
книги / Термическое, термомеханическое и механическое поведение алюминия и его сплавов при различных методах их обработки
..pdfобработке или катода при испарении/распылении (см. рис. 3, б). Данный процесс частично компенсируется повышением теплоемкости, уменьшающим скорость нагрева заготовки или катода. В точке фазового перехода Тпл = 933 К скачкообразно уменьшается плотность алюминия, значительно повышая его чувствительность к охлаждению. Алюминий в состоянии liquid обладает худшими теплофизическим и физико-механическими свойствами по сравнению с solid. Зависимость энтропии S0, плотности ρ и скорости испарения Vисп и теплопроводности λ, теплоемкости Cp0 и КТР алюминия от температуры [1, 7–9] приведена на рис. 4.
1.4.Прочность и жесткость алюминия
взависимости от его термического состояния
Легкость – выдающаяся и наиболее известная характеристика Al. Однако у технического Al низкие значения предела прочности при растяжении σв, предела текучести σт, предела ползучести σп, модуля Юнга E, модуля сдвига G и прочности на сдвиг. В то же время у алюминия высокие значения коэффициента испарения (Kи) и скорости испарения (Vи).
Алюминий и его сплавы обычно демонстрируют плавный переход от упругой деформации к пластической (обозначается σ0,2). Исключение составляют сплавы Al-Mg с содержанием более 2 % Mg, проявляющиеэффектЛюдеравотожженномсостоянии.
Начало пластической деформации обычно не сильно зависит от скорости деформации в отличие, например, от стали. Однако при очень высоких скоростях нагружения наблюдается небольшое увеличение σт.
Алюминий и все его сплавы деформируются во всем температурном режиме (в том числе при циклическом деформировании), т.е. имеют стабильную характеристику потока. Скорость деформационного упрочнения существенно не зависит от скорости деформации до достижения температур выше ~ 373 К [10].
В испытательной машине алюминиевый сплав будет показывать явно более высокую прочность на сжатие, чем на растяжение,
21
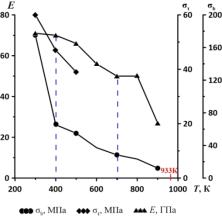
но это частично может быть связано с изменением площади поперечного сечения образцов, увеличивающейся в одном случае и уменьшающейся в другом, в то время как напряжение основано на исходной области. Цилиндрические образцы из более мягких алюминиевых сплавов можно сжать до толстых дисков до образования трещин, и даже в этом случае они могут выдерживать нагрузку. Типичные значения твердости по Бринеллю находятся в диапазоне от 20 для отожженного технически чистого металла до 175 для самого прочного сплава. Показания твердости никогда не следует рассматривать как количественный показатель прочности на разрыв, как это часто делается со сталями, поскольку в алюминии соотношение междуэтимидвумясвойствамидалеконепостоянное[4].
Для алюминия модуль упругости (модуль Юнга) чаще всего имеет округленное значение E = 70 МПа. При кручении модуль сдвига, или модуль жесткости, G = 26 МПа для алюминия, а для стали 83 МПа.
Рис. 5. Зависимость модуля упругости, предела прочности при растяжении и предела текучести технически чистого алюминия от температуры
Предел прочности на растяжение σв и предел текучести σт резко уменьшаются с 200 до 400 К при практически постоянном моду-
22
ле упругости, т.е. минимальном изменении жесткости алюминия (рис. 5). В интервале температур 400–700 К скорость снижения σв и σт значительно меньше. Выше 700 К и до Тпл = 933 К прочность и жесткость алюминия минимальны, т.е. критической температурой техническичистого алюминияявляется200 К(см. рис. 5).
Модуль упругости и жесткости лишь незначительно зависят от состава сплава и температуры. Изменения E и G от среднего значения 70 МПа и 26 ГПа для всех составов алюминиевых сплавов менее +/– 4 %. Текстура алюминия имеет отчетливое влияние на его свойства. Модуль упругости увеличивается за счет наклепа. Коэффициент Пуассона, т.е. поперечная деформация, деленная на продольную деформацию, составляет 0,33 [10].
