
751
.pdf
|
bmin ≈ Lшп + 2δм (1 + sinβ) + 2Вж; |
|
|||||
|
ж.н |
|
|
|
|
|
|
max |
′ |
′′ |
; |
′ |
= Вс – δс; |
′′ |
≈ 0,5Вм, |
bж.н |
= bж.н |
+ bж.н |
bж.н |
bж.н |
где Lшп — длина шпалы, м; δм — допускаемое минимальное расстояние между внутренней стороной желоба и торцами шпал, м (δм = 0,12…0,15 м); Вж — примерные габаритные размеры желоба
по ширине, м (Вж ≈ 1,3…1,5Вж.р); b′ , b′′ — полуширина полосы вырезаемого балласта с поле-
ж.н ж.н
вой стороны и со стороны междупутья, м; Вс — полуширина габарита приближения строений, м; δс
— ограничение приближения рабочего органа к сооружениям, находящимся около пути, м (δс ≈ 0,2 м); Вм — минимально допустимое расстояние между осями соседних путей, м.
При определении соотношения размеров полос балласта вырезаемых выгребным оборудованием и боковыми крыльями необходимо учитывать следующее. С увеличением ширины bж.н растут затраты мощности привода и длина выгребного органа, а также длина подпутной балки. Такие изменения отрицательно влияют на работоспособность выгребного оборудования. Увеличение же bк′ , bк′′ приводит к повышению нагрузок на оголовок желоба, растет сопротивление движению
машины.
С целью эффективной подачи к оголовку желоба балласта, вырезаемого боковыми крыльями, и уменьшения нагрузок на оголовки желобов угол раскрытия крыльев ψ и максимально возможную ширину полосы, вырезаемой крылом с полевой стороны bк′ и стороны междупутия bк′′ , назначают в пределах:
ψ = 25…30°; bк′ = bк′′ = (0,11…0,12)bж.н.
Подпутная балка через промежуточный элемент (усовик) крепится к оголовку желоба в месте установки отклоняющегося ролика. При выбранной ширине вырезки bж.н длина балки составит:
bб = bр.н; bр.н ≈ bв.ж + 2Rр.н,
где bв.ж — расстояние между внутренними сторонами желобов при принятой ширине bж.н, м; Rр.н
—радиус отклоняющих роликов, м.
Радиус Rр.н предварительно назначают по прототипу или принимают с учетом шага Sц тяговой
цепи [Rр.н ≈ (0,8…1,0)Sц].
При компоновке расположения желобов в зоне разгрузки назначают места установки шарниров, соединяющих желоба с рамой привода выгребного органа и места установки отклоняющих роликов (см. рис. 11).
Размещение шарниров и отклоняющих роликов по длине и ширине (bоп, bв.р) машины увязывают с принятой конфигурацией трассы выгребного органа, шириной фермы машины и необходимым местом расположения разгрузочного отверстия (расстояние lраз и высота hраз).
Разгрузка щебня производится у ведущей звездочки в промежутке между концевыми частями восходящего и нисходящего желобов. Минимальная длина разгрузочного отверстия рассчитывается по формуле [3]
lраз = |
|
|
vскbо.васк |
|
|
2h |
, |
(10) |
||
k |
и |
(b |
а |
− А |
) |
|
g |
|||
|
|
от |
ск |
о |
|
|
|
|
|
где bот — ширина отверстия под разгрузку щебня, м; аск — шаг скребков, м; h – высота слоя балласта в желобе, м (h = hск); kи — коэффициент истечения щебня (0,3…0,5); Ао — площадь проекции скребков на участке разгрузки на плоскость разгрузочного отверстия, м2.
Ширину bот назначают равной или больше ширины желоба в корневой части. Минимальное расстояние между шарнирами принимают:
bопmin = (1,2...1,3)lраз .
Максимальное расстояние bопmax будет при угле сходимости желобов β = 0.
При назначенном расстоянии bоп проводят проверку расположения желобов относительно фермы машины. Расстояние между внутренней стороной желоба и фермой машины δф в рабочем состоянии должно быть не менее 0,15…0,20 м, в транспортном — δф ≈ 0,05…0,1 м.
В транспортном положении эту проверку проводят при расположении желобов над уровнем головки рельсов на высоте не менее 350 мм.
Места расположения отклоняющих роликов желобов назначают конструктивно вблизи шарниров крепления желобов. Расстояние между роликами по ширине машины bв.р ≈ (0,9…1,1) bоп.
23
Длины желобов lж.н и lж.в определяют с учетом выбранной конфигурации трассы выгребного органа, принятых размеров между желобами в зонах вырезки балласта и местах его разгрузки, назначенных углах наклона α и высоты разгрузки hраз.
