
Технология конструкционных материалов. Способы получения деталей (за
.pdfЖелезные руды содержат железо в виде оксидов, гидратов оксидов, карбонатов. Пустой породой в железных рудах обычно является кварцит или песчаник, глинистые вещества.
К основным железным рудам относятся:
–магнитный железняк содержит до 65 % железа в виде оксида Fe3O4;
–красный железняк содержит до 60 % железа в виде оксида Fe2O3;
–бурый железняк содержит до 55 % железа в виде гидратов оксидов nFe2O3 mH2O;
–шпатовый железняк содержит до 40 % железа в виде
углекислой соли FeCO3.
Топливо (кокс) в процессе выплавки чугуна выполняет рольне только горючего, но ивосстановителя железаиз руды.
Флюсами при выплавке чугуна в доменной печи служат из-
вестняк CaCO3 или доломит СаСО3 MgCO3. Их назначение переводпустойпороды(восновномSiO2 иAl2O3) вшлак, атакже связываниеиудалениесеры, находящейсявтопливеируде.
Огнеупорным материалом для футеровки доменной печи служит шамот.
4.2. Подготовка руд к плавке
Перед плавкой железные руды подвергают обогащению, агломерации, окатыванию.
Обогащение руды. Увеличение содержания железа в руде достигается: промывкой руды водой, что позволяет отделить часть песчано-глинистой породы; гравитацией (отсадкой), основанной на отделении руды от легкой пустой породы при пропускании под напором воды через руду. Магнетитовые руды обогащают способом магнитной сепарации, основанной на различии магнитных свойств железосодержащих минералов и частиц пустой породы.
11
Для улучшения процесса плавки обогащенную руду (концентрат) перерабатывают в кусковые материалы агломерацией или окатыванием.
Агломерация заключается в спекании руды (40…50 %), известняка (15…20 %), возврата мелкого агломерата и кокса при температуре 1300…1500 С. При этом из руды удаляется часть примесей, разлагаются карбонаты и образуется пористый офлюсованный материал агломерат. Применение офлюсованного агломерата позволяет повысить производительность доменных печей на 10…25 % и уменьшить расход кок-
са на 10…20 %.
Окатывание заключается в окусковании тонко измельченных концентратов. Для этого концентрат, флюсы и топливо увлажняют и загружают во вращающуюся наклонную чашу (гранулятор) или в пустотелый барабан, где и образуются окатыши-шарики диаметром 25…30 мм. Готовые окатыши высушивают и обжигают при 1200…1350 С. Использование окатышей и агломерата улучшает доменную плавку, повышает производительность доменной печи, уменьшает расход топлива.
4.3. Выплавка чугуна
Производство чугуна является восстановительным процессом.
Чугун выплавляют в доменных шахтных печах, выложенных из огнеупорного кирпича и заключенных в кожух из листовой стали толщиной до 35 мм. Современная доменная печь имеет высоту до 35 м с полезным объемом до 5000 м3.
4.4. Физико-химическая сущность доменного процесса
Доменная печь работает по принципу противотока: шихтовые материалы движутся сверху вниз, а навстречу им поднимается поток горячих газов продуктов сгорания топ-
12
лива. При этом происходит горение топлива, восстановление и науглероживание железа, восстановление других элементов, образование шлака.
В районе воздушных фурм углерод кокса, взаимодействуя с кислородом дутья, сгорает, в результате чего температура в этой зоне печи достигает 1800…2000 С. Углекислый газ СО2, взаимодействуя с углеродом кокса, образует оксид углерода СО главный восстановитель железа. Несколько выше, в зоне печи с температурой 700…450 С, часть оксида углерода разлагается с образованием сажистого углерода.
Шихтовые материалы, опускаясь навстречу потоку раскаленных газов, нагреваются, из них испаряется влага, выделяются летучие вещества. При достижении температуры 750…900 С в шихте восстанавливается железо до образования закиси железа FeO. Часть закиси железа опускается до распара и заплечников доменной печи и восстанавливается углеродом кокса.
Ввосстановлении железа участвуют также сажистый углерод и водород.
Врезультате этих реакций образуется твердое губчатое
железо. При1000…1100 С губчатоежелезо науглероживается. Углерод понижает температуру плавления железоуглеродистого сплава, поэтому, опускаясь в нижнюю часть шахты, сплав начинает плавиться, дополнительно насыщается углеродом и другими элементами, восстанавливаемыми из
руды, марганцем, кремнием, фосфором, серой.
Марганец содержится в руде в виде оксидов, легко восстанавливаемых до оксида MnO, который затем частично восстанавливается твердым углеродом.
Кремний содержится в пустой породе руды в виде кремнезема SiO2, также восстанавливается твердым углеродом. Невосстановленныеоксидымарганцаикремнияпереходятвшлак.
13
Фосфор находится в руде, главным образом, в виде соединения Р2О5 3СаО, восстанавливается оксидом углерода и твердым углеродом и почти полностью переходит в сплав.
