
книги / Наноструктурные стали
..pdf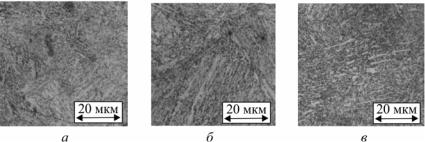
Рис. 2.15. Микроструктура стали 10Х3Г3МФ, подвергнутой холодной пластической деформации методом радиальной ковки со степенями: а – 20 %; б – 40 %; в – 60 %
Тонкая структура стали 10Х3Г3МФ после холодной пластической деформации методом радиальной ковки со степенями 20 и 60 % и гистограммы распределения по размерам реек мартенсита и деформационных ячеек представлены на рис. 2.16.
Анализ тонкой структуры образцов после холодной пластической деформации методом радиальной ковки со степенью 20 % показал, что в материале происходит формирование дислокационных ячеек внутри реек, что приводит к их дополнительной фрагментации (рис. 2.16, в). При этом средний поперечный размер реек в плоскости фольги составляет 257 нм, а средний размер деформационных ячеек 216 нм (табл. 2.4).
Таблица 2.4
Эволюция размеров субструктурных элементов мартенсита стали 10Х3Г3МФ при холодной пластической деформации методом радиальной ковки
Состояние |
Средний размер реек, нм |
Средний |
|
размер |
|||
|
|
ячеек, нм |
|
Исходно закаленное с температур |
355 |
– |
|
горячей ковки состояние |
|||
|
|
||
РК 20 % |
257 |
216 |
|
РК 60 % |
194 |
163 |
|
Относительное изменение |
25 % |
25 % |
|
|
41 |
|
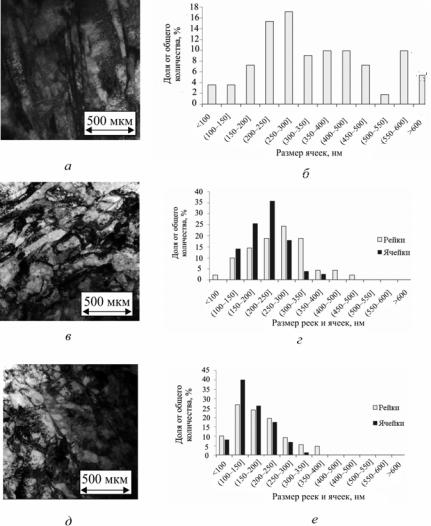
Рис. 2.16. Тонкая структура (а, в, д) и гистограммы (б, г, е) распределения по размерам структурных элементов в плоскости фольги стали 10Х3Г3МФ: а, б – исходно закаленное с температур горячей ковки состояние; в, г – холодная пластичная деформация методом радиальной ковки со степенью 20 %; д, е– состепенью60 %
42
Увеличение степени деформации закаленной стали 10Х3Г3МФ до 60 % приводит к уменьшению среднего поперечного размера рейки мартенсита в плоскости фольги до 194 нм, что сопровождается уменьшением размера ячеек деформации до 163 нм (рис. 2.16, д, е). Другими словами, при увеличении степени деформации закаленной стали 10Х3Г3МФ с 20 до 60 % происходит уменьшение размера рейки и размера дислокационной ячейки на 25 % [49]. Гистограмма распределения среднего поперечного размера рейки в плоскости фольги после деформации со степенями 20 и 60 % носит логнормальный характер.
2.2.2. Интенсивная термоциклическая обработка холоднодеформированных низкоуглеродистых сталей
Использование скоростного нагрева для интенсивной термоциклической обработки. Эволюция структуры холоднодеформированной низкоуглеродистой стали 10Х3Г3МФ. Элек-
тронно-микроскопические исследования исходного состояния закаленной стали 10Х3Г3МФ перед ИТЦО выявили структуру с пакет-
но-реечной фрагментацией со средним размером рейки |
194 нм, |
||
а внутри реек – |
деформационные ячейки со |
средним |
размером |
163 нм (см. рис. |
2.16, д, е). Исходный размер |
аустенитного зерна |
в стали 10Х3Г3МФ 12 мкм.
