
книги / Специальные плазменные технологии
..pdfВид нагрева |
Эффективный КПД, % |
|
Нагрев газа в плазмотроне: |
|
|
аргона............................................................................. |
|
10–70 |
водорода........................................................................ |
|
30–80 |
Нагрев массивного тела: |
|
|
плазменной струей........................................................ |
|
10–50 |
плазменной дугой......................................................... |
|
30–75 |
Нагрев проволоки при распылении: |
|
|
плазменной струей........................................................ |
|
2–5 |
плазменной дугой......................................................... |
|
10 |
Нагрев порошка: |
|
|
при подаче на срез сопла.............................................. |
|
2–4 |
в столбе дуги и струе.................................................... |
|
20 |
Нагрев проволоки в электродуговом металлизаторе...... |
40–90 |
Наиболее экономно используется энергия в процессе электродуговой металлизации, у которой эффективный КПД нагрева распыляемого металла может достигать 90 % мощности дуги.
3.3. ТЕПЛОВЫЕ ПРОЦЕССЫ НА ПОВЕРХНОСТИ ИЗДЕЛИЯ
Движущей силой образования покрытия является тепловая
икинетическая энергия напыляемых частиц. На процесс образования покрытия влияет также плазма, подогревающая, а иногда
иочищающая поверхность изделия, на которую наносят покрытие. Благодаря химической активности плазма может взаимодействовать с напыляемыми частицами, образуя покрытие из нового материала, синтезированного в процессе напыления.
Тепловая мощность двухфазной струи q при плазменном напылении – это количество теплоты, введенное в единицу времени в изделие плазмой и частицами. Отношение тепловой мощности струи к тепловому эквиваленту электрической мощ-
91
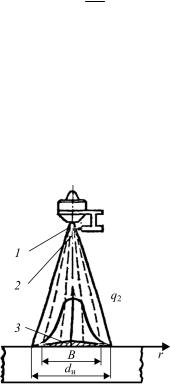
ности дуги будет характеризовать КПД процесса нагрева изделия дугой при плазменном нанесении покрытий:
η= q ,
IU
где I и U – сила тока и напряжение дуги.
Площадь поверхности изделия, через которую теплота двухфазной струи вводится в изделие, называют пятном нагрева (рис. 31). В общем случае диаметр dн пятна нагрева не равен диаметру пятна напыления, который численно равен ширине слоя покрытия В, нанесенного за один проход. Соотношение между этими величинами может меняться в зависимости от фокусировки потока частици сосредоточенностиплазменной струи.
Рис. 31. Схема ввода теплоты напыляемыми частицами и плазменной струей в изделие и распределения удельного теплового потока q2 по пятну нагрева диаметром dн: 1 – плазменная струя; 2 – поток частиц покрытия; 3 – покрытие; r – радиальное расстояние от оси струи
Количество теплоты, вводимой через элементарные площадки поверхности пятна нагрева в единицу времени, называют
92

удельным тепловым потоком q2 двухфазной струи. Удельный тепловой поток распределен по пятну нагрева неравномерно. Наибольшую величину он имеет в центре пятна, где количество частиц покрытия больше, а тепловой поток плазменной струи интенсивнее.
Когда ось струи перпендикулярна напыляемой поверхности, удельный тепловой поток q2(r) расположен симметрично относительно оси струи. В этом случае обычно распределение удельного теплового потока двухфазной струи по площади пятна нагрева dh при распылении может быть описано законом нормального распределения (кривой вероятности Гаусса):
q2 = q2m exp(−kr2 ),
где q2m – наибольший удельный тепловой поток на оси струи;
r – радиальное расстояние рассматриваемой точки от оси струи; k – коэффициент сосредоточенности удельного теплового потока струи, характеризующий форму кривой нормального распределения.
Источник с таким распределением теплового потока называют нормально-круговым. Чем выше коэффициент сосредоточенности k, тем быстрее убывает удельный тепловой поток в пятне нагревасудалениемот центраитем меньшесам диаметрпятна.
Если условно принять за радиус пятна нагрева rн расстояние от центра, на котором удельный тепловой поток q2(rн) равен 0,05 от наибольшего удельного теплового потока q2m в центре пятна, то отсюда можно находить условный диаметр пятна нагрева, который обратно пропорционален корню квадратному из коэффициента сосредоточенности k:
dн = 2 3,0 = 3,46 . |
|
k |
k − |
Предполагая, что частица порошка сферическая и температура ее поверхности мгновенно достигает температуры плав-
93
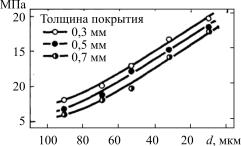
ления, можно определить наибольший размер частиц, при котором происходит полное ее расплавление. Если допустить, что в плазменной струе, температура которой значительно превышает температуру плавления порошка, частицы порошка находятся в течение 0,1 мс, то каждая частица оплавляется на глубину 90 % ее радиуса, т.е. почти до ее середины. Это означает, что порошок расплавляется почти полностью. В связи с этим возникает вопрос о размере частиц d*max порошка, при котором он почти полностью расплавляется. Этот размер частиц зависит от теплофизических характеристик порошка, включая теплопроводность, теплоемкость и плотность напыляемого материала. Чем больше значение dmax, тем лучше протекает процесс напыления порошком. Для плазменного напыления обычно применяют порошок с размером частиц 74–44 мкм. При использовании порошка с меньшим размером частиц практически все частицы в процессе напыления полностью расплавляются.
