
748
.pdf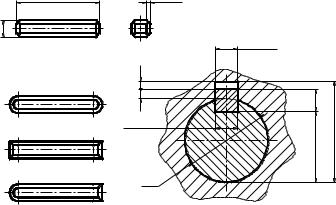
l |
|
f x45° |
|
h |
|
|
|
|
|
b P9/ h9 |
|
Виды исполнения шпонок |
t 2 |
|
|
1. |
|
h |
|
|
1 |
|
|
|
t |
|
|
|
b P9/ h9 |
|
2 |
2. |
|
t 1 |
d+t |
|
|
d- |
|
3. |
d |
|
|
|
|
|
Рис. 5.1. Шпоночное соединение. Сечения. Шпонка призматическая
5.3. Указать размеры выбранной шпонки. Например, описание стандартной шпонки второго исполнения нормального сопряжения при диаметре вала 500 мм (табл. П.5.1) будет иметь вид:
Шпонка 2 — 100 × 50 × 320 ГОСТ 23360–78 (Шпонка 2 — b × h × l ГОСТ 23360–78).
5.4.Установить допуски на посадочные размеры по ГОСТ 23360–78 с учетом заданного типа сопряжения. Посадки шпонок шириной свыше 6 мм для всех типов соединений представлены на рис. 5.2 [4; 7; 9, табл. 4.65], остальные размеры элементов имеют большие допуски [4; 7; 9, табл. 4.66.1], обеспечивающие большие зазоры в сопряжении.
5.5.По ГОСТ 25347–82 установить числовые значения предельных отклонений для размеров всех элементов шпонки и занести в таблицу формы табл. 5.1.
|
|
|
|
|
|
Таблица 5.1 |
|
Размеры и допуски элементов шпоночного соединения |
|
||||
|
|
(пример для вала диаметром 500 мм) |
|
|
||
|
|
|
|
|
|
|
Деталь |
Элемент |
Усл. |
Номинальный размер, |
Допуск |
Отклонение, |
Примечания |
|
|
об. |
м |
|
мм |
|
|
Ширина |
b |
100 |
100h9 |
0 |
Основной вал |
|
–0,087 |
|||||
|
|
|
|
|
|
|
Шпонка призматиче- |
Высота |
h |
50 |
50h11 |
0 |
|
ская |
–0,160 |
|
||||
|
|
|
|
|
||
|
Длина |
l |
320 |
320h14 |
0 |
|
|
–1,400 |
|
||||
|
|
|
|
|
|
|
|
Ширина |
b |
100 |
100N 9 |
0 |
Посадочный раз- |
|
паза |
–0,087 |
мер |
|||
|
|
|
|
|||
Вал |
Глубина |
t1 |
31 |
31+ 0,3 |
+ 0,300 |
|
|
паза |
|
|
|
0 |
|
|
Длина паза |
L |
320 |
320H1 |
+ 2,300 |
|
|
5 |
0 |
|
|||
|
|
|
|
|
||
|
Ширина |
b |
100 |
100JS9 |
+ 0,043 |
Посадочный раз- |
|
паза |
–0,043 |
мер |
|||
Втулка |
|
|
|
|||
Глубина |
t2 |
19,5 |
19,5+ 0,3 |
+ 0,300 |
|
|
|
|
|||||
|
паза |
|
|
|
0 |
|
5.6.Выполнить сборочный чертеж шпоночного соединения в двух проекциях и указать все посадки, в том числе и посадку вала во втулку (см. рис. П.5.1).
5.7.Сделать рабочие чертежи вала и втулки и нанести размеры и предельные отклонения по ГОСТ 2.307–68, шероховатость поверхностей по ГОСТ 2.309–73 и отклонения формы и располо-
жения поверхностей по ГОСТ 2.308–79 (примеры см. прил. 5, рис. П.5.2, П.5.3) [9, с. 271].
Рекомендуется: шероховатость боковых поверхностей шпонки и пазов назначить Rz = 20·10-6 м, остальных ― Rz = 40·10-6 м, допуск параллельности плоскости симметрии паза относительно оси принять равным половине допуска на размер ширины паза; допуск симметричности назначить равным двум допускам на размер ширины данного паза [9, рис. 4.21].
5.8.Начертить схему полей допусков посадок шпонки в пазы вала и втулки. Стандартные шпоноч-
ные посадки назначаются в системе вала, так как шпонка всегда принимается за основной вал (см. рис. 5.2).
