
книги / Машины для строительства, ремонта и содержания автомобильных дорог. Дорожные катки и одноковшовые погрузчики
.pdf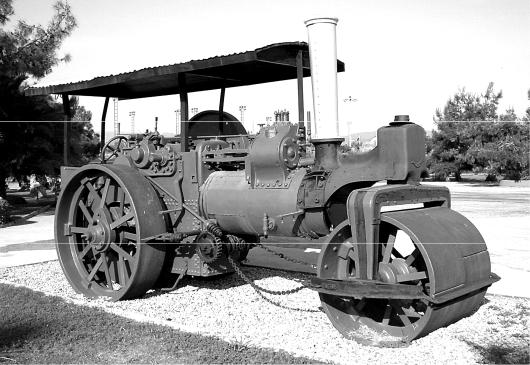
Рис. 1.3. Паровой каток Коломенского механического завода, 1902 г.
Дорожное машиностроение в России
В дореволюционной России объем дорожно-строительных работ был мал, кроме того, почти все работы выполнялись вручную. В 1913 г. парк оборудования для строительства дорог состоял всего из 332 ед., в числе которых было 146 поливочных бочек, 49 снегоочистителей, 88 катков, 14 копров для забивки свай и 2 камнедробилки.
Дороги с твердым покрытием находились преимущественно в западноевропейской части России. Их протяженность в 1913 г. составляла лишь 24 300 км.
Дорожное машиностроение начало развиваться только после 1920 г. В 1926 г. на Онежском заводе (Петрозаводск) было организовано производство первых советских дорожных машин: конных и тракторных утюгов, канавокопателей, конных и тракторных скреперов и других.
В 1930 г. дорожное машиностроение осуществлялось уже на четырех заводах, в том числе и на Рыбинском, который стал одним из ведущих заводов по производству дорожных катков в Советском Союзе. Был создан трест дорожного машиностроения, которому передали шесть заводов для организации на них производства дорожных машин: Онежский, Краснодарский, Рыбинский, Кременчугский, Николаевский и Одесский.
11
Однако количество дорожных машин, выпускаемых российскими заводами, далеко не удовлетворяло потребности в них, так как объемы строительства дорог и крупных промышленных объектов в годы индустриализации ежегодно существенно возрастали. В связи с этим в 1928–1930 гг. Советский Союз купил за границей (в США, Франции, Германии, Англии, Швеции, Дании) в большом количестве экскаваторы, моторные и паровые катки, бетоно- и асфальтосмесители, машины для приготовления черного щебня, автомобильные и прицепные гудронаторы и другие машины.
В те годы уплотнение асфальтобетонной смеси производилось с помощью моторных катков таких типов, как «Буффало», «Остин», «Кемпа», «Кельбле» и других. Например, четырехвалыдовые катки «Остин» массой 10 т и трехвальцовые «Буффало» имели специальные приспособления для безволновой укатки в виде дополнительного среднего барабана, причем распределение давления на вальцы можно было менять путем изменения положения среднего барабана. Первые проходы катки обычно делали с поднятыми средними барабанами, которые включались в окончательной стадии укатки при наличии неровностей покрытий.
Катки «Остин» и «Буффало» имели ряд преимуществ, из которых основными были:
–легкость управления катками при помощи гидросистемы;
–быстрота переключения скоростей и плавность хода;
–наличие дополнительного выравнивающего барабана для получения безволновой поверхности покрытий;
–наличие трех рабочих скоростей от 1,5–2 до 4 и 4,5 км/ч;
–ровная безволновая укатка.
Кроме катков «Остин» и «Буффало» довольно широко применялся и датский пятивальцовый каток «Рингстер». При карбюраторном двигателе каток имел массу 6 т, а при дизельном – 9 т.
Для увеличения массы все вальцы имели водяной резервуар. Передний направляющий валец был сдвоенный, а четыре задних одинакового диаметра – ведущие. При движении катка по неровной поверхности происходит перераспределение нагрузки на вальцы, что способствует получению более ровной поверхности. По желанию каток мог работать как трехвальцовый. Для этого имеются приспособления для поднятия либо средних, либо задних вальцов.
Параллельно с использованием импортного оборудования в нашей стране начали организовывать производство советских дорожных катков. Так, на Кременчугском заводе с 1930 г. был начат выпуск прицепных катков с гладкими металлическими вальцами, а в следующем году – на Рыбинском заводе моторных двухосных трехвальцовых катков.