Результаты дилатометрических и металлографических исследований процесса структурообразования и положения температуры начала мартенситного превращения (Мн) при ИТЦО исходно закаленной и холоднокованой со степенью деформации 60 % стали 10Х3Г3МФ приведены на рис. 2.17 [48].
Исследование процесса ИТЦО закаленной и холоднодеформированной стали 10Х3Г3МФ показало, что наибольшее измельчение зерна аустенита, до 1 мкм наблюдается после первого цикла обработки при 900 ºС. Циклирование до третьего цикла приводит к росту среднего размера аустенитного зерна до 3,5 мкм, а на последующих циклах размер зерна стабилизируется. Наблюдаемая динамика изменения зеренного строения аустенита обусловлена эволюцией
43
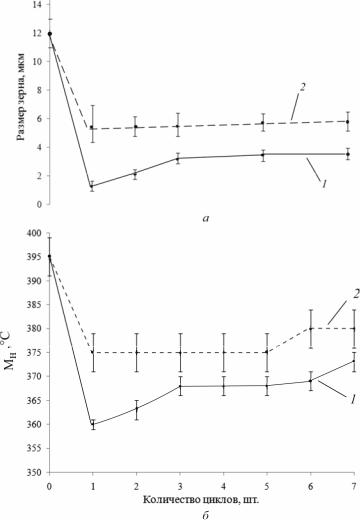
Рис. 2.17. Зависимость среднего размера аустенитного зерна (а) и положения температуры начала мартенситного превращения Мн (б) от количества циклов стали 10Х3Г3МФ после закалки и холодной пластической деформации методом радиальной ковки со степенью 60 %: 1 – ИТЦО при 900 ºС; 2 – ИТЦО при 1000 ºС; 0 циклов – предварительная закалка с температуры
окончания горячей ковки 930 ºС
44
структуры дефектов стали при ИТЦО от цикла к циклу, что прежде всего сказывается на процессах образования и роста зародышей аустенита в межкритическом интервале. Так, при первом скоростном нагреве в межкритическом интервале температур в высокодефектной α-матрице образуется большое количество сферических зародышей аустенита (рис. 2.18, а), преимущественно в области стыков границ реек, рекристаллизованных зерен, субзерен или дислокационных ячеек. Увеличение температуры нагрева приводит к росту этих зародышей, при этом их сферическая форма сохраняется (рис. 2.18, б). При завершении аустенитизации в межкритическом интервале при скоростном нагреве формируется сверхмелкозернистая структура аустенита, состоящая из равноосных зерен, что позволяет получить сверхмелкозернистую структуру аустенита при нагреве, а при закалке – наноструктурный мартенсит.
Во втором цикле нагреву подвергается уже высокодисперсная пакетно-реечная мартенситная структура – зародыши аустенита образуются по механизму востановления структуры и прорастают вдоль межреечных границ (рис. 2.18, в), а их дальнейший рост при более высоких температурах нагрева происходит в направлении тела рейки (рис. 2.18, г). Это приводит к восстановлению аустенитного зерна при нагреве и первичной рекристаллизации с последующим ростом зерна при выдержке. После третьего цикла размер зерна аустенита практически не изменяется.
Циклирование при 1000 ºС приводит к измельчению аустенитного зерна до 5 мкм на первом цикле, а дальнейшее циклирование уже не влияет на его размер. Такая динамика изменения размера аустенитного зерна обусловлена большей скоростью процессов собирательного роста при 1000 ºС, чем при 900 ºС, что приводит кувеличению размера зерна иболее ранней стабилизации структуры приИТЦО.
Положение температуры начала мартенситного превращения (Мн) качественно повторяет динамику изменения размера аустенитного зерна. Это позволяет утверждать, что в исследуемой стали при данном режиме ИТЦО не происходит расслоения твердого раствора, как это наблюдали в работах [34, 35], а положение Мн зависит только от размера зерна аустенита [36].
