
книги / Производство керамзита
..pdfГЛАВА 4. ПРОМ ЫШ ЛЕННОСТЬ ПО ПРОИЗВОДСТВУ КЕРАМЗИТА
4.1. Основные принципы организации и размещения предприятий по производству керамзита
В СССР в настоящее время действует более 300 ке рамзитовых предприятий самой разнообразной мощно сти: от 10—20 до 100—300 и даже 700—800 тыс. м3 в год.
С вводом в эксплуатацию за последние пятилетия |
боль |
|||
шого числа |
предприятий |
производительностью |
100— |
|
200 тыс. м3 и выше доля маломощных установок |
про |
|||
изводительностью менее 50 тыс. mj в год |
резко |
сни |
||
зилась. |
|
|
|
|
Основным |
обжиговым |
оборудованием |
керамзитовых |
|
предприятий |
все еще являются однобарабанные |
вра |
щающиеся печи, количество которых достигает 527. Их размеры отличаются большим разнообразием от12Х1>2 до 60X3,5. После длительного опытного опробования в настоящее время организуется более широкое внедре ние двухбарабанных печей, разработанных ВНИИстромом им. П. П. Будникова, и однобарабанных печей со слоевыми подготовителями, а также агрегатов СМС-197, разработанных НИИкерамзитом.
Д ля переработки глинистого сырья и приготовления гранулированного материала используется серийно вы пускаемое оборудование: валковые дробилки, кирпичеделательные прессы, глиномешалки, бегуны мокрого по мола, перерабатывающие и формующие дырчатые валь цы и т. д.
Выпускаемый керамзит используется в основном как
материал для изготовления |
стеновых |
керамзитобетон |
|
ных конструкций — панелей |
и |
блоков, |
производство и |
применение которых особенно |
выгодно |
на заполнителе |
с насыпной плотностью в пределах 300—400 кг/м3. На его базе приготовляется, в частности, весьма эффектив ный конструкционно-теплоизоляционный бетон класса В 3,5 плотностью 750—800 кг/м3, который практически не удается получить на аглопорите и шлаковой пемзе.
Однако на практике крайне недостаточен выпуск ке рамзита наиболее эффективных марок с насыпной плот ностью до 350—400 кг/м3 В 1980 г. выпуск наиболее эф фективных марок керамзита до 400 кг/м3 в целом по
стране составил всего 8,6% от 401 до 600 — 69% 0ыше 700 кг/м3 — 13,2 %• К 1983 г. выпуск наиболее эффектив ных марок заполнителя уменьшился. Поэтому самой не отложной задачей является радикальное увеличение до 50—80 % выпуска легких и особо легких марок керамзи та с насыпной плотностью до 350—400 кг/м3.
Хотя развитие производства искусственных порИстых заполнителей в дальнейшем целесообразно осуществлять в первую очередь за счет использования различных от ходов промышленности, все же материалы типа керам зита из природного сырья займут и в дальнейшем до стойное место в балансе их выпуска.
Согласно прогнозам ряда специализированных инсти тутов, предполагается, что выпуск заполнителей типа ке рамзита составит в 1990 г. около 40 млн. м3.
Следует подчеркнуть, что керамзитовая промышлен ность располагает большими, еще не использованными резервами. Несмотря на очевидные успехи в создании промышленности керамзита и продолжающийся рост его производства, технический уровень большого числа дей ствующих керамзитовых предприятий не отвечает дости жениям передового отечественного и зарубежного опыта и реальным возможностям, учитывающим научные до стижения в этой области.
В целом по промышленности отмечаются низкие показатели использования мощностей (около 0,75), боль шие удельные капитальные вложения, крайне недоста точна выработка на одного работающего (около 1200 м3 в год), чрезмерно высока себестоимость 1 м3 заполните
ля. |
Однобарабанные |
печи |
не |
приспособлены для |
|||
получения |
легких |
марок |
заполнителя, в |
которых |
|||
к |
тому |
же расход |
топлива |
на обжиг |
дости |
||
гает 6280—8374 кДж |
на |
1 кг керамзита, что в 2—3 раза |
больше, чем в современных двухбарабанных печах, рабо тающих по прогрессивному ступенчатому способу, раз работанному в СССР.
