
748
.pdf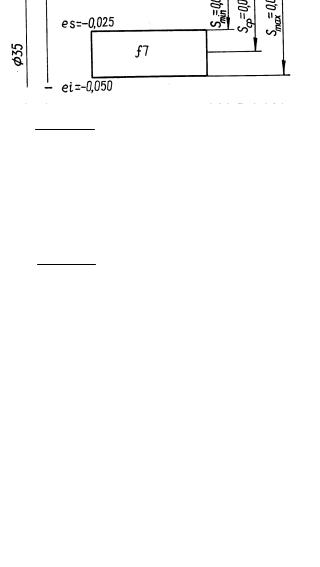
2.2.2.По этому же стандарту выбирается одна из предпочтительных посадок в системе вала. Если из этих посадок нельзя сделать выбор, то переходим к следующему подпункту.
2.2.3.Выбирается непредпочтительная посадка в системе отверстия. Эти посадки в таблицах графически не выделены. В случае отсутствия посадки, удовлетворяющей условию формулы (2.6), переходим к п. 2.2.4.
2.2.4.Назначается непредпочтительная посадка в системе вала или переходим к п.2.2.5.
2.2.5.Допускается образование посадки сочетанием иных стандартных полей отверстия и вала по ГОСТ 25347–82. При этом желательно, чтобы посадка была в системе отверстия или в системе вала и допуск у отверстия был больше, чем у вала (разность может быть не более двух квалитетов). Такие посадки технологичнее.
2.2.6.Если выбор стандартной посадки по пп. 2.2.1, 2.2.2, 2.2.3, 2.2.4, 2.2.5 оказался невозможным, то необходимо провести расчет упрощенным способом с учетом отклонений формы и расположения поверхностей сопрягаемых изделий [7; 9, с. 304; 16] и после определения расчетного зазора выбрать посадку в вышеуказанной последовательности.
Посадки H/h и H/a не назначать!
2.2.7. Сделать проверку выбранной посадки по наименьшей толщине масляной пленки hmin в установившемся рабочем режиме. Жидкостное трение в ПС может быть обеспечено при условии:
hmin ≥ RzD + Rzd, |
(2.7) |
где
|
hS |
|
hmin = |
Smax ст + 2(RzD + Rzd) . |
(2.8) |
Если условия формулы (2.7) не соблюдаются, то возможно полусухое или сухое трение. В этом случае необходимо расчет ПС провести более точным способом [7, 9, 16].
2.3.Определение основных характеристик посадки
2.3.1.Выбранную посадку записать символами и указать отклонения, например:
H7(+0,025)
35 f 7(−−00..025050 ) .
2.3.2.Вычертить в масштабе схему расположения полей допусков, указать характеристики посадки (рис. 2.2).
2.3.3.Дать заключение о сопряжении и его элементах. При этом необходимо указать: систему посадки, предпочтительность посадки, допуски на изготовление отверстия и вала, какая деталь выполнена точнее, значения зазоров и допуск посадки. Например, для посадки
H7(+0,025)
35 f 7(−−00..025050 )
основными показателями являются: посадка с зазором в системе отверстия, предпочтительная, допуск отверстия TD = 0,025 мм, допуск вала Td = 0,025 мм, одинаковая точность изготовления деталей, зазоры Smax = 0,075 мм, Smin = 0,025 мм, Sср = 0,050 мм, допуск посадки с зазором TПS = 0,050 мм (рис. 2.2).
Рис. 2.2. Схема расположения полей допусков посадки 35 H7/f7
2.4.Расчет и выбор посадки уточненным способом
Вобщем случае расчет ПС другими методами сводится к определению относительного оптимального зазора [9, 16]:

Sопт = ψопт d; |
(2.9) |
||
|
|
|
|
ψопт = 0,293К µn/ p , |
(2.10) |
где d ― номинальный диаметр, м; К ― коэффициент, учитывающий угол охвата шейки и отношение l/d; при l/d = 1 ϕ = 180о, К = 1 [7, 16]; µ ― динамическая вязкость масла при 50оС, Па·с; n
―частота вращения, об/мин; p — среднее давление на опору (см. формулу (2.1)). Затем определяются [Smin], [Smax], [TПS] и выбирается посадка.
При упрощенном методе после предварительного определения hmin, [hmin], χmin рассчитываются CR (нагруженность ПС), а затем — [Smin], [Smax], Sопт и выбирается стандартная посадка, обеспечивающая условия неравенств
Smin > [Smin] и [Smax] < Smax.
2.5. Выбор средств измерения
На результаты измерений влияют многие факторы: характер физической величины, метод измерения, качество применяемого СИ, условия среды (температура, давление, влажность), субъективный фактор (человек) и др. Единицы измерения физических величин приведены в табл. П.2.1. Результат измерений отличается от истинного значения измеряемой величины, и разность между ними называется погрешностью измерения (см. тему 4 [11]).
Посадка предопределяет необходимую точность изготовления сопрягаемых деталей и их измерения. В соответствии с номинальным размером, видом контролируемой поверхности и требуемой точностью изготовления детали необходимо установить метод измерения и выбрать СИ [4, 13, 16].
