
книги / Процессы и аппараты в технологии строительных материалов
..pdfУкладкабетоннойсмесискладываетсяизгидродинамического процесса течения смеси. Однако само по себе течение бетонной смеси в рассматриваемом случае происходить не может, поскольку для изготовления плит пустотного настила нужна жесткая смесь. Тиксотропные свойства бетонной смеси обеспечивают ее растекание в форме под воздействием механических колебаний – вибрации. Поэтому управление гидродинамическим процессом течения осуществляется с помощью механического вибрационного процесса, который и следует считать управляющим. Одновременно осуществляется уплотнение бетонной смеси, которая, обтекая пуансоны, заполняет все свободное пространство формы.
Тепловлажностная обработка изделия включает теплообменный и массообменный процессы. Управляющим является теплообменный процесс.
Извлечение изделия из формы – операция, слагающаяся из механических процессов, протекающих последовательно.
В данной операции механический процесс является управляющим.
Анализируя функциональную схему, мы не затрагивали вопрос об оборудовании – механизмах, аппаратах, установках, – используемом для осуществления тех или иных операций.
Более того, мы даже не рассматривали вопрос о том, каким образом мы собираемся осуществлять ту или иную операцию. В то же время нам известно, что каждая операция может быть осуществлена различными способами. Так, для изготовления арматурного каркаса можно применить несколько различных способов сварки: точечную сварку,сваркуподслоемфлюса,контактнуюилиспомощьюэлектрода и т.п. Смешивание компонентов бетонной смеси можно производить в смесителе периодического и непрерывного действия, используя принудительное и гравитационное смешивание. Можно назвать несколькоразличныхспособовформованияизделия:вибрационный, вибропрессование,штамповка,экструзия.
Существует несколько способов тепловлажностной обработки: нагревание глухим или острым паром, электропрогрев, высокочастотный нагрев, «холодный туман» и т.п.
Независимо от выбранного способа осуществления каждой операции функция ее остается неизменной, так же как и ее место
51
впоследовательностиопераций.Такимобразом,функциональная модельотвечаетнавопрос«чтосделать»дляполучениязаданных сырьевых материалов изделия с заданными свойствами. Чтобы ответить на вопрос «как сделать», необходимо разработать структурную модель технологической линии.
7.1.3. Структурная модель
Для разработки структурной модели производства необходимо определить, каким именно способом, с помощью какого оборудования и инструмента следует осуществлять разработанный технологический процесс. Как мы видели, практически каждую из операций можно осуществить различными способами, применяя разное оборудование. Задача проектировщика – определить, какой из способов осуществления каждой операции наиболее целесообразен в конкретных условиях проектирования. Другими словами, проектировщик должен определить наиболее оптимальный вариант осуществления разработанного технологического процесса.
Всвязи с этим встает вопрос о выборе критерия оптимальности.
Взависимости от цели проектируемого производства критерии оптимальности могут быть различными. Однако в промышленности строительных материалов, продукция которой в большинстве случаев является массовой, а критерии качества ее определены СНиПами и ГОСТами, критерием оптимальности производства чаще всего может служить себестоимость продукции при сохранении заданных параметров качества. Так обстоит дело при проектировании новых производств. При решении вопросов реконструкции существующих производств в качестве критерия оптимальности может выступать производительность при заданных критериях качества и сохранения себестоимости.Вцеломрядеслучаеввкачествекритерияоптимальности может быть выбрано качество изделий при заданной производительностии,возможно,себестоимостипродукции.
Таким образом, выбор критерия оптимальности зависит от конкретной цели проектирования. Сравнивая различные варианты структуры проектируемого производства по выбранному критерию оптимальности, проектировщик и должен решить вопрос о конкретной структурной схеме производства.
52
Врассмотренном в предыдущей главе примере целью проектирования является разработка новой технологической линии по производству плит пустотного настила. Условимся, что нам нужно получить плиты одного и того же типоразмера, а производительность проектируемой технологической линии должна обеспечить потребности строительных организаций региона в плитах этого типоразмера. Эта величина составляет несколько десятков тысяч штук плит в год. Такие условия подсказывают нам, что наиболее целесообразным для массового производства однотипных изделий является конвейерный тип технологии.
Этим определяется и структура производства: все операции должны быть расчленены в пространстве, но выполняться одновременно. Эта структура может иметь несколько вариантов
взависимости от имеющихся в распоряжении способов осуществления операций. Конвейер может быть вертикально замкнутым и горизонтально замкнутым. При непрерывном формовании изделий, например с помощью экструзии. Появится операция разрезкидеталей,котораявданномслучаезаменяетоперации,включающие распалубку изделий и подготовку форм, поскольку при экструзионном формовании потребность в формах отпадает.
