
Суперфинишные станки для автомобильной промышленности
..pdf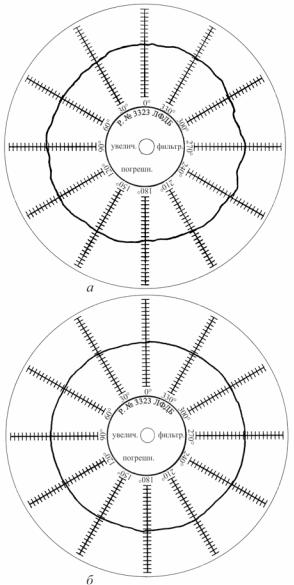
Рис. 1.2. Круглограммы детали: а – после шлифования; б – после суперфиниширования
11
Стр. 11 |
ЭБ ПНИПУ (elib.pstu.ru) |
Кроме перечисленных выше преимуществ процесс суперфиниширования обладает еще рядом достоинств, обусловливающих целесообразность его применения [6]:
1)простота предварительной обработки заготовок (при подготовке под суперфиниширование не требуется тонкое шлифование);
2)высокая производительность, в особенности при бесцентровой обработке с продольной подачей;
3)возможность обнаружения шлифовальных дефектов (отдельных грубых рисок, вырывов и следов шлифовальных вибраций);
4)возможность обработки поверхностей любой геометрии;
5)простота применяемого оборудования, низкая квалификация рабочих;
6)обеспечение работы станка по автоматическому циклу
савтоматической загрузкой заготовок и активным контролем их размеров в процессе обработки;
7)возможность использования как в мелкосерийном, так и в массовом производстве любой отрасли промышленности.
1.2. Физический механизм процесса суперфиниширования
В ГОСТ 23505–79 даны следующие определения: «суперфиниширование – доводка, осуществляемая при одновременно выполняемых колебательном движении абразивного инструмента и вращении заготовки» и «бесцентровое суперфиниширование – суперфиниширование поверхности вращения, при котором технологической базой является обрабатываемая поверхность или ранее обработанная цилиндрическая поверхность».
Суперфиниширование – процесс отделочной обработки поверхностей заготовок мелкозернистыми абразивными, алмазными или эльборовыми брусками. Отличительная особенность процесса состоит в быстром колебательном (осциллирующем)
12
Стр. 12 |
ЭБ ПНИПУ (elib.pstu.ru) |
движении брусков с частотой от 500 до 3000 дв. ход/мин, амплитудой 2–5 мм и небольшими удельными давлениями инструмента (0,05–0,3 МПа) на обрабатываемую поверхность.
Суперфиниширование целесообразно применять для улучшения эксплуатационных свойств деталей, работающих в условиях трения скольжения или качения, поскольку с помощью этого процесса можно получить поверхность шероховатостью до Ra = 0,08…0,16 мкм с минимальными волнистостью и огранкой, удалить дефектный слой металла, образованный при шлифовании, и достигнуть упрочнения поверхностного слоя без ка- ких-либо структурных изменений.
Физическая сущность процесса суперфиниширования заключается в царапании обрабатываемой поверхности одновременно большим количеством мельчайших абразивных зерен [5, 14]. Основными видами взаимодействия зерен с металлом являются микрорезание со снятием тончайших (0,1–0,5 мкм) стружек и трение с пластическим оттеснением металла. При контакте рабочей поверхности бруска с обрабатываемой поверхностью происходит царапание металла одновременно большим числом абразивных частиц. Размер таких частиц при суперфинишировании составляет 5–20 мкм, а их среднее число на поверхности бруска 400–5000 зерен на 1 мм3. Соответствующим выбором условий суперфиниширования (характеристики инструмента, режимов обработки, смазочно-охлаждающей жидкости) можно обеспечить непрекращающееся резание металла в течение длительного времени. При интенсивном резании скорость съема металла достигает 1,0–2,5 мкм/с, происходит исправление погрешностей формы заготовки и удаление дефектного слоя.