Допуск размера является основной характеристикой для расчета допускаемой погрешности измерений, которая составляет 20…30 % допуска размера (табл. П.2.2). Допускаемая погрешность измерений состоит из суммы погрешностей: погрешности СИ (наибольшая составляющая), погрешности установочных мер, погрешности условий измерений, погрешности базирования детали и величины измерительной силы и др. Каждое СИ характеризуется основной погрешностью, величина которой указывается в паспорте. СИ выбирается таким образом, чтобы его наибольшая абсолютная погрешность была меньше допускаемой погрешности измерений (табл. П.2.3). В общем случае выбор СИ проводится в следующей последовательности: устанавливается наименование, тип, пределы измерения прибора (инструмента) и пределы измерений по шкале; рассчитывается предельно допустимая абсолютная погрешность измерения и выбирается СИ, погрешность которого меньше допустимой.
Ниже рассмотрены примеры выбора СИ для деталей, образующих посадки с зазором 35H7/f7 и 20H12/h12 [10, с. 162–172]. Для измерений отверстий 35H7, 20H12 и валов 35f6, 20H12 СИ выбираются в следующей последовательности.
2.5.1.Из ГОСТ 23347–82 устанавливаются отклонения, рассчитываются и записываются в таблицу формы табл. 2.3 допуски каждого размера.
2.5.2.В зависимости от размера и квалитета точности детали из табл. П.2.2 (ГОСТ 8.051–81) для каждого размера определяется допускаемая погрешность измерения и заносится в табл. 2.3.
2.5.3.Из табл. П.2.3 (см. прил. 2) выбирается СИ, предельная абсолютная погрешность которого не превышает допускаемую погрешность измерения. При этом учитываются особенности измеряемых элементов детали (вал или отверстие), пределы измерения, надежность и удобство в эксплуатации и экономическая целесообразность использования данного СИ [4, с. 162–172]. Так, например, для измерения отверстия 35H7 выбран нутромер мод. 109 ГОСТ 9244–75 [4]. Для отверстия 20H12 могут быть использованы два инструмента: штангенциркуль ШЦ-II-160-0,05 ГОСТ 166–89 и нутромер индикаторный второго класса точности НИ 18-50-2 ГОСТ 6507–90, — из которых по экономическим соображениям первый наиболее предпочтителен. Измерение вала 20h12 также проводится штангенциркулем ШЦ-II. Для измерения вала 35f7 могут быть использованы несколько СИ: микрометры
гладкие МК 50-2 (первого и второго класса точности) с погрешностью соответственно ±2,5 мкм и ±4 мкм; рычажная скоба СР50 с погрешностью ±3 мкм. Из перечисленных СИ вала 35f7 наиболее распространенным, простым в обращении и надежным в эксплуатации является микрометр МК-50-2 ГОСТ 6507–90. Поэтому выбран данный инструмент с пределами допускаемой погрешности ± 4 мкм.
Метрологические показатели СИ занести в таблицу формы табл. П.2.3.
Таблица 2.3
Выбор средств измерений
|
Допуск |
Допускаемая |
|
Предельно |
|
|
Средство |
допускаемая |
|||
Размер, мм |
размера, |
погрешность |
|||
измерения (СИ) |
погрешность |
||||
|
мкм |
измерения, мкм |
|||
|
|
СИ, мкм |
|||
|
|
|
|
35H7( |
+0,025 ) |
25 |
7 |
Нутромер мод. 109 |
3,5 |
|
ГОСТ 9244–75 |
||||||
|
0 |
|
|
|
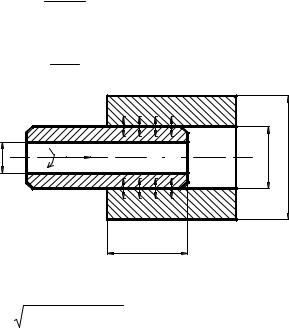
Окончание табл. 2.3
|
|
Допуск |
Допускаемая |
|
Предельно |
|
|
|
Средство |
допускаемая |
|||
Размер, мм |
размера, |
погрешность |
||||
измерения (СИ) |
погрешность |
|||||
|
|
мкм |
измерения, мкм |
|||
|
|
|
СИ, мкм |
|||
|
|
|
|
|
||
|
+0210 ) |
|
|
Штангенциркуль |
|
|
20H12( |
210 |
50 |
ШЦ-П-160-0,05 |
50 |
||
|
0 |
|
|
ГОСТ 166–89 |
|
|
|
|
|
|
|
||
−0,025 |
25 |
7 |
Микрометр МК 50-2 |
4 |
||
35f7( −0,050 ) |
ГОСТ 6507–90 |
|||||
20h12( |
0 |
|
|
Штангенциркуль |
|
|
−0,210 |
210 |
50 |
ШЦ-II-160-0,05 |
50 |
||
) |
|
|
|
ГОСТ 166-89 |
|
Задание 3. Расчет и выбор неподвижной посадки. Выбор средств измерения
Рассчитать и выбрать посадку с натягом для передачи крутящего момента и (или) осевого усилия в соединении вал–втулка.
Геометрические показатели соединения приведены на рис. 3.1: l ― длина сопряжения, м; d1 — внутренний диаметр полого вала, м (для цельного вала d1 = 0); d ― номинальный диаметр сопряжения, м; d2 ― наружный диаметр втулки, м; Мкр ― крутящий момент, Н · м; Fос ― осевая сила, Н.
Материал втулки ― сталь, чугун или бронза, материал вала ― сталь.
Материалы и режим работы сборочной единицы вал–втулка задаются руководителем.