Сера вносится в доменную печь в составе руды и кокса в виде соединений FeS2, FeS, CaSO2, CaS. Значительная часть серы удаляется в виде летучих соединений (SO2, H2S и др.), другая переходит в сплав (FeS) или шлак (СаS).
Таким образом, в зоне распара в доменной печи между собой взаимодействуют кокс, окислы, газы, шлак и сплав из Fe, C, Mn, Si, S, P и других элементов. Полученный сплав железа с углеродом (С от 2,14 до 6,67 %) и называется чугуном. Температура его плавления около 1200 С, сплав находится в жидком состоянии и стекает в нижние зоны печи.
Одновременно в нижней части печи на поверхности жидкого чугуна собирается шлак сплав пустой породы, флюсов, золы топлива, а также часть невосстановившихся оксидов. По мере образования и накопления чугун и шлак выпускают из печи: чугун через3…4 ч, ашлак через1…1,5 ч.
4.5. Продукты доменного производства
Основным продуктом доменного производства является чугун, побочным шлак и колошниковый газ.
В доменной печи получают:
– передельный чугун основной вид чугуна, предназначенный для передела чугуна в сталь. Обычный его состав: 4…4,5 %
С; 0,6…0,8 % Si; 0,25…1 % Mn; до 0,3 % Р и0,07 % S;
– литейный чугун предназначен для переплава и получения фасонных отливок, отличается повышенным содержанием кремния (2,75…3,25 %);
14

– ферросплавы сплавы железа с повышенным содержанием других элементов, например ферросилиция (9…13 % Si), ферромарганца (70…75 % Mn), предназначенные для раскисления и легирования стали.
Шлак используется для производства шлаковаты, шлакоблоков, цемента.
Образующиеся в печи газы (СО, СО2, Н2, СН4, N2 и др.) поднимаются вверх и в зоне колошника отводятся по трубам из печи. Эти газы, называемые колошниковыми, используют в качестве топлива для нагрева воздухонагревателей.
Технико-экономические показатели работы доменной печи:
а) коэффициент использования полезного объема печи
КИПО VP ,
где V полезный объем печи, м3;
Р средняя суточная производительность печи, т.
Для отечественных доменных печей КИПО составляет
0,5…0,7;
б) удельный расход кокса K CA ,
где А расход кокса за сутки, т; С средняя суточная производительность печи, т.
Удельный расход кокса является важным показателем работы доменной печи, так как стоимость кокса составляет около 50 % стоимости чугуна. В нашей стране этот показатель равен 0,5…0,6.
Увеличению выплавки чугуна и уменьшению расхода кокса способствует повышение эффективности обогащения руд, применение офлюсованного агломерата и окатышей.
15

5.Производство стали
5.1.Сущность процесса
Сталь это сплав железа с углеродом, содержание углерода в котором 0,006…2,14 %.
Сталь отличается от чугуна меньшим содержанием углерода, кремния, марганца, примесей серы и фосфора (табл. 1). Исходные материалы для получения стали передельный чугун и стальной лом (скрап).
Таблица 1 Состав передельного чугуна и низкоуглеродистой стали, %
Материал |
C |
Si |
Mn |
P |
S |
|
Передельный |
4,0…4,4 |
0,76…1,26 |
до 1,75 |
0,15…0,30,03…0,07 |
||
чугун |
||||||
|
|
|
|
|
||
Сталь |
0,14…0,22 |
0,12…0,3 |
0,4…0,65 |
0,05 |
0,055 |
|
низкоуглероди- |
||||||
стая |
|
|
|
|
|
Сущностью передела чугуна в сталь является уменьшение содержания углерода и других элементов и перевода их в шлак или газы.
Процесс получения стали является окислительным. Кислород поступает или из атмосферы, или из железной руды, или из других окислителей, либо ванну жидкого чугуна продувают чистым кислородом.
В первую очередь окисляется железо, так как его содержание в чугуне максимально: образуется закись железа FeO. Одновременно с железом окисляются Si, P, Mn, C и др. Образующийся оксид железа при высоких температурах отдает свой кислород более активным элементам примесям в чугуне, окисляя их и переводя в шлак при взаимодействии с флюсами. Реакции окисления примесей идут с выделением
16
большого количества тепла. После почти полного выгорания кремния и марганца, когда жидкий металл хорошо разогрет, начинается окисление углерода, что сопровождается некоторым понижением температуры жидкого металла. Когда содержание углерода в жидкой ванне достигает оптимального значения, продувку прекращают и в ванну вводят раскислители (ферромарганец, ферросилиций или алюминий) для понижения содержания кислорода (который находится в виде закиси железа FeO и охрупчивает металл).
5.2. Способы получения стали
Качество стали зависит от содержания в ней постоянных примесей и газов.
Существуют различные способы получения стали, обеспечивающие разное содержание примесей, а следовательно, и качество стали.
Основными сталеплавильными агрегатами являются: кислородный конвертер, мартеновские и электрические печи.