Увеличение числа движений при суперфинишировании способствует лучшему использованию режущей способности абразивных зерен, поскольку большое число вершин и режущих граней зерен может участвовать в работе, а зерна в этих условиях режут различными гранями. При этом перемещение абразивных зерен в различных направлениях обеспечивает освобождение поверхности заготовки и бруска от стружки, продуктов износа связки и выкрошившихся зерен. Для интенсивного резания
13
Стр. 13 |
ЭБ ПНИПУ (elib.pstu.ru) |
необходимо, чтобы абразивный брусок самозатачивался путем скалывания и вырывания затупившихся зерен из связки. При использовании брусков из сверхтвердых абразивных материалов (алмаза, эльбора) зерна длительное время сохраняют свою остроту, преобладает микроскалывание зерен, а не вырывание, что значительно повышает стойкость брусков.
В отличие от шлифования, при котором контактная поверхность составляет малую часть рабочей поверхности круга, при суперфинишировании брусок прирабатывается к заготовке и соприкасается с ней по значительной части рабочей поверхности. При поверхностном контакте инструмент охватывает и срезает выступающие участки макро- и микронеровностей поверхности. Такой контакт пары брусок – заготовка способствует повышению производительности и точности обработки. Давление при суперфинишировании в 10–100 раз, а скорость резания в 20–100 раз меньше, чем при шлифовании. В результате тепловыделение в зоне обработки значительно ниже, чем при шлифовании, а контактная температура не превышает 50–80 °С. Таким образом, отсутствуют физические причины образования в поверхностном слое микротрещин иприжогов, а такжеостаточных напряженийрастяжения.
До 60–70-х гг. ХХ в. существовало мнение, что суперфиниширование – самопрекращающийся процесс, при котором обработка происходит в пределах высоты микронеровностей без значимого изменения размеров и макрогеометрии поверхности. Как показали многочисленные современные исследования [16, 18, 28, 35, 36 и др.], при суперфинишировании осуществляется съем припусков до 0,005–0,01 мм на диаметр. При этом удаляются микронеровности и частично дефектный поверхностный слой основного металла, а также исправляются погрешности предыдущей обработки в поперечном сечении в виде отклонения от круглости (до 0,2–0,7 мкм) и волнистости (0,05–0,2 мкм). При суперфинишировании отклонение от круглости уменьшается на 50–80 % по отношению к исходной в зависимости от вида погрешности и снимаемого припуска. На исправление поперечного профиля заготовки в большой степени влияет форма исходной погрешности: овальность устранить затруднительно,
14
Стр. 14 |
ЭБ ПНИПУ (elib.pstu.ru) |
значительно легче – огранку, особенно при большом числе граней. Погрешность геометрической формы в продольном сечении (конусообразность, бочкообразность, седлообразность) практически не уменьшается или уменьшается незначительно.
Путем выбора оптимальных характеристик брусков и режимов обработки (припуска, скорости, давления) можно управлять процессом, осуществляя на первой стадии непрекращающееся резание металла в течение достаточно длительного времени, необходимого для исправления погрешностей формы заготовки, удаления исходной шероховатости и дефектного слоя. Затем для получения низкой шероховатости, а также создания благоприятного микрорельефа поверхности и упрочнения поверхностного слоя металла процесс обработки переводят в режим преобладающего граничного трения, при котором съем металла резко сокращается, а брусок выглаживает обрабатываемую поверхность. Такой переход можно осуществить, повышая окружную скорость заготовки, снижая давление ичастоту колебаний бруска.
1.3.Кинематика бесцентрового суперфиниширования
Кинематика суперфиниширования оказывает значительное влияние на скорость съема металла, износ брусков и качество получаемой поверхности. Основные рабочие движения заготовки и шлифовального бруска при суперфинишировании цилиндрических поверхностей складываются из вращения заготовки с окружной скоростью VО, осциллирующего движения бруска со скоростью Vr и продольного возвратно-поступательного перемещения бруска со скоростью VП вдоль обрабатываемой поверхности. При бесцентровом суперфинишировании напроход вращающиеся заготовки перемещаются под осциллирующими брусками за счет составляющей силы трения.
В результате сложения движений: вращения заготовки, осциллирующего движения и подачи бруска – на обрабатываемой поверхности остаются синусоидальные следы от прохождения абразивных зерен. Пути абразивных зерен пересекаются и обра-
15
Стр. 15 |
ЭБ ПНИПУ (elib.pstu.ru) |
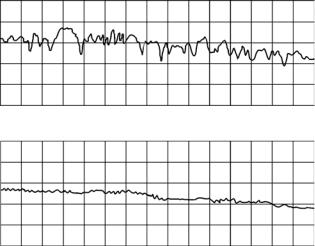
зуют сетку диагональных перекрещивающихся следов, которая на окончательно обработанной поверхности почти не видна. Угол α траектории движения абразивного зерна или угол сетки рисок, образуемой касательной к синусоидальной кривой в точке ее пересечения с осью детали, является важным критерием, характеризующим процесс суперфиниширования. Изменяя угол сетки рисок, можно управлять процессом суперфиниширования, регулируя как съем металла, так и получаемую шероховатость обработанной поверхности.
