
книги / Реконструкция подземного пространства
..pdfнагнетаются через один и тот же инъектор. Раствор силиката натрия вводится
вгрунт заходками 1 м по глубине при погружении инъектора. Затем такими же заходками, но уже в процессе извлечения инъектора производится нагне тание второго раствора. Радиус закрепления грунта составляет 30-100 см. Процесс гелеобразования протекает очень быстро. После полного твердения геля, на что требуется 28 дней, закрепленный песчаный грунт приобретает прочность на одноосное сжатие 2-5 МПа.
При закреплении мелких песков и плывунов, имеющих коэффициент фильтрации в пределах 0,5-1,0 м/сут, в грунт нагнетается подготовленный за ранее гелеобразующий раствор, представляющий собой смесь растворов крепителя и о : пердителя. Варьируя состав отвердителя, можно регулировать
вшироких и) .делах (от 20-30мин до 10-16ч) время гелеобразования. Для
обеспечения обходимого радиуса закрепления в малопроницаемых грунтах применяются рецептуры с большим временем гелеобразования.
Прочность гелей кремниевой кислоты по однорастворным рецептурам невелика. Закрепленные ими пески и плывуны приобретают прочность на одноосное сжатие порядка 0,2 МПа, за исключением кремнефторсиликатной рецептуры, придающей прочность до 2-4 МПа, и силикатно-органических рецептур.
Силикатизация эффективна для закрепления макропористых лессовых грунтов вследствие их высокой проницаемости. Особенностью силикатиза ции лессов является то, что в состав этих грунтов входят соли, выполняющие роль отвердителя жидкого стекла. Поэтому силикатизация лессов проводится классическим однорастворным методом, осуществляемым инъекцией в тол щу лессовых грунтов раствора силиката натрия. Процесс закрепления проис ходит мгновенно, прочность растет очень быстро и может достигать для за крепленного массива 2 МПа и более. Закрепление водоустойчиво, что обес печивает ликвидацию просадочных свойств.
В нашей стране по предложению В.Е.Соколовича применяют газовую силикатизацию песчаных и макропористых лессовых грунтов, основанную на использовании в качестве отвердителя жидкого стекла углекислого газа (ди оксида углерода). Технология способа состоит в том, что в грунт через заби тые инъекторы или специально оборудованные скважины нагнетается угле кислый газ для предварительной активизации грунта, затем раствор силиката натрия и вторично углекислый газ для отверждения. Прочность закреплен ных методом газовой силикатизации песков составляет 0,8-1,5 МПа, лессо вых грунтов - 0,8-1,2 МПа.
Для сплошного закрепления массива грунта инъекторы располагают в шахматном порядке. Уточнение технологической схемы и параметров закре пления производится путем проведения опытных работ. Качество закрепле ния грунтов проверяют бурением контрольных скважин с отбором кернов, вскрытием шурфов с отбором образцов, определением удельного водопоглощеиия, методами электрокаротажа и зондирования.
Слюпизация. Метод закрепления грунтов смолами получил название смолизации. Сущность его заключается во введении в грунт высокомолеку лярных органических соединений типа карбамидных, фенолформальдегидных и других синтетических смол в смеси отвердителями-кислотами, кислыми соля ми.
Через определенное время в результате взаимодействия с отвердителями смола полимеризуется. Обычное время гелеобразования 1,5-2,5 ч при времени упрочнения до 2 сут. Метод смолизации рекомендуется для за крепления сухих и водонасыщенных песков с коэффициентом фильтрации 0,5-25 м/сут. Прочность на одноосное сжатие закрепленного карбамидной смолой песка колеблется в пределах 1-5 МПа и зависит в основном от кон центрации смолы в растворе.
Организация работ по закреплению грунтов смолами аналог ична орга низации работ по силикатизации. Радиус закрепленной области основания со ставляет 0,3-1,0 м в зависимости от коэффициента фильтрации песка. Метод относится к числу дорогостоящих. Закрепление карбамидными смолами ус пешно применялось при строительстве Новолипецкого завода, Харьковского метрополитена.
