
Суперфинишные станки для автомобильной промышленности
..pdfКинематическое условие составим в системе S0. После преобразований оно примет вид
(Rкр cosεctgε − u)sin λ cosϑ + |
|
+ (Acosλ + psin λ)cosε sin ϑ + |
(5.45) |
+ ( p cosλ − Asin λ)sin ε = 0, |
|
где Rкр – максимальный радиус конического шлифовального круга; u, ϑ – криволинейные координаты конической поверхности круга; ε – угол профиля шлифовального круга.
Преобразуем уравнение (5.45) в квадратное уравнение относительно параметра ϑ:
( p cosλ − Asin λ)sin ε − (R |
cosεctgε − u)sin λ tg2 ϑ |
+ |
||||
|
кр |
|
|
|
2 |
|
|
|
|
|
|
|
|
|
+2(Acosλ + psin λ)cosεtg |
ϑ |
+ |
|
(5.46) |
|
|
|
|
2 |
|
|
+(Rкр cosεctgε − u)sin λ + ( p cosλ − Asin λ)sin ε = 0.
Вокончательном виде осевое сечение валка опишется уравнениями:
( p cosλ − Asin λ)sin ε − (R |
cosεctgε − u)sin λ |
tg2 ϑ |
+ |
|
|
||||
|
|
кр |
|
|
|
2 |
|
|
|
|
|
ϑ |
|
|
|
|
|
|
|
|
|
|
|
|
|
|
|
|
|
+ 2(Acosλ + psin λ)cosεtg 2 |
+ |
|
|
|
|
|
|
||
+ (Rкр cosεctgε − u)sin λ + ( p cosλ − Asin λ)sin ε = 0; |
|
|
|
|
|||||
|
|
|
(5.47) |
||||||
|
|
u sin ε sin ϑcosλ − (Rкрctgε − u cosε)sin λ |
|
|
|
|
|
||
tgϕ = |
; |
|
|
|
|
|
|||
u sin ε cosϑ + A |
|
|
|
|
|||||
|
|
|
|
|
|
|
|
||
|
= u sin ε cosϑ + A ; |
|
|
|
|
|
|
|
|
X2 |
|
|
|
|
|
|
|
||
|
|
cosϕ |
|
|
|
|
|
|
|
Z2 = u sin ε sin ϑsin λ + (Rкрctgε − u cosε)cosλ − pϕ. |
|
|
|
|
|||||
|
|
|
|
На рис. 5.25 и в табл. 5.7 приведен пример моделирования шлифования профиля валка из табл. 5.3. Исходные данные: мак-
161
Стр. 161 |
ЭБ ПНИПУ (elib.pstu.ru) |
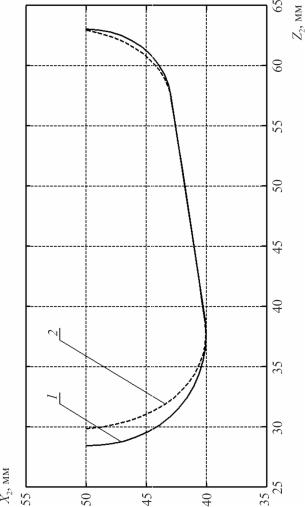
валка для обработки конических поверхностей: |
2 – профиль, полученный при моделировании |
Рис. 5.25. Осевой профиль |
1 – расчетный профиль; |
162
Стр. 162 |
ЭБ ПНИПУ (elib.pstu.ru) |
163 .Стр
ru).pstu.(elib ПНИПУ ЭБ
163
Таблица 5 . 7 Профиль валка для конических поверхностей, полученный при шлифовании
Номер |
Параметры |
Координаты |
Номер |
Параметры |
Координаты |
|||||
профиля |
профиля |
|||||||||
точки |
|
|
точки |
|
|
|||||
|
|
|
|
|
|
|
|
|||
ϑ, град |
u, мм |
Z2, мм |
X2, мм |
ϑ, град |
u, мм |
Z2, мм |
X2, мм |
|||
1 |
164,30 |
– |
–7,903 |
49,990 |
13 |
– |
605,867 |
8,405 |
41,194 |
|
2 |
166,54 |
– |
–7,529 |
47,565 |
14 |
– |
604,265 |
10,279 |
41,475 |
|
3 |
168,78 |
– |
–6,878 |
45,407 |
15 |
– |
602,664 |
12,151 |
41,761 |
|
4 |
171,02 |
– |
–5,946 |
43,559 |
16 |
– |
601,062 |
14,020 |
42,050 |
|
5 |
173,26 |
– |
–4,746 |
42,064 |
17 |
– |
599,461 |
15,887 |
42,344 |
|
6 |
175,50 |
– |
–3,315 |
40,960 |
18 |
– |
597,859 |
17,751 |
42,642 |
|
7 |
177,74 |
– |
–1,712 |
40,282 |
19 |
– |
596,258 |
19,613 |
42,944 |
|
8 |
179,98 |
– |
–0,015 |
40,050 |
20 |
179,44 |
– |
20,385 |
43,133 |
|
9 |
– |
612,273 |
0,887 |
40,112 |
21 |
181,92 |
– |
21,864 |
43,889 |
|
10 |
– |
610,671 |
2,770 |
40,376 |
22 |
184,40 |
– |
23,154 |
45,119 |
|
11 |
– |
