
книги / Подготовка полуфабрикатов для получения бумаги
..pdf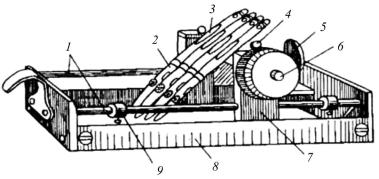
–слабоклееные – расход канифоли 0,5–1,0 % от массы волокна (типографская, мешочная, обойная, афишная и др.);
–неклееные – электроизоляционные, впитывающие, папиросная и др.
Таким образом, процесс проклейки в зависимости от назначения бумаги преследует разную цель, поэтому различны используемые проклеивающие вещества и методы контроля степени проклейки бумаги.
Рассмотрим три основных метода определения степени проклейки бумаги, принятых в России.
Чернильно-штриховой метод характеризует сопротивление бумаги растеканию чернил на ее поверхности и проникновению их
втолщу бумаги. Этот метод особо важен для характеристики основного свойства писчей бумаги. Сущность метода заключается в нанесении четырьмя рейсфедерами на поверхность исследуемой бумаги штрихов стандартными чернилами. Рейсфедеры укрепляют на валу каретки прибора под углом 45° к поверхности бумаги. Степень ее проклейки характеризуется наибольшей шириной штриха, чернила которого не прошли на обратную сторону бумаги (рис. 20).
Рис. 20. Прибор ШПБ для определения степени проклейки бумаги: 1– направляющие рамки прибора; 2 – рейсфедеры; 3 – муфточка; 4 – фиксатор; 5 – ручка; 6 – валик; 7 – опорный ползунок;
8 – основание прибора; 9 – стопорные кольца
51
Поверхностная проницаемость бумаги к действию воды определяется методом Кобба, характеризующим именно поверхностную водостойкость, а не водостойкость бумаги в целом. Метод является важным применительно к определению степени проклейки обойной бумаги, основы для гуммирования, различным видам бумаги с покрытиями. Он основан на поглощении воды поверхностью бумаги при определенных условиях. Результат измерения выражается массой воды (в граммах), поглощенной поверхностью 1 м2 за определенное время.
Для определения сопротивления бумаги прохождению жидкости через ее толщу пользуются методом сухого индикатора. Этот метод заключается в определении времени прохождения жидкости через толщину бумаги. После соприкосновения одной стороны бумаги с жидкостью включается секундомер и отмечается время изменения цвета сухого порошка индикатора, нанесенного на противоположную сторону бумаги. Обычно при опытах пользуются дистиллированной водой с температурой 20±1°С, но при определении степени проклейки фотоподложки может быть использован раствор фотопроявителя или эквивалентный ему 10%-ный раствор соды.
Указанные методы определения степени проклейки бумаги основаны на различных физических принципах измерений и поэтому результаты, полученные разными методами испытаний, непосредственно несопоставимы. В каждом отдельном случае нужно выбирать метод определения степени проклейки, наиболее соответствующий потребительским условиям использования бумаги.
7.2. Основные виды сырья для производства канифольного клея
Живичную канифоль получают при подсочке хвойных пород древесины, главным образом сосны, в которой содержится 75–80 % канифоли и 15–20 % скипидара. Фракционной отгонкой живицу очищают от летучих компонентов, т.е. скипидара.
Экстракционную канифоль (пневый осмол) получают экстракцией из измельченной древесины органическими растворителями
52
(бензол, бензин). Из экстракта после отгонки скипидара получают темную смолу.
Талловую канифоль получают из побочных продуктов сульфатной варки целлюлозы из так называемого сульфатного мыла. Сульфатное мыло обрабатывают серной кислотой и получают талловое масло, а из него перегонкой получают талловую канифоль.
Важным показателем качества канифоли является интенсивность ее окраски. Чем светлее канифоль, тем выше ее качество. Необходимо, чтобы канифоль содержала как можно меньше окисленной смолы, которая образуется при длительном хранении под действием кислорода и света.
Размягчение канифоли начинается при температуре 70 °С, плавление – при 90 °С, плотность – 1,01–1,09 г/см3, ее химическая формула: C20H30O2. Это вещество представляет собой смесь смоляных кислот: абиетиновой, пимаровой, полюстровой и др. Количество смоляных кислот в канифоли характеризуется кислотным числом.
Кислотным числом канифоли называется количество миллиграммов едкого калия (KOH), необходимого для полной нейтрализации свободных кислот, содержащихся в 1 г канифоли (число омыления хорошей канифоли не ниже 66).
