
1158
.pdfУДК 622.311.22.019
И.Е. Фурман, Е.Л. Фурман
Уральский федеральный университет им. первого президента Б.Н. Ельцина
ИЗНОСОСТОЙКОСТЬ КОБАЛЬТОВОГО СТЕЛЛИТА 3В14КБ
Изучено влияние химического состава кобальтового сплава 3В14КБ на его износостойкость. В зависимости от условий эксплуатации детали необходимо использовать сплав с различным содержанием легирующих элементов. Установлены соотношения легирующих элементов в зависимости от условий работы детали, наплавленной данным сплавом.
Износ деталей машин принято подразделять по причинам, его вызывающим. В соответствии с этим различают абразивное, усталостное, адгезионное, коррозионно-механическое изнашивание. Абразивное изнашивание происходит при трении материала под нагрузкой о более твердые тела или частицы. При взаимодействии абразивных частиц с поверхностью деталей машин происходит разрушение поверхностного слоя путем царапания, среза или отрыва неровностей. В лабораторной практике для оценки сопротивления материалов износу нашли широкое применение методы испытаний путем истирания их о поверхность абразивного камня или шкурки в среде незакрепленных абразивных частиц, а также истирания в газоили гидроабразивной среде [1].
Нами изучено влияние химического состава кобальтового сплава 3В14КБ на его износостойкость. Пределы варьирования легирующих элементов в этом сплаве очень велики и составляют обычно несколько процентов, поэтому один и тот же сплав обладает совершенно различными физикомеханическими свойствами, что приводит к ограничению использования этого сплава в промышленности.
Основным механизмом разрушения материалов при абразивном изнашивании является царапание металла твердыми частицами. Поэтому для оценки износостойкости часто применяют испытание материалов путем трения их о шлифовальную шкурку, воспроизводящее механизм царапания при взаимодействии образца со множеством абразивных частиц. Большинство исследователей использовали методику [3], в которой трение образца осуществлялось по одному и тому же следу, что вызывает постепенное уменьшение абразивной способности шкурки и значительно сказывается на результатах