3.1. Порядок расчета и выбора посадки
Вопросы взаимозаменяемости неподвижных посадок рассмотрены в теме № 8 [11].
3.1.1. Определить удельное давление в поверхности сопряжения деталей, необходимое для передачи соответствующей нагрузки [7; 9, с. 361; 16]:
при наличии крутящего момента
2nMкр |
|
|
p = πd 2lf |
; |
(3.1) |
при действии осевой силы |
|
|
|
|
|
|
|
p = |
nFос |
; |
|
(3.2) |
|
|
|
πdlf |
|
|
|
|
|
d1 |
Foc |
Р |
d |
d2 |
|
d |
d d |
|||||
1 |
|
|
|
2 |
|
|
|
|
Mkp |
|
|
|
|
|
l |
|
|
l |
|
|
|
|
Рис. 3.1. Схема неподвижного соединения |
|
при одновременном воздействии крутящего момента и осевой нагрузки
|
n (2M |
кр |
/ d)2 |
+ F |
2 |
|
|
p = |
|
|
ос |
, |
(3.3) |
||
|
πdlf |
|
|
||||
|
|
|
|
|
|
где р ― удельное давление, МПа; n ― коэффициент запаса прочности соединения, в расчетах принять n = 1,1…1,5 [7] (для первой учебной группы n = 1,1; для второй ― n = 1,2 и т.д.); f ― коэффициент трения, выбирается в зависимости от вида запрессовки и материалов сопрягаемых деталей; f = 0,08…0,14 [7; 9, табл. 1.104].
3.1.2. Определить необходимый наименьший расчетный натяг соединения толстостенных цилиндрических изделий по формулам, известным из решения задач Ляме [9]:
C |
D |
+ |
C |
d |
|
|
|
Nmin = [Pmin] d |
|
|
, |
(3.4) |
|||
|
|
|
|
||||
ED |
|
Ed |
|
где Nmin ― наименьший расчетный натяг, м; [Pmin] ― значение наименьшего функционального давления в поверхности сопряжения вал–втулка, необходимого для передачи нагрузки, Па. Принять [Pmin] равным значению удельного давления, рассчитанному по одной из формул (3.1)…(3.3); d ― номинальный диаметр сопряжения, м; ED, Ed ― модули упругости материалов втулки и вала. Для стали Е = 2,0 ·1011 Па [7; 9, табл. 1.106, табл. П.3.2 настоящего издания]; CD, Cd ― коэффициенты для втулки и вала, определяются по формулам [9, табл. 1.107]:
CD = |
1+ (d / d 2 |
)2 |
+ µD ; |
(3.5) |
||||||
|
|
|
|
|
|
|||||
1 |
− (d |
/ d2 )2 |
||||||||
|
|
|
|
|||||||
Cd = |
|
1+ (d |
1 |
/ d)2 |
− µd |
, |
(3.6) |
|||
|
|
|
|
|
||||||
1 |
− (d |
1 |
/ d)2 |
|||||||
|
|
|
|
|||||||
|
|
|
|
|
|
|
|
|
где d1, d, d2 ― геометрические данные неподвижного соединения (см. рис. 3.1); µD, µd ― коэффициенты Пуассона для материалов втулки и вала.
Для стали µ = 0,30, для бронзы µ = 0,35, для чугуна µ = 0,25 [7; 9, табл. 1.106, табл. П.3.3 настоящего издания].
3.1.3. Наименьший функциональный натяг определить по формуле [7, 9, 16]
[Nmin] = Nmin + jш + jt + jц + jn, |
(3.7) |
где Nmin ― наименьший расчетный натяг (см. формулу (3.4)); jш ― поправка, учитывающая смятие неровностей поверхностей деталей при сборке, м (табл. П.3.4), [9, с. 362]; jt ― поправка, учитывающая влияние изменения линейных размеров материалов деталей за счет разницы температур работы и сборки, м [9, с. 363]; jц ― поправка за счет ослабления натяга из-за центробежных сил, м (при диаметре сопряжения деталей d > 500 мм и скорости вращения v > 30 м/с) [7, 9, 16]; jn ― поправка, вносимая повторной запрессовкой, м.
При выполнении данного задания в курсовом проекте можно принять [Nmin] = Nmin + jш, так как первичная сборка (jn = 0) деталей из стали осуществляется при температуре работы соединения (jt = 0), а влияние центробежных сил несущественно (jц = 0).
Поправка jш, учитывающая смятие неровностей при запрессовке, определяется по формуле γш = 2K(RzD + Rzd) [7; 9, табл. 2.68, формула (1.113)].
