
книги / Технология, механизация и автоматизация сварочного производства. Аппараты, оборудование и станки для комплексной механизации
.pdfбочего цикла машины, равное сумме машинного времени и вспомогательно го. —^маш ^в.
Что касается трудоемкости работ Тр, выполняемых ручным способом, и соответствующей численности занятых рабочих Рр, то речь идет о тех рабо тах, которые производятся вне машин и без помощи машин, например, о руч ных подсобных и транспортных работах, о ручной сборке деталей под сварку и т. д. Типичным примером может служить процесс сварки какой-либо кон струкции, часть швов которой выполняется с помощью машин, и трудоем кость их сварки вместе со вспомогательными сварочными операциями равна Тн а часть швов сваривается вручную с трудоемкостью Тр.
Следует четко различать ручные, немеханизированные работы Тр от ручных,вспомогательных операций на машинах, которые, хотя и производят ся вручную, но включаются в объем механизированных работ с трудоемко стью Тм. Итак, основным критерием к а ч е с т в е н н о й оценки уровня ме ханизации и автоматизации сварочных процессов должен служить показа тель У2.
Локальная эффективность и локальный уровень механизации отдель ных агрегатов не характеризуют их общей действительной эффективности в комплексном технологическом потоке. Нередки случаи, когда локальный рост производительности труда на отдельных сварочных операциях влечет за собой снижение уровня производительности других операций, например сборочных, вспомогательных или заготовительных, и общего уровня механи зации труда, например, когда при внедрении автоматической сварки резко были повышены требования к точности заготовок и их сборке, повысилась трудоемкость заготовительных и сборочных работ и соответственно снизился качественный показатель уровня комплексной механизации.
Такие кажущиеся противоречия возникают при оценке уровня механи зации сварочного производства. Они объясняются тем, что уровень механи зации хорошо оснащенной сборочно-сварочной линии ниже, чем одного ус тановленного в ней сварочного станка, несмотря на то, что техническая эф фективность его несомненно ниже, чем всей механизированной линии. Дело в том, что при оценке уровня механизации нельзя ограничиваться только ло кальным показателем машины Угл, а необходимо определять и ее комплекс ный показатель У2. Иначе высокий уровень локальной механизации может создать ошибочное представление о действительном состоянии механизации производства в целом.
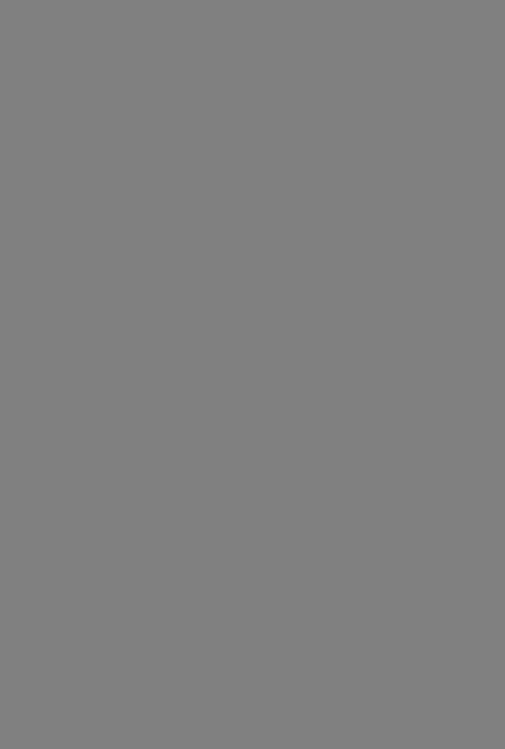
оборудование. В этом случае рационально расчленить изделие на узлы и из готовлять узлы по первой схеме, а по второй схеме осуществлять сборку и сварку всего изделия. Необходимо также учитывать, что расчленение изде лия приводит к изменению технологической схемы его изготовления как на основных стадиях, так и на заготовительной. Расчленение изделия приведет к изменению размеров как узлов, так и деталей их составляющих, для изготов ления которых на заготовительной стадии и при сборке-сварке возможно и целесообразно применять универсальное компактное, высокопроизводитель ное оборудование.
