
книги / Процессы формообразования и инструменты
..pdf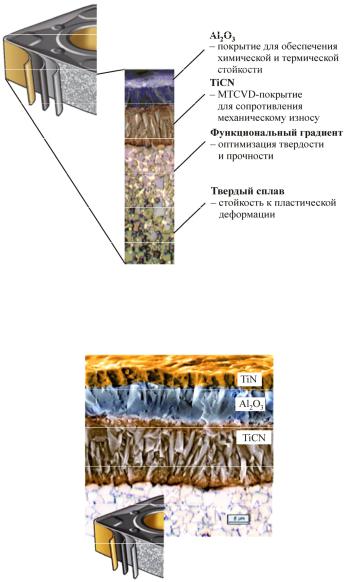
Рис. 4.6. Твердосплавная пластина с нанесенным покрытием
На рис. 4.7 показана режущая пластина с CVD-покрытием.
Рис. 4.7. CVD-покрытие: TiN – нитрид титана; TiCN – карбонид титана; Al2O3 – оксид алюминия
71
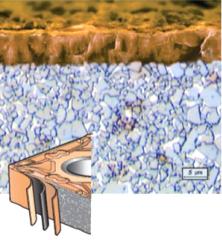
Карбонид титана TiCN обеспечивает износостойкость инструмента. Оксид алюминия Al2O3 работает как термобарьер, защищающий основу пластины от воздействия высоких температур. Нитрид титана TiN позволяет легче определить износ.
На рис. 4.8 показана режущая пластина с PVD-покрытием.
Рис. 4.8. PVD-покрытие
Суммарная толщина покрытия PVD, как правило, не более
3–6 мкм.
PVD-покрытие обычно прочнее, чем CVD-покрытие, и часто используется совместно с мелкозернистыми сплавами для получения острой режущей кромки.
Рациональная область применения конкретного износостойкого покрытия определяется совокупностью его эксплуатационных и технологических свойств, а также экономическими факторами. Идеального инструментального покрытия, одинаково пригодного для всего многообразия условий механической обработки, в настоящее время не существует, поэтому в промышленности применяется большая номенклатура различных методов нанесения покрытий на режущий инструмент и широкая гамма самих покрытий.
72
4.6. Сверхтвердые материалы
Сверхтвердыми принято считать инструментальные материалы, имеющие твердость по Виккерсу при комнатной температуре свыше
35 ГПа.
Сверхтвердые материалы находят широкое применение при обработке высокотвердых деталей при высоких температурах резания.
В машиностроении применяют следующие сверхтвердые материалы: керамику, поликристаллический кубический нитрид бора, поликристаллический алмаз.
4.6.1. Керамика
Все режущие инструменты из керамики отличаются высокой износостойкостью при одновременной возможности работы с высокой скоростью резания. Существует несколько видов керамики, предназначенных для различных областей применения.
Основу оксидной керамики составляет оксид алюминия Al2O3 с добавлением оксида циркония ZrO2, предотвращающего образование трещин. В результате соединения этих элементов образуется материал с повышенной химической стойкостью, но имеющий недостаточную термостойкость.
Смешанная керамика усилена такими соединениями, как карбиды или карбонитриды титана (TiC, TiCN). Данная керамика обладает повышенной прочностью и теплопроводностью.
Керамика, армированная нитевидными кристаллами карбида кремния SiCw, обладает повышенной прочностью, и при ее использовании допускается применение СОЖ. Такая керамика идеально подходит для обработки сплавов на основе никеля.
Керамика на основе нитрида кремния Si3N4 представляет собой еще одну группу керамических материалов. Ее удлиненные кристаллы образуют самоармирующийся материал высокой прочности. Пластины из керамики с нитридами кремния успешно применяются для обработки серого чугуна, однако недостаточная химическая стойкость ограничивает их применение для обработки других материалов.
73
Керамика на основе сиалона (SiAlON) сочетает в себе прочность самоармирующейся структуры из нитрида кремния и улучшенную химостойкость. Сиалоновые материалы идеально подходят для обработки жаропрочных сплавов.
Керамические материалы можно применять для широкого спектра операций и материалов. Чаще всего пластины из керамики используются для высокоскоростного точения, а также для обработки канавок и фрезерования. Специфические свойства каждого керамического сплава при правильном применении обеспечивают высокую производительность.
