
Суперфинишные станки для автомобильной промышленности
..pdfруются исходные погрешности геометрической формы заготовки. Из-за инерционности суперфинишной головки она не успевает полностью копировать форму заготовки и вносит небольшое исправление, которое зависит в основном от радиальных давлений брусков и жесткости технологической системы.
При микрофинишировании (рис. 2.5, б) брусок прижимают к детали непосредственно гидроцилиндром или через промежуточные жесткие звенья, например клинорычажный механизм. При этом достигают съема металла до 30–50 мкм на диаметр. С учетом свойства сжимаемости воздуха во многих микрофинишных станках применен непосредственный пневмоприжим брусков без пружины. На станках фирмы Telenhaus постоянный прижим брусков обеспечивают клапаном давления.
Вбольшинстве современных суперфинишных станков реализована схема прижима с противодавлением, сущность которой заключается в изменении давления в зависимости от съема металла. Примером может служить инструментальная головка суперфинишного станка 3Д871Б [24], приведенная на рис. 2.6. Она представляет собой гидравлический цилиндр 9, на штоке 8 которого закреплена державка 12 с бруском. Шток 8 и поршень 7 выполнены раздельно, что обеспечивает свободное перемещение штока и не требует соблюдения строгой соосности между цилиндром 9 и крышкой 10. Положение бруска фиксируют ромбовидным пальцем 11. Инструментальную головку крепят двумя винтами и планкой 6 на каретке механизма осциллирования станка.
Вштоковую полость цилиндра через отверстие 5 постоянно подводят масло, создающее усилие противодавления и удерживающее брусок в верхнем положении. При подаче масла в отверстие 3 золотник 2 поднимается в верхнее положение, открывается (опускается) обратный клапан 4 и через отверстия, расположенные на его конусе, масло поступает на торец поршня 7, прижимая брусок к детали. Давление в бесштоковой полости постоянно, благодаря чему брусок всегда прижат к детали, производя равномерный съем припуска.
41
Стр. 41 |
ЭБ ПНИПУ (elib.pstu.ru) |
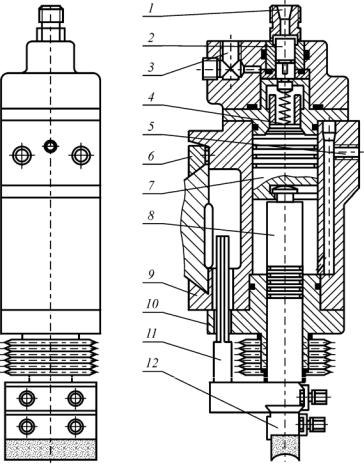
Рис. 2.6. Инструментальная головка суперфинишного станка 3Д871Б
При обработке детали, имеющей погрешности формы в поперечном сечении, брусок будет отжиматься вверх. При этом обратный клапан 4 закрывается, давление на брусок, а следовательно, и на деталь увеличивается. Таким образом увеличивается съем металла и происходит исправление геометрии детали. Для того чтобы поднять брусок вверх, необходимо перекрыть отверстие 3, а масло подавать через отверстие 1. Золотник 2 при
42
Стр. 42 |
ЭБ ПНИПУ (elib.pstu.ru) |
этом опускается вниз, нажимает на обратный клапан 4 и открывает его. Этим обеспечивается слив масла из бесштоковой полости в отверстие 3. Поршень 7 под действием противодавления поднимается вверх и одновременно поднимает брусок.
2.2. Выбор абразивного инструмента для суперфиниширования
Выбор характеристики брусков. Результаты суперфиниши-
рования во многом зависят от правильности выбора характеристики брусков и рациональности режимов резания, так как только в этом случае обеспечиваются необходимая точность, максимальная производительность и минимальный расход брусков. Абразивные инструменты могут обрабатывать различные по твердости материалы и обладают способностью самозатачиваться. Восстановление режущей способности в процессе работы (самозатачивание) происходит в результате обламывания, выкрашивания и вырывания зерен в случае, когда сила резания превосходит прочность зерен или силу их сцепления со связкой. В зависимости от характеристики брусков, режимов резания и обрабатываемого материала свойство самозатачиванияпроявляетсяпо-разному.
Шлифовальные бруски характеризуют следующими основными параметрами: абразивный материал, зернистость, материал связки, твердость, концентрация (для алмазных и эльборовых брусков), геометрическая форма и размеры.
При суперфинишировании наибольшее распространение получили бруски, изготовленные из электрокорунда белого (марок 24А, 25А) и карбида кремния зеленого (марок 63С, 64С). При обработке закаленных сталей используют оба этих материала, а при обработке чугуна и вязких материалов – бруски из карбида кремния зеленого. В отдельных случаях для получения шероховатости Rа = 0,04…0,02 мкм применяют бруски из хромистого электрокорунда (марок33А, 34А) зернистостьюМ3-М1.
