
книги / Механическая обработка пластиков
..pdfБольшие объемы пластиковых отходов являются проблемой для мусорных свалок и мусороперерабатывающих заводов. Пластиковые отходы нужно перерабатывать, так как пластик разлагается в почве 100–300 лет. Ни в коем случае нельзя сжигать пластиковые отходы на открытом воздухе, так как при сжигании выделяются токсичные вещества.
В то же время существует острая проблема загрязнения пластиковыми отходами Мирового океана. Под воздействием течений в Мировом океане образуются скопления пластиковых отходов, как правило в густонаселенных прибрежных зонах. Пластик постепенно разлагается, представляя собой взвесь из мелких кусков пластика. В результате морские животные (медузы, рыбы, млекопитающие), которые не могут разглядеть прозрачные частицы, плавающие в воде, проглатывают их, что может привести животных к смерти. Некоторые пластиковые отходы после долгого пребывания в воде и химических реакций становятся токсичными.
Существуют следующие производственные способы переработки пластика:
1.Пиролиз – термическое разложение органических и многих неорганических соединений. В узком смысле – разложение органических природных соединений при недостатке кислорода (древесины, нефтепродуктов и проч.). В более широком смысле – разложение любых соединений на составляющие менее тяжелые молекулы или химические элементы под действием повышенной температуры. Так, например, теллуроводород разлагается на водород и теллур уже при температуре около 0 °С.
2.Гидролиз – сольволиз водой. Это химическая реакция взаимодействия вещества с водой, при которой происходит разложение этого вещества и воды с образованием новых соединений. Гидролиз соединений различных классов (соли, углеводы, белки, сложные эфиры, жиры и др.) существенно различается.
3.Гликолиз – процесс окисления глюкозы, при котором из одной молекулы глюкозы образуются две молекулы пировиноградной кислоты.
21
4.Метанолиз – алкоголиз с участием метанола. Алкоголиз, как
игидролиз и аммонолиз, протекает по механизму нуклеофильного замещения, т.е. представляет собойчастный случайсольволиза.
В настоящее время открытие новых, более экономически и экологически эффективных, методов переработки пластиковых отходов является актуальной задачей мирового уровня. Например, пластики на основе фенольных смол могут разлагаться грибками белой гнили (процесс длится несколько месяцев).
Контрольные вопросы
1.Какие материалы называют пластиками (пластмассами)?
2.Что из себя представляют полимеры? Их отличие от мономеров?
3.Какими механическими свойствами обладают полимеры?
4.Какими особыми свойствами обладают полимеры вследствие гибкости макромолекул?
5.На какие классы делятся полимеры?
6.Чем отличаются термопласты от реактопластов?
7.Когда и как началось промышленное производство поли-
меров?
8.Какие существуют марки конструкционных и суперконструкционных пластиков? Их отличительные свойства?
9.Чем армируют пластики?
10.Какие компоненты входят в состав стеклопластиков?
11.Какие существуют методы обработки пластиков?
12.Каким образом происходит экструзия пластиков?
13.Каким образом происходит пултрузия пластиков?
14.Как маркируют изделия из пластиков (международные универсальные коды)?
15.Какие существуют методы переработки пластиков?
22
ГЛАВА 2. МЕТОДЫ МЕХАНИЧЕСКОЙ ОБРАБОТКИ ПЛАСТИКОВ
2.1. Анализ работ по механической обработке пластиков
Вопросами механической обработки пластиков занимались такие ученые, как Б.П. Штучный [1], А. Кобаяши [2], А.А. Степанов [3], Р.А. Тихомиров [4] и др. В рассматриваемой литературе указаны основные рекомендации по механической обработке пластиков. Однако эти данные невозможно напрямую применить к современным материалам и режущему инструменту, в связи с их существенным отличием от материалов и инструментов 70–80-х гг. прошлого века.
Вработе Б.П. Штучного [1] рассмотрены процессы обработки пластмасс: точение, сверление, фрезерование, разрезание, нарезание резьбы, абразивная обработка. Даны рекомендации по режимам резания для разных групп пластмасс, имеющих схожие физико-механические свойства и обрабатываемость резанием.