Возможен также и третий вариант - осуществлять сборку и сварку, на пример, многоэлементного изделия путем поэтапного включения деталей в изделие.
Итак, анализ конструкции и сварных соединений для определения воз можности их изменения с целью повышения технологичности является од ной из первых стадий проектирования.
Технические условия на изготовление изделия. Требования к качеству и точности заготовок, собранных и сваренных узлов и конструкции в целом предопределяют необходимость применения тех или иных средств производ ства. В частности, чем выше требования к качеству и точности промежуточ ных элементов и всего изделия, тем больше необходимость в применении механизированных и автоматизированных средств производства, так как при этом легче получить изделие высокого качества.
Условия производства (заводские, монтажные, полевые и др.). В заво дских условиях можно достичь более высокого уровня механизации, чем в полевых условиях или на монтажной строительной площадке. В свою оче редь, механизация производства позволяет существенно повысить произво дительность труда при снижении трудоемкости и себестоимости изготовле ния изделий. Поэтому в последнее время наблюдается тенденция максималь ной индустриализации монтажно-строительных сварочных работ. В качестве примера можно привести сборочно-сварочные линии и установки для заво дского изготовления крупногабаритных нефтерезервуаров методом рулонирования. В настоящее время около 90% всех работ по трудоемкости перене сено на заводы. В строительстве магистральных трубопроводов изготовление длинных секций-плетей перенесено с трассы на полузаводские базы с хоро шо организованной комплексной механизацией.
В тех случаях, когда можно эффективно реализовать комплексную ме
ханизацию строительных работ непосредственно на монтажной площадке или строительной трассе,выполнение сборочно-сварочных работ в централи зованном порядке на специализированных заводах может оказаться нецеле сообразным главным образом из-за добавочных расходов на трудоемкие и сложные транспортные операции. Например, после изобретения рельсосва рочных и трубосварочных машин-комбайнов стало эффективно наращивать пути или трубопроводы в непрерывную нитку непосредственно на трассе.
Тип производства и программа выпуска. Тип производства должен учитываться при определении количества оснастки и синхронизации всех операций. При изготовлении индивидуальной конструкции число приспособ лений должно быть минимальным; при серийном производстве конструкций число приспособлений должно быть увеличено, особенно если учесть воз можность механизации и автоматизации основных и вспомогательных опе раций.
Тип приспособлений - универсальные или специализированные - так же зависит от типа производства. Для крупносерийного производства с большой насыщенностью приспособлениями предпочтение должно отда ваться высокопроизводительным специализированным. Эти приспособления, как и вся оснастка, должны проектироваться с учетом возможности их уста новки в поточные и автоматические линии.
При индивидуальном и мелкосерийном производстве создание специ альных приспособлений приведет к увеличению сроков подготовки произ водства и повышению стоимости изготовления изделия. В этом случае более предпочтительно использовать стандартные универсальные приспособления, применяющиеся для производства самых разнообразных изделий и конст рукций и позволяющие осуществлять на одном рабочем месте несколько операций (сборку, сварку и др.).
Вопросы размещения средств механизации и автоматизации сварочно го производства также неразрывно связаны с программой выпуска и типом производства. Если при единичном и мелкосерийном производстве все обо рудование разместить в механизированные линии по производству того или иного изделия, то окажется весьма неэффективным использование малозагруженных станков и агрегатов. В этом случае оказывается эффективным разделение технологического процесса по операциям: заготовка, сборка сварка и т.д. При этом заготовку следует производить в заготовительном от делении, сборку и сварку - на сборочно-сварочных участках.