Внашем примере изменение условий задачи может привести и к изменению схемы производства при тех же критериях оптимальности. Так, если будет поставлена задача производить плиты пустотного настила различных типоразмеров, более целесообразной может оказаться не конвейерная, а агрегатно-поточная схема производства. Эта схема более гибкая, позволяет при небольшой переналадке оборудования производить различные изделия на одной и той же технологической линии. В нашем случае при аг- регатно-поточном производстве переход с выпуска плит одного типоразмера на другой потребует лишь переналадки форм.
Вслучае производства массивных изделий, например длинномерных ферм, изготовление которых агрегатно-поточным способом потребовало бы мощного и энергоемкого подъемно-транс- портного оборудования, оптимальным станет стендовый способ организации технологического процесса. При этом способе большая часть операций совмещена в пространстве, а выполняются они последовательно одна за другой, т.е. расчленены во времени.
53
Разумеется,структурнаямодельпроизводстваможетизмениться приизмененииспособаосуществлениялюбойизопераций.
Целесообразность выбора способа осуществления операций должна определяться теми же критериями оптимальности, что и при решении вопроса о схеме всей технологической линии. Так, независимо от структурной схемы всей технологической линии, могут быть разработаны различные схемы приготовления бетонной смеси. Выбор этой схемы также диктуется соображениями оптимальности технологии.
7.2. Технологические операции и элементарные процессы
7.2.1. Измельчение
Измельчение(дроблениеипомол)складываетсятолькоизмеханических процессов. Нагреванием за счет трения в большинстве случаев можно пренебречь. Исключением из этого правила является помол минерального сырья, включающего двуводный гипс, последний за счет выделяющегося при помоле тепла может подвергнуться дегидратации с переходом в полуводный гипс. В производстве портландцемента такая ситуация может привести к ложному схватыванию продукции. Но при различных видах осуществляются одновременно несколько элементарных механических процессов – удар, раскалывание, истирание и раздавливание. Эффективность измельчения зависит от правильного выбора совокупности этих элементарных процессов применительно
ксвойствам измельчаемого материала.
Внастоящее время все большее число исследователей считают, что наиболее производительным аппаратом для тонкого измельчения – помола – являются шаровые мельницы. Они обеспечивают заданную производительность при сравнительно небольших константах и энергетических затратах, обеспечивая одновременно сравнительновысокоекачествоизмельченногопродукта.Однакоизмельчение в шаровых мельницах, как и в других существующих ныне измельчительных аппаратах, происходит за счет сжатия материала. Экспериментально установлено, что энергия, затрачиваемая на раз-
54
рушение материала сжимающими усилиями, примерно в 1000 раз больше,чемэнергия,необходимаядляразрушениярастягивающими усилиями (Rсж >> Rраст). При этом только 0,1 % энергии используется дляразрушенияматериала,а99,9%–превращаетсявтепло.Нопока не существует никаких предпосылок для конструирования аппаратов, которые использовали бы принцип растяжения для разрушения материалов. Поэтому пока увеличение доли энергии, затрачиваемой непосредственнонаразрушение,следуетискатьневизменениипринципаработыаппаратов,авоптимальномрежимеизмельчения.
Для мельниц наиболее существенными факторами, влияющими на производительность, являются коэффициент заполнения К, скорость вращения – число оборотов в минуту n, и тонкость помола материала а. В общем виде связь между этими величинами и производительностьюаппаратаможетбытьвыраженаввидефункции:
Vс = f (К, n, a). |
(7.1) |
Относительно конкретного вида этой зависимости имеются немногочисленные и весьма противоречивые данные. Так, на одних предприятиях производительность возрастала с уменьшением числа оборотов,надругих–возрасталасувеличениемихчисла.Важнейшей задачейявляетсяисследованиеэтойзависимостииразработкасистемы автоматического управления помолом для обеспечения его стабильного оптимального режима. В этой работе наиболее достоверные результаты могут быть получены при моделировании процесса помолаисамихмельницнаосноветеорииподобия.
7.2.2.Перемешивание
7.2.2.1.аппараты с мешалками – смесители
Перемешивание – это соединение объемов различных веществ с целью получения однородной смеси (гомогенизация). Для смешивания применяются аппараты с мешалками.
Существуют следующие типы мешалок:
1)Турбинные (с прямыми загнутыми, наклонными плоскостями);
2)Пропеллерные (винт вентилятора);
3)Лопастные;
55
4)Якорные;
5)Рамные;
6)Шнековые;
7)Мешалки, обеспечивающие высокое напряжение сдвига (диск, диск с зубцами и т.д.);
8)Скребковые.
