
2794.Электронно-лучевая сварка
..pdf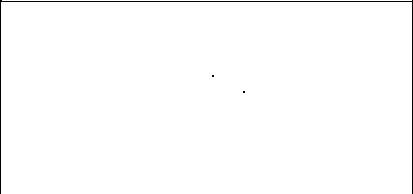
занимает промежуточное место между электрической дугой и мощным концентрированным электронным пучком или лазерным лучом. Если сравнить достижимыe полные мощности концентрированных источников энергии, используемых в настоящее время в промышленности, то самыми мощными являются плазменные и электронно-лучевые источники (их полная мощность может достигать нескольких мегаватт), а самые мощные технологические лазеры, работающие в непрерывном режиме, имеют мощность порядка десятков киловатт (сюда не входят лазеры для военного применения). Источники электропитания лазерных сварочных установок при равной мощности с питающими устройствами электронно-лучевых агрегатов имеют значительно большие габариты из-за меньшего коэффициента полезного действия при трансформации электрической энергии в энергию лазерного луча.
Значенияплoтностимощностиисточника тепла, Вт/м2
103 |
|
|
106 |
|
|
|
109 |
|
|
|
1012 |
|
|
|
1015 |
|
|
|
|
Дуговаясварка |
|
|
|
|
|
|
|
|
|
|
|||
|
|
|
|
|
|
Плазменная |
|
|
|
|
|
|
||||
|
|
|
|
|
|
сварка |
|
|
|
|
|
|
|
|
||
|
|
|
|
|
|
|
|
|
|
|
Лазернаясварка |
|
|
|
||
|
|
|
|
|
|
|
|
|
|
|
ЭЛС |
|
|
|
||
Нагревобразца |
Радиальная теплопере- |
|
Испарениематериала, |
Интенсивное |
||||||||||||
инезначительное |
дачавсвариваемом |
теплопередача илокаль- |
испарение |
|||||||||||||
плавлениемате- |
изделииилокальное |
ноерасплавление сболь- |
ивыбросма- |
|||||||||||||
риала |
расплавлениевзоне |
шимотношениемглуби- |
териалаиз |
|||||||||||||
|
|
|
|
нагрева |
|
нызоныпроплавления |
зонывоздей- |
|||||||||
|
|
|
|
|
|
|
|
|
|
|
кееширине |
ствия |
Рис. 2.1. Распределение плотности мощности источников тепла при сварке и характер протекающих тепловых процессов
С появлением лучевых технологий стало возможным значительно уменьшить размеры зон нагрева материала до высоких температур (сварной шов, зона термического влияния, зона протекания деформационных процессов) и ускорить процесс свар-
161
ки. Мощный пучок электронов и лазерный луч применяются для сварки (как и для плавки, испарения и напыления пленок, локальной размерной обработки, формирования отверстий и резки, поверхностной термической обработки) уже более пяти десятилетий. Высокая плотность мощности теплового источника приводит к почти адиабатическому процессу нагрева части материала изделия и, следовательно, к высокой эффективности использования энергии.
Энергия электронов в пучках, применяемых в технологических процессах, может существенно различаться. Электронные пучки с ускоренными до энергии 175 кэВ электронами применяются для рассмотренных выше методов термического воздействия пучка на материал изделия, в то время как электронные пучки с энергией электронов от 100 кэВ до 10 MэВ являются более эффективными для радиационной (нетермической) обработки материалов и получения покрытий. В качестве примеров здесь можно привести использование высокоэнергетических электронных пучков для отверждения печатных красок в современной полиграфии (взамен ультрафиолетового отверждения, при котором используются дорогие светочувствительные компоненты типографской краски), улучшение термостойкости изоляции электрических кабелей, создание немнущихся гидрофобных тканей и многое другое.
Мощные электронные пучки кроме высокой плотности энергии в зоне взаимодействия с образцом характеризуются и широкими возможностями контроля и гибкого управления их пространственно-энергетическими параметрами. Важнейшие этапы процесса, по которым можно классифицировать технологические электронные пучки, приведены на рис. 2.2.