С точки зрения технологии представляет интерес работа Р.А. Тихомирова [4], в которой описаны различные методы механической обработки пластмасс. Рассматриваются возможности механического разрезания пластмасс приводными ножницами, абразивным инструментом, дисковыми фрезами, ленточными и дисковыми пилами, струями жидкости высокого давления, алмазным инструментом. Описываются возможности точения алмазными резцами, твердым сплавом и быстрорежущей сталью, фрезерование и сверление пластмасс, шлифование и полирование полимеров. Рассматриваются технологические особенности обработки стеклопластиков, реактопластов и термопластов.
Вряде диссертационных работ отражены различные аспекты обработки пластиков.
Вработе О.Ю. Еренкова [5] показано, что предварительное механическое нагружение (растяжение и сжатие) заготовок из полимерных материалов при последующем точении снижает ше-
23
роховатость обработанной поверхности в 2 раза по сравнению с простым точением. Общую тенденцию к снижению шероховатости обработанной точением поверхности после предварительного деформирования путем сжатия можно объяснить следующим образом. После снятия сжимающей нагрузки на заготовку в объеме материала действуют остаточные растягивающие напряжения, обеспечивающие эффект двойного технологического разупрочнения поверхностного слоя заготовки. Во-первых, за счет их действия появляются поверхностные дефекты в виде микротрещин. Во-вторых, в вершинах имеющихся и появившихся микротрещин образуются зоны перенапряжения, или зоны пластической деформации. В данных зонах имеет место частичное разрушение как химических, так и межмолекулярных связей полимера, что и является основой смягчения условий дальнейшей токарной обработки и повышения качества обработанной поверхности. Такой же эффект наблюдается при предварительной обработке заготовок поверхностно-активными веществами. Данные получены для капролона, фторопласта, текстолита и гетинакса.
В работе Л.Н. Шафигуллина [6] установлены закономерности влияния вида, количества и дисперсности наполнителя на эксплуатационные свойства полимерных наполненных композиционных материалов. Определено, что механическая обработка дисперсно-наполненных композиционных материалов оптимальна в интервале наполнения 0,2–0,4. Установлено, что эпоксидные композиты, наполненные гранитным порошком, обладают высокими физико-механическими, технологическими свойствами и качеством обработанных изделий. Введение в композиционные материалы полиамидного волокна повышает их упругие, прочностные, технологические свойства и качество обработанных изделий. Изучено влияние рецептурно-технологических факторов на технологические параметры обработки. Установлено, что изделия из полиэфирных наполненных композиционных материалов следует обрабатывать при более низких подачах (при фрезеровании и сверлении Sz = 0,1…0,2 мм/об) и более высоких скоростях реза-
24
ния (при фрезеровании n = 1000…1500 об/мин; при сверлении n = 500…1000 об/мин), чем изделия из эпоксидных и эпоксиполиуретановых композитов.
Вработе М. Валид [7] получены математические модели для расчета зависимости динамических составляющих силы резания
ивибраций державки резца при точении синтеграна от подачи и скорости резания методом планирования эксперимента.
Вработе О.А. Иванова [8] изучены процессы разрушения в композиционных углепластиках при механической обработке.
Вработе М.В. Доц [9] исследовано влияние режимов резания на шероховатость обработанной поверхности и глубину дефектного слоя при точении стеклопластика твердосплавными резцами ВК8. Выявлено, что при скорости резания более 80 м/мин, подаче более 0,3 мм/об и значении силы резания более 350 Н на поверхности детали появляются прижоги, однако при обработке с малыми скоростями резания и подачей 0,1 мм/об наблюдаются вырывы частиц наполнителя. Установлено, что на рост величины дефектного слоя наибольшее влияние оказывает подача. Так, при ее изменении с 0,1 до 0,71 мм/об его величина увеличивается в 2–3,7 раза для разных типов пластин.
Вработе Е.Б. Бондарь [10] предложена модель оптимизации при точении стеклопластика твердосплавными резцами ВК8, позволяющая определять режимы резания, марку твердого сплава и тип режущей пластины, обеспечивающие максимальную производительность или минимальную себестоимость обработки.
Различные аспекты обработки полимеров и композитов резанием представлены в ряде российских и зарубежных научных публикаций [11–20].