Длина lпр и ширина bпр привода выгребного органа предварительно назначается конструктивно с учетом принятия размеров bоп и hк, lпр ≈ (0,25…0,3)lж, bпр = (0,7…0,8) bоп.
Компоновка узлов выгребного оборудования в последующих разработках корректируется с учетом принятия конструкций желобов и привода выгребного органа, а также конструкций выбранных грохотов и конвейеров.
3.5. Мощность привода выгребного органа
По выбранной технологии производства работ и с учетом испытаний щебнеочистительных машин со скребковыми рабочими органами мощность двигателя привода составит:
Рдв = Рс/ηм; |
(11) |
|
|
Рс = Р1 + Р2 + Р3 + Р4 + Р5 + Р6, |
|
где Р1…Р6 — соответственно мощность, затрачиваемая на копание, разгон щебня, подъем балласта до уровня разгрузки, преодоление сил трения в забое и на восходящем и нисходящем желобах, на преодоление сопротивлений в направляющих роликах, кВт; ηм — КПД привода.
При определении затрат мощности учитывают физико-механические свойства балласта, угол наклона скребков в вертикальной плоскости, угол копания τ, опытные данные [4, 5, 6].
Мощность, затрачиваемая на копание, определяется по зависимости
Р1 = (QмKоKτ) / 1000, |
(12) |
где Qм — производительность оборудования по вырезке балласта скребками, м3/с; Ко — удельное сопротивление балласта копанию, Н/м2; Кτ— коэффициент, учитывающий угол копания τ.
При работе на частично разрыхленном балласте щебня по концам шпал Ко = (5…6) · 105 Н/м2. Для обеспечения устойчивой работы машины на уплотненном балласте принимают Ко = = (7…9) · 105 Н/м2.
С целью снижения сопротивления балласта копанию и интенсивности износа зубьев скребка назначают τ = 40…45°. Коэффициент Кτ при этом равен 0,65…0,7.
Мощность, затрачиваемая на разгон щебня, составит: |
|
|||||
P = K |
р.б |
(П |
м |
ρv2 |
)/(2 1000) , |
(13) |
2 |
|
ск |
|
|
где ρ — объемная масса балласта (1700…1800 кг/м3); vск — принятая скорость движения скребков, м/с; Kр.б — коэффициент разрыхления балласта.
Мощность, необходимая для подъема балласта, определяется:
Р3 = (Пм Нп γб)/ 1000, |
(14) |
где Нп — высота подъема балласта к месту разгрузки, м; γб — объемный вес балласта, Н/м3. Мощность, требуемая для преодоления сил трения в забое, составит:
Р4 = (qщ.з µщ + qc µп)lр vск /1000, |
(15) |
где qщ.з — усредненная погонная нагрузка вырезанного щебня в забое, Н/м; µщ — коэффициент трения щебня о щебень; qc — погонная нагрузка от тяговой цепи со скребками (qc ≈ 2,0…2,5 qщ.з), Н/м; µп — приведенный коэффициент трения тяговой цепи со скребками о балласт и направляющие подпутной балки; lр — расстояние между крайними скребками, производящими вырезку балласта, м.
Мощность, затрачиваемая на преодоление сил трения на желобах, равна:
Р5 = [(qщ.в+ qc ) µс Lж.в+ qc µжLж.н] cosα vск / 1000, |
(16) |
где qщ.в — погонная нагрузка щебня на восходящем желобе, Н/м (qщ.в = (ПмKр.бγр) /(3,6 vск)); µс — коэффициент трения скребков со щебнем о футеровку восходящего желоба; Lж.в, Lж.н — длины
восходящего и нисходящего желобов, м; µж — коэффициент трения тяговой цепи со скребками о днище нисходящего желоба; α — угол наклона желобов к горизонту, град; Kр.б — коэффициент разрыхления балласта (Kр = 1,15…1,2); γр — объемный вес разрыхленного балласта, Н/м3.
Мощность, необходимую на преодоление сопротивлений в направляющих роликах, определяют по зависимости
24

P = |
(Fo + Fн )ωovск |
, |
(17) |
||
|
|
||||
б |
1000 |
|
|
|
|
|
|
|
|
||
где Fо — минимальная сила натяжения тяговой цепи 5,0…7,0 кН; Fн — сила натяжения тяговой |
|||||
|
|
+...+ P5 |
|
||
цепи от рабочих нагрузок, кН Fн |
P1 |
; ωо — коэффициент сопротивления движению це- |
|||
|
vск |
||||
|
|
|
пи (при углах поворота цепи ≈ 90° ωо = 0,1…0,15).
После предварительного выбора двигателя определяют возможную силу в набегающей ветви выгребного оборудования и выбирают или проверяют тяговую цепь. Одновременно производят корректировку компоновки и параметров выгребного оборудования.
