
книги / Расчёт и проектирование систем обеспечения безопасности.-1
.pdf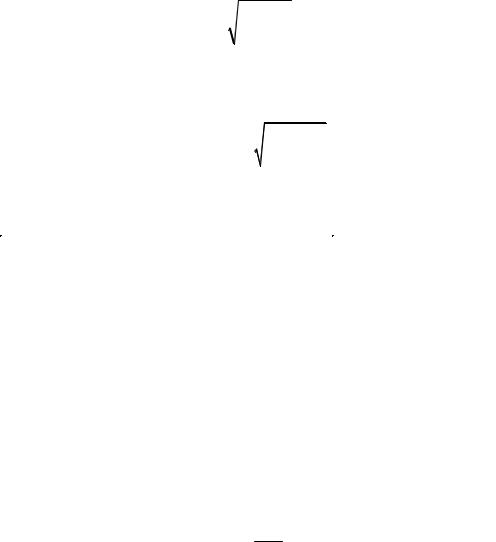
11. Напряженность электрического поля, В/м:
E = |
8i0 H |
, |
4π2 K0 S |
где i0 – диэлектрическая проницаемость вакуума, равная 8,85·10–12 ф/м. 12. Вязкость компонентов, входящих в состав дымовых газов при
рабочих условиях, Н·с/м2,
µ = µ |
|
273 + С |
|
273 + t |
3 |
|
0 |
|
|
|
|
, |
|
Т + С |
|
|||||
|
|
|
273 |
|
где µ0 – коэффициент динамической вязкости газа при нормальных условиях, Н·с/м2; С – коэффициент, характерный для каждого вида газа:
Вид газа |
С |
µо·10–6 , Н·с/м2 |
N2 |
114 |
17 |
Н2O |
961 |
10 |
CO2 |
254 |
13,7 |
O2 |
131 |
20,3 |
13. Вязкость дымовых газов: |
|
|
|||||
|
M |
= ∑ |
Mi |
|
%CO2 MCO 2 |
|
|
|
= 0, 01 |
+ ... , |
|||||
µ |
µi |
µCO2 |
|||||
|
|
|
|||||
где µi – коэффициент динамической вязкости |
i-газа при нормальных |
условиях; М – относительная молекулярная масса газов, кг/кмоль.
M= ∑ai Mi .
14.Коэффициент очистки газа
η = ∑ ηi φi , 100
где ηi – эффективность очистки газового потока от конкретной фракции,
ηi = 1− e− FWд ,
F – удельная поверхность осаждения, м2·с/м3,
F = Fэ/Vг,
Fэ – площадь осаждения осадительных электродов (из паспортных данных выбранного электрофильтра); φi – содержание данной фракции в составе пыли.
141
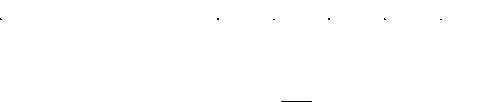
Скорость дрейфа Wд определяется для мелких частиц пыли (< 1 мкм) и для крупных частиц (> 1 мкм). Принимаем следующие размеры средних радиусовчастиц:
Размер частицыd, мкм |
< 1 |
1–2 |
2–15 |
15–30 |
> 30 |
Средний радиус частиц rср, мкм |
0,25 |
1,75 |
4,25 |
11,25 |
65 |
Скорость дрейфа мелких частиц:
Wд = 0,17 10−11 ECk ,
µ
где Сk – поправка Кенингема, равная:
Сk = 1+λ (А/r),
А – численный коэффициент, равный 0,815–1,63; λ – длина свободного пробега молекул газа, м, равна 10–7 .
Вопросы для самоконтроля
1.Как происходит зарядка частиц пыли в электрическом поле?
2.Из каких элементов состоит электрофильтр, их характеристика.
3.Из каких материалов изготавливают корпус электрофильтра?
4.По каким признакам классифицируют электрофильтры?
5.Какие факторы влияют на работу электрофильтра?
6.Типы сухих электрофильтров и области их применения.
7.Особенности конструкции мокрых электрофильтров.
ГЛАВА 6. РАСЧЕТ, ПРОЕКТИРОВАНИЕ СИСТЕМ И ТЕХНОЛОГИЧЕСКОГО ОБОРУДОВАНИЯ ХИМИЧЕСКИХ МЕТОДОВ ОЧИСТКИ
Для очистки газов от вредных газообразных компонентов используют преимущественно сорбционные методы. Процессы сорбции являются процессами массообмена, т.е. диффузного перехода газообразного компонента в жидкую или твердую среду.