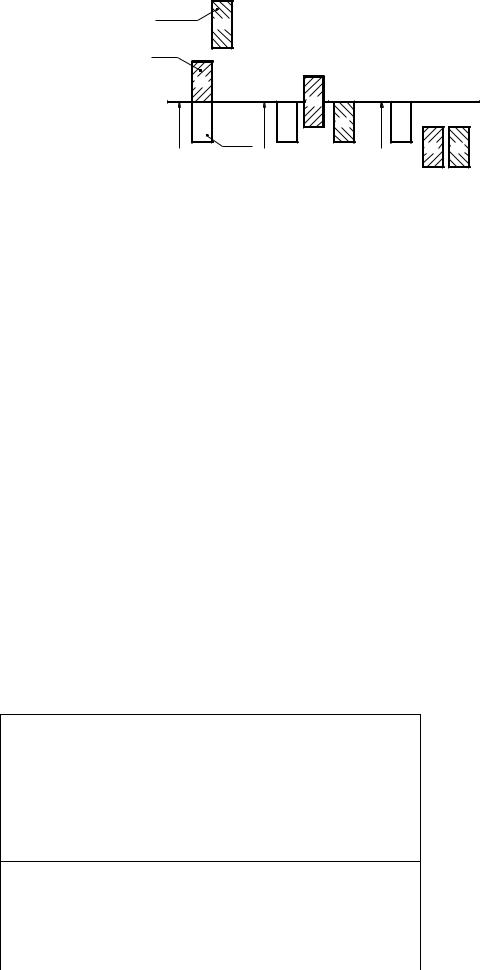
Свободный |
Нормальный |
Плотный |
поле паза |
|
|
|
|
втулки |
D10 |
|
|
|
|
|
|
|
|
поле |
|
|
|
|
вала |
|
|
|
|
H9 |
|
|
|
|
0 |
|
Js9 |
|
0 |
|
|
|
|
|
h9 |
h9 |
N9 |
h9 |
|
b |
b |
|
b |
|
|
поле |
|
P9 |
P9 |
|
шпонки |
|
||
|
|
|
|
Рис. 5.2. Посадки шпонок для разных типов соединения
5.9. Выбрать и занести в таблицу (типа табл. П.2.3) средства измерений для контроля деталей шпоночного соединения [4, с. 315; 9, с. 288; 13, с. 38; 14; 16].
Задание 6. Допуски и посадки шлицевых соединений с прямобочным профилем
Шлицевые соединения имеют более высокую соосность и нагруженность соединяемых деталей по сравнению со шпоночными. Они применяются как для относительно подвижных, так и для неподвижных соединений.
Требуется выбрать посадки сопрягаемых поверхностей подвижного прямобочного шлицевого соединения и рассчитать предельные размеры шлицевых вала и втулки.
Порядок выполнения задания
6.1.Изучить материалы по теме № 10 «Взаимозаменяемость шлицевых соединений» [11].
6.2.Для выполнения задания необходимо из табл П.1.2 (задание № 6) установить исходные данные по варианту, где указаны параметр центрирования и геометрические размеры шлицевого соединения с прямобочным профилем.
6.3.В соответствии с заданием записать полное обозначение шлицевого соединения с прямобочным профилем, где указать центрирующий размер (D, или d, или b), затем число зубьев z (всегда четное число), далее номинальные размеры ― z × d × D × b. Например: d — 8 × 36 × 42 × 7, где d
—центрирующий размер (внутренний диаметр), d = 36 мм; z — число зубьев; D — наружний диаметр, D = 42 мм; b — толщина зуба вала (ширина паза шлицевой втулки), b = 7 мм.
6.4.В зависимости от центрирования (рис. 6.1–6.3) по табл. 6.1 выбрать посадки с зазором (для трех размеров) для заданного шлицевого соединения [9]. В табл. 6.1 приведены допуски и посадки прямобочных шлицевых соединений предпочтительного применения из ГОСТ 1139–80. Более подробная информация содержится в табл. 4.72–4.75 [9].
Таблица 6.1
Соединения шлицевые прямобочные.
Рекомендуемые посадки предпочтительного применения (ГОСТ 1139-80)
Центрирование по наружному диаметру D
Посадки центрирующего диаметра |
Посадки по ширине b |
||||||||||||||||||
|
H7 |
; |
|
H7 |
|
|
|
F8 |
; |
|
F8 |
; |
|
F8 |
|
|
|||
|
f 7 |
|
js6 |
|
|
f 7 |
f 8 |
|
js7 |
||||||||||
|
|
|
|
|
|
|
|
|
|
|
|||||||||
|
|
|
|
|
|
|
|
|
|
|
|
|
|
|
|||||
|
Центрирование по внутреннему диаметру d |
|
|
|
|
|
|
||||||||||||
Посадки центрирующего диаметра |
Посадки по ширине |
||||||||||||||||||
|
H7 |
|
; |
H7 |
|
|
|
D9 |
; |
D9 |
|
; |
F10 |
|
|||||
|
f 7 |
|
|
|
g6 |
|
|
h9 |
|
|
js7 |
|
|
|
js7 |
||||
|
|
|
|
|
|
|
|
|
|
|
|
|
|
|
|
|
|
|
|
Центрирование по боковым сторонам зубьев b
|
|
F8 ; D9 |
D9 |
F10 |
|
||||||
|
|
|
|
|
; |
|
; |
|
|
|
|
|
|
|
|
e8 |
d9 |
|
|||||
|
|
js7 |
|
f 8 |
|
||||||
|
|
|
|
|
|||||||
|
Поля допусков нецентрирующих размеров |
|
|||||||||
Нецентри- |
Поверхность, по кото- |
|
Поля допусков |
|
|||||||
|
рой |
|
|
|
|
|
В |
||||
рующий |
|
|
|
|
|
|
|||||
производят центриро- |
|
Вал |
|
т |
|||||||
диаметр |
|
|
|||||||||
|
вание |
|
|
|
|
|
у |
||||
|
|
|
|
|
|
|
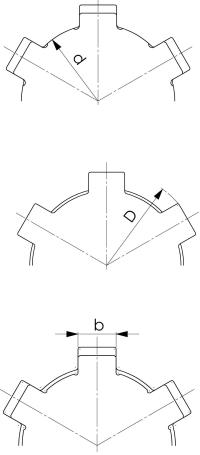
|
|
|
л |
|
|
|
к |
|
|
|
а |
|
|
Не менее d1 |
H |
D |
D или b |
(см. табл. |
1 |
|
|
П.6.1) |
1 |
|
|
|
H |
D |
d или b |
а11 |
1 |
|
|
|
2 |
Рис. 6.1. Шлицевое соединение с прямобочным профилем с центрированием по внутреннему диаметру
Рис. 6.2. Шлицевое соединение с прямобочным профилем с центрированием по наружному диаметру
Рис. 6.3. Шлицевое соединение с прямобочным профилем с центрированием по боковым сторонам зубьев
Известно, что посадка по центрирующему размеру всегда точнее, чем по нецентрирующему. Кроме того, в обозначении шлицевого соединения указывается посадка для размера b (толщина зуба — ширина паза). Поля допусков нецентрирующих диаметров можно не указывать.