Основные параметры мощных электронных пучков – это диаметр пучка, угол сходимости (или расходимости), положение фокуса (минимального сечения) пучка, стабильность характеристик и их воспроизводимость при многократных настройках параметров пучка. Диаметр и положение минимального сечения
162
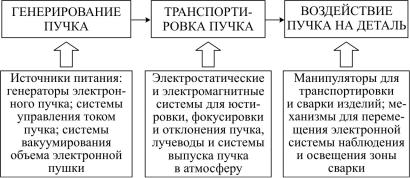
электронного пучка (фокуса) по отношению к рабочей поверхности свариваемого изделия сильно влияют на характер воздействия пучка на материал.
Рис. 2.2. Оборудование для генерации и технологического применения мощных электронных пучков. Общие характеристики и вспомогательное оборудование
Генерирование электронного пучка осуществляется элек- тронно-оптической системой (электростатической частью) электронной пушки. Формирование и точное направление электронного пучка в заданную область поверхности изделия, а также перенос энергии от генератора пучка к обрабатываемому изделию осуществляются системой транспортировки электронного пучка. Транспортировка электронов пучка до обрабатываемого изделия происходит практически мгновенно (со скоростью, близкой к скорости света). В пространстве ускорения электронов необходимо наличие вакуумной среды (давление остаточных газов не должно превышать 10–5 Па). Технологические электронные пучки, как правило, фокусируются магнитными полями, создаваемыми концентрической по отношению к пучку электромагнитной катушкой, называемой фокусирующей линзой. Для создания сильного поля магнитопровод фокусирующей линзы находится в непосредственной близости
163
от фокусирующей катушки с немагнитным промежутком между обмоткой и внутренней цилиндрической поверхностью магнитопровода. Отклонение электронного пучка осуществляется отклоняющей системой, создающей поперечное магнитное поле в двух взаимно перпендикулярных направлениях. Для быстрого отклонения в качестве магнитопровода в отклоняющей системе электронной пушки используются сердечники из высокочастотного феррита, а в некоторых случаях катушки отклоняющей системы изготавливаются без ферромагнитных сердечников. В зависимости от давления в технологической вакуумной камере (вакуум 10–3 –10 –4 Па, форвакуум 10–10 –1 Па или атмосферное давление) система транспортировки должна обеспечить необходимый перепад давления между пространством ускорения электронов в электростатической части электронной пушки и технологическим пространством (вакуумной камерой). При разности значений давления на два-три порядка (между высоким вакуумом в электронной пушке и форвакуумом в технологической вакуумной камере) требуется достаточно узкая анодная диафрагма на выходе пушки, через которую проходит электронный пучок. Около анодной диафрагмы водоохлаждаемого анода в ряде электронных пушек расположены катушки стигматора, предназначенные для устранения деформации сечения электронного пучка и обеспечения совпадения электрической и механической осей электронной пушки.
Для выпуска электронного пучка в атмосферу изпользуют секционированный лучепровод с камерами, давление в которых распределено по градиенту в результате соответствующей дифференциальной откачки каждой из камер, а в последнюю из них производят напуск гелия. Такой лучепровод составлен из конических дюз, соединяющих эти камеры и создающих газодинамический эффект сопротивления для натекающего атмосферного газа. В последнее время для выпуска электронного пучка в атмосферу используется плазменное окно [6]. Для сбора вторичных
164
заряженных частиц, покидающих зону сварки, с целью совмещения оси электронного пучка со стыком между свариваемыми деталями или для управления положением фокусного пятна пучка по отношению к поверхности свариваемого материала в нижней части электронной пушки (после отклоняющих катушек) расположен один или несколько коллекторных электродов [7–10], изолированных от заземленного корпуса пушки и вакуумной камеры.
Из-за наличия пространственного заряда электронов максимальная плотность мощности электронного пучка ограничена величиной 108–10 12 Вт/м2. Лазерные лучи могут быть сфокусированными до более высоких значений плотности мощности. Однако в результате высокой эффективности преобразования электрической энергии сети в энергию электронного пучка (для электронных пучков потери энергии не превышают нескольких процентов) электронные пучки остаются вне конкуренции в области значений мощности, превышающих несколько десятков киловатт.
В то же время из-за возможности транспортировки лазерного луча в воздухе или газовой среде с давлением порядка 1 атм лазеры весьма эффективны для резки с локальным плавлением и последующим выносом жидкого материала потоком защитного инертного газа, а также реактивной силой испаряющегося материала или в результате механизма лазерной абляции. При плазменной резке также используется локальное расплавление металла, который уносится газовым потоком плазмообразующего или защитного газа. При этом из-за большого объема жидкой фазы в зоне резки упрочняемых сталей поверхность реза подвергается закалке, что вызывает проблемы при последующей механической обработке разрезанных этим методом заготовок.