609,070 |
4,651 |
40,644 |
23 |
186,88 |
– |
24,194 |
46,785 |
|
12 |
– |
607,468 |
6,529 |
40,917 |
24 |
189,36 |
– |
24,949 |
48,839 |
симальный радиус круга Rкр = 100,0 мм; шаг винтовой линии р = 40,0 мм. Наладочные параметры: межосевое расстояние А = 140,05 мм; угол перекрещивания осей валка и круга λ = 26°54′30″; угол профиля круга ε = 9°24′; ширина круга l1 = 15,8 мм. Полученные при шлифовании параметры профиля
валка: β1 = 8°36′6″; f1 = –0,056 мм; h1 = 8,7 мм; h2 = 5,6 мм.
Для формообразования нелинейчатой винтовой поверхности шлифовальным кругом с конической производящей поверхностью требуется решение задачи параметрической оптимизации в рамках уравнений (3.51). При этом необходимо обеспечить заданный минимальный радиус валка и угол профиля β1. Величина стрелы прогиба f1 может быть больше заданной, но того же знака (направлена в тело валка). Ширина переходных кривых h1 и h2 должна укладываться в конструктивные размеры валка, полученные при профилировании. В качестве оптимизируемых параметров выступают: межосевое расстояние А, угол перекрещивания λ, угол профиля круга ε. Также необходима коррекция ширины l1 шлифовального круга по сравнению с шириной l рабочего участка валка. Шаг винтовой линии р принимают равным шагу винта валка. Максимальный радиус круга Rкр выбирают по технологическим соображениям.
На основе численного анализа наладочных параметров при шлифовании валка получены следующие результаты. Увеличение углов λ и ε приводит к увеличению угла профиля β1 валка, величины стрелы прогиба f1 и уменьшению ширины h1, h2 переходных кривых. Снижение радиуса круга Rкр вызывает уменьшение параметров f1, h1, h2, а на угол β1 оказывает неоднозначное влияние. Увеличение наладочного параметра А при прочих равных условиях способствует уменьшению параметров f1, h1, h2 и слабо влияет на угол β1.
Стр. 164 |
ЭБ ПНИПУ (elib.pstu.ru) |
6. ФОРМООБРАЗОВАНИЕ ПОПЕРЕЧНОГО СЕЧЕНИЯ ЗАГОТОВОК ПРИ СУПЕРФИНИШИРОВАНИИ
6.1.Общий подход к обеспечению точности формы
впоперечном сечении заготовок
Бесцентровой абразивной обработке присущи сложные фи- зико-механические и геометро-кинематические закономерности формообразования. В общем случае при обеспечении точности следует учитывать большое число различных по математическому и физическому описанию факторов. Многие из этих факторов неуправляемы при обработке, другие же сложно формализовать или требуются экспериментальные исследования. Анализ некоторых физических факторов требует дополнительного установления их функциональной связи с параметрами качества обрабатываемых деталей. Указанные сложности привели к тому, что реализация системного подхода представляет собой трудно разрешимую задачу. Поэтому в настоящее время известны многочисленные частные математические и физические модели, как правило, с одним критерием оптимальности и ограниченным числом учитываемых параметров.
