
книги / Термическое, термомеханическое и механическое поведение алюминия и его сплавов при различных методах их обработки
..pdf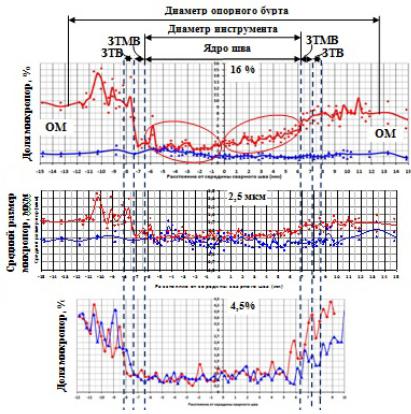
а)
б)
в)
Рис. 40. Усредненная доля (а, в, д) и средний размер микропор по трем дорожкам замера микротвердости (б, г, е) в верхнем (♦)
инижнем (▲) продольном сечении сварного шва, измеренные
внаправлении движения инструмента (см. стр. 93)
91
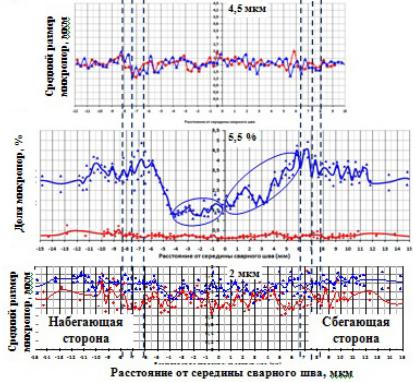
г)
д)
е)
Рис. 40. Окончание
92
(см. рис. 39). На сбегающей стороне скорость роста доли микропор в верхнем продольном сечении, так же как и при минимальном удельном давлении на инструмент, превышает скорость роста доли микропор в нижнем продольном сечении шва. Доля пористости основного металла около ЗТВ в 3 раза меньше по сравнению с аналогичным значением сварного шва, полученного при 180 МПа. Средний размер микропор в основном металле составляет 1,8–2,1 мкм (рис. 40).
В верхнем продольном сечении при максимальном удельном давлении 230 МПа в зонах сварного шва и основном материале, находящемся под опорным буртом, доля микропор составляет 0,1–0,4 %. Средний размер микропор в сварном шве соответствует 0,8–1,4 мкм, в основном материале за пределами опорного бурта – 1,2–1,6 мкм. В ядре шва на набегающей стороне нижнего продольного сечения на расстоянии 4 мм от его осевой линии доля микропор минимальна и составляет 1–1,7 %.
Затем доля микропор в ядре шва резко повышается до 4 % на набегающей стороне, до 4,5 % на сбегающей стороне и колеблется около данных величин в ЗТМВ, ЗТВ и основном материале, находящемся под опорным буртом. Многократное увеличение доли микропор при удалении от центральной линии сварного шва свидетельствует о газовой пористости, вызванной градиентом температуры в сварном шве. За пределами опорного бурта доля микропор основного материала составляет 3 %. В нижнем продольном сечении шва средний размер микропор составляет 1,2–1,8 мкм, в основном материале – 1,5–1,8 мкм.
3.5.Механизм формирования пористости
впоперечном сечении сварного шва в зависимости от удельного давления на инструмент
При недостаточном удельном давлении 180 МПа в начальном поперечном сечении IV шва образуется типичный для набегающей стороны дефект в виде макропор (рис. 41). Переходные
93
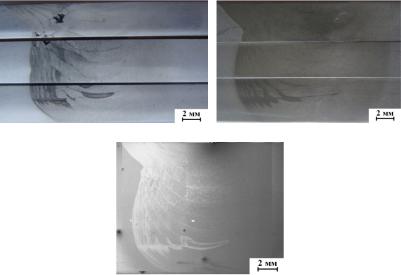
объемы материала шва образуются между областями материала с вращательным движением и областями, в которых материал экструдирует мимо вращающейся оси инструмента [11].
а |
б |
в
Рис. 41. Макропоры в сварном шве в начальном поперечном сечении шва IV. Удельное давление на инструмент, МПа: а – 180; б – 205; в – 230; слева – набегающая сторона, справа – сбегающая сторона
Застой в переходной области на наступающей стороне сварного шва является источником туннельного дефекта – образования макропор. Макропоры с размерами 0,5–1,3 мм образуются в верхнейзонешваинаграницеЗТВ– основнойматериал(рис. 41, а). С повышением удельного давления на инструмент степень перемешивания материала увеличивается, что способствует исключению образования макропор в сварном шве в начальной области шва (рис. 41, б, в).