В последние годы появились работы с предложениями о возможности создания нетоксичных либо слаботоксичных составов для закрепления грун та с использованием карбамидных смол. Указывается, что при соблюдении предлагаемых технологически сложных приемов можно снизить канцерогенность этих смол. В связи с усиленным вниманием к охране окружающей сре ды необходимо более строго подходить ко всем рекомендуемым «универ сальным» химическим реагентам. Так, несомненно вредное воздействие на окружающий незакрепленный грунт и подземные грунтовые воды широко рекомендуемых кислот и щелочей высокой концентрации. Специальными исследованиями В.Е.Соколовича во НИИОСПе были выявлены токсичность и экологическая несостоятельность целого ряда реагентов, рекламируемых для закрепления грунтов в условиях реконструкции, в частности, акриловых, фенольно-формальдегидных, фурановых, хромлигниновых и карбамидных смол с несвязным формальдегидом.
В рекомендациях по укреплению водонасыщенных слабых грунтов за щелачиванием (Уфа, НИИпромстрой) предлагается нагнетать под давлением в слабые пылевато-глинистые грунты концентрированные растворы каусти ка. Предполагается, что под воздействием высококонцентрированного кау стика произойдет частичное поверхностное растворение глинистых минера лов с образованием щелочных алюмосиликатных гелей, способных надежно закреплять слабые грунты. Расчет указывает на чрезмерное количество опас ного реагента на 1 м3 закрепляемого глинистого грунта (от 100 до 160 кг), Под небольшое общежитие в Нижнем Новгороде необходимо закачать 300 т каустической соды. Учитывая высокий уровень грунтовых вод, помимо всего прочего, можно ожидать подщелачивания вод. Сам автор Ф. Е.Волков отме
чает, что «защелачивание глинистых грунтов сопровождается их активным химическим пучением, приводящим к сильным деформациям сооружений, возведенных на таких грунтах».
Глинизация и битумизация. Глинизацию применяют для уменьшения водопроницаемости песков. Технология глинизации заключается в нагнета нии через инъекторы, погруженные в песчаный грунт, водной суспензии бен тонитовой глины с содержанием монтмориллонита не менее 60%. Глинистые частицы, выпадая в осадок, заполняют поры песка, в результате чего его во допроницаемость снижается на несколько порядков.
Битумизацию применяют в основном для уменьшения водопроницае мости трс1.г* ! шоватых скальных пород. Метод сводится к нагнетанию через
скважины |
трещиноватый массив расплавленного битума или специальных |
битумных |
.ульсий. При этом происходит заполнение трещин и пустот, и |
массив с п. |
«штся практически водонепроницаемым. |
Электрохимическое закрепление грунтов. Метод применяют для закре пления водонасыщенных пылевато-глинистых грунтов в сочетании с элек троосмосом. В этом методе через аноды в грунт подают водные растворы со лей многовалентных металлов, которые, соединяясь с глинистым грунтом, коагулируют глинистые частицы. Создаются глинистые агрегаты, сцементи рованные между собой гелями солей железа и алюминия. При этом проч ность грунтов существенно возрастает, резко снижается их способность к на буханию (рис.3.49).
Рис.3.49. Электрохимическое за крепление слабых грунтов в ос новании фундаментов: 1-6 - но мера захваток
Напряжение тока при электрохимическом закреплении составляет 80100 В, плотность тока 5-7 А/м2, расход энергии 60-100 кВтч на 1 м3 закреп ляемого грунта.
Химическое закрепление грунтов позволяет успешно решать многие задачи реконструкции при достаточно сложных инженерно-геологических условиях. Приведем характерный пример из практики работ в г. Петербурге. В 1959-60 гг. для предотвращения аварийных осадок стен сценической части здания Мариинского театра было выполнено химическое закрепление грун тов в основании ленточных фундаментов. Закреплению подлежал песок пы леватый с коэффициентом фильтрации 0,5-1,5 м/сут и пористостью п = 0,44. Толща песков составляла 3-4,5 м ниже подошвы фундамента. Закрепление производили по традиционной схеме с использованием карбамидной смолы плотностью 1,076-1,08 г/см3 и 3% раствора соляной кислоты.
Вначале нагнетали раствор соляной кислоты (400 л), затем - 50 л воды и после этого - раствор смолы (400 л). Нагнетание осуществлялось плунжер ными насосами ПСБ-4 и НР-3 при давлении 0,3 МПа. Объем одной заходки, приходящейся на 1 инъектор, составил 0,6-0,7 м3
Термическое закрепление грунтов. Применяют для упрочнения мало влажных пылевато-глинистых грунтов, обладающих газопроницаемостью. Наиболее часто этот метод используется для устранения просадочных свойств макропористых лессовых грунтов. Глубина закрепляемой толщи достигает 20 м.
