
Технология конструкционных материалов. Способы получения деталей (за
.pdf– непригораемостью способностью смеси не образовывать пригар песка на поверхности отливки, который затрудняет ее механическую обработку.
Кроме того, формовочные и стержневые смеси должны быть негигроскопичными, долговечными и дешевыми.
Состав формовочных и стержневых смесей
Формовочные смеси состоят из кварцевого песка и глины. Кварцевый песок играет роль основы, а глина связующего материала. Глина улучшает огнеупорность, прочность и пластичность, но ухудшает газопроницаемость и податливость. Поэтому глину вводят не более 8…12 % по объему, остальное кварцевый песок, который обеспечивает хорошую огнеупорность и газопроницаемость. Крупнозернистый песок обеспечивает высокую газопроницаемость, но дает шероховатую поверхность отливки и повышает пригар песка. Мелкий песок дает гладкую поверхность отливки, но снижает газопроницаемость смеси. При производстве крупных отливок, где требуется отвод большого количества выделяющихся газов, применяют крупнозернистый песок, а при получении мелкого литья, где шероховатость поверхности является главным требованием, используют мелкозернистый песок.
Пригар предупреждают вводом в смесь противопригарных добавок, таких как каменноугольная пыль, тальк, графит.
Стержни работают в наиболее тяжелых условиях, так как они окружены жидким металлом со всех сторон. Поэтому стержневая смесь должна обладать более высокой прочностью, газопроницаемостью и податливостью. Глина как связующая добавка в стержневой смеси применяется только для крупных стержней простой формы. Для тонких и сложных стержней в качестве связующей добавки используют оксоль, жидкое стекло, смолы, декстрин, патоку и др. Для повыше-
31
ния газопроницаемости и податливости в стержневую смесь вводят древесные опилки или торф (2…3 %), которые в процессе сушки стержня выгорают, образуя поры.
Виды формовочных смесей и их применение
Формовочные смеси делят на облицовочные, наполнительные и единые.
Облицовочную смесь применяют при ручной формовке. Ее наносят на модель слоем толщиной 15…20 мм. Приготавливают ее из свежих песка и глины с добавкой противопригарных материалов.
Наполнительную смесь насыпают поверх облицовочной, заполняя остальную полость литейной формы. Эту смесь приготавливают из оборотной, переработанной после выбивки опок смеси с добавкой 5…10 % свежих песка и глины.
Единую смесь применяют в массовом производстве при машинной формовке для набивки всего объема литейной формы. Приготавливают ее из оборотной смеси с добавкой до 50 % свежих песка и глины.
По состоянию формыперед заливкойметалла различают:
сырые формы, которые изготавливают из большого количества оборотной смеси и применяют для неответственных отливок из чугуна, стали и цветных сплавов массой до
3000 кг;
подсушенные (полусухие) формы из облицовочной смеси, содержащей 2…4 % быстротвердеющих связующих крепителей, для получения ответственных отливок из чугуна
истали с поверхностями большой протяженности (станины, столы станков и др.);
сухие формы из смесей с повышенным содержанием глины и меньшим количеством оборотной смеси, т.е. более прочные и менее газопроницаемые и податливые. Чтобы об-
32
легчить выход газов и повысить податливость, в смеси для сухих форм вводят добавки, выгорающие при сушке (опилки, торф). Сухие формы применяют только для ответственных
икрупных (более 1000 кг) отливок из различных сплавов;
химически твердеющие формы из смеси, содержащей жидкое стекло, которое быстро твердеет при пятиминутной продувке углекислым газом. Такие смеси повышают произ-
водительность при формовке в 3 5 раз, сокращают продолжительность сушки в 10 30 раз и экономят топливо, необходимое для сушки;
самотвердеющие формы и стержни, которые изго-
тавливают из жидких самотвердеющих смесей (ЖСС). Опоки и стержневые ящики заливают смесью с химическими реагентами, переводящими смесь в жидкотекучее состояние. ЖСС хорошо заполняет все извилины формы. Отпадает необходимость в уплотнении смеси. Стержни и формы из ЖСС затвердевают по всему объему при нормальной температуре за 30…40 мин. ЖСС дают возможность механизировать
иавтоматизировать формовку, повысить точность отливок; совместить смесеприготовительное, формовочное и стержневое отделение в одном; улучшить условия труда, избавив литейный цех от шума, пыли и вибраций.