Особое беспокойство вызывают сравнительно низкие экономические показатели не только на предприятиях малой мощности, но даже на таком крупнейшем заводе,
как Лианозовский |
мощностью 800 тыс. м3 |
в год, где вы |
|||
работка на 1 |
работающего |
составляет |
всего |
около |
|
3500 м3, тогда, |
как, |
например |
на Волгоградском |
заводе |
с двухбарабанными печами, с меньшей в 3 раза мощ ностью (250 тыс. м3 в год), достигнута выработка
6000 м3 в год. Таким образом, одного механического уве личения мощности предприятий еще недостаточно для значительного повышения технического уровня и техни ко-экономических показателей производства, если при меняемая технология, а также тип и мощности обору дования остаются без изменений.
В обзорной работе сотрудников НИИкерамзита [100] дана технико-экономическая характеристика рабо ты действующих керамзитовых предприятий, а также намечены основные направления снижения насыпной плотности керамзитового гравия: создание оптимальных условий переработки глинистого сырья и формовки сыр цовых гранул; совершенствование процесса сушки и об жига; обеспечение требований по прочности зерновому составу и однородности свойств керамзитового гравия; экономия топлива, использование вторичных энергоре сурсов и др.
Результаты выполненных в СССР научных исследо ваний по изысканию новых более эффективных способов производства и нового оборудования для производства керамзита настоятельно требуют быстрейшего внедре ния ступенчатого способа изготовления керамзита в двухбарабанных печах, печах кипящего слоя, кольцевых и других проверенных агрегатах.
Целесообразность постройки в том или другом райо не керамзитовых предприятий подлежит тщательному экономическому обоснованию.
Выбор вида заполнителя и мощность предприятия. Постановка и решение вопросов, связанных с возможной организацией производства керамзита, производятся при установленной потребности в пористых заполнителях для изготовления армированных и неармированных лег кобетонных изделий и конструкций. В связи с более вы сокой стоимостью керамзита по сравнению с легкими природными и шлаковыми заполнителями при наличии качественных природных и шлаковых пористых запол нителей или возможности их получения из отходов про мышленности (шлаковая пемза) строить керамзитовые предприятия экономически нецелесообразно.
Для решения вопроса о постройке керамзитового предприятия важно выявить полную потребность в за полнителях всех потребителей данного района с тем, что бы определить оптимальную его мощность. Чем больше мощность керамзитового предприятия, тем ниже будет
себестоимость выпускаемой продукции. Высокая техни ко-экономическая рентабельность производства керамзи та достигается при мощности предприятия 100— 200 тыс. м3 в год и более. При этом годовую мощность керамзитовых предприятий рекомендуется устанавли вать по производительности их основного оборудова н ия— печей и механизмов для обжига керамзита.
Выбор места постройки керамзитового предприятия. Обязательным условием решения о постройке керамзи тового предприятия в данном районе является наличие местного доброкачественного глинистого сырья для из готовления керамзита. Поэтому выбору места постройки керамзитового предприятия и его проектированию долж ны предшествовать выявление и испытание местного гли нистого сырья с установлением технологических пара метров заводского изготовления керамзита, а также ут верждение запасов сырья территориальной комиссией по запасам.
Сырье испытывают в лабораторных и полузаводских условиях. Так как районы постройки керамзитовых пред приятий обычно располагают не одним, а несколькими разновидностями глинистого сырья, обладающего раз личной склонностью к вспучиванию, и поскольку каче ство исходного сырья оказывает решающее влияние на эффективность производства и применения керамзита, важно выявить и испытать лучшие из имеющихся раз новидностей. Поэтому в лабораторных условиях испы тывают возможно большее количество проб, характери зующих сырье различных месторождений данного райо на. В заводских же условиях испытывают одну-две про бы сырья, показавших наилучшее вспучивание и другие благоприятные показатели при лабораторных исследо ваниях.