Вработе Е.Н. Белецкого [11] приведены результаты моделирования силового взаимодействия режущего клина инструмента
идетали применительно к сверлению спиральными сверлами композитных углепластиков ФУТ и УГЭТ. Установлено, что задний угол сверла должен быть больше угла наклона между касательной к деформированной поверхности заготовки и направле-
25
нием скорости резания, который зависит от упругих свойств обрабатываемого материала. Предложена формула для расчета заднего угла. Отличительной особенностью данной модели, в отличие от известных моделей, разработанных для процесса резания металлов, является учет упругих деформаций, которые в случае обработки пластиков имеют существенное значение.
Вработе О.Ю. Еренкова [12] рассмотрена обработка точением капролона и фторопласта Ф-4. Изучен характер разрушения обрабатываемого материала в зоне резания, получены экспериментальные зависимости коэффициента усадки стружки от режимов резания (скорость резания, подача, глубина) при точении. При увеличении скорости резания от 100 м/мин до 300 м/мин коэффициент усадки стружки (укорочения, утолщения) уменьшается с 2 до 1,8 для обоих материалов. При увеличении глубины резания от 0,5 до 5 мм коэффициент усадки стружки уменьшается: для капролона от 1,9 до 1,2; для фторопласта Ф-4 от 2,8 до 1,3. При увеличении подачи от 0,08 до 0,28 мм/об коэффициент усадки стружки уменьшается: для капролона от 2,3 до 1,6; для фторопласта Ф-4 от 2,6 до 1,2. Автор объясняет эти закономерности тем, что при срезании большего объема материала меняется соотношение между напряжениями сдвига и сжатия в деформируемом объеме.
Вработе Ю.М. Зубарева [13] рассмотрена обработка фрезерованием стеклопластика СТЭТ (стеклоткань Т-10, Т-11 и эпоксидная связка) и углепластика УГЭТ (фенолформальдегидная матрица, армированная углеродным волокном «УРАЛ»). Рассмотрен характер деформационных процессов в зоне резания. Представлены фотографии микроструктуры стружек и характера износа режущей кромки инструмента. Стружка образуется путем хрупкого разрушения.
Вработе [14] приведены современные научные представления о свойствах и механике композиционных материалов, в частности о полимерных композиционных материалов (ПКМ). Приведены зависимости для расчета прочности (продольное растяжение и сжатие) композиционных порошковых материалов
26
с матричной структурой и композиционных материалов, армированных дискретными волокнами.
Вработе P.R. Ravikanth [17] рассмотрена обработка точени-
ем углепластика CFRP (Carbon Fiber Reinforced Plastic) твердо-
сплавным резцом. Автор представил результаты оптимизации режимов резания для получения минимальных значений шероховатости обработанной поверхности. Установлено, что оптимальные параметры шероховатости дает точение на следующих режимах резания: число оборотов шпинделя 600 об/мин (диаметр детали 50 мм), подача 0,05 мм/об, глубина 1 мм.
Вработе K. Surinder [18] рассмотрена обработка точением стеклопластика GFRP (Glass Fiber Reinforced Plastic) с использова-
нием алмазного инструмента PCD (PolyCrystalline Diamond). Исследована зависимость шероховатости обработанной поверхности от параметров режущей части инструмента и режимов резания. Установлено, что при изменении радиуса округления режущей кромки (0,4; 0,8 мм) и переднего угла (–6°; 0°; 6°) инструмента изменение параметра шероховатости Ra обработанной поверхности находится
впределах 1,7–1,8 мкм, т.е. является незначительным. При увеличении подачи от 0,05 до 0,2 мм/об шероховатость Ra увеличивается от 1,6 до 2,3 мкм. При увеличении скорости резания от 50 до 160 м/мин и глубины резания от 0,2 до 1,4 мм шероховатость незначительно увеличивается – от Ra = 1,7 мкм до Ra = 2,0 мкм.
Коммерческие организации, являющиеся поставщиками импортных пластиков, не дают в полном объеме рекомендаций по их обработке.
Анализ работ [1–20] по механической обработке полимерных материалов и композиций на их основе свидетельствует о необходимости систематизации сравнительных результатов по влиянию структуры и природы полимеров на технологические параметры их механической обработки и показатели качества обработки изделий. Объектом теоретических и экспериментальных исследований процессов механической обработки ПКМ в большинстве работ являются волокнистые углепластики, органо-
27
пластики и стеклопластики, при этом число работ, связанных с технологическими исследованиями процессов резания ПКМ, армированных дискретными частицами, весьма ограничено.
