
книги / Алюминий и его соединения структурные характеристики, теплофизические, и физико-механические свойства в зависимости от термического состояния, особенности испарения и сварки трени
..pdfсилам во время взлета, посадки, сверхзвуковой скорости маневрирования, приводящим к высоким циклическим нагрузкам и внезапным перегрузкам материала крыла [81]. Проблема сварки АС традиционным способом (клепка, дуговая сварка плавящимся электродом в среде инертного (MIG) или активного газа (MAG), ручная сварка неплавящимися вольфрамовыми электродами в среде защитного газа – аргона (TIG), а также высокоэнергетическая лазерная или электронно-лучевая сварка) заключается в склонности металла шва с высокой теплопроводностью, коэффициентом теплового расширения в сравнительно широком диапазоне температуры застывания и растворимостью водорода в алюминии в расплавленном состоянии к два раза большей усадке при затвердевании, разрушению в зонах теплового воздействия по стыкам деталей и образованию дефектов: рыхлот, цепочек пор в шве и у зоны сплавления, трещин в высокотемпературной ЗТВ, включений прочной оксидной пленки и ферросплавов в шве [81, 82]. Общей проблемой сварки листовых конструкций вследствие большой вероятности разрыва между листами из-за неправильного крепления, неточности процессов производства листов и т.д. является выход материала сварного шва из зоны обработки и эффективной площади поперечного сечения сварной зоны с последующим уменьшением разрыва и дефектностью сварного шва [83]. Оптимальным вариантом решения указанной проблемы является использование сравнительно нового сварочного процесса – сварки трением с перемешиванием (СТП) [74–80].
Алюминиевые деформируемые сплавы, массово применяющиеся в конструкциях ракет-носителей, постепенно перестают удовлетворять требованиям по комплексу механических и эксплуатационных свойств. Становится актуальной проблема улучшения свойств сварных соединений из алюминиевых деформируемых сплавов [75].
Система PDS (машины трения) способна оценить альтернативные, неплоские и криволинейные материалы СТП-инструмен- та, а также материалы конструкций с переменной толщиной и с
71
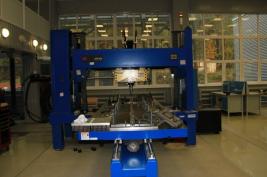
толстым сечением свариваемых деталей; точно измерить и проконтролировать следующие параметры СТП:
–нагрузку и положение пресса;
–нагрузку и положение плеча и/или датчика;
–нагрузку в одной плоскости;
–скорость перемещения;
–частоту вращения и крутящий момент;
–непрерывный процесс сбора данных по СТП и их анализ;
–высокий коэффициент воспроизводимости.
Рис. 24. Установка сварки трением
с перемешиванием I-STIRPDS5 (США) [73–80]
Пятикоординатная система I-STIR™ (рис. 24) благодаря программно управляемому двойному шарнирному соединению со степенями подвижности по наклону и вращению способна сваривать детали двойной кривизны. Инновационная технология системы I-STIR™ обеспечивает максимальную гибкость системы, выполнение сварки инструментом с регулируемым рабочим стержнем и саморегулирующуюся сварку. Технология сварки инструментом с регулируемым рабочим стержнем позволяет системе PDS отводить (втягивать) рабочийстерженьитакимобразомзавариватьотверстиев материале при выходе рабочего стержня, а инструменту с регулируемым рабочим стержнем дает возможность сваривать соединения переменной толщины. Система контроля СТП для обеспечения уста-
72
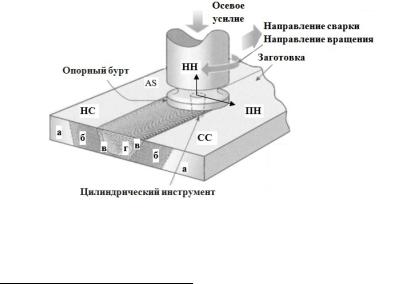
новки дополнительной гибкости может осуществлять контроль инструмента с регулируемым рабочим стержнем; контроль положения либо нагрузки оси плеча2, положения либо осевой нагрузки, положения рабочего стержня на определенном расстоянии от плеча либо отопорнойвставки(т.е. размерперемычки) [74–80].
