
книги / Механическая обработка пластиков
..pdf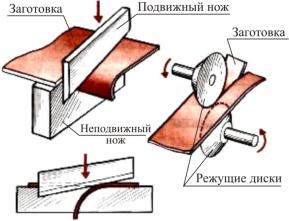
Рис. 2.4. Гильотинные и дисковые ножи
2.3.2. Разрезание абразивным инструментом
Абразивные круги можно использовать при точном разрезании пластика различного профиля (стержни, трубы, оконные профили). Получаемые детали имеют хорошие показатели точности размеров и шероховатости поверхности.
Для разрезания твердых пластиков, особенно имеющих в своем составе абразивные элементы, приводящие к быстрому износу режущего клина инструмента, целесообразно применять абразивные круги (рис. 2.5). Применение для разрезания твердых пластиков абразивных кругов обеспечивает высокую производительность обработки (частота вращения абразивного круга 500–3000 об/мин) и хорошее качество сечения среза, которое часто не требует дополнительной обработки.
Ограничением для применения абразивных кругов может стать повышенная чувствительность обрабатываемого пластика к температуре, а также высокая пластичность (мягкость), которая приведет к налипанию частиц пластика на абразивный круг.
При обработке термопластов нужно учитывать возможность перегрева пластика выше допустимых температурных значений в определенной приповерхностной зоне детали, контактирующей
31
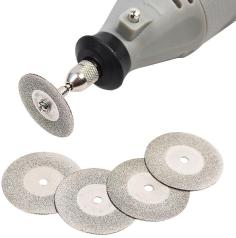
с кругом. Кроме того, при обработке всех типов пластиков повышенные тепловые потоки приводят к более значительным по сравнению с металлами температурным деформациям.
Рис. 2.5. Разрезание с помощью абразивных кругов
Для снижения температуры в зоне резания можно снижать режимы резания, применять СОЖ либо конструкции абразивных кругов, обеспечивающих отвод теплоты.
Применение СОЖ при разрезании пластика абразивными кругами часто необходимо, чтобы избежать засаливания круга и захватить абразивную пыль. При использовании в качестве СОЖ технической воды ее расход составит около 3 л/мин.
В некоторых случаях при разрезании пластиков абразивными кругами наблюдается явление самозатачивания круга. Поскольку связка также контактирует с обрабатываемым пластиком, это приводитк ееистиранию и выпадению изношенных зерен абразива.
2.3.3. Разрезание дисковыми пилами (дисковыми фрезами)
Разрезание пластиков дисковыми пилами (рис. 2.6) целесообразно при разрезе по прямым линиям, когда нет повышенных требований к качеству кромок. Дисковые пилы хорошо зареко-
32
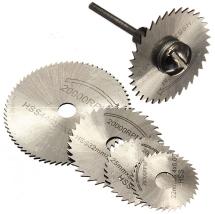
мендовали себя при разрезании винипласта, полистирола, фибры. Обычно используют дисковые пилы диаметром 20–100 мм из быстрорежущей стали.
Рис. 2.6. Разрезание с помощью дисковых пил
Пластики чувствительны к биению дисковой пилы, поэтому необходима качественная посадка дисковой пилы на шпиндель и проверка на величину биения. В случае слишком большого биения увеличиваются неровности на поверхности среза заготовки, а также возможны серьезные деформации, борозды и вырывы значительных кусков материала на выходе зубьев дисковой пилы из обрабатываемого пластика.
При разрезании пластика дисковыми пилами, как и при обработке любым лезвийным инструментом, важно, чтобы режущая кромка зубьев пилы была остро заточенной. Это обеспечивается заданием больших значений переднего и заднего углов инструмента. Также важно следить за величиной износа зубьев и своевременно осуществлять их переточку.
При разрезании твердых и композитных пластиков может потребоваться использование СОЖ для более эффективной работы.
33
При разрезании слоистых реактопластов рекомендуется использовать дисковые пилы, предназначенные для деревообработки. При разрезании листа рекомендуется делать между листом и столом станка подкладки из твердых материалов, чтобы избежать растрескивания кромок.
К недостаткам метода можно отнести наличие шума (в отдельных случаях сильный визг пилы) и пыли при разрезании пластиков.
Не рекомендуется разрезание дисковыми пилами очень твердых композитных пластиков, например стеклопластиков, так как обрабатываемыйматериал крошится, а стойкость пилы небольшая.
При разрезании пластиков также используют дисковые фрезы. Разрезание производится на горизонтально-фрезерных станках. При фрезеровке пластика стружка более интенсивно забивает стружечные канавки, поэтому необходимо углублять стружечные канавки или убирать зубья через один. Для обработки твердых и композитных пластиков, таких как гетинакс, текстолит, стеклопластик, рекомендуется применять твердосплавные дисковые фрезы, обеспечивающие хорошую стойкость.
2.3.4. Разрезание ленточными пилами
Разрезание пластиков ленточными пилами (рис. 2.7) целесообразно применять, когда требуется делать разрезы большой толщины (более 25 мм) или разрезать криволинейные контуры.