142
6.1. АБСОРБЦИОННЫЕ МЕТОДЫ ОЧИСТКИ ГАЗОВ ОТ ГАЗООБРАЗНЫХ СОЕДИНЕНИЙ: ФИЗИКО-ХИМИЧЕСКИЕ ЗАКОНОМЕРНОСТИ ПРОЦЕССОВ ФИЗИЧЕСКОЙ АБСОРЦИИ. ОСНОВЫ ХЕМОСОРБЦИОННЫХ ПРОЦЕССОВ. ТЕХНОЛОГИЧЕСКОЕ ОФОРМЛЕНИЕ РАЗОМКНУТЫХ АБСОРБЦИОННЫХ ПРОЦЕССОВ. ЦИРКУЛЯЦИОННЫЕ ПРОЦЕССЫ ФИЗИЧЕСКОЙ
И ХИМИЧЕСКОЙ АБСОРБЦИИ. ТРЕБОВАНИЯ К АБСОРБЕНТАМ. АППАРАТУРНОЕ ОФОРМЛЕНИЕ АБСОРБЦИОННЫХ ПРОЦЕССОВ.
МЕТОДЫ РЕГЕНЕРАЦИИ АБСОРБЕНТОВ
Абсорбцией называют процесс избирательного поглощения газообразого компонента (сорбтива) из газообразной смеси жидким поглотителем (абсорбентом). Этот процесс ведут в аппаратах, называемых абсорберами. В случае, когда процесс абсорбции идет за счет физического поглощения абсорбентом того или иного газообразного компонента, он называется физической абсорбцией. При наличии химической реакции между поглощаемым компонентом и абсорбентом с образованием нового химического соединения процесс называется хемосорбцией. Возможно сочетание обоих процессов.
Физическая абсорбция является обратимым процессом. Это значит, что при определенных условиях поглощенный газ можно выделить из абсорбента и, следовательно, восстановить последний в его первоначальном состоянии. Такой процесс, называемый десорбцией, широко применяют в технике с целью многократного использования абсорбента.
Расчет абсорберов строится на основе решения уравнения материального баланса, который выражает закон постоянства массы в процессе абсорбции и при противотоке газа и жидкости имеет вид
Мг (yн – yв) = Мж (хн – хв),
где Мг, Мж – массовые расходы газовой смеси и жидкого абсорбента, кг/с; yн и yв – концентрации поглощаемого компонента (сорбтива) в газовой смеси, внизу и вверху абсорбера, кг/кг; хн и хв – концентрации поглощаемого компонента в поглощающей жидкости (абсорбенте) внизу и вверху абсорбера, кг/кг.
Удельный расход абсорбента определяется из уравнения материального баланса абсорбера:
m = Мж/Мг = (yн – yв)/(хн – хв).
143
Вторым основным уравнением, необходимым для расчета процесса абсорбции, является уравнение массопередачи:
М = βF∆yср,
где М – масса поглощенного компонента, кг/с; F – поверхность, через которую идет абсорбция, м2; β – коэффициент массопередачи, кг/м2; ∆yср – средняя движущая сила процесса абсорбции:
∆yср = (∆yн – ∆yв) /2,3 lg (∆yн/∆yв);
здесь ∆yн = yн – yн* – движущая сила внизу абсорбера, кг/кг; ∆yв = yв – yв* – движущая сила вверху абсорбера, кг/кг; yн* – концентрация улавливаемого компонента в газе при равновесном состоянии внизу абсорбера, кг/кг; yв* – то же вверху абсорбера, кг/кг.
Все абсорберы должны иметь развитую поверхность соприкосновения между жидкостью и газом. По способу образования этой поверхности абсорберы условно делят на поверхностные, распыливающие и барботажные.
Поверхностные абсорберы поглощают газ пленкой жидкости, образующейся на поверхностях, смачиваемых жидкостью и омываемых газом. Примером такого пленочного абсорбера может служить трубчатый абсорбер (рис. 6.1), в котором жидкость стекает сверху вниз по внутренней поверхности труб, омываемых поднимающимся снизу вверх газом. Насадочный скруббер, наиболее распространенный из поверхностных абсорберов, представляет собой вертикальный цилиндр, заполненный орошаемой сверху насадкой, сквозь которую снизу вверх проходит газ (см. рис. 6.1). Сильно развитая межфазная поверхность интенсифицирует работу абсорбера.
