
книги / Процессы формообразования и инструменты
..pdfПравильный подбор инструмента позволяет обеспечить заданную точность обработки и повысить экономическую эффективность технологического процесса.
4.2. Инструментальные материалы
Для того чтобы режущий инструмент осуществлял процесс резания, кроме геометрических параметров его режущая часть должна быть выполнена из материала, обладающего следующими характеристиками:
1.Иметь высокую твердость (HRC). Чем больше отношение твердости инструментального материала к твердости обрабатываемого материала, тем лучше режущие свойства инструмента. Чем тверже инструментальный материал, тем эффективнее его сопротивление износу по задней поверхности и деформации.
2.Иметь высокую прочность (σизг). Прочность инструмента должна быть больше прочности обрабатываемого материала. Чем выше прочность инструментального материала, тем меньше вероятность поломки режущей кромки. Стоит отметить, что чем больше твердость материала, тем меньше его прочность.
3.Быть теплостойким. Под теплостойкостью понимается критическая температура, при которой сохраняются режущие свойства.
4.Обеспечивать высокое сопротивление износу.
5. Обладать высокой теплопроводностью – отводить тепло
ине давать перегреваться.
6.Иметь минимальную стоимость.
При выборе инструментального материала необходимо учитывать материал заготовки, ее форму, требования по точности и качеству, а также состояние оборудования.
В начале прошлого столетия инструментальные материалы были немногим тверже обрабатываемого материала. Следовательно, стойкость инструмента была невысокой, а скорость резания и подача очень низкими.
61
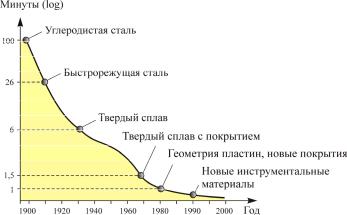
Появление быстрорежущей стали привело к положительным изменениям, которые сказались на уменьшении времени обработки.
Спустя 20 лет твердый сплав без покрытия приблизил требуемое время резания к недостижимым ранее шести минутам. Появление твердого сплава с покрытием снизило время обработки до полутора минут. В настоящее время, с улучшением геометрии и новыми технологиями нанесения покрытия, время резания 500 мм стального прутка составляет менее одной минуты (рис. 4.3) [4, 5].
Рис. 4.3. Диаграмма развития инструментальных материалов
Кроме того, вслед за традиционными марками твердого сплава с покрытием и без него новые инструментальные материалы, такие как кермет, керамика, кубический нитрид бора и поликристаллический алмаз, способствуют оптимизации обработки и повышению производительности.
4.3. Классификация инструментальных материалов
Классификация современных инструментальных материалов и их международное обозначение представлены на рис. 4.4 [2–4].
62
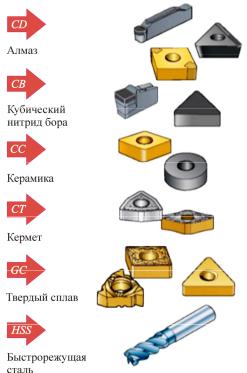
Рис. 4.4. Классификация инструментальных материалов
В данную классификацию не включены углеродистые инструментальные стали (марки У8, У10, У12) и легированные инструментальные стали (марки Х, ХВГ), так как в настоящее время данные материалы практически не используются в связи с их низкой теплостойкостью.
На рис. 4.4 показано, что при изготовлении цельного металлорежущего инструмента применяются быстрорежущие стали, все остальные материалы применяются в виде сменных пластин.
Диаграмма свойств инструментальных материалов представлена на рис. 4.5. Наибольшее применение в современном машиностроении находят твердые сплавы и быстрорежущие стали.
