
книги / Наноструктурные стали
..pdfПри ИТЦО до 900 и 1000 ºС наблюдается тенденция к росту предела текучести (σ0,2) при увеличении количества циклов, что связано с диспергированием структуры на первых циклах, увеличением однородности зеренной структуры аустенита и изменением разориентировок аустенитных зерен при последующих [22].
Таким образом, повышение характеристик прочности при темоциклировании до 900 и 1000 ºС является следствием реализации зернограничного механизма упрочнения. Наилучший комплекс характеристик получен после 5 циклов на 900 ºС: σ0,2 = 1250 МПа,
σв = 1410 МПа, HRC = 40, δ = 14 %, ψ = 62 %.
Испытания на ударную вязкость проводили на маятниковом копре МК-30. Значения ударной вязкости, полученные при испытаниях, приведены в табл. 2.2. Фрактографические исследования проводили на изломах образцов, подвергнутых различным режимам ИТЦО в области старта трещины, при помощи растрового электронного микроскопа Carl Zeiss EVO50.
Таблица 2.2
Результаты испытаний на ударную вязкость образцов из стали 12Х2Г2НМФТ после различных режимов ИТЦО
|
|
|
|
|
|
Температура, ºС |
Средние значения ударной вязкости (КСТ), МДж/м2 |
||||
1 цикл |
3 цикла |
5 циклов |
7 циклов |
||
|
|||||
800 |
0,71 |
0,83 |
0,72 |
0,80 |
|
900 |
0,65 |
0,67 |
0,81 |
– |
|
1000 |
0,72 |
0,65 |
0,79 |
– |
Примечание. Исходное значение КСТ = 0,40 МДж/м2.
В исходном состоянии ударная вязкость стали 0,40 Дж/м2. Поверхность разрушения после испытаний на КСТ представлена на рис. 2.8. Микромеханизмом разрушения в этом случае является квазискол. Около 60 % излома занимают фасетки транскристаллитного скола с развитой субструктурой поверхности, и 40 % – ямки. Местами встречаются ямки-конусы.
Поверхности разрушения после испытаний на КСТ образцов, подвергнутых термоциклированию при 800 ºС, представлены на рис. 2.9. Значения ударной вязкости при термоциклировании при
31
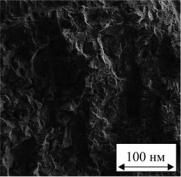
Рис. 2.8. Поверхность разрушения стали 12Х2Г2НМФТ в исходном состоянии (закалка 920 ºС в воду, выдержка 20 мин) после испытаний на ударную вязкость
800 ºС изменяются немонотонно – наибольший прирост ударной вязкости наблюдается при циклировании на 3 цикла, она составила 0,83 МДж/м2, а наименьшие значения – при циклировании на 1 цикл, 0,71 МДж/м2. Микромеханизмом разрушения в этом случае является квазискол. В изломе образцов, подвергнутых термоциклированию при 800 ºС, 1 цикл (рис. 2.9, а), присутствуют преимущественно фасетки транскристаллитного скола с развитой субструктурой поверхности, что является следствием пакетно-реечной фрагментации при закалке, так как границы реек и пакетов являются локальными барьерами вязкости при развитии трещины. Исследование поверхности разрушения образцов после циклирования при 800 ºС, 7 циклов, где вязкость достигает наибольшего значения в этом режиме, позволяет говорить о преимущественно вязком характере разрушения – около 60 % поверхности занимают ямки и ямки-конусы, что, по-видимому, связано с диспергированием структуры после ИТЦО.
