
книги / Мониторинг состояния цементобетонных дорожных конструкций
..pdf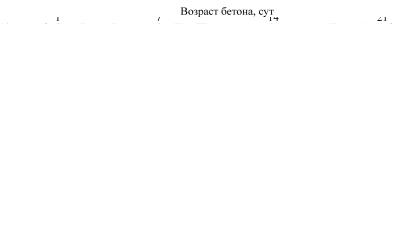
|
|
Рис. 5.3. Изменение прочности бетона лотков |
|||||
|
|
|
|
|
|
Таблица 5.7 |
|
|
|
Прочность бетона после прогрева |
|
|
|||
|
|
|
|
|
|
|
|
Ско- |
Макси- |
|
Кубиковая прочность бетона, МПа |
||||
рость |
маль- |
|
|
|
покрытого |
|
|
подъёма |
ная |
|
|
|
|
|
|
|
|
полимером |
лак-этинолем |
||||
темпе- |
темпе- |
непокры- |
|
||||
|
|
|
|
|
|||
ратуры, |
ратура |
того |
водой |
за 1 раз |
за 2 раза |
за 1 раз |
за 2 раза |
°С |
бетона, |
|
|||||
в час |
°С |
|
|
|
|
|
|
60 |
135 |
20,9/100,0 |
21,1/100,9 |
34,1/163,1 |
31,8/152,1 |
24,9/119,1 |
26,1/124,9 |
|
|
|
|
|
|
|
|
50 |
120 |
27,2/100,0 |
27,5/101,1 |
37,6/138,4 |
37,4/137,5 |
31,3/116,1 |
32,8/120,6 |
|
|
|
|
|
|
|
|
40 |
96 |
29,6/100,0 |
29,5/99,6 |
37,9/127,9 |
37,5/126,6 |
33,1/117,8 |
34,8/117,5 |
|
|
|
|
|
|
|
|
20 |
80 |
31,7/100,0 |
32,7/103,1 |
38,3/120,8 |
37,8/119,2 |
34,6/109,1 |
37,2/117,3 |
|
|
|
|
|
|
|
|
Примечание. Перед чертой даны абсолютные величины прочности бетона, за чертой – в % по отношению к прочности непокрытого бетона.
Покрытие поверхности образцов пленкообразующими материалами влечет за собой увеличение прочности: чем выше температура прогрева, тем больший эффект использования пленкообразующих материалов. Сопоставление полимера К-9 с лак-этинолем показывает, что при температуре прогрева 96 °С и выше полимер К-9 предпочтительней, так как дает больший эффект. Нанесение пленкообразующего материала на поверхность, свободную от опалубки, уменьшает количество испарившейся во-
201
ды (табл. 5.8), способствуя тем самым сохранению влаги в бетоне и последующему набору прочности.
Результаты апробации полимера К-9 в сопоставлении с лак-этинолем производилось на сваях и представлены в табл. 5.9.
