпц.
Пределом пропорциональности σпц называется наибольшее напряже-
ние, при котором справедлив закон Гука (для стали Ст. 3 σпц ≈ 2100 кгс/см2 ≈
210 Мн/м2).
Тангенс угла наклона α прямого участка ОА к оси абсцисс равен модулю упругости:
tgα = σ ε =TE . |
(2.12) |
Выше точки А диаграмма искривляется, закон Гука нарушается, деформации начинают расти быстрее роста напряжений. Очень близко к точке А на криволинейном участке диаграммы можно отметить точку В, соответствующую пределу упругости σуп.
Пределом упругости σуп называется максимальное напряжение, которое может выдержать материал, не обнаруживая признаков остаточной деформации при разгружении.
Точка В находится вблизи точки А, поэтому их часто считают совпадающими.
Если через точку В провести вертикальную линию, то левее этой линии на диаграмме будет зона упругих, а правее – зона упругопластических деформаций (там будут иметь место и упругие, и пластические деформации).
Начиная от некоторой точки С диаграмма имеет горизонтальный (или почти горизонтальный) участок, которому соответствует предел текучести σт. На этом участке деформации растут без увеличения нагрузки – материал как бы «течет».
Пределом текучести σт называется напряжение, при котором де-
формации растут без увеличения нагрузки (для стали Ст. 3 σт≈2400 кгс/см8 ≈
40 Мн/м2).
Соответственно горизонтальный участок диаграммы называют пло-
щадкой текучести .
Явление текучести наблюдается только в малоуглеродистой стали вследствие сдвигов, происходящих внутри кристаллов феррита.
На микрофотографии такой стали (рис. 2.13) при текучести видны кристаллы феррита 1, вокруг них – сетка третичного цементита 2 и перлитовые включения 3.
При пределе текучести хрупкая цементативная сетка начинает разрушаться, а усилия, воспринимаемые ею, передаются на кристаллы феррита. Вследствие этого кристаллы феррита деформируются и в них появляются сдвиги 4 по плоскостям, наклоненным (в большинстве кристаллов) приблизительно под углом 45° к оси стержня, в которых действуют наибольшие касательные напряжения.
31
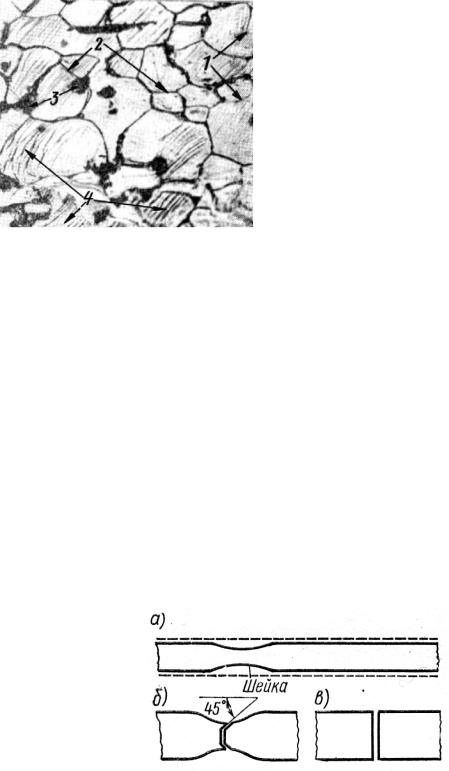
Эти сдвиги видны невооруженным глазом на поверхности отполированных образцов, растянутых до предела текучести, в виде полос, назы-
ваемых линиями Людерса – Чернова.
Начиная с некоторого момента (см. рис. 2.12) при дальнейшем увеличении деформаций нагрузка вновь увеличивается. Происходит «самоупрочнение» стали, причины которого до сего времени недостаточно ясны. Предполагают, что по плоскостям сдвигов
Рис. 2.13 из твердого раствора феррита выделяются новые микрочастицы, препятствующие дальнейшим сдвигам.
Диаграмма изменяется по плавной кривой с наивысшей точкой D, в которой условное напряжение (σ = Р/F) принимает наибольшее значение, достигая предела прочности σв.
Пределом прочности (или временным сопротивлением) σв называет-
ся отношение наибольшей нагрузки, выдерживаемой образцом, к первона-
чальной площади его сечения. Предел прочности – это некоторая условная характеристика, она не является напряжением, при котором материал разрушается, так как при разрушении площадь сечения образца значительно меньше первоначальной (для стали Ст. 3 σв ≈ 4000 кгс/см2 ≈ 400 Мн/м2).
