
Технология конструкционных материалов. Способы получения деталей (за
.pdf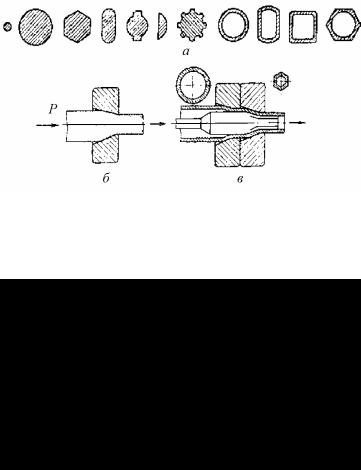
товок 2 через отверстие в матрице 1 (волоке), поперечное сечение которого меньше поперечного сечения заготовки
(рис. 38).
Волочением обрабатывают различные марки стали, цветные металлы и их сплавы. Волочением получают проволоку диаметром 0,002…10 мм и фасонные профили (рис. 39, а)
(призматические и фасонные на- |
|
|||
|
||||
правляющие; сегментные, приз- |
|
|||
матические и фасонные шпонки; |
|
|||
шлицевые валики; опорные приз- |
|
|||
мы, ножи и т.д.). Волочением ка- |
|
|||
|
||||
либруют стальные трубы диамет- |
|
|||
рами от капиллярных до 200 мм, |
|
|||
с толщиной |
стенки |
0,1…10 |
мм, |
|
стальные |
прутки |
диаметрами |
|
|
3…150 мм (см. рис. 39). |
|
Рис. 38. Схема |
||
Исходными заготовками |
для |
волочения |
||
волочения |
служат |
прокатанные |
|
или прессованные прутки и трубы из стали, цветных металлов и их сплавов.
Рис. 39. Примеры профилей (а), получаемых волочением, схемы волочения прутков (б) и труб (в)
81
Волочение осуществляют в условиях холодной деформации, металл упрочняется. Для восстановления пластичности упрочненный волочением металл подвергают промежуточному отжигу.
Инструмент и оборудование для волочения. Инстру-
ментом для волочения служит волочильная матрица 1 (волока) (см. рис. 38). Волоки могут быть цельными, составными и роликовыми. Цельная волока имеет отверстие (очко), состоящее из четырех зон: смазочной воронки I, рабочего конуса II, калибрующего пояска III и выходного конуса IV. Угол рабочего конуса зависит от деформируемого материала и составляет 6…12 . Ширина калибрующего пояска обычно 2…10 мм. Рабочая часть матрицы изготавливается из инструментальных сталей, твердых сплавов и технических алмазов.
При протягивании прутка через отверстие с силой Р возникают силы реакции N, которые обжимают заготовку.
Степень обжатия q F0 F1 F0 , где F1 и F2 площади поперечного сечения соответственно до и после волочения. Допускаемая за один проход q составляет для сталей
10…19 %, для цветных металлов до 36 %. Чтобы не было обрывов, напряжение при волочении не должно превышать 0,6 предела прочности материала заготовки. Для получения профилей необходимых размеров производят волочение за несколько проходов.
Волочение производят на барабанных и цепных волочильных станах. Барабанные станы (рис. 40) служат для волочения проволоки, труб небольшого диаметра, наматываемых в бунты. Исходную заготовку в виде бунта укладывают на барабан 1. Предварительно заостренный конец проволоки пропускают через отверстие волоки 2 и закрепляют на барабане 3, который приводится во вращение от электродвигателя через редуктор и зубчатую передачу 4. Кроме станов для
82
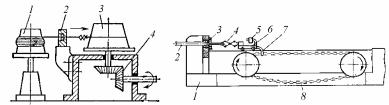
однократного волочения, существуют станы для многократного волочения, которые имеют до 20 барабанов с установленными перед каждым из них волоками. На цепных станах (рис. 41) тянущее устройство совершает прямолинейное воз- вратно-поступательное движение. Такие станы применяют для волочения прутков и труб, которые нельзя наматывать в бунты.
|
|
|
Рис. 40. Схема барабанного |
Рис. 41. Схема цепного |
|
волочильного стана |
||
волочильного стана |
||
|
Конец заготовки 2 (см. рис. 41) пропускается через отверстие в матрице 3 и захватывается клещами 4, которые закреплены на каретке 6, перемещающейся по станине 1 с помощью пластинчатой цепи 8 и крюка 7. Когда изделие выходит из матрицы, натяжение между крюком и цепью уменьшается и противовес 5 поднимает крюк и отсоединяет его от цепи.