Ориентиром в расчетах затрат мощности приводом выгребной цепи могут служить экспериментальные данные [4]. Получена зависимость для определения затрат мощности на ведущей звездочке привода цепи:
Р 4,73П0,64 . |
(18) |
м |
|
Энергоемкость процесса зависит в основном от скорости движения цепи и скорости машины и составляет 0,38…0,4 кВт/(м3/ч).
Пример расчета затрат мощности
Задача. Рассчитать затраты мощности на перемещение скребков под рельсошпальной решеткой в рабочем режиме.
Исходные данные: ширина полосы балластного слоя, вырезаемого скребками bp = 3,5 м; толщина вырезаемого слоя hз = 0,3 м; скорость машины vм = 0,1м/с; скорость движения скребков
= 3,0 м/с; объемная масса разрыхленного щебня ρ = 1800 кг/м3; коэффициент разрыхления балласта Kр.б = 1,2; коэффициент трения между перемещаемым балластом и его неподвижной частью µщ = 0,8; коэффициент трения между тяговой цепью и направляющей подпутной балки µп = 0,4; толщина слоя балласта в шпальном ящике hш.я = 150 мм; боковые крылья выгребного оборудования прикрыты.
Решение. При перемещении скребков под рельсошпальной решеткой мощность привода выгребного оборудования расходуется на: копание балласта Р1, разгон вырезанного щебня до скорости скребков Р2, преодоление сил трения скребков со щебнем о щебень и о направляющую подпутной балки Р4.
|
|
K |
о |
K |
Q |
|
|
|
|
Kр.б |
Пмρvск2 |
|
(qщ.зµщ + qсµп )lрvск |
|
|||
Р = |
|
τ |
|
м |
; |
P = |
|
|
|
|
|
; Р = |
|
. |
|||
|
|
|
|
|
|
|
|
|
|
|
|||||||
1 |
|
1000 |
|
|
|
2 |
|
|
2 1000 |
4 |
1000 |
|
|||||
|
|
|
|
|
|
|
|
|
|
||||||||
Производительность по вырезке Qм и транспортированию Пм балласта скребками и усреднен- |
|||||||||||||||||
ные нагрузки qщ.з, qс составят: |
|
|
|
||||||||||||||
|
|
|
|
|
|
|
|
|
|
|
|
|
|
Qм = bp hз vм = 3,5 0,3 0,1 = 0,105 м3/с; |
|||
|
Пм = bp (hb + 0,5hш.я) vм |
= 3 (0,4 + 0,075) · 0,1 = 0,17 м3/с; |
|
||||||||||||||
|
|
|
|
q |
|
= |
|
Kр.б Пмρg |
|
= |
1,2 0,17 1800 9,8 |
= 1200 Н/м. |
|
||||
|
|
|
|
|
|
|
|
|
|
|
|
|
|
||||
|
|
|
|
|
|
|
|
|
|
|
|
|
|
||||
|
|
|
|
щ.з |
|
|
|
vск |
|
|
|
|
|
3 |
|
|
|
|
|
|
|
|
|
|
|
|
|
|
|
|
|
|
|
Приняв Kо = 7 · 105 Н/м2, Kτ = 0,7, qc = 1,2qщ.з = 1,2·1200 1440 Н/м и учитывая, что по условию задачи lр ≈ bр, получим
Р = |
7 105 |
0,7 0,105 |
= 57 кВт; |
||
|
|
|
|||
|
|
|
|||
1 |
|
|
1000 |
|
|
|
|
|
|
|
|
P = |
1,2 0,17 1800 32 |
|
=1,7 кВт; |
||
|
|||||
2 |
|
2 1000 |
|
||
|
|
|
Р3 = (1200 0,8+1440 0,4) 3,5 3 =16 кВт. 1000
Суммарные затраты мощности на перемещение скребков составят: Рс = Р1 + Р2 + Р3 = 57 + 1,7 + 16 = 74,7 кВт.
25
3.6. Силы, действующие на рабочее оборудование
На части рабочего оборудования действуют следующие основные силы сопротивления балласта: копанию скребками Fк.с, резанию боковыми крыльями Fр.к, перемещению скребков и вырезанного балласта под рельсошпальной решеткой Fв.с; силы отпора Fот.
С учетом экспериментальных данных [5, 6, 7] сопротивление балласта копанию можно определить по зависимости
Fк.с = 10С S (1 + 0,55hз)(1 – (90 – τ)/ 180)kбnр, (19)
где С — показания плотномера; S — подача на один скребок, см; hз — высота забоя, разрабатываемого скребками, см; τ — угол копания, град; kб — коэффициент, учитывающий степень блокирования копания балласта; nр — количество режущих скребков в забое.
Показания плотномера изменяются в широких пределах и зависят от засоренности, грузонапряженности участка, глубины вырезки балласта hр. В расчетах принимают при hр = 20 см С = = 10…12, hр = 35 см С = 20…25, hр ≥ 50 см С = 30…35.
