
книги / Структурные механизмы деформирования и разрушения
..pdf
Образцы, предварительно подвергнутые механической полировке и химическому травлению в течение 10 с (реагенты, используемые в растворе для травления: HNO3 – 2 %, HF – 2 %, H2O – 96 %), исследовались в оптическом (металлографическом микроскопе и интерферометре-профилометре New View) и сканирующем электронном микроскопе. Механическая полировка осуществлялась кремниевыми полировальными кругами с размером зерна от 160 ед. на 1 см2 до 4000 ед. на 1 см2. Завершающая часть полировки проводилась на фетровых кругах с применением алмазных суспензий размером 6, 3 и 1 мкм на последнейстадии.
Химический состав сплава ВТ-6 определялся с помощью сканирующего электронного микроскопа Hitachi S-3400 по спектру излучения отраженных электронов (рис. 2.5): Al – 6,03 %, Ti – 89,56 %, V – 4,40 %. Как показал сканирующий электронный микроскоп, распределениеэлементовпо сплавуравномерно.
|
|
|
|
|
|
|
|
Ti |
|
|
|
|
|
|
Суммарный спектр |
|||
|
|
|
|
|
|
|
|
|
|
|
|
|
|
|||||
|
|
|
|
|
|
|
|
|
|
|
|
|
|
|
|
|||
|
Ti |
|
Al |
|
|
|
|
|
|
|
|
|
|
|
|
|||
|
|
|
|
|
|
|
|
|
|
|
|
|
|
|||||
|
V |
|
|
V |
|
|
|
|
|
|
|
|
||||||
|
|
|
|
|
|
|
|
|
|
|
||||||||
|
|
|
|
|
|
|
|
|
|
|
|
|
|
|
|
|||
|
|
|
|
|
|
|
|
Ti |
|
|
|
|
|
|
|
|
||
|
|
|
|
|
|
|
|
|
|
|
|
|
|
|
||||
|
|
|
|
|
|
|
|
|
|
V |
|
|
|
|
|
|
|
|
|
|
|
|
|
|
|
|
|
|
|
|
|
|
|
|
|||
|
|
|
|
|
|
|
|
|
|
|
|
|
|
|
|
|||
|
|
|
|
|
|
|
|
|
|
|
|
|
|
|
|
|
|
|
0 |
|
|
2 |
4 |
6 |
|
8 |
10 |
12 |
14 |
16 |
18 |
20 |
|||||
Полная шкала 100233 имп. Курсор: 6.126 |
(537 имп.) |
|
|
|
|
|
кэВ |
Рис. 2.5. Суммарный спектр отраженных электронов,
полученный на микроскопе Hitachi S-3400
Образцы изготавливались в 2 этапа. Первый – цилиндрические образцыс постоянным сечением, для определения резонансной длины которых использовалась формула (2.1). Одномерные цилиндрические образцы по одному на каждый исследуемый материал использовались для калибровки нагружающей машины, а также для корректировки значения Ed и резонансной частоты испытаний. Второй этап – изготовление образцов для исследования усталостной долговечности и механизмов инициирования трещины в режиме гигацикловой
31
усталости с переменным сечением (см. рис. 2.3, а), для определения длин которого использовались формулы (2.4), (2.5). Для исследования кинетики роста трещины в режиме гигацикловой усталости изготавливались образцы с геометрией, изображенной на рис. 2.3, б. При такой геометрии представляется возможным рассчитать и контролировать значение коэффициента интенсивностинапряжений K впроцессеэксперимента.
Важно отметить следующие моменты при подготовке образцов: необходимо точное соответствие длины образцов (±0,2 мм) резонансной длине, полученной по формуле (2.5). Поверхность образцов для испытаний на усталостную прочность должна иметь шероховатость не более 0,6 мкм для предотвращения образования трещин с поверхности. Для точной верификации амплитуды смещений необходимо откалибровать машину на высокой частоте с амплитудами, близкими к тем, при которых будут проводиться испытания.
Аспект, который также нужно учитывать при проведении эксперимента, – это нагрев образцов во время испытаний. Некоторые материалы, такие как сталь или титан, могут нагреваться в процессе эксперимента до такой степени, что в результате температурного расширения материала и изменения его упругих свойств от температуры, собственная частота колебаний образца изменяется и выводит систему из резонанса. По этой причине следует обеспечить охлаждение образца и компонентов установки (в особенности пьезоэлектрический преобразователь) во время эксперимента. В данной работе использовалось воздушное охлаждение.
