
книги / Обследование технического состояния металлоконструкций и механизмов подъемно-транспортных машин
..pdfпиллярным проникающим составом (например, производства ФРГ в виде аэрозоля красного цвета). Через 3–5 минут поверхность протирается насухо (если используется керосин) или промывается водой (используется капиллярный состав), после чего она покрывается слоем масла (в первом случае) или белым аэрозольным составом (во втором случае) и обстукивается молотком массой не менее 0,5 кг. При наличии трещин через несколько минут вдоль нее проступает темная полоса.
При керосиновой пробе лучше применять не чистый керосин, а состав, на 70 % состоящий из керосина, на 30 % – из трансформаторного масла и добавок красителя (10 г красной краски типа «Судак» № 111 на 1 л жидкости).
11.2. Поиск дефектов магнитографическим методом
Сущность этого метода заключается в намагничивании контролируемого участка сварного шва и околошовной зоны с одновременной записью магнитного поля на магнитную ленту и последующим считыванием полученной информации с нее специальными воспроизводящими устройствами магнитографических дефектоскопов, оснащенных вторичными преобразователями в виде феррозондов или индукционных головок. Этот сигнал после преобразования поступает на экран электроннолучевой трубки.
Технология магнитографического контроля включает следующие операции (ГОСТ 25225):
1.Осмотр и подготовку поверхности контролируемого изделия. При этом с поверхности контролируемых швов должны быть удалены остатки шлака, брызги расплавленного металла, грязь и т.д.
2.Наложение на шов отрезка магнитной ленты. Перед началом работы магнитная лента должна быть подвергнута размагничиванию. Прижим к шву плоских изделий производят специальной эластичной «подушкой».
41
3.Намагничивание контролируемого изделия при оптимальном режиме в зависимости от типа намагничивающего устройства, толщины сварного шва и его магнитных свойств.
4.Расшифровка результатов контроля. Она состоит в том, что магнитную ленту устанавливают в считывающее устройство дефектоскопа и по сигналам на экранах дефектоскопа выявляют дефекты. Перед просмотром магнитной ленты дефектоскоп настраивают по эталонной магнитограмме с записью магнитного поля дефекта минимально допустимых размеров. Во время воспроизведения регистрируются все дефекты, амплитуда которых превышает максимально допустимую от эталонного импульса величину.
Магнитографический метод в основном применяют для контроля стыковых швов, выполненных сваркой пламенем. Этим методом можно контролировать сварные изделия и конструкции толщиной от 20–25 мм. В качестве дефектоскопа рекомендуется МД-9 с импульсной индикацией и МД-11 с видимым изображением. Наиболее совершенные дефектоскопы – МДУ2У, МД-10ИМ, ГК-1 – имеют двойную индикацию.
Выпускаются два типоразмера передвижных намагничивающих устройств (ПНУ): ПНУ-М1; ПНУ-М2. В полевых условиях для обследования металлоконструкций применяют переносные автономные станции типа СПП-1, СПА-1.
11.3. Обнаружение дефектов вихретоковым методом
Вихретоковые методы контроля (ВМК) основаны на регистрации изменения поля вихревых токов, наводимых в поверхностном слое изделия. Методами вихревых токов обнаруживаются только поверхностные и подповерхностные (на глубине 2–3 мм) дефекты. Рекомендуются для выявления трещин, расслоений, раковин, непроваров и других повреждений на ровных поверхностях металла, например, в конструкции нижней рамы, поворотной рамы, балок-аутригеров.
42
Суть метода заключается в том, что при наличии трещин, раковин, расслоений или других дефектов стрелка прибора показывает резкое падение вихревого тока в металле.
При использовании ВМК следует учитывать, что электропроводность отдельных зон шва и околошовной зоны значительно меняется и возможны большие потери при выявлении дефектов сварки. ВМК может быть использован для фазового
иструктурного анализа указанных зон.
