
книги / Структурные механизмы деформирования и разрушения
..pdfДанные методы являются чувствительными к размеру обрабатываемых данных: чем больше длина вектора, тем меньше погрешность. При этом объем данных особенно влияет на результаты вычислений методами определения вероятности первого возвращения высоты и мультивероятности, а также методом фурье-анализа профилей. Последний является наиболее точным. Вследствие того, что использование различных методов нахождения фрактальной размерности может давать как завышенный, так и заниженный результат, как указано в работе [6], необходимо применять несколько методов для корректного определения фрактальных характеристик.
Одним из интенсивно изучаемых самоафинных объектов является свободная поверхность, образующаяся при прохождении трещины. Как показано в работе [4], профили поверхности трещины обладают свойством самоафинности на широком спектре масштабов (диапазон от 5 нм до 0,5 мм) и соответствуют величине показателя шероховатости порядка 0,8. Автором работы [4] сделан вывод об универсальности значения H ≈0,8 как для различных материалов (стекло, металлы, керамика), так и различных условий образования трещин (усталостные, коррозия под нагрузкой и т.д.). Более того, им обнаружено наличие двух универсальных значений показателя шероховатости: для данной макроскопической скорости распространения трещины νm на масштабах, меньших некоторого значения r ˂ξc(νm), наблюдается режим скейлинга с H ≈0,5, тогда как при r ˂ξc(νm) значение H ≈0,8. Масштаб ξc(νm), на котором наблюдается переход от одного режима скейлинга к другому, становится неразрешимо малым для больших скоростей vm, соответствующих динамическому нагружению. В этом смысле значение H ≈0,5 отвечает режиму начального роста трещины, когда фронт трещины распространяется с малой скоростью, тогда как H ≈0,8 соответствует быстрому распространению трещины – так называемый «незакрепленный» режим движения фронта трещины. Автор [4] выделяет три различных показателя шероховатости: первый описывает структуру в направлении,
21
перпендикулярном распространению трещины, второй – параллельно ему и третий соответствует шероховатости плоскости фронтатрещинывпроцессераспространенияеечерезматериал.
В работе [4] отмечено, что при росте трещины через материал искажения плоскости фронта трещины, вызванные локальной неоднородностью структуры, распространяются в виде упругих волн. Эти волны могут двигаться как вдоль фронта растущей трещины, тем самым они влияют на морфологию плоскости разрушения, так и (как показали недавние исследования) вне этой плоскости. В идеальном материале, где отсутствуют неоднородности, фронт трещины является прямой линией и распространяется в плоскости с постоянной скоростью, зависящей от коэффициента интенсивности напряжений. В неоднородном материале локальная скорость фронта трещины изменяется как в пространстве, так и во времени и отличается от макроскопической: при начальном режиме трещина движется прерывисто.
Неоднородность структуры проявляется в различии прочностных свойств различных участков материала. Одной из наиболее важных характеристик в этом смысле является энергия разрушения (скорость высвобождения энергии). Флуктуации данной величины в неоднородном материале могут вызывать: 1) локальное изменение скорости движения фронта трещины и, как следствие, изменение его формы; 2) изменение направления движения трещины, обусловленное микромеханикой процесса вблизи фронта трещины.
Изучение морфологии поверхности разрушения позволяет получить информацию о временной эволюции фронта трещины и определить коррелированность структуры, обусловленную прохождением волн напряжений. Проведенные эксперименты [4] для различных материалов при различных условиях нагружения были направлены на исследование режима распространения трещины, для которого наблюдается значение H ≈ 0,5, отвечающее случайному распределению неодно-
22
родностей. Было установлено, что амплитуда шероховатости не зависит от средней макроскопической скорости движения трещины, в отличие от верхней границы ξc по масштабам для данного режима. Этот эффект становится более существенным для малых скоростей движения трещины, ввиду роста влияния анизотропии.