45
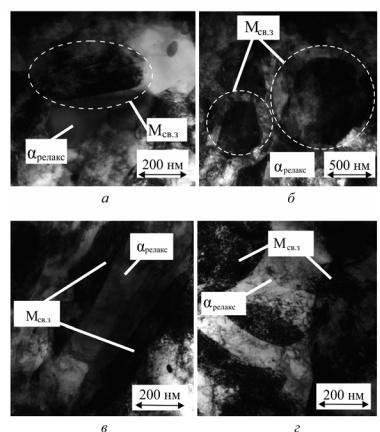
Рис. 2.18. Процесс образования и роста зародышей аустенита в стали 10Х3Г3МФ в первом межкритическом интервале (а, б) и во втором цикле (в, г) ИТЦО после скоростного нагрева в МКИ, выдержки 20 с и закалки в воде: а, в – 750 ºС; б – 770 ºС; г – 790 ºС; Мсв.з – свежезакаленный мартенсит; αрелакс – исходная релаксированная α-фаза
При электронно-микроскопических исследованиях тонкого строения холоднокованой стали после одного цикла ИТЦО при 900 ºС (рис. 2.19, а) в ее структуре выявлены области сферической формы, по-видимому, области бывших аустенитных зерен, внутри которых в результате мартенситного превращения произошла рееч-
46
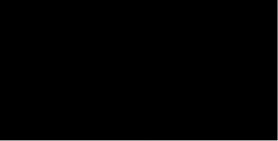
ная фрагментация. Средний размер этих областей соответствует среднему размеру аустенитных зерен, определенных методом металлографического анализа, а средний размер рейки мартенсита
(рис. 2.19, б) равен 95 нм.
а |
б |
Рис. 2.19. Пакетная (а) и реечная (б) структура исходно холоднодефомированной стали 10Х3Г3МФ после ИТЦО при 900 ºС, 1 цикл
Эволюция свойств холоднодеформированной низкоуглеродистой стали 10Х3Г3МФ при интенсивной термоциклической обработке со скоростным нагревом. Результаты исследования ме-
ханических свойств стали 10Х3Г3МФ после холодной пластической деформации методом радиальной ковки со степенью 60 % и последующей ИТЦО приведены в табл. 2.5.
Таблица 2.5 Свойства стали 10Х3Г3МФ после различных режимов обработки
№ |
Режим обработки |
σ0,2 |
|
σв |
δ |
|
ψ |
KCT |
KCU |
|
п/п |
|
|
|
|
|
|
|
|
|
|
|
|
|
|
|
|
|
|
2 |
||
|
|
МПа |
|
% |
МДж/м |
|
||||
1 |
Исходно закален- |
940 |
|
1290 |
16 |
|
63 |
0,21 |
1,30 |
|
ное состояние |
|
|
||||||||
|
|
|
|
|
|
|
|
|
|
|
2 |
РК 60 % |
– |
|
1790 |
7 |
|
53 |
0,55 |
1,32 |
|
3 |
РК 60 % + один |
1360 |
|
1420 |
13 |
|
69 |
0,91 |
|
– |
цикл ИТЦО |
|
|
|
|||||||
|
при 900 ºС |
|
|
|
|
|
|
|
|
|
|
РК 60 % + один |
|
|
|
|
|
|
|
|
|
4 |
цикл ИТЦО |
1100 |
|
1310 |
14 |
|
69 |
1,15 |
|
– |
|
при 1000 ºС |
|
|
|
|
|
|
|
|
|
|
|
|
47 |
|
|
|
|
|
|
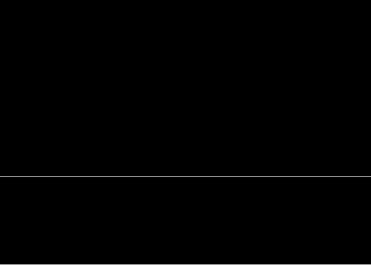
В холоднодеформированном состоянии временное сопротивление разрыву σв исходно закаленной стали 10Х3Г3МФ увеличилось на 40 % относительно исходно закаленного состояния, однако при этом снизились относительное удлинение δ, более чем в два раза, и относительное сужение ψ – на 16 %. На диаграмме растяжения деформированной стали (рис. 2.20) отсутствует участок равномерной пластической деформации, а при достижении временного сопротивления разрыву сразу начинается локализация пластической деформации. Относительноеудлинениехолоднокованой стали10Х3Г3МФ, равное7 %, определяется только локальной деформацией. Такое поведение стали в деформированном состоянии объясняется тем, что при холодной пластической деформации методом радиальной ковки был реализован весь ресурс равномерной пластической деформации в закаленном состоянии без образования микротрещин, а испытание на одноосное растяжение вызывает лишь локализацию деформации при отсутствии равномерного пластического теченияматериала.