165
2.2. ОБЛАСТИ ПРИМЕНЕНИЯ ЭЛС. ПРЕИМУЩЕСТВА И НЕДОСТАТКИ
Сварка электронным пучком – современный метод создания неразъемных соединений локальным расплавлением и последующим затвердеванием материала. Среди специальных способов сварки ЭЛС является наиболее распространенным способом, с помощью которого в индустриально развитых странах производят сварку тысячи тонн металлических конструкций. Это связано с тем, что ЭЛС обеспечивает возможность получения сварных швов с хорошими физико-механическими характеристиками при минимальных структурных изменениях и тепловых деформациях соединяемых деталей. По существующим оценкам мировой объем сварных конструкций, которые изготавливают с использованием ЭЛС, составляет 5 % от объема продукции, получаемой сваркой плавлением (для сравнения: доля электродуговой сварки по оценкам составляет 50 % этого объема). ЭЛС может осуществляться при больших скоростях, с высокой степенью автоматизации технологического процесса; в ряде случаев исключается необходимость в последующих механической и термической обработках; ЭЛС может производиться в существенной близости от термически нестойких элементов конструкции; снижается расход материалов (для ЭЛС не требуется специальных сварочных электродов, защитных газов или флюсов); ЭЛС не требует разделки кромок свариваемых деталей; при сварке толстостенных металлических конструкций обеспечивается существенная экономия электрической энергии.
Основное преимущество сварки мощным остро сфокусированным электронным пучком – это относительно малое количество вводимого тепла, что обусловливает минимальную ширину сварного шва и зоны термического влияния, а также небольшие деформации свариваемого изделия. Диапазон материалов, которые можно сваривать ЭЛС, достаточно широк и включает тугоплавкие и химически активные при высоких темпера-
166
турах материалы, а также материалы с сильно отличающимися физическими свойствами. При разработке технологического процесса ЭЛС для конкретного приложения следует учитывать множество факторов, таких как предварительная подготовка и очистка кромок стыка свариваемых деталей, использование высокого или промежуточного вакуума в технологической камере, геометрические параметры проплавления металла при формировании сварного шва, доступ электронного пучка к месту сварки, производительность и себестоимость технологического процесса ЭЛС. Сравнение различных процессов сварки с использованием в качестве источника тепла электронного пучка, лазерного луча и плазменного потока приведено в табл. 2.1.
Таблица 2 . 1
Сравнение процессов ЭЛС, лазерной и плазменной сварки
Параметр |
Электронный |
Лазер |
Плазма |
|
пучок |
||||
|
|
|
||
Глубина проникнове- |
0,5–200,0 |
0,5–50,0 |
0,1–10,0 |
|
ния, мм |
|
|
|
|
Скорость сварки |
Высокая |
Высокая |
Средняя |
|
Деформация |
Малые |
Малые |
Средние |
|
Плотность мощности, |
109–10 12 |
1011–10 13 |
108–10 10 |
|
Вт/м2 |
|
|
|
|
Максимальная мощ- |
100 |
10 |
15 |
|
ность, кВт |
|
|
|
|
Размер оборудования |
Очень большой |
Большой |
Средний |
|
Сравнение цен, отн. ед. |
5–10 |
10 |
1 |
|
Рабочие ограничения |
Высокое напряже- |
Оптическое |
Ультрафиолетовое |
|
|
ние, рентгеновское |
излучение |
излучение |
|
|
излучение |
|
|
|
Доступ к месту выпол- |
Недостаточный |
Очень |
Удовлетвори- |
|
нения шва |
|
хороший |
тельный |
Не всегда возможно однозначно определить целесообразность применения того или иного сварочного процесса. И элек- тронно-лучевой, и лазерный метод является приемлемым выбо-
167
ром для получения сварных соединений в ответственных дорогостоящих изделиях и узлах с большими значениями толщины металла и существенно отличающимися теплофизическими характеристиками, а также при наличии специфических требований к сварному соединению (наличие гальванического покрытия на деталях, получение соединений металл – стекло или металл – керамика, сварка поверхностей, подвергнутых химико-термичес- кой обработке или закалке поверхности вблизи шва).