В работе [4] говорится о недавних экспериментах по наблюдению изменений фронта трещины, вызванных дефектами поверхности и распространяющихся на значительные расстояния. Эти изменения включают в себя, помимо малоамплитудной составляющей, высокоскоростные импульсы изменения фронта трещины, распространяющиеся практически без изменения формы и обладающие свойством масштабной инвариантности. Автор утверждает, что такие подобные солитонам импульсы показывают важную роль нелинейных эффектов, несмотря на малую величину амплитуды. Нелинейные эффекты включают в себя деформации каквплоскоститрещины, такиперпендикулярно ей.
Среди методов, позволяющих корректно определять скейлинговые свойства поверхностей, помимо фурье-анализа профилей, следует отметить методы вычисления показателя Херста по трехмерным образам поверхности (метод переменного интервала, анализ корреляционной функции перепада высот, метод покрытия поверхности проекцией сетки). Применение данных методов позволяет получить информацию об особенностях морфологии всей поверхности, а не отдельных профилей, исследование которых может быть информативным только в ограниченном числе случаев.
23
2. ИССЛЕДОВАНИЕ ЗАКОНОМЕРНОСТЕЙ РАЗРУШЕНИЯ СУБМИКРОКРИСТАЛЛИЧЕСКИХ
ИПОЛИКРИСТАЛЛИЧЕСКИХ МАТЕРИАЛОВ
ВРЕЖИМЕ МНОГОЦИКЛОВОЙ И ГИГАЦИКЛОВОЙ УСТАЛОСТИ
2.1. Экспериментальные установки для проведения испытаний на гигацикловую усталость
и принцип их работы
Испытательные машины на усталость могут быть классифицированы по типу условий нагружения на исследуемом образце. Например, одноосное нагружение, изгиб, кручение или их комбинация (многоосное нагружение). Можно также классифицировать нагружающие машины по частоте испытаний. Например, для определения S−N кривой для металла в диапазоне до 108 циклов продолжительность испытаний при частоте работы машины 90 Гц может составлять около двух недель. Для описания усталостной кривой необходимо не менее 8 таких тестов, следовательно, общее время испытаний на одной усталостной машине может составить 8−10 недель. Таким образом, моделирование усталостного разрушения на высоких базах испытаний с использованием классических гидравлических или пневматических испытательных машин, работающих на частотах от 10 до 20 Гц, становитсянереальнодлительным[10, 11].
Разработка ультразвуковой испытательной установки позволила испытывать материалы с частотой нагружения до 20 кГц, значительно уменьшая время испытаний. Впервые такое оборудование было разработано профессором Батиасом [11].
Данная усталостная испытательная машина состоит из трех основных компонентов: генератора высокой частоты, пьезоэлектрического преобразователя и системы контроля смещения. На рис. 2.1 представленапринципиальнаясхемаустановки.
24
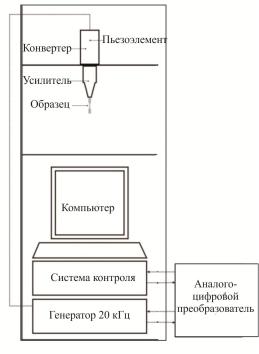
Рис. 2.1. Принципиальная схема ультразвуковой усталостной испытательной машины для R = –1 и комнатной температуры
•Ультразвуковой генератор. Силовой генератор, который трансформирует сигнал напряжения частотой 50–60 Гц в ультразвуковой синусоидальный сигнал частотой 20 Гц.
•Пьезоэлектрический преобразователь (конвертер). Преоб-
разователь трансформирует электрические колебания ультразвуковогогенераторавмеханическиетойжечастоты.
•Ультразвуковой усилитель. Ввиду того, что амплитуда колебаний пьезоэлектрического преобразователя очень мала (около 5 мкм), применяется ультразвуковой усилитель, увеличивающий амплитуду колебаний. Результат усиления зависит от геометрии усилителяиотполученногосигналаконвертера.
25
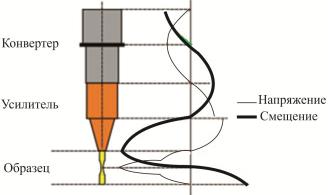
• Система контроля смещения. Испытание на усталость в ультразвуковом режиме контролируется системой контроля смещения. Эта система содержит компьютер, отвечающий за контроль смещения амплитуды и сбор данных. Сбор данных осуществляется аналого-цифровым преобразователем.