|
|
|
|
Таблица 5.8 |
|||
|
Водопоглощение бетона |
|
|
|
|||
|
|
|
|
|
|
|
|
Скорость |
Максимальная |
Водопоглощение бетона, % |
|
||||
подъёма |
|
|
покрытого |
|
|||
температуры, |
температура |
непокрытого |
|
|
|
|
|
|
полимером |
||||||
°С в час |
бетона, °С |
водой |
|||||
|
за 1 раз |
|
За 2 раза |
||||
|
|
|
|
|
|||
40 |
96 |
13,5 |
13,1 |
11,8 |
|
11,9 |
|
|
Количество испарившейся воды, в г |
|
|
|
|||
40 |
96 |
139 |
124 |
86 |
|
79 |
|
|
|
|
|
|
|
|
Таблица 5.9
Характеристики прочности бетона в изделии
|
Значение характеристики в изделиях, |
||||
Характеристика |
покрытых |
покрытых |
|||
полимером |
лак-этинолем |
||||
|
|||||
|
за 1 раз |
за 2 раза |
за 1 раз |
за 2 раза |
|
Средняя прочность, МПа |
19,4/14,7 |
18,5/14,3 |
17,7/16,2 |
19,9/16,8 |
|
Среднеквадратичное отклонение |
19,6/33,4 |
13,5/28,9 |
18,5/32,3 |
19,7/27,6 |
|
Коэффициент вариации прочно- |
10,1/19,8 |
7,3/17,7 |
10,4/19,9 |
10,4/16,4 |
|
сти бетона в изделии (ν) |
|||||
|
|
|
|
||
|
|||||
Примечание. Перед чертой для изделий, покрытых пленкообразующими |
|||||
материалами, за чертой – непокрытых. |
|
|
|
При температуре 80 °С эффект сравниваемых пленкообразующих материалов примерно одинаков. Покрытие полимером К-9 за 2 раза нецелесообразно, так как при этом, по-видимому, нарушается целостность ранее нанесенного слоя. При этом улучшается и структура бетона, о чем свидетельствуют данные, приведенные в табл. 5.10.
202
|
|
|
|
Таблица 5.10 |
|
Характеристика сравниваемых бетонов |
|
||
|
|
|
|
|
|
Значение характеристик бетона в возрасте |
|||
Параметры |
28 суток |
12 месяцев |
||
|
непокрытых |
покрытых |
непокрытых |
покрытых |
Rb, МПа |
23,2 |
27,8 |
26,0 |
30,5 |
R0 |
0,34 |
0,35 |
0,35 |
0,37 |
crc |
|
|
|
|
W, % |
12,7 |
11,5 |
11,3 |
10,9 |
|
|
|
|
|
Из данных видно, что нанесение раствора полимера К-9 и лакэтиноля на поверхность изделия, свободную от опалубки, дает эффект в виде повышения прочности на 31,9 и 15,3 % соответственно. При этом имеет место уменьшение коэффициента вариации прочности (ν), что свидетельствует о более равномерном распределении прочностей по изделиям. Нанесение второго слоя полимера в этом случае уменьшило разброс показателей прочности по изделию, уменьшив среднеквадратичные отклонения и коэффициенты вариации прочности.
Изучение прочностных свойств бетона лотков, изготавливаемых
втермоформах, показало, что по длине и высоте лотков имеет место разброс показателей прочности бетона. Лоток формуется днищем вверх, и прочность уменьшается по направлению снизу вверх, т.е. по направлению движения влаги при прогреве изделия, что согласуется с результатами исследований, изложенными в работах [30, 65]. В первой серии экспериментов среднее значение прочности бетона по высоте лотка изменялось от 19,0 до 29,0 МПа, а по длине – от 25,0 до 35,0 МПа, в целом по лотку от 16,0 до 34,0 МПа. Аналогичный разброс имел место и во 2-й серии экспериментов.
При использовании полимера К-9 как пленкообразующего материала прочность бетона лотков увеличилась на 5,5 % при нанесении полимера
водин слой и на 12,9 % при нанесении в два слоя. При этом изменение средней прочности бетона по высоте изделия составило: при нанесении полимера в один слой – 24,3 %, при нанесении в два слоя – 20,7 %, а в непокрытых лотках – 34,5 %.
По длине лотков средняя прочность изменялась в первом случае на 18,8 %, во втором на 25,8 %, а в непокрытых лотках – на 34,4 %.
203
Апробация полимера на изделиях (сваях и лотках) показала наличие эффекта, несколько меньшего, чем на лабораторных образцах.
Определение стойкости бетона по предлагаемой методике производилось на лабораторных образцах. Значения показателей сравниваемых бетонов приведены в табл. 5.10.
Стойкость бетона образцов, рассчитанная по предлагаемой методике, составила для непокрытых образцов 9,4 года, для покрытых – 12,1 лет.