Перед волочением с заготовки удаляют окалину химическими, механическими или электрохимическими способами, а также с помощью ультразвука или вакуума. Затем на заготовку наносят смазку или после травления и промывки заготовки на нее наносят подсмазочный слой (например, омеднением).
Изменение размеров заготовки при волочении идет последовательно. Степень обжатия для каждого прохода берется одинаковой, и по ней определяют их количество и диаметры калибрующих поясков отверстий волок. Волочение про-
83
изводят без промежуточного отжига перед каждым проходом после волочения.
Для удаления образующейся при отжиге проволоки окалины ее травят в растворе серной кислоты, затем промывают и сушат горячим воздухом.
Волочение труб производят двумя способами: 1) для уменьшения только диаметра трубы без оправки (см. рис. 39, б); 2) для одновременного уменьшения диаметра и стенки трубы, а также для получения фасонных труб с применением оправки (см. рис. 39, в).
Для уменьшения усилия волочения, износа инструмента и улучшения поверхности изделий применяют смазки: твердые, пластичные и жидкие. Некоторые изделия, от которых требуется высокая точность и качество поверхности, подвергают калиброванию при малой степени обжатия.
7.4. Ковка
Ковка процесс деформирования нагретой заготовки 2 между верхним 1 и нижним 3 бойками молота или пресса (рис. 42, а). Кованые заготовки для последующей обработки называют поковками. Ковкой получают поковки массой от 0,1 кг до 300 т. Мелкие и средние поковки куют из сортового проката и блюмов.
Виды операций ковки и инструмент
Протяжка (вытяжка) увеличение длины заготовки и уменьшение ее поперечного сечения (рис. 42, б). Протяжку можно выполнять плоскими и фигурными бойками. Ковка в фигурных бойках (рис. 42, в) позволяет избежать ковочных трещин при ковке низкопластичных сталей и сплавов и получить более точные поковки.
Степень деформации характеризуется отношением поперечного сечения исходной заготовки к конечному попе-
84
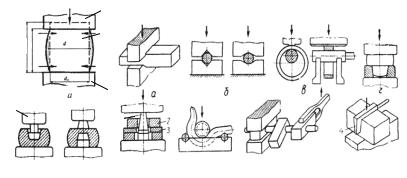
речному сечению, называемому уковкой. Чем больше уковка, тем лучше структура металла и выше его механические свойства. Разновидности протяжки: разгонка (расширение части заготовки); протяжка полого цилиндра на оправке, применяемая при ковке барабанов, труб, цилиндров; раскатка (раздача) колец на цилиндрической оправке для увеличения диаметра (рис. 42, г).