6.5. Рассмотрим примеры обозначения вышеуказанного шлицевого соединения, размеры которого 8 × 36 × 42 × 7, с разными видами центрирования.
6.5.1. Для вышеуказанного прямобочного шлицевого соединения при центрировании по внутреннему диаметру d (см. рис. 6.1) [9, 11]: посадка по центрирующему размеру d ― H7/f7; по наружному диаметру D ― H12/a11 и по поверхностям зубьев и впадин (размер b) ― F10/js7.
Тогда соединение запишется в виде:
d – 8 × 36 |
H7 |
× 42 |
H12 |
× 7 |
F10 |
; |
|
f 7 |
a11 |
js7 |
|||||
|
|
|
|
точность изготовления шлицевой втулки —
d – 8 × 36H7 × 42H12 × 7F10;
точность изготовления шлицевого вала —
d– 8 × 36f7 × 42a11 × 7js7.
6.5.2.При центрировании по наружному диаметру D (см. рис. 6.2) [9, 11]: посадки по D – H7/f7, по боковым поверхностям b – F8/f7.
Тогда соединение запишется, как
D – 8 × 36 |
H11 |
|
× 42 |
H7 |
× 7 |
F8 |
. |
a11 |
f 7 |
|
|||||
|
|
|
f 7 |
6.5.3. При центрировании по боковым сторонам зубьев (см. рис. 6.3) [9, 11]: с посадкой по центрирующему размеру b – F8/js7.
В этом случае соединение запишется, как
b – 8 × 36 × 42 |
H12 |
× 7 |
F8 |
. |
a11 |
|
|||
|
|
js7 |
Следует обратить внимание, что при изменении параметра центрирования рекомендуемые предпочтительные посадки соединений изменяются.
6.6. Для выбранных посадок установить числовые значения предельных отклонений (ГОСТ 25347–82) для всех размеров элементов шлицевого прямобочного соединения. Например:
|
H7(+0,025) |
H12(+0,250 ) |
F10(++00,,013071) |
||
d – 8 × 36 |
|
× 42 |
|
× 7 |
|
f 7(−−00,,050025) |
a11(−−00,,320480 ) |
js7(+−00,,007007 ) |
6.7.Выполнить сборочный чертеж в двух проекциях для рассмотренного шлицевого соединения (рис. П.6.1) [9] и указать посадки.
6.8.Выполнить рабочий чертеж шлицевого вала с обозначением точности изготовления всех размеров, с указанием допусков формы и расположения поверхностей. При этом указать на чертеже шероховатость, материал детали, вид термической обработки и т.д. [9]. Пример рабочего чертежа вала приведен в прил. 6 (рис. П.6.2).
6.9.Выполнить рабочий чертеж шлицевой втулки. При выполнении данного чертежа требования аналогичны (п. 6.8) (рис. П.6.3).
6.10.Выбрать СИ для контроля и измерения шлицевых вала и втулки [9, 11, 13]. Метрологические характеристики СИ занести в таблицу типа табл. П.2.3 (см. прил. 2).
Задание 7. Выбор и расчет характеристик посадок подшипников качения
Подшипник качения (ПК) ― широко распространенный узел, изготавливаемый с высокой точностью на специализированных заводах. Теоретический материал по взаимозаменяемости подшипников качения рассмотрен в теме № 13 [11]. Размеры ПК устанавливаются по его основному условному обозначению ― номеру [3, 4, 9, 14]. Согласно ГОСТ 520–2002 точность изготовления ПК регламентируется классом, который записывается через тире перед условным обозначением. Класс точности ПК (по возрастанию точности) ― 8, 7, 0, 6, 6Х, 5, 4, 2, Т. ПК классов 0 и 6 (нормальной точности) наиболее распространены в машиностроении. Класс 0 на чертеже не указывается. Класс точности ПК определяет не только точность изготовления самого ПК, но и точность изготовления сопрягаемых деталей (посадочный размер вала и размер отверстия корпуса).
Посадки ПК на вал и в отверстие корпуса рассчитываются для каждого кольца отдельно в зависимости от вида нагружения, величины радиальной нагрузки (удельной нагруженности) и режима работы по ГОСТ 3325–85 [9, табл. 4.88…4.90.1].
Рассчитать и назначить посадки для однорядного радиального шарикоподшипника, номер, радиальная нагрузка, вид нагружения и режим работы которого заданы. Внутреннее кольцо подшипника качения устанавливается на вал с натягом и вращается вместе с валом, а наружное кольцо имеет следующий вид нагружения:
–для вариантов заданий, кратных трем, ― колебательное нагружение с нормальным режимом работы;
–для оставшихся четных вариантов заданий ― циркуляционное с перегрузкой до 150 % (нормальный режим работы);
–для остальных нечетных вариантов ― тяжелый режим работы с сильной вибрацией и местным нагружением с перегрузкой до 300 %.