Высоту забоя hз принимают с учетом принятой высоты скребка hск и среднего размера dср частицы щебня (hз = hск+ 2dср; dср = = 35…40 мм).
Для блокированного копания Kб = 1; для полублокированного — Kб = 0,6…0,75.
Из-за большого разброса экспериментальных данных по величине С силу Fк.с определяют также по найденной мощности, затрачиваемой на копание Р1(12). Установленные значения Fк.с по зависимости (19) и по величине мощности Р1 сравнивают между собой и с экспериментальными данными. В дальнейших расчетах используют усредненное значение силы Fк.с.
На зубья скребков действуют сила отпора вдоль оси пути Fк′′.с и сила Fот в вертикальной плоскости, и они составляют:
Fк′′.с = Fк.с sin τ, Fот = (0,20…0,25)Fк.с. |
(20) |
Разработка слоя балласта скребками и боковыми крыльями идет параллельно. Происходит полублокированное вырезание балласта крыльями и практически без образования призмы волочения. Сопротивление балласта резанию в этом случае составит:
Fр.к = Kо Kτ Kб Ар, |
(21) |
где Ар = hр.кbр.к — площадь сечения вырезаемого слоя балласта.
Для боковых крыльев принимают Kо = 100…130 кН/м2. Глубину резания hр.к устанавливают по толщине вырезаемого слоя балласта в междупутье или на плече балластной призмы. Ширину bр.к принимают из размеров предварительно скомпонованного рабочего оборудования.
Сила сопротивления движению скребкового полотна и балласта между скребками в забое рав-
на:
Fв.с = (qщ.з + qс)µсlp, |
(22) |
где qщ.з, qс — усредненный погонный вес щебня, перемещаемого скребками, и погонный вес тяговой цепи со скребками, Н/м; µс — приведенный коэффициент трения скребков с щебнем о щебень; lp — расстояние между крайними скребками в забое, м.
3.7. Расчет и конструирование узлов выгребного оборудования
3.7.1. Цепной скребковый орган
Скребковый орган выполняет две функции: разработку (экскавацию) балластного слоя и транспортирование разрушенного материала. Поэтому к нему предъявляются более высокие требования, чем к подобному органу, выполняющему только транспортирование материала. В частности, при расчетах элементов выгребного органа в первую очередь рассматривают силы, действующие при экскавации балласта.
Выгребной орган может иметь несколько составных частей: экскавационный элемент (резец), с помощью которого разрабатывается уплотненный слой балласта; грузонесущий элемент (скребок), который перемещает разрушенный материал; тяговый элемент (цепь), передающий движение предыдущим двум элементам.
Типом, конструкцией и параметрами составных частей рабочего органа определяется конструкция выгребного оборудования.
Тяговый элемент является важной частью выгребного рабочего органа. От его надежности зависит эффективность работы всего выгребного оборудования.
26
К основным параметрам тяговой цепи относятся: шаг звена Sц, разрушающая нагрузка Fp и масса одного метра цепи. При выборе шага цепи учитывают: способ крепления скребка к звену цепи и требуемое расстояние между скребками по условию заполнения межскребкового пространства материалом. Кроме того, необходимо учитывать эксплуатационные свойства цепи: с увеличением шага уменьшается число шарниров по длине рабочего органа и его масса и, следовательно, уменьшается износ цепи. Однако одновременно требуется увеличить радиусы ведущей звездочки и отклоняющих (направляющих) роликов; растут крутящий момент на ведущем валу и динамические нагрузки на цепь.
Типоразмер цепи выбирают по разрушающей нагрузке [3, 9]:
Fp = KпFр.н, |
(23) |
где Kп — коэффициент запаса прочности цепи (8…10); Fр.н — расчетная сила в набегающей ветви |
|
приводной звездочки тягового органа, кН. |
|
Сила Fр.н равна: |
|
Fр.н = Fmax + Fдин, |
(24) |
где Fmax ≈ 1,05(Fo + Fн); Fo — минимальная сила натяжения тягового органа (5,0…7,0 кН); Fн — сила в набегающей ветви тягового органа, кН; Fдин — динамическая сила в цепи, кН.
В предварительных расчетах Fн определяют по суммарной мощности на приводном валу рабочего органа и скорости тягового органа vск.
Динамическую силу рассчитывают по зависимости
|
|
60v2 qщ Lр.ц |
+ |
K |
q L |
|
|
||||
Fдин |
|
|
ск |
|
|
|
м с с |
, |
(25) |
||
Z |
2 |
|
g |
|
g |
||||||
|
|
|
Sц |
|
|
|
|
где Lр.ц — длина рабочей части тяговой цепи, м; Lс — общая длина цепи, м; qщ, qс — погонный вес вырезанного щебня и цепи со скребками, кН/м; Kм — коэффициент, учитывающий упругость цепи и ее длину (1,3…1,5); Z — число зубьев ведущей звездочки.