Осадка увеличение поперечного сечения d1 до диаметра d исходной заготовки за счет уменьшения ее высоты h1 до h (см. рис. 42, а). Высота исходной цилиндрической заготов-
h1 h
1
е
1
2
d |
|
|
|
|
|
|
|
|
|
|
|
|
|
|
|
|
|
|
|
|
|
|
|
|
|
|
|
|
|
|
|
|
|
|
|
|
|
d |
|
|
|
|
|
|
|
|
|
|
|
|
|
|
|
|
|
|
|
|
3 |
|
|
|
|
|
|
|
|
|
|
|
|
|
|||
|
|
|
|
|
|
|
|
|
|
|
|
|
|
|
|
|
||
|
|
|
|
|
|
б |
|
|
|
в |
|
г |
|
|
|
|
||
а |
|
|
|
|
|
|
|
|
|
|
|
д |
||||||
|
|
|
1 |
|
|
|
|
|
|
|
|
|||||||
|
|
|
|
|
|
|
|
|
|
|
|
|||||||
|
|
|
|
|
|
|
|
|
||||||||||
|
|
|
|
|
|
|
|
|
|
|
|
|
|
|
|
|
||
|
|
|
|
|
|
|
|
|
|
|
|
|
|
|
|
|
||
|
|
|
|
|
|
|
|
|
|
|
|
|
|
|
|
|
||
|
|
|
|
|
|
|
|
|
|
|
|
|
|
|||||
|
|
|
|
|
2 |
|
|
|
|
|
|
|
|
|||||
|
|
|
|
|
|
|
|
4 |
|
|
||||||||
|
|
|
|
|
|
|
|
|
3 |
|
|
|
|
|
|
|
||
|
|
ж |
з |
|
|
и |
к |
|
|
л |
Рис. 42. Основные технологические операции ковки
ки не должна превышать трех диаметров, торцы ее должны быть ровными и параллельными. Местное утолщение заготовки называется высадкой (рис. 42, д).
Прошивка получение в заготовке сквозного отверстия или углубления. Для выполнения этой операции применяют сплошные и пустотелые (для диаметров 400…900 мм) прошивни 1 (рис. 42, е). Прошивку сквозных отверстий в тонких поковках 3 производят с подкладными кольцами (рис. 42, ж). В более высоких поковках сначала прошивают отверстие с одной стороны (примерно на 3/4 глубины), а затем этим же прошивнем заканчиваютпрошивку с другой стороны(рис. 42, з).
85
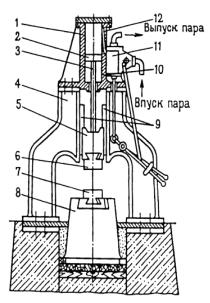
Гибка применяется для изготовления крюков, коленвалов, скоб и т.п. При выборе исходной заготовки надо учитывать искажение формы и уменьшение площади поперечного сечения (утяжку) в зоне изгиба. При гибке могут использоваться подкладки и специальные приспособления (рис. 45, и).
Закручивание поворот одной части заготовки относительно другой на заданный угол применяется при изготовлении коленвалов, сверл и т.п. При закручивании используют ключи, воротки, лебедки (рис. 42, к).
Рубка применяется для разделения заготовки на части, отделения излишка металла и с целью образования в поковке уступов, заплечиков (надрубка). Инструментом для рубки служат прямые и фигурные топоры и зубила 4 (рис. 42, л).
|
|
Оборудованием для ковки служат |
ковочные |
молоты |
||||||||||||
|
|
|
|
|
|
|
|
|
|
|
|
и гидравлические прессы. Мо- |
||||
|
|
|
|
|
12 |
|
|
|
|
лоты создают динамическое |
||||||
1 |
|
|
|
|
|
|
|
|||||||||
|
2 |
|
|
|
Выпускпара |
(ударное) |
воздействие |
инст- |
||||||||
|
|
|
|
|
|
|
|
|
|
|
||||||
|
|
|
|
|
11 |
|
|
|
|
|||||||
|
3 |
|
|
|
|
|
|
|
румента |
|
(верхнего |
бойка), |
||||
|
|
|
|
|
|
10 |
|
|
|
|
|
|||||
|
|
|
|
|
|
|
|
|
|
|
||||||
|
4 |
|
|
|
|
|
|
|
а гидравлические прессы ока- |
|||||||
|
|
|
|
|
|
|
|
|
|
|
||||||
|
|
|
|
|
|
|
|
|
|
|
зывают на заготовку статиче- |