5.2.5. Оценка стойкости пропаренных цементобетонов с добавкой ПЯ-01, защищенных пленкообразующими материалами
В качестве пленкообразующего материала принят препарат К-9 (см. гл. 2). Покрытие пленкообразующим препаратом поверхности лабораторных образцов из бетона 3-го состава производилось сразу после разопалубки. Через 4 часа после покрытия пленкообразующим препаратом образцы подвергались воздействию климата. Характеристики свойств бетона определялись в возрасте 28 суток, 12 месяцев и представлены в табл. 5.11.
Таблица 5.11
Характеристики свойств бетона, защищенного плёнкообразующим препаратом
|
3начения характеристик |
Значения параметров состояния |
|
Характеристика |
свойств бетона в возрасте |
бетона после 12 месяцев |
|
|
28 суток |
12 месяцев |
воздействия климата |
Rb, МПа |
35,5 |
42,5 |
0,197 |
R0 |
0,37 |
0,4 |
0,081 |
crc |
|
|
|
W, % |
10,5 |
9,3 |
–0,114 |
|
|
|
|
Стойкость бетона с добавкой ПЯ-01, защищенного после изготовления от воздействия климата пленкообразующим препаратом К-9, определенная по формулам (5.3) и (5.4), составила 15,9 лет. За предельное состояние принято состояние бетона с добавкой ПЯ-01, испытавшего 75 циклов лабораторного воздействия (см. табл. 5.2 и 5.3). Таким образом, защита пленкообразующим препаратом повысила стойкость бетона с добавкой ПЯ-01 на 16,9 %.
204
Изучение структуры бетона с добавкой ПЯ-01, покрытого пленкой препарата К-9, показало, что по основным характеристикам структуры защищенный бетон близок к бетону, который после изготовления твердел в нормальных условиях.
Основные характеристики структуры представлены в табл. 5.12, а микроструктура цементного камня бетонов изображена на рис. 5.4 и 5.5.
Таблица 5.12 Характеристики структуры бетона образцов в возрасте 29 месяцев
|
|
Бетон, твердевший в условиях |
|||
Характеристики |
Единица |
|
реальной климатической |
||
измере- |
|
среды |
|||
структуры бетона |
нормальных |
||||
ния |
|
|
|||
покрытый |
непокрытый |
||||
|
|||||
|
|
|
пленкой |
||
Непрогидратированные |
% |
7–10 |
7–10 |
10 |
|
реликты |
|||||
|
|
|
|
||
Пористость |
% |
3 |
2-3 |
5 |
|
Размеры пор |
микрон |
60–120 |
80–120 |
80–120 |
|
Размеры микротрещин |
микрон |
10–12 |
2–5 |
7–12 |
|
Гидрогель |
% |
5–7 |
7 |
7–8 |
|
Гидросиликаты и гидро- |
% |
2–3 |
7 |
1,5–2 |
|
окись Са |
|||||
|
|
|
|
||
Гидросульфоалюминат |
% |
0,5 |
– |
1,5–2 |
Микротрещины в защищенном бетоне преимущественно заполнены новообразованиями, что должно быть оценено положительно, в то время как в незащищенном бетоне они полые. Характер новообразований, уменьшение размеров пор, микротрещин, количества непрогидратированных реликтов объясняют увеличение стойкости защищенных бетонов.
Цементный камень бетона, защищенного пленкообразующим препаратом К-9, характеризуется плотной игольчатой структурой, в промежутках между слоевыми кристаллами вторичного портландита наблюдаются мелкие призматические кристаллы и их сплетения. Мелкие кристаллы заполняют поровое пространство, тем самым упрочняют цементный камень.
