
книги / Снижение экологической нагрузки при обращении со шлаками черной металлургии
..pdfнаряду с разработкой и промышленным освоением новых процессов необходимо добиться повышения эффективности использования имеющихся основных фондов.
В ближайшие годы эффективность производства черных металлов можно повысить за счет развития следующих направлений:
−снижение стоимости чугуна;
−замена доменного процесса жидкофазным бескоксовым восстановлением железа из дешевого рудного сырья;
−повышение эффективности кислородо-конвертного производства стали за счет использования синтетического чугуна;
−использование эффективных методов рафинирования металла;
−производство железа прямого восстановления.
Снижение стоимости чугуна. Ввиду того, что при тради-
ционной технологии основную долю (60–70 %) себестоимости стали составляет стоимость сырья и прежде всего чугуна, являющегося основным видом сырья, любое снижение стоимости его производства ведет к существенному снижению себестоимости стали. Для этого используются мероприятия (замена части кокса на дешевые виды каменных углей, вдуваемых в виде пыли и др.), ведущие к снижению стоимости чугуна. Однако при получении чугуна по традиционной технологии в доменных печах, для эффективной работы которых требуется только высококачественное железорудное сырье (окатыши, агломерат) и топливо (кокс), снижение себестоимости чугуна в будущем не представляется возможным.
Замена доменного процесса жидкофазным бескоксовым востановлением железа из дешевого рудного сырья. Этот технологический процесс кроме замены кокса и использования низкокачественного рудного сырья должен включать плавление лома в шахтной печи, отапливаемой технологическими газами процесса жидкофазного восстановления (вторичными энергоресурсами), и непрерывную разливку стали.
21
Указанная технологическая схема производства металла может обеспечить значительное снижение себестоимости стали благодаря замене дорогостоящих видов первичного сырья дешевыми: кокса – энергетическими углями, агломерата и окатышей – дешевой железной рудой (без обогащения или после неглубокого обогащения), а также в результате применения вторичных энергоресурсов для плавления лома.
Кроме того, плавление лома в шахтной печи позволяет упростить задачу выплавки высококачественной стали. В этом случае возможна организация выплавки стали двумя раздельными потоками:
−высококачественной стали – из первичного металла (чугуна), отличающегося высокой чистотой по содержанию примесей цветных металлов;
−стали обычного качества – из вторичного металла (лома), как правило, загрязненного примесями цветных металлов.
Однако процессы жидкофазного бескоксового восстановления железа и плавления лома в шахтной печи пока находятся на стадии внедрения и промышленного испытания. Поэтому
вближайшее время не следует ожидать перевода черной металлургии на новую производственно-технологическую схему.
Повышение эффективности кислородно-конвертерного производства стали за счет использования синтетического чугуна. Новым технологическим процессом, за счет промышленного освоения которого возможно повышение эффективности черной металлургии, является плавление лома в шахтной печи с получением синтетического чугуна, используемого в кислород- но-конвертерном производстве. В этом случае при получении синтетического чугуна может быть организовано удаление примесей цветных металлов, в частности меди. Это позволит решить проблему переработки лома, которая становится все острее, и обеспечить эффективную работу кислородно-конвертерных цехов, дающую повышение производительности при одновременном снижении себестоимости стали и улучшении ее качества.
22
Использование эффективных методов рафинирования металла. Методы рафинирования используются для повышения качества металла. Задача повышения качества стали должна решаться путем расширения применения различных видов ковшовой обработки металла. Из всех видов дополнительной обработки стали, применяемых в промышленности, относительно новым и дающим наибольший эффект повышения качества, является ее обработка материалами, содержащими щелочноземельные и редкоземельные металлы. В настоящее время наиболее доступным и эффективным способом обработки является обработка силикокальцием.
Эффект повышения качества стали, достигаемый при ее обработке кальцийсодержащими материалами, связан с тем, что кальций имеет очень высокое сродство к кислороду и сере и может обеспечивать снижение остаточного содержания этих вредных примесей в жидком металле до очень малых значений (менее 0,001–0,002 %). Кроме того, оксиды и сульфиды кальция, выделяющиеся при кристаллизации металла, образуют мелкодисперсные глобулярные и равномерно распределенные по объему неметаллические включения, которые оказывают минимальное отрицательное влияние на свойства стали. Такое выделение неметаллических включений принято называть их модифицированием.