Напыление материала с использованием более мелкой фракции порошка обеспечивает получение плотного, более качественного покрытия. Уменьшение фракции порошкового напыляемого материала сопровождается повышением прочности сцепления покрытия с подложкой (рис. 32).
Рис. 32. Влияние размера частиц d порошка напыляемого материала на прочность сцепления покрытия с подложкой
94

3.4. ФОРМИРОВАНИЕ ПОКРЫТИЯ ПРИ ПЛАЗМЕННОМ НАПЫЛЕНИИ
При любом способе напыления поверхность основного материала располагают обычно на расстоянии не менее 100 мм от среза сопла горелки. Покрытие образуется из отдельных расплавленных или близких к этому состоянию частиц, которые с высокой скоростью соударяются и наслаиваются на поверхность основы. На рис. 33 показана схема образования покрытия при напылении. При движении к основному металлу в высокотемпературной газовой среде поверхность частиц покрывается оксидной пленкой.
Рис. 33. Схема образования покрытия при напылении: 1 – оксидная пленка; 2 – частицы расплавленного напыляемого материала; 3 – частица при столкновении с поверхностью; 4 – участок механического сцепления; 5 – участок локального сплавления; 6 – не полностью расплавленная частица; 7 – пора; 8 – поверхность основного материала; 9 – основной материал
95
При столкновении с поверхностью основного материала или поверхностью ранее образовавшегося покрытия частицы расплющиваются, образуя тонкий слой, механически сцепленный с поверхностью основного материала или покрытия. При напылении металла скорость охлаждения частиц составляет 106–108 °С/с, а при напылении керамики – 104–106 °С/с, поэтому кристаллизация жидких частиц завершается в течение ничтожно малого промежутка времени.
Прилипание частиц осуществляется посредством их механического сцепления с макровыступами подложки и через места разрушения оксида подложки. В местах разрушения оксидных пленок происходит сплавление металлических частиц с подложкой при высокой прочности сцепления.
В процессе налипания частиц друг на друга наряду с расплавленными попадаются и не полностью расплавленные частицы. Кроме того, внутри покрытия возникают заполненные газом зазоры и пустоты, количество которых определяет пористость покрытия.
При плазменном напылении на воздухе происходит инжекция окружающего воздуха в струю, транспортирующую материал к изделию. Таким образом, движение расплавленных частиц сопровождается взаимодействием их поверхности с кислородом и азотом окружающего воздуха. При плазменном напылении, когда в качестве рабочего газа используют азот, напыляемые частицы могут взаимодействовать с азотом, и продукты их взаимодействия будут входить в состав покрытий.
Большое содержание оксидов обнаруживают в медных покрытиях, напыленных плазменным способом. При плазменном напылении вольфрама на основу из графита могут образоваться как оксиды (WO3, W4О, WO2), так и его нитриды (W2N, W3N2, WN,W2N2 и WN2).
При напылении цинком оксиды не оказывают заметного отрицательного влияния на качество покрытия, но при напылении алюминием интенсивное образование оксидов при по-
96
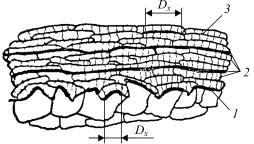
следующей термообработке может препятствовать диффузии алюминия в основу изделия, и алитирование произойдет на недостаточную глубину. При нанесении алюминиевых покрытий увеличение расстояния между горелкой и основным материалом приводит к значительному повышению содержания оксидов в покрытии.
При плазменном напылении сплавами на основе никеля с использованием в качестве рабочего газа аргона состав напыляемого материала практически не изменяется.
3.5. СТРОЕНИЕ ПОРОШКОВОГО ПОКРЫТИЯ
Покрытие – это слоистый материал, состоящий из сильно деформированных частиц, соединенных между собой по контактным поверхностям сварными участками диаметром Dx и площадью
Fx = (πDx2 ) / 4 (рис. 34).
Рис. 34. Схема структуры покрытия: 1 – граница между покрытием и основой; 2 – границы между слоями;
3– граница (контактная поверхность) между частицами
вслое; Dx – диаметр сварного участка; Fx – площадь сварного участка
Сварные участки не заполняют всю площадь контактной поверхности между частицами, поэтому прочность и плотность
97
напыленных покрытий ниже прочности и плотности материала покрытия в компактном состоянии. Прочность самих сварных участков зависит от количества очагов схватывания, образующихся на площади Fx в период удара, деформации и затвердевания частицы, и определяется развитием химического взаимодействия материалов в контакте.
