
Аэрокосмическая техника высокие технологии и инновации – 2014
..pdf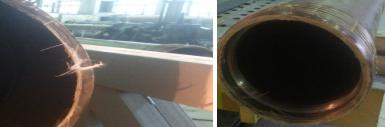
страняются на различные материалы, однако специфика свойств композиционных материалов в них не учтена, поэтому исследование качества поверхности композитов, в частности их шероховатости после механической обработки, имеет большое практическое значение;
3)низкая производительность операции механической обработки, требующей высокой квалификации рабочего, а также длительный цикл по настройке и выверке детали на станке. Необходимо также отметить, что подачу и скорость резанья невозможно увеличить из-за высокой нагрузки на деталь при обработке токарными резцами и фрезами;
4)на поверхности возникают неровности: в слоях материала изменяется структура и химический состав, а также физико-хими- ческие и эксплуатационные свойства изделий.
Аналогичные проблемы возникают при обработке деталей из угольных и стекловолокнистых препрегов для звукопоглощающих конструкций узлов двигателя ПС-90А. Также при проведении механической обработки по отрезке ложных днищ на композиционных деталях, габаритные размеры которых менее 1000 мм, возникают проблемы качества обработанной поверхности в части отслоения нити и ее вырыва (рис. 3).
Рис. 3. Общий вид дефектов детали из композита размером до 1000 мм
Основные причины появления данных дефектов (рис. 2, 3) следующие.
1. Применение обычных токарных резцов при обработке небольших диаметров на токарном станке типа КЖ и диаметров бо-
91
лее 1000 мм на токарно-карусельных станках (резец в процессе обработки неоднократно приходится перетачивать).
2.Использование низких диапазонов вращения шпинделя, а также низких диапазонов продольных ипоперечных подач.
3.Физико-механические характеристики полимерного композиционного материала.
На ОАО «ПЗ «Машиностроитель» сегодня данные проблемы, безусловно, решаются. Например, при сверлении идет внедрение роботизированной техники; при фрезеровании используется импортный инструмент с алмазным покрытием. Однако последние тенденции говорят о том, что необходимо находить альтернативные варианты использования инструмента.
Мировые лидеры, такие как Великобритания, Франция, Швейцария (Sandvik Coromant), а также и КНР, ведут разработки и внедрение инструментов с алмазными покрытиями и различными вариантами геометрии. Основным направлением повышения эффективности обработки композиционных материалов, используемых в продукции гражданского и специального назначения, является фрезерование с высокими диапазонами вращения шпинделя станка. Причем фрезерование не только концевыми фрезами, но и фрезами с алмазным напылением (включая применение попутного и встречного фрезерования).
Задача совместно с кафедрой инновационных технологий в
машиностроении ПНИПУ повысить производительность при изготовлении изделий за счет применения новых конструкций режущего инструмента, подбора оптимальных режимов резания, изучения термодинамических явлений, моделировании процесса механической обработки, что в конечном результате должно привести к повышения качества и снижению себестоимости.
Для повышения конкурентоспособности и эффективности необходимо разработать специализированное решение для фрезерования, а также рассмотреть и дать рекомендации по обработке других деталей для продукции гражданского и специального назначения. Необходимо рассмотреть инструментальное решение для эффективной обработки композитов и пакетов (композит/металл) на станках с ЧПУ. Усовер-
92
шенствование инструмента и разработка специальных решений для особых областей применения играют важнейшую роль в процессе обработки композитов. Необходимо отработать применение специально спроектированного многолезвийного инструмента с поликристаллическим алмазным покрытием и мотора шпинделя (который обеспечит более высокие обороты), так как для обеспечения качества и снижения себестоимостинеобходима высокая стойкость инструмента.
Кроме того, необходимы достижение требуемого уровня качества при обработке композитов (учитывая примеры на рис. 2, 3), контроль качества наряду с высоким уровнем надежности и произ-
водительности обработки, основных критериев выбора инстру-
мента. Необходимо рассмотреть возможность использования фрез с покрытием из поликристаллического алмаза с впаянными профильными вставками. Проанализировать геометрию фрез со вставками и покрытием из поликристаллического алмаза.