Сущность метода термической обработки заключается в том, что через грунт в течение нескольких суток пропускают раскаленный воздух или рас каленные газы. Под действием высокой температуры отдельные минералы, входящие в состав скелета, оплавляются. В результате этого образуются прочные водостойкие структурные связи между частицами и агрегатами грунта. Кроме того, при обжиге грунты теряют значительную часть химиче ски связанной воды, что изменяет свойства грунтов и уменьшает или полно стью ликвидирует просадочность, размокаемость, способность к набуханию.
Температура газов, которыми производится обработка грунта, не должна превышать 750...850°С. Если температура газов окажется выше, стенки скважин оплавляются и становятся газонепроницаемыми. При температурах ниже 300°С ликвидация просадочности лессов не происходит.
Существуют различные способы, оборудование и технологические схемы термического закрепления. Одна из технологий заключается в следующем (рис.3.50): пробуривают скважины диаметром 100...200 мм, которые закры вают специальными керамическими затворами. В затворе оборудуется каме ра сгорания, к которой подают топливо (горючие газы, соляровое масле, нефть и т. п.) и воздух под давлением. Для обеспечения заданной температу ры обжига необходимо, чтобы количество воздуха, нагнетаемого в скважину, было не меньше установленной величины.
Для поддержания температуры 750...850°С расход воздуха на 1 кг го
рючего составляет 34...39 м3 При указанном количестве воздуха и средней газопроницаемости грунта порядка 25 м3/ч количество сгораемого горючего на 1 м длины скважины не должно превышать 0,85 кг/ч. Термическая обра ботка производится непрерывно в течение 5..Л2 сут. После обработки сква жины аппаратуру затворов снимают и переставляют на скважины следующе го участка. В результате термической обработки получается упрочненный конусообразный массив грунта диаметром поверху 1,5...2,5 м, а понизу на глубине 8... 10 м около 0,2...0,4 диаметра поверху.
Рис.5 Установка для обжига прос':. '.очного грунта: 1 - ком прессор; 2 - трубопровод для холодного воздуха; 3 - ем кость для жидкого горючего; 4
-трубопровод для горючего; 5
-фильтр; 6 - насос для подача горючего под давлением в скважину; 7 - форсунка; 8 - затвор с камерой сгорания; 9 - непросадочный грунт; 10 - зона термического упрочнения грунта; 11 - скважина; 12 - просадочный лессовый грунт
Образуется как бы коническая свая из обожженного непросадочного грунта с прочностью до 10 МПа. Каждая такая свая вследствие понижения температуры по мере удаления от скважины окружена оболочкой просадочного грунта в пределах зоны температур ниже 300°С.
Применяется также другая технология, которая позволяет сжигать топ ливо в любой по глубине части скважин, в том числе и в нижней части. В ре зультате этого можно создавать обожженные грунтовые массивы (термосваи) постоянного сечения, с уширением внизу или вверху. Сроки обжига в этом случае несколько сокращаются, упрощается технология работ.
Способ состоит в том, что по длине скважины передвигается камера сгорания, позволяющая обжигать грунт на любом участке скважины. Участок обжига отделяется от остальной части скважины жароупорными диафрагма- ми-отсекателями. Так, при применении жидкого или газообразного топлива форсунка для его сжигания устанавливается в верхней части передвижной
камеры сгорания непосредственно под нижней регулируемой раздвижной диафрагмой.
Грунты обжигают в виде отдельных грунтостолбов под фундаменты ко лонн промышленных цехов или гражданских зданий, а в некоторых случаях производят обжиг грунтового массива в основании всего здания. В этом случае грунтостолбы размещают таким образом, чтобы обожженные упрочненные зо ны соприкасались между собой.
