
книги / Расчёт и проектирование систем обеспечения безопасности.-1
.pdfнеизменной в процессе фильтрации и регенерации, улучшает использование рабочего объема фильтров и дает возможность использовать интенсивные способы регенерации ткани, которые невозможны в бескаркасных фильтрах.
Однако жесткокаркасные элементы обладают рядом недостатков:
–повышенная металлоемкость и трудоемкость изготовления;
–усложнениеобслуживанияфильтров(особеннопризаменерукавов);
–ускорение износа ткани в местах контакта с каркасом из-за трения
ометалл, что исключает использование стеклоткани;
–для нецилиндрических фильтрующих элементов – сложность раскроя и пошива фильтрующего материала, закрепления и герметизации его краев на каркасе;
–необходимость выполнения съемными стенки жесткокаркасных фильтров, что затрудняет герметизацию корпуса.
По системе регенерации
Впромышленных фильтрах регенерацию проводят по двум основным принципам:
–изменение направления хода газа через фильтровальный материал обратная продувка, во время которой происходит выдувание уловленной пыли из рукавов;
–разрушение пылевого слоя на фильтровальном материале его деформацией различными способами – встряхиванием рукавов с использованием специальных механизмов, воздействием на ткань аэродинамических сил извуковых импульсов.
Кроме того, существуют еще два способа регенерации:
а) фильтры с посекционной системой регенерации, когда регенерации подвергается целая секция многосекционного фильтра, во время которой подачу газа отключают;
б) в фильтрах с поэлементной системой регенерации обратной продувке подвергают последовательно отдельные фильтрующие элементы или их группы.
Конструктивное исполнение фильтров этой группы сложнее, чем у первой, из-за введения каркасных элементов и устройства сложных подвижных систем.
Однако они имеют и свои преимущества, а именно: более интенсивную регенерацию и меньшую ее продолжительность; регенерация ткани осуществляют безотключения подачи газа в фильтр.
101
По типу устройств регенерации
Фильтры с посекционной регенерацией выполняют двух основных типов:
–с обратной продувкой;
–с комбинированной регенерацией (продувка и встряхивание). Для небольших фильтров применяют только встряхивание. Фильт-
ры с поэлементной регенерацией бывают:
–с импульсной регенерацией;
–с обратной продувкой через подвижное сопло;
–с обратной струйной продувкой.
Осаждение пыли на твердых элементах фильтра называют стационарной фильтрацией, а очистку газа в слое пыли, уже осевшей в по-
рах фильтра, нестационарной.
Стационарная фильтрация осуществляется в фильтрах, работающих при очень низких концентрациях аэрозолей. Нестационарная фильтрация, по существу, проходит во всех случаях очистки газов.
При стационарной фильтрации гидравлическое сопротивление и эффективность очистки газов не изменяются во времени и по величине определяются только структурой фильтровального материала, характеристиками пыли и параметрами газа. При нестационарной фильтрации и сопротивление фильтра, и эффективность очистки возрастают по мере накопления пыли в фильтровальном материале.
Эффективность очистки газа в тканевых и пористых фильтрах определяется взаимодействием взвешенных в газе частиц с отдельными элементами фильтра и зависит от характеристик частиц пыли и элементов фильтрующего материала, параметров газа и скорости фильтрации.