12
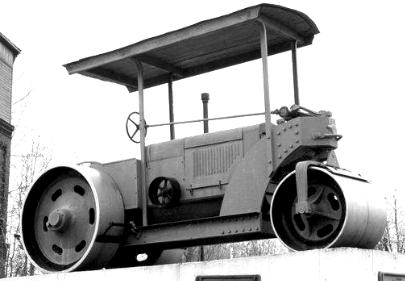
Первый советский моторный каток «Рыбинец» массой 10 т был выпущен 1 мая 1931 г. (рис. 1.4). Он не уступил по своим техническим и экономическим показателям лучшим образцам иностранных дорожных катков.
Рис. 1.4. Моторный каток «Рыбинец» массой 10 т
В1932 г. в Советском Союзе были изготовлены 71 самоходный (из них 2 паровых) и 320 прицепных дорожных катков с гладкими металлическими вальцами.
Заводы дорожных машин начали специализироваться уже на выпуске определенных типов катков: Кременчугский завод выпускал гладкие прицепные катки массой 3–5 т и кулачковые катки массой 4–7 т, а Рыбинский завод – три типа самоходных катков массой 2, 6 и 10–12 т.
В1940 г. производством строительных и дорожных машин занимались уже 25 машиностроительных заводов. Номенклатура дорожных машин к 1940 г. достигла 80 наименований.
Заводами Главстроймаша было изготовлено в 1939 г. 317 самоходных
и445 прицепных катков, а в 1940 г., по неполным данным, соответственно 273
и2574. Однако потребность в дорожных машинах, несмотря на высокие темпы роста их производства, далеко не удовлетворилась. Хотя даже Смоленский завод им. Калинина, кроме профильной техники, изготовлял прицепные катки, а Пушкинский ремонтный завод – моторные катки массой 5 т.
И все же большинство дорожных машин того времени, выпускаемых в основном по образцам зарубежных фирм, находились не на высоком техниче-
13
ском уровне по основным показателям – весу, мощности, производительности, расходу горючего, маневренности и т.д.
В1946 г. производство было налажено на 54 заводах, на которых было изготовлено 295 самоходных и 403 прицепных дорожных катка. Начиная с 1951 г. шло интенсивное освоение новых машин и наращивание объема их производства. В результате было изготовлено 12 504 дорожных катка. Вместо механического ручного управления поворотом началось применение гидравлического управления. В это время также были модернизированы системы управления,
вкоторых начали широко применять пневматику и гидравлику.
В1956–1960 гг. производители сделали еще один шаг вперед по конструированию новых машин, большинство из которых было создано уже советскими конструкторами и инженерами с учетом накопленного опыта. Было изготовлено 12 213 дорожных катков, среди которых созданы первые вибрационные самоходные, а также прицепные катки. На Рыбинском заводе в 1957 г. был изготовлен вибрационный каток Д-422, потом появились Д-484 и Д-317Б, а затем завод перешел к выпуску катка Д-613.
Уже в 1961–1965 гг. на серийное производство было поставлено 470 новых дорожно-строительных машин. Впервые был применен гидростатический при-
вод. С 1963 г. начался выпуску самоходного виброкатка Д-613 массой 4 т, а в 1966 г. – самоходного пневмоколесного катка Д-627 с гидростатической трансмиссией, гидравлическим управлением и двигателем мощностью 110 л.с. Тогда же начали серийно изготовлять полуприцепной каток массой 30 т к одноосному тягачу мощностью 240–300 л.с. и полуприцепной пневматический каток массой 45 т к одноосному тягачу мощностью 360 л.с.
Кроме самоходных и полуприцепных катков серийно изготовлялись прицепные пневмоколесные катки массой 12,5, 25 и 45 т и прицепные кулачковые катки массой 9, 18 и 29 т. Все эти катки были статического действия. Но выпускались и прицепные виброкатки массой 3, 6 и 12 т и самоходные виброкатки массой 1,5 и 4 т. Подавляющее большинство катков к этому времени уже имели гидравлическую систему управления поворотом.
Впериод с 1976 по 1980 г. в производство были введены новые катки
сгидромеханическим приводом ДУ-51 и ДУ-48Б, а также комбинированный каток ДУ-52 с гидростатическим приводом.
1.2. Методы уплотнения
Наиболее распространенными методами уплотнения материалов являются статическое уплотнение, вибрационное, ударный способ и комбинированное
(рис. 1.5).