Основные ограничения по применению керамики связаны с недостаточной стойкостью к термическому шоку и выкрашиваниям. В связи с этим в большинстве случаев при использовании пластин из керамики СОЖ не применяются.
4.6.2. Поликристаллический кубический нитрид бора
Поликристаллический кубический нитрид бора CBN обладает исключительной твердостью в горячем состоянии, что позволяет использовать его при очень высоких скоростях резания. Он также характеризуется хорошей прочностью и термостойкостью.
Современные материалы CBN представляют собой керамические композиты с содержанием порядка 40–65 % CBN. Керамическая связка добавляет кубическому нитриду бора износостойкости, без чего этот материал был бы подвержен химическому износу. Существует группа сверхтвердых материалов с высоким содержанием
CBN – от 85 до почти 100 %.
Для формирования режущей пластины кубический нитрид бора CBN напаивается на заготовку из твердого сплава (рис. 4.9).
Компания Sandvik Coromant закрепляет кубический нитрид с использованием разработанной ими технологией Safe-Lock™ (см. рис. 4.9). Данное крепление обеспечивает высокую прочность режущих кромок на пластинах без задних углов.
Кубический нитрид бора широко используется для чистовой токарной обработки закаленной стали, имеющей твердость более
74
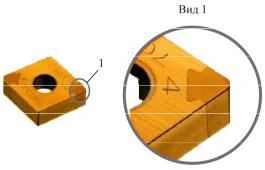
45 HRC. При твердости обрабатываемого материала более 55 HRС пластины из CBN становятся единственно возможным решением, способным заменить традиционно используемые методы шлифования. В более мягкой стали (твердостью ниже 45 HRС) содержится больше феррита, негативно влияющего на износостойкость CBN.
Рис. 4.9. Режущая пластина с CBN
CBN можно также использовать для высокоскоростной черновой обработки серого чугуна как при токарных, так и фрезерных операциях.
4.6.3. Поликристаллический алмаз
Поликристаллический алмаз (PCD) – композитный материал, состоящий из частиц алмаза, объединенных металлической связкой. Алмаз является самым твердым и, следовательно, самым стойким к износу материалом. Как режущий инструмент, он имеет хорошую износостойкость, но ему не хватает химической стойкости при высоких температурах, и он легко растворяется в железе.
Инструмент со вставками из поликристаллического алмаза применяют для обработки цветных металлов, например алюминия с высоким содержанием кремния, а также таких материалов, как металло-мат- ричные композитные материалы (MMC) и пластмассы, армированные углеродным волокном (CFRP). Использование PCD также возможно для суперфинишной обработки титана при условии подвода СОЖ.
75
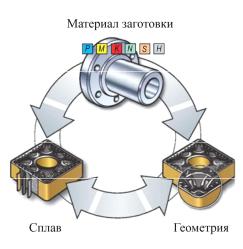
Глава V
ВЫБОР ГЕОМЕТРИИ ИНСТРУМЕНТА
При выборе инструмента для обработки конкретной детали необходимо в первую очередь учитывать три основных параметра: геометрию инструмента, материал режущей пластины и материал заготовки (рис. 5.1).
Рис. 5.1. Факторы, влияющие на процесс резания
Влияние материала заготовки и материала режущей пластины на процесс резания рассмотрено в гл. 2. В данной главе показаны взаимосвязи закономерности геометрии режущего инструмента и процесса резания.
5.1. Выбор углов в главной секущей плоскости
Интенсивность деформационных процессов зависит от величины переднего угла γ (рис. 5.2).
Чем больше угол γ, тем менее напряжен процесс деформации в переходной зоне (резец острый, как лезвие), следовательно, тем
76
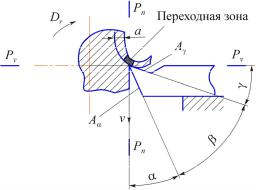
меньше величина силы и образующегося тепла и меньше износ инструмента.
↑γ → ↓ сила → ↓ температура → ↓ износ
Рис. 5.2. Назначение углов в главной секущей плоскости
Но с увеличением угла γ уменьшается угол заострения β, следовательно, уменьшается массивность режущего клина, что ведет к снижению прочности инструмента и его способности сохранять режущие свойства, в результате чего повышается износ инструмента.
↑γ → ↓ β → ↓ массивность клина → ↓ прочность → → ↓ способность сохранять режущие свойства → ↑ износ
На практике передний угол назначают, как правило, в пределах от –10 до +25°.
