
книги / Специальные плазменные технологии
..pdf
qs = |
πTзакB |
, |
|
||
|
2 t |
где Тзак – температура закалки; В – коэффициент аккумуляции теплоты.
В работах В.П. Токмакова, М.В. Гречневой, А.В. Петухова, А.А. Скрипкина, В.Н. Матханова приводятся расчетные данные, позволяющие определить температуру нагрева и скорость охлаждения металла. Построены номограммы для выбора оптимальных режимов плазменного упрочнения. Проведенные этими авторами экспериментальные исследования процесса плазменного упрочнения сталей 9ХФ, 40Х, У8, Х12М показали, что максимальная поверхностная твердость после упрочнения пропорциональна величине углеродного эквивалента Сэкв, а глубина упрочнения зависит от коэффициента температуропроводности. Это позволило авторам установить зависимость вида
HVmax = f (q,v,Сэкв );h = (q,v,а).
Полученные результаты, по мнению авторов, свидетельствуют о хорошем совпадении экспериментальных и расчетных данных, что позволяет, не проводя экспериментов, прогнозировать максимальнуютвердостьиглубину упрочненныхповерхностей.
2.5. СПОСОБЫ ПЛАЗМЕННОГО ПОВЕРХНОСТНОГО УПРОЧНЕНИЯ
Способы плазменного поверхностного упрочнения можно разделить на два больших направления – процессы с материалами в твердом состоянии и при расплавлении их поверхности. На рис. 16 приведена часть вариантов плазменного поверхностного упрочнения, которые возможно осуществить теоретически и практически.
61
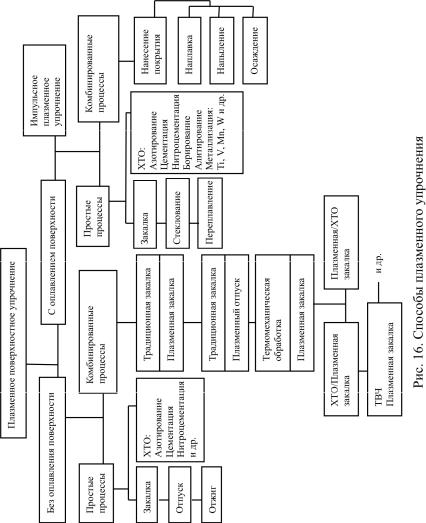
62
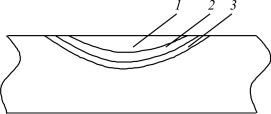
В настоящее время наиболее широко исследуются следующие направления:
1)закалка сплавов из твердого состояния со скоростями нагрева и охлаждения 102–104 °С/с;
2)закалка сплавов из жидкого состояния с высокими ско-
ростями плавления и кристаллизации 102–105 °С/с;
3)поверхностное легирование, наплавка материала, обработка предварительно нанесенных на металл покрытий, нагрев поверхностных слоев после ХТО;
4)оплавление поверхностного слоя и затвердевание с вы-
сокими и сверхвысокими скоростями (104–107 °С/с), приводящие к аморфизации (стеклованию) тонкого поверхностного слоя.
Многочисленные исследования в области плазменного упрочнения с использованием электронной и оптической микроскопии показали, что зона термического воздействия плазменной струи (дуги) имеет форму сегмента и по своему строению аналогична ЗТВ электронного и лазерного луча. При нагреве плазменной струей (дугой) поверхности металла происходит нагрев поверхности до различных температур, вследствие чего он имеет слоистое строение. В зависимости от микроструктуры и микротвердости в сталях по глубине различают три слоя (рис. 17).
Зона оплавления 1 (первый слой) имеет место при закалке с оплавлением. Как правило, зона оплавления имеет столбчатое строение с кристаллами, вытянутыми в направлении теплоотвода. Основная структурная составляющая – мартенсит, карбиды обычно растворяются.
Рис. 17. Схема строения ЗТВ при плазменном упрочнении
63
При оптимальных режимах закалки с расплавлением обезуглероживание не происходит, нет пор и шлаковых включений. При плазменной закалкебез оплавления первыйслой отсутствует.
Второй слой – зона закалки 2 из твердой фазы. Его нижняя граница определяется температурой нагрева до Ас1. В этом случае наряду с полной закалкой происходит и неполная. По глубине данный слой характеризуется структурной неоднородностью. В верхнем слое расположен мартенсит и остаточный аустенит, полученные при охлаждении из гомогенного аустенита. Ближе к исходному металлу наряду с мартенситом имеются элементы исходной структуры: феррит в доэвтектоидной стали
ицементит в заэвтектоидной.
Впереходной зоне 3 (третий слой) металл нагревается ни-
же точки Ас1. Если сталь имеет исходное состояние после закалки или отпуска, то в результате плазменной обработки в этом слое образуются структуры отпуска – троостит или сорбит, характеризуемые пониженной твердостью.
