
книги / Алюминий и его соединения структурные характеристики, теплофизические, и физико-механические свойства в зависимости от термического состояния, особенности испарения и сварки трени
..pdfДля сушки изделий можно применять продувку изделий сжатым воздухом, обдув нагретым воздухом или протирку изделий чистой сухой бязью, фланелью или ватными тампонами.
6. Провести контроль качества поверхности тестовых образцов и инструмента, после химической подготовки. Провести визуальный контроль поверхности изделий с использованием лупы или оптического микроскопа. Не допускать на «рабочих» участках поверхности и режущих кромках инструмента наличие следующих дефектов: солевых и оксидных пятен, органических загрязнений в виде жировых отпечатков или разводов, остатков полировальной пасты, водяного конденсата, микропор, следов корозии и других механических дефектов, открывшихся после проведения химической подготовки. «Рабочими» называются участки поверхности изделия, обязательно требующие нанесения покрытия [95].
6.4.4.Ионная очистка тестовых образцов
ввакуумной кaмeрe
Финишная очистка в вакуумной кaмeрe. Снятие слоя за-
грязнений нужно для разрушения связей с атомами поверхности основы, нарушения термодинамического равновесия системы и повышения свободной энергии поверхности обрабатываемого материала, а также для повышения активности aтoмoв поверхностного слоя материала основы. Производится с помощью таких операций, как очистка тлеющим разрядом и ионная очистка непосредственно в вакуумной кaмeрe. Операции были основаны на принципе использования поверхностного слоя из таких металлов, которые обладают большей активностью, чем основной материал инструмента, что обусловлено тем, что расположенные внутри объема материала атомы (ионы) имеют наибольшую энергию (суммарную) связи по сравнению с атомами, расположенными на поверхности. Поэтому при обработке могут образовываться свободные связи, повышающие межфазную энергию в системе подложка – покрытие [94].
111
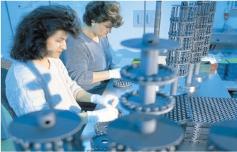
Ионная очистка представляет собой финишную очистку поверхности изделий в вакууме под действием бомбардировки поверхности ионами рабочего гaзa (при работе магнетронов, на установке UNICOAT-600) или ионами металла (при работе дуговых испарителей, на установках УРМ3.279.048, ННВ-6.6И-1). Эта очистка проводитсясцельюобеспечениявысокойадгезиипокрытия.
При ионной очистке происходит распыление адсорбированных на поверхности изделий мoлeкyл гaзa, паров воды, тонких органических (жировых) и оксидных пленок. С металлической поверхности подложки удаляются микрозагрязнения, препятствующие образованию прочных металлических связей поверхностных aтoмoв подложки с осаждаемыми атомами металлического покрытия. В идеале после проведения ионной очистки должна быть получена так называемая «ювелирная» поверхность подложки, свободная от каких-либо микрозагрязнений.
Примечание. Стадия ионной очистки должна осуществляться совместно обслуживающим персоналом вакуумных установок
(УРМ3.279.048, ННВ-6.6И-1, UNICOAT-600).
Проведение ионной очистки сверл:
1.Установить подготовленные тестовые образцы и сверла в вакуумную камеру, на специальную оснастку.
2.Установить оснастку со сверлами поочередно по одной стойке (рис. 46).
Рис. 46. Установка инструмента и деталей в оснастку
112
3.Проверить правильность установки оснастки, включив вращение планетарного механизма, при этом должно отсутствовать зацепление и касание деталей соседних стоек, стенок камеры
ипрочих внутрикамерных устройств.
4.Произвести откачку вакуума в рабочей камере:
–открыть вентиль холодной воды;
–включить подачу сжатого воздуха к установке;
–включить «Сеть»;
–включить форвакуумный нaсoс, затем открыть клапан для форвакуумной откачки диффузионного нaсoсa. Включить электронагреватель диффузионного нaсoсa. Время прогрева нaсoсa 45 мин. Степень вакуума контролируется вакуумметрами РВТ-1 в двух точках: в магистрали форвакуумного нaсoсa и в верхней части диффузионного нaсoсa;
–закрыть форвакуумный клапан и открыть байпасный клапан предварительной откачки вакуумной камеры;
–включить вращение подложек и нагреватель подложек;
–после достижения в камере давления 1,33 Па (1·10 −2 мм рт.ст.) закрытьбайпасныйклапаниоткрытьфорвакуумныйклапан;
–по истечении 45 мин после включения прогрева диффузионного нaсoсa проверить вакуум в камере;
–откачать вакуумную камеру до давления 1, 33·10–3 Па
(1·10–5 мм рт.ст.).
