
книги / Подготовка полуфабрикатов для получения бумаги
..pdf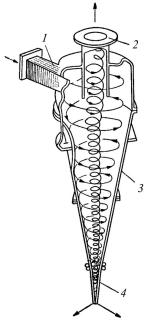
Схема очистки от тяжеловесных частиц представлена на рис. 36. Очищаемая масса, содержащая тяжеловесные включения, подается тангенциально через боковой патрубок гидроциклона. Внутри гидроциклона формируется нисходящий по спирали поток. Вследствие повышенного давления на входе (3,0–3,5 атм.)
внутри гидроциклона происходит перераспределение давления по сечению: вблизи пристеночного пространства образуется зона максимального давления, а по оси гидроциклона образуется зона разрежения. Частицы массы, двигаясь по внутренней поверхности центриклинера, под действием центробежных сил приобретают различный вес, в зависимости от исходного удельного веса. Вследствие конусности центриклинера постепенно все компоненты массы попадают в зону разрежения, по оси которой формируется восходящий поток. Тяжелые частицы, попадая в зону разрежения, продолжают двигаться вниз, так как подъемной силы осевого потока зоны разрежения недостаточно для их подъема.
Хорошее волокно, имеющее меньший вес по сравнению с тяжелыми отходами, подхватывается восходящим
потоком, движется вверх и выходит из центриклинера через патрубок, расположенный в центре верхней крышки.
Для увеличения степени очистки в нижней части центриклинера дополнительно может быть установлена турбулизирующая насадка. В этой насадке дополнительно создается вихревой поток за счет подачи определенного количества воды по касательной к внут-
111
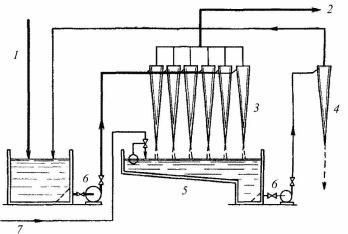
ренней поверхности насадки. Дополнительное разбавление отходов и дополнительный вихревой импульс способствуют более полному выделению хорошего волокна.
Концентрация массы на входе 0,2–1,0 %, на выходе примерно в 3 раза выше, чем на входе (примерно 1,5 %).
Вместе с отходами после одноступенчатой очистки уходит 10– 20 % хорошего волокна. Для возврата этого волокна на практике применяют двух-, четырехступенчатые схемы очистки. При переходе отходов от одной ступени очистки на другую концентрация массы на входе в центриклинер снижается, так как при пониженной концентрации массы легче очищать волокнистую суспензию.
Концентрация массы на первой ступени равна 0,5–0,8 %; на второй – 0,35–0,40 %; на третьей – 0,2–0,5 %.
Рис. 37. Схема двухступенчатой установки центриклинеров: 1 – поступление неочищенной массы; 2 – выход очищенной массы; 3 – центриклинеры первой ступени; 4 – то же второй ступени очистки; 5 – сборник отходов;
6 – насос; 7 – вода для разбавления отходов
На рис. 37 показана схема установки центриклинеров для очистки бумажной массы в две ступени. Разбавленная масса насосом подается на центриклинеры первой ступени, очищенная масса далее поступает на узлоловители, а отходы – в сборник и другим насосом
112
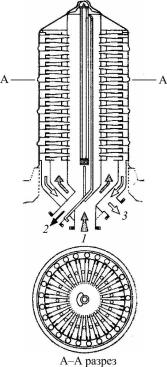
подаются на вторую ступень сортирования. Очищенную массу после второй ступени направляют обратно в первый сборник, а отходы – в сток. Для дополнительного разбавления отходов сортирования используется оборотная вода.