Глубина закаленной зоны зависит от плотности мощности источника нагрева и скорости его перемещения. Глубину закалки или оплавления сталей и чугунов определяют по формуле
Z = Р/(dν) 0'4,
где Z – толщина закаленного или оплавленного слоя; Р – мощность плазмотрона; d – диаметр сопла плазмотрона; ν – скорость перемещения плазмотрона.
Характер распределения микротвердости по глубине δ и ширине L ЗТВ плазменной струи при обработке без оплавления показан на рис. 18.
При варьировании плотности мощности плазменного нагрева обычно регулируют силу тока и скорость перемещения, оставляя другие параметры без изменения. При плазменной закалке больших поверхностей возникает проблема перекрытия соседних закаленных областей. Наиболее широко встречаются два случая последовательного упрочнения полос: обработка плоских по-
64
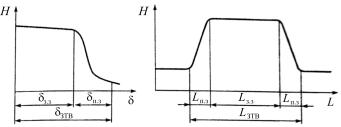
верхностей и обработка цилиндрических поверхностей. При этом важной характеристикой является коэффициент перекрытия,
Kп= S/L3.3,
где S – шаг между закаленными зонами; L3.3 – ширина закаленной зоны.
а |
б |
Рис. 18. Характер распределения микротвердости по глубине (а) и ширине (б) ЗТВ плазменной струи при обработке без оплавления
Полосы могут быть выполнены с перекрытием (при Кп < 1) и без перекрытия (при Kп> 1). Под действием теплового поля, возникающего при формировании очередной полосы, происходит частичный отпуск соседних закаленных зон. При этом распределение твердости по ширине ЗТВ будет представлять собой чередование участков с ее высокими и низкими значениями. Во многих случаях упрочненные полосы располагаются на некотором расстоянии друг от друга так, чтобы обработанная плазменной дугой площадь составляла 20–50 % общей площади, что приводит к наибольшей износостойкости.
Обработку плоских поверхностей ведут по двум схемам выполнения полос (рис. 19): линейной (а) и клеточной (б). После выполнения каждой полосы деталь или плазмотрон периодически смещают в поперечном направлении на расстояние, равное шагу S. Наиболее просто при клеточной схеме полосы выполнять под прямым углом друг к другу и с одинаковым ша-
65
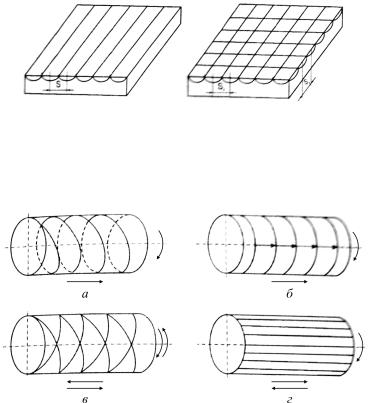
гом по обеим координатам, хотя больших сложностей для наложения полос не под прямым углом и для упрочнения с Sx ≠ Sy нет. Цилиндрические поверхности обрабатывают преимущественно по четырем схемам (рис. 20): а – полосу выполняют по одной винтовой линии; б – полосу выполняют по двум винтовым линиям навстречу друг другу с постоянной осевой подачей S; в– кольцевые полосы выполняют с дискретной осевой подачей S; г – полосы выполняют вдоль оси по образующей с периодическим вращением детали для смещения на шаг S.
аб
Рис. 19. Схемы выполнения упрочняющих полос на плоской детали
Рис. 20. Схемы упрочнения цилиндрических деталей
66
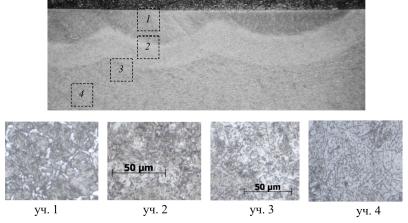
По этим же схемам ведут упрочнение внутренних цилиндрических поверхностей. При этом минимальный внутренний диаметр упрочняемых деталей ограничивают размеры плазмотрона для внутреннего упрочнения.
На рис. 21 представлена макро- и микроструктура закаленного слоя на стали 40Х13, выполненного дугой прямого действия током прямой полярности с оплавлением. Закалочные дорожки выполнены без зазора и перекрытия. Закаленная поверхность прошла механическую обработку.
Ширина упрочненных дорожек 10,3–11,6 мм, глубина зоны оплавления 1,5–2,1 мм, зоны закалки из твердой фазы 2,1–2,8 мм. Структура основного материала образца представляет собой фер- рито-карбидную смесь (уч. 4), характерную для данного материала в состоянии после отжига либо высокого отпуска.