Кроме того, выделяют смесители с отражающими перегородками и без них. Для смешивания зернистых материалов существуют смесители следующих типов:
1) смесители с вращающейся камерой: а) горизонтальные барабанные, б) наклонные барабанные, в) биконические, г) бицилиндрические,
д) V–образные (непрерывного действия);
2)Смесители с неподвижной камерой: а) с мешалкой шнекового типа, б) с лопастными мешалками, в) бегуны, г) с планетарными мешалками,
3)Смесители с вращающейся камерой и мешалкой.
Выбор смесительного аппарата зависит от свойств смешиваемых материалов.
Смешивание – сложная операция, включающая элементарные процессы механического перемещения материала, гидромеханичес- киепроцессыипроцессымассообмена,аврядеслучаев–итеплооб- мена(перемешиваниеснагреванием,паропрогревомит.п.).
7.2.2.2. Гидродинамика смешивания
Скорость жидкости в любой точке можно разложить на три составляющих: радиальную wr, осевую wz и тангенциальную wt (т.е. в цилиндрической системе координат).
wz изменяется при изменении расстояния от лопастей в вертикальном направлении. wt изменяется при изменении и того и другого расстояния. Циркуляция жидкости в аппарате с мешалкой может быть охарактеризована окружным (тангенциальным) и радиально-осевым потоками.
56
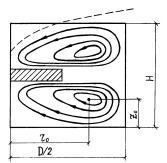
Окружной поток характеризуется объемной производительностью (расходом Vс через радиальное сечение).
Vсc H∫ |
∫R wt drdz , |
(7.2) |
0 |
0 |
|
где Н – высота жидкости в сосуде, R = D/2 – внутренний радиус сосуда, drdz – элементарная площадка в радиальном сечении.
Второй вид циркуляции наиболее существенен для смешивания, т.к., если эта циркуляция отсутствует, смешивание не будет происходить. Этот вид циркуляции может быть оценен при помощи расхода через горизонтальное сечение мешалки Vс.
Vc 22∫π ∫R wz rdz2ϕdz ,
0 r0
где r и φ – координаты в цилиндрической системе координат; r0 – координата точки, в которой циркуляции отсутствует.
Множитель 2 характеризует симметрию радиально-осевой циркуляции относительно лопастей мешалки.
Этот вид циркуляции связан с насосным эффектом мешалки, который заключается в перемещении жидкости вдоль оси мешалки и характеризуется расходом Vp через условную контрольную поверхность dF1 и dF2:
(7.3)
Рис. 7. 1. Схема циркуляции в аппаратах с мешалками
Vp ∫∫w +cosαdF1 = ∫∫w −cosαdF2 , |
(7.4) |
|
F1 |
F2 |
|
гдеw+ иw– –скорости,направленныевнутрьобъема,описываемо- го мешалкой и наружу от него; α – угол между вектором скорости и нормалью к контрольной поверхности в рассматриваемом месте. F1 и F2 – контрольные поверхности, через которые жидкость течет внутрь объема и наружу от него.
Установлена зависимость между расходом радиально-осевой циркуляции и насосным эффектом:
57
Vс2 ≈ 2Vр*.
Величина насосного эффекта может быть замерена экспериментально. Для смесей с твердой фазой такие замеры исключительно сложны,поэтомунасосныйэффектвычисляют.Однакорешениедифференциальных уравнений типа (7.2) – (7.4) не может быть получено аналитически.Поэтомудлявычислениянасосногоэффектаиспользуют метод анализа размерностей. В простейшем случае, когда можно пренебречьвязкостьюисилойтяжести,справедливазависимость
Vp* = f (n, d, ρ).
В соответствии с принципом анализа размерностей
Vp* = Anadb ρе.
Подставив размерности, получим
|
м3 |
|
|
1 |
a |
b кг e |
. |
||
|
с |
|
= A |
[м]b |
м |
3 |
|||
|
|
|
с |
|
|
|
|
(7.5)
(7.6)
(7.7)
Поскольку функция должна быть однородной, т.е. иметь одинаковуюразмерностьобеихчастей,заключаем,чтоа=1,b =3,е=0.
Подставив в (7.6), имеем
V |
p |
= And3 |
(критерий Стренка). |
(7.8) |
|
|
|
|
Безразмерный модуль Vp*/nd 3 называется коэффициентом насосного эффекта Lр. Для подобия мешалок необходимо, чтобы Lp1 и Lp2 были равны.