При выполнении задания рекомендуется в зависимости от размера соединения предварительно принять шероховатость поверхности отверстия RzD = 6,3·10-6 м и вала Rzd = 3,2·10-6 м (табл. 3.1) и рассчитать ее суммарное значение по формуле
jш = 1,2 (RzD + Rzd) ≈ 5 (RаD + Rаd). |
(3.8) |
Таблица 3.1
Шероховатость поверхностей отверстия и вала для посадок с натягом
|
|
Поля допусков |
|
|
|
Поля допусков валов |
|
|||
|
|
отверстий |
|
|
|
|
|
|||
Интервал |
|
|
|
|
|
|
|
|
||
|
H7, R7, S7, |
|
H8, |
|
|
r5, |
h6, p6, r6, s6, |
h7, s7, u7, |
U8, X8, |
|
размеров, мм |
H6 |
|
|
H9 |
||||||
|
|
U7 |
|
U8 |
|
|
s5 |
z6 |
s8 |
Z8 |
|
|
|
|
|
Значения Rz, мкм, не более |
|
|
|||
От 1 до 3 |
1, |
|
|
3,2 |
|
|
0,8 |
|
|
3,2 |
6 |
|
|
|
6, |
1,6 |
|
||||
|
3,2 |
|
|
|
|
3,2 |
|
|||
Свыше 3 до 6 |
|
|
|
|
3 |
|
|
|
||
|
|
|
|
|
|
|
|
|
||
Свыше 6 до10 |
3, |
|
|
6,3 |
|
|
1,6 |
|
|
6,3 |
Свыше 10 до 18 |
|
|
|
|
|
|
|
|
|
|
2 |
|
|
|
|
|
|
|
|
|
|
Свыше 18 до 30 |
6,3 |
|
|
|
10 |
|
3,2 |
|
|
|
|
|
|
|
|
|
|
||||
Свыше 30 до 50 |
|
|
10 |
|
|
|
6,3 |
|
||
|
|
|
|
|
|
|
|
|||
Свыше 50 до 80 |
|
|
|
|
|
3,2 |
|
|
|
|
|
|
|
|
|
|
|
|
|
||
Свыше 80 до 120 |
|
|
|
|
|
|
|
|
|
|
|
|
|
|
|
|
|
|
|
|
|
Свыше 120 до |
6, |
|
|
|
|
|
|
|
|
|
180 |
3 |
|
|
|
|
|
|
|
|
|
Свыше 180 до |
|
|
|
|
|
|
|
6,3 |
|
10 |
250 |
|
|
|
|
|
|
|
|
|
|
|
|
|
|
|
|
|
|
|
|
|
Свыше 250 до |
|
10 |
|
20 |
|
20 |
|
|
10 |
|
315 |
|
|
|
|
|
|
|
|
||
|
|
|
|
|
|
6,3 |
|
|
|
|
Свыше 315 до |
10 |
|
|
|
|
|
|
|
|
|
|
|
|
|
|
|
|
|
|
||
400 |
|
|
|
|
|
|
|
|
|
|
|
|
|
|
|
|
|
10 |
|
|
|
Свыше 400 до |
|
|
|
|
|
|
|
|
|
|
|
|
|
|
|
|
|
|
|
|
|
500 |
|
|
|
|
|
|
|
|
|
|
3.1.4. Определить предельно допустимые давления в поверхностях отверстия и вала:
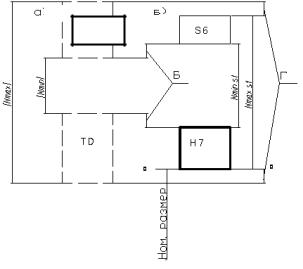
pmaxD = 0,58 σTD [1− (d / d2 )2 ], |
(3.9) |
pmaxd = 0,58 σTd [1− (d1 / d)2 ], |
(3.10) |
где pmax D, pmax d ― предельно допустимые давления в поверхностях отверстия и вала, Па; σTD и σTd ―
пределы текучести материалов втулки и вала, Па (табл. П.3.2, ГОСТ 1050–88); d, d1, d2 ― геометрические исходные данные неподвижного соединения, м (см. рис. 3.1).
Наибольшее функциональное давление [Pmax] выбирается равным меньшему из двух значений, рассчитанных по формулам (3.9), (3.10).
3.1.5. Определить наибольший допустимый (функциональный) натяг неподвижной посадки по формуле
[Nmax] = Nmax jуд + jш – jt, |
(3.11) |
где Nmax ― наибольший расчетный натяг, м,
|
С |
D |
|
C |
d |
|
|
|
Nmax = [Pmax] d |
|
+ |
|
|
, |
(3.12) |
||
|
|
|
|
|||||
|
ED |
|
|
|
|
|
|
|
|
|
Ed |
|
|
где [Pmax] ― значение наибольшего функционального давления, Па (см. п. 3.1.4); jуд ― коэффициент, учитывающий увеличение натяга на торцах охватывающей поверхности; jш ― поправка, учитывающая смятие неровностей поверхностей отверстия и вала, м; jt ― поправка, учитывающая изменение (увеличение) натяга при рабочей температуре.
При выполнении данного задания принять jt = 0, jуд = 1, так как температура сборки и работы сборочной единицы одна, а увеличение натяга на торцах несущественно [7; 9, с. 364]. Тогда определение [Nmax] сводится к определению по формуле
[Nmax] = Nmax + jш, |
(3.13) |
где
jш = 2K(RzD + Rzd) ≈ 5 (RaD + Rad),
здесь RzD и Rzd ― шероховатости поверхностей отверстия и вала, м; K ― коэффициент величины смятия микронеровностей (табл. П.3.4), можно принять 2K = 1,2 [7; 9, с. 362; 16].
3.1.6. По функциональным предельным значениям натягов выбрать стандартную неподвижную посадку, удовлетворяющую условиям:
Nmin ст ≥ [Nmin], |
(3.14) |
Nmax ст ≤ [Nmax], |
(3.15) |
где Nmin ст и Nmax ст ― предельные значения натягов стандартной (выбранной) посадки. Если условия неравенств (3.14), (3.15) не выполняются, то посадка выбрана неверно.
Порядок выбора посадки подобен выбору, рассмотренному в задании 2 (выбор стандартной посадки). Допуск выбранной стандартной посадки с натягом должен быть не менее 60 % от допуска рассчитанной посадки.
