
751
.pdfk |
|
= |
Gз.щ |
. |
(5) |
оч |
|
||||
|
|
Gщ |
|
||
|
|
|
|
Коэффициенты kэ и kоч должны находиться в пределах 0,8…0,9 и 0,03…0,05.
Маневренность характеризуется транспортной скоростью машин, самоходностью, реверсивностью, типажом ходовой части. Транспортная скорость машин в составе поезда и самоходом должна быть не менее 80 км/ч.
Высокие транспортные скорости позволяют уменьшить потери времени при переезде машины к месту работы и обратно, что увеличивает выработку в «окно».
Реверсивность машин в транспортном и рабочем положениях и быстрый перевод из транспортного в рабочее положение и обратно повышает их маневренность и улучшает их использование. Однако часто невозможно придать машине реверсивность в рабочем положении из-за особенностей конструкций рабочего оборудования.
Надежность машин характеризуется безотказностью, долговечностью, ремонтопригодностью, сохраняемостью. Эти показатели надежности обеспечиваются конструктивно-технологи-ческими мероприятиями, в том числе резервированием систем и узлов, простотой управления и обслуживания, защитой механизмов машины системами автоматики.
Безотказная работа в «окно» — основное требование к надежности щебнеочистительных машин.
Ни одна из современных щебнеочистительных машин не отвечает в полной мере предъявляемым требованиям. Рабочая скорость машин типа ЩОМ-4М может достигать 2,5 км/ч при производительности до 2500 м3/ч. Однако при этом глубина очистки (вырезки балласта) hв балластной призмы мала и качество очистки низкое (hв = 0,25…0,03 м, kоч ≈ 0,07…0,1). Машинами СЧ-601, RM-80 достигается глубина очистки 0,6 м, однако рабочая скорость их в этом случае не превышает 0,05 – 0,10 км/ч. Производительность машин составляет 500–600 м3/ч, качество очистки — в пределах нормы (kоч = 0,05…0,07).
13
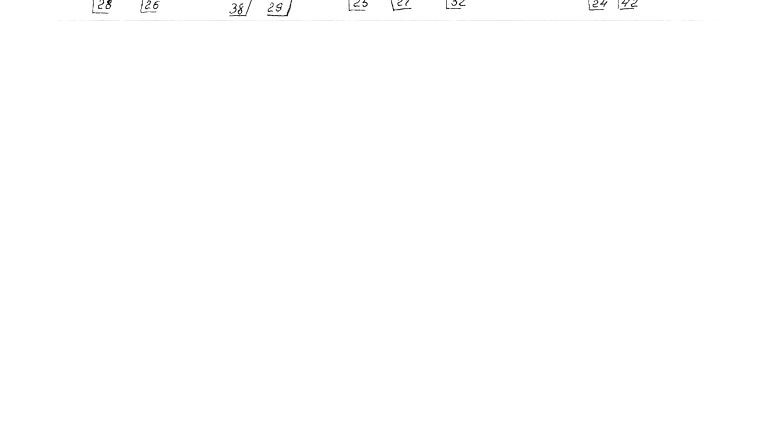
а)
б)
в)
Рис. 7. Щебнеочистительная машина RM-2002:
а — общий вид; б — добывающая секция; в — секция грохочения; 1, 2 — ходовая тележка; 3 — рама; 4 — силовая установка с гидростанцией; 5 — кабина машиниста; 6 — выгребное оборудование; 7 — приемная воронка; 8 — конвейер подачи загрязненного балласта; 9 — загрузочный подвижной конвейер; 10 — загрузочная воронка; 11 — конвейер подачи чистого балласта; 12 — бункер; 13 — конвейер-распределитель чистого балласта; 14 — плуговой распределитель балласта; 15 — агрегат подачи балласта под торцы шпал; 16 — пробивщик шпальных ящиков; 17, 18, 19 — устройство: поддержки решетки, подъемно-рихтовочное, выправочное; 20 — планировщик; 21 — укладчик распределительного полотна; 22 — кабина оператора; 23 — манипулятор; 24, 25, 26 — тяговые тележки; 27, 28 — рама: основная, качающаяся; 29 — шарнир; 30 — силовая установка; 31 — гидростанция; 32 — компрессор;
33 — топливный бак; 34 — воронка перегрузки загрязнителей; 35 — дозировочный конвейер; 36, 37 — виброгрохот; 38
— конвейер подачи чистого балласта; 39, 40 — конвейер подачи загрязнителей; 41 — поворотный разгрузочный конвейер; 42 — кабина машиниста
14
Машины с активными рабочими органами совершенствуются в направлении повышения производительности по экскавации и очистке щебня. Так, машина RM-2002 (рис. 7) состоит из двух секций. Первая — оборудована выгребным устройством повышенной производительности, на второй — применены два грохота. Производительность машины повышена до 1000 м3/ч при глубине очистки 0,4 м. Машина выполнена в самоходном варианте с тяговыми тележками в очистной секции.