205
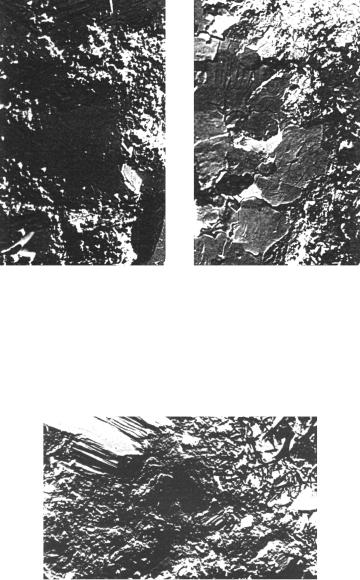
а |
б |
Рис. 5.4. Микроструктура цементного камня (×10 000) бетона, покрытого полимером К-9 (а) и непокрытого (б), твердевших под воздействием климата
Рис. 5.5. Микроструктура цементного камня бетона, твердевшего в нормальных условиях
Вцементном камне незащищенного бетона крупные кристаллы несут
всебе отпечатки зародышей кристаллизации. Контакты крупного заполнителя с цементным камнем неплотные, наблюдаются полые микротрещины шириной 7–12 микрон. Контакты цементного камня с мелким заполнителем выполнены в основном гидросульфоалюминатом.
206
5.2.6. Оценка влияния пластификации цементобетона с добавкой ПЯ-01 и покрытия поверхностей изделия препаратом К-9 на свойства плит ПГ
Исследование проведено на натурных конструкциях – предварительно напряженных ребристых плитах ПГА-IV-2Т размером 3×6 м, предназначенных для покрытия производственных зданий. Плиты изготовлены на заводе ЖБИ в соответствии с ГОСТ 22701.0–77, 22701.1–77.
Испытывались 4 плиты, из них 2 – серийные, выпускаемые заводом, а при изготовлении двух других плит использована добавка ПЯ-01, при этом расход цемента в производственном составе был уменьшен на 10 %. Поверхности одной серийной плиты и одной плиты с добавкой после пропарки и разопалубки покрывались пленкообразующим препаратом К-9. Цель испытаний – оценка и сопоставление фактических прочности, жесткости и трещиностойкости плит в соответствии с требованиями ГОСТа. Методика испытаний изложена в гл. 2, состав бетонов и результаты испытаний представлены в гл. 3.
Плиты и образцы через 1 сутки после изготовления были вывезены на полигон завода и вплоть до испытаний хранились в условиях воздействия климатической среды.
Плиты из бетона без добавки разрушились под нагрузкой 702 кг/м2, что в 1,87 раз превышает расчётную испытательную нагрузку. Прогиб плиты при контрольной нагрузке по жёсткости на 46,3% превышал допускаемое значение, ширина раскрытия трещин при нагрузке, контрольной по трещиностойкости, равной 250 кг/м2, в 2,2 раза превысила допускаемую.
Плита из бетона без добавки, покрытая плёнкообразующим препаратом К-9, разрушились под нагрузкой 578 кг/м2, что в 1,541 раза превышает расчётную испытательную нагрузку. Прогиб плиты при контрольной нагрузке по жёсткости составил 4,46 мм, что меньше допускаемого значения, ширина раскрытия трещин при нагрузке, контрольной по трещиностойкости, равной 250 кг/м2, в 1,6–2 раза превысила допускаемую.
Плиты из бетона с добавкой ПЯ-01 разрушились под нагрузкой 604,44 кг/м2, что в 1,612 раза превышает расчётную испытательную нагрузку. Прогиб плиты при контрольной нагрузке по жёсткости составил 3,5 мм, что меньше допускаемого значения трещин при нагрузке, контрольной по трещиностойкости, равной 250 кг/м2, не появилось. Из этих результатов следовало, что плита удовлетворяет требованиям проекта.
207
Использование добавки ПЯ-01 увеличило прочность бетона в возрасте 28 суток на 11,6 %, а покрытие пленкообразующим препаратом К-9 – на 10,4 %. Пластификация бетона добавкой ПЯ-01 и защита его препаратом К-9 повысила прочность в том же возрасте на 24 %.