|||||
|
5 |
|
|
|
||||||||||||
|
|
Впуск пара |
||||||||||||||
|
|
|
|
|
|
|
|
|
|
|
|
ское действие. |
|
|
||
|
|
|
|
|
|
|
|
|
|
|
|
|
|
|||
|
|
|
|
|
|
|
9 |
|
|
|
|
|
|
|||
|
|
|
|
|
|
|
|
|
Одним из основных типов |
|||||||
|
|
|
|
|
|
|
|
|
|
|
|
|||||
|
|
|
|
|
|
|
|
|
|
|
|
|||||
|
6 |
|
|
|
|
|
|
|
|
|
|
молотов |
для ковки |
являются |
||
|
|
|
|
|
|
|
|
|
|
|
паровоздушные (рис. 43), ко- |
|||||
|
7 |
|
|
|
|
|
|
|
|
|
|
|||||
|
8 |
|
|
|
|
|
|
|
|
|
|
торые приводятся в действие |
||||
|
|
|
|
|
|
|
|
|
|
|
|
паром или сжатым воздухом. |
||||
|
|
|
|
|
|
|
|
|
|
|
|
|||||
|
|
|
|
|
|
|
|
|
|
|
|
На |
станине 4 |
арочного |
||
|
|
|
|
|
|
|
|
|
|
|
|
молота смонтирован рабочий |
||||
|
|
|
|
|
|
|
|
|
|
|
|
цилиндр 1 с парораспредели- |
||||
|
|
|
|
|
|
|
|
|
|
|
|
тельным |
|
устройством |
11. |
|
|
Рис. 43. Схема паровоздушно- |
|
При нажатии педали или ру- |
|||||||||||||
|
|
го молота арочного типа |
|
коятки |
управления |
сжатый |
||||||||||
|
|
|
|
|
|
|
|
|
|
|
|
|||||
|
|
|
|
|
|
|
|
|
|
|
|
|
|
|
|
|
86 |
|
|
|
|
|
|
|
|
|
|
|
|
|
|
|
пар или воздух по каналу 12 поступает в верхнюю полость цилиндра 1 и давит на поршень 2, соединенный штоком 3 с бабой 5, к которой прикреплен верхний боек 6. В результате падающие части 2, 3, 5 и 6 перемещаются вниз и наносят удары по заготовке, уложенной на нижний боек 7, неподвижно закрепленный на массивном шаботе 8. При подаче сжатого пара по каналу 10 в нижнюю полость цилиндра 1 падающие части поднимаются в верхнее положение. Перемещение бабы 5 происходит в направляющих 9.
Ковочные паровоздушные молоты имеют массу падающих частей 1000…8000 кг. На этих молотах изготовляют поковки средней массы (20…350 кг) преимущественно из прокатных заготовок.
Гидравлические прессы изготовляют с максимальным усилием 5…150 МН. Необходимое для деформирования поковки усилие создается с помощью жидкости (водной эмульсии или минерального масла), поступающей под давлением
20…30 МПа.
Гидравлические прессы используются для получения крупных поковок, а также при ковке малопластичных высоколегированных сталей и сплавов цветных металлов.
7.5. Горячая объемная штамповка
Объемная штамповка процесс изготовления поковок в штампах, при котором течение металла в стороны во время деформирования ограничено поверхностями отдельных частей штампа. Рабочая полость штампа при замыкании его составных частей в конце штамповки ручей соответствует форме поковки (рис. 44).
По сравнению со свободной ковкой объемная штамповка имеет в 50–100 раз большую производительность; позволяет получить большую однородность и точность поковок
87
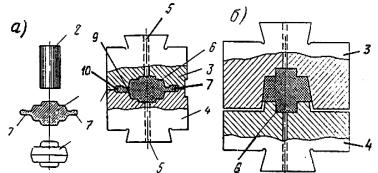
(припуски и допуски на поковку в 3–4 раза меньше, чем при ковке); дает возможность получения поковок сложной формы без напусков; обеспечивает высокое качество поверхности поковок.