До достижения предела прочности продольные и поперечные деформации образца равномерно распределяются по его расчетной длине.
После достижения точки D диаграммы эти деформации концентрируются в одном наиболее слабом месте, где начинает образовываться шейка – местное значительное сужение (рис. 2.14, а), которое быстро прогрессирует.
Рис. 2.14
С этого момента продольная деформация зависит уже не столько от длины образца, сколько от его диаметра. Этим объясняется необходимость иметь для нормальных образцов определенное отношение между длиной
32
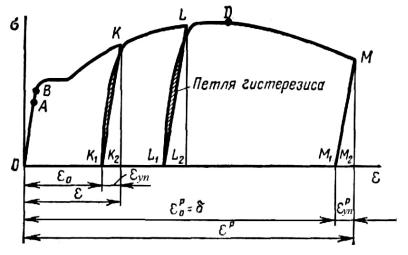
образца и его диаметром для сравнимости результатов испытаний, полученных в разных лабораториях.
За точкой D ординаты диаграммы начинают уменьшаться, нагрузка падает, что объясняется дальнейшим уменьшением поперечного сечения шейки. Наконец происходит разрыв образца. Этому на диаграмме соответствуют точка М и условное напряжение σр.
При разрыве образца появляется поперечная трещина в центре поперечного сечения посередине шейки, а в остальной части сечения скалывание происходит под углом около 45° к оси стержня, так что на одной части разорванного образца образуется выступ, а на другой – кратер (рис. 2.14, б). Такая форма разрушения образцов из малоуглеродистой пластической стали показывает, что разрушение связано со сдвигом по площадкам, наклоненным под углом 45° к оси стержня, где касательные напряжения будут наибольшими.
Если начиная с некоторой точки К диаграммы (рис. 2.15) будем разгружать образец, то диаграмма пойдет по прямой KK1, приблизительно параллельной прямой ОА. Отрезок ОК равен остаточной деформации ε0, соответствующей точке К, а отрезок К1К2 – упругой деформации εуп, соответствующей той же точке. Полная деформация ε равна сумме двух указанных деформаций:
ε = ε0 + εуп.
Рис. 2.15
Если теперь вновь начать нагружать образец, то диаграмма пойдет примерно по линии К1К, образуя небольшую петлю. Эта петля, заштрихованная на рис. 2.15, получается вследствие необратимых потерь энергии деформации. Она носит название петли гистерезиса. Начиная с точки К диаграмма пойдет так, как будто бы не было разгрузки и повторной на-
33
грузки образца, т. е. при повторной нагрузке диаграмма напряжений изменяется по кривой K1KDM вместо кривой OACDM (см. рис. 2.12), характерной для первоначально ненагруженного образца. Это показывает, что при нагружении образца выше предела текучести и последующей его разгрузке металл образца изменил свои свойства: пропала площадка текучести, повысился предел пропорциональности и уменьшилась полная деформация при разрыве (K1M2 < ОМ2) – металл стал как бы более хрупким. Такое изменение свойств металла называют наклепом.
Наклеп может возникнуть не только при растяжении, но и при любых других видах деформаций. При всякой холодной обработке металла, которая вызывает напряжения выше предела текучести, развивается наклеп. Например, продавливание отверстий в стальных листах для постановки болтов или заклепок обходится значительно дешевле сверления этих отверстий. Но при продавливании отверстий их края подвергаются наклепу и становятся хрупкими (что может служить причиной возникновения трещин). Для устранения этого недостатка часто продавливают отверстия меньшего диаметра, после чего рассверливают их до нужного диаметра, удаляя тем самым металл, получивший наклеп.
Иногда, наоборот, наклеп используют в технике. Например, цепи грузоподъемных машин предварительно вытягивают для возникновения в них наклепа, чтобы уменьшить их деформацию и повысить предел пропорциональности.
Наклеп можно устранить последующим отжигом изделия.
При повторной разгрузке образца, начиная от некоторой точки L (см. рис. 2.15), диаграмма опять пойдет по прямой LL1 параллельно первоначальному отрезку ОА, а затем произойдет полное повторение явления, описанного выше. Из рис. 2.15 видно, что отрезок ОМ1 равен остаточной
деформации ε0p = δ, а отрезок М1М2 – упругой деформации образца при
разрыве εупр .