Повышению производительности машины способствует также применение щебнеочистительных комплексов. Например, машина ЩОМ-6Б может работать в сцепе с машиной ЩОМ-6Р. Последняя предназначена для очистки балласта у торцов шпал.
Основным фактором, препятствующим увеличению глубины вырезки балласта машинами с пассивным рабочим органом, является значительное сопротивление перемещению подрезного ножа. На машинах ЩОМ-4М для повышения производительности, увеличения глубины и ширины вырезки балласта применены несколько рабочих органов для разработки и грохочения материала. Вырезка балласта за торцами шпал производится роторными устройствами. Это способствует снижению сопротивления материала перемещению подрезного ножа и дает возможность увеличить глубину вырезки балласта. Для очистки балласта, вырезанного роторами, используется дополнительное щебнеочистительное устройство.
Одним из вариантов совершенствования рабочего оборудования обоих типов машин может быть использование роторов для вырезки балласта под концами шпал и подачи его в продольную траншею, разработанную боковыми роторами. Это будет способствовать снижению сопротивления материала вырезанию и позволит увеличить производительность машины. Для повышения качества очистки балласта, особенно влажного, целесообразно применять двойную очистку грохотами различных конструкций. Возможен и вариант очистки щебня на грохоте с помощью воздушной или водяной струи, а также с помощью специальных щеток.
Следует отметить, что применение цепных скребковых рабочих органов не является единственным направлением в совершенствовании машин данного типа. Основные недостатки цепных рабочих органов: быстрый износ их элементов, высокая энергоемкость, низкий коэффициент полезного действия (0,4…0,65), значительная металлоемкость. При вырезке балласта необходимо стремиться к тому, чтобы как можно меньший объем балласта подвергался резанию (копанию). Необходим рабочий орган с подрезанием слоя балласта с последующим обрушением и разрыхлением верхних слоев балластной призмы. Это способствовало бы сокращению энергозатрат на вырезание балласта и уменьшению дробления частиц щебня.
Скребковые рабочие органы практически исчерпали возможности улучшения эксплуатационных характеристик и повышения производительности без существенного повышения энергозатрат. Опыт применения машин для разработки грунтов и горных пород показывает, что более эффективными являются рабочие органы роторного типа.
3.ВЫГРЕБНОЕ ОБОРУДОВАНИЕ МАШИН
СЦЕПНЫМ СКРЕБКОВЫМ РАБОЧИМ ОРГАНОМ
3.1.Общие сведения
Взависимости от требуемой производительности машины разрабатывают односекционные или двухсекционные. В последнем случае одна секция (добывающая) оборудована рабочими органами для выемки и транспортирования загрязненного балласта (выгребное оборудование). Вторая секция — для очистки балласта и транспортирования чистого щебня и загрязнителей (RM-2002, ЩОМ-1200).