2.2. Принципы механизации и автоматизации
сварочного производства
При разработке систем комплексной механизации или автоматизации
сварочного производства обычно руководствуются одним из двух основных принципов:
-принципом дифференциации, т. е. расчленения производственного процесса на элементарные операции, выполняемые отдельными машинами - универсальными или специализированными;
-принципом интеграции, т. е. объединения нескольких разнородных или однородных операций и выполнения их многооперационной, комбини рованной машиной - комбайном.
Сварочный процесс, как технологический, обычно делится на операции (переходы), выполняемые на одном рабочем месте (станке, установке) одним исполнителем или несколькими. Степень расчленения процесса на операции
ипереходы определяется характером производства (единичное, серийное, массовое), технологическими особенностями процесса, наличием соответст вующего оборудования, квалификацией обслуживающего персонала и др. Наиболее полно принцип дифференциации выражен в массовом производст ве. Наряду с простотой и надежностью применяемого при этом оборудова ния, не требующего высокой квалификации оператора, он характеризуется использованием большого количества единиц оборудования и его общей ме таллоемкостью, занимаемой производственной площадью, общей численно стью обслуживающего персонала, затратами времени на транспортировку, установку и закрепление изделий и др., что является его существенным не достатком.
Противоположностью дифференциации является интеграция производ ственного процесса, состоящая в объединении нескольких его элементов для выполнения их на одном станке, установке или рабочем месте одним опера тором или одной бригадой. При интеграции отдельные операции становятся по существу переходами одной комплексной операции.
Комплексная механизация и автоматизация сварочного производства предполагает интеграцию как родственных, так и не родственных технологи ческих процессов, совмещенных в едином комплексе электросварочного оборудования. Примерами совмещения родственных процессов могут слу жить контактная стыковая сварка и термообработка термоупрочняемых ста лей и сплавов; дуговая сварка под флюсом и наплавка; многоэлектродная
контактная точечная или шовная сварка и т. д. Примерами интеграции не родственных технологий являются, например, сборка и сварка, обработка и сварка; стыковая сварка со срезкой грата; автоматическая ориентация шва относительно горелки; автоматическая сборка, в том числе с подогревом для плотной посадки деталей; сварка и съем готовых изделий; плазменная резка и автоматическая маркировка заготовок; плазменно-механическая обработка тел вращения и др.
К перспективным направлениям повышения уровня механизации и ав томатизации сварочного оборудования следует отнести переналаживаемое сварочное оборудование с интеграцией родственных и не родственных свар ке технологических процессов, построенное на агрегатно-модульном прин ципе с высокой степенью унификации.
Высокий уровень автоматизации эффективен, главным образом, в мас совом и крупносерийном производстве, охватывающем лишь 15 - 25% всей продукции машиностроения. Повышение уровня механизации и автоматиза ции серийного, мелкосерийного, а в некоторых случаях и единичного произ водства оказывается возможным благодаря концентрации изготовления сварных конструкций на специализированных производственных единицах, таких как участок, цех, на основе применения групповой технологии, а также повышению производственной гибкости средств механизации и автоматиза ции.
Реализация идей интеграции операций в производстве сварных конст рукций стала возможна благодаря повышению надежности оборудования и развитию методов и средств механизации и автоматизации сварочных про цессов. Интеграция операций может быть реализована путем создания мно гопозиционных, роторных и многоместных установок и станков, применения многоместных сборочно-сварочных приспособлений и одновременной свар ки несколькими автоматами или головками. При этом отдельные элементы операции могут выполняться последовательно, параллельно (одновременно) либо последовательно-параллельно. При последовательном выполнении эле менты операции осуществляются при нескольких последовательных положе ниях изделия или сварочного инструмента либо последовательно нескольки ми инструментами.