Контроль процесса термического закрепления сводится к определению количества тепла, которое прошло через скважину в окружающий грунт. По сле окончания работ отбирают образцы закрепленного грунта на различном расстоянии от скважины и испытывают их в лабораторных условиях. При термическом закреплении массива в виде отдельных термосвай рекомендует ся проведение опытного закрепления с испытанием термосвай статической нагрузкой. При сплошном обжиге грунтов в основании, когда грунтостолбы соприкасаются друг с другом, испытывают обожженный массив штампами площадью не менее 10000 см"
Метод предварительного замораживания грунтов применяется при откопке котлованов, опускных колодцев, проходе шахтных стволов и тонне лей в водонасыщенных плывунных грунтах. К достоинствам метода относят ся: полное устранение водопритока и исключение опасности прорыва плыву нов; к недостаткам - трудность разработки мерзлого грунта, высокая стои мость замораживания, отрицательная температура в забое.
Для охлаждения и замораживания грунта пробуриваются скважины, которые оборудуются замораживающими колонками. По питающей трубе диаметром 25-50 мм в колонку подается охлаждающий раствор. Поднимаясь по внешней трубе диаметром 100-114 мм, он отнимает теплоту у грунта. В качестве охлаждающего раствора чаще всего применяется водный раствор (рассол) хлористого кальция с плотностью 1,23-1,25 г/см3, температура за мерзания которого равна -28-к35°С.
Рассол выполняет функцию переносчика холода: в замораживающих скважинах он отнимает тепло у грунта, а на замораживающей станции отдает тепло, охлаждаясь сам. Получение низких температур на замораживающих станциях основано на принципах испарения кипящих при низкой температу ре жидкостей - хладоагентов (аммиак, углекислота, фреоны). На холодиль ных установках в качестве хладоагентов чаще всего используется аммиак. Переход аммиака в газообразное состояние (испарение) происходит в испа рителе. Тепло для испарения аммиак получает от рассола. Из испарителя па ры аммиака всасываются компрессором при температуре -25 °С и давлении 0,155 МПа. Сжатый горячий газообразный аммиак поступает в конденсатор, где охлаждается водой до +15^20°С и переходит в жидкое состояние. Из конденсатора под давлением 0,8-1,0 МПа аммиак направляется к испарите лю, на входе которого стоит дроссель для понижения давления с 0,8-1,2 МПа до 0,155 МПа. Аммиак закипает, температура его падает, и цикл повторяется.
Вторым замкнутым циклом на холодильных установках является движение рассола. Из замораживающих скважин рассол поступает нагретым на 3-5°С.
Рис.3.51 .Замораживающая колонка: 1 - башмак; 2 - питательная труба; 3 -диафрагма; 4 - отводящая трубка; 5 - замораживающая труба
Третьим замкнутым циклом на холодильной установке является дви жение воды для охлаждения. Отнимая тепло у горячего аммиака в конденса торе, она охлаждается в градирне или водоеме.
Для нормального протекания процесса замораживании грунта холодопроизводительность установки должна быть порядка 250 ккал/ч на каждый квадратный метр площади боковой поверхности замораживающих колонок. Таким образом, для 100 колонок глубиной по 20 м необходимая хладопроизводительность составляет
Q = ndl • 100 • 250 = 3,14 • 0,1 • 20 • 100 • 250 = 157000 ккал/ч. |
(3.1) |
Серийно выпускаемые замораживающие установки имеют производи тельность от 60 до 400 тыс. ккал/ч. Радиальная скорость нарастания ледог рунтового цилиндра вокруг скважин составляет в среднем в песках -2,5 см/сут, в глинах -1-1,5 см/сут. Замораживающие скважины располагают
на расстоянии друг от друга 0,9-1,2 м; таким образом, теоретически за 20-30 дней образуется сплошная, водонепроницаемая, прочная ледопородная стена. Практически промораживание ведут не менее двух месяцев. После этого холодопроизводительность может быть снижена до 30-40% от первоначальной; этого достаточно для поддержания грунта в замороженном состоянии.
