
книги / Процессы формообразования и инструменты
..pdf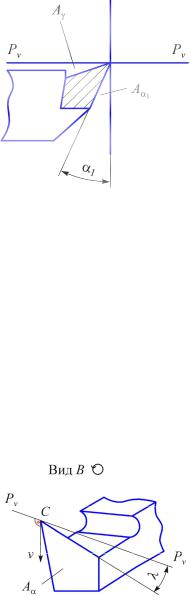
Рис. 2.12. Угол во вспомогательной секущей плоскости
Вспомогательный задний угол α1 (альфа один) – это угол во вспомогательной секущей плоскости между вспомогательной задней поверхностью и перпендикуляром к основной плоскости, проходящим через точку вспомогательной режущей кромки.
Вспомогательный задний угол способствует снижению трения между вспомогательной задней поверхностью резца и обработанной поверхностью заготовки.
2.6. Угол плоскости резания
На рис. 2.13 представлен токарный резец со стороны главной режущей кромки (вид В на рис. 2.10).
Рис. 2.13. Угол наклона главной режущей кромки
21
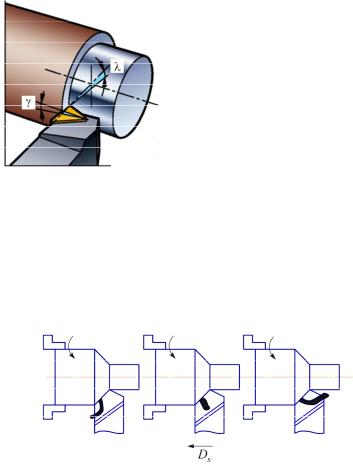
Угол наклона главной режущей кромки λ (лямбда) – это угол, образованный режущей кромкой и линией, проведенной через вершину резца параллельно основной плоскости.
Угол наклона главной режущей кромки определяется геометрией пластины и конструкцией державки (рис. 2.14).
В зависимости от положения вершины резца относительно главной режущей кромки угол λ может быть равен нулю, отрицательным
или положительным. Если главная режущая кромка расположена ниже основной плоскости, то угол λ отрицательный, если выше – положительный, если совпадает – равен нулю.
Угол λ определяет направление схода стружки (рис. 2.15).
а |
б |
в |
Рис. 2.15. Влияние угла λ на направление схода стружки:
а – λ < 0; б – λ = 0; в – λ > 0
При положительном угле λ стружка отводится в сторону обработанной поверхности, при отрицательном – в сторону обрабатываемой поверхности, при λ = 0 – в направлении, перпендикулярном к главной режущей кромке.
22
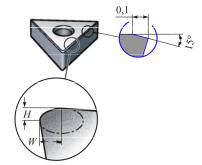
2.7. Режущая кромка и радиус при вершине инструмента
Форма режущей кромки и радиус при вершине резца определяют окончательную геометрию обработанной детали [2–4].
Вершина инструмента (см. рис. 2.4) получается путем пересечения режущих кромок – главной и вспомогательной. Главная режущая кромка получается путем пересечения передней и главной задней поверхностей. Вершина инструмента и главная режущая кромка – это элементы режущего лезвия, которые первыми вступают в процесс резания и оставляют след на микрогеометрии обработанной детали.
В современном машиностроении к форме вершины инструмента
иглавной режущей кромки предъявляются повышенные требования. Доказано, что после заточки токарного резца на режущей кром-
ке и вершине режущего инструмента образуется заусенец. При первом контакте такого инструмента с заготовкой заусенец отрывается с поверхности лезвия. Это приводит к снижению точности размерной обработки, так как фактически инструмент стал короче на величину заусенца.
Для усиления режущей кромки и повышения точности размерной обработки режущую кромку округляют или формируют на ней отрицательную фаску (рис. 2.16).
б
а
Рис. 2.16. Режущая кромка: а – округление режущей кромки; б – отрицательная фаска
23
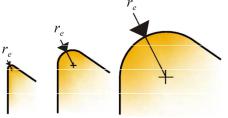
Величина округления режущей кромки не превышает 80 мкм. Соотношение W/H (см. рис. 2.16) зависит от области применения пластины.