7.3. Виды канифольного клея и его приготовление
Варка канифольного клея представляет собой процесс нейтрализации смоляных кислот канифоли щелочью, в качестве которой применяют едкий натр или карбонат натрия. При этом протекают реакции
С19Н29СООН + NаОН → С19Н29СООNа + Н2О,
2С19Н29СООН + Nа2CO3 → 2С19Н29СООNа + Н2О + CO2
с образованием смолянокислого натрия (резината натрия).
Для полной нейтрализации канифоли требуется 13 % NаОН или
17% Nа2СО3 к массе канифоли.
Взависимости от количества непрореагировавшей смолы различают следующие виды клея:
53
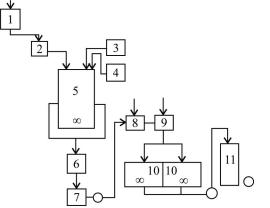
–высокосмоляной с содержанием смолы до 70–90 %;
–белый с содержанием смолы до 40 %;
–нейтральный, или бурый.
В последнем случае нейтрализованы практически все кислоты. Выбор вида клея определяется жесткостью производственной воды. Бурый клей хорошо проклеивает в мягкой воде, белый – в во-
де средней жесткости, высокосмоляной – в жесткой воде.
Схема приготовления белого клея горячим способом из расплавленной канифоли представлена на рис. 21.
Рис. 21. Схема приготовления белого клея горячим способом из расплавленной канифоли: 1 – плавильник канифоли; 2 – мерник расплавленной канифоли; 3 – бак для раствора щелочи; 4 – бак с горячей водой; 5 – реактор с мешалкой и паровой рубашкой; 6 – фильтр; 7 – мерник клея; 8, 9 – инжекторы; 10 – промежуточныебаки; 11 – бакдля храненияклея
Канифоль расплавляется в плавильнике и через мерник поступает в реактор вместе с щелочью и водой. Реактор имеет быстроходную мешалку. Процесс ведется при температуре 95–105 °С
втечение 1 ч. После реакции клей имеет концентрацию 300 г/л. Он фильтруется и собирается в баки-сборники. Затем насосом-доза- тором подается на первую ступень эмульгирования и разбавления
винжектор (рис. 22), куда подается горячая вода. Концентрация клея снижается до 100 г/л.
54
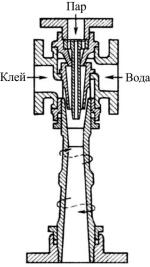
На второй ступени подается холодная вода и концентрация клея становится равной 20 г/л при температуре 20–25 °С. Из баков для хранения клея он подается в расходные баки бумажной фабрики. Клей готовится в клейно-минеральном отделе бумажной фабрики. Полный оборот реактора из расплавленной канифоли составляет 1,5 ч. При работе с кусковой канифолью время варки увеличивается до 2–2,5 ч, оборот реак-
тора 2,5–3 ч.
При варке высокосмоляного клея |
|
|
в реактор необходимо добавить защит- |
|
|
ный коллоид – казеин, так как частицы |
|
|
этого клея быстро коагулируют. |
|
|
Канифольный клей с высоким со- |
|
|
держанием свободной смолы различ- |
|
|
ных марок широко применяется за ру- |
|
|
бежом. Изготовляется клей на типовой |
|
|
установке (рис. 23). Расплавленная ка- |
Рис. 22. Инжектор |
|
нифоль из бака 1 поступает в эмуль- |
||
для диспергирования |
||
сер 5 вместимостью 2 м3, куда подается |
||
клеевых частиц |
||
также вода, щелочь из бака 3 и в про- |
|
цессе варки казеинат натрия из бака 4. Эмульсер снабжен быстроходной мешалкой (1500 мин–1) и рассчитан на одновременную загрузку 400 кг канифоли. На одну варку расходуется 22 кг казеина, 2,2 кг едкого натра для растворения казеина и 11 кг едкого натра для нейтрализации канифоли. Время варки в эмульсере примерно 1 ч.
