
книги / Специальные плазменные технологии
..pdf3. ПЛАЗМЕННОЕ НАПЫЛЕНИЕ ПОРОШКОВЫХ ПОКРЫТИЙ
Использование износостойких, коррозионно-стойких, жаростойких, химически стойких, электроизоляционных, теплоизоляционных и других видов покрытий позволяет повысить эксплуатационные характеристики металлических конструкций, работающих в тяжелых условиях. Большое распространение в настоящее время получили методы нанесения покрытий напылением. Использование плазменной струи для нанесения порошковых покрытий позволяет не только изменять свойства поверхности конструкционных материалов, но и дает возможность создавать новые композиционные материалы и покрытия, которые не могут быть получены другими методами. Плазменное напыление позволяет создавать покрытия практически из любых материалов, в том числе керамических.
3.1. СУЩНОСТЬ И РАЗНОВИДНОСТИ НАНЕСЕНИЯ ПОРОШКОВЫХ ПОКРЫТИЙ
Существует две разновидности процесса напыления порошковыхпокрытий.
В первом случае напыление осуществляют в основном при атмосферном давлении частицами материала покрытия размером 10–150 мкм. Во втором – напыление при пониженном давлении атомами или ионами, которые, осаждаясь и конденсируясь на поверхности изделия (детали), образуют покрытия. Конденсацией можно наносить покрытия сложного состава. Для этого смешивают потоки пара различных компонентов или создают условия для синтеза вещества покрытия путем химического взаимодействия парового потока с окружающей газовой ат-
81
мосферой. Например, таким способом получают покрытия из оксидов, карбидов, нитридов и других соединений.
Нанесение покрытий испарением и конденсацией требует создания сложных технологических условий для получения вакуума, испарения напыляемого вещества.
Нанесение покрытий конденсированными частицами ведут с помощью газотермических методов напыления. В этих методах материал покрытия подвергают нагреву и плавлению каким-либо источником теплоты, а затем диспергируют и разгоняют газовым потоком. Для получения газотермических покрытий сложного состава его компоненты заранее вводят в напыляемые частицы.
В зависимости от источника теплоты различают следующие методы газотермического нанесения покрытий: электродуговую металлизацию, газопламенное напыление, детонационное напыление, газовое напыление, плазменное напыление. В настоящее время развивается газотермическое нанесение покрытий в динамическом вакууме, разряжение создается непрерывной интенсивной откачкой атмосферы камеры. Этот процесс в первую очередь применяют для плазменного напыления и дуговой металлизации.
Высокая эффективность и универсальность этих методов обусловлена следующими особенностями:
–возможность нанесения покрытий из различных мате-
риалов;
–получение покрытий на самых различных конструкциях
иматериалах: металлах, стеклах, керамике, пластмассах, тканях, бумаге и др.;
–отсутствие деформации и понижение прочности изделия, на которое наносится покрытие, поскольку напыление не вызывает его существенного нагрева;
–небольшая потребность в материалах для покрытий, поскольку их толщина обычно составляет 100–500 мкм;
–высокая производительность газотермических методов напыления, которая колеблется для различных процессов от 1 до 20 кг/ч распыленного материала;
82
–регулирование в широких пределах свойств напыленных покрытий.
Недостатками являются:
–низкий коэффициент использования энергии – от 0,02 до 0,18 при напылении проволочных материалов и от 0,001 до 0,02 при напылении порошками;
–наличие остаточной пористости и других видов несплошностей, от 2 до 15 %;
–сравнительно невысокая адгезионная и когезионная прочность покрытия (максимальное значение составляет от 80 до
100 МПа);
–высокий уровень шума при открытом ведении процесса
(от 60 до 100 дБ);
–большие потери напыляемого материала при нанесении покрытий на небольшие детали;
–сложный и длительный процесс подготовки поверхности под напыление.
Общим для всех газотермических методов является то, что материал покрытия нагревается, распыляется и ускоряется в высокотемпературном газовом потоке (рис. 27). На поверхность изделия или основы напыляемый материал поступает в диспергированном состоянии, в виде мелких расплавленных или пластифицированных частиц, которые ударяются о нее, деформируются и, закрепляясь, накладываются друг на друга, образуя слоистое покрытие.
В высокотемпературный источник нагрева 1 напыляемый материал может подаваться в виде порошка или проволоки (прутка) 2. В случае нанесения покрытий из проволоки она на-
гревается, плавится и диспергируется с торца, находящегося в высокотемпературной области источника нагрева. При напылении порошков частицы, попадая в высокотемпературный поток, нагреваются на некотором участке А. Одновременно частицы распределяются в газовом потоке и ускоряются им на участке Б в соответствии с законом газодинамики.