14
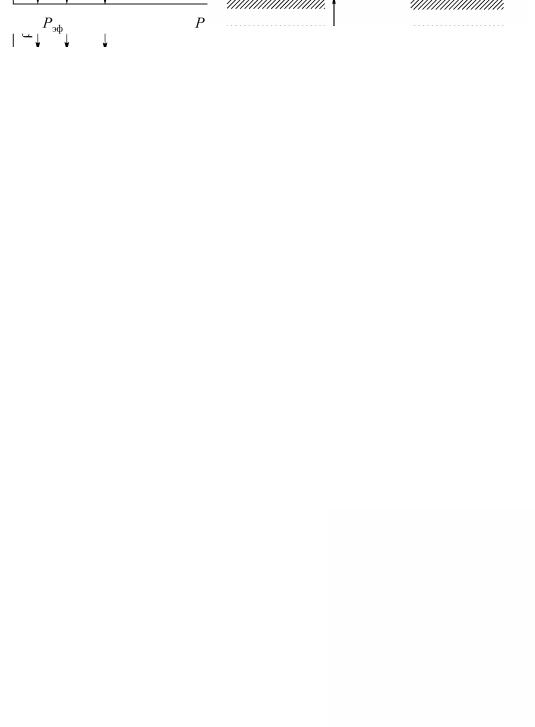
|
|
|
|
|
|
|
|
|
|
|
|
|
|
|
|
|
|
а |
б |
в |
Рис. 1.5. Способы уплотнения дорожно-строительных материалов: а – укатка; б – трамбование; в – виброуплотненне
Указанные методы уплотнения характерны тем, что рабочий орган перемещается по поверхности уплотняемого материала путем качения или скольжения. Наибольшим разнообразием отмечаются рабочие органы, перемещающиеся по поверхности материала способом качения.
Рабочие органы уплотняющих машин выполняются в виде плиты плоского или криволинейного профиля, в виде гладких, кулачковых, решетчатых, пластинчатых, ребристых вальцов и в виде пневматических колес. Уплотнение материала различными рабочими органами называют комбинированным методом уплотнения.
Сущность уплотнения заключается в увеличении количества связей в материале и упрочнении их. Это достигается повышением плотности материала. Под воздействием механической нагрузки частицы уплотняемого материала сближаются, что увеличивает прочность
ивязкость материала, уменьшает водопроницаемость. В результате уплотнения из рыхлой смеси формируется новый материал, свойства которого существенно отличаются от исходного.
Эффективность уплотнения зависит от величины уплотняющих нагрузок (рис. 1.6)
ивремени их действия. По мере увеличения нагрузки эффективность уплотнения уменьшается. При уплотняющей нагрузке, равной нулю, в материале действуют толь-
ко внутренние силы, которым соответствует начальное значение плотности ρнач.
15
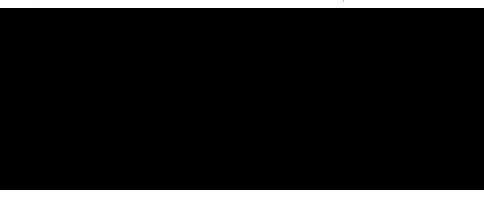
По мере увеличения уплотняющей нагрузки плотность материала приближается к своему предельному значению ρ.
Таким образом, может быть выделена нагрузка Рэф, при увеличении которой уплотнение становится малоэффективным, а соответствующая ей плотность ρопт – оптимальной для данных условий уплотнения.
Виды рабочих органов катков по ГОСТ 21994–82 показаны на рис. 1.7.
Рис. 1.7. Виды рабочих органов катков: 1 – гладкий палец; 2 – решетчатый валец; 3 – кулачковый валец; 4 – пластинчатый валец; 5 – ребристый валец;
6 – пневматические колеса
Выбор метода уплотнения материала определяется его структурой. Для каждой из структур может оказаться эффективным несколько методов уплотнения. В каждом случае выбор эффективного метода уплотнения производится экспериментальным путем. Все методы уплотнения обеспечиваются с помощью рабочих органов катков. Статическое уплотнение создается гладким вальцом или вальцом с другой формой рабочей поверхности при малой скорости машины. Вибрационное уплотнение обеспечивается благодаря установке вибровозбудителя, воздействующего на рабочий орган. Трамбующее действие при укатке создается на высокой скорости передвижения кулачкового вальца, а также падающими грузами.