|
|
|
|
|
|
|
|
|
|
|
|
5 |
|
|
|
|
|
|
|
|
|
|
|
|
|
|||||
|
|
|
|
|
|
|
|
|
|
|
|
|
|
|
|
|||||||||||||||
|
|
|
|
2 |
|
|
|
|
|
|
|
|
|
|
|
|
|
|
|
|
|
|
|
|
|
|
|
|
|
|
|
|
|
|
|
|
|
|
|
|
|
|
|
|
|
|
|
|
|
|
|
|
|
|
|
|
|
||||
|
|
|
|
|
|
|
|
|
|
|
|
|
|
|
|
|||||||||||||||
|
|
|
|
|
|
|
|
|
9 |
|
|
|
|
|
|
|
|
|
|
|
|
|
|
|
|
|
||||
|
|
|
|
|
|
|
|
|
|
|
|
|
|
|
6 |
|
|
|
|
|
|
|
|
|
|
|||||
|
|
|
|
|
|
|||||||||||||||||||||||||
|
|
|
|
|
|
|
|
|
3 |
|
||||||||||||||||||||
|
|
|
||||||||||||||||||||||||||||
|
|
|
|
|
|
|
|
|
|
|
|
|
|
|
|
|
|
|
|
|
|
|
||||||||
|
|
|
|
|
|
|
|
|
|
|
|
|
|
|
|
|
|
|
3 |
|
|
|
|
|
|
|
|
|
|
|
|
|
|
|
|
|
|
|
|
|
|
|
|
|
|
|
|
|
|
|
|
|
|
|
|
|
|
|
|||
|
|
|
|
|
|
10 |
|
|
|
|
|
|
|
|
|
|
|
|
|
|
|
|
|
|
|
|||||
|
|
|
|
|
|
|
|
|
|
|
|
|
|
|
|
|
|
|
|
|
|
|
|
|
||||||
|
|
|
|
|
|
|
|
|
|
|
|
7 |
|
|
|
|
|
|
|
|
|
|
|
|||||||
|
|
|
|
|
|
|
6 |
|
|
|
|
|
|
|
|
|
|
|
|
|
|
|
|
|
|
|
|
|||
|
|
|
|
|
|
|
|
|
|
|
|
|
|
|
|
|
|
|
|
|
|
|
||||||||
|
|
|
|
8 |
|
|
|
|
|
4 |
|
|
|
|
|
|
|
|
|
|
|
|||||||||
|
|
|
|
|
|
|
|
|
|
|
|
|
|
|
|
|
|
|
||||||||||||
|
|
|
|
7 |
|
|
|
|
|
|
|
|
|
|
|
|
|
|
|
|
|
|
|
|
|
|||||
|
7 |
|
|
|
|
|
|
|
|
|
|
|
|
|
|
|
|
|
||||||||||||
|
|
|
|
|
|
|
|
|
|
|
|
|
|
|
|
|
|
|
|
|
|
|
|
|
|
|
|
|
|
|
|
|
1 |
|
|
|
|
|
|
|
|
|
|
|
|
|
|
|
|
|
|
|
|
|
|
|
|
|
|||
|
|
|
|
|
|
|
|
|
|
|
|
|
|
|
|
|
|
|
|
|
|
|
|
|
|
|
|
|
||
|
|
|
|
|
|
|
|
|
|
|
|
|
|
|
|
|
|
|
|
|
|
|
|
|
|
|
|
4 |
|
|
|
|
|
|
|
|
|
|
|
|
|
|
|
|
|
|
|
|
|
|
|
|
|
|
|
|
|
||||
|
|
|
|
|
|
|
|
|
|
|
|
|
|
|
|
|
|
|
|
|
|
|
|
|
|
|
|
|||
|
|
|
|
|
|
|
|
|
|
|
|
|
|
|
|
|
|
|
|
|
||||||||||
|
|
|
|
|
|
|
|
|
|
|
|
|
|
|
|
|
|
|
|
|
|
|
|
|
|
|||||
|
|
|
|
|
|
|
|
|
|
|
5 |
|
|
|
|
|
6 |
|
|
|
|
|
|
|
|
|||||
|
|
|
|
|
|
|
|
|
|
|
|
|
|
|
|
|
|
|
|
|
б |
|||||||||
|
|
|
|
|
|
|
|
|
|
|
|
|
|
|
|
|
|
|
|
|
|
|
||||||||
|
|
|
|
|
|
|
|
|
|
|
|
|
|
а |
|
|
|
|
|
|
Рис. 44. Штампы для горячей штамповки: а открытый; б закрытый; 1 готовая поковка; 2 заготовка; 3 подвижная часть штампа; 4 неподвижная часть штампа; 5 канавка; 6 поков-
ка; 7 заусенец; 8 заусенечная канавка; 9 узкий мостик; 10 магазин
Горячей объемной штамповкой изготовляют заготовки для ответственных деталей автомобилей, тракторов, сельскохозяйственных машин, самолетов, железнодорожных вагонов, станков и т.д.
