
1158
.pdf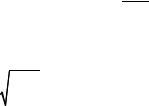
Для получения из аналитического расчета истинных значений температур, возникающих в контактной зоне при круглом торцовом шлифовании, необходимо определить величину плотности теплового потока q0, поступающего в шлифуемую деталь. Общую тепловую мощность, выделяющуюся в зоне контакта, можно определить из выражения N = PVz к.
Разделив эту величину на площадь S зоны контакта, можно найти пол-
ную плотность теплового потока в зоне шлифования: q1 = PzSVк . Доля тепла β,
поступающая в деталь, может быть определена из выражения [2]
β = |
|
1 |
|
, |
|
|
|
2 V |
|
||
1+t |
|
i |
|
|
|
|
haπ |
|
|
где t – истинная глубина шлифования.
Таким образом, для аналитического расчета температуры плотность теплового потока, поступающего в деталь, может быть найдена из выражения
q0 = q1β.
Полученные аналитические зависимости позволяют рассчитать температуру в каждой точке шлифуемой поверхности детали и температурное поле в нижележащих слоях на i-м радиусе шлифуемого торца.
Особенностью процесса круглого торцового шлифования является непостоянство его теплонапряженности в различных точках по радиусу шлифуемой детали Rд i . Кроме того имеет место многократное повторение про-
ходов, т.е. источник тепла, зона контакта шлифовального круга с изделием, встречается при своем движении с теплопроводящим пространством, предварительно нагретыми предыдущими проходами. В этом случае температурное поле будет представлять собой суперпозицию температурных полей многих источников, последовательно проходящих над данной точкой теплопроводящего пространства. В полученных выражениях (4) и (5) безразмерные координаты X, Z и безразмерная полуширина H теплового источника будут определяться по формулам (см. рис. 1):
X = |
Vдi cos γi x |
, |
Z = |
Vдi cos γi z |
, |
H = |
Vдi cos γi h |
, |
|
2a |
2a |
2a |
|||||||
|
|
|
|
|
|
где Vд i – скорость детали, соответствующая среднему радиусу режущей ленточки круга.
61
Стр. 61 |
ЭБ ПНИПУ (elib.pstu.ru) |
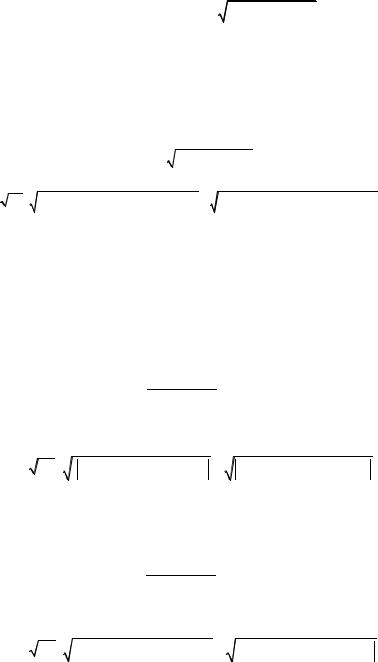
Температурное поле будет определяться суммой интегралов (4) в виде
n |
2aq0 |
|
|
U2 |
|
Θ = ∑i=0 |
|
|
∫exp(−ξ)K0 ( X 2 cos2 γi +ξ2 )dξ, |
(6) |
|
πλV cos |
γ |
|
|||
|
дi |
|
i U |
|
|
|
|
|
1 |
|
где U1 = (Z − nL0 + H )cos γi ; U2 = (Z − nL0 − H )cos γi ; L0 – безразмерная длина окружности; n – число проходов при съеме припуска.
