
книги / Механическая обработка пластиков
..pdf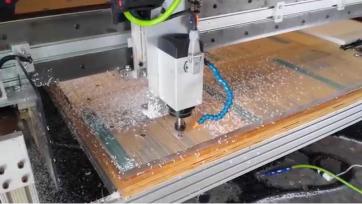
резание осуществлялось вдоль слоев, а не поперек. Это позволяет избежать сколов и получить более чистую поверхность.
2.6. Обработка пластиков осевым инструментом
2.6.1. Сверление деталей из пластиков
Сверление отверстий в деталях из пластиков можно осуществлять на обычных металлорежущих станках, вертикальносверлильных (рис. 2.16), токарных, фрезерных. Также можно применятьэлектрическиеипневматические дрели.
Основной проблемой при обработке сверлением пластиков, особенно твердых и слоистых, является скалывание кромок детали при выходе сверла. Чтобы избежать сколов, рекомендуется подкладывать на выходном торце детали пластины из дерева или пластика. Также можно разработать специальное кондукторное приспособление с подкладкой-кольцом на выходную кромку отверстия. При сверлении отверстий в тонких деталях можно обрабатывать их пакетом, зажимая в тисках.
Рис. 2.16. Сверление отверстия в оргстекле
В зависимости от обрабатываемости резанием конкретной марки пластика сверление может осуществляться быстрорежу-
51
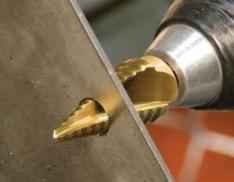
щими и твердосплавными сверлами. В зависимости от условий обработки могут быть использованы как стандартные сверла, так и сверла со специальными конструкциями. Например, для сверления отверстий небольшой глубины можно использовать универсальное ступенчатое сверло «елочка» (рис. 2.17). При сверлении пластиков силы резания незначительны, поэтому можно использовать сверла с сердечником небольшой толщины.
Рис. 2.17. Ступенчатое сверло «елочка»
С целью уменьшения трения по задней поверхности режущего клина сверла задний угол делают ступенчатым, т.е. на задней поверхности клина делают ленточку. Также с целью снижения трения направляющих кромок сверла можно уменьшать ширину кромок и увеличивать обратную конусность сверла.
Поскольку пластики обладают повышенными упругими свойствами, при сверлении отверстий в деталях из пластиков наблюдается значительная усадка размеров отверстий. Величина усадки зависит от параметров обработки и свойств обрабатываемого пластика, поэтому при наладке операции сверления необходимо заранее экспериментально определить величину усадки отверстия и учесть ее при выборе диаметра сверла.
Некоторые пластики, особенно твердые и слоистые, склонны к образованию трещин при больших усилиях резания, поэтому
52
для сверления отверстий больших диаметров рекомендуется разбить операцию на несколько проходов, начиная со сверления маленького диаметра, а затем рассверливая его постепенно на более большие, вплоть до требуемого. При небольшой глубине отверстия также хорошо подойдет ступенчатое сверло «елочка».
При сверлении отверстий в деталях из пластиков рекомендуется делать обдувку зоны резания струей сжатого воздуха с целью охлаждения сверла и его очистки от продуктов резания. Стружка при резании может походить на сливную или быть в виде порошкообразных частиц. При сверлении глубоких отверстий можно использовать стратегию периодического вывода сверла с поливом водоэмульсионной СОЖ.
При обработке отверстий в реактопластах нужно более внимательно подбирать геометрию инструмента и режимы резания, так как почти все материалы данного типа пластиков являются труднообрабатываемыми. Наибольшие трудности возникают, если ведется обработка глубоких отверстий втекстолитах и стеклопластиках.
В качестве осевого инструмента обычно применяются стандартные сверла, зенкера и развертки, с режущей частью из быстрорежущих сталей или твердых сплавов. Однако при обработке труднообрабатываемых композитных пластиков, когда условия в зоне резания слишком тяжелые, могут потребоваться специальные конструкции осевого инструмента.