Предлагаем также рассмотреть возможность проектирования, изготовления и применения специального режущего инструмента (фрез с применением упрочняющих покрытий) при фрезерной обработке, при обработке на карусельном станке фрезой вместо резцов при токарной операции. Проведение данных исследований, а самое главное – применение на практике методов более эффективной механической обработки композитов позволит существенно повысить производительность и качество обработки изделий на ОАО «ПЗ «Машиностроитель».
Список литературы
1.ГОСТ 2789-73. Шероховатость поверхности. Параметры
ихарактеристики. – М., 1973.
2.ГОСТ 25142-82. Шероховатость поверхности. Термины
иопределения. – М., 1982.
3.Ягодкин Ю.Д., Сулима А.М., Шулов В.А. Поверхностный слой и эксплуатационные свойства деталей машин. – М.: Машиностроение, 1988.
93
МАТЕМАТИЧЕСКОЕ МОДЕЛИРОВАНИЕ ТЕРМОДИНАМИЧЕСКИХ ПРОЦЕССОВ В ЗОНЕ РЕЗАНИЯ ПРИ ГЛУБИННОМ ШЛИФОВАНИИ ЖАРОПРОЧНЫХ СПЛАВОВ
В.Ф. Макаров, С.П. Никитин
Пермский национальный исследовательский политехнический университет, Пермь, Россия
e-mail: makarovv@pstu.ru, perkan@perm.ru
Представлены результаты теоретического исследования устойчивости при глубинном шлифовании лопаток турбины газотурбинных двигателей. Для исследования использована термодинамическая модель плоскошлифовального станка, которая позволяет изучить влияние параметров динамической системы станка и процесса шлифования на устойчивость системы и предел выносливости лопаток турбины газотурбинных двигателей.
Для изготовления рабочих и сопловых лопаток турбины газотурбинных двигателей (ГТД) используют жаропрочные литейные никелевые сплавы. Основными технологическими процессами обработки базовых поверхностей лопаток ГТД являются процессы глубинного шлифования. Для повышения производительности и эффективности глубинного шлифования при заданных параметрах качества необходимо прогнозирование качества деталей при обработке лопаток газотурбинных авиадвигателей, выявление взаимосвязи эксплуатационных показателей качества лопаток с параметрами поверхностного слоя и технологическими показателями процесса глубинного шлифования [1]. Значительное внимание должно быть уделено исследованию динамики и устойчивости процесса, термодинамическим явлениям при профильном глубинном шлифовании [2, 3]. Качество поверхностного слоя заготовки определяется одновременным воздействием геометрического, силового и теплового факторов, являющихся функциями процесса шлифования и имеющих непосредственную связь с относительными колебаниями формообразующих узлов станка [4].
94
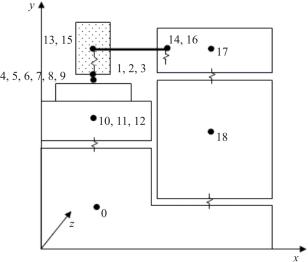
В рамках решения задачи были проведены теоретические исследования влияния конструктивных параметров и режимов резания на устойчивость и уровень температур при глубинном шлифовании. Для исследований в данной работе использована математическая модель теплодинамической системы шлифовального станка [4], учитывающая взаимодействие упругих, тепловых явлений и процесса резания. Для построения математической модели использован метод электрической аналогии, который позволяет отразить как тепловые, механические, так и процессы другой физической природы. На рис. 1 приведена расчетная схема динамической системы шлифовального станка.
Рис. 1. Расчетная схема шлифовального станка
В модели упругая система станка представлена в виде отдельных сосредоточенных масс, соединенных жесткостями и обладающих определенным демпфированием колебаний. Для сокращения числа степеней свободы и упрощения модели некоторые связи между соседними элементами принимаются абсолютно жесткими, если ожидаемое перемещение по соответствующим координатам мало влияет на относительные смещения шлифовального круга и
95
стола. В качестве сосредоточенных масс выделены: станина и основание станка (точка 0); стол (точки 10, 11, 12); колонна со шлифовальной бабкой (точка 18); гильза шлифовального шпинделя (точка 17); шлифовальный круг (точки 1, 2, 3). Шпиндель шлифовального круга представлен как стержень, закрепленный в гильзе шпинделя и испытывающий изгибные деформации (точки 13, 15, 14, 16). При моделировании динамики процесса резания необходимо учесть особенности процесса глубинного шлифования.