В качестве насадки часто применяют тонкостенные керамические или стальные кольца высотой, равной диаметру, изменяющемуся в пределах 15–150 мм. Мелкие кольца засыпают навалом, а крупные укладывают рядами, сдвинутыми относительно друг друга. Иногда в качестве насадок применяют кокс или дробленый кварц с размерами кусков
25–100 мм.
Основными характеристиками насадки являются ее удельная поверхность f0 и свободный объем V0 – отношение объема пустот к объему, занимаемому насадкой.
144
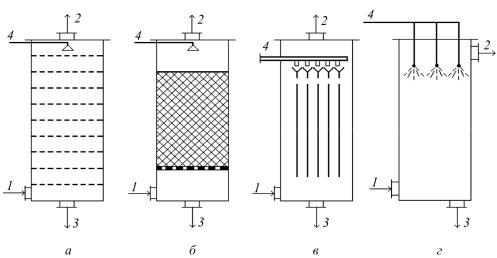
Рис. 6.1. Абсорбционные методы очистки: а – тарельчатые; б – насадочные; в – пленочные; г – распыливающие
Подвод орошающей жидкости осуществляют с помощью оросителя, обеспечивающего равномерное орошение насадки. Количество жидкости, подаваемой на 1 м2 поверхности насадки в единицу времени, называется плотностью орошения L; она зависит от типа насадки и находится обычно в пределах 5–20 м3/(м2ч).
Преимуществом насадочных абсорберов является простота устройства, что особенно важно при работе с агрессивными средами. Насадочные скрубберы малопригодны для работы с загрязненными газами и жидкостями вследствие забивания насадки и трудности ее регенерации, а также затрудненным отводомтепла, выделяющего припоглощениигаза.
Распыливающий полый абсорбер (см. рис. 6.1) представляет собой вертикальный цилиндр, в верхней части которого расположена система форсунок, равномерно распыливающих подаваемую в абсорбер жидкость. Газ, подводимый в абсорбер снизу, поднимается вверх и орошается мелкораспыленной жидкостью. Отвод газа осуществляют через верхнюю часть абсорбера, а жидкости – через нижнюю коническую его часть.
Размер капель жидкости в полом абсорбере не должен быть меньше 0,8–1,0 мм. Хотя при тонком распылении увеличивается межфазная поверхность и интенсифицируется массообмен, одновременно резко возрастает каплеунос, что вызывает значительные трудности вследствие образования отложений как в верхней части абсорбера, так и на последующих участках газоотводящего тракта.
145

К преимуществам полых распыливающих абсорберов относятся простота устройства, низкое гидравлическое сопротивление, возможность работы с загрязненными газами, легкость осмотра, чистки и ремонта. Недостатки этих аппаратов – невысокая эффективность, значительный расход энергии на распыливание жидкости, трудность работы с загрязненными жидкостями из-за засорения форсунок, повышенный расход абсорбента, низкие допустимые скорости газа, ограниченные уносом капель жидкости.
Распыливающие полые абсорберы применяют главным образом для поглощения хорошо растворимых газов. В последнее время получают распространение абсорберы с распылением жидкости в потоке движущегося газа со скоростью до 100 м/с. Такие абсорберы по устройству аналогичны скрубберам Вентури; они характеризуются большой интенсивностью ивысокой эффективностью. Их основным недостатком являются высокие энергозатраты вследствиебольшого гидравлического сопротивления.
В химической технологии применяют также барботажные тарельчатые абсорберы, однако в металлургии для целей очистки газов они не получили распространения.
Основы расчета абсорберов
Диаметр аппарата D выбирают, исходя из уравнения расхода, согласно которому
D = 4Vг / πw0 ,
где Vг – расход газа через аппарат, м3/с; w0 – скорость, отнесенная к полному сечению аппарата, м/с.
Скорость газа в абсорбере лимитируется ростом каплеуноса и гидравлического сопротивления. В полых аппаратах без каплеуловителей скорость обычно не превышает 1–1,5 м/с, в насадочных абсорберах и полых абсорберах с каплеуловителями – 5–5,5 м/с.
Необходимый объем абсорбера или поверхность насадки определяют из уравнения массопередачи. Для полых распыливающих аппаратов уравнение массопередачи применяют в следующем виде:
M = βVVa ∆ yср,
где М – масса поглощенного компонента, кг/с; Vа – рабочий объем абсорбера, м3; βv – объемный коэффициент массопередачи, кг/(м3-Па-ч); ∆уср – средняя движущая сила процесса абсорбции, Па.