При полном цикле лабораторных испытаний сырья устанавливают и определяют: влажность в естественном состоянии: однородность и характер структуры глини стой породы: засоренность каменистыми, известковистыми и другими включениями; вспучиваемость; интервал вспучивания, огнеупорность; размокаемость; пластич ность; гранулометрический, минералогический и валовой химический состав, включая щелочи и органические при меси, а также плотность полученного керамзита. Осо бое внимание при этом обращается на возможное улуч шение качества сырья корректированием его состава же
лезистыми, органическими и другими добавками (иприт ные огарки, ССВ, соляровое масло, болотная руда, неф тешлам и др.).
При полузаводских испытаниях сырья опытным путем выявляются и устанавливаются наиболее эффективные методы его переработки, гомогенизации и изготовления гранулированного полуфабриката: технологические па раметры тепловой обработки материала перед обжигом; оптимальные параметры обжига и охлаждения керамзи та; качественная характеристика керамзита (плотность, морозостойкость, прочность, влагопоглощение), а также плотность и прочность керамзитобетона на основе опыт ной партии заполнителя.
Результаты заводских испытаний, а также испыта ния керамзита в бетоне в совокупности с данными ла бораторных исследований составляют основу рекоменда ций для проектирования керамзитового предприятия на базе испытуемого сырья.
Испытания сырья проводят в соответствии с «Указа ниями по испытанию сырья для производства керамзи тового гравия» в организациях, располагающих необхо димым опытом и оборудованием (ВНИИстром, НИИкерамзит, НИИСМИ УССР, НИИСМ БССР).
Привязка керамзитового предприятия. Определяющи ми факторами при выборе конкретного места постройки и привязки керамзитового гравия являются: близость к источнику сырья и удобства его доставки, а также бли зость строящегося предприятия к потребителям керам зита и удобства доставки его к ним.
В зависимости от местных условий керамзитовое про изводство может быть организовано: в виде цеха при заводах железобетонных изделий и домостроительных комбинатах. Технико-экономическая целесообразность такого размещения определяется близостью к потреби телям и возможностью подключения технологического потока производства керамзита к технологическому по току изготовления керамзитобетонных конструкций, коо перации по использованию части оборудования, а также объединением управления; в виде цеха при керамиче ских заводах. Целесообразность такого размещения пре допределяется родственностью технологии, возмож ностью кооперирования по использованию оборудования, ремонтных цехов и объединением управления; как само стоятельного предприятия, что экономически может быть
оправдано лишь при постройке керамзитового завода большой мощности.
Проектная организация при привязке керамзитового предприятия, используя действующие типовые проекты, изучает и учитывает местные условия и вносит в проект необходимые коррективы. Особенно важно учесть разно образнейшие особенности местного глинистого сырья, его способности к переработке, грануляции и вспучиванию, а также климатические условия, что может потребовать изменения закладываемого в проект оборудования и ком поновочных решений.