7.1.Расчет основных характеристик посадок ПК
7.1.1.По варианту задания (табл. П.1.2, зад. № 7) установить ПК, класс точности изготовления ПК и нагрузку. По номеру подшипника определить его основные геометрические размеры: наружный D, внутренний d диаметры, ширину B и радиус закругления r или фаски колец, а также установочные размеры сопрягаемых с ПК деталей ― диаметры заплечика вала d2min, заплечика
корпуса D2max и ширину проточки b1 (табл. П.7.1, П.7.2) [1, с. 144, 145; 3, табл. 1, с. 424–431; 10, с. 121–123].
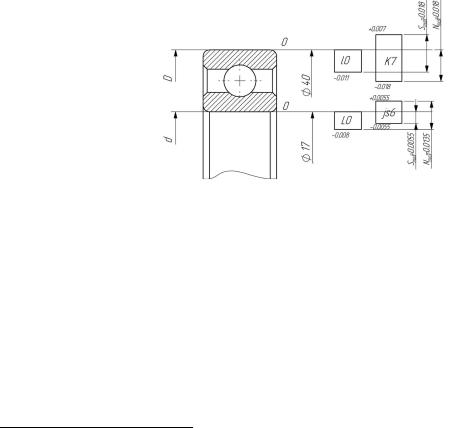
7.1.2. Определить интенсивность радиальной нагрузки р, кН/м, на посадочной поверхности циркуляционно нагруженного (вращающегося) кольца [3…5, 9, 10, 14, 16]:
p = |
F |
k1 k2 k3, |
(7.1) |
|
|||
|
b |
|
где F ― заданная радиальная нагрузка на опору, кН; b ― рабочая ширина посадочного места ПК, м; b = B – 2r, r ― радиус закругления м; B — ширина ПК, м; или b = B – r – b′, где b′ ― ширина проточки (табл. 7.3); k1 ― динамический коэффициент посадки, определяемый характером нагрузки:
–при нормальном режиме работы (перегрузки до 150 %, умеренные вибрации и толчки) k1 = 1;
–при тяжелом режиме (перегрузки до 300 %, сильные удары и вибрация) k1 = 1,8; k2 ― коэффициент, учитывающий ослабление посадочного натяга за счет тонкостенной втулки или полого вала (табл.
П.7.3) [9, табл. 4.90.28 или 16, табл. 9.5]; k2 = 1 при сплошном вале и толстостенном корпусе; k3 ― коэффициент неравномерности распределения радиальной нагрузки между рядами тел катания (для двух
иболее рядов) [9, табл. 4.90.2; 16, с. 239]; k3 = 1 для однорядного радиального ПК.
7.1.3.По величине p из формулы (7.1) с учетом класса точности ПК и вида нагружения определить поле допуска вала (табл. П.7.4) [9, табл. 4.90.1; 16, табл. 9.3].
7.1.4.Определить поле допуска отверстия корпуса с учетом режима работы, вида нагружения и класса точности ПК:
– при циркуляционном нагружении — по табл. П.7.4, П.7.5, [9, табл. 4.90.1; 16, табл. 9.4];
– при местном нагружении ― по табл. П.7.6 [9, табл. 4.89.2; 16, табл. 9.6];
– при колебательном нагружении ― [9, табл. 4.89.1].
7.1.5.По прил. 7 (табл. П.7.4; П.7.5; П.7.6) или [9, табл. 4.87, 4.88, 4.89.1, 4.91; 16, с. 233] уточнить выбранные посадки ПК на вал (в системе отверстия) и в корпус (в системе вала). Записать посадки ПК на вал и в корпус символами и в скобках указать числовые значения отклонений, для чего по ГОСТ
520–2002 [9, табл. 4.82] установить допускаемые отклонения на среднее значение внутреннего dпр и наружного Dпр диаметров ПК [3, 10], а также отклонения на размеры вала и отверстия корпуса по ГОСТ 25347–82 согласно выбранным полям допусков (см. пп. 7.1.3 и 7.1.4).
7.1.6.Вычертить схемы полей допусков для посадки ПК на вал (в системе отверстия) и для посадки ПК в отверстие корпуса (в системе вала) по вышеустановленным отклонениям (рис. 7.1). Определить основные характеристики каждой посадки (см. задание 1). Полученные натяги и зазоры можно проверить по приложению к ГОСТ 3325–85 или [9, табл. 4.92].
Рис. 7.1. Схема полей допусков посадок ПК класса 0 на вал (в системе отверстия) и в корпус (в системе вала)
при колебательном нагружении
7.1.7. Установить предельные значения радиального (исходного) зазора ПК* основного ряда (табл. 7.1) по ГОСТ 24810–81 [3, табл. 1, с. 161]. Определить среднее значение исходного зазора ― зазора между телами катания и дорожками колец ПК до его установки в подшипниковом узле:
S0 = Scp = |
Smax + Smin |
. |
(7.2) |
|
2 |
||||
|
|
|
7.1.8. После установки ПК на вал и в корпус из-за возможных натягов произойдет деформация беговой дорожки циркуляционно-нагруженного кольца (или обоих колец), что приведет к уменьшению исходного зазора и образованию нового ― посадочного зазора S1.
Величина диаметральной деформации беговой дорожки определяется:
* S0 — зазор между телами катания и дорожками колец ПК после изготовления; S1 — зазор после установки ПК в узле (установочный); S2 — рабочий зазор — зазор в рабочем режиме ПК.
