
книги / Наноструктурные стали
..pdf(рис. 2.21, в). Благодаря формированию высокодисперсной структуры (см. рис. 2.17, 2.19) значения ударной вязкости стали 10Х3Г3МФ, обработанной по режиму «РК 60 % + нагрев 900 оС», находятся на высоком уровне и достигают значения 0,91 МДж/м2 (см. табл. 2.5), что в 4 раза выше по сравнению с исходно закаленным состоянием. Излом образца не наследует характер макрорельефа от холоднодеформированного состояния и отражает характер распределения микротвердости по сечению – однородный, плоский по всему сечению, с развитыми областями боковой утяжки.
Увеличение температуры скоростного нагрева холоднодеформированной стали 10Х3Г3МФ с 900 до 1000 оС вызывает более интенсивное протекание процессов собирательной рекристаллизации аустенита и огрубление структуры (см. рис. 2.17), что обусловливает некоторое снижение твердости (см. рис. 2.21, г) относительно нагрева на 900 оС: твердость сердцевины прутка оказывается несколько ниже, чем твердость периферии – 415 и 435 HV соответственно. Такой характер распределения микротвердости приводит к росту уровня ударной вязкости (КСТ) образцов, обработанных по режиму «РК 60 % + нагрев 1000 оС», до 1,15 МДж/м2 (см. табл. 2.5). При этом неоднородность в распределении твердости по сечению образцов после интенсивной термической обработки на 1000 оС проявляется в строении излома – в центральной части плоского участка излома наблюдается более рыхлая поверхность.
Таким образом, после одного цикла ИТЦО при 900 ºС холоднокованой стали в результате получения высокодисперсной структуры происходит повышение пластичности и ударной вязкости. При этом сохраняются высокие значения предела текучести (на 45 % выше исходно закаленного состояния) и временного сопротивления разрыву (на 10 % выше исходно закаленного состояния). На диаграмме растяжения стали в таком дисперсном состоянии после достижения предела текучести наблюдается развитый участок равномерной пластической деформации порядка 4 %, при этом практически не происходит деформационного упрочнения, т.е. предел текучести и временное сопротивление разрыву имеют близкие
51
значения (см. табл. 2.4). Такие закономерности пластического течения характерны для высокодисперсных структур.
После одного цикла ИТЦО при 1000 ºС исходно деформированной стали 10Х3Г3МФ характеристики пластичности имеют такие же значения, как и после ИТЦО при 900 ºС. На диаграмме одноосного растяжения участок равномерной деформации составляет также 4 %, но при этом по причине более крупного зерна наблюдаются меньшие значения характеристик прочности и больший уровень деформационного упрочнения.
Использование ускоренного нагрева при интенсивной тер-
мической обработке. Интенсивная термическая обработка в соляных печах-ваннах применима, как правило, только для заготовок и изделий небольшого размера и массы. Более технологичной является интенсивная термоциклическая обработка с применением ускоренного нагрева посадкой в горячую печь (4 °С/с) с воздушной атмосферой.
Рассмотрим структуру и свойства низкоуглеродистой стали 10Х3Г3МФТ при холодной пластической деформации низкоуглеродистой стали методом радиальной ковки и последующей многократной интенсивной термической обработке с нагревом посадкой в горячую печь.
Эволюция структуры холоднодеформированной низкоуглеродистой стали 10Х3Г3МФТ при интенсивной термоцикличе-
ской обработке. Исследование тонкой структуры стали 10Х3Г3МФТ, сформированной при охлаждении на воздухе от температуры окончания горячей статической ковки (около 950 °С), показало, что в исходном состоянии перед холодной пластической деформацией методом радиальной ковки сталь имеет структуру пакетного мартенсита. В структуре наблюдается реечная фрагментация внутри пакета (средний поперечный размер рейки в плоскости фольги 310 нм), высокая плотность дислокаций (порядка 1010– 1012 см–2) и кристаллографически ориентированные карбиды, сформированные в процессе автоотпуска мартенсита при охлаждении на воздухе (рис. 2.22, а).