Примечание. После расчета и выбора посадки с натягом необходимо уточнить соответствие между точностью изготовления деталей и шероховатостью их поверхности по табл. 3.1 и при необходимости провести корректировку в расчетах и повторно выбрать посадку.
а) |
б) |
S6 |
Рис. 3.2. Схемы полей допусков посадки с натягом:
а— схема полей посадки, рассчитанной с функциональными натягами;
б— схема полей выбранной стандартной посадки
Для выбранной стандартной посадки построить схемы полей допусков, указать числовые значения отклонений (рис. 3.2), определить основные характеристики (Nmax, Nmin, TПN) и рассчитать величины запаса прочности при эксплуатации соединения Б и запаса прочности при сборке Г по формулам:
Б = Nmin ст – [Nmin], |
(3.16) |
Г = [Nmax] – Nmax ст. |
(3.17) |
3.2. Проверка правильности выбора посадки с натягом
Для того, чтобы проверить правильность выбора посадки с натягом, т.е. способность детали на неразрушаемость при сборке, необходимо определить наибольшее удельное давление p1max, возникающее в поверхности сопряжения при наибольшем натяге выбранной стандартной посадки:
p1max = |
Nmax ст − 2K(RzD + Rzd) |
, |
(3.18) |
||||||
C |
D |
|
C |
d |
|
||||
|
|
|
|
||||||
|
|
|
+ |
|
|
|
|
||
|
|
|
|
|
|
|
|||
|
d |
ED |
|
|
|
|
|
||
|
|
|
Ed |
|
|
где K ― коэффициент величины смятия шероховатости при запрессовке (см. табл. П.3.4) [7, 9, 16]. Тогда наибольшие значения напряжений в поверхностях отверстия и вала после сборки дета-
лей определяются по формулам:
σ |
|
= p1 |
1 |
+ (d / d |
2 |
)2 |
, |
(3.19) |
||||
|
|
|
− (d / d |
|
|
)2 |
||||||
|
D |
max 1 |
2 |
|
|
|||||||
|
|
|
|
|
|
|
|
|
|
|
||
|
|
σd = |
|
2pmax |
|
|
. |
|
(3.20) |
|||
|
|
1− (d |
1 |
/ d)2 |
|
|||||||
|
|
|
|
|
|
|
|
|
|
|
|
При сборке детали не разрушатся, если соблюдаются условия:
σTD ≥ σD ; |
(3.21) |
σTd ≥ σd , |
(3.22) |
где σTD , σTd ― пределы текучести материалов втулки и вала, МПа (табл. П.3.3).
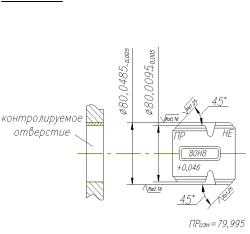
3.3. Расчет усилия запрессовки при сборке деталей
Определить усилие запрессовки Rп, Н, деталей по формуле
Rп = p1max πdlfп, |
(3.23) |
где p1max ― см. формулу (3.18); d, l ― размеры рассматриваемого соединения, м; fп ― коэффициент трения при повторной запрессовке,
fп = (1,15…1,20) f [9, с. 364],
где f ― коэффициент трения,
f = 0,08…0,14 [7; 9, табл. 1.104].
3.4. Выбор средств измерения
Выбор СИ подробно рассмотрен в задании 2, п. 2.5. Рассчитав метрологические характеристики СИ, составьте и заполните таблицу формы табл. П.2.3.
Задание 4. Расчет исполнительных размеров калибров для контроля гладких изделий
Гладкие предельные калибры ― бесшкальные средства измерений, которые применяются для контроля деталей в крупносерийном производстве. Перед выполнением задания рекомендуется изучить материалы темы № 14 [11].
Для контроля деталей, образующих посадку с зазором — в задании 2 (для четных вариантов) или неподвижную посадку — в задании 3 (для нечетных вариантов), назначить рабочие предельные калибры. В качестве исходных данных для расчета исполнительных размеров рабочих калибров для контродя деталей принять их размеры и точность изготовления в соответствии с выбранной посадкой.
Порядок выполнения задания
4.1.Установить наименования калибров, их назначение, конструкции и способы контроля [4, 5, 11, 14, 16].
4.2.По ГОСТ 14807–69 … ГОСТ 14827–69 выбрать конструкцию калибра-пробки.
4.3.Выбрать конструкцию калибра-скобы по ГОСТ 18355–73 … ГОСТ 18357–73, ГОСТ 18358–93
…ГОСТ 18367–93, ГОСТ 18369–73.