83
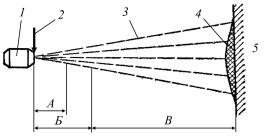
Рис. 27. Схема процесса газотермического нанесения покрытий: 1 – высокотемпературный источник нагрева; 2 – напыляемый материал; 3 – частицы напыляемого материала; 4 – покрытие; 5 – основа; А – дистанция, на которой происходит нагрев напыляемого материала; Б – дистанция, на которой частицы ускоряются газовым потоком; В – область свободного движения частиц
Участок Б обычно протяженнее участка А. Далее на участке В частицы 3 направленно перемещаются к основе 5 и образуют на ней покрытие 4. При напылении частицы плавятся, испаряются и вступают в химическое взаимодействие с нагретым газом и окружающей средой. Удар и деформация частиц приводят к их чрезвычайно быстрой кристаллизации и охлаждению со скоростями, достигающими 100–108 К/с. Газотермические покрытия в целом и их отдельные элементы отличаются необычным строением, поскольку они образуются из быстро кристаллизующихся частиц малого размера. Для образования покрытия напыляемые частицы должны быть нагреты и иметь достаточно высокую скорость. При газотермическом нанесении покрытий частицы напыляют в расплавленном или пластичном состоянии. Скорость частиц составляет десятки и сотни метров в секунду.
В результате распыления материала плазменной струей получают двухфазную струю, которая состоит из напыляемых частиц (размер 10–150 мкм) и нагретого газа. При ударе о поверхность детали частицы деформируются и, накладываясь друг на друга, образуют покрытие. Одновременно двухфазный поток
84
нагревает поверхность детали в зоне напыления. Энергетические характеристики двухфазного потока, количество частиц и их распределение в потоке регулируются в зависимости от требований технологии.
Свойства покрытия и его равномерное нанесение на поверхность детали зависят от распределения частиц в потоке как по массе и скорости, так и по их энергетическому состоянию. Одной из важнейших задач технологии и аппаратуры для нанесения покрытий является создание двухфазных потоков с заданным распределением и энергией частиц.
В процессе напыления в двухфазном потоке происходит взаимодействие между частицами и газом. Вследствие высокой температуры газа это взаимодействие протекает быстро и в зависимости от состава газа может вести к образованию новых веществ – нитридов, оксидов, карбидов и других соединений. Поэтому состав газа двухфазного потока и его химическая активность являютсяважным параметромпроцессаполученияпокрытия.
3.2. ПЛАЗМЕННОЕ НАПЫЛЕНИЕ ПОРОШКОВЫХ ПОКРЫТИЙ
Для нанесения покрытия плазменным напылением материал покрытия в виде порошка или проволоки вводят в плазменную струю столба дуги, где он нагревается и ускоряется по направлению к основе (рис. 28). Для нанесения покрытий применяют низкотемпературную плазму, сформированную при атмосферном давлении. Температура в такой плазме составля-
ет 103–105 К.
Достоинством атмосферной низкотемпературной плазмы являются ее хорошие технологические свойства, которые определяются высокой энтальпией и хорошими переносными свойствами плазмы, т.е. способностью передавать температуру и скорость напыляемым частицам.
85
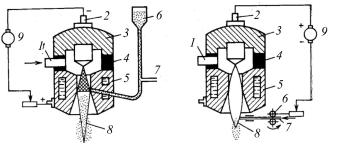
аб
Рис. 28. Схема плазменного напыления: а – порошком; б – проволокой; 1 – подвод плазмообразующего газа; 2 – катод плазмотрона; 3 – корпус катода; 4 – изолятор; 5 – корпус анода; 6 – порошковый питатель (механизм подачи проволоки, рис. б); 7 – подвод транспортирующего
газа; 8 – плазменная струя; 9 – источник питания
При плазменном нанесении покрытий с использованием порошков, несмотря на высокую температуру плазмы, трудно добиться равномерного и полного плавления всего напыляемого материала. Это объясняется рядом причин. Большинство неметаллических материалов имеют низкую теплопроводность, и поэтому частицы таких материалов медленно прогреваются в плазме. Время пребывания частиц в плазме составляет порядка ~10–3 с и часто оказывается недостаточным для полного плавления на всю глубину частиц. Характеристики двухфазного потока, состоящего из плазмы и напыляемых частиц, а также распределение частиц в плазме определяют не только их нагрев и ускорение, но и условия формирования покрытия и распределения его толщины по поверхности детали.
В настоящее время для нанесения покрытий в качестве плазмообразующих газов используют аргон, гелий, азот, водород, аммиак, воздух, природный газ, углекислый газ и их смеси, также были разработаны распылители, использующие для стабилизации дуги и распыления воду.
86
Для повышения эффективности нагрева и плавления частиц в плазме применяют высокоэнтальпийные газы, имеющие большое теплосодержание при относительно низких температурах (4000–7000 К). В плазме с высокой температурой частицы с поверхности начинают интенсивно испаряться, в результате чего вокруг частицы образуется паровая рубашка, препятствующая ее теплообмену с плазмой и снижающая эффективность нагрева. Благодаря высокому теплосодержанию плазма двухатомных газов охлаждается медленнее плазмы одноатомных газов и поэтому образует плазменные струи большей протяженности. Увеличение длины струи приводит к увеличению пути (или времени пребывания) напыляемых частиц в плазме, что дает возможность расплавлять частицы при меньшей температуре плазмы.