Приготовление формовочных и стержневых смесей начи-
нают с подготовки исходных материалов. Кварцевый песок сушат, просеивают и распределяют по бункерам над смесителями. Глину и каменный уголь дробят, сушат и затем тонко измельчают. Отработанную смесь регенерируют: спекшиеся куски дробят
ипропускают через магнитный сепаратор для отделения металлических включений. После подготовки все исходные компоненты смешивают в нужных пропорциях в бегунах. Увлажненная формовочная смесь выдерживается в бункерах-отстойниках 3…4 чдлявыравниваниявлажностиповсемуобъему.
33
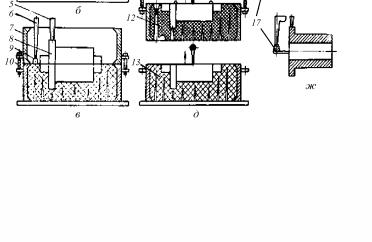
3.3. Технология ручной формовки
При изготовлении крупных отливок (станины металлорежущих станков, прокатные станы, изложницы и др.), а также в единичном и мелкосерийном производстве мелких и средних отливок широко используют ручную формовку.
Формовка в двух опоках по разъемной модели произво-
дится следующим образом:
1) для изготовления нижней полуформы на подмодельную доску 3 устанавливают нижнюю половину модели 2 и нижнюю опоку 1 (рис. 10, а);
Рис. 10. Формовка в двух опоках по модели
2)на модель наносят слой облицовочной и затем наполнительной смеси, трамбовкой уплотняют ее, излишки срезают линейкой на уровне верхней кромки опоки и накалывают душником вентиляционные каналы 4 (рис. 10, б);
3)готовую нижнюю полуформу переворачивают на
180 , устанавливают верхнюю полумодель 8, модели шлакоуловителя 9, стояка 6, выпора 5 и верхнюю опоку 7, соединив ее с нижней штырями 10 (рис. 10, в);
34
4)набивку верхней полуформы повторяют в той же последовательности, что и нижней, а затем вырезают литниковую чашу 11, удаляют из формы модели стояка 6 и выпора 5
(см. рис. 10, в, г);
5)для удаления полумоделей из полуформ верхнюю полуформу 12 снимают с нижней 13 и переворачивают ее на
180 ; формовочную смесь вокруг полумоделей смачивают водой; в полумодели забивают подъемники 14 и с их помощью полумодели удаляют из полуформ; таким же образом удаляют из формы модель шлакоуловителя 9 (см. рис. 10, в, г, д);
6)разрушенные участки полуформ исправляют; прорезают питатели 17 в нижней полуформе; устанавливают на стержневые знаки стержень 15; нижнюю полуформу накрывают верхней и нагружают грузами 16 (рис. 10, е);
7)после заливки формы металлом и его кристаллизации форму разрушают и освобождают готовую отливку вместе
слитниковой системой (рис. 10, ж).
Для деталей простой конфигурации (плиты, подкладки и др.), у которых верхняя поверхность плоская, применяют
открытую почвенную формовку. При этом способе верх изготовленной в почве формы остается открытым. Сущность формовки в том, что модель вдавливают в подготовленную постель из формовочной смеси. Затем смесь вокруг модели уплотняют трамбовкой, срезают излишки смеси, вырезают литниковый и сливной каналы. Для крупных отливок постель делают твердую. Дно утрамбованной ямы прокладывают слоем кокса толщиной 50…80 мм, из которого затем на поверхность детали выводят вентиляционные трубы. Кокс засыпают наполнительной смесью.
Безопочная формовка заключается в том, что опоки применяют только для изготовления формы. После ее сборки опоки снимают и используют для изготовления новой фор-
35
мы. Сплав заливают в форму без опоки. Способ применяют для изготовления мелких отливок. Безопочная формовка дает большую экономию, облегчается выбивка отливок.
Стержни изготавливают вручную в стержневых ящиках или по шаблонам. Стержневой ящик (см. рис. 8, в) состоит из двух половин, которые соединяют струбцинами и набивают стержневой смесью. В стержень вставляют каркас из проволоки и прокалывают сквозные вентиляционные каналы. Затем стержневой ящик раскрывают и готовый стержень отправляют в сушку.