Основные требования к проектам керамзитовых пред приятий. Важнейшими требованиями к типовым и инди видуальным проектам керамзитовых предприятий, ко торые будут строиться в ближайшие годы, являются, безусловно, обязательная предварительная проверка на надежность работы закладываемого в проектах основно го оборудования; полная механизация и высокая сте пень автоматизации производственных процессов с по следующим переходом на автоматизированные линии по производству керамзитового гравия и песка; оптималь ная мощность для районов сосредоточенного строитель
ства 300—600 тыс. м3 и выше, |
а для |
остальных |
райо |
||||
нов и сельского |
строительства |
100—300 |
тыс. м3 |
в год; |
|||
оснащение |
керамзитовых |
предприятий |
высокопро |
||||
изводительным |
специально |
|
приспособленным |
для |
|||
производства |
керамзита |
оборудованием: двухбара |
|||||
банными |
печами, печами |
|
кипящего |
слоя, |
корот |
||
кими однобарабанными печами с |
проверенными в |
работе на надежность запечными теплообменниками, хо лодильниками с регулируемым режимом охлаждения и максимальным использованием теплоты для возврата в печь, равновеликой мощности перерабатывающего, гра нулирующего и другого оборудования; переработка сырья в одну смену с хранением глины в гомогенизато рах при круглосуточной работе узлов грануляции, обжи га, охлаждения и сортировки (для технологической ли нии с двухбарабанной печью); снижение расходов теп лоты на обжиг керамзита до 2512—2930 кДж/кг; ради кальное повышение технико-экономической эффектив ности производства керамзита.
4.2. Заводы по производству керамзита
Бескудниковский комбинат строительных материалов. В начале 50-х годов в Бескудникове (Москва) построен первый в стране цех керамзитового гравия, работающий по технологии, разработанной нами в Институте строи тельной техники. Ныне мощность комбината составляет 700 тыс. м3 керамзита в год. Особенно оригинальной компоновкой отличается новый цех керамзитового гра вия № 12 производительностью 400 тыс. м3 в год, пост роенный в 1963 г. по проекту Мосгипростройиндустрии (рис. 60).
Важная особенность технологии Бескудниковского комбината состоит в том, что здесь успешно использу ются обычные местные слабовспучивающиеся суглинки. Полезная толща бескудниковских покровных суглинков составляет обычно 1,5—4,5 м. Характеристика одной из проб бескудниковского суглинка приведена в табл. 23. Основными глинообразующими минералами суглинка являются гидрослюда, гидрохлорит с небольшой при месью монтмориллонита. Содержание свободного квар ца колеблется в пределах 35—47 %, но в лучших раз ностях не превышает 40—43 %. Число его пластичности 8— 10.
В природном состоянии бескудниковский суглинок
вспучивается слабо, коэффициент |
вспучивания 1,7— |
2,1, а плотность 0,9— 1,2 г/см3. При |
добавке же органи |
ческих веществ, а особенно совместно железистых и ор ганических добавок (пирита, болотной и железной ру ды, солярового масла, мазута и т. д.), вспучиваемость его резко возрастает, достигая коэффициента вспучива ния 3—4 и плотность в куске 0,65—0,85 г/см3.
По предложению В. Я. Хайкина и И. С. Окунева, Бескудниковский комбинат строительных материалов и конструкций первым в стране опробовал в производст венных условиях и внедрил способ повышения вспучи ваемое™ местных слабовспучивающихся суглинков сов местным вводом в исходное сырье железистых и органи ческих добавок. Творческий подход к внедрению этого важного мероприятия обеспечил перевод в короткие сро ки всех вращающихся печей комбината на выпуск легко го керамзита с насыпной плотностью 400—500 кг/м3.