Для разрезки применяют обычные ленточные пилы, используемые в металлообработке. Поскольку для лезвийного инструмента при обработке пластиков нужна острая режущая кромка, можно выбирать пилы, рекомендованные для резки цветных металлов. Ширина полотна ленточной пилы выбирается в зависимости от толщины разреза. Например, при толщине разреза 10 мм полотно пилы должно быть толщиной не менее 2 мм, а при толщине разреза 30 мм – не менее 6 мм.
Ленточные пилы хорошо отводят тепло от зоны резания, поэтому в большинстве случаев применение СОЖ не требуется.
34
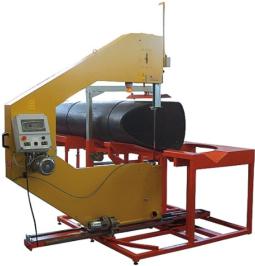
Рис. 2.7. Разрезание с помощью ленточных пил
Таблица 2.1
Пиление пластиков
Марка обрабатываемого |
Геометрия инструмента |
Скорость |
||
Передний |
Задний |
Шаг |
резания, |
|
пластика, аббревиатура |
угол, ° |
угол, ° |
зубьев, мм |
м/мин |
|
||||
Полипропилен, PP |
2–5 |
20–30 |
3–8 |
500 |
Полифенилен, PPE |
5–8 |
15–30 |
3–8 |
300 |
Полиоксиметилен, POM |
0–5 |
20–30 |
2–5 |
500–800 |
Полиамид, PA |
2–5 |
20–30 |
3–8 |
500 |
Полиэтилентерефталат, PET |
5–8 |
15–30 |
3–8 |
300 |
Поликарбонат, PC |
5–8 |
15–30 |
3–8 |
300 |
Политетрафторэтилен, PTFE |
5–8 |
20–30 |
2–5 |
300 |
Полиэфиримид, PEI |
0–4 |
15–30 |
2–5 |
500 |
Полисульфон, PSU |
0–4 |
15–30 |
2–5 |
500 |
Полифениленсульфид, PPS |
0–5 |
15–30 |
3–5 |
500–800 |
Полиэфирэфиркетон, PEEK |
0–5 |
15–30 |
3–5 |
500–800 |
Полиимид, PI |
0–3 |
5–10 |
10–14 |
800–900 |
Армированные полимеры* |
10–15 |
15–30 |
3–5 |
200–300 |
Примечание: * полимеры, армированные (наполненные) стекловолокном, углеволокном, графитом и другим, необходимо обрабатывать твердосплавным инструментом.
35
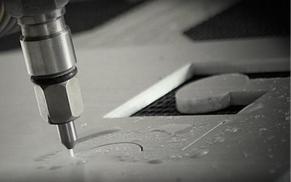
К недостаткам метода можно отнести небольшую точность размеров и шероховатости поверхности разреза.
Рекомендации по режимам резания и геометрии инструмента для пиления наиболее распространенных марок пластиков представлены в табл. 2.1.
2.3.5. Гидроабразивная резка
Одним из современных методов разрезания пластиков является гидроабразивная резка (рис. 2.8), которая представляет собой резание обрабатываемого материала струей жидкости с примесью абразива под высоким давлением. Экспериментально установлено, что обработка с помощью тонких струй (диаметром 0,1–0,2 мм) при высоком давлении (около 1000 кгс/см2) дает качественный результат при резке листовых пластиков.
Рис. 2.8. Гидроабразивная резка
Эффективность процесса гидроабразивной резки зависит от ряда факторов, таких как энергетические параметры гидроабразивной струи (давление гидроабразивной струи, диаметр сопла и расстояние между соплом и поверхностью детали), интенсивность разрушения материала в зоне резания (скорость подачи детали относительно гидроабразивной струи, толщина и ширина реза), фи- зико-механические свойства обрабатываемого материала.
36
При увеличении давления истечения гидроабразивной струи и уменьшении диаметра сопла производительность процесса гидроабразивной резки увеличивается, при этом шероховатость обработанной поверхности уменьшается.
В результате гидроабразивной резки пластиков в качестве продуктов резания остается порошкообразная масса из мелких частиц пластика.
Гидроабразивная резка листовых пластиков представляет собой сложный гидродинамический процесс. Скорость гидроабразивной струи уменьшается по мере ее удаления от сопла, при этом часть струи распыляется, а часть сохраняет плотность и направление движения, таким образом, часть струи совершает полезную работу, а часть теряет энергию, распыляясь в прилегающих слоях воздуха. На поверхности струи образуются пульсирующие волны и турбулентность. Для обеспечения максимальной эффективности и производительности гидроабразивной резки необходимо подобрать оптимальные параметры гидроабразивной струи, которые зависят от давления истечения и диаметра сопла.
Кдостоинствам метода можно отнести высокую производительность и качество обработки, возможность разрезки любого фигурного профиля, низкий шум и отсутствие запыленности рабочего места.