Поверхность разрушения образцов, подвергнутых термоциклированию при 900 и 1000 ºС, после испытаний на КСТ представлена на рис. 2.10. После первого цикла ИТЦО наблюдается смешанный микромеханизм разрушения – квазискол и вязкий, т.е. на поверхности разрушения встречаются фасетки транскристаллитного скола при циклировании при 900 и 1000 ºС, 1 цикл, а основную
32
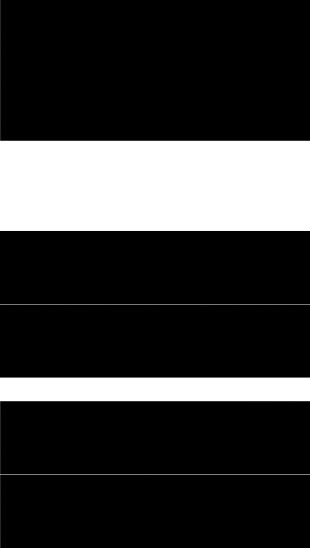
а б
Рис. 2.9. Поверхность разрушения стали 12Х2Г2НМФТ после испытаний на ударную вязкость (КСТ):
а – ИТЦО на 800 ºС, 1 цикл; б – ИТЦО при 800 ºС, 7 циклов
а |
б |
в г
Рис. 2.10. Поверхность разрушения стали 12Х2Г2НМФТ после испытаний на ударную вязкость (КСТ): а – ИТЦО при 900 ºС, 1 цикл; б – ИТЦО при 900 ºС, 5 циклов; в – ИТЦО при 1000 ºС, 1 цикл; г – ИТЦО при 1000 ºС, 5 циклов
33
площадь поверхности разрушения занимают ямки. Ударная вязкость при термоциклировании при 900 и 1000 ºС принимает наименьшие значения после одного цикла (0,72 и 0,65 МДж/м2), что объясняется наличием хрупких мест в изломе. Наибольшие значения ударной вязкости наблюдаются после пятикратного циклирования и составляют 0,79–0,81 МДж/м2, что сопровождается отсутствием участков хрупкого разрушения и преобладанием ямокконусов в изломе.
Интенсивная термоциклическая обработка по проведенным режимам во всех случаях приводит к повышению ударной вязкости исследуемой стали в два раза по сравнению с ударной вязкостью
висходном состоянии.
2.2.Интенсивная термоциклическая обработка конструкционных сталей в исходно холоднодеформированном состоянии методом радиальной ковки
Вподразд. 2.1 показана целесообразность измельчения структуры исходно закаленных системно легированных низкоуглеродистых сталей методами интенсивной термоциклической обработки. При этом эффективным способом измельчения структуры оказался многократный циклический скоростной нагрев до температур пол-
ной аустенитизации (выше Ас3) с короткими выдержками и последующей закалкой на мартенсит [28].
Вработе [22] показано, что наибольшее измельчение структуры методами термоциклической обработки достигается в случае наличия в исходном состоянии высокой плотности дефектов кристаллического строения. Такое состояние можно создать как с помощью закалки, так и холодной деформацией.
Авторами [8] показано, что низкоуглеродистые стали со структурой пакетного мартенсита наряду с высокой прочностью обладают высокой пластичностью, что дает возможность подвергать закаленные низкоуглеродистые стали холодной пластической деформации промышленным способом – радиальной ковкой (РК). Характерной особенностью этого метода является то, что при при-
34
ложении усилия одновременно несколькими радиально перемещающимися бойками реализуется схема неравномерного всестороннего сжатия [6]. Описанная схема деформации позволяет получить высокую степень холодной пластической деформации без образования трещин в обрабатываемом материале, а локализация очага деформации в сочетании с поворотом заготовки приводит к тому, что металл подвергается циклическому формоизменению. В итоге накопленная суммарная деформация может превысить среднюю деформацию, определяемую уковом. Такое воздействие должно привести к получению дополнительных дефектов кристаллического строения в закаленных сталях и, как следствие, оказать воздействие на фазовые и структурные превращения в сталях при последующей интенсивной термической обработке [48].
Для исследования эволюции структуры, субструктуры и механических свойств исходно закаленных сталей в процессе холодной пластической деформации и последующей интенсивной термоциклической обработки выбраны конструкционные системно легированные низкоуглеродистые стали 10Х3Г3МФ и 10Х3Г3МФТ.
2.2.1. Эволюция структуры и свойств закаленной низкоуглеродистой мартенситной стали при холодной пластической деформации методом радиальной ковки
Сталь 10Х3Г3МФ подвергали холодной пластической деформации на радиально-ковочной машине SXP-16 с круга диаметром 19 мм на круг 12 мм, что составляет 60 % деформации. Ковка проходила в три прохода – 20, 40 и 60 % деформации – по режиму: скорость подачи 180 мм/мин, скорость ударов бойков 1000 уд/мин и скорость вращения заготовки 25 об/мин. В качестве степени пластической деформации принимали величину укова ε, определяемую по результатам изменения площади поперечного сечения образца до и после ковки.