На рис. 2.16 показан вид нормального образца в различные моменты испытания его на растяжение.
На рис. 2.16, а показан образец до испытания, на рис. 2.16, б – образец, нагруженный до предела прочности, на рис. 2.16, в – образец непосредственно перед разрывом и на рис. 2.16, г – образец после разрыва. В каждой половине разорванного образца исчезает упругая часть деформации и сохраняется остаточная ее часть. Поэтому длина образца, составленного из двух половин после разрыва, lр меньше, чем его длина непосредственно перед разрывом l2.
Растяжение образца сопровождается его нагреванием и намагничиванием. Эти явления особенно заметны около места разрыва.
34
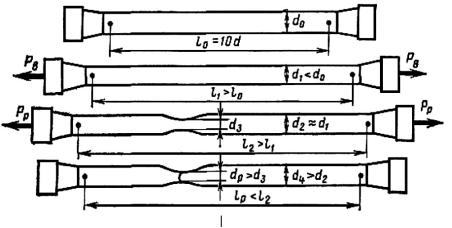
а)
б)
в)
г)
Рис. 2.16
После испытания определяют относительное остаточное удлинение образца после разрыва
δ = |
l p −l0 |
= |
∆l p |
(2.13) |
|
l0 |
l0 |
||||
|
|
|
(для стали Ст. 3 δ ≈ 21 – 23 %) и относительное остаточное уменьшение площади поперечного сечения в шейке после разрыва
ψ = |
F0 − Fp |
= |
∆Fp |
, |
(2.14) |
|
|
||||
|
F |
F |
|
||
|
0 |
|
0 |
|
|
где F0 – площадь сечения до деформации;
Fp – площадь сечения шейки (для Ст. 3 ψ ≈ 60 – 70 %).
Для определения δ и ψ измеряют диаметры и расчетные длины образцов (между нанесенными рисками) до и после испытания. Рассмотренные выше напряжения – пределы пропорциональности σпц, упругости σуп, текучести σт и прочности σв – называют характеристиками прочности материала, так как они характеризуют его прочность.
Полное относительное остаточное удлинение δ и относительное остаточное уменьшение поперечного сечения при разрыве ψ называют ха-
рактеристиками пластичности материала, так как они характеризуют деформационную способность материала, доведенного до разрушения.
2.5. Проверка прочности и определение необходимых размеров бруса при растяжении (сжатии)
В предыдущих параграфах рассматривалась задача о распределении напряжений и деформаций в брусе при действии продольных сил. Однако вопрос о том, как назначить размеры стержня, чтобы он мог надежно и долговечно сопротивляться заданной нагрузке, не решался. Этот вопрос
35
является одним из главных вопросов сопротивления материалов. В условиях массового строительства возникает проблема экономии строительного материала при полной гарантии прочности конструкции.
В тех случаях, когда размеры стержня заданы, возникает задача об определении грузоподъемности стержня, т. е. определении силы, которую стержень может выдержать, не претерпевая каких-либо изменений, опасных для его долговечной работы.
Для решения указанных вопросов необходимо провести специальные расчеты. Существует три метода решения этих задач:
1)расчет по разрушающим нагрузкам;
2)расчет по допускаемым напряжениям;
3)расчет по предельным состояниям.
Все три метода преследуют одну цель – обеспечить сооружению прочность и долговечность. Первый метод предусматривает определение минимальной нагрузки, которая разрушает сооружение, с тем, чтобы сравнить эту нагрузку с предполагаемой для строящегося сооружения. Второй метод до недавнего времени широко применялся в строительном деле и до сих пор применяется в машиностроении. По этому методу размеры элемента сооружения должны назначаться так, чтобы во всех сечениях напряжения, вызываемые нагрузкой, не превышали некоторой допускаемой величины.
2.5.1.Метод разрушающих нагрузок
Вкачестве условия прочности при этом методе расчета выставляется требование, чтобы наибольшая нагрузка на сооружение не превосходила некоторой допускаемой нагрузки [Р], которая равна разрушающей (опасной) нагрузке, деленной на некоторый коэффициент n > 1, который называется коэффициентом запаса прочности:
P ≤[P]= |
Pраз |
. |
(2.15) |
max |
n |
|
Коэффициент запаса n принимается на основе целого ряда соображений, аналогичных тем, которые подробно рассмотрены в методе расчета по допускаемым напряжениям.