Материалом для получения стали в кислородном конвертере служит жидкий передельный чугун и стальной лом. Для наводки шлака добавляют железную руду и известь, а для его разжижения боксит и плавиковый шпат. Продувку конвертера ведут кислородом. В кислородных конвертерах выплавляют конструкционные стали с разным содержанием углерода, кипящие и спокойные, низколегированные стали. Способ является высокопроизводительным (400…500 т/ч в кислородном конвертере емкостью 300 т), имеет малую металлоемкость, поэтому становится основным способом производства стали.
В связи с тем что мартеновский процесс получения стали малопроизводителен, в настоящее время онприменяется редко.
Производство стали в электропечах имеет ряд преимуществ: способность быстрого нагрева и поддержания заданной
17
температуры в пределах до 2000 С, возможность создания окислительной, восстановительной или нейтральной атмосферы, а также вакуума. Это позволяет выплавлять стали и другие сплавы с минимальным количеством вредных примесей, с оптимальным содержанием компонентов, отличающихся высоким качеством и обладающих специальными свойствами.
Металлургические печи подразделяют на дуговые и ин-
дукционные.
Источником тепла в дуговых электропечах служит электрическая дуга, возникающая между электродами и шихтой при пропускании тока через электроды.
Электродуговые печи имеют емкость 0,5…400 т. Сталь выплавляют, главным образом, в основных электропечах с окислением и без окисления примесей.
Плавку с окислением обычно применяют для получения углеродистых сталей. Шихтой служит стальной лом, передельный чугун, коксдлянауглероживанияидобавка2…3 % извести.
Плавка без окисления применяется для получения легированной стали из скрапа и отходов соответствующего состава. Производство стали сводится к переплаву шихты, хотя в процессе плавки не исключено и окисление некоторых примесей, а также введение при необходимости некоторых компонентов.
В индукционных печах плавку обычно проводят методом переплава отходов легированных сталей или чистого по сере и фосфору углеродистого скрапа и ферросплавов, помещенных в тигель. Тигель расположен в водоохлаждаемом индукторе, через который проходит переменный ток. Ток создает магнитный поток, который наводит в металлической шихте мощные вихревые токи, нагревающие ее до расплавления.
После расплавления шихты на поверхность металла подают шлак: в основных печах известь и плавиковый шпат,
18
в кислых бой стекла и другие материалы, богатые кремнеземом SiO2. Шлак защищает металл от окисления и насыщения газами атмосферы, уменьшает потери тепла и угар легирующих элементов.
Плавка в вакууме позволяет получать сплавы с минимальным содержанием газов и неметаллических включений, легировать сплавы любыми элементами.
Индукционные печи имеют емкость от десятков килограммов до 5 т, в отдельных случаях емкость их достигает
25…30 т.
Индукционные печи по сравнению с дуговыми обладают рядом преимуществ:
а) отсутствие дуги позволяет выплавлять металлы с малым содержанием углерода и газов;
б) возникающие электродинамические силы перемешивают жидкий металл, способствуя выравниванию химического состава и всплыванию неметаллических включений;
в) индукционные печи отличаются небольшими размерами, что позволяет помещать их в специальные камеры и создавать любую атмосферу или вакуум.
5.3. Разливка стали
Выплавленную сталь выпускают в сталеразливочный ковш 2 (рис. 1) и разливают в изложницы 1 или кристаллизаторы 3 установок для непрерывной разливки.
Изложницы чугунные формы для получения слитков различного сечения и массы от 10 до 300 т. Легированные стали иногда разливают в слитки массой в несколько сотен килограммов.
Применяют два способа разливки стали в изложницы: сверху и сифоном.
19
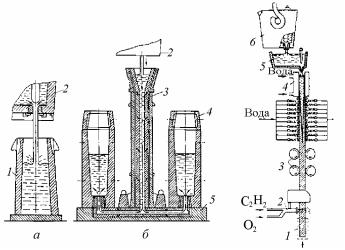
При разливке сверху (см. рис. 1, а) сталь заливают из ковша 2 в каждую изложницу 1 отдельно. Поверхность слитков вследствие попадания брызг жидкого металла на стенки изложницы может быть загрязненной пленками оксидов.
При сифонной разливке (см. рис. 1, б) сталью заполняют одновременно от 2 до 60 установленных на поддоне 5 изложниц через центровой литник 3 к каналам в поддоне. Сталь поступает в изложницы снизу, что обеспечивает плавное, без разбрызгивания их заполнение, поверхность слитка получается чистой, сокращается время разливки. Сталь в надставке 4 сохраняется в жидком состоянии, благодаря чему уменьшаются усадочная раковина и отходы слитка при обрезке.
Рис |
|
|
|
. 1. Разливка стали в изложницы: |
Рис. 2. Схема установки |
||
а разливка сверху, б сифонная |
непрерывной разливки |
||
|
разливка |
стали |
Разливку сверху обычно применяют для углеродистых, а разливку сифоном для легированных сталей.
Непрерывная разливка стали производится на специ-
альных установках УНРС (рис. 2). Жидкую сталь из ковша 6
20