Выражению (6) можно придать вид, приемлемый для инженерных расчетов [3]:
Θ = |
2q a |
|
|
|
(Z +H ) cos γi |
( |
X |
|
cos |
|
γi +ξ |
|
|
+ |
2q a |
× |
|
||||||
πλV |
cos γ |
|
∫ |
exp(−ξ)K0 |
2 |
2 |
2 |
)dξ |
πλV cos γ |
|
|||||||||||||
|
|
|
0 |
|
|
|
|
|
|
|
|
|
|
|
|
|
0 |
|
|
|
|||
|
|
дi |
|
|
i |
|
(Z −H ) cos γ |
i |
|
|
|
|
|
|
|
|
|
|
дi |
|
i |
(7) |
|
|
|
|
|
|
|
|
|
|
|
|
|
|
|
|
|
|
|
||||||
|
n |
|
( |
|
(Zi |
− Li min(max) − Hi)cos γi |
|
− |
|
(Zi − Li min(max) + Hi )cos γi |
|
||||||||||||
× |
∑ 2π |
|
|
|
) . |
||||||||||||||||||
|
0 |
|
|
|
|
|
|
|
|
|
|
|
|
|
|
|
|
|
|
|
|
|
|
В выражении (7) первое слагаемое описывает температурное поле полосового источника тепла за единичный n-проход, а второе – накопившуюся остаточную температуру к началу n-прохода.
Применительно к нашему случаю длина безразмерной окружности L0 разбита на две дуги Limax, Limin, следовательно, будет две остаточные темпера-
туры: на дуге Limin (при n-четном проходе) и дуге Limax (при n-нечетном проходе). Остаточная температура на дуге Limin
Θ1 = πλ 2q0a γ Θ1*ост ,
Vдi cos i
где Θ1*ост – безразмерная остаточная температура.
Θ1*ост = 2π( (Zi − Li min − Hi )cos γi − (Zi − Li min + Hi )cos γi ),
где Zi – безразмерная координата на i-м радиусе; Нi рина теплового источника на i-м радиусе.
Остаточная температура на дуге L
Θ2 = πλ 2q0a γ Θ2*ост ,
Vдi cos i
где Θ2*ост – безразмерная остаточная температура.
Θ2*ост = 2π( |
|
(Zi − Li max − Hi )cos γi |
|
− |
|
|
(Zi − |
||
|
|
|
|||||||
|
|
Limin, imax = |
Vдilimin, i max |
|
, |
||||
|
|
2a |
|
||||||
|
|
|
|
|
– безразмерная полуши-
Li max + Hi )cos γi ).
62
Стр. 62 |
ЭБ ПНИПУ (elib.pstu.ru) |
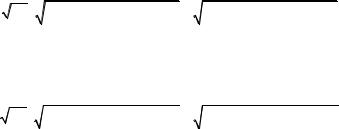
где limin, imax определяются |
(см. |
рис. 1) на |
i-м радиусе детали, |
|
li max = 2Rдi (π−αi ), li min = 2Rдiαi , |
αi – угол между i-м радиусом детали и осью Z, |
|||
|
|
R2дi + Rср2 −(Rср − h)2 |
|
|
αi = arccos |
|
|
. |
|
|
2Rдi Rср |
|||
|
|
|
|
|
|
|
|
|
|
Угол γi, входящий в выражение (7), определяется по формуле
|
π |
|
R2дi + Rср2 −(Rср − h)2 |
|
|
γi = |
|
−αi = arcsin |
|
. |
|
2 |
2Rдi Rср |
||||
|
|
|
|||
|
|
|
|
|
Таким образом, учитывая вышеизложенное, алгоритм расчета температуры из выражения (7) будет следующий:
1. На первом проходе безразмерная поверхностная температура (X = 0)
Θ* = |