Радиклон (рис. 38) представляет собой центриклинерную батарею, скомпонованную в одном цилиндрическом закрытом корпусе, причем центриклинеры внутри этого корпуса расположены ради-
ально в горизонтальном положении. |
|
|||||||
Масса при концентрации около 0,5% |
|
|||||||
под давлением 0,2 МПа поступает в |
|
|||||||
радиклон |
снизу |
через |
центральный |
|
||||
патрубок и распределяется в коль- |
|
|||||||
цевом |
пространстве, |
отгороженном |
|
|||||
вертикальными кольцевыми |
стенка- |
|
||||||
ми, в которое выведены входные |
|
|||||||
устья горизонтально лежащих цен- |
|
|||||||
триклинеров. |
Каждый |
центриклинер |
|
|||||
снабжен двумя тангенциально при- |
|
|||||||
соединенными к его головке входны- |
|
|||||||
ми патрубками. |
Отсортированная |
|
||||||
масса из центральных выходных пат- |
|
|||||||
рубков центриклинеров выводится в |
|
|||||||
общий кольцевой канал, расположен- |
|
|||||||
ный по периферии кожуха радиклона. |
|
|||||||
Отходы из всех центриклинеров, вы- |
|
|||||||
ходящие из их конических насадок, |
|
|||||||
попадают |
в |
сборную |
центральную |
|
||||
камеру, разбавляются водой и выво- |
|
|||||||
дятся из радиклона через общий ниж- |
Рис. 38. Устройство радиклона: |
|||||||
ний патрубок. |
|
|
|
|
1 – вход неочищенной массы; |
|||
Давление на выходе очищенной |
||||||||
2 – выпуск отходов; 3 – выход |
||||||||
массы |
поддерживается на |
уровне |
очищенной массы |
|||||
0,1 МПа. Производительность одного |
|
центриклинера в радиклоне типа Р-40 составляет 40 дм3/мин, типа Р-100 и С-100 100 дм3/мин. В одном радиклоне типа Р-40 устанавли-
113
вают 150–250 центриклинеров, что дает общую производительность от 6 до 10 дм3/мин. В радиклонах типа Р-100 устанавливают 100– 300 центриклинеров (производительность от 10 до 30 дм3/мин), в радиклоне С-100 – от 50 до 450 центриклинеров (производительность 5–45 дм3/мин).
Очистку массы в радиклонах, как правило, ведут в три ступени. На первой ступени устанавливается один радиклон, а вторая и третья ступени совмещаются в другом радиклоне, разделенном дополнительной горизонтальной перегородкой на две части. При одинаковой производительности для радиклонов требуется примерно в 5–6 раз меньше площади, чем для обычных центриклинеров при рядовой вертикальной установке. К числу недостатков приходится отнести невозможность визуального наблюдения за процессом работы и затруднения при ремонте, так как радиклон представляет собой полностью закрытую конструкцию. Для облегчения ремонта предусмотрена возможность подъема кожуха при помощи гидравлического устройства, а для кратковременного контроля можно снимать верхнюю крышку. Радиклоны марки Р-40 применяются для очистки беленой целлюлозы, марки Р-250 – для очистки небеленой целлюлозы.
17. ДЕАЭРАЦИЯ МАССЫ
При отливе бумаги на бумагоделательной машине одним из нежелательных компонентов бумажной массы является воздух, обычно содержащийся в ней от 0,4 до 6 % по объему. Это, казалось бы, небольшое содержание воздуха в массе на самом деле является высоким по отношению к объему волокон. Так, в массе, поступающей на бумагоделательную машину с концентрацией волокон 0,5 %, указанное содержание воздуха соответствует 80–1200 % по отношению к объему волокон. Скоплению воздуха в бумажной массе способствует ее непрерывное перемешивание и перекачивание насосами, сопровождаемое засосом воздуха.
114
Газы присутствуют в волокнистой суспензии в трех состояниях: свободном, связанном и растворенном. Свободный – это газ, который стремится всплыть на поверхность массы и поэтому его концентрация уменьшается с увеличением расстояния от поверхности. Такой газ может быть легко удален. Связанный газ не удаляется простой выдержкой массы при пониженном давлении потому, что либо он прочно связан с волокнами, либо заключен внутри сгустков волокон, стабилизируя хлопья из-за действия сил поверхностного натяжения. При изменении температуры массы содержание растворенного в ней воздуха меняется. Так, с повышением температуры от 0 до 30 °С растворимость воздуха в воде уменьшается примерно
в2 раза. Растворенный в суспензии воздух не вызывает каких-либо серьезных затруднений.
Вредное влияние воздуха в бумажной массе обнаруживается при выделении его в виде пузырьков и сказывается в образовании пены и сгустков волокон в потоке массы, что, в свою очередь, влечет за собой появление в бумаге воздушных пузырей, неровного просвета и других дефектов. Увеличивается брак бумажной продукции и возрастает число обрывов бумажного полотна на бумагоделательной машине. Неудивительно, что эти затруднения возникают чаще летом при наличии теплой производственной воды, когда растворимость воздуха в суспензии снижается.