При обработке труднообрабатываемых (высокопрочных) материалов выбирают отрицательное значение переднего угла.
чем ↑ твердость обрабатываемого материала → берут ↓ γ чем ↓ твердость обрабатываемого материала → берут ↑ γ
В табл. 5.1 приведены примеры назначения переднего угла режущих пластин для разных групп обрабатываемых материалов.
77
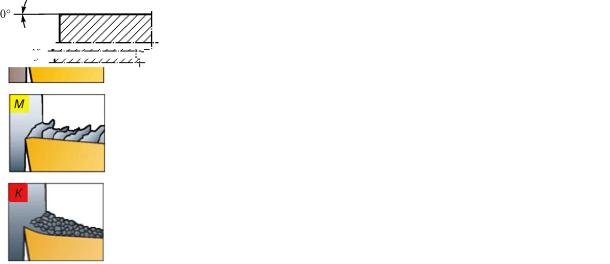
78
|
|
|
Таблица 5.1 |
|
Назначение переднего угла |
|
|
|
|
|
|
Материал заготовки |
|
Вид обработки |
|
|
|
|
|
|
Чистовая (F) |
Получистовая (M) |
Черновая (R) |
|
|
|
|
|
|
|
|
|
|
|
|
|
|
|
|
В табл. 5.1 показано, что в условиях нагруженной обработки величина фаски на режущей кромке увеличивается.
Главный задний угол α (см. рис. 5.2) предназначен для обеспечения положения главной задней поверхности относительно поверхности резания, т.е. минимального контакта с поверхностью резания.
Чем меньше угол α, тем больше пятно контакта, следовательно, увеличивается трение и возрастает температура. Повышение температуры ведет к увеличению износа инструмента.
чем ↓ α → ↑ пятно контакта → ↑ трение → ↑ температура → ↑ износ
Угол α стараются обеспечивать максимально большим, но с увеличением угла α будет уменьшаться угол заострения β и, следовательно, снижаться массивность режущего клина, что приведет к снижению прочности инструмента.
Большее значение угла α выбирают при обработке более упругих материалов.
чем ↑ α → ↓ β → ↓ массивность → ↓ прочность
При обработке различных материалов широкое применение находят режущие пластины без задних углов (см. гл. 1). Данные пластины массивны и обладают повышенной прочностью. Важно понимать, что нельзя устанавливать резец относительно детали с главным задним углом 0°, поэтому пластины без задних углов устанавливаются в державке под наклоном.
5.2. Назначение углов в плане
Главный угол в плане ϕ определяет положение главной режущей кромки в процессе резания (рис. 5.3).
Чем меньше главный угол в плане ϕ, тем больше угол при вершине инструмента ε, следовательно, увеличивается массивность режущей части, что приводит к повышению стойкости инструмента.
чем ↓ ϕ → ↑ ε → ↑ массивность → ↑ стойкость
79
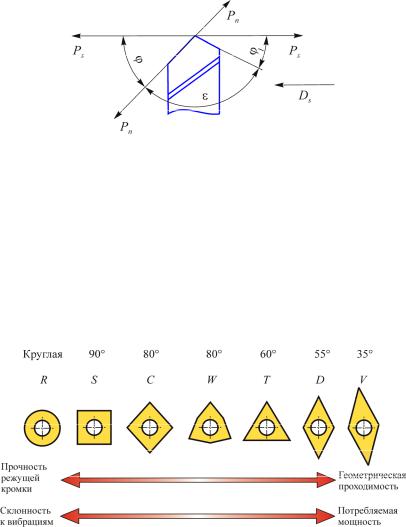
Рис. 5.3. Назначение углов в плане
При уменьшении главного угла в плане увеличивается радиальная составляющая силы резания, что ведет к снижению точности (см. гл. 1).
чем ↓ ϕ → ↑ радиальная сила → ↑ точность Для обеспечения точности обработанной поверхности целесо-
образно использовать инструменты с углом ϕ больше 90°. Однако при таком значении угла наблюдается минимальная стойкость инструмента из-за минимального значения угла при вершине ε (рис. 5.4).
Рис. 5.4. Влияние угла при вершине на процесс резания
Максимальное значение угла ε при вершине пластины обеспечивает ей более высокую прочность и надежность обработки.
В табл. 5.2 представлены рекомендации по выбору пластин.
80