Согласно ГОСТ 3647–80 шлифовальные материалы должны иметь следующую зернистость:
43
Стр. 43 |
ЭБ ПНИПУ (elib.pstu.ru) |
шлифзерно – 200, 160, 125, 100, 80, 63, 50, 40, 32, 25, 20, 16; шлифпорошки – 12, 10, 8, 6, 5, 4; микропорошки – М63, М50, М40, М28, М20, М14;
тонкие микропорошки – М10, М7, М5, М3, М2, М1.
В зависимости от процентного содержания основной фракции обозначение зернистости дополняют буквенными индексами В, П, Н, Д.
Согласно ГОСТ 2456–82 шлифовальные бруски на керамической и бакелитовой связках должны изготавливаться из абразивных материалов и иметь зернистость, указанную в табл. 2.1. Однако стандарт допускает выпускать бруски из других групп шлифовальных материалов и с другой зернистостью.
Таблица 2 . 1
Выбор марки и зернистости шлифовальных брусков
(ГОСТ 2456–82)
Абразивный материал |
Марка материала |
Зернистость |
|
Электрокорунд белый |
25А |
25-5 |
|
24А, 23А |
25-М7 |
||
|
|||
Карбид кремния зеленый |
64С, 63С |
16-М7 |
В соответствии с ГОСТ 19202–80 установлена следующая шкала твердости абразивного инструмента:
ВМ1, ВМ2 – весьма мягкий; М1, М2, М3 – мягкий; СМ1, СМ2 – среднемягкий; С1, С2 – средний;
СТ1, СТ2, СТ3 – среднетвердый; Т1, Т2 – твердый; ВТ – весьма твердый;
ЧТ – чрезвычайно твердый.
Цифры 1, 2, 3 справа от буквенного обозначения дополнительно определяют твердость абразивного инструмента в порядке ее возрастания. Определение и контроль твердости производят на приборе Роквелла типа ТР (ГОСТ 23677–79).
44
Стр. 44 |
ЭБ ПНИПУ (elib.pstu.ru) |
Структуру абразивного инструмента характеризуют содержанием абразивного материала в единице его объема. Абразивные инструменты изготавливают со структурами от № 1 до № 12. Чем выше номер структуры, тем больше связки и меньше зерен в единице объема инструмента. Структуры № 1–4 называют закрытыми (плотными), №5–8 – средними, №9–12 – открытыми.
Шлифовальные бруски, используемые при суперфинишировании, изготавливают на керамической (К) и бакелитовой (Б) связках. Наибольшее распространение получили бруски на керамической связке, которая обеспечивает интенсивное самозатачивание бруска. Керамическая связка, обладая большой жесткостью, позволяет абразивным зернам внедряться на большую глубину и производить интенсивное резание. Упругая и эластичная бакелитовая связка не допускает значительного внедрения абразивного зерна в металл, так как наиболее выступающие зерна, внедряясь в металл, одновременно вдавливаются в связку, предоставляя возможность следующему ряду зерен участвовать в работе. Таким образом, увеличивается количество абразивных зерен, участвующих в работе, и одновременно уменьшается удельное давление. Малая глубина внедрения зерен дает малый съем металла и создает условия для быстрого перехода к режиму полирования.
Керамическая связка имеет значительную химическую стойкость и водостойкость, может работать с любым видом СОЖ и без охлаждения, позволяет получать абразивный инструмент любой зернистости и твердости. Шлифовальные бруски на керамической связке изготавливают методами прессования и литья. Недостатком керамической связки является ее хрупкость, которая при увеличении частоты колебаний бруска в ряде случаев приводит к скалыванию его кромок. Для уменьшения хрупкости и устранения сколов применяют пропитку брусков серой.
Литые бруски имеют ряд преимуществ по сравнению с прессованными: обладают высокой однородностью структуры и большим количеством режущих зерен на их рабочей поверхности, быстро и хорошо прирабатываются в поверхности детали,
45
Стр. 45 |
ЭБ ПНИПУ (elib.pstu.ru) |
равномерно изнашиваются и хорошо самозатачиваются. Все это обеспечивает длительное сохранение режущей способности бруска, увеличивая съем металла в 1,6–2,8 раза по сравнению с прессованными брусками той же зернистости. Применение литых брусков, обладающих равномерным распределением зерен и связки с малыми колебаниями твердости, позволяет получить низкую шероховатость поверхности Ra = 0,032…0,020 мкм.
Бакелитовая связка имеет более высокую прочность и упругость, чем керамическая, но обладает невысокой теплостойкостью (примерно 200 °С) и недостаточной устойчивостью к воздействию СОЖ. При использовании СОЖ, содержащей более 1,5 % щелочей, абразивный инструмент на бакелитовой связке «размокает», несколько теряя при этом твердость и прочность.