63
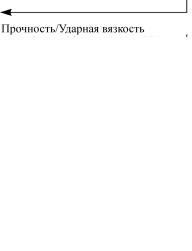
|
Из анализа рис. 4.5 следует, |
|||
|
что при |
обработке |
материалов |
|
|
в тяжелых условиях (черновое то- |
|||
|
чение, точение на удар) следует |
|||
|
выбирать материалы, обладаю- |
|||
|
щие высокими прочностными ха- |
|||
|
рактеристиками, – быстрорежу- |
|||
|
щие стали. В случае назначения на |
|||
|
ударное точение хрупких мате- |
|||
|
риалов (CD, CB, CC на рис. 4.5) |
|||
|
режущая кромка резца разрушится. |
|||
|
4.4. Быстрорежущие стали |
|||
Рис. 4.5. Свойства |
Быстрорежущие |
стали |
обо- |
|
значаются |
буквами, |
соответст- |
||
инструментальных материалов |
вующими карбидообразующим и |
|||
|
||||
|
легирующим элементам |
(Р – |
вольфрам, М – молибден, Ф – ванадий, А – азот, К – кобальт, Т – титан, Ц – цирконий). За буквой следует цифра, обозначающая среднее содержание элемента в процентах (содержание хрома до 4 % в обозначении марок не указывается). Цифра, стоящая в начале обозначения стали, указывает на содержание углерода в десятых долях процента. Например, сталь марки А11Р3М3Ф2 содержит 1,1 % С, 3 % W, 3 % Мо, 2 % V.
В табл. 4.4 показаны сравнительные характеристики быстрорежущих сталей [4, 5].
Достоинствами быстрорежущих сталей являются: высокая прочность, надежность, высокая технологичность, низкая цена. Объем инструментов из быстрорежущих сталей на рынке составляет 30–40 % от общего объема режущих инструментов. Из данного материала изготовляют зуборезные инструменты, протяжки, сверла, метчики и т.п.
64
|
|
|
|
|
Таблица 4.4 |
|
|
Сравнительные характеристики быстрорежущих сталей |
|
|
|||
|
|
|
|
|
|
|
Инструментальный |
Свойства |
Маркировка |
|
|
Группы |
|
|
|
Применение |
обрабаты- |
|||
материал |
Теплостойкость |
Прочность |
по ГОСТу |
|||
|
θкр, °С |
σизг, МПа |
|
|
|
ваемости |
Быстрорежущая |
600–620 |
3000–3700 |
Р18, Р6М5 |
Изготовление универ- |
Р, K |
|
сталь нормальной |
|
|
|
сального инструмента |
|
|
производительности |
|
|
|
|
|
|
|
|
|
|
|
|
|
Быстрорежущие |
630–640 |
2500–3000 |
Ванадиевые – |
Обработка |
труднооб- |
P, M, S |
стали повышенной |
|
|
Р18Ф2, Р14Ф4. |
рабатываемых и жаро- |
|
|
теплостойкости (ко- |
|
|
Кобальтовые – |
прочных материалов |
|
|
бальтовые и вана- |
|
|
Р9К5, Р9К10 |
|
|
|
диевые) |
|
|
|
|
|
|
|
|
|
|
|
|
|
Быстрорежущие |
640–650 |
2000–2700 |
Р9М5Ф2К8, |
Обработка материалов |
M, S, H |
|
стали повышенной |
|
|
Р12М3Ф2К8 |
HRC > 45–60, жаро- |
|
|
теплостойкости (ко- |
|
|
|
прочных, |
нержавею- |
|
бальтованадиевые) |
|
|
|
щих и труднообраба- |
|
|
|
|
|
|
тываемых материалов |
|
|
|
|
|
|
и сплавов |
|
|
|
|
|
|
|
|
|
65
66
Окончание табл. 4.4
Инструментальный |
Свойства |
Маркировка |
|
|
|
|
Группы |
|
|
|
Применение |
|
обрабаты- |
||||
материал |
Теплостойкость |
Прочность |
по ГОСТу |
|
||||
|
θкр, °С |
σизг, МПа |
|
|
|
|
|
ваемости |
Высокой теплостой- |
700–720 |
2000–2500 |
В11М7К23, |
Чистовая |
и получис- |
M, S |
||
кости |
|
|
В18М25К4 |
товая обработка тита- |
|
|||
|
|
|
|
новых, |
высоколегиро- |
|
||
|
|
|
|
ванных, |
труднообраба- |
|
||
|
|
|
|
тываемых |
материалов |
|
||
|
|
|
|
и сплавов |
|
|
|
|
|
|
|
|
|
|
|
||
Порошковые |
635–640 |
2600–3500 |
Р6М5К5-МП, |
Черновая |
и получис- |
M, S |
||
|
|
|
Р9К5-МП |
товая обработка |
жа- |
|
||
|
|
|
|
ропрочных и высоко- |
|
|||
|
|
|
|
прочных |
сталей |
и |
|
|
|
|
|
|
сплавов |
|
|
|
|
|
|
|
|
|
|
|
|
|
4.5. Металлокерамические твердые сплавы
Твердый сплав – продукт порошковой металлургии, состоящий из частиц карбидов вольфрама (WC) и кобальтовой связки (Co). В твердых сплавах количество карбидов вольфрама достигает 80 %. Также в состав твердого сплава входят карбиды других элементов (карбиды титана TiC, карбиды тантала TaC), играющих особую роль при формировании градиентной основы.