Если учесть силу вязкости и силу тяжести, а также некоторые размеры аппарата (емкости), которые могут оказать влияние на насосный эффект, то
Vp* = f (n, d, ρ, μ, g, l1, l2, ...). |
(7.9) |
После преобразования методом анализа размерностей имеем
Vp * |
nd3с |
|
n2d |
l |
|
l |
|
|
|
|||
|
|
|
= f |
|
, |
|
, 1 |
, |
|
2 |
, ... . |
(7.10) |
nd |
3 |
|
µ |
g |
|
|||||||
|
|
|
|
d |
|
d |
|
|
В (7.10)
58
wlρ = nd 2ρ = Re,
µ µ
(т.к. ndπ = w – скорость, π, как постоянная величина, исключает-
ся), а d = l. |
w2 |
= |
n2d |
|
= Fr . |
|
|
||||
Поэтому |
gl |
g |
|
|
|
||||||
|
|
|
|
|
|
|
|
|
|||
|
|
|
l |
|
l |
|
|
|
|
||
|
Lp = f |
|
|
2 |
|
|
|||||
|
Re,Fr, |
1 |
, |
|
,L |
. |
(7.11) |
||||
|
d |
d |
|||||||||
|
|
|
|
|
|
|
|
Таким же способом можной найти зависимости для расчета времени перемешивания смеси, расчитать необходимую скорость для получения однородной суспензии, эмульсии, мощности мешалки (и следовательно, мощность двигателя).
Мощность N, расходуемая на перемешивание, – это энергия, передаваемаяперемешиваемойсистемойвединицувремениспомощью мешалки и затрачиваемая на оборудование конвективных потоков (вихрей).Этаэнергиявконечномсчетепереходитвтеплоту.
Из-за потерь в редукторе и других системах передачи мощность двигателя Nд должна быть больше мощности N.
Nд = |
N |
(7.12) |
|
КПДp |
|||
|
где кпд – кпд редуктора.
Для расчета величины N следует учесть все факторы, влияющие на перемешивание:
Или |
|
|
|
N = f (n, ρμ, g, dz). |
|
|
|
|
|
N = Anaρbμcgedf. |
|
(7.13) |
|
|
|
|
|
|
||
Подсчитав размерности, получим |
|
|
||||
|
кг м2 |
b+c −3b−c+e+ f a−b−c−2e |
(7.14) |
|||
|
с |
3 |
|
=[кг]b+c[[мм]]–3b–c+e+f[[v]м |
a–b–c–2e. |
|
|
|
|
|
|
|
|
Отсюда |
|
|
|
1 = b + c, |
|
|
|
|
|
|
2 = –3b – c + e + f, |
|
(7.15) |
|
|
|
|
–3 = – a – c – 2e. |
|
|
59
Выразим все показатели степени через с и е, тогда
а = 3 – 2е – с, |
|
b = 1 – c, |
(7.16) |
f = 5 – 2c – e. |
|
После подстановки в (7.13), имеем
N = C n3–2e–c3–2e–cρ1–cμegd+5–2c–e
или |
|
|
|
5 |
|
−c |
2 |
|
−e |
||
|
N |
|
|
ρ |
d |
||||||
|
|
= A nd |
|
|
n |
|
|||||
|
3 5 |
ρ |
|
|
|
||||||
|
n d |
|
µ |
|
|
|
g |
|
N/n3 d5ρ – модифицированный критерий Эйлера; nd2 ρ/μ – модифицированный критерий Рейнольдса; n2d/g – модифицированный критерий Фруда.
Поэтому Eu = ARe–cFr–e, или
Eu = ARebFre. |
(7.17) |
Это критериальное уравнение, описывающее мощность для различных групп геометрически подобных мешалок.
Вмомент пуска необходимо преодолеть силы инерции смеси
ивращающихся частей аппарата (механические характеристики процесса), и мощность мешалки может превысить рассчитанную по уравнению (7.17). Эта мощность называется пусковой мощностью. В связи с этим возникает вопрос, нужно ли предусматривать резервную мощность, чтобы избежать перегрузок двигателя. На этот счет нет единого мнения. Ряд авторов считают, что этот резерв мощности необходим. Другие полагают, что современные электродвигатели вполне могут выдержать кратковременные перегрузки, поэтому резерв мощности не нужен.
Очевидно,здесьнадоисходитьизусловийконкретногослучая. Если обозначить время от момента включения двигателя до момента, когда будет достигнута постоянная скорость вращения мешалки, как время пуска τ, то может возникнуть два случая. Первый случай, если допустимое время перегрузки двигате-
ля τg больше времени пуска или равно ему τg > τ.
Вэтом случае резервная мощность не нужна.
60