146
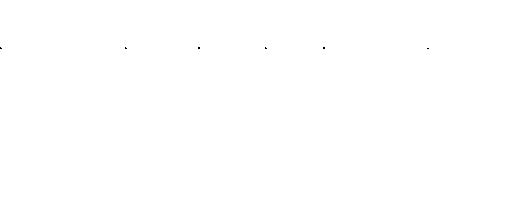
Для насадочных аппаратов необходимую поверхность насадки определяют по уравнению
Fн = М/β∆уср.
Необходимый объем насадки рассчитывают по величине удельной поверхности насадки f0 (табл. 6.1):
Vн = Fн/f0.
Рабочую высоту абсорберов Н определяют на основании принятого диаметра и необходимого рабочего объема абсорбера или насадки:
Н = 4Va/πD2.
Для полого абсорбера величина Н представляет собой высоту расположения нижнего пояса форсунок, для насадочного абсорбера – толщину слоя насадки.
Гидравлическое сопротивление полых абсорберов невелико и в зависимости от плотности орошения составляет 0,2–0,4 кПа. В насадочных абсорберах основным является гидравлическое сопротивление насадки, которое может быть подсчитано по формуле
∆р = ξ w2ρгН/2,
где Н – толщина слоя насадки, м; ξ – коэффициент сопротивления, который принимают в соответствии с данными табл. 6.1.
Таблица 6.1
Характеристики некоторых насадок
Вид насадки |
Удельная |
Свободный |
Удельная |
Средний |
Эквивалент- |
поверхность |
объемVс, |
масса, |
коэффициент |
ныйдиаметр |
|
|
f0, м2/м3 |
м3/м3 |
кг/м3 |
сопротивленияξср |
dэкв, мм |
Кольцакерамические, |
|
|
|
|
|
правильноуложен- |
|
|
|
|
|
ные, размером, мм: |
|
|
|
|
|
50× 50× 5 |
110 |
0,73 |
650 |
10–12 |
27 |
100× 100× 100 |
60 |
0,72 |
650 |
1 |
48 |
Кольцакерамические, |
|
|
|
|
|
беспорядочнолежа- |
|
|
|
|
|
щие, размером, мм: |
|
|
|
|
|
25× 25× 3 |
260 |
0,75 |
530 |
500–600 |
15 |
50× 50× 5 |
90 |
0,78 |
530 |
130–140 |
35 |
Кварцразмером, мм: |
|
|
|
|
|
25 |
120 |
0,32 |
1600 |
– |
10,5 |
75 |
42 |
0,46 |
1380 |
80 |
44 |
147
6.2. АДСОРБЦИОННЫЕ МЕТОДЫ ОЧИСТКИ ГАЗОВ ОТ ГАЗООБРАЗНЫХ СОЕДИНЕНИЙ. КИНЕТИКА АДСОРБЦИИ-ДЕСОРБЦИИ. ДИНАМИКА АДСОРБЦИИ. ОПРЕДЕЛЕНИЕ ВРЕМЕНИ ЗАЩИТНОГО ДЕЙСТВИЯ СЛОЯ И ВЫСОТЫ РАБОТАЮЩЕГО СЛОЯ. МЕТОДЫ РЕГЕНЕРАЦИИ АДСОРБЕНТОВ. КОНСТРУКЦИИ АДСОРБЕРОВ. ИНТЕНСИФИКАЦИЯ АДСОРБЦИОННЫХ ПРОЦЕССОВ
Адсорбцией называют процесс избирательного поглощения одного или нескольких компонентов (сорбтивов) из газовой смеси поверхностью твердого поглотителя-адсорбента. Этот процесс ведут в аппаратах, называемых адсорберами.
Вкачестве адсорбентов применяют пористые твердые вещества
сбольшой удельной поверхностью, относимой к единице массы. Поры, т.е. капиллярные каналы, условно можно разделить на макро- и микропоры. Макропоры имеют диаметр более 2 мкм, в то время как размеры микропор соизмеримы с размерами адсорбируемых молекул.
Адсорбенты характеризуются поглотительной способностью, определяемой концентрацией сорбтива в единице массы или объема вещества. Наиболее часто применяемыми адсорбентами являются активированные угли, силикагели и цеолиты.
Активированные угли – продукты сухой перегонки углеродсодержащих материалов – имеют удельную поверхность 600–1700 м/г с размером гранул 1–5 мм и насыпной плотностью 400–600 кг/м3. Разновидностью их являются угли из полимерных материалов, которые имеют мелкопористую, но более упорядоченную структуру и потому обладают большой механической прочностью. Отличительной их особенностью является повышенная адсорбционная активность в области малых концентраций поглощаемого компонента. В последнее время появился новый тип углеродных адсорбентов – активированные углеродные волокна, применяемые в виде тканей, лент, нетканого материала, войлока и т.п., обладающие следующими преимуществами: хорошим сочетанием адсорбционных и фильтрующих свойств; высокой адсорбционной активностью; удобством аппаратурного оформления, высокой химической, термической и радиационной стойкостью.