исследований. Поэтому для определения износостойкости поверхностно упрочненных образцов по закрепленному абразиву была создана установка, позволяющая образцу все время скользить по свежей поверхности абразива, при
131
Стр. 131 |
ЭБ ПНИПУ (elib.pstu.ru) |
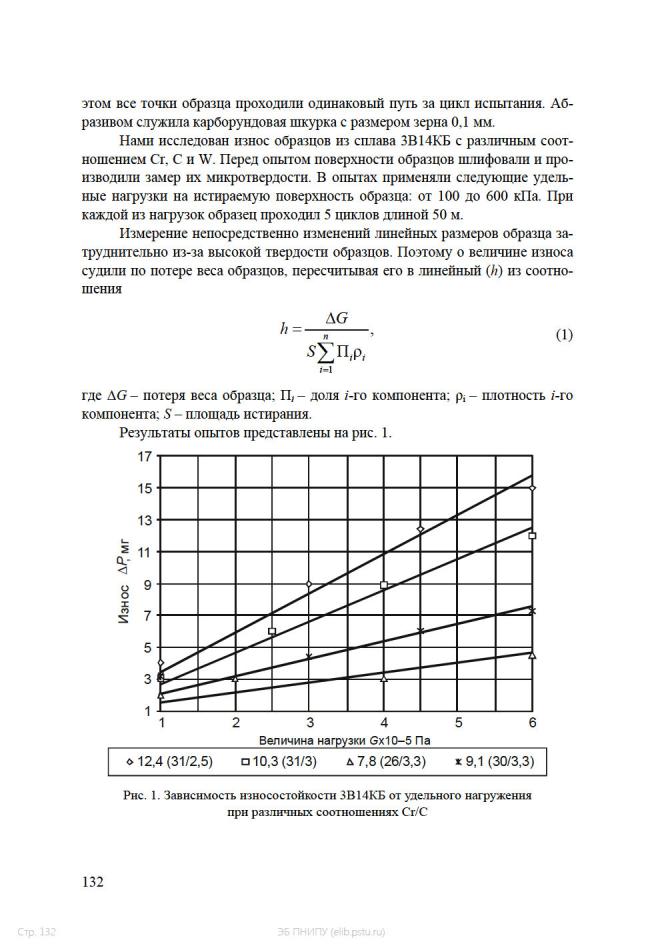
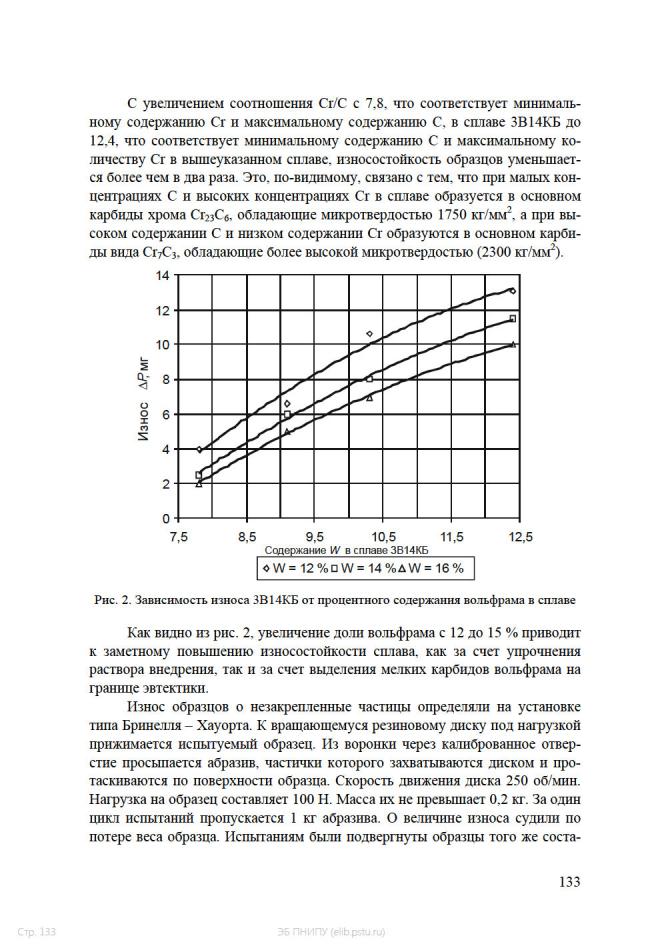
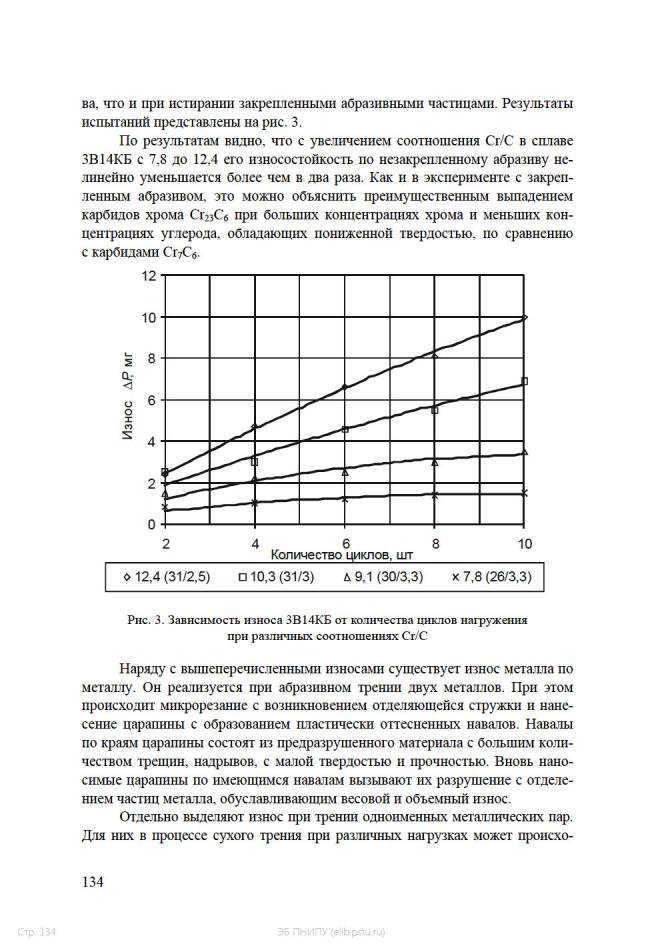
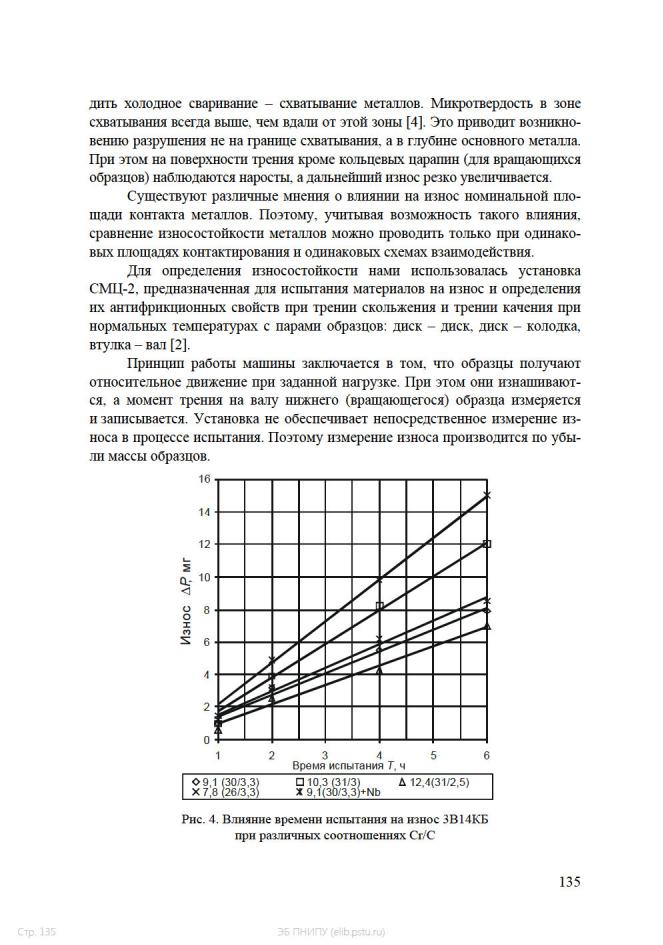
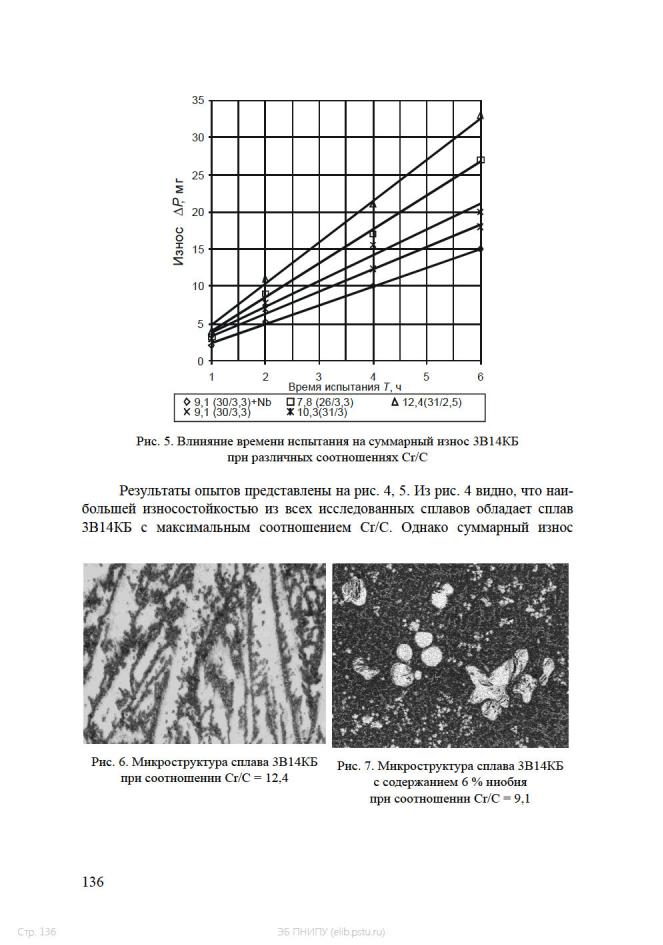
сплава с таким соотношением в контакте с образцом из стали ШХ15 максимальный, а суммарный износ сплава, содержащего 6 % ниобия, минимален. Это по-видимому связано с тем, что грубые карбиды Cr23C6 (рис. 6), которые наблюдаются в сплаве 3В14КБ с соотношением Cr/C = 12,4, изнашивают контробразец из стали ШХ15. Напротив, карбиды ниобия, образующиеся в сплаве 3В14КБ с 6 % ниобия, как это видно из рис. 7, обладают округлой формой и практически не изнашивают контробразец. Это позволяет рекомендовать этот сплав для наплавки подшипника качения высоконагруженных агрегатов, таких как нефтяные долота.