Изменяя угол α, можно управлять процессом суперфиниширования, регулируя как съем металла, так и получаемую шероховатость обработанной поверхности. Изменения микрорельефа обработанной поверхности видны на профилограммах (рис. 1.3): при α = 40…50° микрорельеф представляет собой сетку следов резания (рис. 1.3, а), а при α = 70…85° поверхность сглажена в результате пластического деформирования вершин микронеровностей (рис. 1.3, б).
а
б
Рис. 1.3. Профилограммы деталей в зависимости от угла α сетки рисок
16
Стр. 16 |
ЭБ ПНИПУ (elib.pstu.ru) |
Исследованиями установлено, что наиболее интенсивные резание металла и самозатачивание бруска осуществляются при α = = 40…50°. Это объясняется тем, что зерна бруска, перемещаясь по траектории, имеющей форму синусоиды, непрерывно изменяют свое положение по отношению к направлению движения и работают различными гранями. При этом изменяется направление действия силы резания на режущие зерна бруска и происходит интенсивное самозатачивание рабочей поверхности бруска, сопровождающееся как частичным выкрашиванием целых зерен, так и их скалываниемсобразованием новых вершин играней.
При увеличении угла α до 65–85° траектория движения режущих зерен трансформируется и приближается к кольцевой линии. Зерна в этом случае работают лишь определенными гранями, а направление действия силы резания почти не изменяется, в результате чего зерна затупляются. Поры шлифовального бруска забиваются осколками выкрошенных зерен, частицами металла, и процесс резания переходит в режим трения. Шероховатость поверхности заготовки уменьшается, и она приобретает характерный зеркальный блеск.
Таким образом, управлять процессом суперфиниширования можно, изменяя угол сетки рисок в процессе цикла обработки. Оптимальным является следующий кинематический цикл: на первом этапе для быстрого исправления погрешностей формы, удаления исходной шероховатости и дефектного слоя работают с α = 40…50°, на втором этапе производят полирование поверхности, для чего увеличивают α за счет повышения скорости вращения детали в 2–10 раз и более. При обработке в режиме, обеспечивающем непрерывное самозатачивание брусков, за счет большой площади контакта с обрабатываемой поверхностью достигается исправление отклонения от круглости и волнистости поверхности. Чем выше абсолютные значения скоростей при соблюдении оптимального соотношения между ними, тем эффективнее процесс суперфиниширования. Поэтому, как правило, работают с максимальной для данного оборудования скоростью колебаний бруска, а окружную скорость заготовки устанавливают с учетом указанных соотношений (табл. 1.1).
17
Стр. 17 |
ЭБ ПНИПУ (elib.pstu.ru) |
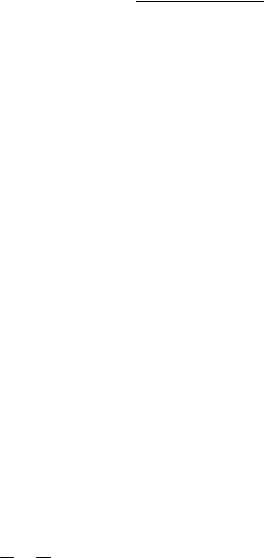
Таблица 1 . 1 Выбор кинематического цикла суперфиниширования [5]
Шероховатость |
Число |
|
Vr |
Время обработки |
|
Угол α, |
на каждой ступени, |
||||
после обработки |
ступеней |
||||
Ra, мкм |
цикла |
град |
Vs |
% от общего |
|
|
|
|
|
времени цикла |
|
0,16 |
1 |
40…50 |
0,8…1,2 |
100 |
|
0,08 |
1 |
40…50 |
0,8…1,2 |
50…60 |
|
2 |
60…70 |
1,7…2,7 |
50…40 |
||
|
|||||
0,04 |
1 |
40…50 |
0,8…1,2 |
50…60 |
|
2 |
60…70 |
1,7…2,7 |
40…25 |
||
|
3 |
75…85 |
3,7…11,4 |
10…15 |
|
|
1 |
40…50 |
0,8…1,2 |
40…50 |
|
0,02 |
2 |
60…70 |
1,7…2,7 |
40…20 |
|
3 |
75…80 |
3,7…5,7 |
10…15 |
||
|
|||||
|
4 |
85…88 |
11,4…28,6 |
10…15 |
Наиболее интенсивный съем металла происходит в начальный период обработки. Это объясняется тем, что при значительной шероховатости возникает большое удельное давление на отдельные зерна бруска, в результате чего происходит его интенсивное самозатачивание и резание металла осуществляется острыми зернами. Затем, когда исходная шероховатость снижается и уменьшается удельное давление на зерна, износ бруска снижается, и процесс резания стабилизируется. При работе брусками оптимальной характеристики съем припуска в дальнейшем происходит пропорционально времени обработки. В брусках из эльбора зерна длительное время сохраняют свою остроту, поэтому повышение Vr в этом случае способствует увеличению съема металла. Однако во избежание образования налипов металла на рабочей поверхности бруска следует работать со скоростью не больше 30–40 м/мин.