Отрицательная фаска позволяет пластине выдерживать нагрузки при прерывистом резании (ротационное точение, фрезерование).
Радиус при вершине является участком лезвия, оставляющим след на обработанной поверхности. От величины радиуса при вершине re (рис. 2.17) зависят точность и качество обработанной поверхности.
Рис. 2.17. Радиус при вершине
Увеличение rе уменьшает шероховатость обработанной поверхности, но вызывает увеличение нагрузки на резец и приводит к возникновению вибраций. В современном машиностроении для обеспечения точности резания стремятся вести обработку инструментом
сминимальным радиусом при вершине.
2.8.Изменение углов режущего инструмента при установке на станке
Встатической системе координат углы резца рассматриваются в момент, когда инструмент находится в состоянии покоя, при расположении точек его режущей кромки на уровне оси центров станка, а оси резца – перпендикулярно оси центров. При подъеме и опускании точек режущей кромки относительно линии центров значения
углов γ и α будут изменяться (рис. 2.18).
24
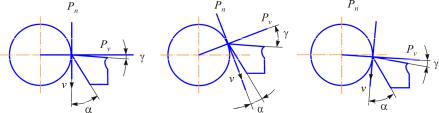
а |
б |
в |
Рис. 2.18. Изменение углов режущего инструмента при установке на станке:
а– на оси обрабатываемой детали; б – выше оси обрабатываемой детали;
в– ниже оси обрабатываемой детали
Вслучае, когда резец расположен на оси обрабатываемой детали (рис. 2.18, а), изменений переднего и главного заднего углов не наблюдается, углы соответствуют значениям углов в статической системе координат.
При установке резца выше оси обрабатываемой детали происходит отклонение вектора скорости резания вправо. Следовательно, меняются положения плоскостей резания и основной. Происходит увеличение переднего угла и уменьшение главного заднего угла
(рис. 2.18, б).
Если резец установлен ниже оси обрабатываемой детали, происходит отклонение вектора скорости резания влево (рис. 2.18, в), в результате чего уменьшается передний угол и увеличивается главный задний угол.
На практике чаще всего резец устанавливают по оси центров.
2.9.Изменение углов инструмента в процессе резания
Впроцессе резания статические углы инструмента изменяются. Изменение величин переднего и заднего углов вызывается сложным относительным движением инструмента и заготовки, в результате чего изменяется положение поверхности резания.
25

На рис. 2.19 представлена схема изменения углов инструмента в процессе резания. Условно режущий инструмент представляет собой клин с углами α и γ.
а |
б |
Рис. 2.19. Изменение углов инструмента в процессе резания:
а– одно рабочее движение; б – два рабочих движения
Вслучае, когда траектория движения инструмента совпадает
свектором скорости резания, изменения углов в процессе резания не наблюдается (рис. 2.19, а).
Предположим, что инструменту сообщается одновременно два движения (рис. 2.19, б). Одно из движений главное, совершающееся со скоростью v, второе (движение подачи) совершается со скоро-
стью vs. Результирующая скорость двух движений будет ve. Таким образом, в процессе обработки плоскость резания будет проходить по результирующему вектору скорости. В свою очередь, в кинематике это приводит к изменению переднего и главного заднего углов.
При поперечном точении в результате сочетания вращательного движения заготовки и поперечного перемещения резца траекторией движения точек режущей кромки является архимедова спираль, касательная к которой будет действительной плоскостью резания.
Впроцессе сверления в результате возникновения результирующего движения (сумма движений вращения сверла и подачи) на
26
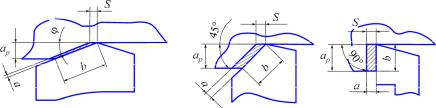
главной задней поверхности инструмента происходит кинематическое уменьшение главного заднего угла. В связи с этим главную заднюю поверхность сверла изначально затачивают с переменным задним углом, что позволяет компенсировать в процессе резания возникновение кинематического изменения заднего угла.