Вкачестве отечественных дефектоскопов для проведения вихревой дефектоскопии рекомендуются ВД-89Н, ВИТ-2, ВИТ-3, а также другие дефектоскопы, обеспечивающие надежность контроля качества.
Методика контроля заключается в следующем:
– внешний осмотр изделия и устранение наружных дефектов, мешающих проведению контроля;
– установка полезадающей системы на контролируемый участок и пропускание тока через возбуждающую катушку;
–сканирование датчика и регистрирующих приборов вдоль поверхности контролируемого объекта;
–расшифровка результатов контроля и оценка качества изделия.
На результаты исследования методом вихревого контроля значительное влияние оказывает зазор между датчиком и контролируемой поверхностью. Максимальный допустимый зазор 2 мм.
11.4. Метод ультразвуковой дефектоскопии
Ультразвуковая дефектоскопия предназначена для обнаружения дефектов (нарушения сплошности и однородности материалов) в полуфабрикатах, готовых изделиях и сварных соединениях, для измерения глубин и координат их залегания, измерения толщин за счет изменения скорости распространения
43
и затухания ультразвуковых колебаний в материале. В качестве отечественных ультразвуковых дефектоскопов используются УД2В-П12, УД2В-П45.
12. ОБСЛЕДОВАНИЕ КАНАТНО-БЛОЧНЫХ СИСТЕМ, МЕХАНИЗМОВ И ДРУГИХ УЗЛОВ
Работы по проверке состояния механизмов, канатноблочных систем и других узлов должны включать внешний осмотр с целью анализа общего состояния, работоспособности и необходимости проведения дальнейших измерений, а также проведение необходимых измерений.
Перед проведением обследования механизмы и другие подвергаемые осмотру узлы грузоподъемной машины должны быть очищены от грязи, коррозии, снега, избытка влаги и смазки.
При внешнем осмотре выявляют:
–общее состояние всех механизмов и наличие повреждений их отдельных узлов и деталей;
–наличие или отсутствие деформаций, коррозии и необходимость их устранения;
–наличие или отсутствие вытекания смазки из редукторов;
–качество затяжки элементов крепления механизмов;
–соответствие регулировки узлов механизмов (например, тормозов механизма передвижения и т.п.) требованиям эксплуатационной и нормативной документации.
Особое внимание необходимо обращать на следующие возможные дефекты:
–трещины в рамах, корпусах редукторов или рычагах тормозов, в тормозных шкивах и т.п. узлах;
–поломку тормозных пружин;
–износ зубчатых зацеплений;
–износ ходовых колес;
–выработку (износ) шарнирных соединений, тормозных шкивов, обкладок тормозов, дорожек качения ОПУ, крюка и т.п.;
44
–ослабление болтовых соединений;
–нарушение соосности валов, соединенных зубчатой или втулочно-пальцевой муфтой;
–неудовлетворительную балансировку тормозного шкива или барабана;
–износ и разрушение уплотнений.
Для блоков канатной системы характерны следующие повреждения, которые могут привести к обрыву или перетиранию каната:
–трещины или сколы реборды;
–износ по ручью или реборде блока;
–отсутствие смазочного материала в подшипниках и как следствие – их поломка, стопорение блока.
Для оценки норм браковки канатов по числу оборванных проволок рекомендуется пользоваться таблицей [1]. Наиболее опасными местами по обрыву проволок являются те участки каната, которые за период работы проходят по большому числу блоков.
Кроме того, следует контролировать места крепления каната на барабанах и на конструкциях крана.
Опасными местами, где может появиться коррозия, являются те, в которых скапливается влага и где канат редко или совсем не перемещается по блокам (например, на нижних обоймах стреловых полиспастов кранов-погрузчиков, кранов с балочной
стрелой или на уравнительных блоках стрелового расчала). В этих случаях канат бракуется раз в 5 лет независимо от числа обрывов проволок.
Необходимость разборки механизмов при осмотре определяет комиссия.