Карбиды вольфрама, титана и тантала обладают высокой твердостью и тугоплавкостью. Чем больше в твердом сплаве карбидов, тем выше его твердость и теплостойкость, но ниже механическая прочность. При увеличении содержания кобальта растет прочность, но твердость и теплостойкость снижаются.
Определенная форма заготовки твердого сплава традиционно придается путем прессования порошка либо методом экструзии. Затем полученная заготовка пластины подвергается спеканию.
Втабл. 4.5 показаны сравнительные характеристики твердых сплавов [5].
С введением новых марок твердых сплавов с покрытием значительно расширилась область их использования. В настоящее время твердые сплавы являются основным инструментальным материалом, обеспечивающим высокопроизводительную обработку.
Твердым сплавам с износостойким покрытием удалось преодолеть недостатки как твердых сплавов без покрытия, так и других инструментальных материалов: с увеличением прочности снижается износостойкость. Наносимый слой карбидов или нитридов тугоплавких металлов в несколько микрометров резко изменил производительность и износостойкость твердосплавных инструментов.
На рис. 4.6 показана твердосплавная пластина с нанесенным покрытием [4].
Внастоящее время применяются различные методы нанесения износостойких покрытий на режущие инструменты. Наиболее широко применяются методы физического осаждения покрытий (PVD)
ихимического осаждения покрытий из паровой фазы (CVD).
67

68
Таблица 4.5
Сравнительные характеристики твердых сплавов
Инструмен- |
Свойства |
Маркировка |
|
|
|
||||
тальный |
|
|
Применение |
|
Теплостойкость |
Прочность |
по ГОСТу |
||
материал |
θкр, °С |
σизг, МПа |
|
|
Однокарбидный |
950–1100 |
1170–1600 |
ВК, ВК8 |
Прочность и ударная вязкость сплавов ВК |
твердый сплав |
|
|
|
увеличивается по мере возрастания содержа- |
|
|
|
|
ния кобальта. В таком же порядке уменьшает- |
|
|
|
|
ся твердость сплавов этой группы. |
|
|
|
|
Обработка материалов, дающих при резании |
|
|
|
|
стружку надлома: чугунов, цветных металлов. |
|
|
|
|
Работа на более высоких скоростях резания, |
|
|
|
|
чем у инструментальных сталей |
|
|
|
|
|
Двухкарбидный |
1000–1150 |
980–1400 |
ТК, Т30К4 |
Обработка сталей и цветных металлов (лату- |
твердый сплав |
|
|
|
ней), дающих при резании сливную стружку. |
|
|
|
|
В отличие от однокарбидных твердых сплавов |
|
|
|
|
обладают большей стойкостью к окислению, |
|
|
|
|
твердостью и теплостойкостью, меньшими |
|
|
|
|
значениями тепло- и электропроводности, мо- |
|
|
|
|
дуля упругости. |
|
|
|
|
Увеличение содержания в твердом сплаве |
|
|
|
|
карбидов вольфрама и титана при соответст- |
|
|
|
|
вующем уменьшении содержания кобальта |
|
|
|
|
ведет к повышению теплостойкости твердых |
|
|
|
|
сплавов. |
|
|
|
|
|

|
|
|
|
|
Продолжение табл. 4.5 |
|
|
|
|
|
|