52
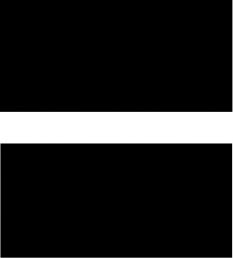
Холодная пластическая деформация методом радиальной ковки закаленной стали приводит к дополнительной фрагментации структуры за счет формирования деформационных ячеек внутри мартенситных реек (рис. 2.22, б). При этом средний размер деформационных ячеек составляет 140 нм, а средний поперечный размер рейки в плоскости фольги уменьшается до 200 нм.
аб
вг
Рис. 2.22. Тонкая структура стали 15Х3Г3МФТ после различных режимов обработки: а – закалка с температур горячей статической ковки; б– холодная пластическая деформация методом радиальной ковки; в – однократный нагревдо900 °С; г– однократныйнагревдо1000 °С
После холодной пластической деформации методом радиальной ковки со степенью 60 % проводили ИЦТО с ускоренным нагревом посадкой образцов в горячую печь и последующим закалочным охлаждением в воде. Характер изменения размера зерна при ИТЦО приведен на рис. 2.23.
Установлено, что при циклировании на 900 °С наиболее дисперсная зеренная структура аустенита со средним размером зерна
53
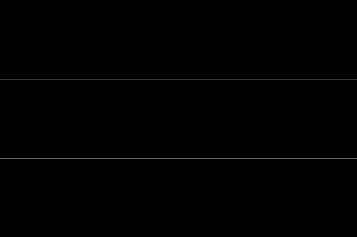
3 мкм формируется после первого цикла. Дальнейшее циклирование приводит к росту аустенитного зерна со стабилизацией его среднего размера на уровне 4–5 мкм. Такая тенденция изменения размера аустенитного зерна обусловлена тем, что в первом цикле ИТЦО нагреву подвергается сталь в холоднодеформированном состоянии, при этом проходит формирование большого количества зародышей аустенита в межкритическом интервале температур. При последующих циклах нагреву подвергается уже закаленная структура, что вызывает восстановление аустенитного зерна и некоторый его собирательный рост.
Рис. 2.23. Изменение среднего размера аустенитного зерна в зависимости от количества циклов ИТЦО стали 10Х3Г3МФТ:
1 – ИТЦО при 900 °С; 2 – ИТЦО при 1000 °С
ИТЦО при 1000 °С исходно холоднодеформированной стали 10Х3Г3МФТ приводит к получению более крупного зерна аустенита со средним размером 6 мкм на первом цикле в результате более интенсивного развития процессов собирательного роста аустенитного зерна при более высокой температуре по сравнению с ИТЦО при 900 °С. Однако общая динамика изменения зеренной структуры аустенита при циклировании при 1000 °С сохраняется. Различия
54
вразмере аустенитного зерна между центральной частью прутка
ипериферией после различных режимов ИТЦО не обнаружены.
По результатам металлографического анализа образцов стали 10Х3Г3МФТ, подвергнутых ИТЦО при 900 и 1000 °С, установлено, что наибольший эффект диспергирования структуры достигается на первом цикле обработки, а последующие циклы приводят к укрупнению структуры. Таким образом, однократный нагрев является наиболее перспективным для дальнейшего исследования.
Исследование методом просвечивающей электронной микроскопии тонкой структуры стали 10Х3Г3МФТ после циклирования при 900 и 1000 °С выявило пакетно-реечное строение разной дисперсности. Так, после однократного нагрева при 900 °С со средним размером аустенитного зерна 3 мкм наблюдается структура мартенсита со средним поперечным размером рейки в плоскости фольги 80 нм (рис. 2.22, в), а после однократного нагрева при 1000 °С в состоянии со средним размером зерна 6 мкм – размер рейки 290 нм (рис. 2.22, г). Уменьшение среднего поперечного размера рейки мартенсита в плоскости фольги по сравнению с исходно закаленным состоянием вызвано диспергированием аустенитного зерна, так как уменьшение аустенитного зерна вызывает снижение размеров мартенситного пакета [12], что, в свою очередь, приводит к уменьшению размеров рейки.
Результаты исследования однородности распределения микротвердости по сечению прутка стали 10Х3Г3МФТ после различных режимов обработки приведены на рис. 2.24.