Плиты, изготавливаемые по установившейся на заводе технологии, не удовлетворяли требованиям ГОСТа по жесткости и трещиностойкости. Применение добавки ПЯ-01 и пленкообразующего препарата К-9 улучшило качество плит ПГ, повысились жесткость и соответственно трещиностойкость. Наибольший положительный эффект наблюдается при использовании добавки ПЯ-01 и последующей защите бетона от климатических воздействий пленкообразующим препаратом К-9.
5.3. Технико-экономическая эффективность анализируемых способов смягчения негативного воздействия климата на цементобетон
При подсчете технико-экономической эффективности за базовую принята существующая на заводе ЖБК технология производства плит ПДН. Расчет экономической эффективности произведен в соответствии с указаниями СН 509-78, по которым выявляется экономическая эффективность от внедрения новых технологических процессов, обеспечивающих экономию производственных ресурсов без изменения конструктивных решений.
Сравнивались варианты, представленные в табл. 5.13.
|
Таблица 5.13 |
|
|
Варианты изменения технологий |
|
|
|
|
|
|
Долго- |
Вариант |
Изменение технологии |
веч- |
|
|
ность |
1 |
Существующая технология (базовая) |
20 лет |
2 |
Использование добавки ПЯ-01 без экономии цемента |
17,3 лет |
3 |
Использование добавки ПЯ-01 при экономии цемента |
17,4 лет |
4 |
Использование форсированного режима пропарки |
16,8 лет |
5 |
Защита препаратом К-9 при использовании добавки ПЯ-01 |
20,3 лет |
|
и экономии цемента |
|
6 |
Использование форсированного режима пропарки изделий |
15,2 лет |
|
из бетона с добавкой ПЯ-01 при экономии цемента |
|
208
Таблица 5.14
Изменение технологических параметров
Параметры |
|
Варианты технологий |
|
|||
2 |
|
3 |
4 |
5 |
6 |
|
|
|
|||||
|
|
|
|
|
|
|
Снижение водопотребности |
5 % |
|
15 % |
|
15 % |
15 % |
Снижение расхода цемента |
|
|
10 % |
|
10 % |
10 % |
Увеличение удобоукладываемости |
в 2 раза |
|
|
|
|
|
Сокращение времени термообработки |
|
|
|
4 часа |
|
4 часа |
Дополнительные затраты на покрытие |
|
|
|
|
4 |
|
плёнкообразующим препаратом К-9, руб. |
|
|
|
|
|
|
|
|
|
|
|
|
Изменение технологии по вариантам сопровождается изменением отдельных технологических параметров, которые представлены в табл. 5.14.
Исходные данные для определения экономической эффективности представлены в табл. 5.15.
Таблица 5.15 Исходные данные для расчёта экономической эффективности
Показатель |
Обосно- |
|
Варианты технологий |
|
|||||
вание |
1 |
2 |
3 |
4 |
5 |
6 |
|||
|
|
||||||||
|
|
|
|
|
|
|
|
|
|
Годовой |
объём вы- |
План |
31 550 |
31 550 |
31 550 |
35 715 |
31 550 |