Поскольку все факторы, влияющие на эффективность, трудно учесть, то ее определяют опытным путем, однако в ходе экспериментов установлено, что влияют они на этот показатель следующим образом:
1)чем крупнее частицы пыли и больше их плотность, тем эффективнееониосаждаются поддействием сил инерцииигравитационных сил;
2)частицы размером менее 0,3 мкм осаждаются на твердых элементах пористого материала в основном только под действием теплового движения газовых молекул;
3)чем больше размеры твердых элементов пористого материала, тем выше эффективность осаждения частиц пыли;
4)чем меньше размер пор фильтра, тем более эффективно происходит осаждение пыли, так как при малом расстоянии между твердыми
102
элементами линии тока запыленного газа будут проходить на более близком расстоянии от этих элементов. Но при этом гидравлическое сопротивление возрастает гораздо быстрее, чем эффективность улавливания частиц пыли;
5)с повышением температуры газа повышается его вязкость. Поэтому осаждение на фильтровальной поверхности крупных частиц под действием сил инерции снижается, а эффективность осаждения мелких частиц под действием теплового движения газовых молекул увеличивается. Гидравлическое сопротивление фильтровального материала с повышением температуры газа возрастает;
6)с повышением скорости фильтрации инерционное осаждение крупных частиц возрастает, а осаждение под действием теплового движения газовых молекул уменьшается. Однако при большой скорости фильтрации возможны отрыв уже осевших частиц и унос вместе с газовым потоком;
7)чем больше поверхность фильтра, тем выше эффективность очистки;
8)с увеличением слоя пыли на фильтровальном материале эффективность улавливания пыли возрастает, однако при этом повышается гидравлическое сопротивление, при большом значении которого фильтрация газа может практически прекратиться.
Для создания требуемой скорости фильтрации по обе стороны фильтра необходимо поддерживать соответствующий перепад давлений. Величину этого перепада определяет расход энергии вентилятора или дымососа и поэтому является важной конструктивной и эксплуатационной характеристикой.
Скорость фильтрации в большинстве фильтров невелика, и процесс фильтрации происходит при ламинарном режиме движения газа.
Сопротивление фильтра пропорционально скорости газа, его вязкости
итолщинеслояфильтраизависитотструктурыфильтровальногоматериала
идругихфакторов. Оно может быть представлено каксуммасопротивлений собственнопористогофильтрующегослояислояосевшейпыли.
Эксплуатационные характеристики фильтров в значительной мере определяются их пылеемкостью (это количество пыли, которое фильтр способен удержать при непрерывной работе между периодами регенерации или смены фильтровального материала, г/м2 или мг/м2). Этот параметр зависит от размера пыли и минимален при улавлива-
103
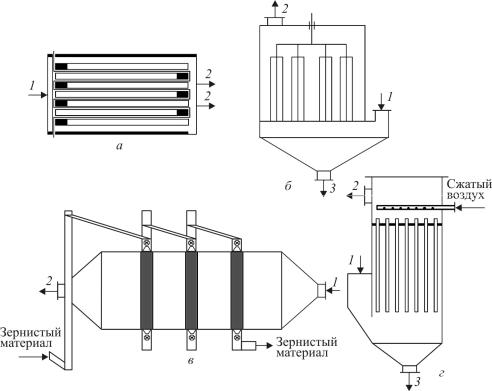
нии мелких частиц. На рис. 5.5 представлены аппараты с различными фильтрующими материалами.
Тканевые фильтры. Материалы, применяющиеся в фильтрах. Требования к ним. Расчет тканевого фильтра
Классификация промышленных фильтров. В этих фильтрах фильт-
ровальный слой выполнен в виде рукавов (тогда фильтры называют рукавными) илис плоскойразверткойткани.
Тканевые рукавные фильтры с высокой эффективностью применяют при очистке технологических и вентиляционных газов промышленных предприятий и гражданских объектов от частиц пыли размером более 0,1 мкм. Рассмотрим принцип действия такого фильтра.
Запыленный газ через входной патрубок поступает в бункер. Входной патрубок обычно располагают в верхней части бункера, но в некоторых случаях газ вводят в фильтр через патрубок, расположенный в его
Рис. 5.5. Фильтры: а – волокнистые; б – тканевые; в – зернистые; г – керамические
104
боковой части. В бункере газ разворачивается, в результате чего выпадают наиболее крупные частицы пыли, и входит в рукава, насаженные на патрубки, которые установлены на дырчатом листе. Число отверстий с патрубками в листе равно числу рукавов. Верхняя часть рукавов заглушена, они подвешены к раме, соединенной стержнем с механизмом встряхивания. Запыленный газ проходит через ткань рукавов и оставляет на их внутренней поверхности пыль. Очищенный от пыли газ поступает в корпус фильтра, откуда выводится через патрубок чистого газа. Осевшую в рукавах пыль удаляют при помощи механизма встряхивания и одновременно обратной продувкой рукавов. Для этого через патрубок, установленный в верхней части корпуса, подается воздух при помощи вентилятора, встроенного в рукавный фильтр или установленного вне его. Продувочный воздух проходит через ткань рукавов в направлении, обратном движению газа, и ломает корку пыли, осевшую на внутренней поверхности рукавов.