πλVдi cos γi |
Θ = J |
Z |
i |
+ H |
i ) |
cos γ − J |
Z |
i |
− H |
i ) |
cos γ |
. |
|||||||||||||||||
|
|
|
|
|||||||||||||||||||||||||||
|
|
2q0a |
|
( |
|
|
|
|
|
|
i |
( |
|
|
i |
|
||||||||||||||
|
|
|
|
|
|
|
|
|
|
|
|
|
|
|
|
|
|
|
|
|
|
|
|
|
|
|||||
2. Остаточная безразмерная температура к началу второго прохода |
||||||||||||||||||||||||||||||
Θ1*/ |
= |
2π( |
|
(Zi − Li min − Hi )cos γi |
|
− |
|
|
(Zi − Li min + Hi )cos γi |
|
|
). |
||||||||||||||||||
|
|
|
|
|||||||||||||||||||||||||||
Безразмерная температура в результате второго прохода: Θ* |
= Θ* + Θ* / . |
|||||||||||||||||||||||||||||
|
|
|
|
|
|
|
|
|
|
|
|
|
|
|
|
|
|
|
|
|
|
|
|
|
2 |
1 |
||||
3. Остаточная безразмерная температура к началу третьего прохода |
||||||||||||||||||||||||||||||
/ |
|
2π( |
|
|
(Zi − Li max − Hi )cos γi |
|
|
|
|
|
(Zi − Li max + Hi )cos γi |
|
). |
|||||||||||||||||
Θ*2 |
= |
|
|
|
|
− |
|
|
|
|||||||||||||||||||||
|
|
|
|
|
|
|||||||||||||||||||||||||
Безразмерная |
|
|
температура |
в |
|
|
|
результате |
|
третьего |
|
|
|
|
прохода: |
/
Θ*3 = Θ*2 + Θ*2 … и т.д.
Выполним расчет максимальных поверхностных температур по формуле (7) при следующих условиях круглого торцевого шлифования корпуса автомобильного гидротолкателя на станке Supfina-802: абразивный круг 6 65×50×20 25АМ28М111К; шлифуемый материал – сталь 15ХГЮА, λ = 22,59 Вт/ (м °С), a = 5 10−6 м2 /с [1]; геометрические парамет-
ры зоны контакта инструмента с деталью h =1,875 10−3 м, S = 5,295 10−5 м2 ; параметры режима шлифования nк = 2750 об/мин, nд = 450 об/мин, ступени осевой подачи инструмента (Vп1 =10−5 м/с, Vп2 = 6 10−6 м/с,Vп3 = 4 10−6 м/с).
63
Стр. 63 |
ЭБ ПНИПУ (elib.pstu.ru) |
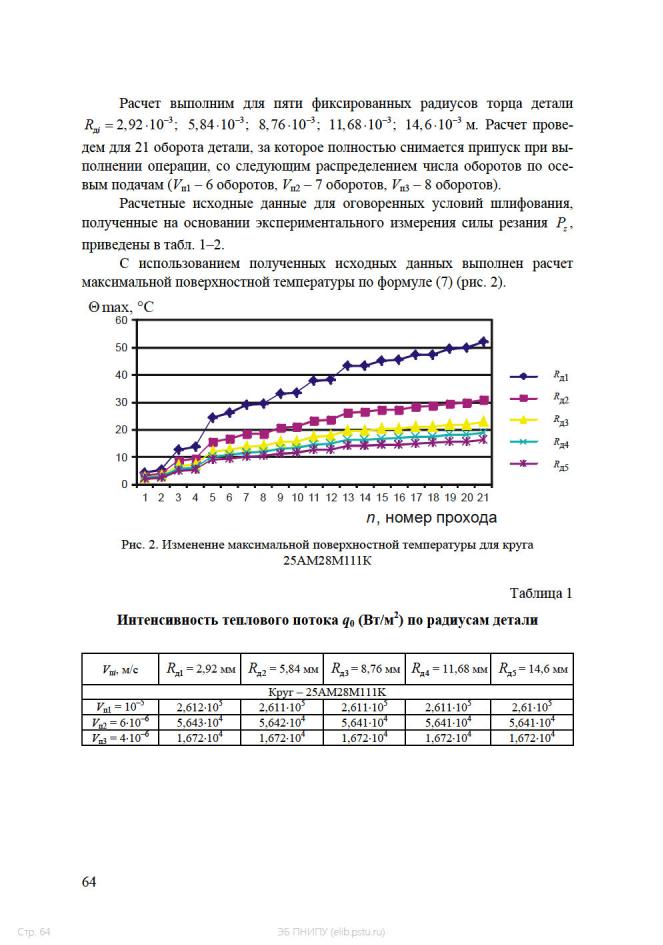
|
|
|
|
|
|
|
Таблица 2 |
|
|
Расчетные значения γi, Vдi |
|
|
|||
|
|
|
|
|
|
|
|
Rдi , мм |
2,92 |
|
5,84 |
8,76 |
|
11,68 |
14,6 |
γi , рад |
0,737 |
|
0,425 |
0,368 |
|
0,367 |
0,388 |
Vдi , м/с |
0,138 |
|
0,275 |
0,413 |
|
0,55 |
0,668 |
Полученные численные значения максимальных поверхностных температур не превышают предела теплостойкости стали 15ХГЮА [4], а следовательно, при выполнении операции круглого торцового шлифования для принятых технологических условий обработки не будет происходить изменение показателей исходного физико-механического состояния поверхностного слоя шлифуемых деталей.