Генератор возбуждает конвертер, инициирующий периодические напряжения, усиливающиеся в волноводе (механический усилитель) [12]. Амплитуда смещения достигает своего максимума U0 на свободном торце образца, где она может быть измерена динамическим сенсором (рис. 2.2). Максимальное напряжение сосредоточено в центре образца (с коэффициентом асимметрии цикла R = –1). В течение ультразвукового усталостного испытания деформация может быть напрямую измерена с помощью закрепленных наповерхностиобразцатензодатчиков.
Рис. 2.2. Поля напряжений и смещений системы конвертер−усилитель−образец [12]
Вследствие того, что все компоненты системы находятся в упругой области нагружения, условия резонанса предполагают линейность связи напряжений и деформаций [12]. Непосредственно перед испытанием производится калибровка испытательной машины с использованием оптических, емкостных или тензометрических датчиков для обеспечения условий резонанса.
26

Номинальная резонансная частота вибраций нагружающего устройства близка к 20 кГц, и нарушение условий резонанса более чем 0,5 кГц является критерием остановки испытания, что связывается с образованием усталостной трещины. Таким образом, если система контроля обнаружит частоту менее 19,5 кГц, то тест будетостановлен.
Для классических усталостных испытаний эксперимент проводится на внешней рабочей частоте испытательной машины, которая, как правило, отличается от собственной частоты образца. Для ультразвуковых испытательных машин внешняя рабочая частота, поддерживаемая машиной, должна быть одной из собственных частот образца [13].
Испытания на гигацикловую усталость проводятся в диапазоне частот от 10 до 190 кГц, исследуемый материал предполагается изотропным и однородным в области линейных упругих деформаций, реализуемых в течение всего цикла нагружения. Напряжения выше предела пропорциональности (текучести), где деформационные зависимости обнаруживают выраженную нелинейность, не поддерживаются ультразвуковыми испытательнымимашинами[10].
Таким образом, на образцы, предназначенные для исследования гигацикловой усталости, накладываются определенные условия, чтобы они находились в резонансе с системой. Для того чтобы собственная частота колебаний цилиндрического образца совпадала с частотой колебаний машины, его длина из соображений волновой теории должна быть:
l |
1 |
|
Ed |
, |
(2.1) |
2 f |
|
||||
|
|
|
|
где l – длина цилиндрической части образца; f = ω/2π – частота, соответствующая первой гармонике колебаний; Ed – динамический модуль упругости исследуемого материала; ρ − плотность исследуемого материала. Резонансная длина для
27

первой моды колебаний цилиндрического образца, определяемая формулой (2.1), обратно пропорциональна частоте испытаний, что определяет верхний диапазон частот, реализуемый на макроскопических образцах [12]. Оптимальной частотой испытаний является 20 кГц, так как при больших частотах линейные размеры образцов становятся не представительными.
Для усталостных испытаний образцов с переменным сечением амплитуды напряжений и деформаций зависят от формы образца. Образцы для ультразвуковых усталостных испытаний имеют минимальное сечение в центре (рис. 2.3, а). Длина L1, называемая резонансной длиной, определяется в ходе численного решения. Образцы для изучения роста трещины при гигацикловых режимах (рис. 2.3, б) разрабатываются подобным образом, но с треугольным концентратором в центре образца для инициирования роста трещины.
а |
б |
Рис. 2.3. Геометрия образцов для испытаний на гигацикловую усталость: на выносливость (a) и на рост трещины (б) [12]
Сечение образца S(x) для геометрии, изображенного на рис. 2.2, а, определяется следующим образом:
S(x) R2 , |
L2 |
|
x |
|
|
L, |
|
|
|
|
(2.2) |
|||
|
|
|
|
|
|
|||||||||
S(x) R1 ch( x), |
|
|
x |
|
L2 , |
|
|
(2.3) |
||||||
|
|
|
|
|
||||||||||
|
|
1 |
|
|
|
|
|
|
R |
|
|
|
||
L L1 L2 , |
|
|
|
|
|
arsh |
|
2 |
|
, |
(2.4) |
|||
L2 |
|
R1 |
||||||||||||
|
|
|
|
|
|
|
|
|
|
|
||||
28 |
|
|
|
|
|
|
|
|
|
|
|
|
|

где S(x) – профиль сечения образца вдоль оси; x – координата; R2 – радиус цилиндрической части; L2 – половина длины суженной части образца; L – половина полной длины образца; R1 – радиус минимального сечения; L1 – длина цилиндрической части; – параметр скругления.