Математическая модель должна учитывать, что изменения условий обработки (режимы резания, геометрия и характеристика круга, и др.) влияют на силы резания через изменение фактического, а не номинального сечения срезаемого слоя.
Методом прямой аналогии и сделанных допущений получена следующая эквивалентная схема, которая отражает динамику тепловых процессов при шлифовании (рис. 2).
Представленная математическая модель описывает основные теплодинамические процессы при шлифовании. Она обладает достаточной гибкостью и универсальностью, позволяет отображать нюансы тепловых и механических упругих процессов при различных режимах резания и характеристике шлифовального круга.
Использование разработанной математической модели позволило выявить ряд закономерностей. Качество поверхностного слоя определяется динамикой и устойчивостью процесса шлифования, термодинамическими явлениями при профильном глубинном шлифовании. Вынужденные колебания в динамической системе при глубинном шлифовании могут приводить к значительным колебаниям температуры резания. Характеристика шлифовального круга и режимы резания могут значительно снижать устойчивость системы станка, что вызывает повышенные колебания в динамической системе станка при глубинном шлифовании. Для обеспечения качества обработки лопаток и повышения эффективности глубинного шлифования целесообразно внедрить методику, включающую прогноз устойчивости динамической системы шлифовального станка на основе математического моделирования и корректировку режимов резания и технических характеристик круга.
96
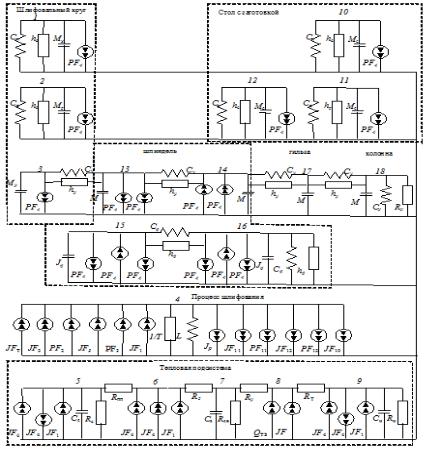
Рис. 2. Эквивалентная схема термодинамической системы шлифовального станка: Cz, Cy, Cx, Cφ – приведенные жесткости соответствующих подсистем; hz, hy, hx – приведенные коэффициенты демпфирования механических подсистем; Rс, Rпп, Rz, Ry, Rсв, Rтз, Rи,– коэффициенты сопротивления тепловому потоку в зоне шлифования; Mz, My, Mx, Jφ – приведенные инерционные параметры подсистем; L – условная податливость процесса резания единичной величины; Тp – постоянная времени стружкообразования; Jp – номинальная сила резания, определяемая припуском; Qтз – источник тепла от трения по задней поверхности зерен; PF, JF – фиктивные источники,
отражающие взаимодействие подсистем
97
Работа выполнена при финансовой поддержке Минобрнауки РФ (договор №02.G25.310016) в рамках реализации Постановления Правительства РФ №218 «О мерах государственной поддержки развития российских высших учебных заведений и организаций, реализующих комплексные проекты по созданию высокотехнологического производства» от 12.02.13.
Выводы
1.Математическая модель позволяет исследовать влияние на качество поверхностного слоя динамики и устойчивости процесса шлифования, термодинамических явлений при профильном глубинном шлифовании.
2.Выявлена зависимость колебаний температуры в зоне резания при глубинном шлифовании от вынужденных колебаний в динамической системе станка.
3.Выявлено влияние характеристики шлифовального круга и режимов резания на снижение устойчивости системы станка, что вызывает повышенные колебания в динамической системе станка при глубинном шлифовании.