2.10. Сечение среза
Глубина резания, частота вращения шпинделя или инструмента и подача характеризуют процесс резания с технологической стороны, т.е. с точки зрения обеспечения процесса резания. Однако при одной и той же подаче и глубине резания в зависимости от формы режущей кромки и ее расположения (углов в плане) изменяются ширина и толщина поперечного сечения срезаемого слоя. Стоит отметить, что от значений ширины и толщины сечения среза будут зависеть процессы деформаций, температура резания и условия теплоотвода.
Толщина и ширина среза представляют собой не толщину и ширину стружки, а расчетные размеры сечения среза до образования стружки (рис. 2.20).
Ширина срезаемого слоя, или ширина среза, b (мм) – расчетная длина контакта главной режущей кромки с поверхностью резания.
Толщина срезаемого слоя, или толщина среза, а (мм) – расстояние между двумя последовательными положениями главной режущей кромки за один оборот заготовки.
Рис. 2.20. Формирование, ширина и толщина среза
27
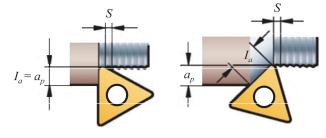
Толщина и ширина среза связаны с подачей и глубиной следующими соотношениями:
а = S sin ϕ, |
|
||
b = |
ap |
. |
(2.2) |
|
sin ϕ |
|
Из формул (2.2) видно, что при постоянных подаче и глубине резания с увеличением угла ϕ толщина среза а увеличивается, а ширина b уменьшается.
Максимальная толщина стружки а становится меньше при уменьшении подачи и главного угла в плане.
Значение главного угла в плане и глубины резания определяют эффективную длину режущей кромки la (рис. 2.21). Эффективная длина режущей кромки – это часть режущей кромки, которая находится в непосредственном соприкосновении с обрабатываемой поверхностью [1, 4].
Рис. 2.21. Эффективная длина режущей кромки
Из рис. 2.20 и 2.21 следует, что при увеличении эффективной длины режущей кромки увеличивается ширина b срезаемого слоя.
В табл. 2.3 показана зависимость между главным углом в плане, эффективной длиной режущей кромки, подачи и толщиной стружки.
Увеличение эффективной длины режущей кромки способствует повышению эффективности теплоотвода из зоны резания и снижению износа инструмента.
28

|
|
|
|
|
|
Таблица 2.3 |
|
Влияние угла в плане на толщину стружки |
|
|
|||
|
|
|
|
|
|
|
Параметры |
|
|
Значение |
|
|
|
|
|
|
|
|
|
|
Угол в плане ϕ, град |
|
|
|
|
|
|
|
90–95 |
75 |
60 |
|
45 |
48,7 |
|
|
|
|
|
|
|
Отношение толщины |
1 |
0,96 |
0,87 |
|
0,71 |
0,75–0,39 |
стружки к подаче |
|
|||||
|
|
|
|
|
|
|
|
|
|
|
|
|
|
Эффективная длина ре- |
|
|
|
|
|
|
жущей кромки la при |
2 |
2,08 |
2,3 |
|
2,82 |
5,1 |
ар = 2 мм |
|
|
|
|
|
|
29
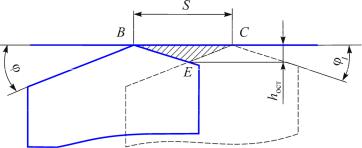
При прохождении токарным резцом зоны резания с заданной подачей на обработанной поверхности остается остаточное сечение среза. На рис. 2.22 треугольник ВСЕ является остаточным сечением среза.
Рис. 2.22. Остаточное сечение среза
Остаточное сечение среза определяет величину шероховатости обработанной поверхности. Исключить появление остаточного сечения на обработанной поверхности невозможно, его можно лишь минимизировать.
Величина остаточного сечения зависит от величины подачи и значения углов в плане. Чем меньше подача, тем меньше высота остаточного сечения.
30