Силикагели – синтетические минеральные адсорбенты, являющиеся гелями кремниевой кислоты, выпускаются в разных модификациях. Удельная поверхность силикагелей изменяется в пределах 400–700 м/г, размер гранул 0,2–7 мм, насыпная плотность 400–800 кг/м3. Преимуще-
148
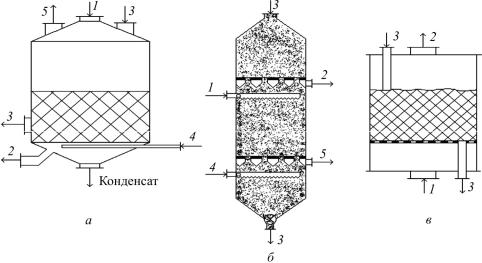
ствами силикагелей являются их негорючесть, высокая механическая прочность, а также низкая температура регенерации.
Цеолиты – синтетические или природные алюмосиликаты, отличающиеся мелкой и строго регулярной системой пор. Цеолиты проявляют молекулярно-ситовое действие, которое заключается в их способности не пропускать молекулы, размеры которых больше размера пор. В связи с этим цеолиты, называемые также молекулярными ситами, обладают высокой селективностью поглощения. Размер гранул цеолитов 2–5 мм, насыпная плотность 600–900 кг/м3. Цеолиты применяют для разделения газов, имеющих различные размеры молекул, а также для целей осушки, так как они имеют высокую поглотительную способность по отношению к водяным парам.
Устройство адсорберов
По конструкции адсорберы могут быть вертикальные, горизонтальные и кольцевые (рис. 6.2).
Рис. 6.2. Адсорберы: а – с неподвижным слоем; б – с движущимся слоем; в – с псевдоожиженным слоем
При неподвижном слое адсорбента процесс адсорбции носит периодический характер и протекает в четыре стадии. Первая стадия – собственно адсорбция, т.е. насыщение поглотителя адсорбируемым компонентом τад. Газовую смесь подают в адсорбер, пропускают через слой адсорбента и выводят из аппарата. Вторая стадия – десорбция по-
149

глощаемого компонента из слоя адсорбента τдес. Подачу газовой смеси прекращают. Через барботер в аппарат подают водяной пар, при этом смесь паров десорбированного компонента и воды, а также конденсат удаляют через соответствующие патрубки. Третья стадия – сушка поглотителя τсуш. Подача водяного пара прекращается, после чего влажный поглотитель сушится горячим воздухом, поступающим в аппарат. Четвертая стадия – охлаждение поглотителя τохл. Подача горячего воздуха прекращается, после чего поглотитель охлаждается холодным воздухом. По окончании четвертой стадии цикл работы аппарата повторяется. Загрузку и выгрузку поглотителя производят периодически через люки. Для того чтобы процесс адсорбции не прерывался, необходимо иметь, как минимум, два попеременно работающих адсорбера.
В кипящем слое процесс адсорбции протекает более интенсивно, чем в неподвижном слое, вследствие уменьшения внешнедиффузионного сопротивления из-за более высоких скоростей газового потока и внутридиффузионного сопротивления из-за меньших размеров зерен адсорбента. При интенсивном перемешивании в кипящем слое происходит сильное истирание зерен адсорбента, в связи с чем последний должен обладать повышенной механической прочностью.
Основы расчета адсорберов
Необходимый диаметр адсорбера находят по заданному расходу газовой смеси Vг и скорости газа wг:
D = Vг / 0, 785wг .
В промышленных условиях скорость газа принимают равной 0,1–0,25 м/с. Высота адсорбера зависит от толщины слоя адсорбента Н и определяется заданным временем защитного действия слоя τад, которое обусловлено технологическими требованиями.
Приближенно продолжительность собственно процесса адсорбции можно определить, исходя из концентраций адсорбированного компонента соответственно в начальный и конечный моменты процесса адсорбции хj и х2. Если масса адсорбента в слое равна Мад, то количество поглощаемого компонента за один цикл составит
М = Мад (х2 – х1).
Массу адсорбента легко определить по площади поперечного сечения F, толщине слоя и насыпной плотности ρнас:
150