На эксплуатируемых машинах применяют одну тяговую цепь специального изготовления с боковым закреплением на ней скребков. Скребок делается заодно со звеном цепи. Это повышает устойчивость скребка при разработке и транспортировании щебня. Кроме того, для повышения устойчивости скребка в подпутной балке и в желобах предусмотрены направляющие для тяговой цепи.
При использовании тяговой цепи из прототипа (машины-аналога) с неизвестной разрушающей нагрузкой выполняют проверочный расчет ее элементов: пластин, валиков, втулок [3, 8].
В используемых в настоящее время рабочих органах разработка и перемещение балласта осуществляется одним элементом, т.е. экскавационный и грузонесущий органы совмещены. Это достигнуто посредством установки резцов на кромке скребка (комбинированные скребки).
При конструировании комбинированные скребки, в первую очередь, рассматривают как элементы, производящие разрушение щебеночного слоя. По форме они бывают прямоугольные или трапецеидальные и представляют собой единый элемент, состоящий из трех частей: корневой, основной лопатки и кромки с резцами. Изготавливают скребки из листовой стали или отливают заодно со звеном тяговой цепи. В первом случае скребки жестко соединяются со звеном цепи болтами или заклепками. Резцы применяют цилиндрической, конической, прямоугольной формы. Их количество зависит от высоты скребка и в среднем составляет 4…5 резцов. С целью эффективного разрушения уплотненного балласта и повышения устойчивости скребков резцы устанавливаются под углом τ = 40…45° к поперечному направлению движения скребков (рис. 12).
Цилиндрические и конические резцы имеют хвостовик, с помощью которого они соединяются с кромкой скребка и закрепляются с возможностью проворота вокруг их продольной оси. Такие резцы проворачиваются относительно гнезда крепления хвостовика, что снижает интенсивность их износа. С целью увеличения срока службы основной части скребка в гнездах закрепления хвостовиков устанавливают сменные втулки.
27
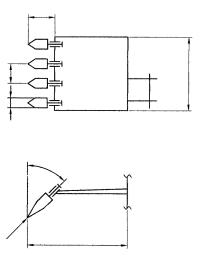
|
e |
|
ск |
о.р |
h |
b |
|
р |
|
d |
|
|
τ |
Fк.с |
|
|
bск |
Скребки разрабатывают по установленным ранее параметрам bск и hск, откорректированным после принятия размеров желоба и с учетом параметров тяговой цепи.
Ширину резцов (или их диаметр) dp и расстояние между ними bо.р назначают с учетом размеров частиц щебня dср (см. рис. 12):
dp = (1,2…1,6)dср;
bо.р = (2…2,5)dр.
Вылет резца относительно внешней кромки скребка принимают равным:
e = (1,5…2,0)dp.
Принятая конструкция основной части скребка и резцов корректируется при расчете их на прочность. Полагают, что общая сила сопротивления балласта копанию Fк.с действует на 1/3 всех
Рис. 12. Схема |
|
|
|
3F |
|
к расчету параметров скребка |
скребков nр, находящихся в забое F′ |
= |
к.с |
. Расчету подле- |
|
|
|||||
|
|
к.с |
|
n |
|
|
|
|
|
р |
|
жат сечения наибольшего нагружения основной части скребка и отдельного резца. Проверяют также крепление резца к лопатке скребка и основания скребка к звену тяговой цепи.
3.7.2. Восходящий и нисходящий желоба
Желоб можно разделить на три части: приемная часть с боковыми крыльями (оголовок), транспортирующая и разгрузочная. Разгрузочная часть шарнирно соединена с рамой привода выгребного органа, что позволяет перемещать желоба поперек оси пути. Рама привода, в свою очередь, шарнирно соединена с опорной стойкой выгребного оборудования. Шарнир на стойке позволяет перемещаться желобам в вертикальной плоскости. Таким образом, рама привода и корпус желоба
ввертикальной плоскости представляют собой единое целое. Применяются и другие способы соединения желобов с рамой привода выгребного органа и с опорой стойки.
Перемещение желобов осуществляется с помощью гидроцилиндров, которые присоединены к желобам в местах, близких к оголовку. Это позволяет уменьшить величины изгибающих моментов
вкорпусах желобов и производить манипулирование желобами с приложением наименьшей силы
вгидроцилиндрах.
Конструктивной особенностью выгребного органа и соответственно корпуса желоба является боковое крепление скребков к тяговой цепи, и они вместе находятся в корпусе желоба.