Например, узкая канавка стандартных сверл часто приводит к тому, что в ней застревает мелкая пылевидная стружка. Ввиду этого на сверле может потребоваться сделать более широкую стружечную канавку. Это возможно сделать на стандартном сверле, поскольку при обработке пластиков возникают гораздо меньшие силы резания, чем при обработке металлов, и таким образом, ослабленное поперечное сечение сверла не окажет влияния на его прочность при резании.
На качество резания реактопластов оказывает влияние угол при вершине сверла, который рекомендуется назначать в пределах значений 50 –60 . При данных параметрах геометрии сверла
53
наблюдается его наименьший износ, поскольку осевая составляющая силы резания уменьшается, на единицу длины режущей кромки приходится меньшая нагрузка. При выходе сверла из обрабатываемого материала значительно уменьшаются или полностью исчезают явления выкрашивания кромки отверстия.
Рекомендации по режимам резания и геометрии инструмента для сверления наиболее распространенных марок пластиков представлены в табл. 2.4.
Таблица 2.4
Сверление пластиков
|
Геометрия |
Скорость |
|
||
Марка обрабатываемого |
инструмента |
Подача, |
|||
пластика, аббревиатура |
|
|
резания, |
мм/об |
|
Передний |
Задний |
||||
м/мин |
|||||
|
угол, ° |
угол, ° |
|
||
|
|
|
|||
Полипропилен, PP |
10–20 |
5–15 |
50–150 |
0,1–0,3 |
|
Полифенилен, PPE |
10–20 |
8–10 |
50–100 |
0,2–0,3 |
|
Полиоксиметилен, POM |
15–30 |
5–10 |
50–200 |
0,1–0,3 |
|
Полиамид, PA |
10–20 |
5–15 |
50–150 |
0,1–0,3 |
|
Полиэтилентерефталат, PET |
10–20 |
5–10 |
50–100 |
0,2–0,3 |
|
Поликарбонат, PC |
10–20 |
8–10 |
50–100 |
0,2–0,3 |
|
Политетрафторэтилен, PTFE |
5–20 |
10–16 |
150–200 |
0,1–0,3 |
|
Полиэфиримид, PEI |
10–20 |
3–10 |
20–80 |
0,1–0,3 |
|
Полисульфон, PSU |
10–20 |
3–10 |
20–80 |
0,1–0,3 |
|
Полифениленсульфид, PPS |
10–30 |
5–10 |
50–200 |
0,1–0,3 |
|
Полиэфирэфиркетон, PEEK |
10–30 |
5–10 |
50–200 |
0,1–0,3 |
|
Полиимид, PI |
5–10 |
5–10 |
80–100 |
0,02–0,1 |
|
Армированные полимеры* |
5–10 |
6 |
80–100 |
0,1–0,3 |
Примечание: * Полимеры, армированные (наполненные) стекловолокном, углеволокном, графитом и другим, необходимо обрабатывать твердосплавным инструментом.
2.6.2. Зенкерование и развертывание деталей из пластиков
Операции зенкерования и развертывания используют после операции сверления в том случае, если необходимо повысить точностьразмеровотверстияи качество обработаннойповерхности.
54
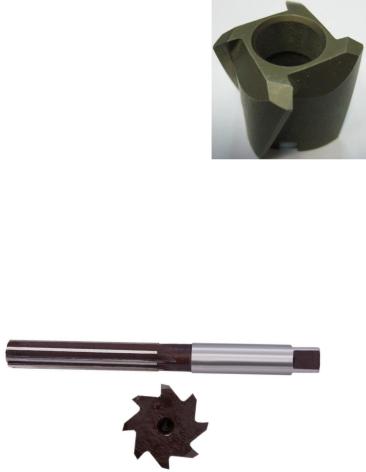
Зенкерование считается получистовой операцией. Зенкер (рис. 2.18) отличается от сверла более высокой жесткостью и большим числом режущих зубьев, что обеспечивает большую жесткость зенкера по сравнению со сверлом и, соответственно, лучшее качество обработки. Если при сверлении отверстий получают точность раз-
меров по 12–14-му квалитетам, а шеро- Рис. 2.18. Зенкер насадной ховатость Ra порядка 12,5 мкм, то при
операции зенкерования получают точность размеров по 9–11-му квалитетам, а шероховатость Ra порядка 3,2 мкм.