Для определения разрушающей нагрузки в конструкциях из материалов, обладающих большой пластичностью и сравнительно небольшим упрочнением, принимается упрощенная диаграмма растяжения (сжатия), показанная на рис. 2.17, в которой площадка текучести распространяется безгранично.
В этом случае при центральном растяжении и сжатии разрушающая сила определяется равенством
Pраз = ∫σТ dF = σT F. |
(2.16) |
36 |
|
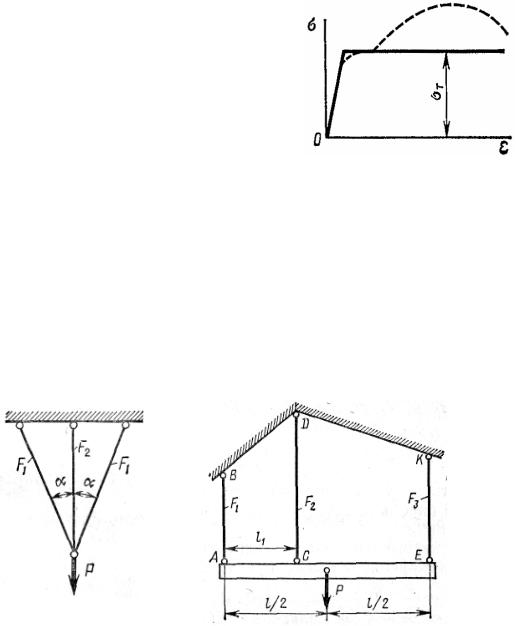
Для хрупких материалов вместо предела текучести надо взять предел прочности:
Pраз = σвF. |
(2.17) |
В статически неопределимых системах из пластичных материалов появление текучести только в одном наиболее нагруженном элементе еще не приводит систему к разрушению.
Так, например, если в статически неопределимой системе, изображенной на рис. 2.18, при увеличении силы Р напряжения, равные пределу текучести, появятся вначале в среднем или крайних стержнях, то это еще не вы-
ведет конструкцию из строя, так как в других стержнях напряжения будут меньше предела текучести. Для полного разрушения конструкции необходимо, чтобы текучесть появилась во всех стержнях. В этом случае разрушающая сила определится из условия равновесия
Pраз = 2N1 cos α + N2 = 2F1σT cos α + F2σT .
Более сложно определить разрушающую нагрузку в задаче, показанной нарис. 2.19, гдебесконечножесткийбрусудерживается тремястержнями.
Рис. 2.18 |
Рис. 2.19 |
Здесь сила Рраз определяется из условия текучести по крайней мере двух стержней. Так, если стержень АВ менее напряжен, а в двух других стержнях CD и ЕК появилась текучесть, то Рраз определится из условия равенства нулю суммы моментов относительно точки А
∑M A = Pраз 12 − F2σT l1 − F3σT l = 0.
37

Аналогично можно составить еще два уравнения, если предположить, что текучесть появится в двух стержнях АВ и ЕК или стержнях АВ и CD. Из трех найденных значений сил в расчет вводится наименьшая сила, которая и считается разрушающей.
2.5.2. Метод допускаемых напряжений
По методу допускаемых напряжений требуется, чтобы наибольшее напряжение в стержне не превосходило так называемого допускаемого напряжения, которое обозначается [σ]. Например, при растяжении условие прочности имеет вид
σmax = |
N |
≤[σ]. |
(2.18) |
|
|||
|
Fnetto |
|
Предполагая, что действующее напряжение равно допускаемому, получим
N = [σ].
Fnetto
Из этого уравнения можно определить требуемую площадь при заданной силе или, наоборот, допускаемую силу при заданных размерах сечения.
Допускаемые напряжения равны опасным напряжением σоп, деленным на коэффициент запаса прочности n:
[σ]= |
σоп |
. |
(2.19) |
|
|||
|
n |
|
Для хрупких материалов за опасные напряжения принимают предел прочности σоп = σв, поэтому
[σ]= σв ,
n1
для пластических материалов – предел текучести σоп = σТ , следовательно,
[σ]= σТ .
n2
Очевидно, что коэффициент запаса n1 должен быть больше n2, так как после появления пластических деформаций стержень еще не разрушается.