35 715 |
|
пуска плит ПДН, шт. |
|
|
|
|
|
|
|
||
То же, м3 |
|
|
53 000 |
53 000 |
53 000 |
60 000 |
53 000 |
60 000 |
|
Снижение расхода це- |
Тех. |
|
|
30 |
|
30 |
30 |
||
мента на 1 м3 бетона |
процесс |
|
|
|
|||||
Стоимость 1 т цемен- |
Фин. |
2370 |
2370 |
2370 |
2370 |
2370 |
2370 |
||
та, руб. |
|
план |
|||||||
|
|
|
|
|
|
|
|||
Снижение расхода па- |
Тех. |
|
|
|
80,8 |
|
80,8 |
||
ра, кг |
|
процесс |
|
|
|
|
|||
|
|
|
|
|
|
|
|||
Стоимость 1 т пара |
Фин. |
414 |
414 |
414 |
414 |
414 |
414 |
||
план |
|||||||||
|
|
|
|
|
|
|
|
||
Снижение |
трудоза- |
Тех. |
|
|
|
|
|
|
|
трат (чел.·час) формо- |
процесс |
|
0,14 |
|
|
|
|
||
вания 1 м3 изделия |
|
|
|
|
|
|
|
||
Снижение расхода во- |
Тех. |
|
|
|
|
|
|
||
ды (л) на приготовле- |
процесс |
|
7 |
20 |
|
20 |
20 |
||
ние 1 м3 бетона |
|
|
|
|
|
|
|
209
Окончание табл. 5.15
Показатель |
|
Обосно- |
|
Варианты технологий |
|
|||||
|
вание |
1 |
2 |
3 |
4 |
5 |
6 |
|||
|
|
|
|
|||||||
Стоимость 1 м3 воды, |
Бухгал- |
4 |
4 |
4 |
4 |
4 |
4 |
|||
руб. |
|
|
|
терия |
||||||
|
|
|
|
|
|
|
|
|
||
Расход ПЯ-01(кг) |
на |
Тех. |
|
1,27 |
1,27 |
|
1,27 |
1,27 |
||
1 м3 бетона |
|
|
процесс |
|
|
|||||
Стоимость |
ПЯ-01 за |
Бухгал- |
|
10 000 |
10 000 |
|
10 000 |
10 000 |
||
1 т, руб. |
|
|
терия |
|
|
|||||
|
|
|
|
|
|
|
|
|||
Мощность |
вибросто- |
Энерго- |
48 |
48 |
48 |
48 |
48 |
48 |
||
лов, КВт |
|
|
цех |
|||||||
|
|
|
|
|
|
|
|
|||
Экономия заработной |
|
|
|
|
|
|
|
|||
платы |
при |
формова- |
Расчёт |
|
100 |
|
|
|
|
|
нии 1 м3 плит ПДН, |
|
|
|
|
|
|||||
руб. |
|
|
|
|
|
|
|
|
|
|
Экономия |
затрат |
на |
|
|
|
|
|
|
|
|
содержание |
и |
экс- |
Расчёт |
|
500 |
|
|
|
|
|
плуатацию |
оборудо- |
|
|
|
|
|
|
|
||
вания, руб. |
|
|
|
|
|
|
|
|
|
|
Расход К-9 на 1 м3 бе- |
Расчёт |
|
|
|
|
2,2 |
|
|||
тона, кг |
|
|
|
|
|
|
|
|
|
|
Стоимость К-9 за тон- |
Бухгал- |
|
|
|
|
8500 |
|
|||
ну, руб. |
|
|
терия |
|
|
|
|
|
||
|
|
|
|
|
|
|
|
|||
Дополнительные |
за- |
|
|
|
|
|
|
|
||
траты |
на |
нанесение |
Расчёт |
|
|
|
|
4 |
|
|
плёнкообразующего |
|
|
|
|
|
|
|
|||
препарата, руб/м3 |
|
|
|
|
|
|
|
|
||
Основные |
производ- |
Бухгал- |
|
|
|
|
|
|
||
ственные фонды, тыс. |
терия |
84 000 |
84 000 |
84 000 |
84 000 |
84 000 |
84 000 |
|||
руб. |
|
|
|
|
|
|
|
|
|
|
Срок |
службы плит, |
Расчёт |
20 |
17,3 |
17,6 |
16,8 |
20,3 |
15,2 |
||
годы |
|
|
|
|
|
|
|
|
|
|
Расчёт себестоимости изготовления 1 м3 плит ПДН представлен
втабл. 5.16.
1.Сырьё и материалы.
По 2-му варианту увеличение стоимости сырья и материалов соста-
вит
12,7 × 10 – 7 × 0,04 = 12,67 руб.
210