Рис. 21. Макро- (х8) и микроструктура (х400) закаленного слоя на стали 40Х13, обработанного с оплавлением поверхности
Зона оплавления (уч. 1) представляет собой структуру мартенситного типа с ферритной сеткой по границам кристаллитов. У границы сплавления в основном материале наблюдаются структура мартенситного типа (уч. 2). В зоне термовлияния –
67

структура мартенсита отпуска с плавным переходом к структуре основы (уч. 3). Микротвердость различных участков представлена в табл. 5.
|
|
|
|
Таблица 5 |
|
Микротвердость различных зон упрочненного слоя |
|||||
|
|
|
|
|
|
Образец |
Микротвердостьпозонам, Нμ50, кгс/мм2 |
||||
Зона |
ЗТВуграницы |
ЗТВ |
|
Основной |
|
|
оплавления |
сплавления |
|
материал |
|
|
|
|
|||
Соплавлением |
482–533 |
429–460 |
267–479 |
|
238–239 |
Безоплавления |
поверхность |
зоназакалки |
241–478 |
|
238–239 |
|
502–527 |
488–507 |
|
|
|
Плазменная поверхностная термообработка на токе обратной полярности благодаря особенностям теплопередачи в изделие позволяет получать упрочненные слои достаточной глубины без оплавления поверхности. При таком варианте термообработки происходит равномерный нагрев по ширине упрочненной зоны, и за счет катодных явлений на поверхности изделия обеспечиваются высокие скорости нагрева и охлаждения, необходимые для проведения закалки поверхности.
При обработке без оплавления поверхности стали 40Х13 на токе обратной полярности получается равномерный упрочненный слой глубиной 2,5 мм с шириной дорожки в 20–25 мм со структурой мелкодисперсного мартенсита (рис. 22) и равномерным распределением твердости по глубине упрочненной зоны
(см. табл. 5).
Плазменное упрочнение в жидких средах расширяет воз-
можности поверхностного упрочнения металлов: повышает производительность и качество обработки; позволяет осуществить комбинированное воздействие на рабочие поверхности деталей; улучшает эксплуатационные свойства изделий. При плазменном нагреве не всегда удается избежать накопления теплоты в обрабатываемом изделии. С целью устранения нако-
68
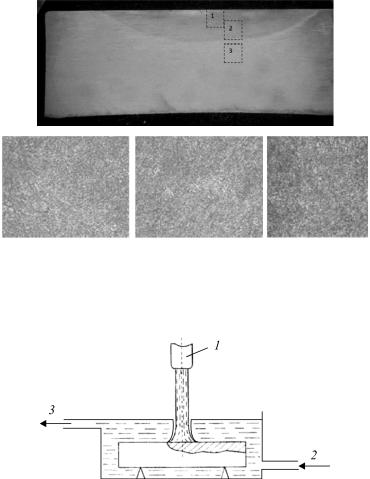
пления теплоты в изделии используют плазменное упрочнение в жидких средах. Обрабатываемое изделие погружают в жидкость таким образом, чтобы над его поверхностью была жидкая прослойка определенной толщины (рис. 23), последняя зависит от параметров плазменной струи и свойств жидкости.
уч. 1 |
уч. 2 |
уч. 3 |
Рис. 22. Макро- (х8) и микроструктура (х250) образца, обработанного без оплавления поверхности на токе обратной полярности, сталь 40Х13
Рис. 23. Схемапроцессаплазменногоупрочнениявжидких средах: 1 – плазмотрон; 2 – вводводы; 3 – выводводы
69
Благодаря газодинамическому напору плазменной струи в жидкой прослойке создается воронка, через которую происходит термическое воздействие плазмы на обрабатываемую поверхность. Обработку осуществляют в полузамкнутом объеме, ограниченном со всех сторон жидкостью. При движении плазменной струи относительно детали нагретая до температуры структурных превращений поверхность сразу закрывается жидкостью, которая охлаждает ее. Если использовать не воду, а активные жидкие среды типа растворов различных солей, на поверхность можно дополнительно химически воздействовать.
Установлено, что коэффициент сосредоточенности и максимальный тепловой поток в центре пятна нагрева при обработке в воде возрастают примерно на 20 %. Площадь пятна нагрева уменьшается на такую же величину по сравнению с плазменной закалкой на воздухе. При плазменном упрочнении в жидкой среде скорость охлаждения повышается в пять-шесть раз, вследствие чего максимальная твердость сталей возрастает до 20 % по сравнению с упрочнением на воздухе.
Преимуществом рассматриваемого способа является практически полное отсутствие деформаций обрабатываемого изделия. Повышение скорости нагрева сокращает температур- но-временный интервал роста зерна и гомогенизации аустенита, однако в ряде случаев этого недостаточно для эффективного управления формированием структуры, так как при плазменном упрочнении одновременно со скоростями нагрева увеличиваются и скорости охлаждения. Это тормозит распад аустенита, смещая его в мартенситную область. Решить поставленную задачу позволяет сочетание высоких скоростей нагрева и термоциклирования. С увеличением числа циклов мартенситная структура упрочненного слоя характеризуется более высокой степенью дисперсности по сравнению с дисперсностью при обычной закалке, что способствует повышению трещиностойкости упрочненных слоев.
70