Результаты изучения механизма образования микропор в поперечном сечении шва по его длине в направлении движения
94
инструмента приведены на рис. 42. Установлены сквозные микропоры на границе основной материал – ЗТВ в месте искривления сварного шва на набегающей стороне на расстоянии 5,8 мм от осевой линии шва. По длине шва микропоры по размеру уменьшаются (рис. 42, а, в, д). В начальном поперечном сечении шва IV образуются многочисленные микропоры с кристаллической структурой размерами 85 × 175 мкм (увеличенный фрагмент 1) и 20 × 40 мкм (увеличенный фрагмент 2), а также цепочка микропор с размерами 20 × 45 мкм (увеличенный фрагмент 3) (см. рис. 42, а). В направлении движения инструмента микропоры в верхней части шва уменьшаются до 18 × 20 мкм (см. рис. 42, в) и до 10 × 13 мкм
(см. рис. 42, д).
В нижней части шва в начальном поперечном сечении шва образуется поверхностная трещина протяженностью 404 мкм, свидетельствующая о полном отсутствии перемешивания вследствие недостаточной глубины опускания инструмента или некачественного выравнивания инструмента по отношению к совместной линии свариваемых пластин (см. рис. 42, б) [11]. В среднем и конечном поперечном сечении шва образуются газовые поры, уменьшающиеся по размеру в направлении движения инструмента (см. рис. 42, г, е). Зигзагообразные кривые 1 и 2 на рис. 42, г являются следствием природного оксида алюминия на поверхности соединяемых пластин. Недавние исследования [11, 91] с помощью просвечивающей электронной микроскопии подтвердили, что эти кривые действительнопосоставу соответствуютчастицамAl2O3.
При минимальном удельном давлении на инструмент 180 МПа в ядре шва на сбегающей стороне в основании инструмента образуются многочисленные макропоры до 800 мкм (рис. 43). С увеличением удельного давления макропоры в корне шва исключаются. В ЗТВ и ЗТМВ на набегающей стороне образуются мелкие газовые поры (рис. 43, б). Результатом напряженного состояния нижней части шва и нарушения его сплошности являются микротрещины (рис. 43, в).
95
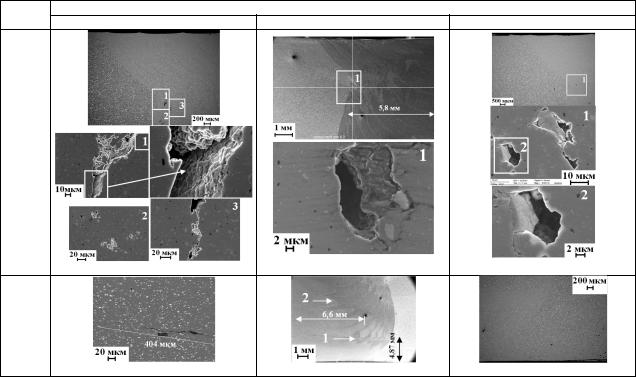
96 |
Часть |
|
Микропоры в поперечном сечении по длине шва |
|
|
шва |
Начальное – IV |
Среднее – V |
Конечное – VI |
Верх
а |
в |
д |
Корень
б |
г |
е |
Рис. 42. Образование микропор в поперечном сечении шва в направлении движения инструмента (удельное давление 230 МПа)
96
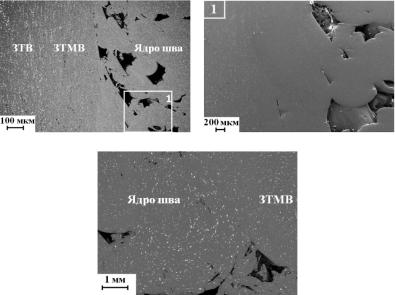
а |
б |
в
Рис. 43. Образование макропор в основании инструмента:
а– на набегающей стороне; б – на сбегающей стороне;
в– увеличенный фрагмент участка (удельное давление 180 МПа)
Врезультате можно заключить, что для случаев удельного давления на инструмент 205 и 230 МПа доля микропор является допустимой и условно сопоставимой. Характер изменения доли пор для каждого случая нагрузки является уникальным, так для случая сварки при 230 МПа в верхней части шва наблюдается константальный уровень количества микропор (0,3–0,4 %) и их размеров (~1,2–1,25 мкм). Однако в нижнем продольном сечении шва наблюдается экстремальный характер распределения микропор. При удельном давлении на инструмент 230 МПа картина обратно противоположная минимальному удельному давлению.