Примерами сварочного оборудования, применяемого при таком виде интеграции операций, являются сборочно-сварочные станки (комбинирован ные машины) с последовательным выполнением сборки и сварки; многоме
стные установки и станки; установки с кантовкой изделия для наложения швов с разных сторон изделия; многопозиционные станки последовательного действия. Наиболее полным образом идея интеграции сварочных операций путем их последовательного выполнения с одного установа изделия реализу ется с применением сварочных роботов.
При интеграции с параллельным выполнением элементов операции осуществляются одновременно на одном рабочем месте несколькими сва рочными автоматами (головками, инструментами) или на нескольких изде лиях. При этом элементы операции могут начинаться как одновременно, так и со сдвигом во времени, меньшим продолжительности выполнения самого короткого элемента. Для одновременного выполнения элементов операций на одном рабочем месте могут применяться различные многоголовочные ус тановки и станки для дуговой сварки, роторные сварочные установки.
Последовательно-параллельному выполнению элементов операций присущи особенности как последовательной, так и параллельной интеграции.
Типичный производственный процесс (римскими цифрами обозначены номера операций) может быть представлен тремя вариантами маршрутных схем:
1. Процесс осуществляется несколькими однооперационными машина ми, связанными между собой транспортными устройствами и буферными на копителями (промежуточными складами полуфабрикатов). Такая система машин представляет собой поточную линию или ее участок с гибкой связью между технологическими машинами:
2. Процесс осуществляется однооперационными машинами с жесткой транспортной связью, не имеющей буферных накопителей. Такая система представляет собой сблокированную поточную линию (или ее участок):
3. Процесс осуществляется одной многооперационной машиной—ком байном:
Первые две схемы построены на принципе дифференциации операций, третья - на принципе интеграции.
Сравнивая эти три схемы по числу вспомогательных операций, можно обнаружить, что замена расчлененной линии первого типа одной многоопе рационной машиной третьего типа позволяет исключить из процесса шесть промежуточных операций по передаче, хранению и выдаче полуфабрикатов
из накопителей (вариант 1).
Замена нескольких жестко сблокированных машин второго типа одной многооперационной комбинированной машиной третьего типа влечет за со бой сокращение числа вспомогательных операций на три (вариант 2).
В общем случае замена нескольких однооперационных машин одной многооперационной позволяет исключить промежуточные вспомогательные операции: при замене варианта 1 число вспомогательных операций, исклю
ченных из процесса, |
|
*1 = 2(л-1), |
(12) |
при замене варианта 2 число вспомогательных операций, исключенных из процесса,
/2 = ( /i - l) . |
(13) |
Здесь п - число технологических операций; / - |
число вспомогательных опе |
раций, исключенных из процесса. |
|
Объединение производственных операций позволяет значительно со кратить суммарную продолжительность и трудоемкость не только вспомога тельных операций, но и основных - технологических, в особенности если это объединение производится как совмещение операций во времени и простран стве с превращением их в одну комплексную операцию. В этом случае общая продолжительность совмещенных операций, а зачастую и их трудоемкость, равна продолжительности и трудоемкости той из них, которая имеет наи большее операционное время при независимом выполнении и при той же степени механизации.
Для оценки эффективности интеграции операций по сравнению с диф ференциацией используется коэффициент увеличения производительности труда Кт = Т0 Р0 / ( Т„ Р„), (14)
где Т0 и Р0 - соответственно время цикла и число рабочих при изготовлении сварного узла на нескольких отдельных установках поточной линии (при дифференциации операций); Ти и Ри - то же, на агрегате с интеграцией опе раций. Обычно для небольших агрегатов Ри = 1. В то же время для группы отдельных установок Р0 > 1 и чаще всего равно числу установок в ней. Со вершено очевидно, что интеграция целесообразна при Кт > 1.
Для групп отдельных установок время цикла регламентируется про должительностью самой длительной операции:
То = ^3 -*■^В.О ^0.0 ^Вэ |
(15) |
где t3- время загрузки изделия; /„.о и t0 0- соответственно вспомогательное и основное время самой длительной операции; tB- время выгрузки изделия.