Включение механизма встряхивания и вентилятора обратной продувки осуществляется автоматически по мере достижения заданного гидравлического сопротивления фильтровальных рукавов. В период удаления пыли из рукавов в фильтр или его секцию прекращается подача газа, и фильтр отключается от коллектора чистого газа при помощи дроссель-клапана. При регенерации рукавов разрушается и удаляется из них только часть слоя пыли, в результате чего уменьшается сопротивление оставшегося слоя.
Пыль из рукавов ссыпается в бункер и при помощи шнека выводится через пылевыпускной патрубок, на котором установлен герметический затвор. Обычно фильтры выполняют с двумя и более секциями. Рукава очищают в каждой секции по очереди, в остальных в это время очищают газ.
Входные и выходные патрубки каждой секции соответственно объединяют общими коллекторами запыленного и чистого газов. Продувочный воздух через коллектор запыленного газа поступает на очистку в рабочие секции фильтра. В зависимости от конструкции фильтра количество проду- вочноговоздухасоставляет1,5–1,8 м3/(м2·мин), адавление1275–1470 Па.
Включение механизма встряхивания и вентилятора обратной продувки осуществляется автоматически по мере достижения заданного гидравлического сопротивления фильтровальных рукавов.
Кроме механического вибрационного встряхивания и обратной продувки удаление пыли из рукавов осуществляют кручением рукавов, аэродинамическим встряхиванием извуковой регенерацией.
105
При аэродинамическом встряхивании очистка рукавов происходит в результате пульсирующей подачи газа или воздуха между рукавами или подачи импульса сжатого воздуха внутрь каждого рукава при избыточном давлении сжатого воздуха 0,4–0,8 МПа и частоте импульсов 0,1–0,2 с. Расход продувочного воздуха составляет 0,1–0,4 % от количества очищаемых газов.
В этом случае отпадает необходимость в механизации операции встряхивания. Однако такой метод не обеспечивает равномерной регенерации рукавов в фильтре, так как вблизи сопел рукава очищаются слишком интенсивно, а на некотором расстоянии от них – недостаточно. Этот метод регенерации применяют при очистке газов от крупной пыли.
Фильтровальные ткани выбирают в зависимости от характеристик газа и содержащейся в нем пыли, температуры газов, стойкости против воздействия кислот, щелочей, света влаги, а также структуры пыли.
К тканям предъявляют следующие требования:
–обеспечение высокой пылеемкости при фильтрации;
–способность удерживать на своей поверхности такое количество пыли, которое обеспечивает высокую эффективность очистки газа от мелкодисперсной пыли;
–высокая механическая прочность при многократных изгибах;
–стойкость к истиранию;
–способность к легкому удалению пыли с поверхности ткани. Фильтровальные ткани могут быть ткаными и неткаными.
По характеристике поверхности ткани могут быть гладкими и ворси-
стыми. К первым относятся хлопчатобумажные ткани, лавсан, стекловолокно; онииспользуютсядляочисткигазаотволокнистойизернистойпыли.
К ворсистым тканям относятся суконные и шерстяные ткани, нитрон, капрон с шерстью; их применяют для очистки только от зернистой пыли, так как волокнистая пыль сцепляется с ворсом ткани и плохо удаляется при регенерации. Ворсистую ткань располагаю ворсом внутрь рукава в сторону входа запыленного газа.
Хлопчатобумажные ткани и шерсть относятся к природным материалам. Хлопчатобумажные ткани обладают хорошими фильтрующими свойствами; для повышения стойкости к кислотам их подвергают специальной обработке. Но их применяют притемпературе газов не выше85 ° С.
Шерстяные ткани также обеспечивают надежную очистку газа и обладают значительно большим сроком службы, чем хлопчатобумажные (9–12 мес.). Температура газового потока – не выше 100 ° С.