Кнедостаткам метода относится ограничение по толщине реза, так как при увеличении толщины реза энергозатраты на формирование требуемой струи резко увеличиваются, а качество поверхности реза уменьшается.
При разрезании полимерных композиционных материалов гидроабразивной струей может наблюдаться интенсивное разрушение частиц менее прочной части композиции и свободное вымывание отделившихся от матрицы частиц более прочной части композиции. Таким образом, гидроабразивная резка при обработке труднообрабатываемых композитных пластиков, приводящих
кинтенсивному абразивному износу лезвийного инструмента, может стать максимально эффективным методом обработки.
37
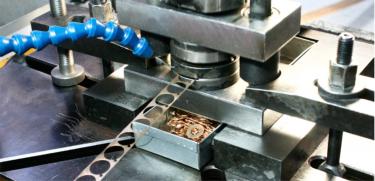
2.3.6. Разрезание штамповкой
Пластики являются одними из самых лучших материалов для штамповки благодаря своим пластичным свойствам. С помощью современного оборудования можно создать любые пластиковые элементы самого сложного профиля и узора. Для разделительной штамповки обычно используют листовые и рулонные заготовки. При разделительной штамповке осуществляют отрезку деталей, вырубку по контуру, пробивку отверстий и пазов, формирование сложных поверхностей.
В качестве оборудования для различных операций разделительной штамповки пластиков используют прессы. Для штамповки простых пластиков обычно достаточно использовать простые модели прессов усилием 10–50 кН, так как предел прочности этих пластиков очень маленький, а пластичность большая. Для штамповки композитных пластиков, особенно прочных, могут потребоваться прессы усилием 50–1000 кН.
Рис. 2.9. Вырубка на эксцентриковом прессе
Разделительную штамповку деталей из пластиков, имеющих простую конфигурацию, можно осуществлять на кривошипных и эксцентриковых прессах (рис. 2.9), в том числе ручных. Разделительная штамповка деталей из пластиков, имеющих сложную
38
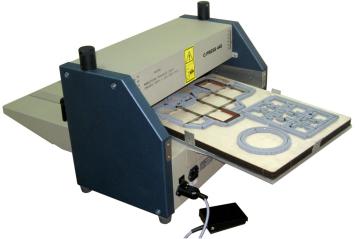
Рис. 2.10. Фигурная штамповка на гидравлическом прессе
конфигурацию, при повышенных требованиях к точности размеров, осуществляется на гидравлических прессах (рис. 2.10), так как при равномерном и плавном приложении нагрузки качество штамповки выше, чем при ударном. Также на прессе возможна разделительная штамповка листовых деталей из пластика многослойными пакетами. В некоторых случаях осуществляется предварительный подогрев заготовки из пластика.
2.4.Точение пластиков
2.4.1.Особенности точения деталей из пластиков
Токарная обработка является самым распространенным методом лезвийной обработки деталей. Точением получают детали из пластиков, имеющие форму тел вращения: валы, диски, трубы, втулки, кольца и др. Точение пластиков осуществляют на металлообрабатывающих станках, применяя металлорежущий токарный инструмент (для резания пластиков важно, чтобы режущая кромка инструмента была остро заточенной).
39
Поскольку пластики обладают значительно меньшей прочностью, чем металлы, при их точении возникают незначительные силы резания, что позволяет вести обработку с любыми сечениями среза на легком оборудовании с невысокими значениями мощности привода станка.
Заготовки в виде прутков и валов точат с зажимом в кулачках, при этом в месте зажима на заготовке из пластика могут остаться отпечатки от вдавливания в пластик прижимных поверхностей кулачков. Это связано с тем, что большинство пластиков, в том числе и композитных, являются очень мягкими и необходимое усилие зажима, даже осуществленное по большой площади поверхности детали, в большинстве случаев оставляет значительные вмятины. Исходя из этого важно разработать технологию точения деталей из пластиков, предусматривающую отсутствие таких поврежденных участков на готовой детали. Например, можно после обработки последним технологическим переходом осуществлять отрезку детали от прутковой заготовки.
Заготовки в виде дисков и колец необходимо закреплять в цанговых патронах или специальных оправках. Важно помнить, что большинство пластиков обладают ярко выраженными упругими и пластичными свойствами, поэтому необходимо обеспечить равное усилие зажима по всей посадочной поверхности детали, чтобы минимизировать коробление после снятия готовой детали из приспособления.
Кроме обычных деталей, токарной обработкой из пластиков можно получать такие изделия, как пленочные ленты, для производства которых используют специальные токарно-лущильные станки. Ленту-пленку (целлулоидную пленку, ленту ФУМ) получают из цилиндрической заготовки путем радиальной подачи ножевого резца. Чтобы обеспечить постоянство толщины пленки, необходимо постоянство скорости и усилия резания. Поскольку диаметр заготовки при срезании пленки постепенно уменьшается, для сохранения постоянной скорости резания число оборотов шпинделя должно постепенно увеличиваться, что обеспечивается
40