При суперфинишировании деталей из специальных сталей и сплавов, отличающихся большой пластичностью и малой твердостью (коррозионно-стойкие стали, жаропрочные сплавы и др.), рекомендуют предварительную обработку производить брусками на керамической связке, а окончательную для достижения шероховатости Ra = 0,063…0,020 мкм – брусками на бакелитовой связке с графитом. Графит, введенный в бакелитовую связку, предотвращает налипание металла на брусок. Также бруски с графитовым наполнителем применяют для получения поверхностей с низкой шероховатостью. Съем металла при обработке этими брусками минимален. Такие бруски вырезают из шлифовальных кругов, изго- тавливаемыхпоОСТ2-И70-1–78 на связке ГФ.
Обработка алмазными брусками значительно повышает производительность суперфиниширования, так как их период стойкости в десятки раз выше, чем у обычных абразивных брусков. Алмазные зерна долгое время сохраняют свои режущие свойства, что обеспечивает более интенсивный съем металла. Алмазные бруски представляют собой державку с нанесенным на нее рабочим алмазоносным слоем, который состоит из зерен природных или синтетических алмазов, связки и наполнителя. Алмазные бруски характеризуют: маркой материала, зернистостью, связкой, твердостью и концентрацией алмаза.
46
Стр. 46 |
ЭБ ПНИПУ (elib.pstu.ru) |
Согласно ГОСТ 9206–80Е марки алмазных порошков имеют следующие обозначения:
1) из зерен природных алмазов: А – шлифпорошки; АМ – микропорошки;
АН – микропорошки с повышенной абразивной способностью;
2) из зерен синтетических алмазов: АС – шлифпорошки; АСМ – микропорошки;
АСН – микропорошки с повышенной абразивной способностью;
АР – шлифпорошки из синтетических поликристаллических алмазов.
Вкачестве связки в алмазных брусках применяют керамические, органические (бакелитовые) и металлические связующие вещества. Алмазные бруски выпускают с 50-, 100- и 150%-ной концентрацией алмазов. При 100%-ной концентрации алмазов
в1 мм3 алмазоносного слоя содержится 4,89 карата (0,878 мг) алмазного порошка. Это составляет 25 % объема алмазоносного слоя, остальные 75 % объема занимают связка и наполнитель. При 50%-ной концентрации алмазного порошка будет соответственно в два раза меньше.
Восновном алмазные бруски изготавливают на металлических связках марок М1-М3. Освоено также производство брусков на металлосиликатных связках марок МС и МК, эластичных органических и никелевых связках. Эластичные бруски изготавливают на каучукосодержащихсвязкахмарокР4, Р9, Р11, Р13, Р14.
При суперфинишировании применяют также шлифовальные бруски из эльбора. Преимуществами эльбора перед алмазом, как инструментальным материалом, являются его высокая
теплостойкость (1300–1400 °С) и диффузионная устойчивость. Эльборовые бруски характеризуют: маркой материала, зернистостью, связкой, твердостью и концентрацией эльбора. Бруски из эльбора на керамической связке целесообразно использовать
47
Стр. 47 |
ЭБ ПНИПУ (elib.pstu.ru) |
при обработке заготовок высокой твердости, в первую очередь из легированных сталей, имеющих в своей структуре карбиды, нитриды и другие составляющие, твердость которых близка к твердости обычных абразивных материалов. Так, при суперфинишировании азотированной и цементированной сталей интенсивность съема металла брусками из эльбора в 1,4–1,5 раза, а при обработке быстрорежущей стали в 5–7 раз выше, чем брусками из карбида кремния. Характерной особенностью брусков из эльбора является их высокая стойкость.
Шлифзерно и шлифпорошки эльбора выпускают двух марок: ЛО – обычной механической прочности и ЛП – повышенной механической прочности. Микропорошки производят также двух марок: ЛВМ – с высоким содержанием основной фракции и ЛПМ – с повышенным содержанием основной фракции.
Согласно ОСТ 2-МТ79-2–75 зернистость эльбора имеет следующие обозначения:
шлифзерно – Л20, Л16; шлифпорошки – Л12, Л10, Л8, Л5, Л4;
микрошлифпорошки – ЛМ63, ЛМ50, ЛМ40, ЛМ28, ЛМ20,
ЛМ14, ЛМ10, ЛМ7, ЛМ5;
особо тонкие микрошлифпорошки – ЛМ3, ЛМ1. Применение алмазных и эльборовых брусков экономически
выгодно при обработке заготовок из твердых сплавов и закаленных сталей с высокой твердостью, имеющих высокую исходную шероховатость, крупногабаритных деталей (шпинделей, валков бумагоделательных машин, прокатных станов и др.), а также в условиях массового производства, когда износ брусков велик и затрачивается значительное время на их смену.