2.3.Установка для испытаний на гигацикловую усталость
Вработе используется методология, базирующаяся на классических стандартах и результатах пионерских исследовательских работ [11, 12, 14], поскольку применение ультразвуковых систем для нагружения в гигацикловом режиме усталости еще не имеет определенного стандарта испытаний.
32
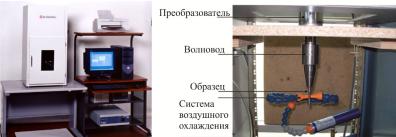
В данной работе использовалась ультразвуковая усталостная нагружающая машина фирмы SHIMADZU (рис. 2.6, а). На рис. 2.6, б изображена конфигурация машины для испытания образцов при коэффициенте асимметрии цикла R = –1. Образец в его верхней части крепился к волноводу, а другой его конец оставался свободным. Некоторые материалы в процессе эксперимента испытывают сильный нагрев, для исключения его вредного влияния (изменения резонансных характеристик) использоваласьсистемавоздушногоохлаждения.
а |
б |
Рис. 2.6. Внешний вид установки для испытаний в гигацикловом режиме: а – вид машины с системой контроля смещений и генератором; б – вид машины с закрепленным образцом во время испытаний
На данных испытательных ультразвуковых усталостных машинах, как и на прочих ультразвуковых машинах, задается контроль по смещению. Согласно формулам определения резонансной длины (2.3), (2.4) для каждого исследуемого материала (сплав ВТ-6, Grade-4 в исходном состоянии, Grade-4 в ультрамелкозернистом состоянии) разработана своя геометрия образцов. По аналитическим формулам (2.10) и (2.11) с помощью программного пакета ANSYS были рассчитаны параметры перевода амплитуды уровня напряжений в амплитуду колебаний (рис. 2.7).
33
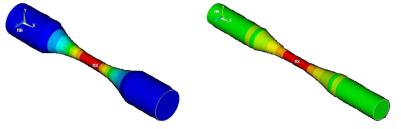
а |
б |
Рис. 2.7. Распределение напряжений по образцу в процессе усталостного эксперимента, полученное в результате расчетов по формуле (2.10) в математическом пакете ANSYS: а – исходное состояние; б – состояние УМЗ-2
Таким образом, по амплитуде колебаний свободного торца образца можно оценить уровень напряжений в его центральной части и иметь возможность проводить усталостные испытания в режиме контроля смещений.
2.4. Результаты испытаний на гигацикловую усталость
Предел выносливости материала ВТ-6 не был определен заранее, поэтому при испытании первого образца нагрузка осуществлялась ступенчатым образом с постепенным повышением амплитуды. Второй образец испытывался с предельной нагрузкой, прикоторойразрушилсяпервыйобразец.
Разрушение образцов сопровождается резким ростом температуры на поверхности и образованием окалины при разрушении в случаях, когда значение амплитуды нагружения близко к пределу усталости.
Результаты испытаний представлены на сводном графике, где они сопоставлены с данными из работы [12] для сплава Ti6Al4V. Усталостное разрушение сплава ВТ-6 на базе 109 циклов нагружения произошло при напряжении σ= 495±5 МПа. Разрушения титана Grade-4 на базе 109 циклов нагружения произошли при напряжениях 275 МПа для исходного состояния и
34
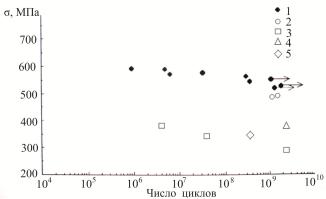
375 и 340 МПа для состояний УМЗ-1 и УМЗ-2 соответственно
(рис. 2.8).