Исходными данными при конструировании желоба являются: конфигурация трассы выгребного органа, конфигурация и размеры тяговой цепи и скребков, предварительно установленные размеры рабочей части желоба (Вж.р, Нж.р, lж.н, lж.в).
Предварительно намечают контуры корпуса желоба и устанавливают размеры рабочей части желоба и направляющих путей (рис. 13). Затем выполняют прочностные расчеты и уточняют размеры поперечных сечений желоба. При установлении размеров частей желоба предусматривают установку защитных плит (футеровки).
28
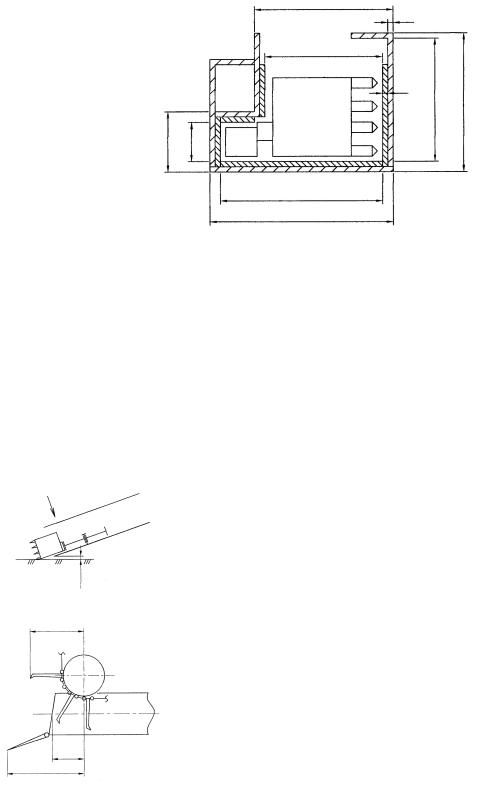
Вж
δж
Вж.р
δф
ж.н |
п |
Н |
Н |
Вж.ц
Вж.н
ж.р |
|
Н |
ж |
|
Н |
Рис. 13. Поперечное сечение желоба
Ширина основной части желоба на уровне расположения тяговой цепи равна:
Bж.ц = Bж.р + bц + δц ,
где Вж.р — ширина рабочей части желоба, м; bц — ширина звеньев цепи, м; δц — зазор между цепью и стенкой желоба, м (δц = = 10…15 мм).
Высота направляющего пути определяется:
Hп = hц + δц ,
где hц — высота звена цепи, м.
Габаритные размеры желоба по ширине и высоте составят: по верхней части скребков и выше
Bж = Вж.р + 2δж + 2δф ; |
Hж = Hж.р + 2δж + δф ; |
|
на уровне направляющего пути |
|
|
А |
|
Bж.н = Вж.ц + 2δж + 2δф ; |
|
Hж.н = Hп + 2δж + 2δф , |
|
h |
где δж — толщина стенок и днища желоба, м; δф — толщина листов |
|
футеровки, м. |
||
р |
|
|
|
По |
опыту проектирования предварительно можно принять δж = |
А= 8…10 мм; δф = 6…8 мм.
При разработке желобов особое внимание обращают на конструирование их приемной части (оголовка) (рис. 14). Оголовок разрабатывают с учетом присоединения к нему бокового крыла, подпутной балки, а также установки направляющего ролика тяговой цепи.
Основное назначение направляющих роликов — это изменение направления движения выгребного органа и уменьшение сил сопротивления его перемещению.
Ролик на нисходящем желобе должен обеспечить плавный переход звеньев цепи с направляющего пути желоба на направляющий путь подпутной балки. На восходящем желобе, наоборот, обеспечить плавный переход цепи с подпутной балки на направляющий путь желоба. Максимальный выход корпуса ролика внутрь желоба не должен превышать 25…35 мм.
При выборе места расположения ролика на восходящем желобе увязывают вылет скребков ac c вылетом подрезной кромки днища желоба aр.к. Скребки должны подрезать максимально возможную часть ширины балластной призмы, находящуюся перед желобом. Необходимо также увязать расположение резцов и подрезной кромки желоба по высоте hp.
В практике проектирования оборудования принимают
29
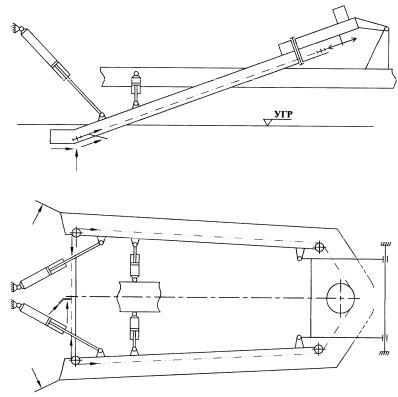
aр.к = (0,8…0,9) ac и |
hmin = (0,5…1,0) dср, |
|
p |
где dср — средний размер частицы щебня.