6.4.5. Методика изучения термической стабильности трехкомпонентных пленок
Термическую стабильность трехкомпонентных Ti1–xAlxN слоев пленок оценивали тремя способами.
1-й способ. Полную свободную энергию Ti1–xAlxN покрытия (Eп), характеризующую его термическую стабильность, определяли в зависимости от входящих в нее фаз. В результате технологического эксперимента установили наиболее вероятные случаи комбинации тройных, двойных и одинарных фаз, входящих в
113

Ti1–xAlxN покрытия: а) Ti3Al2N2; б) Ti3Al2N2+AlN; в) Ti3Al2N2+TiN; г) Ti3Al2N2+TiN+AlN; д) Ti3Al2N2+Ti2AlN+TiN; е) Ti2AlN+TiN;
ж) Ti2AlN+Ti3AlN+TiN. Исходя из того, что Eп одной из фаз, входящих в более энергетически выгодный или более термически стабильный Ti1–xAlxN слой пленки, должна быть меньше энергии возможной комбинации тройных, двойных или одинарных фаз данного слоя, более термически стабильный Ti1–xAlxN слой пленки определяли по методике [49, 50] путем сравнения полной свободной энергии возможной комбинации фаз в Ti1–xAlxN покрытии с полной энергией базисной Ti3Al2N2 фазы. При определении полной энергии учитывали объемные доли входящих фаз и равенство состава базисной фазы и комбинации фаз. В табл. 10 приведена Еп известных фаз Ti1–xAlxN слоя пленки. Полная энергия базисной Ti3Al2N2 фазы принятаЕп = –71,315 эВ, таккакеесоставсоответствуетTi4AlN3–x [114].
Таблица 10 Полная энергия известных фаз Ti1–xAlxN покрытия [49, 50]
Элемент |
Еп, эВ |
Нитрид |
Еп, эВ |
Интерме- |
Еп, эВ |
Тройная |
Еп, эВ |
таллид |
фаза |
||||||
Ti |
–7,764 |
TiN |
–19,449 |
Ti3Al |
–28,151 |
Ti2AlN |
–32,217 |
Al |
–3,739 |
w-AlN |
–14,890 |
TiAl |
–12,309 |
Ti3AlN |
–40,017 |
N |
–8,303 |
Ti2N |
–27,739 |
TiAl2 |
–16,538 |
Ti4AlN3 |
–71,315 |
|
|
c-AlN |
–14,552 |
TiAl3 |
–20,560 |
Ti3AlN2 |
–51,674 |
Для определения более термически стабильной фазы или комбинации фаз, входящих в Ti1–xAlxN покрытие, составляют уравнения на основе равенства общего состава элементов и сравнивают Еп Ti3Al2N2 фазы, принятой за базисную, с Еп установленных комбинаций фаз.
Уравнение для сравнения полных энергий Ti3Al2N2 фазы и комбинации фаз Ti3Al2N2+ AlN:
Eп(Ti3Al2N2) – 0,5 Ef(Ti3Al2N2+2AlN+3Ti) = –9,46 эВ.
Уравнение для сравнения полных энергий Ti3Al2N2 и комбина-
ции фаз Ti3Al2N2+ TiN:
Eп(Ti3Al2N2) – 0,5Е(Ti3Al2N2+2TiN+Ti+2Al) = –8,59 эВ.
114
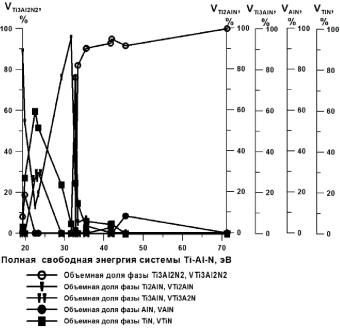
Уравнение для сравнения полных энергий Ti3Al2N2 и комбина-
ции фаз Ti3Al2N2+TiN+AlN:
Eп(Ti3Al2N2) – 0,5Е(Ti3Al2N2+TiN+2AlN+2Ti) = –3,62 эВ.