Если напряжение достаточно велико или выдерживается достаточно долго, образец в конечном итоге выходит из строя в режиме, который имел бы место при постоянно увеличивающейся нагрузке. В этом отношении поведение Al аналогично поведению других металлов, и для обозначения этой формы отказа используется термин «разрыв при ползучести». Предел ползучести σп металлов снижается с повышением рабочей температуры, как и у других металлов. Отсюда следует, что σп не может быть выражен одним числом, а должен быть связан с рабочими температурами, временем и величиной деформации. На этих кривых деформация увеличивается в четыре этапа: во-первых, упруго, при нагружении (от O до A на верхней кривой); во-вторых, с уменьшающейся скоростью (от А до В); в-третьих, с почти постоянной скоростью, которая может быть пренебрежимо мала при низких напряжениях и температурах (от B до C); и наконец, с возрастающей скоростью (от C до D), что приводит к отказу (рис. 6). В этом примере только верхняя кривая вошла в финальную стадию [4].
На рис. 7 показана взаимосвязь между свойствами и характеристиками различных групп алюминиевых сплавов. Например, натуральный нелегированный Al серии 1ХХХ обладает пределом прочности на разрыв около 70 МПа, меньше в 10 раз (700 МПа), чем у некоторыхмоделейсерии7XXX [4].
23
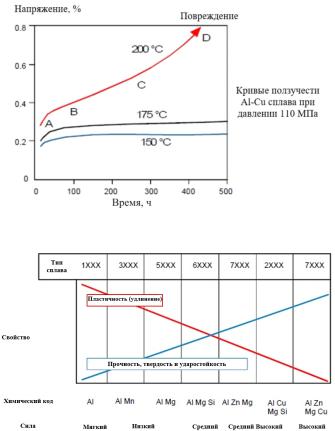
Рис. 6. Кривые ползучести Al-Cu сплава при давлении 110 МПа [4]
Рис. 7. Влияние легирующего элемента на прочность, твердость, ударостойкость и пластичность алюминия [4]
Прочность алюминиевых сплавов снижается с повышением температуры, исключая эффекты старения в узких диапазонах температур при различных периодах выдержки. Время выдержки важно в случае холоднодеформированных или термообработанных сплавов [4].
Для групп деформируемых сплавов приняты следующие обозначения [11]:
24
1XXX – нелегированный 99 % Al;
2ХХХ – медь: основной легирующий элемент; существенно увеличивает прочность, допускает дисперсионное твердение, пластичность и свариваемость снижает коррозионную стойкость; 3ХХХ – марганец: увеличивает прочность за счет упрочне-
ния твердого раствора и улучшает упрочнение; 4ХХХ – кремний: повышает прочность и пластичность, в со-
четании с магнием вызывает дисперсионное твердение; 5ХХХ – магний: увеличивает прочность за счет упрочнения
твердого раствора и улучшает упрочняющую способность; 6ХХХ – магний – кремний; 7ХХХ – цинк – магний: значительно увеличивает прочность,
дает возможность дисперсионного твердения, может вызвать коррозию под напряжением;
8ХХХ – другие элементы – например, Li, существенно увеличивает прочность и модуль Юнга, способствует выделению вторичных фаз, снижает плотность.