4.4.Эскизы выбранных калибров выполнить на листах формата А4. На рис. 4.1 и 4.2 в качестве примеров приведены эскизы калибров для контроля деталей, образующих посадку с натягом
H8(+0,046 )
80 u7(+00,132 ) . +0,102
Рис. 4.1. Двухсторонний предельный рабочий калибр-пробка 80H8( 0+0,046 )
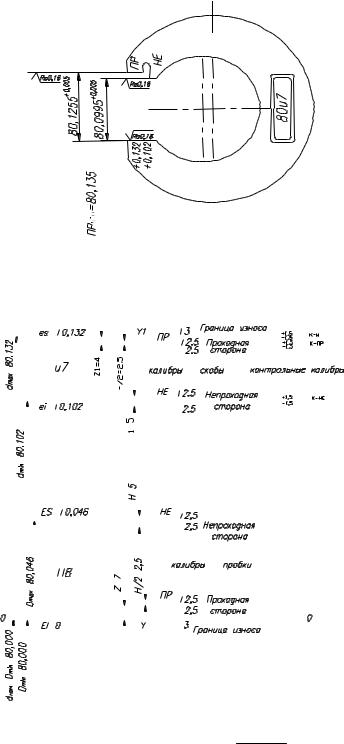
Рис. 4.2. Односторонний двухпредельный рабочий калибр-скоба 80u7( ++00,,132102 )
4.5. На листе формата А4 выполнить схемы полей допусков для контролируемых деталей и соответствующих им рабочих калибров (рис. 4.3).
а) |
|
|
|
|
|
|
|
б) |
|
|
|
|
|
|
|
|
|
в) |
|
|
|
|
|
|
|
|||||||||||||||||||||||||||||||
|
|
|
|
|
|
|
|
|
|
|
|
|
|
|
|
|
|
|
|
|
|
|
|
|
|
|
|
|
|
|
|
|
|
|
|
|
|
|
|
|
|
|
|
|
|
|
|
|
|
|
|
|
|
|
|
|
|
|
|
|
|
|
|
|
|
|
|
|
|
|
|
|
|
|
|
|
|
|
|
|
|
|
|
|
|
|
|
|
|
|
|
|
|
|
|
|
|
|
|
|
|
|
|
|
|
|
|
|
|
|
|
|
|
|
|
|
|
|
|
|
|
|
|
|
|
|
|
|
|
|
|
|
|
|
|
|
|
|
|
|
|
|
|
|
|
|
|
|
|
|
|
|
|
|
|
|
|
|
|
|
|
|
|
|
|
|
|
|
|
|
|
|
|
|
|
|
|
|
|
|
|
|
|
|
|
|
|
|
|
|
|
|
|
|
|
|
|
|
|
|
|
|
|
|
|
|
|
|
|
|
|
|
|
|
|
|
|
|
|
|
|
|
|
|
|
|
|
|
|
|
|
|
|
|
|
|
|
|
|
|
|
|
|
|
|
|
|
|
|
|
|
|
|
|
|
|
|
|
|
|
|
|
|
|
|
|
|
|
|
|
|
|
|
|
|
|
|
|
|
|
|
|
|
|
|
|
|
|
|
|
|
|
|
|
|
|
|
|
|
|
|
|
|
|
|
|
|
|
|
|
|
|
|
|
|
|
|
|
|
|
|
|
|
|
|
|
|
|
|
|
|
|
|
|
|
|
|
|
|
|
|
|
|
|
|
|
|
|
|
|
|
|
|
|
|
|
|
|
|
|
|
|
|
|
|
|
|
|
|
|
|
|
|
|
|
|
|
|
|
|
|
|
|
|
|
|
|
|
|
|
|
|
|
|
|
|
|
|
|
|
|
|
|
|
|
|
|
|
|
|
|
|
|
|
|
|
|
|
|
|
|
|
|
|
|
|
|
|
|
|
|
|
|
|
|
|
|
|
|
|
|
|
|
|
|
|
|
|
|
|
|
|
|
|
|
|
|
|
|
|
|
|
|
|
|
|
|
|
|
|
|
|
|
|
|
|
|
|
|
|
|
|
|
|
|
|
|
|
|
|
|
|
|
|
|
|
|
|
|
|
|
|
|
|
|
|
|
|
|
|
|
|
|
|
|
|
|
|
|
|
|
|
|
|
|
|
|
|
|
|
|
|
|
|
|
|
|
|
|
|
|
|
|
|
|
|
|
|
|
|
|
|
|
|
|
|
|
|
|
|
|
|
|
|
|
|
|
|
|
|
|
|
|
|
|
|
|
|
|
|
|
|
|
|
|
|
|
|
|
|
|
|
|
|
|
|
|
|
|
|
|
|
|
|
|
|
|
|
|
|
|
|
|
|
|
|
|
|
|
|
|
|
|
|
|
|
|
|
|
|
|
|
|
|
|
|
|
|
|
|
|
|
|
|
|
|
|
|
|
|
|
|
|
|
|
|
|
|
|
|
|
|
|
|
|
|
|
|
|
|
|
|
|
|
|
|
|
|
|
|
|
|
|
|
|
|
|
|
|
|
|
|
|
|
|
|
|
|
|
|
|
|
|
|
|
|
|
|
|
|
|
|
|
|
|
|
|
|
|
|
|
|
|
|
|
|
|
|
|
|
|
|
|
|
|
|
|
|
|
|
|
|
|
|
|
|
|
|
|
|
|
|
|
|
|
|
|
|
|
|
|
|
|
|
|
|
|
|
|
|
|
|
|
|
|
|
|
|
|
|
|
|
|
|
|
|
|
|
|
|
|
|
|
|
|
|
|
|
|
|
|
|
|
|
|
|
|
|
|
|
|
|
|
|
|
|
|
|
|
|
|
|
|
|
|
|
|
|
|
|
|
|
|
|
|
|
|
|
|
|
|
|
|
|
|
|
|
|
|
|
|
|
|
|
|
|
|
|
|
|
|
|
|
|
|
|
|
|
|
|
|
|
|
|
|
|
|
|
|
|
|
|
|
|
|
|
|
|
|
|
|
|
|
|
|
|
|
|
|
|
|
|
|
|
|
|
|
|
|
|
|
|
|
|
|
|
|
|
|
|
|
|
|
|
|
|
|
|
|
|
|
|
|
|
|
|
|
|
|
|
|
|
|
|
|
|
|
|
|
|
|
|
|
|
|
|
|
|
|
|
|
|
|
|
|
|
|
|
|
|
|
|
|
|
|
|