Подрезную кромку желоба делают со скосом с целью уменьшения сопротивления балласта резанию частью кромки, перед которой балласт не вырезан скребками, а также для эффективной подачи щебня боковым крылом на скребки.
Вылет бокового крыла aб.к также увязывают с вылетом скребков. С целью эффективного заполнения балластом межскребкового пространства принимают aб.к 2aс.
Подобную компоновку ролика делают и на нисходящем желобе.
Расположение отклоняющих роликов в верхней части желоба должно способствовать уменьшению разброса частиц щебня при разгрузке желоба и обеспечивать рациональный угол охвата ведущей звездочки тяговой цепью.
Разгрузочная часть желоба должна обеспечивать свободную разгрузку щебня в приемный бункер при любом рабочем положении желобов в горизонтальной и вертикальной плоскостях. Она разрабатывается с учетом ранее полученных параметров выгребного оборудования (п. 3.4).
При расчете на прочность рассматривают наиболее нагруженный желоб (восходящий) (рис. 15).
А
С
D
В
Fр′′.к Fот Fк′′F.с с.н
Fр.к
Fн′.н
Fс′.н
Fк.с
Fв.с
С
Fн′′.н В D
Fс′′.н |
А |
Fр.к |
|
Рис. 15. Схема для расчета желобов на прочность и выбора гидроцилиндров
В вертикальной плоскости остов желоба рассматривают как консольную балку на двух опорах. Одна из них — шарнир на опорной стойке рамы машины (точка А), вторая — узел присоединения к желобу гидроцилиндра изменения положения желоба в вертикальной плоскости (точка В). Желоб изгибается под действием сил Fк′′.с и сил отпора Fот на скребках, передаваемых через подпут-
ную балку на оголовки желобов.
В этой же плоскости желоб изгибается составляющей силой, действующей на его оголовок от бокового крыла Fp′′.к , и вследствие приложения силы в тяговой цепи Fс′′.н . Необходимо также учитывать силы тяжести рабочего органа и балласта, находящихся на желобе.
В горизонтальной плоскости рассматривают изгиб желоба под действием силы Fн.н в набегающей ветви тяговой цепи, предполагая, что изгибу не препятствует подпутная балка (например, она прогибается). Силы резания, действующие на боковые крылья, при этом не учитываются. Опорами желоба в этом случае являются шарниры соединения желоба с рамой привода вы-
30
гребного органа (точка С) и узел присоединения к желобу штока гидроцилиндра поперечного смещения желобов (точка D).
По эпюрам изгибающих моментов устанавливают наиболее опасное сечение желоба и проверяют его на прочность. При необходимости делают корректировки в размерах элементов желоба (футеровку в расчетах на прочность не учитывают).
При расчетах параметров желоба устанавливают величины и направление действия сил реакций в его опорах (точках В и D шарнирных соединений желоба), которые в дальнейшем используют для расчета элементов опор, шарниров желоба и выбора гидроцилиндров подъема и сдвига оголовка желоба.
Для расчета отклоняющих роликов определяют силы, действующие в набегающей и сбегающей ветвях тяговой цепи. Рассчитывают результирующую силу и подбирают подшипники. Затем с учетом конструкции и размеров элементов скребковой цепи, выбранных подшипников и желоба разрабатывают корпуса роликов, оси и опорные узлы осей.
Сила в тяговой цепи при выходе ее из забоя зависит в основном от сопротивления балласта копанию Fк.с и волочению Fв.с. Для предварительных расчетов силы в набегающей Fн.н и сбегающей Fс.н ветвях ролика на оголовке желоба (нижний ролик) принимают:
Fн.н = Fк′.с + Fв.с ; Fc.н ≈1,03Fн.н ,
где Fк′.с — проекция суммарной силы сопротивления балласта копанию на направление движения тяговой цепи, кН.
Силы в набегающей Fн.в и сбегающей Fс.в ветвях ролика в зоне разгрузки (верхний ролик) определяют по суммарной мощности Рс, затрачиваемой на привод выгребного органа, и скорости скребков vск с учетом силы натяжения тяговой цепи.
С помощью гидроцилиндров выполняют несколько манипуляций. Основные из них — это приведение желобов из транспортного положения в рабочее и наоборот, изменение величины заглубления рабочего оборудования в процессе вырезки балласта, а также надежное удержание заходной части желобов и, соответственно, подпутной балки на заданном уровне.
Для выбора гидроцилиндров подъема желобов принимают условие расчета: производится выглубление выгребного оборудования во время рабочего процесса (начальный момент выглубления); рассматривают наиболее нагруженный желоб. В этом случае на оголовок желоба и на его транспортирующую часть действуют те же самые силы, которые рассматривались при расчете желоба на прочность. Кроме того, необходимо учитывать силу тяжести остова желоба, а также вес рамы с приводом выгребного органа. Для расчета силы, необходимой на подъем желоба, рассматривают сумму моментов всех действующих на оборудование сил относительно шарнира стойки рамы машины (точка А, см. рис. 15).