Обозначения основных термических состояний алюминиевых сплавов следующие:
F – состояние изготовления; О – отожженный;
Н – деформационная закалка (холодная обработка): всегда следует две или более цифр для обозначения объема холодной работы и вида термической обработки, которые были выполнены; W – термообработанный раствор: применяется к сплавам, которые затвердевают при комнатной температуре (естественное старение) после термообработки раствора. За обозначением следует время, указывающеенапродолжительностьестественного старения;
Т – термически состаренный:
T1 – охлажденный и выдержанный естественным путем; T2 – охлажденный, холодная обработка и естественная вы-
держка;
T3 – термообработанный раствор, холодная обработка и естественное старение;
25
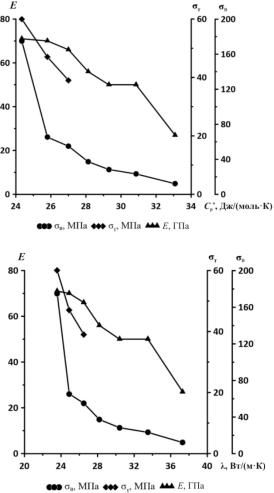
T4 – термообработанный раствор и естественное старение;
T5 – охлажденный и искусственно состаренный;
T6 – раствортермообработанныйиискусственносостаренный;
а
б
Рис. 8. Зависимость физико-механических свойств алюминия от теплоемкости (а) и теплопроводности (б) [1, 4]
26
T7 – раствор термообработанный и усредненный или стабилизированный;
T8 – термообработанный раствор, холодная обработка и искусственносостаренный;
T9 – термообработанный раствор, искусственное старение и холодная обработка.
Теплофизические и физико-механические свойства алюминия взаимосвязаны. На рис. 8 показана зависимость физикомеханических свойств алюминия от теплоемкости (рис. 8, а) и теплопроводности (рис. 8, б). Несмотря на увеличение поглощения определенного количества тепла алюминием при нагревании, теплоемкость алюминия повышается с 26 до 31 Дж/(моль·К). Зависимость σв, σт и Е от теплоемкости и теплопроводности незначительно отличается (см. рис. 8, б).
Таким образом, можно сделать вывод, изменение теплофизических свойств незначительно влияет на прочность и жесткость технического алюминия.
1.5. Электродуговое испарение алюминия для формирования тонкопленочных покрытий
Преимущество метода электродугового испарения (ЭДИ) связано с его уникальной способностью генерировать плазму высокой плотности, которая образуется при практически полной ионизации катодного материала в катодных пятнах (КП) вакуумной дуги [12]. Генерация плазмы и макрочастиц тесно связана с формированием взрывного кратера, характерного для катодных дуг. Температура и размер КП являются регуляторами, контролирующими условия испарения атомов и поддержания разряда. Максимальный уровень температуры в небольших КП достигается за более короткий промежуток времени, чем в больших пятнах. Процесс эмиссии трансформируется из автоэлектронного в термоавтоэлектронный по мере увеличения КП. Размер КП пропорционален плотности ионного тока и степени ионизации потока плазмы [13].
27
Непрерывное движение КП вдоль ограниченной рабочей поверхности катода приводит к средней равновесной температуре поверхности, определяемой условиями охлаждения, а также диаметром и длиной катода [14]. Интенсивное тепловое воздействие на поверхность катода вызывает сложные физико-химические процессы, которые приводят к структурным и фазовым превращениям в поверхностном слое катода [15, 16]. Из-за высокой плотности энергии в области КП во время процессов взрыва образуются как однофазные системы: твердое тело, жидкость, газ (пар) и плазма, так и двухфазные системы: твердое тело – жидкость, жидкость – газ и твердое вещество – газ (в случае металлического катода). Преобразование материала катода из твердого состояния в плазму путем фазовых превращений поддерживает работу дугового разряда и делает плазму катодной дуги и нанесенные покрытия такими особенными [17]. Перераспределение фазовой концентрации по поверхности катода и градиент состава образующихся покрытий по толщине является следствием локального плавления зоны эрозии при нарушении теплоотвода от некоторых КП и деформации катода при длительном сроке его эксплуатации [17, 18].
Макрочастицы, образующиеся в КП вместе с плазмой, могут находиться в жидком или твердом состоянии [15, 19]. Эмиссия макрочастиц, выбрасываемых из КП в процессе осаждения покрытия, приводит к снижению ее качества. Количество микрокапель на фиксированной площади покрытия изменяется из-за толщины катода, тока дуги, времени осаждения покрытия и обратно пропорционально расстоянию между катодом и подложкой, напряжению смещения на подложке и давлению азота [20]. Катодное азотирование (отравление) [15] и фильтрация макрочастиц являются наиболее оптимальными способами подавления образования крупных макрочастиц в плазме [21]. Катодное охлаждение также является эффективным методом уменьшения количества макрочастиц в покрытии. Система принудительного охлаждения обеспечивает такой режим работы катода, при котором его средней температуры поверхности недостаточно для протекания тока
28
термоэлектронной эмиссии [13, 21]. Поддержание температуры катода на заданном уровне может быть достигнуто путем уменьшения тока дуги и ускорения движения КП [7, 21]; поддержания или контроля тока дуги во времени [22].