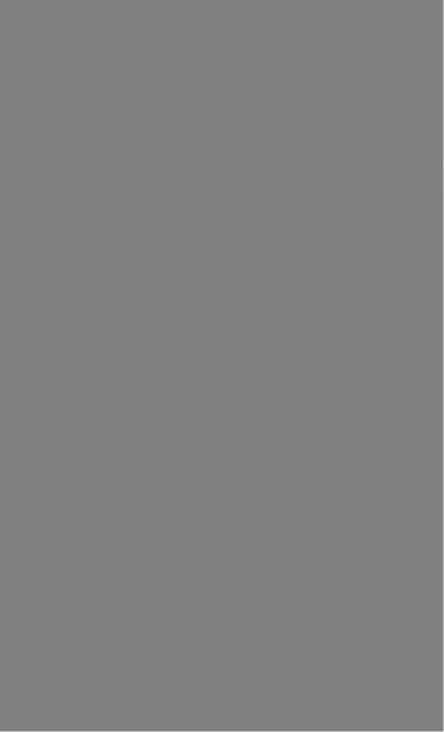
■Фракции
суглинка
о |
о |
о |
о |
о |
< |
|
V |
н |
|
со |
|
tu |
МпО
о |
о |
О |
о |
о |
CQ |
ьс |
£ |
а |
|
о |
|
|
со |
ппп |
Сумма |
Органические примеси |
Коэффициент вспучива ния |
Природный |
71,82 |
13,62 |
3,99 |
0,89 |
0,53 |
0,53 |
1,02 |
0,93 |
2,42 |
1,33 |
0,07 |
3,35 |
100,5 |
0,26 |
0,95 |
1,9 |
Менее |
58,68 |
20,88 |
7,35 |
0,9 |
0,53 |
0,64 |
0,58 |
1,7 |
2,19 |
0,75 |
0,06 |
6,19 |
100,45 |
0,54 |
0,48 |
3.8 |
0,01 мм |
|
|
|
|
|
|
|
|
|
|
|
|
|
|
|
|
Менее |
53,19 |
21,8 |
9,11 |
0,78 |
0,7 |
0,7 |
0,53 |
2,24 |
2,63 |
1,04 |
0,06 |
7,58 |
100,36 |
0,88 |
0,38 |
4.9 |
0,005 мм |
|
|
|
|
|
|
|
|
|
|
|
|
|
|
|
|
Менее |
51,14 |
23,96 |
10,16 |
0,8 |
0,72 |
0,72 |
0,23 |
1.9 |
1,77 |
0,41 |
Следы |
8,77 |
100,52 |
1,23 |
0,25 |
6,5 |
0,001 мм |
|
|
|
|
|
|
|
|
|
|
|
|
|
|
|
|
Рис. 61. Технологическая схе ма производства керамзита в цехе № 12 Бескудниковского
комбината строительных мате
риалов и конструкций |
2--кам |
|||||
/ —ящичный подаватель; |
||||||
невыделительные вальцы, |
3 —двух- |
|||||
вальная глиномешалка; 4 —дырча |
||||||
тые вальцы; 5 —сушильный |
бара |
|||||
бан; |
6 |
—бункер |
сырца; |
7 |
лен |
|
точный |
|
питатель; |
|
8 —пылеосадн* |
||
тельная |
камера; |
9 —вращающаяся |
||||
печь; |
10 —барабанный |
холодиль |
||||
ник; 11 |
—элеваторы; |
12 —вентиля? |
||||
торы; |
13 —циклоны; |
14 —дробиль |
||||
но-сортировочное |
отделение; |
15 — |
||||
склад готовой продукции; |
15 |
лс |
||||
точные |
конвейеры |
|
|
|
работающий на отходящих газах, подсушивает материал для двух вращающихся печей. Подсушенные гранулы подаются элеваторами наверх в расходные бункера для питания печей. Загрузку вращающихся печей ведут дис ковыми питателями диаметром 2000 мм с двумя выхо дами.
Керамзит обжигают природным газом в четырех вра щающихся печах длиной 40 м и диаметром 2,5 м. После отвердевания керамзитовый гравий поступает в барабан ные холодильники размером 22X2,3 м, установленные под печами, для охлаждения до 50—70 °С.
На сортировку и склад керамзитовый гравий отбира ют системой конвейеров и элеваторов. Помимо закрыто го силосного склада предусмотрена открытая благоуст роенная площадка для хранения керамзита.
На основе выпускаемого легкого керамзита Бескуд никовский комбинат строительных материалов и конст рукций изготовляет эффективные керамзитобетонные конструкции, в том числе панели наружных стен с плот ностью керамзитобетона 900— 1000 кг/м3, хорошо заре комендовавшие себя при постройке многоэтажных зда ний в Москве.
Пример выпуска в течение многих лет легкого ке рамзитового гравия из суглинков свидетельствует о ре альной возможности использования этого вида местно