|
|
|
|
|
|
|
|
|
|
|
|
|
|
|
|
|
|
|
|
|
|
|
|
|
|
|
|
|
|
|
|
|
|
|
|
|
|
|
|
|
|
|
|
|
|
|
|
|
|
|
|
|
|
|
|
|
|
|
|
|
|
|
|
|
|
|
|
|
|
|
|
|
|
|
|
|
|
|
|
|
|
|
|
|
|
|
|
|
|
|
|
|
|
|
|
|
|
|
|
|
|
|
|
|
|
|
|
|
|
|
|
|
|
|
|
|
|
|
|
|
|
|
|
|
|
|
|
|
|
|
|
|
|
|
|
|
|
|
|
|
|
|
|
|
|
|
|
|
|
|
|
|
|
|
|
|
|
|
|
|
|
|
|
|
|
|
|
|
|
|
|
|
|
|
|
|
|
|
|
|
|
|
|
|
|
|
|
|
|
|
|
|
|
|
|
|
|
|
|
|
|
|
|
|
|
|
|
|
|
|
|
|
|
|
|
|
|
|
|
|
|
|
|
|
|
|
|
|
|
|
|
|
|
|
|
|
|
|
|
|
|
|
|
|
|
|
|
|
|
|
|
|
|
|
|
|
|
|
|
|
|
|
|
|
|
|
|
|
|
|
|
|
|
|
|
|
|
|
|
|
|
|
|
|
|
|
|
|
|
|
|
|
|
|
|
|
|
|
|
|
|
|
|
|
|
|
|
|
|
|
|
|
|
|
|
|
|
|
|
|
|
|
|
|
|
|
|
|
|
|
|
|
|
|
|
|
|
|
|
|
|
|
|
|
|
|
|
|
|
|
|
|
|
|
|
|
|
|
|
|
|
|
|
|
|
|
|
|
|
|
|
|
|
|
|
|
|
|
|
|
|
|
|
|
|
|
|
|
|
|
|
|
|
|
|
|
|
|
|
|
|
|
|
|
|
|
|
|
|
|
|
|
|
|
|
|
|
|
|
|
|
|
|
|
|
|
|
|
|
|
|
|
|
|
|
|
|
|
|
|
|
|
|
|
|
|
|
|
|
|
|
|
|
|
|
|
|
|
|
|
|
|
|
|
|
|
|
|
|
|
|
|
|
|
|
|
|
|
|
|
|
|
|
|
|
|
|
|
|
|
|
|
|
|
|
|
|
|
|
|
|
|
|
|
|
|
|
|
|
|
|
|
|
|
|
|
|
|
|
|
|
|
|
|
|
|
|
|
|
|
|
|
|
|
|
|
|
|
|
|
|
|
|
|
|
|
|
|
|
|
|
|
|
|
|
|
|
|
|
|
|
|
|
|
|
|
|
|
|
|
|
|
|
|
|
|
|
|
|
|
|
|
|
|
|
|
|
|
|
|
|
|
|
|
|
|
|
|
|
|
|
|
|
|
|
|
|
|
|
|
|
|
|
|
|
|
|
|
|
|
|
|
|
|
|
|
|
|
|
|
|
|
|
|
|
|
|
|
|
|
|
|
|
|
|
|
|
|
|
|
|
|
|
|
|
|
|
|
|
|
|
|
|
|
|
|
|
|
|
|
|
|
|
|
|
|
|
|
|
|
|
|
|
|
|
|
|
|
|
|
|
|
|
|
|
|
|
|
|
|
|
|
|
|
|
|
|
|
|
|
|
|
|
|
|
|
|
|
|
|
|
|
|
|
|
|
|
|
|
|
|
|
|
|
|
|
|
|
|
|
|
|
|
|
|
|
|
|
|
|
|
|
|
|
|
|
|
|
|
|
|
|
|
|
|
|
|
|
|
|
|
|
|
|
|
|
|
|
|
|
|
|
|
|
|
|
|
|
|
|
|
|
|
|
|
|
|
|
|
|
|
|
|
|
|
|
|
|
|
|
|
|
|
|
|
|
|
|
|
|
|
|
|
|
|
|
|
|
|
|
|
|
|
|
|
|
|
|
|
|
|
|
|
|
|
|
|
|
|
|
|
|
|
|
|
|
|
|
|
|
|
|
|
|
|
|
|
|
|
|
|
|
|
|
|
|
|
|
|
|
|
|
|
|
|
|
|
|
|
|
|
|
|
|
|
|
|
|
|
|
|
|
|
|
|
|
|
|
|
|
|
|
|
|
|
|
|
|
|
|
|
|
|
|
|
|
|
|
|
|
|
|
|
|
|
|
|
|
|
|
|
|
|
|
|
|
|
|
|
|
|
|
|
|
|
|
|
|
|
|
|
|
|
|
|
|
|
|
|
|
|
|
|
|
|
|
|
|
|
|
|
|
|
|
|
|
|
|
|
|
|
|
|
|
|
|
|
|
|
|
|
|
|
|
|
|
|
|
|
|
|
|
|
|
|
|
|
|
|
|
|
|
|
|
|
|
|
|
|
|
|
|
|
|
|
|
|
|
|
|
|
|
|
|
|
|
|
|
|
|
|
|
|
|
|
|
|
|
|
|
|
|
|
|
|
|
|
|
|
|
|
|
|
|
Рис. 4.3. Схема полей допусков калибров для деталей, образующих посадку с натягом 80 H8(0+0,046 ) :
u7(++00,,132102 )
а — допуски для деталей, отклонения в мм; б — допуски для калибров, отклонения в мкм; в — допуски для контрольных калибров, отклонения в мкм
4.5.1.По ГОСТ 25347–82 вычертить схему расположения полей допусков отверстия и вала с указанием условных обозначений, предельных отклонений и предельных размеров (см. рис. 4.3, а).