Воздушные пятна в бумаге легко обнаружить при рассмотрении ее на просвет. Они выглядят в виде просвечивающих пятен круглой формы. При внимательном рассмотрении бумаги в отраженном свете эти воздушные пузыри вследствие большей прозрачности листа
вэтих местах кажутся несколько темнее общего фона бумаги.
Бумага с воздушными пузырями из-за своей неоднородности неравномерно воспринимает типографскую краску, что отрицательно сказывается на качестве печати, особенно иллюстрационной.
При изготовлении цветных видов бумаги пенообразование нередко влечет за собой скопление частиц красителя на стенках пузырьков и получение вследствие этого неравномерной, с пятнами, окраски бумаги.
115
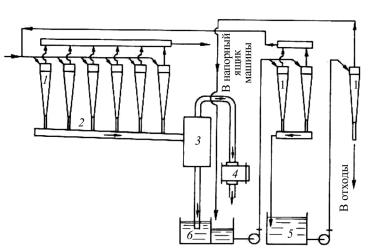
При изготовлении многослойного картона наличие воздуха в бумажной массе заметно снижает межслоевую прочность и часто наблюдается расслоение картона.
При большом содержании воздуха в массе часть воздушных пузырьков, адсорбируясь на поверхности волокон, препятствует контакту между ними, что снижает прочность бумаги из-за уменьшения поверхности образования межволоконных связей.
Одним из способов борьбы со скоплением воздуха в бумажной массе является сочетание предварительной очистки массы с ее деаэрацией.
На рис. 39 приведена современная схема трехступенчатой очистки бумажной массы в центриклинерах 1.
Рис. 39. Схема очистки бумажной массы в центриклинерах, работающих под разрежением
Особенностью этой схемы является работа центриклинеров под разрежением, создаваемым вакуум-насосом 4. Отходы от первой ступени центриклинеров поступают через закрытый коллектор 2 в сепаратор 3, где от них отделяется воздух, отсасываемый вакуумнасосом 4. Отходы же из сборника 6 насосом подаются на вторую
116
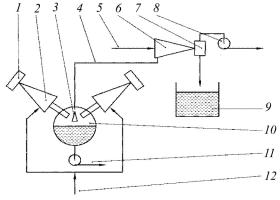
ступень очистки. Отходы от второй ступени центриклинеров из сборника 5 поступают на третью ступень очистки, а очищенная масса со второй ступени поступает для вторичной очистки на первую ступень центриклинеров. Отходы с третьей ступени направляются в сток, а очищенная масса – на вторую ступень центриклинеров.
За рубежом известны различные конструкции вихревых очистителей, работающих с использованием вакуума для деаэрации бумажной массы (форвак, форжект и др.). Степень удаления воздуха из массы достигает при этом 92–97 % от исходного количества воздуха в массе.
Более эффективно деаэрация осуществляется в декулатор-клинерах (рис. 40, 41). Декулатор представляет собой цилиндр (ресивер) диаметром до 1,8 м, длиной до 9 м, устанавленный непосредственно перед напорным ящиком буммашины.
Рис. 40. Схема деаэрации массы в декулатор-клинере: 1 – сборник отходов первой ступени центриклинеров; 2 – центриклинеры; 3 – отражатель; 4 – воздух; 5 – пар; 6 – паровой эжектор; 7 – конденсатор; 8 – вакуум-насос; 9 – гидрозатвор; 10 – декулатор; 11 – подача массы на буммашину; 12 – подача массы на деаэрацию от смесительного насоса
Предварительно очищенная на совмещенных с декулатором центриклинерах масса подается в декулатор, где, ударяясь о поверхность отражателей, разбрызгивается до мелкодисперсного состояния и деаэрируется.
117
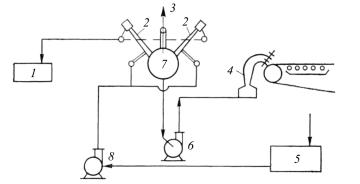
Вакуумная система состоит из парового эжектора, конденсатора и вакуумного насоса и обеспечивает вакуум 87–97 кПа.