Точность формы поверхностей вращения зависит от точности двух основных элементов – образующей и направляющей. Образующая в общем случае может иметь произвольную форму, но на практике чаще всего представляет собой прямую (цилиндрические и конические поверхности) или окружность (сферические и тороидальные поверхности). Для нормирования точности формы в продольном сечении используют комплексный показатель – отклонение профиля продольного сечения.
Идеальная форма поперечного сечения тела вращения представляет собой круг. Точность формы в поперечном сечении нормируют с помощью комплексного показателя – отклонения от круглости, а также частных видов отклонений – овальности и огранки.
165
Стр. 165 |
ЭБ ПНИПУ (elib.pstu.ru) |
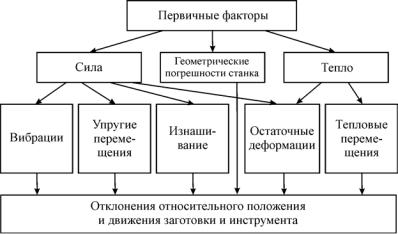
Любое технологическое воздействие имеет соответствующую физическую природу, определяющую характер взаимодействия элементов технологической системы. Многочисленные исследования точности машин [1, 3, 4, 11, 16 и др.] показали, что большинство факторов влияют на погрешности через силу и тепло. Последние, в свою очередь, вызывают различного рода перемещения элементов ТС и тем самым нарушают заданное относительное положение или движение элементов ТС. Первичные факторы через силу и тепло воздействуют на заготовки, вызывая их тепловые и упругие перемещения, изнашивание, остаточные деформации и вибрации (рис. 6.1). К первичным факторам также можно отнести геометрические погрешности элементов станка, которые непосредственно влияют на нарушение относительного движения инструмента и заготовки.
Рис. 6.1. Влияние первичных факторов на точность обработки
Наиболее известен расчетно-аналитический метод определения суммарной погрешности механической обработки, созданный научными школами А.П. Соколовского и В.М. Кована, который опирается на принцип суперпозиции. Действие каждой из составляющих погрешности рассматривается независимо от
166
Стр. 166 |
ЭБ ПНИПУ (elib.pstu.ru) |
других, а суммарная погрешность складывается суммированием элементарных по определенным правилам. Метод оправдывает себя в очень жестко регламентированных условиях, когда параметры технологических процессов не изменяются или изменяются незначительно. В общем случае суммарная погрешность формируется из первичных погрешностей, общее число которых превышает 20.
Функциональные связи геометрических, кинематических и силовых параметров формообразования и геометрии деталей при бесцентровой абразивной обработке показаны на рис. 6.2.
Экспериментальными исследованиями установлена значительная склонность бесцентрового шлифования и суперфиниширования к технологическому наследованию погрешностей формы поверхностей заготовок. Технологическим наследованием называют явление переноса свойств объектов от предшествующих технологических операций к последующим. Научный анализ вопросов технологического наследования пока не нашел в технической литературе [1, 3, 4] достаточно полного отражения. Представление процесса наследования обычно воспринимается как процесс детерминированный. Это означает, что при одном и том же комплексе исходных параметров при каждом последующем повторении операций будет возникать один и тот же результат. Вместе с тем становится очевидным, что детерминированный подход к явлению несколько обедняет его представление. Более полным должен быть учет случайного фактора. Действительно, любой технологический процесс характеризуется целым рядом параметров, которые имеют случайный характер. Все эти параметры случайным образом суммируются в ходе технологического процесса, поэтому и результат представляется случайной величиной.