В настоящее время обработка стали кальцием недостаточно распространена и сводится в основном к вдуванию порошка силикокальция в ковш. Поэтому важной задачей является расширение использования обработки стали кремнием, что обеспечит повышение качества металла в рамках существующего произ- водственно-технологического процесса.
Производство железа прямого восстановления. Приме-
нение технологий по производству железа прямого восстановления (или губчатого железа) в основном в виде металлизированных окатышей DRI (Direct Reduced Iron) и горячебрикетиро-
23
ванного железа НBI (Hot Briquetted Iron) по-прежнему, как и несколько десятилетий назад, считается одним из самых перспективных направлений для эффективного развития мировой металлургии.
Известно, что использование губчатого железа при выплавке стали (в основном в электродуговых печах) позволяет производить наиболее высококачественный, экономически выгодный (с относительно низкой энергоемкостью) и экологически чистый металл (по сравнению с доменным процессом), пригодный для удовлетворения самых высоких требований таких отраслейпотребителей, как машиностроение, авиа-, судостроение и т.д.
Однако, несмотря на непрерывную рекламу ряда сравнительно новых технологических процессов (Midrex, ITmk3), постоянный рост производства продукции прямого восстановления железа и увеличение инвестиций в его расширение по всему миру (в том числе и в России) идет сравнительно медленно. Темпы освоения данных технологий явно не успевают за потребностями металлургии. Промышленное производство железа непосредственно из руды, минуя доменный (с использованием кокса) процесс, появилось в 1970-х гг. Первые установки прямого восстановления железа были малопроизводительны, а конечный продукт имел сравнительно много примесей.
Широкое распространение этого процесса началось в 1980-х гг., когда в горно-металлургическом комплексе началось широкое применение природного газа, который идеально подошел для прямого восстановления железной руды. Кроме того, помимо природного газа в процессе прямого восстановления железа оказалось возможным использование продуктов газификации углей (в частности бурых), попутного газа нефтедобычи и другого топлива-восстановителя.
Технологические изменения, происшедшие в 1990-е гг., позволили значительно снизить капитало- и энергоемкость различных процессов прямого восстановления железа, в результате
24
чего произошел новый скачок в производстве продукции DRI, который продолжается до сих пор.
В типовом процессе восстановления железа основной компонент природного газа – метан – разлагают окислением в присутствии катализатора в специальных аппаратах – реформерах, получая смесь восстановительных газов – окиси углерода и водорода. Эта смесь поступает в высокотемпературный реактор,
в который подается |
также обрабатываемая |
железная руда. |
Есть технологии DRI, |
использующие метан |
непосредственно |
в реакторе, а также восстановительные пылеугольные смеси. Все эффективные методы прямого восстановления качест-
венного железа фактически используют единственный процесс: богатое железорудное сырье (руда или окатыши с содержанием железа не менее 70 %) восстанавливается при высоких температурах до содержания железа 85–90 % и более специальной газовой смесью. Именно поэтому основное производство железа прямого восстановления главным образом сосредоточено в странах, обладающих большими запасами нефти (т.е. попутного газа), природного газа и железной руды, а также ограниченных в ресурсах альтернативного металлолома (т.е. в странах Латинской Америки, Ближнего и Среднего Востока).
На сегодня в мире наиболее широко распространены технологии прямого восстановления железа компании Midrex (США), установки которой работают во многих странах с 1971 г. Лидирующие позиции в DRI эта компания удерживает последние 29 лет подряд. В 2007 г. по технологиям Midrex произведено около 40 млн т DRI, или 60 % от общего мирового производства по данной технологии.
В табл. 1.3 представлены технико-экономические показатели черной металлургии России и некоторых стран мира.
25
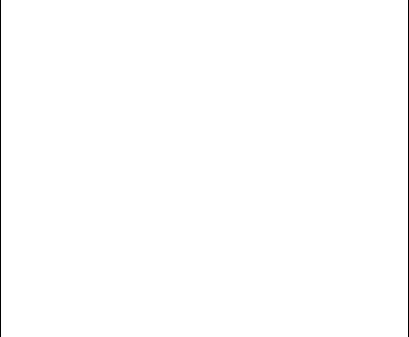
Таблица 1 . 3
Технико-экономические показатели черной металлургии на 2007 г.