В интервале температур -Ю ...-20°С предел прочности льда на сжатие составляет 2,0-4,0 МПа, глины - 7-15 МПа. При расчетах ледогрунтовых стенок на прочность величина расчетного сопротивления принимается -25% от предела прочности (табл.3.5), так как льдистые грунты при напряжениях свыше этого уровня проявляют значительную ползучесть.
|
|
|
|
Таблица 3.4 |
|
Грунт |
Предел прочности (МПа) при температуре, V |
||||
от -1до -5 |
от-5 до-10 |
от-Юдо -5 |
от -1 до -20 |
||
|
|||||
Песок |
2,5-8,5 |
8,5-12,7 |
12,7-14,4 |
14,4-15,2 |
|
Супесь |
2,0-6,5 |
6,5-8,5 |
8,5-10,5 |
10.5-12,2 |
|
Суглинок и глина |
1.5-4,5 |
4,5-6,0 |
6,0-7,5 |
7,5-9,0 |
|
Илы |
1,0-1,5 |
1,5-3,5 |
3,5-4,5 |
4,5-6,5 |
|
Лед |
- |
- |
1,3-1,8 |
1,8-2,0 |
|
|
|
|
Толщина стенки замороженного грунта 5 (м) определяется расчетом на давление воды и давление грунта во взвешенном состоянии. При кольцевой форме стенки в плане и осесимметричной гидростатической нагрузке расчет выполняют по формуле Ломе
R |
\ |
(3.2) |
|
-1 , |
|||
8 = 0,6DB |
|||
\ R - 2 p |
) |
|
где D6 - внутренний диаметр ледопородной стенки, м; R - расчетное сопро тивление на сжатие мерзлого грунта, МПа; р - суммарное расчетное давле ние воды и грунта на ледопородную стенку на уровне дна котлована, МПа.
В мировой практике существует богатый арсенал различных химиче ских реагентов, способных закрепить грунт основания на достаточно дли тельный период. К достоинствам химических способов относятся: высокая степень механизации всех операций; возможность упрочнения грунтов до за данных проектом параметров в их естественном залегании; сравнительно ма лая трудоемкость, резкое сокращение ручного неквалифицированного труда по откопке траншей, а также сравнительно невысокая стоимость исходных материалов (возможность использования отходов производства) (рис.3.52). В начале 60-х гг. для улучшения свойств грунтов основания широко использо вался кубовый остаток - отход производства кремнийорганических соедине ний (этилсиликат натрия). Были укреплены грунты в основании фундаментов здания тяговой подстанции трамвая в г. Усолье-Сибирское Иркутской облас ти. Деформации этого относительно легкого здания произошли из-за нерав номерных поднятий силами морозного пучения и соответствующих просадок
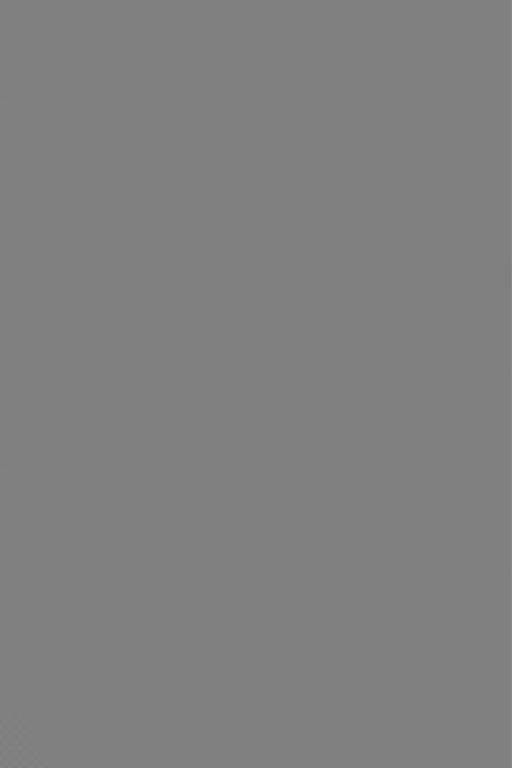
по
Наиболее распространенные конструкции анкеров изображены на рис.3.54. Грунтовые анкеры применяют в промышленном, гражданском, транс портном и гидротехническом строительстве. Их используют для закрепления ог раждений котлованов, стен подземных сооружений, опускных колодцев, откосов и склонов, фундаментов дымовых труб, мачт и башен и т. д.
Рис.3.54. Применение анкерных устройств: а) крепление котлована; б) крепление днища и стенок дока или шлюза; в), г) восприятие выдергивающих сил в фунда ментах дымовых труб и мачт ЛЭП; д) крепление откоса; е) усиление подпорной стенки; ж) крепление свода подземного перехода; з) противодействие взвешиваю щему давлению грунтовой воды на тоннели; и) восприятие опрокидывающего мо мента от перекрытия ангара