Из граничных условий (2.2)−(2.4) можно определить резонансную длину образца:
|
|
1 |
|
k |
k |
|
|
|
|
|
|
|
|
2 |
|
|
|
|
|||
|
|
L |
|
1 |
arctg |
1 |
|
ch( L ) th( L ) |
|
|
, |
(2.5) |
|||||||||
|
|
|
|
|
|
|
|||||||||||||||
где |
2 |
k 2 . Таким образом, решение уравнения колебаний |
|||||||||||||||||||
в образце |
|
|
|
|
|
|
|
|
|
|
|
|
|
|
|
|
|
|
|
|
|
|
|
|
|
|
|
|
|
|
2 |
|
|
|
|
|
|
|
|
|
(2.6) |
||
|
|
|
U (x) p(x)U (x) k U (x) 0 |
|
|
|
|||||||||||||||
в зависимости от геометрии будет иметь вид |
|
|
|
|
|
||||||||||||||||
|
|
U (x) A |
(L |
, L |
|
sh( x) |
|
|
|
|
L , |
|
|
(2.7) |
|||||||
|
|
) |
|
, |
x |
|
|
|
|||||||||||||
|
|
|
|
|
|||||||||||||||||
|
|
|
0 |
|
|
1 |
2 |
|
ch( x) |
|
|
|
|
2 |
|
|
|
|
|||
|
|
|
|
|
|
|
|
|
|
|
|
|
|
||||||||
|
|
U (x) A0 cos(k(L x)), L2 |
|
L, |
|
|
|
||||||||||||||
|
|
|
x |
|
|
(2.8) |
где U(x) – перемещения на поверхности образца в зависимости от продольной координаты x; A0 – константа;
(L |
, L |
) |
cos(kL1) ch( L2 ) |
. |
(2.9) |
|
|||||
1 |
2 |
|
sh(L2 ) |
|
|
|
|
|
|
Напряжение и деформация для минимального сечения цилиндрического образца в соответствии с этим решением следующее:
(x) A0 (L1, L2 )
29
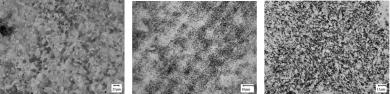
|
ch( x) ch( x) sh( x) sh( x) |
, |
|
(2.10) |
ch2 ( x) |
|
|||
|
|
|
|
|
|
(x) Ed A0 (L1, L2 ) |
|
|
|
|
ch( x) ch( x) sh( x)sh( x) |
, |
(2.11) |
|
|
ch2 ( x) |
|
|
|
где – деформация; – напряжения.
2.2. Исследуемые материалы
Исследования проводились для образцов чистого титана марки Grade-4 и сплава титана ВТ-6 (Ti6Al4V) в разных состояниях микроструктуры: исходного поликристаллического состояния, где средний размер зерна составлял 25 мкм; субмикрокристаллическое состояние УМЗ-1, средний размер зерен в котором составил 100 нм, и субмикрокристаллическое состояние УМЗ-2, в котором средний размер зерен 200 нм (рис. 2.4). Измельченное зерно было получено путем равноканального углового прессования с различными условиями термомеханической обработки.
а |
б |
в |
Рис. 2.4. СтруктуратитанаGrade-4 (изображения, полученныеоптическим металлографическим микроскопом): a – исходное состояние, размер зерна ≈25 мкм; б – состояние УМЗ-1, размер зерна ≈100 нм; в – состояние
УМЗ-2, размерзерна≈200 нм
30