Показатели |
Россия |
США |
Япония |
Украина |
|
|
|
|
|
|
|
Структура |
сталеплавильного производства, % |
|
|||
Кислородно-конвертерный |
61,9 |
51,1 |
73,6 |
48,9 |
|
способ |
|||||
|
|
|
|
||
Электросталь |
15,9 |
48,9 |
26,4 |
4,2 |
|
Мартеновский способ |
22,2 |
– |
– |
46,9 |
|
Доля непрерывного литья |
57,7 |
97,0 |
97,7 |
23,1 |
Усредненный сквозной коэффициент на производство 1 т проката, кг/т
Железорудные материалы |
1480 |
1010 |
1070 |
1640 |
|
Кокс |
425 |
267 |
293 |
519 |
|
Чугун |
865 |
642 |
726 |
866 |
|
Лом |
446 |
677 |
488 |
490 |
|
|
Другие параметры |
|
|
||
Средний расходный коэф- |
|
|
|
|
|
фициент стали на 1 т про- |
1200 |
1150 |
1095 |
1250 |
|
ката, кг/т |
|
|
|
|
|
Усредненный показатель |
|
|
|
|
|
выплавки стали на 1 рабо- |
150 |
400 |
630 |
100 |
|
тающего, т/чел. |
|
|
|
|
|
Средняя оплата труда, |
3,8 |
32 |
34 |
0,8 |
|
долл/чел.-ч |
|||||
|
|
|
|
Металлургия использует 25 % от всей потребляемой российской промышленностью воды. При этом в большинстве случаев после промышленного использования эта вода не обрабатывается должным образом и, загрязненная, попадает в поверхностные и грунтовые воды. Тяжелые металлы, нефтеотходы, фенолы и ряд других элементов, присутствующих в сбрасываемой воде, делают ее непригодной для дальнейшего использования, а порой становятся причиной массовой гибели биоресурсов в близлежащих водоемах. Установлено, что предприятия черной металлургии выбрасывают в атмосферу до 25 % металлосодержащей пыли и окиси углерода от общего количества этих веществ, попадающих в атмосферу в результате промышленных
26
процессов. На металлургию приходится распространение в атмосфере почти 50 % неутилизируемых промышленностью окислов серы (только предприятиями Заполярного филиала «Норильского никеля» выбрасывается в атмосферу 979 тыс. т серы в год) [1]; кроме того, технологический цикл подразумевает выбросы в атмосферу целого спектра токсичных для человеческого организма веществ, включая бензопирен, фториды, соединения марганца, ванадия и хрома. Однако эта цифра составляет около 10 % от общего объема сброса. Металлургической компании «Северсталь» удалось на 98,2 % замкнуть водооборотный цикл и закрыть 5 стоков в естественные водоемы. В настоящее время вопросы экологии находятся в центре внимания руководства и общественных организаций металлургического комплекса, но на устранение проблем, копившихся десятилетиями, потребуется определенный период времени. Так, даже действующие нормативные документы нуждаются в уточнении, поскольку металлургам довольно часто приходится сталкиваться с комплексом нерешенных юридических вопросов.
* * *
Таким образом, в технологии производства стали еще долгое время будет сохраняться использование чугуна, полученного из рудного сырья. Существующий технологический процесс необходимо переводить на схему, предусматривающую переработку железорудного сырья в агрегатах бескоксового жидкофазного восстановления, плавления лома в шахтных печах с получением синтетического чугуна и выплавку стали в агрегатах непрерывного действия. Интенсификация производства стали и уменьшение образования отходов возможны лишь при коренной перестройке технологии получения металла.
Одной из нерешенных проблем металлургии остается проблема утилизации шлаков. Ранее данный вопрос не находил должного внимания, вследствие того что экологическая нагрузка предприятий на окружающую среду не являлась лимити-
27
рующим показателем. Образующиеся после выплавки металла шлаки накапливались в отвалах и шламохранилищах, отнимая городские и сельскохозяйственные земли (так, только на территории металлургических предприятий Уральского региона скопилось свыше 6 млрд т подобных отходов). Использование шлака в строительстве из-за низкой цены природных материалов было нерентабельным. В настоящее время происходит удорожание природных материалов, идущих на получение строительных компонентов. Ужесточение экологических норм и законодательства, увеличение платежей за размещение отходов позволяют рассматривать шлаки как сырье для получения строительных материалов.