Для чистовых, финишных операций обработки отверстий применяется развертывание, которое осуществляется развертками (рис. 2.19). При операции развертывания получают точность размеровпо 6–8-му квалитетам, ашероховатость Ra порядка 0,63 мкм.
Рис. 2.19. Развертка цилиндрическая
Зенкерование и развертывание отверстия в деталях из пластиков целесообразно проводить в одной операции разными переходами, т.е. за одну установку, чтобы обеспечить соосность инструментов при обработке. Необходимо применять кондукторные приспособления для обеспечения точности.
Какправило, зенкерыиразверткисмазываютмаслянымиСОЖ.
55
При выборе конструкции зенкеров для обработки отверстий в деталях из пластиков нужно учитывать физико-механические особенности пластиков: усадку отверстий, упругие деформации и тепловое расширение пластика.
При резании пластиков важно иметь острый режущий клин, что достигается большими значениями переднего и заднего углов инструментов.
При зенкеровании и развертывании отверстий в деталях из композитных пластиков, содержащих абразивные частицы, нужно особенно внимательно следить за износом инструмента, так как при потере остроты режущей кромки возможны выпадения частиц абразива под площадку износа по задней поверхности инструмента, в результатечегонаобработаннойповерхностимогутпоявитьсяриски.
2.6.3. Нарезание резьбы метчиками
Основной особенностью нарезания резьбы метчиками в пластиках является возникновение риска застревания метчика в детали из-за больших сил упругости, характерных для пластиков. Ввиду этого конструкции метчиков для обработки пластиков имеют свои особенности: минимальное число зубьев (2–3 зуба), широкие стружечные канавки.
Геометрические параметры метчиков выбираются в зависимости от марки обрабатываемого пластика и точности резьбы. Режимы резания назначаются минимальными, чтобы избежать поломок метчиков, особенно при выкручивании из детали. По этой же причине нарезание резьбы метчиками малых диаметров лучше проводить вручную воротком.
Для снижения сил трения при резании и предотвращения застревания метчиков в детали рекомендуется смазывать метчики масляными СОЖ.
Для обеспечения требуемой точности резьбы рекомендуется крепить метчик в плавающем патроне, что позволяет метчику точно самоустанавливаться по оси отверстия.
56
Из-за повышенных упругих свойств пластиков необходимо учитывать величину усадки размеров резьбы после обработки. Для компенсации усадки необходимо увеличивать диаметр сверла, используемого для получения предварительного отверстия под резьбу, а также наружный и средний диаметр метчика.
2.7.Абразивная обработка пластиков
2.7.1.Шлифование деталей из пластиков
Вязкие пластики практически не поддаются обработке шлифованием, шлифование применяется только для обработки твердых пластиков. Особенно эффективно шлифование труднообрабатываемых композитных пластиков, содержащих в своем составе абразивные элементы, поскольку лезвийный инструмент при обработке таких пластиков интенсивно изнашивается. Таким образом, шлифование может стать хорошей альтернативой лезвийной обработке. Шлифование деталей из твердых пластиков применяют на чистовых операциях для получения высокой точности размеров (5–7-й квалитеты) и шероховатости обработанной поверхности (Ra = 0,63…1,25 мкм), а также для черновых операций.
Для шлифования пластиков используют обычные металлорежущие станки (круглошлифовальные, плоскошлифовальные, лен- точно-шлифовальные) и ручной инструмент (рис. 2.20). Обработка пластиков ведется различными методами шлифования: плоское шлифование периферией или торцом круга; круглое наружное шлифование в центрах; внутреннее шлифование; бесцентровое наружное и внутреннее шлифование; ленточное шлифование.
Для шлифования используют шлифовальные круги, ленты, шкурки, пасты. Шлифовальные круги состоят из абразивного материала природного или искусственного происхождения, в основном представляющего собой минералы высокой твердости (алмаз, корунд, кварц). Алмазные круги имеют высокую твердость и абразивные свойства, хорошую теплопроводность. Корунд – это кристаллический оксид алюминия Al2O3, активно ис-
57
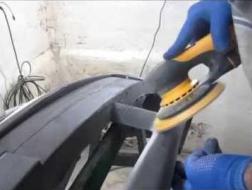
пользуется для производства шлифовальных кругов и паст. Кварц используют для производства абразивных шкурок.