4.Для обеспечения качества обработки жаропрочных сплавов
иповышения эффективности глубинного шлифования целесообразно внедрить методику, включающую прогноз устойчивости динамической системы шлифовального станка на основе математического моделирования и корректировку режимов резания и технических характеристик круга.
Список литературы
1.Макаров В.Ф. Современные методы высокоэффективной абразивной обработки жаропрочных сталей и сплавов: учеб. посо-
бие. – СПб.: Лань, 2013. – 320 с.
2.Полетаев В.А., Волков Д.И. Глубинное шлифование лопаток турбин: библиотекатехнолога. – М.: Машиностроение, 2009. – 272 с.
3.Никитин С.П. Теоретическое исследование устойчивости при обработке шлифованием / Вестн. УГАТУ. – 2013. – Т. 17,
№8 (61). – С. 38–44.
98
4. Никитин С.П. Моделирование процесса резания при шлифовании с учетом взаимодействия упругой и тепловой систем //
Вестн. УГАТУ. – 2009. – Т. 12. – № 4(33). – С. 61–65.
СОВРЕМЕННЫЕ ПРОБЛЕМЫ МЕХАНИЧЕСКОЙ ОБРАБОТКИ ПОЛИМЕРНЫХ КОМПОЗИЦИОННЫХ МАТЕРИАЛОВ В СПЕЦИАЛЬНОМ МАШИНОСТРОЕНИИ
В.Ф. Макаров, В.В. Ширинкин
Пермский национальный исследовательский политехнический университет, Пермь, Россия
ОАО «Пермский завод “Машиностроитель”», Пермь, Россия e-mail: makarovv@pstu.ru, v-shirinkin@mail.ru
Проведен анализ проблемы сверления отверстий ø2,0 мм в ячеистых конструкциях из композиционного материала марки ВПС-33 (стеклотекстолита) и существующих на ОАО «Пермский завод «Машиностроитель» методов их решения. Автором изучено применение роботизированной техники для повышения производительности процесса сверления композиционного материала на основе полимерного связующего. Затронутые в статье проблемы мало изученыи требуютдальнейших исследований.
Одним из актуальных и наиболее востребованных направлений развития новой техники в настоящее время является использование композиционных материалов в различных вариантах конструкций. Уникальные свойства композиционных материалов позволяют во многих случаях значительно повысить эксплуатационные характеристики конструкций изделий. Также применение композиционных материалов позволяет снизить трудоемкость и материалоемкость изготовления изделий путем получения окончательно изготовленных деталей и узлов изделий, требующих минимальной обработки. Все это способствует росту конкурентоспособности российских товаров на мировом рынке.
Реализация возможностей и конструкционных свойств, заложенных в композиционных материалах, зависит от большого количества переменных факторов. Одним из таких факторов является
99
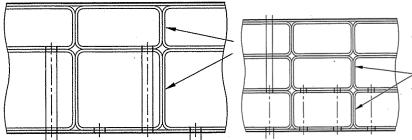
обеспечение качества обработки изделий. Наиболее распространенными методами обработки композиционных материалов является механическая (лезвийная) обработка. Одна из основных причин ограниченного применения немеханических методов формообразования отверстий, таких как гидравлическая струйная, электрофизическая или лазерная обработка, заключается в том, что многие детали и сборочные единицы имеют требования по обеспечению формообразования глухих отверстий. Второй, немаловажной, причиной является негативное влияние на композиционный материал воды или других жидкостей и высоких температур.
На сегодняшний день на ОАО «Пермский завод “Машиностроитель”» существуют следующие проблемы получения отверстий на деталях и сборочных единицах, изготовленных из композиционных материалов.
1. Низкая производительность процесса механической обработки ячеистых конструкций (сверление отверстий ø2,0 мм), обусловленная рядом причин:
–низкие скорости резанья;
–периодические поломки режущего инструмента (сверла ломаются в связи с попаданием на перегородки ячеек (рис. 1));
Рис. 1. Двух- и трехуровневые трубчатые структуры рассматриваемых кожухов
–многократныеперестановки, выверкиизакреплениякондуктора;
–отсутствие возможности применения смазочно-охлаждающих жидкостей на водной основе из-за влагопоглощающих свойств материала кожуха.
100