– при посадке с натягом внутреннего кольца ПК
|
|
|
dmax = Nэф |
d |
; |
|
|
|
(7.3) |
|||
|
|
|
d0 |
|
|
|
||||||
|
|
|
|
|
|
|
|
|
|
|
|
|
|
|
|
|
|
|
|
|
|
|
|
|
Таблица 7.1 |
|
|
|
Исходные радиальные зазоры в радиальных |
|||||||||
|
|
|
|
однорядных шарикоподшипниках [3, 10] |
||||||||
|
|
|
|
|
|
|
|
|
|
|
||
Диаметр отверстия |
|
Радиальный зазор для рядов, 10-6 м |
|
|
||||||||
|
|
|
|
|
Дополнительных |
|
|
|||||
подшипника качения, мм |
Основного |
|
|
|
|
|
||||||
|
|
6-го |
7-го |
8-го |
|
|||||||
|
|
|
|
|
|
|
||||||
Свыше |
До |
min |
max |
|
min |
max |
min |
max |
min |
max |
|
|
— |
2,5 |
|
|
|
|
|
|
|
|
|
|
|
2,5 |
10 |
5 |
16 |
|
3 |
10 |
11 |
25 |
— |
— |
|
|
10 |
18 |
8 |
22 |
|
|
|
14 |
16 |
30 |
23 |
38 |
|
18 |
24 |
|
|
|
|
|
15 |
|
|
25 |
41 |
|
24 |
30 |
10 |
24 |
|
5 |
|
18 |
33 |
28 |
46 |
|
|
30 |
40 |
|
26 |
|
|
|
16 |
21 |
39 |
33 |
51 |
|
40 |
50 |
12 |
29 |
|
|
|
|
24 |
42 |
35 |
56 |
|
50 |
65 |
13 |
33 |
|
|
|
|
28 |
48 |
43 |
66 |
|
65 |
80 |
14 |
34 |
|
|
|
20 |
29 |
55 |
51 |
76 |
|
80 |
100 |
16 |
40 |
|
|
|
23 |
34 |
62 |
58 |
89 |
|
100 |
120 |
20 |
46 |
|
|
|
25 |
41 |
71 |
66 |
102 |
|
120 |
140 |
|
53 |
|
|
|
|
46 |
86 |
76 |
119 |
|
140 |
160 |
23 |
58 |
|
8 |
28 |
51 |
96 |
86 |
135 |
|
|
160 |
180 |
24 |
65 |
|
|
|
30 |
57 |
106 |
96 |
152 |
|
180 |
200 |
29 |
75 |
|
|
|
|
67 |
121 |
112 |
168 |
|
200 |
225 |
33 |
83 |
|
|
|
35 |
75 |
130 |
120 |
180 |
|
225 |
250 |
35 |
90 |
|
|
|
|
85 |
145 |
135 |
200 |
|
250 |
280 |
40 |
100 |
|
|
|
40 |
95 |
160 |
150 |
220 |
|
280 |
315 |
45 |
105 |
|
|
|
45 |
100 |
165 |
160 |
230 |
|
315 |
355 |
50 |
115 |
|
10 |
50 |
105 |
175 |
170 |
245 |
|
|
355 |
400 |
55 |
125 |
|
|
|
55 |
110 |
185 |
180 |
260 |
|
– при посадке с натягом наружного кольца
Dmax = Nэф1 |
D0 |
, |
(7.4) |
|
|||
|
D |
|
где dmax, Dmax ― наибольшая величина диаметральной деформации беговой дорожки внутреннего и наружного колец; Nэф, N1эф ― эффективные натяги (два разных) внутреннего и наружного колец ПК,
Nэф = 0,85 Nmax, |
(7.5) |
где Nmax ― наибольший натяг выбранной стандартной посадки соответствующего кольца (см. пп. 7.1.2–7.1.6); d, D ― внутренний и наружный диаметры ПК, м; d0, D0 ― приведенные средние диаметры внутреннего и наружного колец, рассчитываются по формулам:
– внутреннего кольца
d0 = d + |
D − d |
; |
(7.6) |
||
4 |
|||||
|
|
|
|
||
– наружного кольца |
|
|
|
|
|
D0 = D – |
D − d |
|
. |
(7.7) |
|
|
|
||||
4 |
|
7.1.9. Определить посадочный зазор S1 ПК после его установки по одной из формул (7.8) – (7.10):
– при посадке с натягом на вал
S1 = S0 – |
dmax, |
(7.8) |
где S0 ― исходный зазор, определяется по формуле (7.2); |
|
|
– при посадке ПК с натягом в корпус |
|
|
S1 = S0 – |
Dmax; |
(7.9) |
– при посадке ПК с натягом на вал и в корпус |
|
|
S1 = S0 – ( dmax + Dmax). |
(7.10) |
При выполнении курсового проекта принять равенство посадочного и рабочего зазоров, т. е. S2 = S1, где S2 ― рабочий зазор ПК при t = 50 °C.
Проверка правильности расчета и выбора посадок
Посадки ПК выбраны верно, если соблюдается условие:
0 < S2 ≤ 50 ·10-6. |
(7.11) |
При S2 < 0 между кольцами ПК и телами катания образуется натяг, что приводит к заклиниванию и разрушению деталей. Поэтому при образовании натяга необходимо выбрать ПК с увеличенным исходным зазором S0 (см. табл. 7.1, дополнительный 7-й или 8-й ряды) и вновь рассчитать S2. При рабочем зазоре S2 более 50 мкм (для ПК классов 0 и 6) появится радиальное биение, поэтому необходимо назначить ПК из 6-го дополнительного ряда с уменьшенным исходным зазором (см. табл. 7.1). Рабочий зазор, по величине близкий к нулю, считается оптимальным.