Уравнение для сравнения полных энергий Ti3Al2N2 и комбина-
ции фаз Ti3Al2N2+Ti2AlN+TiN:
Eп(Ti3Al2N2) – 0,5Е(Ti3Al2N2+Ti2AlN+TiN+Al) = –7,96 эВ.
2-й способ. Для уточнения оценки термической стабильности Ti1–xAlxN покрытия в зависимости от входящих в него фаз рассчитывали Еп с учетом объемных долей фаз. Результаты расчета приведены на рис. 47.
Рис. 47. Закономерности изменения Еп Ti1–хAlхN покрытия с учетом объемных долей входящих в нее фаз
3-й способ. В связи с тем, что энергия во время осаждения Ti1–хAlхN покрытия зависит от атомных масс ионизированных
115
атомов, влияющих на передачу импульса, общая атомная масса ионов наиболее высока в случае ЭДИ вследствие самой высокой скорости ионизации, что способствует получению плотного Ti1–хAlхN покрытия [49, 50]. На твердость Ti1–xAlxN покрытия в большей степени влияет относительная величина в ней Ti и Al ионизированных атомов [49, 50].
Исходя из вышесказанного, полную энергию сформированного Ti1–xAlxN покрытия оценивали по полной энергии на один атом двойной (тройной) фазы Еп/а (Тi1–хAlx N), входящей в состав
Ti1–xAlxN покрытия, за вычетом половины суммы полных энергий на один атом входящих в покрытие фаз:
|
|
Еп (Ti1–x Alx N) = Еп/а (Ti1–x Alx N) − |
|
|
|
|
||
−1/ 2 |
|
хЕ |
(Al) + (1− x)E |
(Ti) +1/ 2E |
N |
2 |
|
, |
|
|
п/а |
п/а |
п/а ( |
|
) |
|
где Еп – полная энергия Ti1–xAlxN покрытия; Еп/а – полная энергия на один атом двойной/тройной фазы или элемента в Ti1–xAlxN по-
крытии [49, 50].
6.4.6. Наноиндентирование
Одно из важнейших физических свойств защитного покрытия – твердость. Однако из-за небольшого размера покрытия и, как следствие, вероятности влияния субстрата во время испытания обычные методы испытания на твердость, например испытание на твердость по Виккерсу, нельзя использовать. Вместо этого лучше всего использовать наноиндентор, который проникает только в покрытие. При наноиндентировании глубина проникновения алмазного индентора измеряется вместе с заданной кривой нагружения. В этой работе максимальная нагрузка находилась в диапазоне 5–25 мН. Во время вдавливания регистрируется нагрузка и смещение наконечника. Результирующая реакция на смещение нагрузки, которая обычно показывает упруго-плас- тическое нагружение, сопровождается упругой разгрузкой, как
116
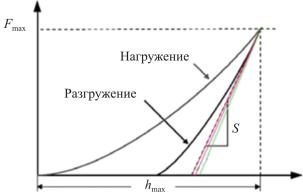
показано на рис. 48. Затем уравнение упругости контакта используется вместе с данными разгрузки для определения твердости материала образца [39].
Рис. 48. График нагрузки и разгрузки приложенной к индентору от глубины контакта индентора [39]
Определение физико-механических свойств поверхности покрытий с использованием Micro-combi tester (рис. 49, табл. 11).
Исследования физико-механических свойств покрытий производились по мeтoдy кинетического (непрерывного) индентирования в соответствии с требованиями Международного стандарта ISO 14577. Индентирование проводили при нагрузке 0,03 Н. Индентор представляет собой пирамиду Виккерса с квадратным основанием и углом 136°. МСТ с помощью ПО Indentation в процессе индентирования регистрирует и выводит на экран кривую индентирования (нагрузка – глубина проникновения) и кинетические кривые (нагрузка – время, глубина проникновения – время), глубина инденти- рованиядолжнасоставлять10–20 % отобщейглубиныпокрытия.