Вверхней части шва количество пор минимальное при 230 МПа, максимальное – при 180 МПа, достигая максимальных значений 14–15 % в ЗТВ и в основном материале сварного шва. Выявлены
97
средние размеры микропор для каждого из удельных давлений на инструмент. Так, для 230 МПа нагрузки средний размер микропор по всем продольным сечениям составил 1,4 мкм, для 205 МПа нагрузки средний размер микропор – 1,45 мкм. Для 180 МПа нагрузки средний размер микропор является не очевидным, так как наряду с микропорами в шве при данной нагрузке встречаются одиночные мезо- и макропоры.
Распределение пористости в зависимости от удельного давления на инструмент изучено в четырех направлениях: в продольном сечении в направлении движения инструмента и по высоте шва, в поперечном сечении перпендикулярно движению инструмента и по длине шва. Полученные результаты позволили установить механизм пористости в данных направлениях.
Недостаточное удельное давление на инструмент (180 МПа), обеспечивающее меньшую работу и количество тепла на единицу длины сварного шва, вызывает образование в его начальной области экстремально большого количества поверхностных макропор с размерами более 1 мм, уменьшающихся до одиночных мезопор и строчных микропор в направлении движения инструмента. Природа появления пор определена как газовая из-за малых степеней деформации металла в силу недостатка нагрузки и недостатка температуры в начале сварки и, как следствие, попадания воздуха в тело шва. Важным является исчезновение макропор и мезопор примерно на середине сварного шва (~20–25 мм от торца), что в свою очередь свидетельствует о достижении необходимой температуры металла за счет трения и реализации нормальных условий сварки, при которых воздух перестает участвовать в процессе сварки. Повышенная пористость в ЗТМВ, ЗТВ и в основном металле, находящемся под воздействием опорного бурта, вызвана выкрашиванием упрочняющей фазы вследствие градиента температур на границе ЗТВ – основной материал.
В верхней зоне поперечного сечения шва, полученного при недостаточном удельном давлении на инструмент, так же как и в продольном сечении, образуются макропоры с размерами 0,5–1,3 мм.
98
Наблюдаются макропоры преимущественно на границе ЗТВ – основной материал. С повышением удельного давления на инструмент степень перемешивания материала увеличивается, что способствует исключению образования макропор в начальной области сварного шва. Однако повышение удельного давления на инструмент не исключает образование микропор в данной области. В месте искривления сварного шва на его набегающей стороне установлены сквозные микропоры с кристаллической структурой на границе основной материал – ЗТВ, которые уменьшаются по длине. Пористость сварного шва вызвана уменьшением температуры и механического воздействия на инструмент, приводящим к неоднородному перемешиванию материала в процессе СТП и увеличению размера микропор в корне шва.
Установлено, что для уменьшения доли микропор верхнего продольного сечения с 2–15 до 0,7–2,3 % достаточно повышения удельного давления до 205 МПа, а для аналогичного понижения доли микропор в нижнем продольном сечении необходимо повышение удельного давления до 230 МПа [76].
99
4.ИССЛЕДОВАНИЕ СТРУКТУРЫ
ИСВОЙСТВ МАТЕРИАЛОВ И ПОКРЫТИЙ
4.1. Методика изготовления микрошлифов
Для нанесения вакуумных покрытий предъявляют повышенные требования к подготовке поверхности изделий перед осаждением. Это связано с тем, что формирование покрытий происходит на атомарном уровне и его структура и свойства в большей степени будут зависеть от состояния поверхности подложки. Присутствие на поверхности подложки макроскопических и микроскопических дефектов поверхности существенно повлияет на образовавшуюся структуру и свойства получаемого покрытия.
Вакуумные покрытия относятся к классу тонкопленочных покрытий (1–3 мкм) и не дают «нивелирующего» эффекта (снижение шероховатости поверхности), а полностью воспроизводят рельеф исходной поверхности подложки. Таким образом, поверхность изделий должна иметь тот класс чистоты поверхности, которую требуется иметь готовому изделию с покрытием.
К недопустимым дефектам исходной поверхности можно отнести трещины, сколы, заусенцы, продукты термической обработки, очаги коррозии, в связи с тем, что наличие приводит к ухудшению качества покрытия и нарушению адгезии (отслоению покрытий) [94].
Оборудование и материалы, используемые для изготовления микрошлифов:
–шлифовально-полировальный станок НЭРИС (рис. 44);
–наждачные шкурки (различной зернистости);
–алмазная паста, с различным содержанием алмазных порошков АСМ или АМ;
–ткань для полировки: фетр, бархат, тонкое сукно.
Этапы изготовления микрошлифов:
1. Шлифовка поверхности образца набором полировальных шкурок разной зернистости на шлифовально-полировальном станке наждачными шкурками.
100