Высокая режущая способность алмазных и эльборовых брусков затрудняет получение низкой шероховатости поверхности и наиболее благоприятного микрорельефа поверхности, так как процесс суперфиниширования трудно перевести в режим тре- ния-полирования. В то же время повышение производительности обработки и стойкости брусков является актуальной задачей на предварительных операциях при съеме увеличенных припусков (10–20 мкм). Большое влияние на свойства алмазного инст-
48
Стр. 48 |
ЭБ ПНИПУ (elib.pstu.ru) |
румента оказывают механические свойства связки. Чаще всего не удается полностью использовать возможности алмазных зерен: когда связка слишком мягкая, то она быстро изнашивается, и алмазные зерна выкрашиваются слишком рано.
Хорошие результаты при суперфинишировании закаленных сталей показывают бруски без связки, получаемые прессованием абразивных зерен ударной волной [29]. Данная технология позволяет изготавливать инструмент без связки более прочным (в 2–2,5 раза), чем традиционные абразивные инструменты. Это приводит к многократному повышению стойкости шлифовальных брусков. Кроме того, большое количество зерен, участвующих в работе резания, способствует одновременному повышению производительности и снижению шероховатости поверхности.
Рекомендации по выбору абразивного материала и связки брусков приведены в табл. 2.2.
Таблица 2 . 2
Выбор абразивного материала и связки брусков для суперфиниширования
Обрабатываемый материал |
Абразивный материал |
Связка |
Стали незакаленные, цветные |
электрокорунд белый |
керамическая |
марок 23А, 24А, 25А |
|
|
сплавы, нержавеющая сталь |
карбид кремния зеле- |
керамическая |
|
ный марок 63С, 64С |
|
Конструкционные и легиро- |
карбид кремния зеле- |
керамическая |
ванные стали закаленные |
ный марок 63С, 64С |
|
Высоколегированные и инст- |
|
керамическая, |
рументальные стали закален- |
алмаз |
бакелитовая, |
ные |
|
металлическая |
Стали закаленные (оконча- |
электрокорунд хроми- |
керамическая |
стый марок 33А, 34А |
|
|
тельная обработка) |
карбид кремния зеле- |
бакелитовая |
|
ный марок 63С, 64С |
с графитом |
Твердые сплавы, керамика |
эльбор |
керамическая |
Чугун, цветные металлы |
карбид кремния зеле- |
керамическая |
|
ный марок 63С, 64С |
|
|
|
49 |
Стр. 49 |
ЭБ ПНИПУ (elib.pstu.ru) |

На выбор характеристики бруска влияют следующие факторы: марка обрабатываемого материала и его твердость, исходная шероховатость поверхности заготовки, требуемая шероховатость поверхности детали после обработки.
Выбор зернистости шлифовального бруска производят в зависимости от исходной и требуемой шероховатости поверхности (табл. 2.3). Чем грубее исходная поверхность, тем крупнее должна быть выбрана зернистость брусков. Увеличение зернистости приводит к увеличению производительности, но одновременно увеличивается и шероховатость обработанной поверхности. В случае, когда заданную шероховатость можно получить брусками смежных зернистостей, применяют более крупнозернистые бруски, обеспечивающие более интенсивный съем металла. При работе в несколько переходов зернистость брусков последовательно уменьшают. Меньшая шероховатость поверхности достигается с помощью литых брусков. Например, для получения шероховатости Ra = 0,32…0,16 мкм можно применять как прессованные бруски зернистостью М40, М28, так и литые бруски зернистостью М14.
Таблица 2 . 3
Выбор зернистости шлифовальных брусков в зависимости от требуемой шероховатости поверхности
Исходная |
Требуемая шероховатость поверхности Ra, мкм |
||||
шерохова- |
0,63…0,32 |
0,32…0,16 |
0,16…0,08 |
0,08…0,04 |
0,04…0,02 |
тость Ra, мкм |
|||||
2,5…1,25 |
М40 |
М40, М28 |
М28, М20 |
– |
– |
1,25…0,63 |
М40 |
М28, М14 |
М20, М14 |
М14 |
– |
0,63…0,32 |
– |
М20, М14 |
М14, М10 |
М14, М10 |
М10 |
0,32…0,16 |
– |
– |
М14, М10 |
М10, М7 |
М7 |
0,16…0,08 |
– |
– |
– |
М7 |
М7 |
В табл. 2.4 приведены данные об интенсивности съема металла при суперфинишировании сталей брусками из карбида кремния зеленого и эльбора.
50
Стр. 50 |
ЭБ ПНИПУ (elib.pstu.ru) |