На основании полученного производственного опыта фирмой «Сеспель» выделены основные требования к оборудованию
итехнологическому процессу СТП:
–жесткость несущих элементов конструкции прижимного устройства;
–отсутствие зазора в стыке свариваемых деталей;
–правильное сопряжение лицевых поверхностей свариваемых деталей без излома;
–оптимальная геометрия инструмента;
–соблюдение режимов сварки – усилия по Z, скорости сварки, частотывращенияинструмента, угланаклонаинструмента[74–80].
Рис. 25. Металлографические характеристики сварного соединения при СТП: а – основной материал; б – зона термического влияния (ЗТВ); в – зонатермомеханическоговлияния(ЗТМВ); г– ядросварногошва(часть ЗТМВ); НН – нормальное направление, ПН – поперечное направление
2 При работе с датчиком исследования поверхности положение плеча можно контролировать через обратную связь такого датчика.
73
В связи с асимметрией схемы сварки различают набегающую сторону (НС), где направление линейной скорости подачи инструмента совпадает с направлением вращения, и противоположную сбегающую сторону (СС) (рис. 25). Со сбегающей стороны металл переносится на набегающую сторону [82]. Вырабатываемое тепло и деформация в процессе СТП приводит к формированию в поперечном сечении сварного шва четырех макроструктурно различных зон [84–86].
Формирование структуры сварного шва (СШ) в процессе СТП. Твердотельный характер процесса СТП в сочетании с необычным инструментом и асимметричным характером СШ приводит к весьма различным микроструктурам вследствие нескольких одновременно протекающих термомеханических процессов [84]. На микроструктуру СШ влияет скорость нагрева, охлаждения, пластической деформации и перемешивания, явления динамической рекристаллизации, а также механическая целостность соединения. Типичное сечение СТП состоит из нескольких зон (рис. 26, а, б) с вытянутой в напpавлении вpащения инстpумента
ипластического течения матеpиала формой [87]:
1.Зона перемешивания (ядро и динамическая зона рекристаллизации) с сильно деформированными зернами, примерно соответствующая расположению рабочего стержня во время сварки. Зерна в зоне перемешивания равноосные и часто на порядок меньше, чем зерна в основном материале. Уникальная особенность зоны перемешивания заключается в наличии нескольких концентрических колец, которые в публикациях называют «луковичные» структуры. Точное расположение данных колец до сих пор не установлено, хотя известно число, размер и текстура зерен.
2.Зона на поверхности сварного шва (СШ), материал которой увлекается плечом от «стороны отхода» СШ вокруг задней части инструмента и выходит на «стороне набегания».
3.Зона термомеханического влияния (ЗTMВ), находящаяся по обе стороны движения, характеризуемая более низкими воз-
74
никающими напряжениями, температурой и меньшим эффектом сварки на структуру шва. Несмотря на то, что микроструктура ЗТМ деформирована, в отличие от зоны перемешивания, она более похожа на структуру основного материала. ЗТМВ технически относится ко всей деформируемой области и часто используется для описания любой зоны, не относящейся к «стороне набегания»
иповерхностной зоне.
4.Околошовная зона термического влияния (ЗТВ), являющаяся общей для всех сварочных процессов. Материал ее не подвергается пластической деформации, но находится под влиянием теплового воздействия процесса (температура ниже, чем в ЗТМВ), приводящего к некоторым микроструктурных изменениям особенно, если микроструктуры термически неустойчивые.
Из научных публикаций установлены четыре региона ЗТВ: деформированные зерна (ДЗ), мелкие зерна (МЗ), критические (КЗ) и докритические зерна (ДЗ) (рис. 26, в) [81, 88].