|
Инструмен- |
Свойства |
Маркировка |
|
|
|
тальный |
|
|
Применение |
|
|
Теплостойкость |
Прочность |
по ГОСТу |
||
|
материал |
θкр, °С |
σизг, МПа |
|
|
|
|
|
|
|
Предел прочности при изгибе и ударная вяз- |
|
|
|
|
|
кость увеличиваются с ростом содержания ко- |
|
|
|
|
|
бальта, приэтом уменьшается износостойкость. |
|
|
|
|
|
Сплавы Т30К4 и Т15К6 применяются при |
|
|
|
|
|
чистовой и получистовой обработке сталей с |
|
|
|
|
|
высокими скоростями резания и малыми на- |
|
|
|
|
|
грузками на инструмент, а сплавы Т5К10 и |
|
|
|
|
|
Т5К12 предназначены для работы в тяжелых |
|
|
|
|
|
условиях ударных нагрузок с пониженной |
|
|
|
|
|
скоростью резания |
|
|
|
|
|
|
|
Трехкарбидный |
700–800 |
1300–1600 |
ТТК, |
Карбид тантала уменьшает ползучесть твер- |
|
твердый сплав |
|
|
ТТ7К12 |
дых сплавов, существенно повышает предел |
|
|
|
|
|
усталости при циклическом нагружении, а |
|
|
|
|
|
также термостойкость и стойкость к окисле- |
|
|
|
|
|
нию на воздухе. |
|
|
|
|
|
Основная область применения трехкарбидных |
|
|
|
|
|
сплавов – резание с очень большими сечения- |
|
|
|
|
|
ми среза в условиях точения и строгания, а |
|
|
|
|
|
также обработка с тяжелыми ударами. В этих |
|
|
|
|
|
случаях повышенная прочность, обусловлен- |
|
|
|
|
|
ная наличием карбидов тантала, компенсиру- |
69 |
|
|
|
|
ет их пониженную теплостойкость |
|
|
|
|
|
|
|
|
|
|
|
70
Окончание табл. 4.5
Инструмен- |
Свойства |
Маркировка |
|
Применение |
|
|
тальный |
|
|
|
|
||
Теплостойкость |
Прочность |
по ГОСТу |
|
|
||
материал |
θкр, °С |
σизг, МПа |
|
|
|
|
Безвольфрамо- |
900–1000 |
1400–1600 |
ТН20, |
Применяются |
для замены |
вольфрамовых |
вый твердый |
|
|
КНТ16 |
твердых сплавов с целью снижения себестои- |
||
сплав (кермет) |
|
|
|
мости инструмента (отказ от дорогостоящего |
||
|
|
|
|
вольфрама). |
|
|
|
|
|
|
Характеризуются пониженной склонностью к |
||
|
|
|
|
адгезионному взаимодействию с обрабаты- |
||
|
|
|
|
ваемым материалом, что уменьшает износ ин- |
||
|
|
|
|
струмента при обработке сталей и позволяет |
||
|
|
|
|
получать при их обработке низкую шерохова- |
||
|
|
|
|
тость обработанной поверхности и высокую |
||
|
|
|
|
размерную точность. Пониженная склонность |
||
|
|
|
|
к адгезии также важна при обработке никеля, |
||
|
|
|
|
магнитных сплавов и других вязких мате- |
||
|
|
|
|
риалов. |
|
|
|
|
|
|
Прочностные |
характеристики |
безвольфрамо- |
|
|
|
|
вых твердых сплавов во многих случаях ниже, |
||
|
|
|
|
чем у вольфрамосодержащих твердых сплавов. |
||
|
|
|
|
Значительная нестабильность свойств и низ- |
||
|
|
|
|
кая циклическая прочность не дают возмож- |
||
|
|
|
|
ности рекомендовать керметы в качестве ин- |
||
|
|
|
|
струментальных материалов для автоматизи- |
||
|
|
|
|
рованного производства |
|
|
|
|
|
|
|
|
|