Повреждения, близкие к предельным, которые были выявлены в результате внешнего осмотра, должны быть измерены. Результат измерения, например по износу, сравнивают либо с размером, где износ практически отсутствует, либо с размером, указанным в чертеже.
45
Необходимость измерить износ и степень выкрашивания зубьев шестерен и колес зубчатых передач редукторов может быть определена по появлению повышенного шума при работе механизма и / или повышении температуры нагрева корпуса (последнее в ряде случаев может свидетельствовать и об отсутствии смазки).
Проверка наличия смазки в редукторах проверяется с помощью щупа, маслоуказательных пробок, глазков либо проверкой через люк в крышке. Уровень масла должен находиться между верхней и нижней отметками маслоуказателя.
Основные характерные повреждения и дефекты механизмов канатно-блочных систем, других узлов и конкретные места их возможного появления приведены в прил. 6.
13. ПРОВЕРКА ОПОРНО-ПОВОРОТНОГО УСТРОЙСТВА КРАНА
Измерение распространяется на краны как с поворотной, так и неповоротной башней и предназначено для определения перекоса (суммарного люфта или рабочего зазора) шариковой или роликовой поворотной опоры (опорно-поворотного устройства, или ОПУ) при проведении обследования или испытаниях крана в рабочем состоянии. Методика может использоваться при измерениях перекоса и других кранов.
Измерение перекоса ОПУ проводится для решения вопроса о возможности дальнейшей эксплуатации опоры. Признаком предельного состояния, при котором опора не допускается к дальнейшей эксплуатации, является перекос (за счет технологического люфта опоры и износа ее дорожек катания) более 0,004. Измерения проводят на действующем кране, находящемся в рабочем состоянии, как в летний, так и в зимний период при температуре воздуха не ниже –20 °С при ветре не более 10 м/с. Положение поворотной части крана по отношению к неповоротной (в плане) – произвольное. Перед проведением измерений
46
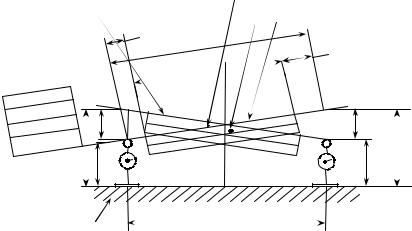
необходимо убедиться, что все болты крепления опоры имеются в наличии и затянуты моментом, отвечающим эксплуатационной документации.
Для измерения величины перекоса φ опоры производятся замеры линейных перемещений противоположных точек А и Б полуобойм (рис. 10) опоры, жестко закрепленных к поворотной части крана, относительно его венца, закрепленного к неповоротной части. Линейные перемещения определяются по разнице измерений при ненагруженном кране и с номинальной нагрузкой на крюке.
Положение полуобойм с номинальным грузом на крюке
l
» |
аi |
«0 » + «аi |
«0 » |
|
|
Ходовая рама или неповоротная рама башни
Положение полу-
обойм без груза на крюкеПоворотная
ОПУ платформа (ра-
l
l
Д
Б
l
бi
бi |
«0 » |
«0 » - |
|
Рис. 10. Схема для измерения линейных перемещений полуобойм ОПУ кранов: Д – диаметр полуобойм; l – расстояние от полуобоймы до оси ножки индикатора; l – расстояние между ножками индикаторов; А и Б – линейные перемещения (по шкале индикаторов); «0» – установочная высота индикатора
Перемещения в каждой точке измеряются в вертикальной плоскости, проходящей через ось симметрии стрелы-противо-
47
веса с помощью двух индикаторов часового типа или иным способом.
Индикаторы устанавливаются неподвижно на неповоротной части крана на штативах по оси симметрии: поворотная платформа (противовесная консоль) – стрела, на одинаковом расстоянии от центра вращения опоры или внешней вертикальной поверхности полуобойм опоры.
Места под установку оснований штативов индикаторов и места упора их наконечников должны быть очищены от грязи. Ножки индикаторов должны быть расположены вертикально, наконечниками вверх, с упором их в нижний лист поворотной части.