Выгребное оборудование машин состоит из восходящего и нисходящего желобов с боковыми крыльями, подпутной балки, скребкового рабочего органа и его привода, механизмов управления рабочим оборудованием.
На машинах, предназначенных для очистки стрелочных переводов, с целью увеличения ширины вырезки балласта применены подпутные балки увеличенной длины и один из желобов — телескопический.
С помощью скребковых рабочих органов производится вырезка и транспортирование балласта под решеткой, а также транспортирование щебня на грохот.
Вскребковом рабочем органе можно применять различные варианты сочетаний элементов, режущих и волочащих материал. На эксплуатируемых машинах применяют скребки с укрепленными на них резцами (с зубьями). Известны рабочие органы, в которых резцы и скребки установлены
15
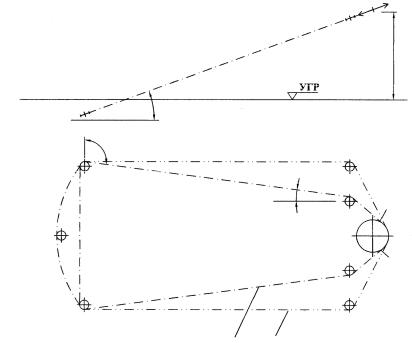
отдельно. Подобные рабочие органы можно использовать и на щебнеочистительных машинах. Возможны и другие комбинации рабочего оборудования.
3.2. Размещение оборудования на машине
Важным вопросом при компоновке рабочего оборудования на машине является выбор конфигурации трассы движения рабочего органа выгребного устройства.
Основными параметрами трассы являются: общая Lс и рабочая Lщ длина; высота подъема балласта hв.п, угол наклона в вертикальной плоскости α; наибольший угол изменения направления движения органа γ.
При выборе трассы необходимо предусмотреть возможность: частичного изменения направления движения рабочего органа и длины Lс для различных условий производства работ (на перегоне, на стрелочных переводах); быстрого приведения рабочего органа из транспортного положения в рабочее и наоборот; совмещения технологических (вырезка балласта) и транспортных операций; перемещения рабочего органа с минимальным количеством поворотов и по трассе наименьшей длины. Одновременно необходимо решать вопросы размещения привода рабочего органа. На рис. 8 показаны варианты применяемых на машинах и возможных трасс скребковых рабочих органов.
Существенное влияние на выбор базы машины и ее производительность оказывает угол наклона трассы в вертикальной плоскости α (см. рис. 8, 9). С увеличением угла α снижается производительность выгребного оборудования по транспортированию балласта. При малых углах α увеличивается трасса движения рабочего органа, что в свою очередь требует увеличения базы машины. На эксплуатируемых машинах α = 25…35°.
а)
hр
|
α |
|
γ |
3 |
2′ |
б) |
|
|
β |
|
|
|
|
1 |
|
|
|
|
2 |
|
|
|
|
|
|
|
3′ |
|
|
1′ |
|
|
|
6′ |
|
|
|
|
|
|
|
|
|
5 |
6 |
|
|
|
|
|
|
|
4 |
5′ |
|
|
|
|
|
а б Рис. 8. Варианты трасс выгребного скребкового органа:
а— вид сбоку; б — вид в плане
Взависимости от характера выполняемых технологических операций трассу можно разбить на участки: экскавационно-транс-портирующий [зону забоя (3–4), см. рис. 8]; транспортирования балласта (4–5), разгрузочный (5–1–2); холостого хода (2–3).
Все участки трасс а и б (см. рис. 8), кроме разгрузочного, прямолинейны, с резкими переходами от одного к другому, особенно в зоне забоя. На участке разгрузки трассы представляют собой ломаную линию. Трассы имеют различные углы изменения направления движения рабочего орга-
на γ в зоне забоя и углы сходимости β (см. рис. 8, б). Участки 2′–3 и 4–5′ могут быть расположены практически параллельно рабочей оси машины (см. рис. 8, б).