Рис. 2.20. Диаграммы одноосного растяжения стали 10Х3Г3МФ после закалки и холодной пластической деформации со степенью 60 % методом радиальной ковки (1), после одного цикла ИТЦОна900 ºС(2) иодногоциклаИТЦОна1000 ºС(3)
48
Ударная вязкость KCU после деформации практически не изменяется, а КСТ возрастает более чем в 2,5 раза. Если рассматривать значение KCU как сумму удельных работ зарождения и распространения трещины при динамических испытаниях, а КСТ только как работу распространения трещины, то в кованой стали увеличивается работа распространения трещины, но снижается работа ее зарождения.
Результаты дюрометрического анализа стали 10Х3Г3МФ в исходно закаленном состоянии и после холодной пластической деформации методом радиальной ковки показали, что распределение микротвердости по сечению исходно закаленного прутка однородно и находится на уровне 390 HV. Ударная вязкость КСТ исходно горячекованого прутка составляет 0,21 МДж/м2 (см. табл. 2.5), а макрорельеф излома характеризуется наличием областей боковой утяжки и развитой плоской однородной по всему сечению центральной областью (рис. 2.21, а) [50].
Холодная пластическая деформация методом радиальной ковки со степенью 60 % приводит к повышению общего уровня твердости (рис. 2.21, б), но при этом меняется характер ее распределения по сечению образца: формируются две области материала – сердцевина и периферия. Сердцевина отличается высоким и однородным уровнем твердости порядка 510 HV. На периферии микротвердость неоднородна и плавно снижается в направлении от центра к краям образца. В сравнении с исходно закаленным состоянием ударная вязкость после радиальной ковки со степенью 60 % возрастает более чем в 2,5 раза и достигает значений 0,55 МДж/м2 (см.
табл. 2.5).
Фрактографический анализ показал, что при разрушении в условиях динамических испытаний стали 10Х3Г3МФ, подвергнутой холодной пластической деформации методом радиальной ковки со степенью 60 %, трещина изменяет направление движения на границах между сердцевиной и периферией. В результате такого движения трещина формирует развитый макрорельеф поверхности разрушения образца, повторяющий профиль распределения микро-
49
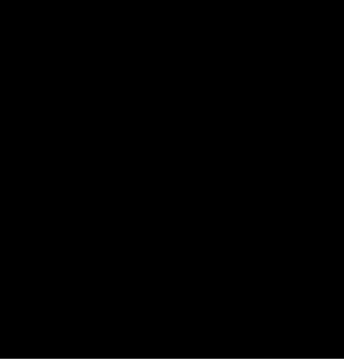
твердости по сечению (см. рис. 2.1, б), а боковая утяжка при этом отсутствует. Все эти явления в совокупности приводят к увеличению работы уровня ударной вязкости (КСТ) по сравнению с исходно закаленным состоянием.
Рис. 2.21. Изломы стали 10Х3Г3МФ после испытаний на КСТ и распределение микротвердости по сечению образцов в исходно закаленном состоянии (а), после холодной пластической деформации методом радиальной ковки со степенью 60 % (б), после холодной пластической деформации
методом радиальной ковки с последующим однократным нагревом на 900 оС (в) и 1000 оС (г). ×8
Интенсивная термическая обработка с нагревом на 900 оС холоднодеформированных образцов вызывает изменение характера распределения твердости: твердость находится на одном уровне (порядка 460 HV) и однородна по всему сечению образца
50