Перемещения определяются как среднеарифметическая величина по показаниям индикаторов при трехкратном подъемеопускании груза. Расстояние l, мм, между точками, где производятся замеры,
l = Д + 2 |
l, |
(3) |
где Д – внешний диаметр полуобойм, мм; |
l – расстояние от по- |
|
луобойм до оси ножки индикатора, мм. |
|
|
Измерение расстояний l, Д и |
l производят с помощью ме- |
таллической линейки, рулетки, штангенциркуля и угольника. Проще измерять расстояние l с учетом внешнего диаметра Д колец полуобойм опоры и двух расстояний l от наружной вертикальной стенки полуобойм до оси ножки индикатора. Расстояние l следует выбирать минимальным, необходимым для установки индикатора.
Установку индикаторов рекомендуется проводить после того, как предназначенный для подъема груз уложен в исходное положение для подъема и застроплен. При этом ножка заднего (со стороны противовеса) индикатора должна быть при установке утоплена примерно на 5 мм, переднего (со стороны стрелы) – на 1–2 мм, а нулевое деление «0» поворотной шкалы индикатора совмещено с его стрелкой.
48
Измерения линейных перемещений аi, бi проводят при подъеме груза на высоту 100–200 мм и опускании его до ослабления стропов.
Перекос φ определяется по формуле
φ = |
А Б |
= 0,004, |
(4) |
|
l |
|
|
где А и Б – среднеарифметические результаты |
измерений |
(аi и бi) перемещений по шкале индикатора соответственно со стороны противовеса и стрелы при подъеме номинального груза.
14.ОБСЛЕДОВАНИЕ МЕХАНИЗМОВ ЭЛЕКТРО-
ИГИДРООБОРУДОВАНИЯ
14.1. Обследование состояния электрооборудования
Проверка состояния электрооборудования должна включать следующее:
–внешний осмотр электрооборудования и проведение необходимых для анализа работоспособности измерений (проверок);
–оценку соответствия установленного электрооборудования эксплуатационной документации;
–контрольную проверку работоспособности электрооборудования.
Внешний осмотр электрооборудования должен проводиться одновременно с проверкой действия элементов электрооборудования при имитации работы вручную, осуществляемой для контроля отсутствия механических заеданий. Внешний осмотр следует проводить последовательно по отдельным узлам электрооборудования, при этом необходимо проверить:
–электродвигатели;
49
–панели управления;
–пускорегулирующие резисторы;
–пульт управления и монтажный пульт;
–тормозные электромагниты и электродвигатели электрогидравлических толкателей;
–кабели, провода, элементы и т.д.
Перечень работ, выполняемых при этом, зависит от конкретного типа грузоподъемной машины, типа электропривода и рода питающего электрического тока.
Контроль за работоспособностью электрооборудования заключается в проверке функционирования всех механизмов согласно электросхеме, в том числе плавности переключения аппаратов с фиксацией их по позициям, обеспечение плавности пуска и торможения механизмов, безотказности включениявыключения электросистем.
При осмотре электродвигателей проверяют:
–отсутствие механических повреждений (поломки мест крепления, нарушения целостности клеммных коробок и др.);
–отсутствие влаги внутри двигателя (из-за конденсата или недостаточного уплотнения на клеммных коробках);
–исправность щеток, коллекторов или контактных колец (отсутствие заеданий щеток, нагара на щетках и их частичного или полного разрушения, отсутствие значительного почернения коллектора или контактных колец);
–исправность контактов реле и пускателей (износ главных
ивспомогательных контактов пускателей и реле не должен превышать 50 % первоначальной толщины контакта).
При осмотре тормозных электромагнитов и электродвигателей электрогидравлического толкателя проверяют:
–отсутствие заеданий и перекосов магнитной системы;
–надежность крепления электромагнитов;
–исправность катушек электромагнитов и обмоток электрогидротолкателя путем измерения их электрического сопротивления (в случае длительного перерыва в работе крана).
50