106
Ткани из синтетических волокон более стойки к воздействию высоких температур и агрессивных компонентов. Для повышения сопротивляемости таких материалов механическим воздействиям и истиранию их подвергают термической обработке. Так, рукава из силиконизированного стекловолокна или из многослойных тканей могут работать при температуре выше 300 ° С и обладают повышенной прочностью. Металлоткани обладают хорошей мехнической прочностью, высокой химической стойкостью и газопроницаемостью, удовлетворительной пылеемкостью в процессе фильтрации при высоких температурах. Для очистки газа, имеющего температуру до 600 ° С, применяют фильтровальные ткани из иглопробивных фетров, которые выполнены из металлических волокон. Асбестовые ткани используют для очистки газов при температурах до 500 ° С. Если температура газов достигает 900 ° С применяют фильтровальные элементы
сразвернутой поверхностью изкерамики.
Втканевых фильтрах из хлопчатобумажных и шерстяных тканей не допускается очистка влажных газов, так как влажная пыль может образовывать в порах ткани газонепроницаемую корку. При низких температурах возможна конденсация из газа водяных паров, которые также осаждаются на ткани. Для исключения конденсации необходимо, чтобы температура очищаемых газов была на 15–20 ° С больше температуры точки росы. Поэтому при низкой температуре газов их специально подогревают перед вводом в фильтр, а корпус фильтра термоизолируют. При высокой температуре газов их специально охлаждают.
Рукавные фильтры в зависимости от конструкции могут работать под разрежением или под избыточным давлением. В первом случае вентилятор устанавливают за фильтром по ходу движения газа, который просасывается через фильтр. Во втором случае подлежащий очистке газ нагнетают в фильтр вентилятором, стоящим до фильтра. Всасывающие фильтры, работающие под разрежением, должны быть герметичными.
По форме корпуса рукавные фильтры могут быть прямоугольными и реже круглыми или овальными.
Тканевый фильтровальный материал используется также в фильтрах с плоской разверсткой ткани, которую натягивают на проволочный каркас. Фильтрующие элементы в таких фильтрах имеют прямоугольную и реже клиновидную форму, которая обеспечивает большую поверхность фильтрации, чем в рукавных. Однако в них труднее удаляется пыль, сложнее сменяется фильтрующий слой и служит он по времени меньше.
107

При эксплуатации рукавных фильтров требуется соблюдать правила техники безопасности, которые исключают возможность воспламенения горючей пыли и отравления обслуживающего персонала при очистке токсичных газов.
В необходимых случаях следует применять фильтры и вентиляторы во взрывобезопасном исполнении и осуществлять очистку газов только под разрежением; своевременно удалять пыль из фильтра; устранять источники возникновения искр и статических зарядов; исключать возможность образования взрывоопасных смесей газа и пыли с атмосферным воздухом.
Расчет рукавного фильтра
1. Учитывая допустимую температуру газа для ткани лавсан, равную 130 ° С, определяем подсос воздуха с температурой 30 ° С, необходимый для охлаждения газа с заданной температурой до tг = 130 ° С. Используем балансовое уравнение:
Ссм (V0г + V0в) tсм = V0гCг tг + V0вCвTв,
где tсм, tг, tв – температуры смеси, газа и воздуха, ° С; V0г, V0в – объемы газа и воздуха при нормальных условиях, м3/ч; Cсм, Cг, Cв – теплоемкости смеси, газа и воздуха, Дж/(м3·К).
Принимаем Cсм = Cг = Cв, тогда
V = V0гtсм −V0гtсм .