2.2. Особенности обработки пластиков
Механическая обработка пластиков используется для обеспечения современных конструкторско-технологических требований к деталям, которые невозможно обеспечить методами первоначального формообразования(прессование, экструдирование, спекание).
Поскольку для конструктивно сложных деталей (или малого объема выпуска) нецелесообразно готовить специальную оснастку для первоначального формообразования, детали из пластиков изготавливают механической обработкой на обычном металлообрабатывающем оборудовании.
На качество механической обработки пластиков оказывают влияние характеристики применяемого оборудования и технологической оснастки, режущего инструмента, режимов резания, технологических условий в зоне резания, конструктивные особенности обрабатываемой детали.
Результаты экспериментальных исследований [1–20] показывают, что при обработке пластиков нужно использовать острую режущую кромку, чтобы избежать подмятия обрабатываемого материала под режущий клин.
На точность обработки пластиков существенное влияние оказывают конструктивные особенности деталей, такие как длина обработки (вылет от шпинделя) и толщина стенок детали, поскольку пластики обладают повышенной упругой деформацией (малой жесткостью). Вследствие этого при проектировании операции следует предусматривать технологические способы повышения жесткости детали при обработке: люнеты, пробки, ребра жесткости. Зажим в приспособлении тонкостенных деталей необходимо осуществлять с равномерным усилием по всей площади тонкостенного конструктивного элемента.
Для обеспечения точности размеров необходимо учитывать температурные деформации пластиков, которые возникают при
28
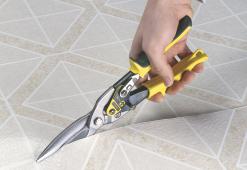
нагреве детали в процессе обработки и последующем охлаждении. Для уменьшения температурных деформаций применяют жидкостное или воздушное охлаждение. Поскольку большинство пластиков отличаются высоким коэффициентом теплового расширения, контроль размеров осуществляют на охлажденных деталях.
Пластики сильно подвержены возникновению остаточных напряжений в поверхностном слое детали, что приводит к существенным по сравнению с металлами деформациям. Для снятия остаточных напряжений детали из пластиков рекомендуется подвергать термообработке (отпуск), после которой выполняют окончательные операции.
2.3.Механическое разрезание пластиков
2.3.1.Разрезание ножами
Разрезание ножами применяется для разрезания пластиков в виде листов небольшой толщины либо в форме лент. Термопласты и реактопласты режутся одинаково хорошо.
При разрезании тонколистового пластика для обеспечения качества разреза нужно, чтобы плоскость лезвий ножниц была перпендикулярна плоскости листа.
Рис. 2.1. Резание пластика ручными ножницами
Резание ручными ножницами (рис. 2.1) осуществляется по принципу действия режущего клина на обрабатываемый материал.
29
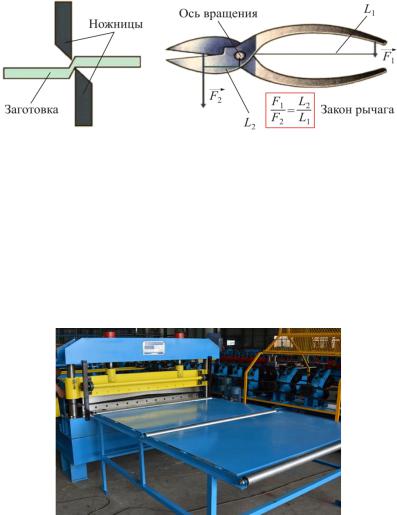
Для того чтобы уменьшить усилие, прилагаемое для разрезания материала, в ножницах используется принцип рычага (рис. 2.2). Кроме того, разрезание лучше выполнять небольшими резами, особенно в случаеразрезания сложного профиля.
Рис. 2.2. Принцип рычага: L1 – длинное плечо; L2 – короткое плечо
С целью автоматизации процесса резки в промышленных масштабах используют различные виды станков для листовой резки материала (рис. 2.3), которые используют различные виды ножей (рис. 2.4). Элементы из листового пластика определенного фиксированного размера получают путем периодического движения ножей в вертикальном направлении (гильотина) или путем вращения режущего инструмента (диски). Разрезание вращающимися дисками является болеепроизводительным процессом, чемразрезаниеножами.
Рис. 2.3. Станок для резки листов с гильотинными ножами
30