Список литературы
1.Резников А.Н., Резников Л.А. Тепловые процессы в технологических системах. – М.: Машиностроение, 1990. – 228 с.
2.Сипайлов В.А. Тепловые процессы при шлифовании и управление качеством поверхности. – М.: Машиностроение, 1978. – 167 с.
3.Расчет температурного поля при многопроходном шлифовании торцом круга / В.А. Сипайлов [и др.] // Повышение надежности и долговечности изделий машиностроения: докл. конф. / Перм. политехн. ин-т. – Пермь, 1972. – С. 139–143.
4.Журавлев В.Н. Машиностроительные стали. Справочник. – М.: Машиностроение, 1992. – 246 с.
Получено 1.07.2010
Стр. 65 |
ЭБ ПНИПУ (elib.pstu.ru) |
УДК 621.923
А.А. Плотников, Г.В. Плотникова
Пермский государственный технический университет
ИССЛЕДОВАНИЕ УПРОЧНЕНИЯ ПОВЕРХНОСТНОГО СЛОЯ МИНИАТЮРНЫХ ДЕТАЛЕЙ В ЗАВИСИМОСТИ
ОТ СОСТОЯНИЯ МИКРОВЫГЛАЖИВАЮЩЕГО ИНСТРУМЕНТА
Проведены исследования основных показателей качества обработанных поверхностей при алмазном микровыглаживании в зависимости от длины пути трения алмазного микровыглаживателя. Рассмотрен показатель качества – упрочнение поверхностного слоя при микровыглаживании сталей и цветных сплавов.
Исследование качества поверхностей обрабатываемых миниатюрных деталей в зависимости от состояния обрабатывающего инструмента является одним из важных аспектов технологического обеспечения качества при алмазном микровыглаживании [1]. Упрочнение поверхностного слоя – важнейший показатель качества, характеризующий уровень технологического обеспечения качества и производительности алмазного микровыглаживания миниатюрных деталей [2] на основе технологического критерия.
Степень упрочнения определяется коэффициентом упрочнения, характеризует упрочняющую способность алмазного микровыглаживателя и определяется по формуле
Купр = |
HV20мик |
, |
|
||
|
HV20исх |
где HV20мик – микротвердость исходной поверхности перед алмазным микровыглаживанием, ГПа; HV20исх – микротвердость поверхности после алмазного микровыглаживания, ГПа.
По приведенной выше формуле рассчитаны численные значения коэффициента упрочнения Купр на различных участках рабочего пути микровыглаживания Lм. Величины показателей на разных отрезках их рабочих путей скольжения для используемых в исследованиях материалов приведены в табл. 1–4. Графическое отображение закономерностей изменения коэффициента упрочнения Купр по длине рабочего пути трения Lм алмазных микровыглаживателей для сталей 20 и 16Х16Н3МАД представлено на рис. 1, цветных сплавов – латуни ЛС59–1Т и дюралюминия Д1Т – на рис. 2.