Основными моментами технологической наследственности являются установление факта переноса определенного свойства от предшествующей операции к последующим, а также количественная сторона вопроса. Объективное существование наследственных связей не означает, что во всех случаях их необходимо
167
Стр. 167 |
ЭБ ПНИПУ (elib.pstu.ru) |
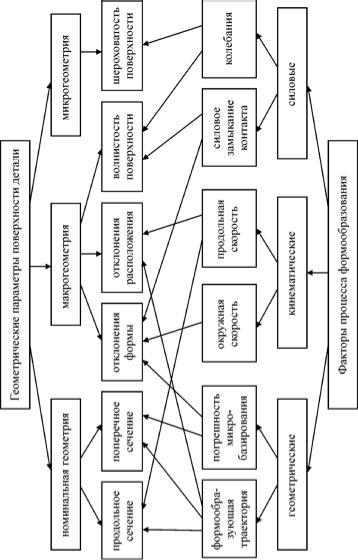
Функциональные связи параметров формообразования и геометрии деталей |
при бесцентровом суперфинишировании |
Рис. 6.2. |
|
168
Стр. 168 |
ЭБ ПНИПУ (elib.pstu.ru) |
учитывать. Если, например, речь идет об изготовлении машиностроительных изделий нормальной точности, наследственная доля погрешности может оказаться сравнительно малой. Основными будут традиционные погрешности, характерные для большинства технологических процессов изготовления машин. В тех же случаях, когда допустимые погрешности должны быть малыми по величине и их устранение представляется достаточно сложной технологической задачей, наследственная доля допуска может не только быть соизмеримой с допуском, но и превосходить его. Следовательно, закономерности технологического наследования необходимо использовать прежде всего в прецизионном машиностроении.
Анализ литературных данных, экспериментальные исследования и многолетний опыт эксплуатации станков в подшипниковой промышленности показали, что вклад геометрических, кинематических и силовых факторов при бесцентровом шлифовании составляет примерно 50 %.
Предлагаемая методология исследований рассматривает процесс формообразования с декомпозицией на подсистемы и описание их детерминированными и стохастическими моделями. Основной является формообразующая подсистема, заданная детерминированными геометрическими, кинематическими и силовыми параметрами. Именно в этой подсистеме формируются показатели технологической надежности. Влияние других подсистем рассматривается в виде возмущающих воздействий. В большинстве случаев они имеют стохастическую природу.
Для анализа процесса формообразования создана система критериальных оценок точности обработки через параметры наладки оборудования, включающая: результирующий вектор отклонений формообразующей траектории; приведенную погрешность базирования; статистические коэффициенты исправления формы заготовок. Результирующий вектор отклонений траектории заготовок относительно инструмента определяется по детерминированным геометрическим моделям с учетом погрешностей элементов формообразующей подсистемы станка и точности ус-
169
Стр. 169 |
ЭБ ПНИПУ (elib.pstu.ru) |
тановки наладочных параметров. Приведенная погрешность базирования представляет собой безразмерный коэффициент, показывающий отношение среднеарифметического значения (САЗ) мгновенных погрешностей базирования при перемещении заготовки к отклонению формы заготовки, вызывающей эту погрешность. Статистические коэффициенты исправления формы заготовок (как правило, среднеарифметическое значение и среднеквадратическое отклонение (СКО)) формируются на основании экспериментальных данных или в результате моделирования по методу Монте-Карло с учетом стохастической природы этих данных. При минимизации целевой функции основной критерий выбирается по максиминному принципу, а остальные критерии становятся ограничениями задачи.
Задача обеспечения точности решается на этапах проектирования, наладки станков, обработки, измерения и подналадки станков на основе оптимизации (рис. 6.3). На этапе проектирования выполняют расчет формообразующих элементов: профилирование ведущего круга бесцентровых шлифовальных станков и валков суперфинишных станков, расчет параметров устройства правки абразивных кругов, формообразование валков суперфинишного станка.
На этапе наладки в первую очередь определяют кинематические и силовые параметры процесса, их изменение в зависимости от геометрической наладки станка. Устанавливают влияние точности наладочных параметров на погрешности относительной траектории заготовки и инструмента. При суперфинишировании различных деталей на валках постоянного профиля рассчитывают параметры формообразующей траектории.
Измерительная задача при исследовании процессов образования погрешностей в условиях технологического наследования состоит в том, чтобы построить измерение не величины, а процесса и оценить возможные погрешности измерения процесса. Методологическая основа такого подхода к решению задачи измерения состоит в том, что процесс, с точки зрения классификации причин появления погрешностей, можно представить как
170
Стр. 170 |
ЭБ ПНИПУ (elib.pstu.ru) |