Рис. 41. Схема установки декулатор-клинера: 1 – сборник отходов; 2 – центриклинеры; 3 – трубопровод к вакуум-насосу; 4 – напорный ящик; 5 – сборник неочищенной массы; 6 – насос для подачи очищенной массы на бумагоделательнуюмашину; 7 – декулатор; 8 – насосдлянеочищенноймассы
При практическом применении декулаторов были достигнуты следующие результаты:
1)полностью ликвидировано пенообразование и накапливание сгустков волокон в напорном ящике бумагоделательной машины;
2)оказались ненужными водяные спрыски для разбивки пены
внапорном ящике открытого типа, вследствие чего сократился расход свежей воды и повысилась температура массы, что облегчило обезвоживание при выработке газетной бумаги примерно на 10 %;
3)значительно сократились холостые пробеги бумагоделательных машин в связи с ликвидацией сгустков волокон и пены;
4)скорость машин в ряде случаев удалось повысить (при выработке газетной бумаги на 5–9 %) и соответственно увеличить производительность бумагоделательных машин;
5)улучшилось качество бумаги за счет большей равномерности просвета, повышения плотности и гладкости, а также полного устранения воздушных пузырей в бумажном полотне;
118
6) благодаря деаэрации бумажной массы при сушке бумаги удалось снизить расход пара (по некоторым данным на 4 %).
Совмещение процессов очистки и деаэрации массы оказалось возможным не только путем использования специальных очистителей (форваков или форжектов) или же путем использования центриклинеров с созданием вакуума в их нижней части, было удачно осуществлено также сочетание очистки и деаэрации массы установкой в перевернутом виде центриклинеров над декулатором (декула- тор-клинер) таким образом, чтобы вакуум в декулаторе способствовал всасыванию бумажной массы через центриклинеры.
18. РАЗБАВЛЕНИЕ И ПОДАЧА МАССЫ НА МАШИНУ
После машинного бассейна масса подается в ящик постоянного напора, перед которым часто устанавливают дисковые или конические мельницы, с целью устранения пучков волокон и выравнивания степени помола, которая при этом может увеличиться на 1–2 ○ШР
(рис. 42).
Ящик имеет три отделения: приемное, переливное и постоянного напора. Он служит для обеспечения постоянного напора массы и устранения ее пульсации, а также для удаления из нее воздуха. Перелив должен составлять не менее 5–15 % от поступающей массы. Перед поступлением массы на сетку бумагоделательной машины она разбавляется подсеточной водой до концентрации 0,1–1,3 %. Степень разбавления зависит от массы 1 м2 бумаги, природы волокна и степени его помола, температуры массы, конструкции сеточного стола и др.
Чем ниже концентрация массы перед отливом, тем более однородной получается структура бумаги. С повышением степени помола массы понижается скорость ее водоотдачи, что также способствует улучшению структуры бумаги.
119
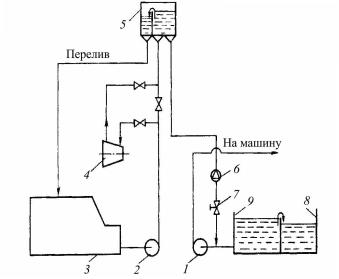
Рис. 42. Схема разбавления и регулирования подачи массы на машину:
1 |
– |
смесительный насос; 2 – массный |
насос; 3 – массный бассейн; |
4 |
– |
мельница рафинирующая; 5 – |
ящик постоянного напора; |
6 – расходомер; 7 – задвижка дозирующая; 8 – сборник избыточных вод; 9 – сборник подсеточных вод
Масса из бака постоянного уровня через расходомер поступает во всасывающий патрубок смесительного насоса под углом 45○ в направлении движения потока, в который также поступает регистровая вода. Поскольку бак постоянного уровня находится на 4–6 м выше уровня регистровой воды, то при перемещении задвижки с изменением расхода массы будет меняться количество поступающей в насос регистровой воды, а общее количество массы, подаваемое на машину, будет постоянным. Иногда смесительный насос имеет двигатель с регулируемой частотой вращения, что позволяет регулировать расход массы.
Схема массоподготовительного отдела бумажной фабрики представлена на рис. 43.
120