ЭЛС – бесспорный выбор при необходимости соединения деталей с толщиной свыше 6 мм (за один проход без предварительной разделки кромок). Для небольшого годового объема свариваемых изделий (порядка тысяч или десяток тысяч сварных соединений) с небольшой глубиной проплавления эффективной является лазерная сварка. Следует отметить, что способность лазерного луча достигать недоступных для электронного пучка областей (например, при использовании оптических волокон) позволяет широко применять лазерную сварку для получения сварных швов во внутренних полостях свариваемого изделия. Комбинация из лазерного луча и плазменного или электродугового источника энергии широко применяется для сварки крупногабаритных корпусных узлов в судостроении и вагоностроении. Для обеспечения максимальной гибкости производства, непосредственного применения в широком диапазоне технологических условий, более низких критических требований к получаемым сварным соединениям и малых капитальных затрат лучшим технологическим выбором является плазменная и дуговая сварка с использованием различных электродов под слоем флюса или в защитных газах.
ЭЛС имеет очевидные преимущества при массовом производстве (сотни тысяч деталей в год). Применение вакуума как защитной среды для расплавленного металла обходится в 10…30 раз дешевле, чем защита зоны сварки аргоном при аргонодуговой сварке неплавящимся электродом. При ЭЛС деталей из легких металлов и сплавов не требуется применения
168
антиотражающих покрытий, как это необходимо в случае лазерной сварки. Изделия тяжелого машиностроения часто свариваются электронным пучком не в высоком, а в промежуточном вакууме (форвакууме). Электронные пучки с энергией 150 кэВ и выше могут выводиться из вакуумного пространства электронной пушки в атмосферу и производить сварку при атмосферном давлении, как уже упоминалось выше. Однако в этом случае необходима защита оператора-сварщика элек- тронно-лучевой сварочной установки от тормозного рентгеновского излучения, возникающего при соударении электронного пучка с металлом в зоне сварки. В исключительных случаях для ЭЛС крупногабаритных изделий создавались вакуумные камеры с целью создания локального вакуума, частью которых являлось само свариваемое изделие (труба большого диаметра, корпус корабля). Эти камеры после выполнения участка шва в допускаемом их габаритами пространстве передвигаются на новое место, и после откачки вакуума сварка продолжается снова.
Основные преимущества ЭЛС основаны на достижении в электронном пучке высокой плотности энергии, легком управлении параметрами пучка и возможности полной автоматизации процесса сварки. Вакуум как рабочая среда и значительное расстояние от электронной пушки до свариваемого изделия также являются положительными особенностями процесса. На рис. 2.3 показаны схематично наложенные одно на другое поперечные сечения сварных швов, полученных при электроннолучевой (1), плазменной (2) и аргонодуговой сварке (3). Отношение общих площадей зон проплавления соответствует отношению вложенной энергии при этих сварочных процессах, и, таким образом, наименьшая энергия вводится в свариваемое изделие при ЭЛС. При этом приспособления для крепления свариваемого изделия, необходимые для предотвращения механических деформаций и перемещения изделия во время сварки, обладают меньшей массой и габаритами, а иногда вообще не
169
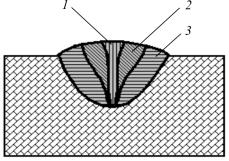
требуются. Термические деформации и напряжение в свариваемых изделиях при ЭЛС значительно меньше, чем при других способах сварки, а основная кристаллическая структура и свойства металла шва и околошовной зоны изменяются незначительно. Маленький объем жидкого металла при ЭЛС сильно уменьшает уровень внутреннего напряжения, и в большинстве случаев не является необходимой дополнительная термическая обработка сварного шва. Маленькая зона термического влияния около шва при ЭЛС, которая является результатом воздействия концентрированной энергии пучка, и невысокие значения температуры основного металла сварочной конструкции во время процесса сводят к минимуму деформации свариваемых деталей.
Рис. 2.3. Сравнениепоперечныхсеченийсварныхшвов приразличныхспособахсварки: 1 – ЭЛС; 2 – плазменная сварка; 3 – электродуговаясварка
ЭЛС дает возможность сваривать прецизионные детали приборостроения с микронными размерами. В то время, как электрическая дуга трудно управляется при очень малых значениях мощности, электронный пучок является удобным тепловым источником для прецизионного соединения тонких деталей и микросварки. Проблемой здесь может являться малый размер ванны расплавленного металла, который требует высокой точности подготовки стыка свариваемых деталей и обеспечения
170