В покрытии можно выделить структурные элементы, которые отражают процессы его формирования и разделяются границами раздела с определенными свойствами. Граница раздела между покрытием и основой 1 определяет прочность сцепления между ними. Свойства самого покрытия обусловливаются прочностью сцепления частиц в нем 3 (см. рис. 34). Граница раздела между слоями (межслойная граница) 2, полученная за один проход распылителя, возникает из-за различной длительности выдержки между нанесением частиц в слое и между слоями. За период выдержки межслойного нанесения поверхность ранее нанесенного слоя покрытия загрязняется, окисляется, и контактные процессы между ней и напыляемыми частицами затрудняются, что иявляется причинойвозникновения границы.
Структура слоя, сформированного за один проход, неоднородна и определяется различными размерами, температурой и скоростью частиц, находящихся в периферийной и центральной зоне двухфазного потока. Кроме того, наблюдается экранирующее действие периферийных частиц по отношению к частицам центральной зоны потока. Толщина слоя в различных покрытиях колеблется в очень широких пределах в зависимости от назначения покрытия, технологии его нанесения, материалов, входящих в состав покрытия, и т. п. Наиболее часто встречаются покрытия с толщиной слоя от 10 до 100 мкм.
Условия образования границ между слоями и между частицами определяются длительностью пребывания в атмосфере. В зависимости от размеров и конфигурации напыляемого изделия, траектории перемещения распылителя «пауза» между моментами наложения слоев может достигать секунд и десятков
98
секунд. Это время на несколько порядков больше времени паузы между взаимодействием частиц в слое, нанесенном за один проход. В период между напылением слоев на поверхности покрытия происходит адсорбция газов, окисление и отложение пылевидных фракций распыляемого материала и его оксидов. Образование покрытия последовательной укладкой множества деформирующихся частиц неизбежно приводит к появлению микропустот, в первую очередь на стыках частиц. Взаимодействие с атмосферой, адсорбция газов и оседание пылевидных фракций ухудшает свойства межслойных границ.
Структура и свойства покрытия зависят от гранулометрического состава напыляемого порошка. С уменьшением размера частиц порошка улучшается заполнение покрытия – плотность его увеличивается, объем микропустот уменьшается, строение покрытия становится более однородным. Однако слишком мелкие порошки непригодны для плазменного напыления.
Большие затруднения возникают при попытках транспортировки и ввода в распылитель частиц размером 10 мкм и менее. Такие порошки не могут быть заранее подготовлены и выровнены по размеру частиц обычными методами подготовки порошков, поскольку они не рассеиваются на ситах. Мелкие порошки слипаются из-за влажности и проявления сил молекулярного сцепления и образуют конгломераты из нескольких частиц при подаче их потоком транспортирующего газа. Будучи введены в плазму, мелкие частицы могут в ней полностью испариться. Мелкие порошки в плотной окружающей атмосфере быстро теряют скорость, отклоняются от заданной траектории и не достигают напыляемой поверхности. Обычно для напыления рекомендуются порошки с размером частиц 40–70 мкм. Сцепление между частицами в покрытии, а также сцепление между основой и покрытием возникают в результате действия ряда сил: сил механического зацепления, слабых невалентных сил взаимодействия (типа сил Ван-дер-Ваальса), химических сил связи. Силы двух первых типов отличаются нестабильностью, обычно имеют
99
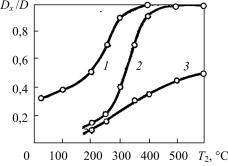
низкий уровень, и поэтому их не следует принимать в расчет при создании покрытия. Хотя при напылении на материалы с сильно развитой поверхностью (пористые керамика и графит) прочность механического сцепления покрытий с подложкой может достигать 10–15 МПа.
Следствием химического взаимодействия является приваривание частиц, которое приводит к образованию очагов схватывания в контакте. Чем больше очагов схватывания, тем выше прочность сцепления частиц. Приваривание частицы наступает только при подогреве основы до определенной температуры, которую обозначают Т2 и называют температурой химического взаимодействия. При температуре подложки ниже Т2 частицы легко отделяются от основы, поскольку химическое взаимодействие не получает необходимого развития. Температура Т2 (рис. 35), при которой образуется прочное сцепление, существует практически для всех сочетаний материалов частиц и основы: элементов, сплавов, простых или сложных веществ.
Рис. 35. Характеризмененияотносительной величины пятнахимическоговзаимодействия Dx/D взависимости оттемпературыподогрева основыТ2 при нанесениичастиц (диаметр 100–200 мкм) серебра насеребро
(чистота99,99 % Ag): 1 – частицынагретывыше
Тпл(v1≈40 м/с); 2 – частицынагретыдоТпл (v1≈20…40 м/с); 3 – частицы нагретыдоТпл (v1≈5 м/с)
100