Из-за внедрения новых технических решений получения чугуна и стали, расширения сортамента металла меняется состав шлаков. Образующиеся шлаки обладают физико-химическими свойствами, отличными от получавшихся ранее. Они требуют дополнительного исследования.
Вследствие того что технология получения металла не будет изменена коренным образом еще долгое время, образование шлаков останется крупнотоннажным, и тема исследований в данном направлении будет актуальной и на современном этапе.
Список литературы
1. Казармщиков И.Т. Производство металлических конструкционных материалов: учеб. пособие. – Оренбург: Изд-во Оренб. гос. ун-та, 2004. – С. 5–9, 76–81.
3. Экономическая география и региональная экономика / сост. К.А. Гуляева. – Н. Новгород: Изд-во Нижегор. гос. ун-та, 1996.
28

2. ОСНОВНЫЕ ТЕХНОЛОГИЧЕСКИЕ СХЕМЫ
ОБРАЗОВАНИЯ ШЛАКОВ ЧЕРНОЙ МЕТАЛЛУРГИИ
Роль шлаков в процессе производства стали исключительно велика. Шлаковый режим, определяемый количеством и составами шлака, оказывает большое влияние на качество готовой стали, стойкость футеровки и производительность сталеплавильного агрегата. Шлак образуется в результате окисления составляющих части шихты из оксидов футеровки печи, флюсов и руды. По свойствам шлакообразующие компоненты можно разделить на кислотные (SiO2; P2O5; TiO2; и др.), основ-
ные (CaO; MgO; FeO; MnO и др.) и амфотерные (Al2O3; Fe2O3; Cr2O3; и др.) оксиды. Важнейшими компонентами шлака, оказывающими основное влияние на его свойства, являются окси-
ды SiO2 и CaO [1].
Шлак выполняет несколько важных функций в процессе выплавки стали:
1) связывает все оксиды (кроме СО), образующиеся в процессе окисления примесей чугуна. Удаление таких примесей, как кремний, фосфор и сера, происходит только после их окисления и обязательного перехода в виде оксидов из металла
вшлак. В связи с этим шлак должен быть надлежащим образом подготовлен для усвоения и удержания оксидов примесей;
2)во многих сталеплавильных процессах служит передатчиком кислорода из печной атмосферы к жидкому металлу;
3)в мартеновских и дуговых сталеплавильных печах через шлак происходит передача тепла металлу;
4)защищает металл от насыщения газами, содержащимися
ватмосфере печи.
29
Изменяя состав шлака, можно отчищать металл от таких вредных примесей, как фосфор и сера, а также регулировать по ходу плавки содержание в металле марганца, хрома и некоторых других элементов.
Для того чтобы шлак мог успешно выполнять свои функции, он должен в различные периоды сталеплавильного процесса иметь определенный химический состав и необходимую текучесть. Эти условия достигаются использованием в качестве шихтовых материалов плавки расчетных количеств шлакообразующих – известняка, извести, плавикового шпата, боксита и др.
Свойства и химический состав шлака зависят от видов производства, которые необходимо рассмотреть как основу для определения величины влияния шлака на окружающую среду.
2.1. Доменные шлаки
2.1.1.Подготовка к выплавке чугуна
Для выплавки чугуна в доменных печах используют железные руды, топливо, флюсы в виде специально подготовленной смеси (шихты). При доменной плавке могут использоваться также отходы производства, содержащие Fe, Mn, CaO, MgO. К ним относят колошниковую пыль, окалину, сварочный и мартеновский шлаки.
Современное доменное производство предъявляет к железорудным материалам очень высокие требования. Эти материалы должны иметь:
−высокое содержание железа;
−низкую концентрацию вредных примесей;
−оптимальный размер кусков (20–40 мм);
−высокую прочность, чтобы при транспортировке и в ходе плавки куски не разрушались с образованием мелких фракций;
30