Установлено, что в исходно закаленном состоянии наблюдается однородное распределение микротвердости по сечению, а после холодной радиальной ковки возникает ярко выраженная неоднородность: упрочненная сердцевина и периферия с пониженной твердостью и некоторым повышением твердости непосредственно у самой поверхности. Упрочнение сердцевины обусловлено наложением полей деформации от четырех бойков при холодной радиальной ковке в условиях стеснения пластической деформации в этой области [6]. Увеличение твердости в поверхностных слоях,
55
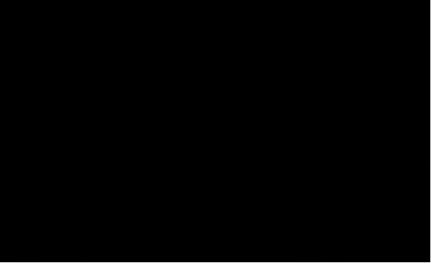
по-видимому, вызвано высокими контактными напряжениями при воздействии бойков в процессе холодной пластической деформации методом радиальной ковки.
Рис. 2.24. Распределение микротвердости стали 10Х3Г3МФТ после различных режимов обработки: 1 – закалка с температур горячей статической ковки; 2 – холодная пластическая деформация методом радиальной ковки; 3 – однократный нагрев до 900 °С; 4 – однократный нагрев до 1000 °С; серым цветом показаны экспериментальные данные, черным – аппроксимирующие
кривые (полином 6-й степени)
Однократный нагрев при 900 или 1000 °С холоднодеформированной стали вызывает падение общего уровня твердости с изменением характера ее распределения: твердость сердцевины цилиндрических образцов становится ниже твердости периферийных областей. Уровень твердости после одного цикла ИТЦО при 900 °С выше, чем после обработки при 1000 °С при одинаковом характере распределения твердости по сечению. Уменьшение общего уровня твердости прутка вызвано более полным устранением механического наклепа и релаксацией остаточных напряжений при однократной фазовой перекристаллизации.
56
Характеристики механических свойств стали 10Х3Г3МФТ после различных режимов обработки приведены в табл. 2.6.
Таблица 2.6
Механические свойства стали 10Х3Г3МФТ после различных режимов обработки
Режим обработки |
σ0,2 |
σв |
δ |
|
ψ |
KCU, |
МПа |
|
% |
МДж/м2 |
|||
Закалка от температур ста- |
910 |
1250 |
15 |
|
59 |
1,32 |
тической горячей ковки |
|
|||||
(исходное состояние) |
|
|
|
|
|
|
РК 60 % |
1590 |
1600 |
7 |
|
53 |
1,39 |
Однократный нагрев |
1190 |
1330 |
14 |
|
66 |
1,48 |
на 900 °С |
|
|||||
|
|
|
|
|
|
|
Однократный нагрев |
1065 |
1280 |
15 |
|
68 |
1,90 |
на 1000 °С |
|
|||||
|
|
|
|
|
|
Холодная пластическая деформация методом радиальной ковки закалкой стали 10Х3Г3МФТ вызывает увеличение характеристик прочности в результате механического наклепа и снижение пластичности, а ударная вязкость остается практически на уровне исходно закаленного состояния. Характер диаграммы одноосного растяжения холоднодеформированной стали свидетельствует об отсутствии участка равномерной пластической деформации при растяжении, а пластичность при испытаниях обусловлена только локальной пластической деформацией (рис. 2.25).
Однократный нагрев на 900 °С после холодной пластической деформации исследуемой стали вызывает повышение характеристик прочности, в том числе предела текучести на 30 %, и характеристик надежности, в том числе ударной вязкости (КСU) на 14 %, при сохранении уровня пластичности относительно исходно закаленного состояния (см. табл. 2.6). Применение однократного нагрева до 1000 °С вызывает менее выраженный рост предела текучести (на 17 %) при существенном увеличении уровня ударной вязкости
(КСU) на 44 %.
57
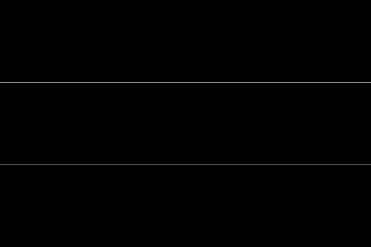
Рис. 2.25. Диаграммы одноосного растяжения стали 10Х3Г3МФТ после различных режимов обработки: 1 – исходно закаленное состояние; 2 – холодная деформация методом радиальной ковки; 3 – однократный нагрев до 900 °С; 4 – однократный нагрев до 1000 °С
Диаграмма одноосного растяжения стали 10Х3Г3МФТ после однократного нагрева до 900 и 1000 °С имеет выраженную площадку равномерной пластической деформации порядка 8 %, что характерно для материалов с дисперсной структурой.