В качестве заготовок для горячей штамповки применяют прокат круглого, квадратного, прямоугольного профилей, а также периодический.
Недостатки объемной штамповки: сложность и дороговизна инструмента-штампа, ограниченность массы поковок (0,3…100 кг, в отдельных случаях до 3 т), так как усилия деформирования при штамповке гораздо выше, чем при ковке.
88
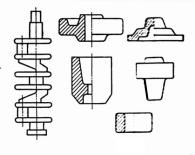
Виды штампов и способы штамповки
Различают объемную штамповку в открытых и закрытых штампах.
Штамповка в открытых штампах. В открытых штам-
пах (см. рис. 44, а) между подвижной 3 и неподвижной 4 частями штампа имеется зазор 8 заусенечная (или облойная) канавка, в которую вытекает избыточный объем 7 металла заготовки 2. Образующийся при этом заусенец (облой) затем обрезается в специальных штампах.
Штамповка в закрытых штампах (рис. 44, б) характе-
ризуется тем, что полость штампа в процессе деформирования остается закрытой. Зазор между подвижной 3 и неподвижной 4 частями штампа при этом постоянный и небольшой, так что образование заусенца в нем не предусмотрено.
При штамповке в закрытых штампах необходимо соблюдать равенство объемов заготовки и поковки, иначе при недостатке металла не заполнятся углы полости штампа, а при избытке металла размер поковки по высоте будет больше требуемого. Как правило, штамповкой в закрытых штампах получают поковки, показанные на рис. 45.
Существенное преимущество штамповки в закрытых штампах уменьшение расхода металла, более благоприятная макроструктура, так как волокна обтекают контур поковки, а не перерезаются
вместе выхода металла в заусенец. Металл деформируется
вусловиях всестороннего неравномерного сжатия при бóльших сжимающих напря-
жениях, |
чем |
в открытых |
Рис. 45. Штампованные поковки, |
штампах. |
Это |
позволяет по- |
полученные в закрытых штампах |
|
|
|
89 |
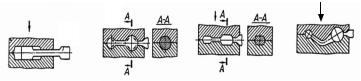
лучать большие степени деформации и штамповать малопластичные сплавы.
Поковки простой формы штампуют в одноручьевых штампах с одной полостью. Сложные поковки с резкими изменениями сечения по длине изготовляют в многоручьевых штампах с последовательным деформированием заготовки в нескольких ручьях с постепенным приближением ее к окончательной форме поковки.
Ручьи штампов в многоручьевых штампах разделяют на заготовительные и штамповочные.
Заготовительные ручьи предназначены для получения фасонной заготовки, в них металл перераспределяется для подготовки к окончательной штамповке. В заготовительных ручьях производят: осадку (обычно на плоской площадке штампа); протяжку удлинение части заготовки 1 (рис. 46, а);
1
а |
|
б |
|
в |
|
г |
|
|
|
|
|
|
|
|
|
|
|
|
|
|
Рис. 46. Схемыгорячейобъемнойштамповкиизаготовительных ручьев
подкатку местное увеличение сечения заготовки за счет утонения соседних участков (рис. 46, б); пережим уширение заготовки поперек ее оси; формовку для придания заготовке формы, приближающейся к форме поковки в плоскости разъема (рис. 46, в); гибку (рис. 46, г), а также отрубку заготовок при штамповке из прутка.
Штамповочные ручьи бывают черновые (предварительные) и чистовые (окончательные). Черновой ручей не имеет облойной канавки. Его назначение предохранить чистовой
90