Рассмотрим образцы стали 10Х3Г3МФ в исходно горячекованом состоянии и после холодной пластической деформации методом радиальной ковки со степенью деформации 60 % (рис. 2.11).
35
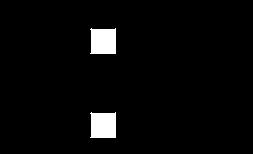
1
2
Рис. 2.11. Прутки стали 10Х3Г3МФ в исходном горячекованом состоянии (1) и после радиальной ковки, степенью деформации 60 % (2)
Дюрометрический анализ процессов холодной радиальной ковки стали 10Х3Г3МФ. Для изучения однородности свойств по сечению образцов стали 10Х3Г3МФ, подвергнутой холодной пластической деформации методом радиальной ковки со степенями 20, 40 и 60 %, использовали методы дюрометрического анализа: измерение твердости методом Роквелла и микротвердости по Виккерсу. Данные о диаметре образцов стали 10Х3Г3МФ представлены в табл. 2.3.
|
|
Таблица 2.3 |
Режимы обработки, обозначения и диаметры образцов |
||
стали 10Х3Г3МФ |
|
|
|
|
|
Режим обработки |
Обозначение |
Номинальный |
диаметр образца, мм |
||
Исходное состояние: |
Исх. зак. |
19 |
закалка с температур горячей |
|
|
ковки |
|
|
Исх. зак. + радиальная ковка |
РК 20 % |
16 |
со степенью деформации 20 % |
|
|
Исх. зак. + радиальная ковка |
РК 40 % |
14 |
со степенью деформации 40 % |
|
|
Исх. зак. + радиальная ковка |
РК 60 % |
12 |
со степенью деформации 60 % |
|
|
|
36 |
|
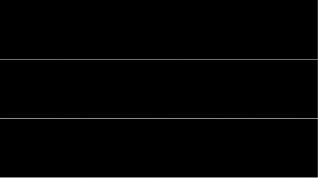
Для оценки однородности распределения свойств с помощью дюрометрического анализа по методу Роквелла проводили измерение твердости в двух областях: в центральной части (сердцевине) и на краю (периферии) сечения деформированного образца. Результаты измерения твердости получены как среднее арифметическое 3–4 измерений. Результаты представлены на рис. 2.12.
Рис. 2.12. Твердость центра и края образцов стали 10Х3Г3МФ, обработанных по различным режимам:
Как видно из представленных результатов, различия в значениях твердости сердцевины и периферии холоднодеформированного прутка, определенных методом Роквелла, незначительны и составляют 1–2 единицы шкалы HRC, что сопоставимо с погрешностью метода и прибора. Данный факт можно объяснить двумя причинами: либо анизотропия свойств по сечению образцов отсутствует, либо метод измерения твердости по Роквеллу обладает недостаточной чувствительностью для оценки неоднородности распределения свойств по сечению образцов. Однако следует отметить, что увеличение степени деформации приводит к увеличению уровня твердости и разницы в твердости центра и края.
Более эффективным для оценки однородности свойств по сечению холоднодеформированных образцов в силу своей высокой чувствительности является метод измерения микротвердости по Виккерсу. Микротвердость измеряли с помощью микротвердомера Model 402MVD на исходно закаленных образцах, а также на образ-
37
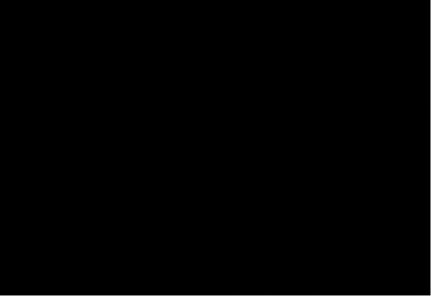
цах, подвергнутых после закалки с прокатного нагрева на структуру пакетного мартенсита холодной пластической деформации методом радиальной ковки со степенями 20, 40, 60 %. На каждом образце измерения проводили по двум взаимно перпендикулярным диаметрам от края до края образца. Шаг между точками измерений 0,3 мм.