Рабочие органы могут быть жесткие или эластичные. Вальцы являются же-
сткими рабочими |
органами, пневматические шины – |
эластичными. Шины |
в процессе укатки |
деформируются, что увеличивает |
поверхность контакта |
с материалом и более равномерно распределяет давление на этой поверхности. Вибрационное уплотнение материала наряду с виброкатками производят вибрационными плитами. Рабочий орган может колебаться как с отрывом, так и без отрыва от поверхности материала. Режим работы вибрационной машины с отрывом рабочего органа от поверхности материала называют вибротрам-
бованием.
16
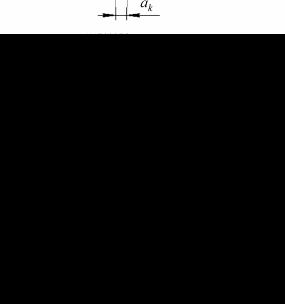
Ударный способ уплотнения отличается от вибрационного уплотнения низкой частотой вынуждающей силы рабочего органа. Этот способ заключается в ударном действии рабочего органа на материал при значительной высоте сбрасывания.
1.2. Статическое уплотнение
Статическое уплотнение обеспечивается укаткой. Уплотняющее действие катков зависит от максимальных контактных давлений, распределения давлений по площади контакта, размеров поверхности контакта, скорости укатки
ичисла проходов. Максимальные контактные давления оказывают основное влияние па прочность материала. Размеры пятна контакта определяют толщину уплотняемого слоя материала. Увеличение минимального размера пятна контакта приводит к увеличению толщины уплотняемого слоя.
Увеличение длины контакта рабочего органа с материалом и уменьшение скорости передвижения приводит к увеличению времени нагружения уплотняемого материала. Это положительно сказывается на качестве уплотнения материала с вязкими свойствами.
Схема взаимодействия вальца катка с материалом показана на рис. 1.8. В процессе качения вальца, на который действует вертикальная нагрузка G
итяговое усилие Т, контактные давления на материал возникают по дуге, середина которой смещена в сторону движения относительно линии действия силы G.
Рис. 1.8. Распределение давления под вальцом катка
17

Максимальное давление qmax также смещено в сторону движения на величину аk. Под действием сил, приложенных по поверхности контакта, работа материала в различных зонах выполняется по-разному. Выделяют три характерные зоны. В начальный момент соприкосновения одной из точек окружности вальца с поверхностью слоя материал частично перемещается в направлении движения. Для ведущего вальца эти перемещения относительно малы. Во второй зоне, т.е. зоне максимального давления, горизонтальное смещение материала незначительно, а вертикальная деформация включает необратимую hн и обратимую hо части. При выходе исходной точки поверхности вальца из соприкосновения с материалом полная деформация слоя уменьшается на величину обратимой части.
Максимальное контактное давление определяют по формуле
qmax = k q1E0 / Rв ,
где q1 – линейное давление, Н/м;
Е0 – модуль деформации грунта, Па; Rв – радиус вальца, м;
k – безразмерный коэффициент; для неподвижного вальца k = 0,5. Модуль деформации характеризует способность материала сопротивляться
внешней нагрузке. Для грунтов оптимальной влажности в начале уплотнения модуль Е0 = 1,0...10 МПа. В конце уплотнения для связных грунтов Е0 = 15...
20 МПа, для несвязных грунтов Е0 = 10...15 МПа.
Пневматические шины (в отличие от вальцов) под действием нагрузки деформируются, и зона действия максимального давления расширяется (рис. 1.9). С понижением давления воздуха в шинах при одной и той же нагрузке на колесо глубина активной зоны может как увеличиваться, так и уменьшаться. Уменьшение давления вызывает увеличение площади контакта, что увеличивает активную зону. Вместе с этим напряжение на поверхности снижается, и глубина зоны уменьшается. Результирующее действие давления воздуха в шинах зависит от формы беговой дорожки шин и ее конструктивного исполнения. Плотность грунта при снижении давления уменьшается.
Глубина активной зоны изменяется также при постоянном давлении воздуха в шипах по мере увеличения числа проходов катка. По мере увеличения числа проходов катка по одному месту площадь контакта с материалом уменьшается и давление увеличивается. На рыхлом и уплотненном материале площадь контакта может отличаться в 2,4–3,5 раза.