7.2. Графическая часть задания
Взаимозаменяемость деталей подшипникового узла обеспечивается точностью изготовления размеров (допусками на размеры), а также качеством присоединительных поверхностей, т.е. допусками на форму, расположение и шероховатость [11, приложения]. В прил. 7 (табл. П.7.1–П.7.6) приведены материалы для выполнения задания. На рабочих чертежах указываются допуски на размеры. На посадочный размер крышки назначить допуск d10. Указать шероховатость (табл. 7.2), отклонения формы и расположения поверхностей всех элементов деталей [4, табл. 11, с. 296; 9, табл. 4.93…4.95, с. 378; 11].
Таблица 7.2
|
Шероховатость посадочных поверхностей деталей, |
|||
|
сопрягаемых с подшипником качения |
|||
|
|
|
|
|
|
|
Номинальный диаметр, мм |
|
|
Посадочная |
Класс точности |
до 80 |
св. 80 до 500 |
|
поверхность |
подшипника качения |
Шероховатость по |
|
|
|
|
ГОСТ 2789–73 Ra, мкм |
|
|
|
0 |
1,25 |
2,50 |
|
Вал |
6, 5 |
0,63 |
1,25 |
|
|
4 |
0,32 |
0,63 |
|
Отверстие |
0 |
1,25 |
2,50 |
|
корпуса |
6, 5, 4 |
0,63 |
1,25 |
|
Торцы заплечика |
0 |
2,50 |
2,50 |
|
вала и корпуса |
6, 5, 4 |
1,25 |
2,50 |
|
7.2.1.Начертить сборочный чертеж подшипникового узла, указать все посадки символами и числовыми значениями. В прил. 7 на рис. П.7.1 приведен в качестве примера сборочный чертеж редуктора.
7.2.2.Начертить рабочие чертежи вала, корпуса и крышки. При наличии на валу и в корпусе канавок-проточек указать их размеры в соответствии с табл. 7.3. Примеры оформления графической части задания приведены в прил. 7 (рис. П.7.2– П.7.4.) [1; 3; 4, с. 299; 9, с. 380; 16, с. 235].

Таблица 7.3
Размеры канавок в отверстии корпуса и на валу по ГОСТ 8820–69
Номинальные диаметры |
|
Размеры канавок, мм |
|
||
D, d, мм |
D1 |
d1 |
b′ |
R, r |
|
Св. 10 до 50 |
D + 0,5 |
d – 0,5 |
3 |
0,5 |
|
Св. 50 |
до 100 |
D + 1,0 |
d – 1,0 |
5 |
0,5 |
Св. |
100 |
D + 1,0 |
d –1,0 |
8 |
1,0 |
Задание 8. Расчет размерных цепей
В соответствии с заданием № 8 (табл. П.1.3) рассчитать точность размеров сборочной или технологической линейной РЦ (прил. 8, рис. П.8.1–П.8.4), если известны размеры составляющих звеньев, кроме одного А4, и задано замыкающее — исходное звено А0 с отклонениями. Расчет провести методом «максимум — минимум», обеспечивающим полную взаимозаменяемость. Решение задачи выполнить способом одинаковой точности изготовления всех размеров РЦ, т. е. способом назначения на все размеры допусков одного квалитета [4, с. 485; 9, с. 4…108; 14; 16].
Порядок выполнения задания
8.1.Для выполнения данного задания изучить материал темы № 17 (Размерные цепи) [11], где изложены методы расчета линейных размерных цепей (РЦ).
8.2.По исходным данным в черновике составить схему линейной РЦ, указать увеличивающие
→ |
← |
|
|
Ai |
, уменьшающие Aj звенья, а также замыкающее (исходное) звено А0 [7; 9; 11; 16]. |
||
|
8.3. Определить размер неуказанного звена по формуле |
|
|
|
m → |
n ← |
|
|
А0 = ∑Ai |
− ∑Aj , |
(8.1) |
|
i=1 |
j=1 |
|
где A0 ― номинальный размер замыкающего (исходного) звена, мм; m ― количество увеличивающих звеньев; n ― количество уменьшающих звеньев.
8.4. Установить квалитет точности изготовления размеров РЦ.
Принцип полной взаимозаменяемости при решении РЦ обеспечивается при условии:
|
m |
→ |
n |
← |
|
|
|
ТА0 ≥ ∑T Ai |
+ ∑T Aj , |
|
(8.2) |
||
|
i=1 |
j=1 |
|
|
|
|
|
|
|
|
m |
→ |
|
где ТА0 |
― допуск замыкающего звена, мкм; ∑T Ai |
― сумма допусков увеличивающих звеньев, |
||||
|
|
|
|
i=1 |
|
|
n |
← |
|
|
|
|
|
мкм; ∑T Aj ― сумма допусков уменьшающих звеньев, мкм. |
||||||
j=1 |
|
|
|
|
|
|
8.4.1. Определить меру точности для каждого составляющего звена РЦ. |
||||||
Допуск любого звена устанавливается по формуле |
|
|||||
|
|
Tai = aiii, |
|
|
(8.3) |
где ai ― количество единиц допуска; ii ― единица допуска (мера точности), мкм. Подставляя допуск каждого составляющего звена РЦ (8.3) в формулу (8.2), получим:
ТА0 = a1i1 + a2i2 + … + am+n im+n, |
(8.4) |
где m + n ― общее количество составляющих звеньев РЦ.
Единица допуска (мера точности) для размеров от 1 до 500 мм определяется по формуле [1; 9; 16]
ii = 0,45 3 |
D |
+ 0,001D , |
(8.5) |
где D ― среднегеометрическое значение размеров начала и конца интервалов, куда входит рассматриваемый размер.