2.3.Влияние размера элементов структуры
итекстуры горячей пластической деформации на уровень характеристик прочности и надежности
Как показано, повышение уровня характеристик прочности и надежности сталей со структурой пакетного мартенсита возможно за счет измельчения аустенитного зерна при термическом воздействии. При уменьшении размера аустенитного зерна также диспергируется субструктура пакетного мартенсита. Помимо диспергирования структуры мартенсита на уровень механических свойств листовых низкоуглеродистых сталей существенное влияние оказывает
58
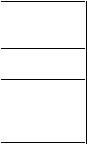
направление вырезки образцов относительно направления прокатки, так как при такой обработке в стали формируется волокнистое строение [51].
Наиболее широкие температурно-временные условия получения структуры пакетного мартенсита реализуются в системно легированных низкоуглеродистых сталях, одной из которых является сталь 12Х2Г2НМФТ [10].
Данный подраздел посвящен установлению взаимосвязи размера элементов структуры и субструктуры, направления вырезки образцов и уровня характеристик прочности и надежности закаленной листовой низкоуглеродистой стали 12Х2Г2НМФТ.
Изучение тонкой структуры стали 12Х2Г2НМФТ после исследуемых режимов термической обработки выявило реечное строение пакетного мартенсита разной дисперсности (табл. 2.7). Так, средний поперечный размер рейки в плоскости фольги при варьировании размера аустенитного зерна от 2,5 до 65 мкм изменяется от 96 до 341 нм. При этом наблюдается прямо пропорциональная зависимость среднего поперечного размера рейки в плоскости фольги от размера аустенитного зерна (рис. 2.26), что находится в полном соответствии с работой [52]. Степень достоверности аппроксимации такой зависимости линейной функцией составляет 99 %.
Таблица 2.7
Режимы термической обработки стали 12Х2Г2НМФТ и полученное структурное состояние
№ |
Термическая обработка |
Средний размер |
Средняя тол- |
|
аустенитного зерна |
щина рейки |
|||
п/п |
||||
|
dа, мкм |
bp, нм |
||
|
|
|||
1 |
ТЦО при 900 °С, 5 циклов, вы- |
2,5 |
96 |
|
держка 25 с, охлаждение в воде |
||||
2 |
ТЦО при 1000 °С, 5 циклов, вы- |
10 |
206 |
|
держка 25 с, охлаждение в воде |
||||
3 |
Закалка с 900 °С, выдержка 30 |
18 |
230 |
|
мин, охлаждение в воде |
||||
|
59 |
|
|
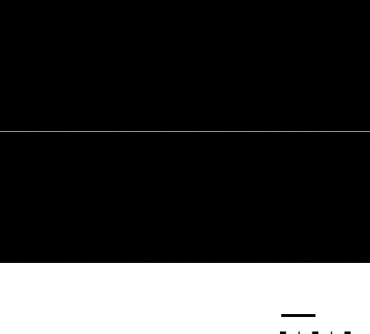
Окончание табл. 2.7
№ |
Термическая обработка |
Средний размер |
Средняя тол- |
|
аустенитного зерна |
щина рейки |
|||
п/п |
||||
|
dа, мкм |
bp, нм |
||
|
|
|||
4 |
Закалка с 1100 °С, выдержка 30 |
40 |
271 |
|
|
мин, охлаждение в воде |
|
|
|
5 |
Закалка с 1200 °С, выдержка 30 |
65 |
341 |
|
мин, охлаждение в воде |
Рис. 2.26. Зависимость характеристик прочности (σв, σ0,2) и
среднего поперечного размера рейки закаленной |
стали |
12Х2Г2НМФТ от размера аустенитного зерна |
– свой- |
ства, определенные на поперечных образцах; |
– |
свойства, определенные на продольных образцах
Механические испытания проводили на образцах из стали 12Х2Г2НМФТ, вырезанных как в продольном, так и в поперечном направлении относительно направления прокатки (рис. 2.27).
Результаты исследования характеристик прочности также представлены на рис. 2.26. Из приведенных зависимостей видно, что направление вырезки образцов из листовой заготовки не оказывает существенного влияния на уровень характеристик прочности. Установ-
60