Сила, которую должен развивать гидроцилиндр, определяют с учетом углов его наклона в вертикальной и горизонтальной плоскостях.
Для выбора гидроцилиндров смещения выгребного оборудования в поперечном направлении рассматривают условия расчета: во время рабочего процесса необходимо произвести смещение оборудования одним гидроцилиндром.
Требуемую силу на смещение оборудования определяют из уравнения моментов всех сил, действующих на выгребное оборудование, относительно верхних шарниров желобов (точка С, см. рис. 15).
Сопротивление повороту желобов оказывают силы: копания на скребках Fк.с; трения скребков и вырезанного балласта в забое Fв.с; сопротивления балласта смещению тыльной стороной одного из боковых крыльев (с полевой стороны пути); трения в верхних шарнирах желобов.
Силу, которую должен развивать гидроцилиндр, определяют с учетом его расположения в пространстве.
3.7.3. Привод выгребного органа
Основными элементами привода являются: двигатели, редуктор, ведущие звездочки (ведущие валы). Применяют различные сочетания компоновок этих элементов: двигатель, редуктор с ведущей звездочкой на выходном валу; два двигателя, редуктор с одной ведущей звездочкой на выходном валу; два двигателя, редуктор с двумя ведущими звездочками на выходных валах.
Выбор типа привода и место его размещения зависят от силы в тяговой цепи, требуемой мощности, конфигурации трассы выгребного органа, условий технического обслуживания и ограничений, связанных с необходимостью вписывания машины в габарит подвижного состава.
31
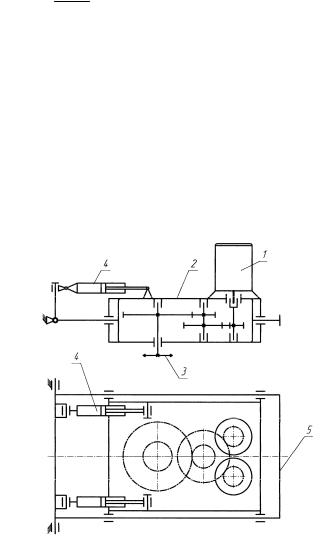
Привод, как правило, располагают в местах наибольшего нагружения тягового органа. Из схемы трассы движения рабочего органа видно, что таким местом является участок разгрузки желобов. Он также удобен и по соображениям вписывания рабочего оборудования в габарит подвижного состава (см. рис. 15).
Расчет параметров привода включает в себя: выбор электродвигателя или гидродвигателя, определение размеров ведущих звездочек, передаточного числа механизма, выбор редуктора. Исходными данными для расчета элементов привода являются: необходимая мощность Рдв привода и скорость движения скребков vск. При этом ранее установленную мощность Рдв (11) уточняют по зависимости
F v
Pдв = окηмск ,
где Fок — окружная сила на приводной звездочке, кН.
Для определения Fок используют метод обхода по контуру (трассе) [3, 8, 9].
При затратах мощности до 100 кВт используют электродвигатели трехфазные с короткозамкнутым ротором; более 100 кВт — двигатели с фазным ротором.
Гидродвигатели устанавливают аксиально-поршневого типа.
По известным параметрам двигателя, назначенным скорости скребков и диаметру ведущей звездочки определяют необходимое передаточное число между валом двигателя и выходным валом редуктора (валом звездочки). Составляют кинематическую схему привода и компонуют элементы привода (рис. 16). Редуктор привода либо рассчитывают, либо подбирают. Если применяют специальный редуктор, то при его разработке необходимо предусмотреть узлы присоединения к нему двигателя и механизма натяжения, а также места опирания редуктора на направляющие штанги.
Рис. 16. Схема привода и механизма натяжения выгребного органа: 1 — электродвигатель; 2 — редуктор; 3 — ведущая звездочка;
4 — гидроцилиндр; 5 — рама с направляющими штангами
При использовании типового редуктора его вместе с двигателем устанавливают на промежуточную раму с опиранием последней на направляющие штанги основной рамы привода.
При разработке редуктора или его выборе особое внимание необходимо обратить на выходной вал и на крепление к нему ведущей звездочки. Консольная часть вала испытывает значительные изгибные и скручивающие нагрузки. Это следует учитывать при расчете или проверке выходного вала на прочность и жесткость. Соединение звездочки с валом целесообразно осуществлять с помощью шлицев. По сравнению со шпоночным соединением они имеют высокую несущую способность и обеспечивают хорошее центрирование звездочки, что весьма важно при высокой скорости движения скребков.
32