Рассмотрим процесс передачи движения от валков к заготовке. Как правило, валки вращаются с равными постоянными
угловыми скоростями ω1 и ω2 , имеющими одинаковое направление (рис. 1.4). Поскольку в общем случае значения результи-
18
Стр. 18 |
ЭБ ПНИПУ (elib.pstu.ru) |
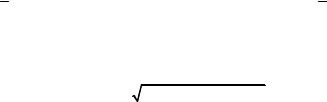
рующих скоростей V1 и V2 валков в различных сечениях не совпадают, ведущим будет только один из них. При отсутствии проскальзывания заготовка имеет окружную скорость, равную окружной скорости VО ведущего валка в точке контакта. При наладке станка валки должны быть развернуты на угол λ таким образом, чтобы составляющая вектора скорости VП вдоль траектории движения заготовки имела одинаковое направление с осью Z, т.е. движение осуществлялось от входа к выходу из зоны обработки [37]. Решением силовой задачи установлено, что ведущим всегда будет правый валок (с индексом 1).
Скорость валка в точке контакта с заготовкой находится по формуле
|
V |
= |
ω |
|
R |
, |
(1.1) |
где ω – угловая скорость вращения ведущего валка; R – ради- ус-вектор валка в точке контакта.
Скорость окружной подачи заготовок при суперфинишировании
V = Rω cos2 |
α cos2 λ + sin2 α . |
(1.2) |
О |
|
|
Скорость продольной подачи заготовок при суперфинишировании
VП = Rωcosα sin λ . |
(1.3) |
В выражениях (1.2) и (1.3) подразумевается, что параметры R, ω и α относятся к ведущему валку.
Кинематика суперфиниширования оказывает значительное влияние на скорость съема металла, износ брусков и качество поверхности [6]. Основные рабочие движения заготовки 1 и шлифовального бруска 2 при суперфинишировании цилиндрических поверхностей включают вращение заготовки со скоростью VО, продольное перемещение со скоростью VП и осциллирующее движение бруска со скоростью Vr (рис. 1.5). Как следствие результирующего движения на обрабатываемой поверхности создается сетка синусоидальных следов.
19
Стр. 19 |
ЭБ ПНИПУ (elib.pstu.ru) |
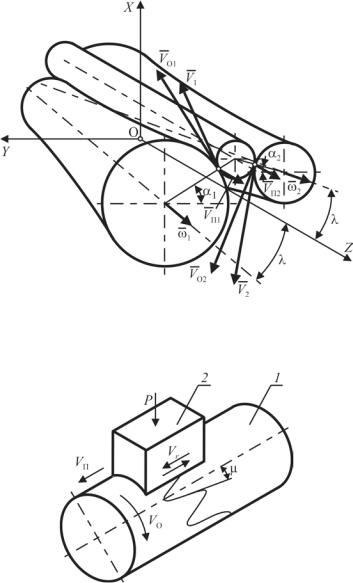
Рис. 1.4. Схема для расчета скоростей при бесцентровом суперфинишировании
Рис. 1.5. Схема суперфиниширования: 1 – заготовка; 2 – шлифовальный брусок
20
Стр. 20 |
ЭБ ПНИПУ (elib.pstu.ru) |