Необходимость введения коэффициентов запаса прочности объясняется следующими обстоятельствами:
а) разбросом в определяемых из опыта величинах σт или σв для данного материала;
б) невозможностью точно установить действующие нагрузки;
38
в) неточностью принятых методов расчета (например, неучетом местных напряжений);
г) неточностью изготовления деталей.
При назначении коэффициентов запаса, а значит и допускаемых напряжений, кроме перечисленных выше соображений необходимо также учитывать и другие факторы:
1)качество и степень однородности материала. Например, для стали коэффициент запаса принимается ~1,5, для бетона ~3, для естественного камня, материала весьма неоднородного, коэффициент запаса принимается ~10;
2)долговечность и значимость сооружения или машины. Если, например, из одинаковой стали изготовляется постоянный мост со сроком службы 50 – 70 лет и временный мост со сроком службы 3 – 5 лет, то, естественно, в последнем случае коэффициент запаса должен быть меньше;
3)уровень развития техники. С развитием техники повышаются качество изготовления материала и точность обработки деталей, точность расчетов. Поэтому со временем коэффициенты запаса уменьшаются, а допускаемые напряжения увеличиваются.
2.5.3. Метод предельных состояний
Одним коэффициентом запаса трудно учесть многочисленные факторы, которые для различных сооружений могут проявляться в разных сочетаниях.
Для более полного учета влияния различных факторов строительные конструкции в настоящее время рассчитываются по более прогрессивному методу предельных состояний.
Предельным состоянием называется такое состояние конструкции, при котором она перестает удовлетворять заданным, эксплуатационным требованиям.
Метод расчета по предельным состояниям имеет целью не допускать наступления предельных состояний при эксплуатации и возведении конструкций. Строительные нормы и правила (СНиП) разделяют предельные состояния на две группы.
Первая группа – по потере несущей способности (вследствие разрушения) или непригодности к эксплуатации (вследствие текучести материала, сдвигов в соединениях и других факторов).
Вторая группа – по непригодности к нормальной (без ограничений) эксплуатации(вследствиенедопустимыхперемещений, колебанийитрещин).
Классификация предельных состояний принята по признаку их ответственности за степень потери эксплуатационной способности.
Рассмотрим расчет конструкций по первой группе предельных состояний вследствие потери несущей способности при растяжении.
39
Проверка прочности производится по формуле расчетного напряжения
σрасч = |
N |
≤ R. |
(2.20) |
|
F |
||||
|
|
|
Здесь R – расчетное сопротивление материала – сопротивление, принимаемое при расчете данной конструкции
R = |
Rн |
, |
(2.21) |
|
k |
||||
|
|
|
где Rн – нормативное сопротивление материала, устанавливаемое нормами проектирования с учетом условий контроля и статистической изменчивости. Величина нормативного сопротивления может равняться величине контрольной или браковочной характеристики материала (пределу текучести или пределу прочности), устанавливаемой государственным стандартом;
k – коэффициент безопасности по материалу (принимаемый не менее 1,1), учитывающий возможные отклонения сопротивления материала от нормативного. Значения коэффициентов безопасности устанавливаются нормами проектирования в зависимости от свойств материала, их статистической изменчивости и нестатистических факторов (например, отличие сопротивления материала в конструкции и образцах, допуски в размерах профилей и пр.);
N – расчетное усилие, принимаемое при расчете элементов конструкции
N = N нn + N нn |
2 |
+..., |
(2.22) |
||
1 |
1 |
2 |
|
|
где N1н; N2н , ... – усилия, возникающие в элементах конструкции от различных
видовнормативныхнагрузок, устанавливаемыхнормамипроектирования; n1, n2, ... – коэффициенты перегрузки, учитывающие случайные от-
клонения нагрузок от нормативных значений вследствие изменчивости нагрузок или отступлений от условий нормальной эксплуатации. Значения коэффициентов перегрузки устанавливаются нормами проектирования для каждого вида предельного состояния с учетом значимости сооружений и условий их эксплуатации;
F – геометрическая характеристика сечения (при растяжении и сжатии – площадь сечения).
При необходимости расчетные сопротивления еще уменьшаются путем введения коэффициентов условий работы m, учитывающих особенности работы материала и конструкции, не отраженные в расчете прямым путем (например, приближенность расчетной схемы и предпосылок расчета, температура, влажность и агрессивность среды и пр.) и коэффициентов надежности kн, учитывающих степень ответственности и капитальности конструкции и значимости наступления данного предельного состояния.
40