Резкое изменение направления трассы рабочего органа в зоне забоя (увеличение угла γ) отрицательно влияет на равномерность процесса копания балласта, условия транспортирования материала и на надежность узлов выгребного оборудования. При входе скребков в зону забоя происходит ударное воздействие их на балласт, что неблагоприятно сказывается на эффективности работы выгребного органа. Выход скребков из зоны забоя с резким изменением направления движения (от
16
участка 3–4 к участку 4–5) приводит к разбросу щебня под действием центробежных сил и, как следствие, ухудшается заполнение балластом пространства между скребками.
При малых углах сходимости β разброс щебня при его разгрузке уменьшается, однако длина участка разгрузки при этом увеличивается.
На эксплуатируемых машинах углы γ = 100…110°, β = = 12…20°. Существенно изменить конфигурацию трассы скребкового рабочего органа, особенно в зоне забоя, сложно. Связано это главным образом с ограничениями размещения выгребного оборудования на машине, обусловленными размерами путевой решетки, габаритов подвижного состава и приближения строений.
При разработке выгребного оборудования необходимо предусмотреть устройства, способствующие снижению ударного воздействия скребков на балласт и повышению эффективности заполнения пространства между ними. С этой целью, например, можно использовать конфигурацию трассы скребков в зоне забоя по ломаной линии (3–3′–4) (см. рис. 8, б). Для создания такой трассы необходима подпутная балка более сложной конструкции, чем на имеющихся современных машинах.
На эксплуатируемых машинах на оголовках желобов устанавливают боковые крылья, с помощью которых можно изменять ширину полосы вырезаемого слоя балласта. Кроме того, снижаются ударные нагрузки на рабочий орган, так как скребки начинают воздействовать на уже разрыхленный щебень. Подача крылом балласта к восходящему желобу способствует уменьшению разброса частиц щебня и повышению эффективности заполнения балластом пространства между скребками.
После выбора трассы рабочего органа производят предварительную компоновку выгребного оборудования на раме машины. При этом учитывается следующее. Щебень необходимо вырезать из-под шпал, на плечах балластной призмы и в междупутье. При работе в кривых ферма машины и, следовательно, оборудование смещаются относительно оси пути. Так, на кривых с радиусом 300 м при существующих базах машин смещение оси фермы относительно оси пути в поперечном направлении достигает 120…140 мм. Вырезка балласта не должна производиться близко к колесным парам ходового оборудования. Расстояние между подпутной балкой и рельсовыми захватами путеподъемного оборудования по длине машины должно быть минимальным. Промежуток между забоем и местом выгрузки под решетку очищенного балласта устанавливают с учетом высоты и угла естественного откоса отсыпаемого чистого щебня, удобства демонтажа подпутной балки и необходимости размещения дополнительного оборудования, например, для отсыпки песчаной подушки и ее уплотнения.
При компоновке рабочего оборудования необходимо обратить внимание на взаимное расположение опорной (корневой) части и оголовка выгребного оборудования (рис. 9). Опорную часть стремятся располагать как можно ближе к тележке (расстояние lк). По высоте от уровня головки рельса hк она и расположенное на ней оборудование не должны выходить за пределы габарита подвижного состава. Оголовок выгребного устройства (расстояние lз) располагают так, чтобы угол наклона конвейерной части устройства к горизонту α не превышал 40°.
Путеподъемное устройство размещают перед или после подпутной балки как можно ближе к оголовку и как можно дальше от передней тележки (расстояние lп.т).
Для предварительной компоновки, например, машины типа СЧ-601, можно принять:
lк = (0…1,0)lт; lз = (0,5…0,7)lо; hк = (0,7…0,8)Hг; lп ≈ ±1,5…2,0 м; lп.т ≥ 5,0 м,
где lт — база тележки, м; lо — база машины, м; Hг — высота габарита подвижного состава, в который требуется вписать машину, м.