Проведенные исследования показали, что сплав типа стеллит 3В14КБ не является универсальным. В зависимости от условий эксплуатации детали необходимо использовать сплав с различным соотношением хрома и углерода. Для деталей, работающих в абразивных средах, необходимо использовать сплавы с минимальным соотношением Cr/C, а для деталей, работающих в условиях трения металла по металлу – с максимальным соотношением Cr/C. Кроме того, в последнем случае в сплав необходимо вводить сильные карбидообразующие элементы типа ниобия, тантала и гафния для образования мелких карбидов глобулярной формы.
Список литературы
1. Топеха П.К. Основные виды износа металлов. – М.: Машгиз, 1962. –
383 с.
2.Хрущев М.М., Бабичев М.А. Исследования изнашивания металлов. – М.: Издательство АН СССР, 1960. – 352 с.
3.Тененбаум М.М. Износостойкость конструкционных материалов
идеталей машин. – М.: Машиностроение, 1966. – 332 с.
4.Кащеев В.Н. Процессы в зоне фрикционного контакта металлов. – М.: Машиностроение, 1978. – 213 с.
Получено 5.07.2010
Стр. 137 |
ЭБ ПНИПУ (elib.pstu.ru) |
УДК 538,95
А.Л. Каменева
Пермский государственный технический университет, Научный центр порошкового материаловедения Пермского государственного технического университета
УСТАНОВЛЕНИЕ КОРРЕЛЯЦИОННОЙ СВЯЗИ ПРОЦЕССА ФОРМИРОВАНИЯ ПЛЕНОК НА ОСНОВЕ TI–AL–N МЕТОДОМ ЭЛЕКТРОДУГОВОГО ИСПАРЕНИЯ И ПРОЦЕССОВ, ПРОТЕКАЮЩИХ НА ПОВЕРХНОСТИ
ИСПАРЯЕМЫХ КАТОДОВ
Изучены процессы, протекающие в приповерхностных слоях испаряемого материала титанового и алюминиевого катодов в условиях электродугового испарения. Установлено, что все процессы, участвующие в формировании пленки, неравновесные. Равномерность и постоянство температуры поверхности катода способствует равномерному стравливанию его материала, позволяет управлять и контролировать процесс получения пленок со стабильной структурой и свойствами.
Многочисленными комплексными исследованиями накоплен большой опыт по установлению взаимосвязи состава, структуры и условий осаждения многокомпонентных пленок Ti–Al–N методом электродугового испарения [1–4]. За последние десятилетия исследователи добились значительного повышения надежности изделий с указанными пленками; были выяснены
иустранены многие факторы, ухудшающие их эксплуатационные характеристики, однако проблема их стабилизации находится на стадии совершенствования. В определенной степени невоспроизводимость результатов закладывается уже в процессе формирования пленки. Для повышения эффективности технологического процесса и получения пленок с контролируемой структурой
истабильными свойствами существует необходимость в экспериментальном изучении процессов, протекающих не только на поверхности формируемой пленки, но и на поверхности испаряемых катодов. Представляет значительный интерес изучение морфологических особенностей областей испарения катодов для выявления структурных свойств, наследуемых в процессе осаждения пленок.
Целью настоящей работы являлось изучение процессов, протекающих
вприповерхностных слоях материала титанового и алюминиевого катодов
138
Стр. 138 |
ЭБ ПНИПУ (elib.pstu.ru) |
в условиях электродугового испарения, и установление их взаимосвязи с процессом формирования пленки на основе Ti–Al–N.