Клей с высоким содержанием свободной смолы обладает рядом серьезных достоинств. Он устойчив к солям жесткости производственной воды и может быть успешно использован в условиях жесткой производственной воды. Вместе с тем вполне себя оправдала и многолетняя практика его применения в условиях мягкой производственной воды. Частицы высокосмоляного клея имеют в среднем диаметр 1 мкм, тогда как частицы белого клея – 3–4 мкм. При ис-
55
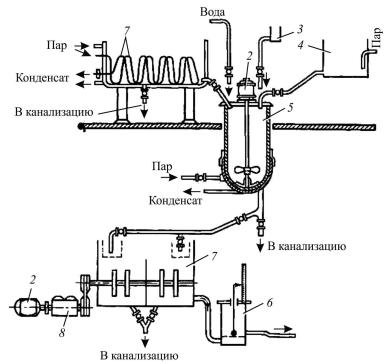
пользовании высокосмоляного клея может существенно экономиться сернокислый алюминий. В этом случае отношение расхода канифоли к сернокислому алюминию составляет 1 : 1 и рН среды при проклейке примерно 6, тогда как при применении белого клея это соотношение обычно поддерживается в пределах от 1 : 1,5 и даже до
1 : 2, а рН среды 4,5–5.
Рис. 23. Схема установки для приготовления высокосмоляного клея: 1 – бак для плавления канифоли; 2 – электродвигатели; 3 – бачок для щелочи; 4 – бак для растворения казеина; 5 – бак для варки клея (эмульсер); 6 – мерник; 7 – сборник готового клея; 8 – редуктор
Возможность получения хороших результатов проклейки при более высоком значении рН обеспечивает лучшую сохранность одежды бумагоделательных машин (сеток и сукон), меньшую корро-
56
зию оборудования и большую долговечность изготовляемой бумаги. Наличие в клее высокого содержания свободной смолы дает возможность поддерживать на заключительной стадии сушки более низкую температуру сушильной поверхности, чем в случаях белого и, тем более, бурого вида клея. Высокосмоляной клей устойчив при высокой концентрации. Он может быть изготовлен с концентрацией 400–500 г/л, и в этих условиях при централизованном изготовлении клея его можно в виде клея-пасты перевозить в бочках на предприятия бумажной промышленности. Наконец, важным преимуществом высокосмоляного клея является возможность получения хороших результатов проклейки бумаги при наличии трудно проклеиваемых исходных волокнистых материалов (тряпичных волокон).
Для повышения гидрофобных свойств высокосмоляного клея его можно сочетать с парафином, содержание которого в этом случае составляет 20 %.
Применяют также усиленный или укрепленный канифольный клей, изготовленный на основе модифицированной канифоли. Для этой цели канифоль подвергают гидрированию, этерификации, полимеризации. Это необходимо потому, что в обычной канифоли под действием света и кислорода воздуха происходят необратимые процессы, которые отрицательно влияют на проклейку бумаги. Вследствие высокой температуры плавления модифицированной малеиновым ангидридом канифоли (более 125 °С) процесс нейтрализации щелочью затруднен. Поэтому добавляют обычную канифоль. Таким образом, в усиленном клее только 15–25 % модифицированной канифоли.
Усиленный клей выпускается в виде пасты с содержанием сухого вещества около 70 %. Клей поступает бочках, выдерживается в водяной бане, где подогревается и становится жидким. Модифицированная канифоль может выпускаться в виде порошка, который добавляют к канифольному клею.
Укрепленный клей может быть нейтральным, белым, высокосмоляным в зависимости от условий производства. Клей обладает высокой степенью дисперсности, следовательно, улучшает равно-
57
мерность проклейки. Расход канифоли снижается на 40–50 %. Меньше чувствуются сезонные затруднения с проклейкой. Практически не бывает случаев расклейки бумаги.
К недостаткам применения укрепленного клея можно отнести повышенную электризацию бумаги и флотацию бумажной массы. Последнее сказывается на равномерности подачи массы.
7.4. Основы теории процесса канифольной проклейки
Явления, происходящие при проклейке бумажной массы, весьма сложны и еще недостаточно изучены. Сложность процесса обусловлена коллоидными свойствами веществ, участвующих в проклейке, неоднородностью химического состава целлюлозы, смоляного клея, алюминиевых солей, воды и других компонентов бумажной массы и изменчивостью состава клеевой эмульсии и сернокислого глинозема, подверженных гидролизу.
Как было указано выше, смоляная эмульсия состоит из резината натрия и частиц свободной неомыленной смолы. Резинат натрия, являясь солью слабой кислоты и сильной щелочи, повергается гидролизу, в результате чего образуется коллоидная смола и едкий натр:
С19Н29СООNа + Н2О С19Н29СООН + NаОН.