17
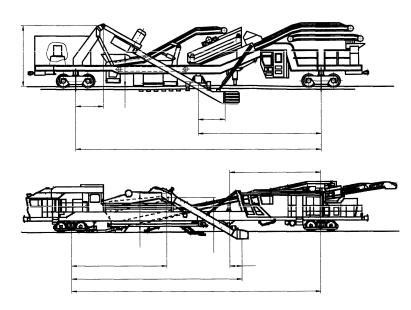
а)
hк
lк
б)
раз |
|
h |
lп |
|
|
|
lп.т |
|
lо |
lп.т
h |
раз |
к |
|
|
h |
lк |
lп |
|
lз |
|
lо |
Рис. 9. Схема компоновки оборудования на машине: а — СЧ-601; б — RM-80
Предлагаемые соотношения могут изменяться в более широких пределах и зависят от особенностей конструкций выгребного и путеподъемного оборудований.
Место разгрузки скребкового рабочего органа назначают по высоте hраз (см. рис. 9, а, б) с учетом необходимости размещения конвейера для транспортирования вырезанного балласта или грохота для его очистки, а также ограничения габаритами подвижного состава. По опыту проектирования
hраз = (1,7…2,0)hф,
где hф — расстояние от уровня головки рельса до верхнего пояса фермы в месте установки разгрузочного устройства.
Вопрос о месте размещения привода рабочего органа выгребного оборудования решают с учетом предполагаемых его конструкции и изменений нагрузок на рабочий орган по длине его трассы, а также ограничений, связанных с необходимостью вписывания оборудования в габариты подвижного состава. В устройствах (конвейерах), подобных выгребному оборудованию, рекомендуется устанавливать привод в месте наибольшего нагружения тягового органа. В рассматриваемых вариантах трассы скребкового органа его приводной вал должен располагаться после участка 4–5. Здесь же удобно размещать привод и по соображениям вписывания оборудования в габариты подвижного состава.
Компоновку остального рабочего оборудования производят по различным вариантам. Так, например, на машинах типа СЧ-601 выгребное оборудование выгружает балласт на конвейер, который подает его на грохот. Из грохота чистый щебень подается на путь через дозирующее устройство, а загрязнители конвейерами транспортируются и выгружаются на обочину или в специализированный состав.
На машинах типа RM-80 выгребное оборудование подает загрязненный балласт непосредственно на грохот. Чистый щебень подается на путь конвейерами.
Таким образом, возможны различные компоновки рабочего оборудования, и они зависят в основном от производственно-технических требований к машине, принятой ее базы, схемы энергоснабжения, габаритов подвижного состава, в который должна быть вписана машина.
3.3. Основные параметры оборудования
При очистке балластной призмы выполняются операции: вырезка балласта под рельсошпальной решеткой и по концам шпал; транспортирование материала к оголовку желоба; транспортирование балласта по желобу к месту разгрузки; разгрузка балласта в грохот (RM-80) или выгрузка балласта на промежуточный конвейер для подачи его на грохот (СЧ-601); грохочение. Рабочие процессы должны протекать непрерывно. Это будет обеспечено при выполнении условий:
Пог ≥ Kр.б Пм; Птр ≥ Пог; Пгр ≥ Птр, |
(6) |
18
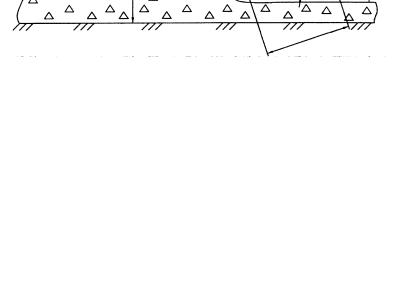
где Пог — производительность оборудования по транспортированию к оголовку желоба балласта, разрабатываемого скребками и боковыми крыльями, м3/с; Kр.б — коэффициент разрыхления балласта; Пм — требуемая производительность машины, м3/с; Птр — производительность выгребного оборудования по транспортированию балласта в восходящем желобе, м3/с; Пгр — производительность оборудования по грохочению, м3/с.