66
Стр. 66 |
ЭБ ПНИПУ (elib.pstu.ru) |
Таблица 1
Изменение параметров микровыглаживания в зависимости от длины пути алмазного микровыглаживателя по стали 20
Длина пути L, км |
Микротвердость HV20, МПа |
Коэффициент упрочнения |
|
|
Купр, ед. |
1 |
2600 |
1,27 |
2 |
2580 |
1,26 |
3 |
2540 |
1,24 |
6 |
2480 |
1,21 |
9 |
2410 |
1,18 |
12 |
2310 |
1,13 |
15 |
2290 |
1,12 |
18 |
2270 |
1,11 |
21 |
2270 |
1,11 |
24 |
2250 |
1,10 |
27 |
2210 |
1,08 |
30 |
2210 |
1,08 |
Таблица 2
Изменение параметров микровыглаживания в зависимости от длины пути алмазного микровыглаживателя
по стали 16Х16Н3МАД
Длина пути L, км |
Микротвердость HV20, МПа |
Коэффициент упрочнения |
|
|
Купр, ед |
0 |
5340 |
1,668 |
1 |
5850 |
1,828 |
2 |
5230 |
1,634 |
15 |
4690 |
1,465 |
18 |
4620 |
1,443 |
21 |
4230 |
1,321 |
24 |
3470 |
1,084 |
27 |
3300 |
1,031 |
30 |
3640 |
1,138 |
67
Стр. 67 |
ЭБ ПНИПУ (elib.pstu.ru) |
Таблица 3
Изменение параметров микровыглаживания в зависимости от длины пути алмазного микровыглаживателя по латуни ЛС59–1Т
Длина пути L, км |
Микровердость HV20, МПа |
Коэффициент упрочнения |
|
|
Купр, ед. |
1 |
1730 |
1,27 |
2 |
1690 |
1,24 |
3 |
1650 |
1,21 |
6 |
1590 |
1,17 |
9 |
1540 |
1,13 |
12 |
1530 |
1,12 |
15 |
1480 |
1,08 |
18 |
1460 |
1,07 |
21 |
1450 |
1,07 |
24 |
1410 |
1,04 |
27 |
1420 |
1,04 |
30 |
1400 |
1,03 |
Таблица 4
Изменение параметров микровыглаживания в зависимости от длины пути алмазного микровыглаживателя по дюралюминию Д1Т
Длина пути L, км |
Микротвердость HV20, МПа |
Коэффициент упрочнения |
|
|
Купр, ед. |
1 |
1150 |
1,34 |
2 |
1120 |
1,31 |
3 |
1110 |
1,30 |
6 |
1100 |
1,29 |
9 |
1070 |
1,25 |
12 |
1060 |
1,24 |
15 |
1010 |
1,18 |
18 |
1000 |
1,17 |
21 |
1000 |
1,17 |
24 |
1000 |
1,17 |
27 |
1010 |
1,18 |
30 |
990 |
1,16 |
Как следует из вида полученных уравнений коэффициента сглаживания, кривые зависимостей для всех материалов имеют параболический характер.