0в |
tв − tсм |
|
2. Расход газа, идущего на фильтрование, при нормальных условиях, м3/ч,
Vсм = V0г + V0в,
3. Запыленность газа перед фильтром в рабочих условиях, г/м3,
Z раб = Z |
V0г |
. |
|
1 |
1 V |
||
|
|
см |
4. Допустимая удельная газовая нагрузка на фильтр, м3/(м2·мин),
qф = qн · С1 · С2 · С3 · С4 · С5,
где qн = 1,2 м3/(м2·мин) – для черных и цветных металлов; коэффициенты: С1 = 0,7 – для регенерации с обратной продувкой; С2 = 1,04 – при
108
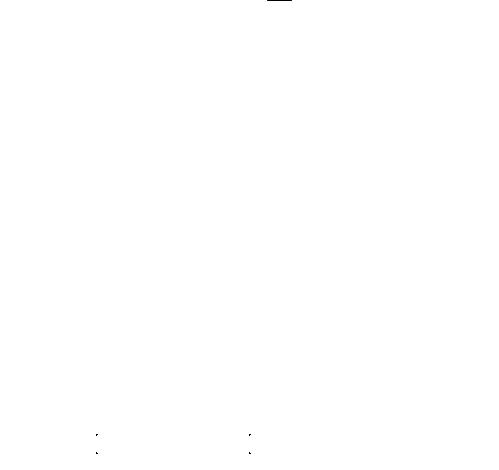
начальной рабочей запыленности Z1 = 7,9 г/м; С3 = 0,9 – при dm = 3 мкм; С4 = 0,725 – при tг = 130 ° С; С5 = 1 – при остаточной концентрации пыли более 30 мг/м. Скорость фильтрации, м/с,
WФ = qф/60.
5. Полное гидравлическое сопротивление фильтра ∆Р, Па, складывается из сопротивления корпуса ∆Рк и сопротивления фильтровальной перегородки ∆Рф:
∆Р= ∆Рк + ∆Рф.
Гидравлическое сопротивление корпуса фильтра, Па,
∆ Рк= ξρг Wвх2 ,
2
где Wвx – принимаемая скорость газа при входе в фильтр, м/с, равная 10; ξ – задаваемый средний коэффициент сопротивления при Wвx = 5–15 м/с, равный 2; ρг – плотность газа при рабочих условиях, кг/м:
ρ |
|
= ρ |
|
273Рв ± Рг |
. |
||
|
|
|
|
||||
|
г |
|
0г (273 + tг )101,3 |
||||
Гидравлическое сопротивление фильтровальной перегородки при |
|||||||
заданном ∆Р |
|
|
|
|
|
|
|
|
|
∆Рф = ∆Р – ∆Рк. |
|||||
6. Продолжительность периода фильтрования между двумя реге- |
|||||||
нерациями |
|
|
|
|
|
|
|
τф = |
∆ Рф / WфМг− А |
||||||
|
|
|
. |
||||
|
BW Z |
раб |
|||||
|
|
|
|
|
|
|
|
|
|
|
|
ф 1 |
Коэффициенты А и В выбираются по нижеприведенным данным в зависимости от среднемедианного размера частиц и вида пыли:
dm, мкм |
А, м–1 |
В, м/кг |
Вид пыли |
10–20 |
(1100–1500) 10 6 |
(6,5–16) 10 9 |
Кварцевая Цементная |
2,5–3 |
(2300–2400) 10 6 |
80–10 9 |
Сталеплавильная |
0,5–0,7 |
(13000–15000) 10 6 |
330–10 9 |
Кремниевая |
109
Динамический коэффициент вязкости газа при рабочих условиях, Па·с,
|
+ С |
Т |
1,5 |
|
µ = µ0 |
273 |
|
|
. |
Т + С |
|
|||
|
273 |
|
7. Количество регенераций в течение 1 ч
nр = 3600/(τф + τр).
8. Расход воздуха на регенерацию (скорость обратной продувки равна скорости фильтрования), м3/ч,
Vp = (Vcv – nр – τр)/3600.
9. Необходимая фильтровальная площадь, м2,
Fф = (Vcм + Vp)/60qф.
10.Тип рукавного фильтра выбирается из справочников.
11.Площадь фильтрования Fp, отключаемая на регенерацию в течение 1 ч, м2,
Fp = (Nc – Fc – np – τp) /3600.
12. Уточненное количество воздуха, расходуемое на обратную продувку в течение 1 ч, м,
Vp = Wф – Nc – Fc – np – τp.
13.Окончательная уточненная площадь фильтрования, м2,
14.Продолжительность периода фильтрования должна быть выше суммарного времени регенерации остальных секций, с,
15.Фактическая удельная газовая нагрузка
110