Такое автоматическое повышение давления недостаточно для качественного уплотнения материала. Постепенное повышение контактного давления от прохода к проходу путем изменения давления воздуха в шинах является
18
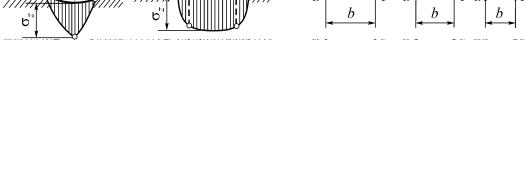
|
|
|
|
|
|
|
|
|
|
|
|
|
|
|
а |
б |
в |
Рис. 1.9. Схема распределения вертикальных напряжений в покрытии от массы катка: а – с гладкими вальцами; б – с пневмоколесами; в – площадка воздействия гладкого вальца на уплотняемое покрытие; 1–3 – проходы катка по одному следу; b – ширина площадки между точками а и с; φ – угол контакта; σZ – напряжение в грунте; стрелка А показывает направление движения катка
одним из основных правил при выполнении технологического цикла уплотнения.
Постепенное повышение давления к концу уплотнения позволяет избежать одностороннего смещения материала в поперечном направлении, создать относительно равномерную осадку во всех сечениях поперечного профиля дороги
иповысить качество уплотнения.
1.4.Вибрационное уплотнение
Под действием силы, приложенной к рабочему органу и имеющей переменное направление, последний совершает колебательные движения. Частицы и агрегаты материала под действием рабочего органа начинают вибрировать, от чего силы трения и сцепления между частицами и агрегатами уменьшаются, материал легко деформируется и приходит в более плотное состояние.
Частицы материала имеют различную массу; силы инерции, действующие на них, определяются этой массой и ускорениями при колебательном движении. В результате этого движения свойства материала изменяются, материал приобретает свойства жидкости. Физически связанная вода в грунте переходит
всвободное состояние. После прекращения вибрации вода вновь обволакивает частицы материала.
Наибольшие перемещения частиц относительно друг друга наблюдаются
внесвязных грунтах, в которых действуют только силы трения. В связных ма-
19
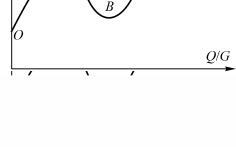
териалах к силам трения добавляются силы сцепления, которые не могут быть преодолены в значительной мере инерционными силами при вибрации, поэтому в связных материалах вибрация вызывает только упругие деформации.
Основными параметрами колебаний частиц являются: амплитуда, частота, скорость, ускорение.
Частицы материала имеют различные размеры и массу, что способствует возникновению различных инерционных сил н относительного перемещения зерен. Тяжелые зерна при относительно длительном времени вибрирования опускаются вниз, а легкие остаются наверху. Такое расслоение материала является недопустимым, так как снижает качество конструктивного слоя дорожной одежды или другого сооружения. Существует оптимальное время вибрирования – время, в течение которого смесь не расслаивается, а достигается ее наибольшая плотность. Для цементобетонной смеси это время составляет 30 с, для асфальтобетонной – около 60 с.
Амплитуда колебаний рабочего органа вибрационной машины и уплотняемого материала зависит от частоты вынуждающего воздействия. Подобно системам, обладающим упругими свойствами, в грунтах и других материалах возникают резонансные явления. При этом колеблются значительные объемы материала с большими амплитудами. Вместе с тем плотность существенно не повышается.
Увеличение вынуждающей силы ведет к увеличению амплитуды колебаний. В зависимости от отношения вынуждающей силы к весу рабочего органа один период его колебания на материале может соответствовать нескольким оборотам дебалансного вала вибровозбудителя. Периодическое изменение вынуждающей силы вызывает изменение деформации. Однако деформация отстает от соответствующего изменения напряжения. Данное обстоятельство вызывает отрыв рабочего органа от материала при определенных его свойствах даже в том случае, если вынуждающая сила меньше веса.
Рис. 1.10. Зависимость плотности грунта от отношения вынуждающей силы к весу рабочего органа
Зависимость плотности грунта от отношения вынуждающей силы Q к весу рабочего органа G показана на рис. 1.10. На участке ОA колебания рабочего органа являются гармоническими; амплитуда и инерционное воздействие на грунт увеличиваются по мере увеличения отношения Q/G. Вследствие этого плотность возрастает. На участке АВ амплитуда также продолжает увеличиваться, однако колебания становятся беспорядочными и эффективность уплотнителя падает.
20