Условия (6) являются основой для расчета параметров рабочих органов машины. Производительность машины непрерывного действия определяют по формуле
Пм = Арvм, |
(7) |
где Ар — площадь поперечного сечения разрабатываемого слоя щебня, м2; vм — скорость движения машины, м/с.
Разрушение балластного слоя скребками производится не по всей его толщине hв. Вырезается нижняя часть балластного слоя толщиной hз. Верхняя часть слоя толщиной hоб удаляется после его обрушения в результате действия скребков на нижние слои и продавливателя балласта в шпальных ящиках (рис. 10). При конструировании рабочего оборудования важным является правильный подбор соотношений между указанными толщинами слоев балласта. В зависимости от толщины слоя балласта под шпалой, его состояния по загрязненности и прочностным характеристикам в расчетах принимают:
hв = hБ – (2…3)dср; hз = (0,3…0,5)hв;
hобср hв – hз + 0,5hш.я ,
где hБ — толщина слоя балласта под шпалой, м; dср — средний размер частиц щебня, мм (d = 0,04 м); hобср — средняя толщина обрушающегося слоя балласта, м; hш.я — толщина слоя балласта в шпальном ящике, м.
Площадь поперечного сечения приблизительно определяют по зависимости
Ар (bвв + bвн ) (hв + 0,5hш.я ) ,
2
где bвв, bвн — ширина поперечного профиля вырезаемой части по верху и по низу балластной призмы.
bск
Рис. 10. Схема разработки слоя балласта скребками
Производительность Пм служит основой для расчета параметров скребкового полотна, обеспечивающего подачу материала из балластной призмы к оголовку рабочего (восходящего) желоба (см. соотношения 6).
Производительность оборудования по транспортированию балласта к оголовку желоба составит:
Пог = kнbскhскvск, |
(8) |
где kн — коэффициент заполнения балластом пространства между скребками (kн = 0,7…0,8); bскhск — ширина и высота скребков, м; vск — скорость движения скребков, м/с.
Размеры скребка принимают в увязке с толщиной вырезаемого слоя и угла наклона скребков α:
19

h ≤ hз sinβ ; bск ≈ (1,0…2,0)hск. ск sin(α + β)
При использовании комбинированных скребков ширина bск включает в себя и длину резцов. На эксплуатируемых машинах hск ≈ 250…350 м.
С целью эффективного заполнения балластом межскребкового пространства шаг скребков назначают с учетом их скорости, длины забоя, шага цепи Sц, скорости машины и размеров частиц балласта. Предварительно принимают:
aск = (2…4) Sц или aск = (6…8)dср.
Условие эффективного заполнения пространства между скребками определяют, используя со-
отношение |
|
|
|
|
|
|
|
||
|
b h a′ k |
н |
≥ |
( |
SA +V |
k |
р |
, |
|
|
ск ск ск |
|
p б.к ) |
|
|
||||
′ |
|
vм |
|
|
|
|
|
|
|
где aск |
= aск – δск; S = aск v |
|
— подача на скребок, м; Ар — площадь поперечного сечения балла- |
||||||
|
|
ск |
|
|
|
|
|
|
стной призмы, разработанной скребками, м2; Vб.к — объем балласта, подаваемого на скребки боковыми крыльями, м3; δск — усредненная толщина лопатки скребка, м.
На машинах типа СЧ-601, RM-80 применяют специальные тяговые цепи с Sц = 125…150 мм, шаг aск = 2Sц; скорость vск = = 2,5…4,0 м/с.
Используя зависимости (7) и (8) и выполняя условие (6), уточняют предварительно назначенные размеры скребков.