Одним из ключевых факторов, определяющих совместные структуры, является температура, образующаяся при сварке. Определение температуры в сварных соединениях представляет интерес для понимания совместной структуры и свойств. Для измерения температуры поверхности могут быть использованы пирометры; при СТП сталей видимые изменения цвета можно наблюдать невооруженным глазом. Поверхностная и внутренняя температуры могут быть измерены с помощью термопары, прикрепляемой на поверхности или внутри путем вставки через просверленные отверстия. В таких местах, как ядро и области под плечом, где движется/течет металл не представляется возможным непосредственно измерить температуру с помощью термопар, так же как и пирометров, потому что они находятся вне поля зрения. Данную проблему исследователи решают с помощью компьютерного моделирования, но пока малоэффективно [89].
75
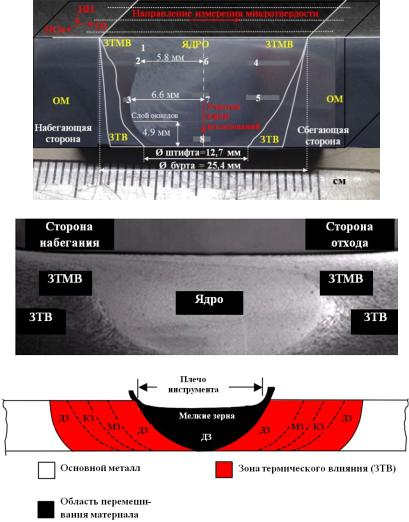
а
б
в
Рис. 26. Сварка трением с перемешиванием: а – схематичное изображение зон СШ [85]; б – поперечное сечение СШ алюминиевых листов [85]; в – микроструктурные зоны СШ [89]
76
Установлена зависимость твердости сварного шва из алюминиевых сплавов от их исходного состояния. Распределение величины твердости алюминиевых сплавов 2ХХХ, свариваемых СТП, отличается от других алюминиевых сплавов 1ХХХ, 3ХХХ-7ХХХ [88]. Многочисленными исследованиями выявлено, что твердость сварного соединения алюминиевых сплавов в основном зависит от размера зерна, микроструктурных факторов и распределения мелких частиц [81]. Каждому сплаву соответствует свой минимальный размер зерна, который может быть достигнут за счет сочетания минимального температурного воздействия и достаточно большого механического перемешивания. В большинстве публикаций изучают зависимость размера зерна в ядре от двух параметров сварки: скорости вращения и скорости подачи [84, 87, 89, 90].
Влияние удельного давления на размер зерна, микроструктуру, химический состав и распределение твердости в сварном шве не исследовано [75].
4.2. Изучение влияния удельного давления на микроструктуру, химический состав и распределение твердости в сварном шве
Пластины с размерами 75/27/12 мм (длина/ширина/толщина) из алюминиевого деформируемого сплава AA2024-О, изготовленные методом прокатки, были сварены СТП при различной величине удельного давления (qр) на инструмент из хромоникелькобальтового сплава MP159 (Ø 12,7 мм) при использовании опорного бурта (Ø 25,4 мм) (рис. 27, табл. 6).
Химический состав основного материала АА2024-О сле-
дующий, мас.%: Si – 0,5; Fe – 0,5; Cu – 3,8–4,9; Mn – 0,3–0,9; Mg – 1,2–1,8; Cr – 0,10; Zn – 0,2; Ti – 0,15; другие – 0,20; Al – ос-
нова. Для обеспечения воспроизводимости процесса при каждом удельном давлении (qр) были получены три различных сварных соединения.