Для иллюстрации принципа совмещения операций рассмотрим два технологических процесса и соответственно две системы комплексной меха низации, построенных по разным принципам, но предназначенных для вы пуска одних и тех же сварных изделий, например, кузовов шахтных вагоне ток. Кузов (рисунок в табл. 2) состоит из цилиндрической части - боковины 2
и двух днищ - лобовин 1. Технологической задачей является их сборка и сварка двумя сплошными швами по контуру лобовин. Этому процессу долж на предшествовать формовка цилиндрической боковины из плоского листа.
Таблица 2 Характеристика процесса, основанного на принципе дифференциации
Но |
|
Название |
|
|
|
Кол-во |
|
Схема |
|||
мер |
|
операции |
|
Оборудование |
Операционное |
операции |
|||||
опе |
|
|
|
|
|
рабо |
время, мин |
т |
|||
|
|
|
|
|
|
|
чих |
||||
рации |
|
|
|
|
|
|
|
|
|||
Подача плоской заготов |
Гибочные |
вальцы |
2 |
5 |
|||||||
|
|||||||||||
|
ки боковины, |
вальцовка |
с транспортными |
|
|
||||||
I |
боковины, |
выдача ее |
на |
устройствами |
|
|
|||||
|
стеллаж (промежуточный |
|
|
|
|
||||||
|
склад) |
|
|
|
Сборочный |
кон |
3 |
5 |
|||
|
Подача боковины и лобо |
||||||||||
II |
вин в сборочный кондук |
дуктор с |
транс |
|
|
|
|||||
тор, |
сборка |
кузова |
на |
портными |
устрой |
|
|
аь |
|||
|
прихватках, выдача |
его |
ствами |
|
|
|
|||||
|
на промежуточный склад |
Автосварочная |
2 |
5 |
|||||||
|
Подача собранного кузо |
||||||||||
ш |
ва на автосварочную ус |
установка с транс |
|
|
|||||||
тановку, |
сварка двух |
портными |
устрой |
|
|
||||||
|
швов, |
выдача |
готового |
ствами |
|
|
|
||||
|
кузова на поток |
|
|
|
|
|
Таким образом, рассматриваемый технологический процесс состоит из трех основных операций: I - формовка боковины (заготовительная опера ция); П - сборка боковины с двумя лобовинами; III - сварка двух криволи нейных швов, соединяющих лобовины с боковиной.
Кроме того, должны выполняться различные вспомогательные и транспортные работы, число и продолжительность которых зависят от вы бранного оборудования и организации механизации, в частности, от степени совмещения операций во времени и пространстве.
Ниже представлены схемы расположения оборудования и технологи ческого процесса изготовления кузова:
схема, построенная по принципу дифференциации - расчленения опе раций:
Ш Поток
и схема, построенная по принципу совмещения операций:
Здесь 1 - плоские боковины; 2 - отформованные боковины; 3 - лобовины; 4 - собранные кузова. Состав оборудования, число рабочих и операционное вре мя приведены соответственно в табл.2 и 3.
Таблица 3 Характеристика процесса, основанного на принципе
совмещения операций
Номер |
Название |
|
|
||
опера |
Оборудование |
||||
операции |
|||||
ции |
|
|
|||
Подача плоской заготовки |
Вальцесварочная |
||||
|
|||||
|
боковины и двух лобовкн, |
установка с |
тра |
||
|
вальцовка |
боковины, |
нспортными |
уст |
|
I, II, III сборка ее с |
лобовинами, |
ройствами |
|
сварка двух швов, выдача готового кузова на поток
Число |
Операци |
Схема |
|
рабо |
онное |
||
операции |
|||
чих |
время, мин |
||
& |
|||
2 |
5 |
Практика сварочного производства наглядно свидетельствует об эф фекте, который может быть достигнут концентрацией и объединением тех