Рис. 2.8. Результаты испытаний на гигацикловую усталость титана Grade-4 и сплава ВТ-6 в сравнении с литературными данными: 1 – данные по усталостной долговечности для сплава Ti6Al4V [12]; 2 – для ВТ-6; 3 – для титана Grade-4 в исходном состоянии; 4 – для титана Grade-4 в состоянии УМЗ-1; 5 – для титана Grade-4
в состоянии УМЗ-2
Результаты усталостных испытаний сплава титана ВТ-6 (Ti6Al4V) в гигацикловом режиме нагружения хорошо согласуются с данными работы [13]. Прослеживается предсказанное в работе [13] влияние микроструктуры материала на его усталостные характеристики в режиме гигацикловой усталости. Субмикрокристаллическое состояние титана Grade-4 УМЗ-1 с наименьшим размером зерна ≈100 нм проявляет самые высокие усталостные свойства по сравнению с состоянием УМЗ-2, где размер зерна составляет ≈200 нм, и поликристаллическим состоянием структуры с размером зерна 25 мкм.
Для установления механизмов разрушения в режиме гигацикловой усталости поверхности разрушения всех образцов исследовались с применением электронной микроскопии, а также оптическим и профилометрическим микроскопами.
35
2.5. Методы качественного и количественного анализа морфологии поверхностей разрушения
Разрушенные образцы исследовались сканирующим электронным, оптическим металлографическим микроскопами и интерферометром-профилометром New View 5010 для определения качественных и количественных морфологических признаков скейлинга поверхности разрушения. При усталостных испытаниях образовалось 2 типа разрушенных образцов. Первый тип – образцы разрушались непосредственно во время эксперимента. Второй, когда образцы, обладающие явными признаками разрушения (сильное изменение резонансной частоты испытаний, выход усталостной трещины на поверхность), уже были не способны выдерживать усталостную нагрузку в резонансной частоте. Поверхность разрушения образцов второго типа вскрывалась квазистатическим растяжением на гидравлической растягивающей машине. Предполагается, что поверхность разрушения в режиме гигацикловой усталости уже сформировалась в процессе эксперимента и занимает большую часть поверхности разрушения, что выявляется изменением резонансной частоты испытаний. Для минимизации влияния квазистатического растяжения во время долома образцыохлаждались до температуры жидкого азота, чтобы разрушение имело квазихрупкий характер в зоне долома и дополнительно не изменяло морфологию уже сформированнойповерхности.
При разрушении цилиндрических образцов за число циклов, соответствующее многоцикловой усталости (106−107), трещина образуется на поверхности образца (рис. 2.9, а). При разрушении на базе 109 циклов и более трещина образуется внутри образца, и на поверхности разрушения видна характерная для такого режима усталости область излома – «рыбий глаз» (fish-eye), в центре которой находится очаг разрушения, окруженный областью с фрагментированной (субмикрокристаллической) структурой (светлая область), (рис. 2.9, б). Аналогичные картины разрушения наблюдались в работах [14−19], и формирование трещины связывается с
36
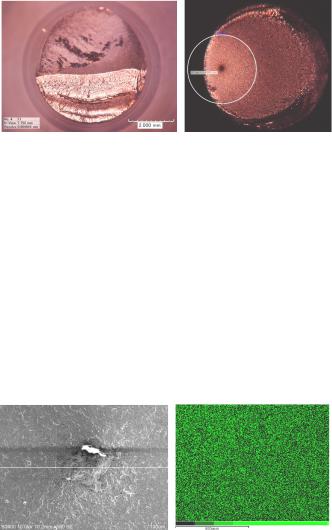
выраженными процессами полигонизации в объемах исходных зерен в ходе гигациклового нагружения [18].
аб
Рис. 2.9. Изображение поверхности разрушения Ti, полученное на оптическом микроскопе: а – инициирование трещины с поверхности образца; б – инициирование трещины под поверхностью образца
Значительный интерес представляет случай, когда трещина образуется под поверхностью образца вблизи внутренних концентраторов напряжений. В роли концентраторов выступают такие внутренние дефекты, как включения, поры, границы раздела фаз и т.п. Поверхность разрушения исследовалась на сканирующем электронном микроскопе с использованием дополнительного модуля INCA, который позволяет строить карту распределения химических элементов по спектру отраженных электронов с целью установления степени однородности материала и характера очага разрушения (рис. 2.10).