Гидролиз резината натрия происходит лишь в присутствии волокон, когда образующаяся щелочь поглощается целлюлозой и уходит из сферы действия. В чистых водных растворах этот процесс происходит в очень малой степени. Таким образом, при проклейке бумаги белым и высокосмоляным клеями в результате гидролиза клеевой эмульсии появляется третий компонент – коллоидная смола, отличающаяся более высокой степенью дисперсности по сравнению с частицами неомыленной смолы.
Коллоидная смола и частицы неомыленной смолы обладают в водной среде, как и целлюлозное волокно, отрицательным зарядом. Поэтому, чтобы зафиксировать смолу на волокне, необходимо перезарядить один из компонентов. Эту роль выполняет сернокис-
58
лый глинозем, который вступает в химические и коллоиднохимические реакции с резинатом натрия, солями жесткости воды и зольными элементами волокна. Направление этих реакций во многом зависит от рН среды и от того, в какой форме находятся соединения алюминия, так как сернокислый алюминий также гидролизуется и в зависимости от кислотности среды может находиться либо в диссоциированном состоянии – в ионной форме, либо в недиссоциированном состоянии – в форме гидроксида алюминия.
Гидролиз происходит по схеме
A12(SO4)3 + 6Н2O 2А1(ОН)3 + 3H2SO4,
или в ионной форме
2Аl3 3SO24 6НОН 2А1 ОН 3 6Н 3SO24 .
При повышении кислотности среды увеличивается количество ионов алюминия, а при повышении щелочности, наоборот, – количество недиссоциированного гидроксида алюминия. Каждый из компонентов глинозема вступает в соответствующие взаимодействия с волокном и клеевой эмульсией.
Выпадение резината алюминия – следствие ионной реакции между резинатом натрия и сернокислым алюминием, которая происходит почти мгновенно:
6C19H29COONa + A12(SO4)3 → 2(С19Н29СОО)3А1 + 3Na2SO4.
Резинат алюминия нерастворим в воде и тотчас выпадает в осадок, оседая на волокне. Эта реакция происходит при рН массы 4,5 и ниже.
Роль сернокислого глинозема в процессе осаждения свободной смолы на волокне заключается в том, что он понижает рН и разрушает сольватную оболочку смоляной частицы, вызывая коагуляцию клея. При этом часть резината натрия превращается в резинат алюминия или гидролизуется с образованием свободной смолы, а сульфат алюминия гидролизуется с образованием гидроксида алюминия и сульфата натрия.
59
Ионы алюминия вступают также в обменную реакцию с одно- и двухвалентными катионами золы волокна, вызывая понижение отрицательного заряда целлюлозы и тем самым снижая потенциальный барьер, облегчая в дальнейшем проведение гетерокоагуляции смоляных осадков.
Получающаяся в результате гидролиза сульфата алюминия гидроксид алюминия адсорбирует из раствора трехвалентные ионы алюминия и приобретает положительный заряд. Обладая большой поверхностью и зарядов, она коагулирует взвеси и в том числе коллоидную смолу, частицы которых она доводит до изоэлектрического состояния и даже сообщает им положительный заряд.
Коллоидная смола вместе с хлопьями резината алюминия захватывает более крупные частицы свободной смолы и оседает вместе с ними на волокнах. Коллоидные частицы свободной смолы, стабилизированные казеином, значительно медленнее коагулируют в результате электролитной коагуляции по сравнению с коллоидной смолой и особенно с резинатом алюминия. Поэтому последний значительно ускоряет процесс осаждения на волокне свободной смолы.
Удержанию клеевых частиц способствует развитая при размоле поверхность волокон и их хорошая адсорбционная способность.
Показано, что в отсутствие посторонних материалов отрицательный заряд смолы быстро изменяется на положительный при добавлении небольшого количества сульфата алюминия (1:1) и что клееная целлюлоза достигает изоэлектрического состояния при значительно меньшем количестве сульфата алюминия (почти в 4 раза), нежели неклееная. Таким образом, можно считать установленным, что смола перезаряжается легче целлюлозы, меньшим количеством глинозема, следовательно, при действии сульфата алюминия образуется положительно заряженный осадок смолы, который осаждается на отрицательно заряженных волокнах.
Установлено, что эффективность проклейки бумаги и электрокинетический потенциал смоляного осадка изменяются параллельно, что дает основание считать, что главным фактором проклейки бумаги является электрокинетический потенциал клеевого осадка.
60