Методика проведения эксперимента. Рельеф поверхности титанового и алюминиевого катодов после процесса испарения электродуговым испарителем при оптимальных технологических условиях исследовали на растровом электронном микроскопе BS 300 с приставкой для микроанализа EDAX Genesis 2000. Использовали различные способы охлаждения катодов: комплексной и оборотной водой для установления влияния температурного состояния поверхности катодов в процессе их испарения. Экспериментально установили, что при охлаждении поверхности катода комплексной водой ее температура на входе (Тохл вод) соответствовала ~ 291–292 К, на выходе ~ 293– 294 К; оборотной водой: на входе – ~ 299–300 К, на выходе – ~ 301–302 К.
Результаты эксперимента и обсуждение. Установлено [5], что на про-
цессы, протекающие на поверхности катодов в результате их испарения и пленок в процессе их формирования методом электродугового испарения,
оказывают влияние функциональные |
характеристики |
материалов катодов |
||
(таблица). |
|
|
|
|
Функциональные характеристики распыляемых материалов [5] |
||||
|
|
|
|
|
Параметр |
|
Аl |
|
Ti |
|
|
|
|
|
Пространственная группа |
|
Fm3m |
|
С6mmc |
Параметр элементарной ячейки, нм |
|
0,4040 |
α-Ti: a = 0,2951, c = 0,4697 |
|
Температура плавления, К |
|
933 |
|
1944 |
Коэффициент распыления, атом/ион |
|
1,24 |
|
0,33 |
Показано [6], что при длительной эксплуатации катода происходит ее деформирование и, как следствие, нарушение теплоотвода от отдельных участков, ведущее к локальному плавлению поверхностного слоя области распыления катода, перераспределению концентрации фаз по поверхности катода и значительному отличию состава сформированной пленки от состава катода. Металлические однофазные однокомпонентные катоды со средним размером кристаллитов (областей когерентного рассеяния рентгеновского излучения) 20−100 нм имеют гладкую поверхность области испарения. На изучаемых поверхностях областей испарения однофазных катодов со следами механообработки на исходной поверхности, изготовленных методом ковки и имеющих средний размер кристаллитов несколько миллиметров (рис. 1, а), из-за анизотропии скорости испарения различно кристаллографически ориентированных зерен формируется рельефная поверхность (рис. 1, б). Для катода, изготовленного из легкоплавкого материала Al с размером зерен до 5 мм, наблюдается различная картина рельефа поверхности различно ориентированных зерен (рис. 1, в).
139
Стр. 139 |
ЭБ ПНИПУ (elib.pstu.ru) |
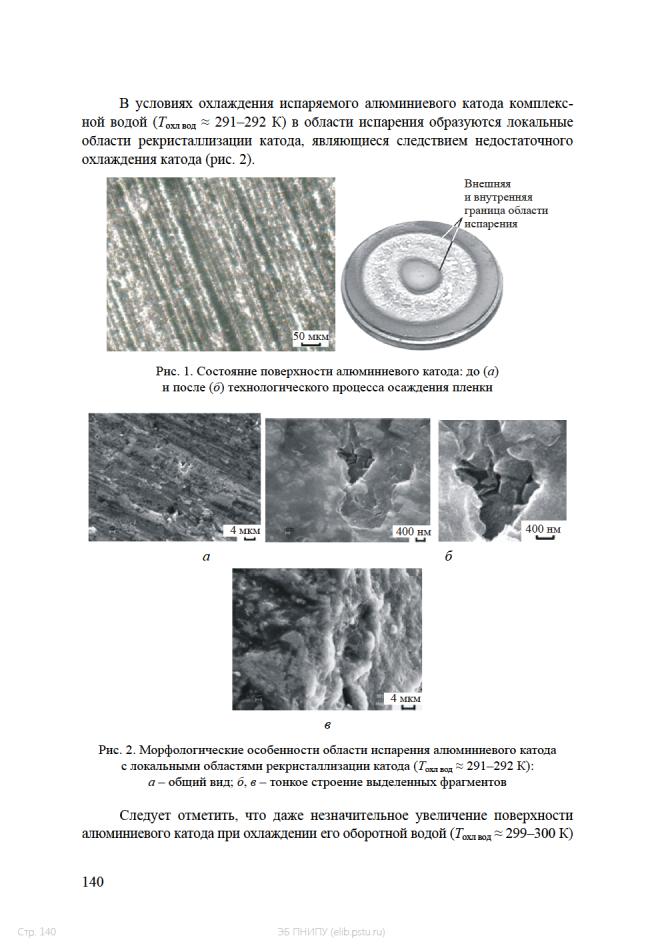