3.4. Технология машинной формовки. Формовочные машины
Машинную формовку применяют в массовом и серийном производстве мелких и средних отливок. Она имеет ряд преимуществ перед ручной формовкой: облегчает труд формовщика; повышает производительность труда и точность отливок, что экономит 10…15 % металла за счет уменьшения припусков на обработку; уменьшает брак. Единая формовочная смесь подается в бункер, расположенный над формовочной машиной, и дозатор выдает определенную порцию смеси в опоку.
Прессовые машины наиболее производительны, так как уплотнение смеси с их помощью занимает лишь 4…5 с. В машинах с верхним прессованием (рис. 11, а) уплотняющее давление действует сверху. На столе машины 1 закрепляют модельную плиту 2 с моделью 3, устанавливают опоку 4 и на нее наполнительную рамку 5. Опоку и рамку заполняют формовочной смесью из бункера. При подъеме стола колодка 6 входит в наполнительную рамку, запрессовывая смесь в опоку. После завершения прессования стол с модельной оснасткой опускают в исходное положение.
36
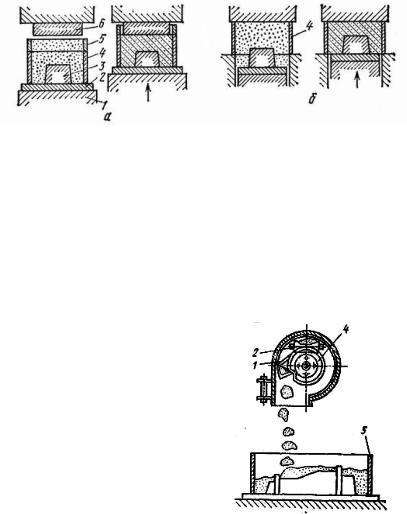
В машинах с нижним прессованием (рис. 11, б) формовочная смесьуплотняетсясамой моделью имодельнойплитой.
Недостатком этих способов прессования является неравномерность уплотнения формовочной смеси.
6 |
|
|
|
|
|
|
||
4 |
|
|
||||||
5 |
|
|
|
|
|
|
||
4 |
|
|
|
|
|
|
||
3 |
|
|
|
|
|
|
||
2 |
|
|
|
|
|
|
||
|
|
|
|
|
|
|
|
|
|
|
|
|
|
|
|
|
|
|
1 |
|
|
|
|
|
||
|
|
а |
б |
Рис. 11. Схемы прессовых машин: а верхнее прессование; б нижнее прессование
Встряхивающие машины используют для уплотнения формовочной смеси в полуформах массой от 100 кг до 40 т.
Стол, с установленными на нем модельной плитой с моделью и опокой, встряхивается, и формовочная смесь в опоке уплотняется под действием сил инерции частичек смеси.
На встряхивающих машинах уплотнение смеси по высоте опоки также неравномерное: большее около модели, меньшее в верхней части опоки. Чтобы лучше уплотнить
верхние слои смеси, на встряхи- |
|
|
|
|
|
|
|
||||
|
|
|
3 |
|
|
|
|||||
вающих |
машинах |
применяют |
|
|
|
|
|
|
|||
|
|
|
|
|
|
|
|||||
|
2 |
|
|
|
|
|
|||||
подпрессовку. |
|
|
|
|
|
|
|
|
|
||
|
|
|
|
1 |
|
|
|
|
|
||
Пескометами (рис. 12), об- |
|
|
|
|
|
|
|
||||
|
|
|
|
|
|
|
|||||
ладающими более высокой про- |
|
|
|
|
|
|
|
||||
изводительностью, |
чем |
прессо- |
|
|
|
|
|
|
|
||
|
|
|
|
4 |
|
||||||
вые и встряхивающие машины, |
|
|
|
|
|||||||
|
|
|
|
|
|
|
|||||
набивают |
крупные |
и |
средние |
|
|
|
|
|
|
|
|
формы и стержни. Пескометы |
|
|
|
|
|
|
|
||||
заполняют |
одновременно |
две |
|
|
|
|
|
|
|
||
опоки формовочной смесью, |
уп- |
|
|
|
|
|
|
|
|||
|
Рис. 12. Схема пескомета |
||||||||||
лотняют ее и обеспечивают |
по |
|
|
|
|
|
|
|
|||
|
|
|
|
|
|
|
37
всей высоте опоки равномерное уплотнение смеси. Формовочную смесь 2 подхватывают вращающиеся метательные ковши 1 (лопасти) и выбрасывают через отверстие 3 в опоку 4. Формовочная смесь хорошо и равномерно уплотняется в опоках любой высоты.