68
Стр. 68 |
ЭБ ПНИПУ (elib.pstu.ru) |
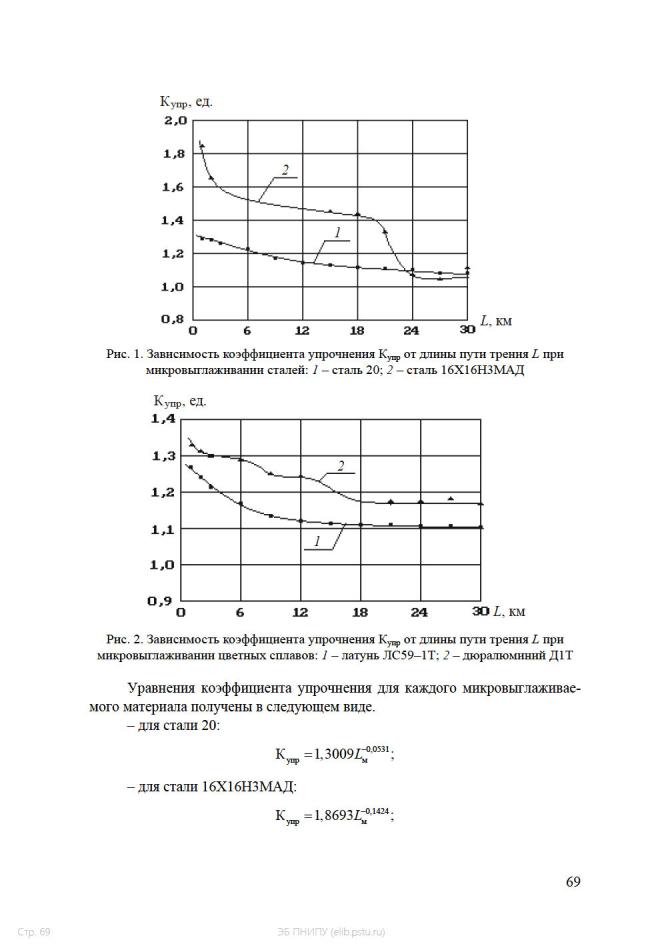
– для латуни ЛС59–1Т:
Купр =1,2927L−м0,0644 ;
–для дюралюминия Д1Т:
Купр =1,3607L−м0,0458 .
Результаты исследований показывают, что самый высокий коэффициент упрочнения достигнут у легированной стали 16Х16Н3МАД. Максимальное значение коэффициента упрочнения для этой стали достигает 1,6–1,8.
Высокое значение коэффициента сохраняется до значений трения микровыглаживателя L = 18–20 км. Затем ресурс инструмента исчерпывается, и он нуждается в переточке.
Несколько ниже коэффициент упрочнения конструкционной стали 20. Здесь его максимальное значение Купр = 1,3. На участке пути трения до 12 км значение коэффициента сглаживания падает до 1,1. На этом ресурс инструмента исчерпывается, и он нуждается в переточке.
У цветных сплавов – латуни ЛС59–1Т и дюралюминия Д1Т – характер изменения упрочнения примерно одинаков. Максимальное значение упрочнения для них составляет Купр 1,3. При этом, несмотря на постепенное уменьшение, удовлетворительное значение коэффициента сглаживания у дюралюминия Д1Т сохраняется на всем пути микровыглаживания – до 30 км. У латуни ЛС59–1Т наблюдается аналогичная картина при несколько низком значении коэффициента. При достижении значения пути трения 24 км значение коэффициента упрочнения становится Купр 1,1.
Параметры уравнений коэффициента упрочнения для различных марок обрабатываемых материалов миниатюрных деталей, рассчитанные по выведенным выше формулам, даны в табл. 5.
|
|
|
|
|
|
|
|
|
Таблица 5 |
Коэффициенты уравнений основных параметров качества алмазных |
|||||||||
|
|
|
|
микровыглаживателей |
|
|
|||
|
|
|
|
|
|
|
|
|
|
Пара- |
Обозна- |
|
Формула |
Коэф- |
Тип обрабатываемого материала |
||||
метр |
чение |
|
фициент |
Сталь 20 |
16Х16Н3 |
ЛС59–1Т |
Д1Т |
||
|
|
|
|
|
|
|
|
|
|
Упроч- |
Купр, ед. |
К |
|
= а Lk4 |
а4 |
1,3009 |
1,8693 |
1,2927 |
1,3607 |
нение |
|
упр |
4 м |
к4 |
–0,0531 |
–0,1424 |
–0,0644 |
–0,0458 |
Результаты работы позволяют сделать следующие выводы.
1. Выполнено исследование качества поверхностей при алмазном микровыглаживании миниатюрных деталей в зависимости от состояния рабочей
70
Стр. 70 |
ЭБ ПНИПУ (elib.pstu.ru) |