Рассчитанные по формуле (8.5) значения единиц допуска для размеров от 1 до 500 приведены в табл. 8.1 [9, табл. 3.3, с. 22; 16, с. 256].
|
|
|
|
|
|
|
|
|
|
|
Таблица 8.1 |
|
|
|
|
|
|
Значения единиц допуска для всех интервалов размеров от 1 до 500 мм |
|
|
|
|
|
|
|||||||
|
|
|
|
|
|
|
|
|
|
|
|
|
|
|
|
|
|
|
|
|
|
|
Интервал размеров, мм |
|
|
|
|
|
|
||
Свыше |
1 |
|
3 |
6 |
10 |
18 |
30 |
50 |
|
80 |
120 |
|
180 |
250 |
|
До |
3 |
|
6 |
10 |
18 |
30 |
50 |
80 |
|
120 |
180 |
|
250 |
315 |
|

Единица |
0,5 |
0,7 |
0, |
1,0 |
1,3 |
1,5 |
1,8 |
2,1 |
2,5 |
2,8 |
3,2 |
|
допуска |
|
|||||||||||
5 |
3 |
9 |
8 |
1 |
6 |
6 |
7 |
2 |
9 |
2 |
|
|
i, мкм |
|
|||||||||||
|
|
|
|
|
|
|
|
|
|
|
|
8.4.2. Определить количество единиц допуска. По условию задания все размеры РЦ должны иметь один квалитет точности, тогда
a1 = a2 = a3 = … = am+n = aср. |
(8.6) |
Используя равенство (8.6) и формулу (8.4), определить среднее количество единиц допуска:
|
|
|
|
TA0 |
|
[мкм] |
|
aср = |
|
|
|
|
|
[мкм]. |
(8.7) |
i |
+ i |
2 |
+ i + ...+ i |
m+n |
|||
|
1 |
|
3 |
|
|
8.4.3. Из табл. 8.2. (ГОСТ 25346–89) или [9, табл. 1.8] установить ближайший квалитет, соответствующий вышерассчитанному среднему количеству единиц допуска aср. За каждым квалитетом закреплено определенное число единиц допуска. Если a окажется средним значением между квалитетами, то при назначении допусков составляющих звеньев рекомендуется использовать два соседних квалитета (см. табл. 8.2). Большее число квалитетов назначить для увеличивающих звеньев. Чем больше aср, тем больше цифра квалитета, тем больше допуск и тем «грубее» выполнен размер.
8.5. Для каждого размера назначить допуски с учетом выбранного квалитета. Для увеличивающих звеньев рекомендуется назначить допуски, как для основного отверстия (основное отклонение Н), а для уменьшающих ― как для основного вала (h)*. Для всех звеньев РЦ проставить числовые значения предельных отклонений по ГОСТ 25347–82 с учетом квалитета и размера.
Таблица 8.2
Соответствие между квалитетами точности и количеством единиц допуска
Обозначение допусков (квалитет) |
T |
T |
T |
T |
T |
T 1 |
T 1 |
T 1 |
T 1 |
T 1 |
T 1 |
T 1 |
T 1 |
T 1 |
|
|
|
|
|
|
|
|
|
|
|
|
|
|
|
Количество единиц допуска, а |
7i |
10i |
16i |
25i |
40i |
64i |
100i |
160i |
250i |
400i |
640i |
1000i |
1600i |
2500i |
|
|
|
|
|
|
|
|
|
|
|
|
|
|
|
|
|
|
|
|
|
|
|
|
|
|
|
|
|
|
8.6. Одно звено (лучше уменьшающее) оставить компенсирующим (зависимым). Отклонения этого звена должны обеспечить (с учетом отклонений остальных размеров) заданные отклонения исходного (замыкающего) звена. Отклонения компенсирующего звена рассчитываются по формулам:
m |
→ |
n |
← |
|
EsA0 = ∑Es Ai |
− ∑Ei Aj , |
(8.8) |
||
i=1 |
|
j=1 |
|
|
m |
→ |
n |
← |
|
EiA0 = ∑Ei Ai |
− ∑Es Aj , |
(8.9) |
||
i=1 |
|
j=1 |
|
|
где Еs ― верхнее отклонение звена РЦ; Еi ― нижнее отклонение звена РЦ.
8.7.Сделать проверку. Полученные допуски звеньев просчитать по формуле (8.2), и если условие выполняется, то задача решена правильно. В противном случае решение неверное, так как не обеспечивается принцип полной взаимозаменяемости.
8.8.Выполнить графическую часть работы, которая включает чертеж узла (рис. П.8.1–П.8.4) с нанесенными размерами РЦ и отклонениями. Замыкающее звено на чертеже не проставляется. Начертить схему РЦ с обозначением всех звеньев, их номинальных размеров и предельных отклонений, включая замыкающее звено.
Задание 9. Резьба метрическая. определение размеров, допусков и отклонений резьбового соединения
Из табл. П.1.3 установить исходные данные своего задания (по варианту).
Нормативные документы для метрической резьбы, образующей посадку с зазором: ГОСТ 9150–2002; ГОСТ 8724–2002; ГОСТ 24705–2004; ГОСТ 16093–2004*.
*Существуют и иные способы определения и назначения отклонений размеров РЦ, например, расчет средних отклонений, обеспечивающих симметричное расположение полей допусков [1; 4; 5…7; 9, с. 4…108; 14; 16]. Возможна корректировка допусков.
*Перечень государственных стандартов, используемых для выполнения заданий, приведен в прил. 10.