а |
б |
Рис. 2.10. Очаг разрушения (а) и распределение элементов (б) на поверхности разрушения образца титана Grade-2
37
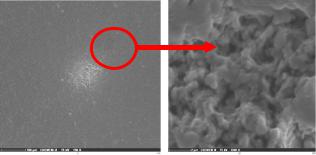
Анализ карты распределения химических элементов, полученной по спектру отраженных электронов, позволяет установить, что элементы вокруг и внутри очага на поверхности разрушения распределены равномерно, что также подтверждает предположение о роли микропористости в формировании очага разрушения.
При исследовании одного из образцов сплава ВТ-6 вблизи очага трещины была обнаружена область локализации микропористости, которая, однако, не инициировала очаг разрушения (рис. 2.11). Следовательно, можно предположить, что при гигацикловом режиме нагружения очаг трещины образуется вблизи дефекта, вокруг которого реализуется наибольшая концентрация напряжений. Данный дефект доминирует в процессе накопления усталостных повреждений, которые локализуются вокруг него и которые впоследствии инициируют трещину-лидера. Концентрация напряжений и усталостных повреждений вблизи остальных внутренних дефектов уже не достаточна для образования усталостной трещины, и наличие одного очага разрушения является характерным признаком морфологии поверхности разрушения при гигацикловом режиме нагружения
[12, 15].
аб
Рис. 2.11. Очаг усталостного разрушения образца ВТ-6 (увеличение ×150) (а) и локализация микропор вблизи места инициирования трещины (увеличение ×7000) (б)
38
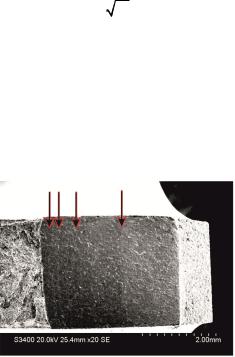
Изучение кинетики роста трещины в режиме гигацикловой усталости проводилось на образцах стали R4, подвергнутых циклическому нагружению с частотой 20 кГц при варьировании амплитуды приложенных напряжений с целью обеспечения
постоянства значения ∆K~∆σ l при росте трещины. Поверх-
ность разрушения образца изучалась методом электронной микроскопии (микроскоп Hitachi S-3400), позволившей установить характерные морфологические признаки распространения трещины при коррекции величины ∆K. На рис. 2.12 представлено изображение поверхности разрушения, на которой прослеживается стадийность прорастания трещины в виде следов, оставленных фронтом трещины, вследствие изменения условий нагружения (выделенострелками).
Рис. 2.12. Поверхность разрушения образца стали R4
С целью установления количественных характеристик морфологии поверхности разрушения плоских и цилиндрических образцов, подвергнутых, соответственно, много- и гигацикловому нагружению, анализировались данные поверхностного рельефа (шероховатости), полученные с помощью интерферометрапрофилометра New View 5010. Интерференционный микроскоп New View представляет собой бесконтактный оптический трехмерный профилометр высокой точности: разрешение по оси z
39
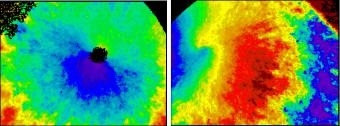
0,1 нм вдоль высоты рельефа и 0,5 мкм по осям x и y в горизонтальнойплоскости.
На поверхности разрушения цилиндрических образцов исследовались области вблизи очага разрушения и вдали от него и проводилась оценка масштабно-инвариантных характеристик в терминах показателя Херста. Анализ закономерностей рельефа поверхности разрушения позволил установить два механизма распространения инициированной трещины в образцах сплава ВТ-6. Первый, когда трещина распространяется равномерно во все стороны, при этом рельеф вокруг очага разрушения имеет области возвышения и понижения профиля поверхности, равномерно отдаляющиеся от очага трещины (рис. 2.13, а). Второй механизм характеризуется распространением трещины по спирали, где с разных сторон очага разрушения возникают области пониженного и повышенного профиля, которые расходятся от места инициирования в виде гребней спирали (рис. 2.13, б). При отдалении от очага разрушения на расстояние более 600 мкм различия в рельефе пропадают.
а |
б |
Рис. 2.13. Очаг трещины и область ее распространения в образцах сплава ВТ-6, соответствующие различным механизмам распространения трещины: а – равномерное по всем направлениям; б – распространение трещины по спирали
Возможно, данные механизмы связаны с условиями нагружения образцов, так как в случае со спиралевидным
40