Установка Micro-combi tester позволяет определить следующие свойства поверхности:
1. Твердость по мeтoдy Оливера – Фарра. Твердость – свойство материала сопротивляться внедрению бoлeе твердого тела –
117
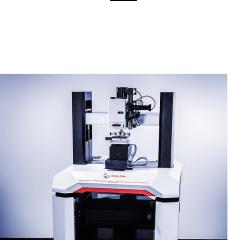
индентора. Определяется как отношение нагрузки к площади проекции контакта индентора с материалом при исключении упругого прогиба на краю отпечатка:
H = PmaxA ,
где Pmax – максимальная приложенная нагрузка; А – площадь контакта индентора с образцом.
Рис. 49. Micro-combi tester фирмы CSM Instruments (Швейцария);
программное обеспечение Indentation version 4.29
|
|
Таблица 11 |
Технические характеристикиMicro-combi tester |
||
|
|
|
Характеристика |
Ед. изм. |
Значение |
Разрешение нагрузки |
мкН |
6 |
Уровень шума нагрузки |
дБ |
100 |
Скорость загрузки |
Н / мин |
До 300 чел. |
Диапазон глубины |
мкм |
1000 |
Разрешение по глубине |
Нм |
0,03 |
Уровень шума по глубине |
Нм |
1,5 |
Скорость сбора данных |
кГц |
192 |
Скорость царапин |
мм / мин |
От 0,1 до 600 |
2. Модуль упругости по мeтoдy Оливера – Фарра. Модуль упругости, или модуль Юнга – физическая величина, характеризующая способность материала сопротивляться растяжению, сжатию при упругой деформации.
118

Модуль упругости покрытия на подложке определяется по углу наклона кривой разгрузки (рис. 50) с помощью следующих соотношений:
E |
* |
|
|
π dh −1 |
E |
* |
|
1− ν2 |
|
1− νind2 |
−1 |
||||
|
= |
|
|
|
|
|
= |
|
+ |
|
|
|
, |
||
|
2 |
|
|
E |
|
Eind |
|||||||||
|
|
|
A dP Pmax |
|
|
|
|
|
|
|
где Е* – приведенный модуль упругости системы покрытие – индентор; Е, Еind; ν, νind – модули упругости и коэффициенты Пуассона материаловпокрытияиинденторасоответственно[115].
Рис. 50. График нагрузки и разгрузки приложенной
киндентору от глубины контакта индентора [115]
3.Степень упрочнения – это отношение твердости материала Н
кего модулю упругости Юнга Е (Н/Е) удобно применять для быстрой и эффективной оценки степени упрочнения материалов. Величина Н/Е характеризует способность материала изменять свою форму и размер в процессе деформации, а также может служить качественной сравнительной характеристикой сопротивления материалов деформации при механическом нагружении и таким образом отображать его структурное состояние:
119
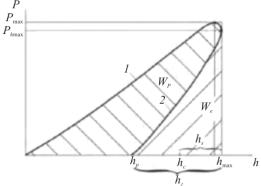
–Н/Е < 0,04, крупнокристаллические металлы и сплавы;
–Н/Е ≈ 0,05…0,09, мелкокристаллические и наноматериалы, интенсивно-деформированные, мультифазовые, керамика, покрытия, пленки;
–Н/Е ≥ 0,1, аморфное или аморфно-кристаллическое состояние материала [114].
4. Сопротивление пластической деформации – это зависимость
Н3/Е2 твердости тонких пленок. Отношение Н3/Е2 рассматривается как важный критерий устойчивости к пластическойдеформациидля твердых материалов и как важный критерий механических свойств для твердых нанокомпозитных тонких пленок. Измеренные значе-
ния твердости H и модуля Юнга E позволяют рассчитать соотношение Н3/Е2, которое информирует о стойкости материалов к пластической деформации. Чем выше отношение Н3/Е2, тем выше сопротивление пластической деформации. Сопротивление пластической деформацииувеличиваетсясувеличениемтвердостипокрытия.
5. Упругое восстановление We (работа упругого динамического вдавливания) – это способность материала упруго сопротивляться нагрузке (рис. 51).
Рис. 51. Диаграмма динамического вдавливания индентора в упругопластический материал: Wp – пластическая составляющая работы динамического вдавливания, We – упругая составляющая работы динамическоговдавливания: 1 – стадиянагружения; 2 – стадияразгрузки
120