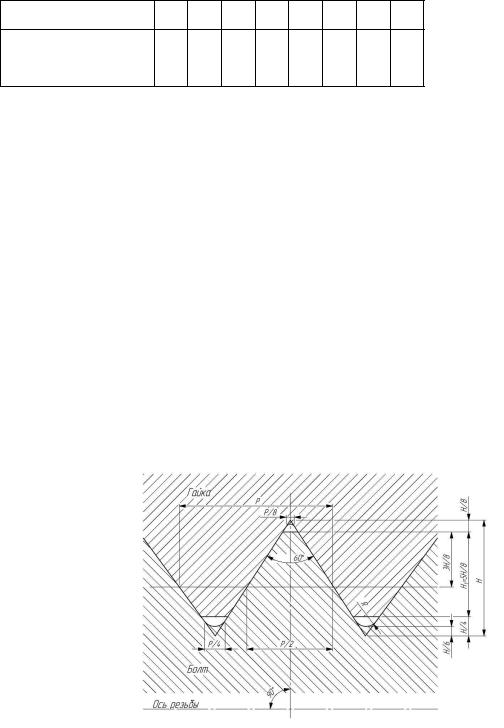
9.1.Порядок выполнения задания
9.1.1.Записать резьбовое соединение метрической резьбы: вид резьбы, наружный размер, посадка и шаг Р для мелкой резьбы. Если в обозначении резьбы шаг указан, значит, резьба с мелким шагом. Крупный шаг резьбы в маркировке не указывается и определяется по ГОСТ 8724–2002 в зависимости от наружного диаметра (табл. 9.1).
Таблица 9.1
Резьба метрическая с крупным шагом. Диаметры и шаги, мм
Наружный диаметр резьбы
Крупный шаг
9.1.2. По табл. 9.2 (ГОСТ 24705–2004) рассчитать номинальные размеры наружного, среднего и внутреннего диаметров резьбы с учетом равенства диаметров (d = D) и с учетом соответствующего шага резьбы [9, 16].
|
|
|
|
|
|
|
|
|
|
|
|
|
|
|
|
|
Таблица 9.2 |
|
|
|
|
Размеры среднего и внутреннего диаметров метрических резьб, мм |
|
|
|
||||||||||||
|
|
|
|
|
|
|
|
|
|
|
|
|
|
|
|
|
||
|
|
|
|
Диаметр резьбы |
|
|
|
|
|
|
|
Диаметр резьбы |
|
|
||||
|
Шаг |
|
|
(болт и гайка) |
|
|
|
Шаг |
|
|
(болт и гайка) |
|
|
|||||
|
резьбы Р |
|
Средний |
Внутренний |
|
резьбы Р |
|
Средний |
|
|
Внутренний |
|
||||||
|
|
|
диаметр d2, D2 |
диаметр d1, D1 |
|
|
|
|
|
диаметр d2, D2 |
|
диаметр d1, D1 |
|
|||||
|
1,0 |
|
d – 1 + 0,350 |
d – 2 + 0,917 |
|
|
2,0 |
|
|
d – 2 + 0,701 |
|
d – 3 + 0,835 |
|
|||||
|
1,25 |
|
d – 1 + 0,188 |
d – 2 + 0,647 |
|
|
2,5 |
|
|
d – 2 + 0,376 |
|
d – 3 + 0,294 |
|
|||||
|
1,5 |
|
d – 1 + 0,026 |
d – 2 + 0,376 |
|
|
3,0 |
|
|
d – 2 + 0,051 |
|
d – 4 + 0,752 |
|
|||||
|
1,75 |
|
d – 2 + 0,863 |
d – 2 + 0,106 |
|
|
3,5 |
|
|
d – 3 + 0,727 |
|
d – 4 + 0,211 |
|
|||||
|
В качестве примера рассмотрим резьбу М20 – 7H/6g. Установим шаг резьбы (см. табл. 9.1) и |
|||||||||||||||||
номинальные размеры всех диаметров (рис. 9.1). Шаг резьбы равен 2,5 мм. |
|
|
|
|
|
|||||||||||||
|
Диаметры |
наружной |
резьбы |
(болта), |
мм: |
наружный |
|
диаметр |
d |
= |
||||||||
= |
20,000; |
|
средний |
диаметр d2 |
= d |
– |
2 |
+ |
|
0,376 |
= |
20,000 |
– |
2,000 |
+ |
|||
+ |
0,376 = |
18,376; |
внутренний |
диаметр |
d1 |
= |
d |
– 3 |
+ |
0,294 |
= |
20,000 |
– |
|||||
– 3,000 + 0,294 = 17,294. |
|
|
|
|
|
|
|
|
|
|
|
|
|
|
|
|||
|
Для внутренней резьбы (гайки): наружный диаметр D = 20,000; внутренний диаметр D1 = d1 = |
|||||||||||||||||
17,294; |
|
средний |
диаметр |
|
|
D2 |
|
= |
|
|
d2 |
|
= |
|||||
= 18,376. |
|
|
|
|
|
|
|
|
|
|
|
|
|
|
|
|
|
Рис. 9.1. Резьба метрическая. Профиль
9.1.3. Для указанного сопряжения резьбы с зазором (прил. 9, табл. П.9.1, ГОСТ 16093–2004) определить числовые значения отклонений и допуски (мм) на соответствующие номинальные диаметры отдельно для наружной (болта) и внутренней (гайки) резьб [9, 16].
Для болта: верхние отклонения es диаметров d, d2, d1 равны –0,042 мм; нижнее отклонение ei наружного диаметра d составляет –0,377 мм; нижнее отклонение ei среднего диаметра d2 равно –0,212 мм; при этом нижнее отклонение ei внутреннего диаметра d1 не нормируется.