77
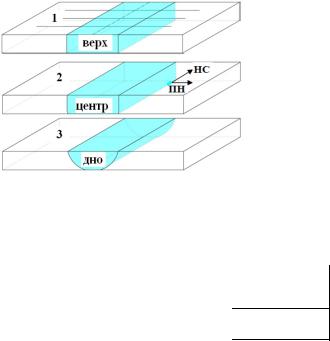
Рис. 27. Схема разрезания сварных пластин AA2024-Т4
|
|
|
|
Таблица 6 |
|
Технологические параметры СТП |
|
||
|
|
|
|
Глубина |
qр, |
Скорость |
Скорость |
Угол наклона |
|
МПа |
вращения, об/мин |
подачи, мм/мин |
инструмента |
вдавливания, мм |
180 |
300 |
300 |
1,5° |
11,3 |
205 |
300 |
300 |
1,5° |
11,3 |
230 |
300 |
300 |
1,5° |
11,3 |
Для проведения исследований микроструктуры тестовые образцы 40/27/12 мм (длина/ширина/толщина) были вырезаны из сваренных пластин АА2024-Т4 перпендикулярно скорости сварки с использованием разрезной машины Discotom-50 (Struers). Поперечные шлифы сварных швов были механически отшлифованы на абразивных дисках (Р320, Р800, Р1200, Р2000) шлифовальных станков LaboPol-2 (Struers) с использованием воды и жидкости DP-Lubricant, затем отполированы с использованием шлифовальной алмазной жидкости DP-Lubricant Blue с дисперсностью 3, 1 и 0,25 мкм и алмазной жидкости, содержащей Al2O3 с дисперсностью 0,1 мкм, на полировальном станке LaboPol-5 (Struers).
Изготовленные микрошлифы были очищены в этиловом спирте в ультразвуковой ванне Struers Metason 200 НТ (методика Aalto University, Finland) и просушены. Травление поперечного сечения сварного шва осуществлено составом Келлера (100 мл
78
HCl, 100 мл HNO3, 25 мл HF, 100 мл H2O). Исследование микро-
структуры поперечного сечения сварного шва до и после травления проведено на аналитическом автоэмиссионном электронном микроскопе Ultra 55 с EDX энергодисперсионным анализатором.
Для изучения распределения твердости сварного шва по сечению тестовые образцы были разрезаны на 3 части (вверх, центр, дно) параллельно направлению скорости сварки (см. рис. 27). Поверхности 1, 2, 3 каждой части тестовых образцов были отшлифованы, отполированы и обезжирены по вышеописанной методике. Твердость поверхностей 1, 2, 3 была измерена при нагрузке 200 г с шагом 0,3 мм в трех параллельных направлениях с использованием автоматизированного микротвердомера DuraScan 70 (EMCO-TEST) с системой микроанализа. Три параллельные дорожки замеров твердости на поверхности 1 показаны на рис. 27. Рентгеноспектральный микроанализ поверхностей 1, 2, 3 сварного шва проведен на спек-
трометре фирмы Oxford Instruments Analitical, модель PMI MASTER UVR Pro с высокочувствительным датчиком UVR в режиме «Искра». Количество прожигов произведено от 9 до 12 в зависимостиот текущихусловийизмеренийипогрешности.
79
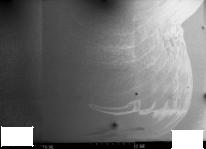
5.ЗАВИСИМОСТЬ СТРУКТУРЫ СОСТАВА
ИТВЕРДОСТИ СВАРНОГО ШВА ОТ УДЕЛЬНОГО ДАВЛЕНИЯ НА ИНСТРУМЕНТ
5.1.Твердость и микроструктурные характеристики шва в зависимости от величины удельного давления на инструмент
Верхняя поверхность зоны перемешивания (ЗП) шире нижней, так как верхняя поверхность подвергается экстремальной деформации и фрикционному нагреву от воздействия инструмента в процессе СТП (рис. 28). Весь сварной шов распределяется между сторонами НС и СС несимметрично. Более интенсивный поток металла образуется на НС, поскольку тангенциальная составляющая вращения имеет то же направление, что и направление подачи, в то время как на СС эти направления противоположны. Более высокий градиент пластической деформации вызван большей деформацией, которая в конечном итоге приводит к довольно четкой границе между зоной термического влияния (ЗТВ) и основным материалом (ОМ) на НС [91]. Граница между ЗТВ и основным материалом на СС неясная в связи с различным пластическим течением между НС и СС при угле наклоназаднейчастиинструмента1,5° [92].
СС НС
Рис. 28. Микрофотография сварного шва после травления
Профили твердости, измеренной в направлении дорожек, изображены на рис. 29. Твердость основного материала по всему
80