4.5.2.На схеме полей допусков деталей вычертить схему полей допусков рабочих калибров (см. рис. 4.3, б) с указанием условных обозначений и предельных отклонений (табл. П.4.1).
На рис. 4.3, в указаны отклонения контркалибров для калибров-скоб.
Для рабочих калибров-пробок отклонения непроходной (НЕ) стороны калибра отсчитываются
от наибольшего предельного размера отверстия Dmax, а проходной (ПР) стороны ― от наименьшего размера отверстия Dmin (с учетом величины смещения Z). Предельный размер износа проходного калибра-пробки устанавливается величиной У (см. табл. П.4.1).
Для рабочих калибров-скоб отклонения непроходного (НЕ) калибра устанавливаются относительно наименьшего предельного размера вала dmin, а проходной (ПР) стороны ―относительно
наибольшего размера вала dmax (с учетом смещения Z1). Граница износа проходного калибраскобы указывается величиной У1.
4.6. Рассчитать исполнительные размеры ― размеры на изготовление рабочих калибров (ГОСТ 24853–81) [4, 5, 14, 16]. Расчет исполнительных размеров непроходной (НЕ) и проходной (ПР) сторон калибра-пробки выполняется по формулам:
НЕ = (Dmax + H/2)-H, |
(4.1) |
ПР = (Dmin + Z + H/2)-H. |
(4.2) |
НЕ = (35,025 + 0,002)-0,004 = 35,027-0,004, ПР = (35,000 + 0,0035 + 0,002)-0,004 = 35,0055-0,004.
Для калибра 35Н7 числовые значения составляют (см. табл. П.4.1): предельный размер изношенной проходной стороны калибра-пробки
ПРизн = Dmin – У |
(4.3) |
или |
|
ПРизн = 35,000 – 0,003 = 34,997; |
|
исполнительные размеры калибра-скобы |
|
НЕ = (dmin – H1/2) + H1, |
(4.4) |
ПР = (dmax – Z1 – H1/2) + H1, |
(4.5) |
ПРизн = dmax + У1 |
(4.6) |
и для калибра 35f7 |
|
НЕ = (34,950 – 0,002) +0.004 = 34,948 +0.004, |
|
ПР = (34,975 – 0,0033 -0,002) +0.004 = 34,9695 +0.004, ПРизн = 34,975 + 0,003 = 34,978.
Точность изготовления калибров, в отличие от гладких деталей, указывается не двумя, а одним отклонением, равным величине допуска. При этом отклонение проставляется в одну сторону (в тело): для пробок ― в сторону уменьшения размера (в минус), а для калибров-скоб ― в сторону увеличения (в плюс) (см. рис. 4.1, 4.2). Проверку правильности расчета исполнительных размеров калибров можно сделать по ГОСТ 21401–75.
4.7. На эскизах калибров нанести маркировку, указать исполнительные размеры и размеры предельно изношенных проходных калибров.
Задание 5. Определение допусков и предельных размеров для шпоночных соединений
Определить допуски и предельные размеры шпоночных соединений.
Назначить соединение с призматической шпонкой для сопряжения вал–втулка (вместо посадки с зазором), рассмотренного в задании 2. Размеры сохраняются. Тип шпоночного сопряжения и форму исполнения шпонки выбрать в соответствии с номером варианта:
–для вариантов заданий, кратных трем, назначить свободное сопряжение и первое исполнение формы шпонки;
–для четных оставшихся вариантов ― нормальное сопряжение и второе исполнение;
–для оставшихся нечетных вариантов ― плотное сопряжение и третье исполнение формы шпонки [9, табл. 4.64].
Порядок выполнения задания
Перед выполнением задания изучить тему №8 «Взаимозаменяемость шпоночных соединений» [11].
5.1.В зависимости от диаметра вала по ГОСТ 23360–78 установить номинальные размеры элементов деталей шпоночного соединения (табл. П.5.1) [4, с. 303; 9, табл. 4.64]. Результаты выбора номинальных размеров при диаметре вала 500 мм приведены в табл. 5.1. Основными (посадочными) размерами сопряжения являются: ширина шпонки, ширина паза вала и втулки. Данные размеры требуют относительно высокой точности изготовления (см. рис. 5.1).
5.2.Длину шпонки назначить стандартной из ряда предпочтительных чисел, исходя из ширины втулки [4, с. 303; 9, табл. 4.64 (см. примечания)]. Посадка шпонки по длине указана на рис. П.5.1.