В нескольких научных работах обсуждается связь динамики изменения КП с шероховатостью поверхности покрытия [15, 23], загрязнением поверхности [24, 25], ее температурой [26] и включениями [16], управлением магнитным полем [18], свойствами материала, такими как рабочая функция [27] и когезионной энергией [7, 21, 27]. В статье [28] установлено влияние структурных и фазовых превращений в зоне эрозии катодов и/или мишеней из тугоплавких металлов Ti и Zr на процесс структурообразования покрытия TixZr1-xN при ЭДИ, магнетронном распылении на постоянном токе или их комбинировании. Несмотря на многолетний опыт оптимизации и использования ЭДИ, снижение нестабильности свойств покрытий остается актуальной проблемой, в частности, в понимании общих закономерностей формирования реальной структуры покрытия [27, 29].
Структурная стабильность и стойкость в окислительных средах при температурах до 1273 К являются обязательными защитными требованиями к покрытиям. В связи с экономическими факторами и конкурентным давлением для ведущих компаний особенно интересным является дальнейшее увеличение применяемой термомеханической нагрузки с целью продления рабочих циклов режущих инструментов и деталей машин, используемых в автомобильной, авиационной и космической промышленности [30].
Уменьшение теплоотдачи в катод и снижение скорости нагрева катодного пятна при увеличении температуры до Tпл = 933 K происходит из-за уменьшения теплопроводности и температуропроводности Al, а также увеличения его теплоемкости. Равновесная температура конца термодинамического (фазового) перехода второго порядка твердое тело → жидкость соответствует Tпл = 933 К. Резкое уменьшение теплоемкости, теплопроводности и температуропроводности алюминия в данной точке характери-
29
зуется сильным экзотермическим эффектом, который приводит к резкому увеличению внутренней энергии, изменению симметрии во взаимном расположении частиц, росту объема катода до 6,60 %. Из-за дальнейшего повышения температуры Al его коэффициент теплового расширения увеличивается при снижении удельной прочности и удельной жесткости до 12 и 2 раз соответственно, изменяя поведение катода при испарении.
Теплоемкость и скорость нагрева катодного пятна в жидкой фазе стабилизируются при дальнейшем его нагреве до температуры испарения Al, равной 1423 К. Наблюдается небольшое увеличение теплопроводности и температуропроводности, а также ускорение отвода тепла в катод. Однако количество макрочастиц в жидкой фазе в плазме, на поверхности и в поперечном сечении покрытия увеличивается во много раз. Таким образом, при температуре катодного пятна T ≥ 933 K катод наиболее чувствителен
кскорости охлаждения.
1.6.Эволюция структуры и дефектность катодного пятна легкоплавкого алюминия при его электродуговом испарении
В качестве материала легкоплавкого катода использовали алюминий технической чистоты марки А85: Al 99,85 вес.%, Si 0,06 вес.%, Fe 0,08 вес.%, Cu 0,01 вес.%, Mn 0,02 вес.%, Mg 0,02 вес.%, Zn 0,02 вес.%, Ga 0,02 вес.%, Ti 0,008 вес.%, остальное 0,02 вес.% (ГОСТ 11069–2001).
Микроструктуру и дефекты зоны эрозии катодных пятен Ti и Al и покрытий Ti1-xAlxN изучали с помощью автоэмиссионного электронного микроскопа Ultra 55 в зависимости от способа охлаждения катодов и скорости нагрева подложки и покрытия. Микроструктуру покрытия Ti1-xAlxN исследовали на разных этапах его структурообразования. Для проведения локального рентгеноспектрального анализа использовали систему микроанализа EDX микроскопа Ultra 55. Количественный микрорентгеноспектральный
30