Для корректного сопоставления результатов измерения микротвердости образцов стали 10Х3Г3МФ, обработанных по различным режимам, данные представлены в виде графиков, построенных относительно центра образца. Ноль на горизонтальной оси соответствует центру образца, положительное и отрицательное направления оси Х – направления от центра к краю образца, лежащие на одном диаметре. Представим усредненные по результатам двух измерений по взаимно перпендикулярным диаметрам значения микротвердости по сечению прутков стали 10Х3Г3МФ после обработки по различным режимам (рис. 2.13).
Рис. 2.13. Распределение микротвердости по сечению прутка стали 10Х3Г3МФ в исходно закаленном с температур горячей ковки и холоднодеформированном состоянии методом радиальной ковки с различными степенями деформации
38
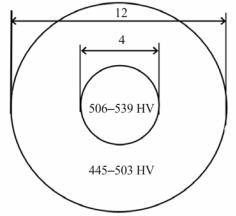
Распределение микротвердости по сечению прутка в исходно закаленном состоянии однородно и находится на уровне порядка
390 HV.
Распределение микротвердости по сечению прутков, подвергнутых холодной пластической деформации методом радиальной ковки со степенями 20, 40 и 60 %, можно охарактеризовать как неоднородное, при этом выражены две области (рис. 2.14): относительно однородная по свойствам сердцевина прутка с максимальным уровнем микротвердости и периферия, где твердость плавно убывает от границы с сердцевиной к краю образца. При этом снижение твердости идет практически до уровня исходно закаленного горячекованого состояния. У самой поверхности наблюдается резкое падение твердости, что, по-видимому, связано с наличием обезуглероженного слоя в исходно горячекованом прутке. Сувеличением степени деформации такой характер распределения твердости сохраняется, а общий уровень твердости повышается. Так, после холодной пластической деформации методом радиальной ковки со степенью 20 % твердость сердцевины прутка находится науровне примерно 450 HV, после РК 40 % – 470 HV, после РК60 % – 510 HV.
Рис. 2.14. Распределение микротвердости по сечению прутка из стали 10Х3Г3МФ, подвергнутого холодной пластической деформации
методом радиальной ковки со степенью 60 %
39
Можно сделать вывод, что холодная пластическая деформация методом радиальной ковки повышает общий уровень микротвердости стали 10Х3Г3МФ, при этом формируется ярко выраженная неоднородность твердости по сечению прутка: относительно однородная сердцевина с максимальным уровнем твердости и периферия, где твердость плавно убывает к краю образца. С увеличением степени холодной пластической деформации происходит повышение общего уровня твердости образца. Так, при степени пластической деформации 60 % твердость сердцевины образца увеличивается на 30 % (с 390 до 510 HV).
Исследование структурных изменений при холодной ради-
альной ковке стали 10Х3Г3МФ. Для установления закономерностей эволюции структуры исходно закаленной стали 10Х3Г3МФ при холодной пластической деформации методом радиальной ковки были проведены исследования микроструктуры на микрошлифах
сиспользованием оптического микроскопа Carl Zeiss Axio Observer A1m при увеличении до 1000 крат и исследования тонкой структуры на тонких фольгах, приготовленных по стандартной методике
сиспользованием просвечивающего электронного микроскопа Technai G2 FEI при ускоряющем напряжении 200 кВ.
Рассмотрим микроструктуру образцов стали 10Х3Г3МФ, подвергнутых холодной пластической деформации методом радиальной ковки со степенями 20, 40 и 60 % (рис. 2.15), структура на образцах снята на половине радиуса сечения прутка.
Как видно, увеличение степени холодной пластической деформации не приводит к разрушению реечного строения, т.е. даже после радиальной ковки со степенью 60 % морфология пакетного мартенсита сохраняется.
Встали 10Х3Г3МФ после закалки на воздухе с температуры горячей ковки наблюдается пакетно-реечное строение с высокой плотностью дислокаций внутри реек мартенсита (рис. 2.16), средний размер рейки мартенсита в плоскости фольги составляет 355 нм. Следует отметить, что в тонкой структуре исследуемой стали наблюдается эффект наследования мартенситом части дефектов кристаллического строения аустенита, сформированных во время горячей ковки.
40