Рис. 2.20. Шлифование пластикового бампера
Для качественного шлифования деталей из термопластов рекомендуется выбирать достаточно хрупкий абразив (алмаз) и достаточно хрупкую и пористую связку (керамическую), чтобы обеспечить процесс самозатачивания шлифовального круга, который позволит избежать засаливания круга и термодеструкции (прижогов) поверхности обрабатываемого пластика. Для чистовых операций выбирают более мелкую зернистость круга и меньшие режимы резания (особенно глубину). Возможно применение шлифовальных кругов с электрокорундом на бакелитовой связке. Шлифовальные ленты используют с карбидом кремния.
Для шлифования деталей из реактопластов (текстолиты, стеклопластики) рекомендуется использовать алмазные круги на бакелитовой связке зернистостью 16. При использовании корундовых и карборундовых абразивных кругов, даже при обработке менее твердых слоистых пластиков, круги быстро засаливаются, приводя к браку деталей и быстрому выходу из строя кругов.
Для обработки поливинилхлорида, волокнита, полистирола используют наждачные диски. Для обработки полиамидов, поли-
58
метилакрилата используют хлопчатобумажные (суконные) круги, намазанные шлифовальной пастой.
Режимы резания выбирают исходя из необходимости обеспечения требуемого качества деталей и максимальной производительности обработки. Окружную скорость резания можно назначать максимальную (30–35 м/с), определяемую прочностью выбранного шлифовального круга. Как правило, при шлифовании пластиков СОЖ не применяют.
2.7.2. Полирование деталей из пластиков
Полирование пластиков применяется для отделочной обработки поверхностей детали, т.е. получения блестящей глянцевой поверхности. При полировании удаляются неглубокие дефекты поверхности (риски, царапины). Полирование производится с помощью полировальных кругов и паст.
Полирование пластиков можно осуществлять механическим, термическим и химическим способами. Термическое полирование применимо только к термопластам, оно производится путем оплавления неровностей поверхности детали струей нагретого газа, что легко осуществимо благодаря низкой температуре плавления пластиков. Химическое полирование пластиков осуществляется путем воздействия специального химического вещества – растворителя, который небезопасен для человека. Наиболее распространенным и безопасным методом полирования пластиков остается механический метод.
В общем случае механическое полирование выполняется в три этапа: предварительное полирование, окончательное и глянцевание (протирка). Механическое полирование осуществляется на специальных полировальных станках (рис. 2.21) либо ручным инструментом.
На полировальных станках используют полировальные шайбы, которые состоят из нескольких слоев полировальных кругов, предназначенных для осуществления всех технологических переходов – от предварительного до окончательного полирования.
59
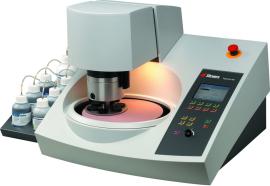
Рис. 2.21. Полирование пластика на специальном станке
Срок службы полировальных шайб обычно составляет 70–80 ч непрерывной работы. Износ полировальных кругов проявляется тем, что круги лохматятся, отдельные нити распускаются. Разлохматившиеся кромки кругов необходимо отрезать, в противном случае качество полировки может значительно снизиться. На полировальном станке полировальная шайба находится в защитном кожухе, который подключен к системе вытяжной вентиляции, поскольку износ полировальных кругов сопровождается выделением текстильной пыли и частиц вредных компонентов полировальных паст, например окиси хрома.
Рекомендованная частота вращения полировального круга для термопластов составляет 1000–1500 об/мин, для реактопластов – 1500–2000 об/мин. Для предварительного полирования применяют твердые прошитые полировальные круги (хлопчатобумажные, фланелевые, суконные), для окончательного – мягкие непрошитые (бязь, байка, муслин).
На операциях полирования применяют полировальные пасты, зернистость абразива которых должна уменьшаться от предварительного к окончательному полированию. Вместо паст могут применяться и абразивныепорошки, смешанные своскомили маслами.
Окончательное полирование совмещают с протиркой. Полировальную пасту наносят на одну половину полировального кру-
60