Вследствие того что температура и скорость плазмы распределены по сечению струи неравномерно, скорость частиц на оси струи выше, чем на ее периферии. Движение частицы вещества в неизотермическом потоке газа, каким является плазменная струя, определяется суммарным действием на нее ряда сил, направление и величина которых различна.
Основной силой, действующей на напыляемую частицу в потоке плазмы, является сила аэродинамического сопротивления. Все другие силы имеют величину следующего порядка малости.
Частицы напыляемого материала ускоряются плазменным потоком вследствие действия сил вязкости и динамического напора. Для решения задачи о движении частиц в плазме обычно вводят рядупрощающих допущений:
–частицы являются сферическими и имеют одинаковый диаметр;
–распределение частиц по сечению канала сопла равно-
мерное;
–частицы не взаимодействуют между собой и со стенкой
сопла;
87
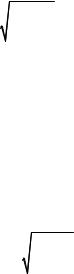
–присутствие частиц конденсированной фазы в плазме не влияет на термодинамические и теплофизические свойства газа;
–испарения частиц не происходит.
Сучетом этих допущений уравнение движения частицы
впотоке плазмы имеет вид
v |
= v |
3γпcx |
x, |
|
2γ1d |
||||
1 |
п |
|
||
где x путь, пройденный частицей; v1 |
– скорость частицы; vп – |
скорость плазмы; γ1 – плотность материала частицы; γп – плот-
ность плазмы; сх – коэффициент аэродинамического сопротивления частицы.
После определенных преобразований постоянных и интегрирования можно получить уравнение, определяющее убывание скорости газа в сопле плазмотрона, обусловленное присутствием частиц в потоке:
v |
|
|
G ' |
|
3γп сx |
|
|
п |
= exp |
− |
|
|
|
x |
, |
v |
G |
|
2γ d |
||||
|
|
|
|
|
|||
г |
|
|
п |
1 |
|
|
где vг – скорость газа в плоскости ввода порошка в сопло. Полученное уравнение в первом приближении определяет
убывание скорости газа в сопле плазмотрона, обусловленное присутствием частиц в потоке. Однако сложно определить коэффициент сопротивления сх.
При распылении плазмой небольшой мощности стержней и проволоки скорость частиц составляет 50–150 м/с. Скорость зависит от размера частиц, плотности их материала, траектории движения и мощности плазмы. С увеличением размера частиц скорость их падает.
88
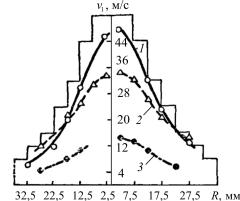
Скорость частиц распределена по пятну напыления радиусом R неравномерно (рис. 29). Особенно сильно изменяется скорость мелких частиц, у которых она на периферии пятна может быть в 3–5 раз ниже, чем на оси струи. У более крупных частиц перепад скорости меньше.
Рис. 29. Характер распределения скорости частиц различного диаметра в пятне напыления: (1) d = 100–150; (2) d = 150–200; (3) d = 300–350 мкм
Мелкие частицы диаметром менее 100 мкм быстрее набирают скорость в плазме (рис. 30) и быстрее ее теряют. Наибольшую скорость частицы обычно имеют приблизительно на расстоянии 40–60 мм от среза сопла плазмотрона.
Высокие скорости частиц можно получить в гелиевой и аргоновой плазме, что объясняется особенностью плазменных струй этих газов и в первую очередь большой скоростью истечения из сопла. Высокая скорость истечения возникает вследствие нагрева этих газов до большей температуры по сравнению с двухатомными газами, а следовательно, и более сильным их расширением. Например, при одинаковой энтальпии азот будет иметь температуру 5000 °С, аргон – 13 000 °С, агелий – 17 000 °С.
89
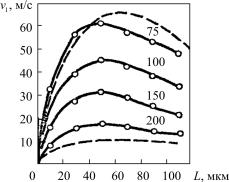
При напылении в аргоно-гелиевой плазме получены скорости частиц порошка кобальта с карбидом вольфрама, равные 305 м/с. Эта скорость в два раза больше скорости частиц при напылении аргоно-водородной плазмой. Износостойкость покрытий, напыленных высокоскоростными частицами, оказывается в три раза выше, чем у покрытий, полученных при скорости частиц 130 м/с.
Рис. 30. Сопоставление скоростичастиц, определенной потрекамнафотографиидвухфазногопотока (штриховаякривая верхняя– максимальная; штриховая криваянижняя– минимальная) ирассчитанной
из высотызатвердевшихчастиц(сплошныекривые). Цифры накривых – диаметрчастицпорошка
В настоящее время разработаны и освоены плазмотроны для нанесения покрытий, которые позволяют получить при напылении скорость частиц выше 300 м/с. Большое увеличение скорости частиц достигается при нанесении покрытий в разреженной контролируемой атмосфере, где скорость плазмы может достигать нескольких Махов.
Эффективный КПД для ряда плазменных процессов и электродуговой металлизации представлен ниже:
90