По способу извлечения модели из готовой формы
формовочные машины выпускают со штифтовым съемом готовой полуформы и с поворотной плитой. При ручной формовке точность отливки снижается от того, что перед извлечением из формы модель расталкивают в стороны. При машинной формовке точность отливки выше, так как извлечение модели из формы механизировано.
Машинная формовка стержней обеспечивает более высокую производительность и точность, чем при ручной формовке. Используют прессовые и встряхивающие машины, а также пескометы. Для изготовления стержней применяют также мундштучные, пескодувные и пескострельные машины.
Мундштучные машины применяют для изготовления стержней простой формы с постоянным поперечным сечением по длине. Стержневая смесь вытесняется поршнем через мундштук, и стержень разрезается на части.
На пескодувных машинах изготавливают стержни любой сложности. В пескодувный резервуар стержневая смесь поступает из бункера, транспортируется сжатым воздухом, заполняет стержневой ящик и одновременно уплотняется. Производительность машины 240…360 стержней в час.
Более широко применяют пескострельные машины. Они более производительные. Пескодувные и пескострельные машины можно применять также при набивке опок.
38
3.5. Заливка форм, выбивка отливок и стержней, обрубка и очистка отливок
Заливка форм
При заливке формы струя жидкого металла может: размыть поверхность формы, в результате в отливке образуются земляные раковины; сдвинуть или поднять стержень, что приведет к искажению конфигурации отливки; гидростатическим давлением раздать плохо уплотненную смесь, что увеличит размеры и массу отливки; образовать газовые раковины в отливке за счет быстрого скопления газов и паров в форме при испарении влаги и сгорании органических добавок в смеси.
Недостаточно перегретый расплав плохо заполняет щелевидные полости формы, вызывая брак отливки в виде недоливов. Слишком перегретый металл приводит к образованию усадочных и газовых раковин и увеличивает пригар формовочной и стержневой смеси. Оптимальная температура заливки в форму расплава составляет: для стального литья
1390…1550 С, чугунного 1220…1400 С.
Расплав перед заливкой в формы выдерживают в ковше для выделения газов и всплывания шлака. Заливку производят, не прерывая струи для предупреждения охлаждения и окисления расплава, засасывания воздуха и шлака в полость формы.
Выбивка отливок и стержней
Выбивка отливок. Мелкие и средние отливки выбивают из форм на выбивных решетках. Форму ставят на выбивную решетку, которая вибрирует, форма подбрасывается и соударяется с решеткой. Смесь проходит сквозь решетку, а опока с отливкой остается на решетке.
39
Выбивка стержней. Стержни из отливок выбивают на пневматических вибрационных машинах. Отливку прижимают к упору. При вибрации стержень разрушается и высыпается из отливки.
Крупные стержни вымывают из отливки мощной струей воды, используя гидравлические установки.
Обрубка и очистка отливок
Обрубка отливок. После освобождения отливки из формы и выбивки стержней производят удаление литниковой системы и прибылей.
В отливках из чугуна литниковая система и прибыли легко отбиваются молотком, а из стали и цветных сплавов их удаляют эксцентриковыми прессами-кусачками, ленточными или дисковыми пилами, а также газокислородной резкой. Заливы или неровности на отливке обрубают пневматическим зубилом или зачищают абразивным кругом.
Очистка отливок. Очистку отливки от пригоревшей формовочной смеси производят вручную стальными щетками или пневматическим зубилом.
Мелкие отливки загружают вместе со звездочками из белого чугуна во вращающийся барабан, и при взаимном трении одна о другую, а также о звездочки отливки очищаются от пригоревшей формовочной смеси. При пневматической пескоструйной и дробеструйной очистке отливок струя сжатого воздуха сильно раздувает пыль, поэтому чаще используют механическую дробеметную очистку потоком стальной или чугунной дроби.
Виды брака и контроль качества отливок
Основные виды брака. Брак отливок делят на исправимый и неисправимый. Отливки с неисправимым браком направляют на переплавку, а исправимый брак устраняют. Основными видами брака являются:
40