Для определения размеров желоба и уточнения параметров скребков рассматривают производительность выгребного оборудования по подъему вырезанного балласта к месту разгрузки [3, 8]:
Птр = Вж.р hск kз kжvск, |
(9) |
где Вж.р — рабочая ширина желоба, м; kз — коэффициент заполнения желоба; kж — коэффициент, учитывающий угол наклона конвейера α.
При угле наклона α = 30…40° kз = 0,6…0,7, kж = 0,7…0,8.
По требуемой производительности (Птр ≥ Пог) определяют необходимую рабочую ширину желоба Вж.р и корректируют размеры скребка:
bск ≈ Вж.р – 2δж,
где δж — конструктивный зазор между корневой частью, зубьями скребка и стенками желоба, м (δж ≈ 15…20 мм).
Ширину желоба проверяют с учетом размера dср средних частиц балласта. Bж.р ≥ (5…7) dср.
Для повышения прочностных свойств желоба и предотвращения вылета щебня из желоба при высокой скорости скребков рабочую высоту Hж.р принимают Hж.р ≈ (1,5…2) hск.
3.4. Компоновка выгребного оборудования
Компоновка оборудования — это многовариантная задача, решение которой зависит от конкретных исходных данных по вырезке балласта, выбранного варианта трассы выгребного органа, предварительно установленных основных параметров оборудования, базы машины.
Основными параметрами, учитываемыми при компоновке оборудования, являются: ширина захвата вырезаемого балластного слоя выгребным рабочим органом bж.н и боковыми крыльями bк′ и bк′′ , длина восходящего lж.в и нисходящего lж.н желобов, угол наклона желобов в вертикальной
плоскости α, угол сходимости желобов β, расстояние между опорными шарнирами желобов в зоне разгрузки bоп (рис. 11).
20
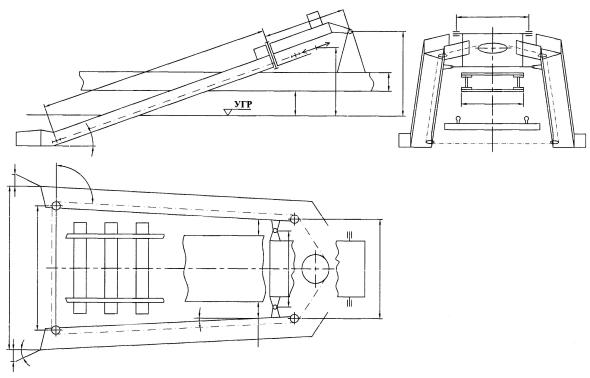
lж.в
α
к |
γ |
b
ж.н |
р.н |
b |
b |
β
Ψ
b к
lпр |
|
bпр |
|
|
|
|
|
к |
|
|
h |
|
|
ф |
|
|
H |
ф |
раз |
|
h |
h |
Вф |
|
|
δ ф
bоп bв.р
δ ф
Рис. 11. Компоновка выгребного оборудования
21
Исходные данные для компоновки: требуемые глубина hв и ширина bвн вырезки балластного слоя (bвн = bж.н + bк′ + bк′′ ), размеры рельсошпальной решетки, ширина Вф и высота Нф фермы машины в рассматриваемом сечении, высота расположения нижнего пояса фермы относительно уровня головки рельса hф, размеры габарита подвижного состава, в который вписывают выгребное оборудование, и габарита приближения строений.
Компоновку узлов выгребного оборудования начинают с определения положения оголовков желобов относительно рельсошпальной решетки. Предварительно устанавливают возможные размеры полос, вырезаемых выгребным рабочим органом и боковыми крыльями. Затем с учетом ранее рассчитанных параметров желобов, рекомендаций по проектированию и опыта эксплуатации машин принимают решение о расположении оборудования (см. рис. 11).
Минимально bжmin.н и максимально bжmax.н возможную ширину полосы балласта, вырезаемую выгребным органом, определяют при угле наклона боковых крыльев к оси пути ψ = 0:
22